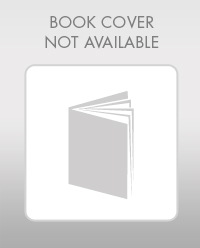
Principles Of Operations Management
11th Edition
ISBN: 9780135173930
Author: RENDER, Barry, HEIZER, Jay, Munson, Chuck
Publisher: Pearson,
expand_more
expand_more
format_list_bulleted
Concept explainers
Question
Chapter 12, Problem 39P
Summary Introduction
To determine: If Company HP must accept the quantity discount from the new supplier.
Expert Solution & Answer

Want to see the full answer?
Check out a sample textbook solution
Students have asked these similar questions
Dietary Management in a Nursing Home.
As detailed as possible.
Dietary Management in a Nursing Home.
As detailed as possible.
Dietary Management in a Nursing Home.
As detailed as possible.
Chapter 12 Solutions
Principles Of Operations Management
Ch. 12 - Ethical Dilemma Wayne Hills Hospital in tiny...Ch. 12 - Prob. 1DQCh. 12 - Prob. 2DQCh. 12 - What is the purpose of the ABC classification...Ch. 12 - Prob. 4DQCh. 12 - Explain the major assumptions of the basic EOQ...Ch. 12 - Prob. 6DQCh. 12 - Prob. 7DQCh. 12 - Prob. 8DQCh. 12 - What impact does a decrease in setup time hive on...
Ch. 12 - Prob. 10DQCh. 12 - Prob. 11DQCh. 12 - Explain the following: All things being equal, the...Ch. 12 - Prob. 13DQCh. 12 - Prob. 14DQCh. 12 - Prob. 15DQCh. 12 - When demand is not constant, the reorder point is...Ch. 12 - Prob. 17DQCh. 12 - State a major advantage, and a major disadvantage,...Ch. 12 - L. Houts Plastics it a large manufacturer of...Ch. 12 - Prob. 2PCh. 12 - Jean-Mane Bourjollys restaurant has the following...Ch. 12 - Lindsay Electronics, a small manufacturer of...Ch. 12 - Prob. 5PCh. 12 - Prob. 6PCh. 12 - William Sevilles computer training school, in...Ch. 12 - Prob. 8PCh. 12 - Prob. 9PCh. 12 - Matthew Liotines Dream Store sells beds and...Ch. 12 - Southeastern Bell stocks a certain switch...Ch. 12 - Lead time for one of your fastest-moving products...Ch. 12 - Annual demand for the notebook binders at Duncans...Ch. 12 - Thomas Kratzer is the purchasing manager for the...Ch. 12 - Joe Henrys machine shop uses 2,500 brackets during...Ch. 12 - Prob. 16PCh. 12 - Prob. 17PCh. 12 - Prob. 18PCh. 12 - Prob. 19PCh. 12 - Prob. 20PCh. 12 - Cesar Rego Computers, a Mississippi chain of...Ch. 12 - Prob. 22PCh. 12 - Prob. 23PCh. 12 - Prob. 24PCh. 12 - Prob. 25PCh. 12 - M. P. VanOyen Manufacturing has gone out on bid...Ch. 12 - Chris Sandvig Irrigation, Inc., has summarized the...Ch. 12 - Prob. 28PCh. 12 - Prob. 29PCh. 12 - Prob. 30PCh. 12 - Prob. 31PCh. 12 - Prob. 32PCh. 12 - Prob. 33PCh. 12 - Prob. 34PCh. 12 - Prob. 35PCh. 12 - Prob. 36PCh. 12 - Prob. 37PCh. 12 - Prob. 38PCh. 12 - Prob. 39PCh. 12 - Prob. 40PCh. 12 - Barbara Flynn is in charge of maintaining hospital...Ch. 12 - Prob. 42PCh. 12 - Authentic Thai rattan chairs (shown in the photo)...Ch. 12 - Prob. 44PCh. 12 - Prob. 45PCh. 12 - Prob. 46PCh. 12 - Prob. 47PCh. 12 - Gainesville Cigar stocks Cuban agars that have...Ch. 12 - A gourmet coffee shop in downtown San Francisco is...Ch. 12 - Prob. 50PCh. 12 - Prob. 51PCh. 12 - Henrique Correas bakery prepares all its cakes...Ch. 12 - Prob. 53PCh. 12 - Prob. 1CSCh. 12 - Prob. 2CSCh. 12 - Prob. 3CSCh. 12 - Prob. 1.1VCCh. 12 - Prob. 1.2VCCh. 12 - Prob. 1.3VCCh. 12 - Prob. 1.4VCCh. 12 - Prob. 1.5VCCh. 12 - Prob. 1.6VCCh. 12 - Prob. 1.7VCCh. 12 - Prob. 2.1VCCh. 12 - Prob. 2.2VCCh. 12 - Prob. 2.3VCCh. 12 - Prob. 2.4VCCh. 12 - Inventory Control at Wheeled Coach Controlling...Ch. 12 - Prob. 3.2VCCh. 12 - Inventory Control at Wheeled Coach Controlling...
Knowledge Booster
Learn more about
Need a deep-dive on the concept behind this application? Look no further. Learn more about this topic, operations-management and related others by exploring similar questions and additional content below.Similar questions
- Dietary Management in a Nursing Home. As detailed as possible.arrow_forwardFor dietary management in a nursing home. As detailed as possible.arrow_forwardA small furniture manufacturer produces tables and chairs. Each product must go through three stages of the manufacturing process – assembly, finishing, and inspection. Each table requires 3 hours of assembly, 2 hours of finishing, and 1 hour of inspection. The profit per table is $120 while the profit per chair is $80. Currently, each week there are 200 hours of assembly time available, 180 hours of finishing time, and 40 hours of inspection time. Linear programming is to be used to develop a production schedule. Define the variables as follows: T = number of tables produced each week C= number of chairs produced each week According to the above information, what would the objective function be? (a) Maximize T+C (b) Maximize 120T + 80C (c) Maximize 200T+200C (d) Minimize 6T+5C (e) none of the above According to the information provided in Question 17, which of the following would be a necessary constraint in the problem? (a) T+C ≤ 40 (b) T+C ≤ 200 (c) T+C ≤ 180 (d) 120T+80C ≥ 1000…arrow_forward
- As much detail as possible. Dietary Management- Nursing Home Don't add any fill-in-the-blanksarrow_forwardMenu Planning Instructions Use the following questions and points as a guide to completing this assignment. The report should be typed. Give a copy to the facility preceptor. Submit a copy in your Foodservice System Management weekly submission. 1. Are there any federal regulations and state statutes or rules with which they must comply? Ask preceptor about regulations that could prescribe a certain amount of food that must be kept on hand for emergencies, etc. Is the facility accredited by any agency such as Joint Commission? 2. Describe the kind of menu the facility uses (may include standard select menu, menu specific to station, non-select, select, room service, etc.) 3. What type of foodservice does the facility have? This could be various stations to choose from, self-serve, 4. conventional, cook-chill, assembly-serve, etc. Are there things about the facility or system that place a constraint on the menu to be served? Consider how patients/guests are served (e.g. do they serve…arrow_forwardWork with the chef and/or production manager to identify a menu item (or potential menu item) for which a standardized recipe is needed. Record the recipe with which you started and expand it to meet the number of servings required by the facility. Develop an evaluation rubric. Conduct an evaluation of the product. There should be three or more people evaluating the product for quality. Write a brief report of this activity • Product chosen and the reason why it was selected When and where the facility could use the product The standardized recipe sheet or card 。 o Use the facility's format or Design one of your own using a form of your choice; be sure to include the required elements • • Recipe title Yield and portion size Cooking time and temperature Ingredients and quantities Specify AP or EP Procedures (direction)arrow_forward
- ASSIGNMENT: Inventory, Answer the following questions 1. How does the facility survey inventory? 2. Is there a perpetual system in place? 3. How often do they do a physical inventory? 4. Participate in taking inventory. 5. Which type of stock system does the facility use? A. Minimum stock- includes a safety factor for replenishing stock B. Maximum stock- equal to a safety stock plus estimated usage (past usage and forecasts) C. Mini-max-stock allowed to deplete to a safety level before a new order is submitted to bring up inventory up to max again D. Par stock-stock brought up to the par level each time an order is placed regardless of the amount on hand at the time of order E. Other-(describe) Choose an appropriate product and determine how much of an item should be ordered. Remember the formula is: Demand during lead time + safety stock = amount to order Cost out an inventory according to data supplied. Remember that to do this, you will need to take an inventory, and will need to…arrow_forwardHuman Relations, Systems, and Organization Assignments ORGANIZATION: Review the organization chart for the facility • Draw an organization chart for the department. • . Identify and explain the relationships of different units in the organization and their importance to maintain the food service department's mission. Include a copy in your weekly submission. There is a feature in PowerPoint for doing this should you want to use it. JOB ORGANIZATION: ⚫ A job description is a broad, general, and written statement for a specific job, based on the findings of a job analysis. It generally includes duties, purpose, responsibilities, scope, and working conditions of a job along with the job's title, and the name or designation of the person to whom the employee reports. Job description usually forms the basis of job specification. • Work with your preceptor or supervisor to identify a position for which you will write a job description. Include a copy of the job description you write in your…arrow_forwardASSIGNMENT: Production Sheet Watch at least 3 workers prepare foods. Write down what they do and the amount of time it takes for them to complete the task. Calculate the production cost. Example: Food Item: Green Beans Time Worker #1 Worker #2 Worker #3 Start End Time (Hours) Time Time Activity Activity Activity (Hours) (Hours) 11:45 am 12:01 pm 0.27 Steam and 0.05 Microwave blenderize pureed frozen green green beans beans 16.25 Total Production Time 3 minutes minutes Hourly Wage $16.07 $12.28 24% Benefits *** $3.86 $2.95 Labor Costs $5.37 $0.76 *** Check with facility to see Benefit %arrow_forward
- Menu Planning and Quality Monitoring Rotation site: Hospital/Commercial Foodservice Rotation Objectives: Menu development (this will be your Theme Meal) 1. Develop a modified menu (vegetarian, vegan, gluten-free, etc.) that is appropriate in texture, color, flavor, eye appeal, temperature, and methods of preparation. 2. Develop a menu that takes into consideration food preferences due to clients' ethnicity and age group. 3. Develop menus that fulfill the nutritional needs of the target population. 4. Develop a modified menu that maintains consistency with a regular menu. 5. Demonstrate knowledge of operational constraints and limitations when designing menus 6. Identify appropriate type and amounts of foods for an emergency plan. ACTIVITY: Quality improvement monitoring 1. Participates in rounds to get feedback from clients on Theme Meal menu. 2. Takes corrective actions if necessary according to results of the quality measures 3. Completes one or more critical incident reports for the…arrow_forwardWork with the chef and/or production manager to identify a menu item (or potential menu item) for which a standardized recipe is needed. Record the recipe with which you started and expand it to meet the number of servings required by the facility. Develop an evaluation rubric. Conduct an evaluation of the product. There should be three or more people evaluating the product for quality. Write a brief report of this activity • Product chosen and the reason why it was selected When and where the facility could use the product The standardized recipe sheet or card ○ Use the facility's format or о Design one of your own using a form of your choice; be sure to include the required elements Recipe title " Yield and portion size ■ Cooking time and temperature Ingredients and quantities Specify AP or EP Procedures (direction)arrow_forwardItem Prepared: Work with one or more cold food production workers to learn job descriptions, flow of work, how the menu items are prepared and served, and needs for further training or process improvement. Document a specific menu item you prepared. Record the temperature of a product when it goes into the refrigerator or blast chiller. Record how long it took for the product to cool to the appropriate temperature. Evaluate the menu item you were involved in preparing. Follow the product and process to completion and utilize resources to correct any wrong procedures you observe. Take your notes and write a brief report of the actual experience based on the following criteria: 1. Pre-preparation 2. Preparation 3. Compare menu item to diets it is used for by completing a nutritional analysis 4. Temperatures during and after preparation. 5. Tray service to patient or guest (how it looks, holds up, appropriate temperature maintained from production through delivery) 6. Waste disposal (what…arrow_forward
arrow_back_ios
SEE MORE QUESTIONS
arrow_forward_ios
Recommended textbooks for you
- Purchasing and Supply Chain ManagementOperations ManagementISBN:9781285869681Author:Robert M. Monczka, Robert B. Handfield, Larry C. Giunipero, James L. PattersonPublisher:Cengage LearningMarketingMarketingISBN:9780357033791Author:Pride, William MPublisher:South Western Educational Publishing
- Practical Management ScienceOperations ManagementISBN:9781337406659Author:WINSTON, Wayne L.Publisher:Cengage,Contemporary MarketingMarketingISBN:9780357033777Author:Louis E. Boone, David L. KurtzPublisher:Cengage Learning
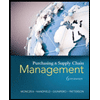
Purchasing and Supply Chain Management
Operations Management
ISBN:9781285869681
Author:Robert M. Monczka, Robert B. Handfield, Larry C. Giunipero, James L. Patterson
Publisher:Cengage Learning
Marketing
Marketing
ISBN:9780357033791
Author:Pride, William M
Publisher:South Western Educational Publishing
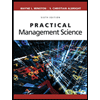
Practical Management Science
Operations Management
ISBN:9781337406659
Author:WINSTON, Wayne L.
Publisher:Cengage,
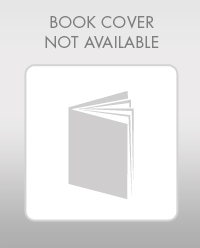
Contemporary Marketing
Marketing
ISBN:9780357033777
Author:Louis E. Boone, David L. Kurtz
Publisher:Cengage Learning
Inventory Management | Concepts, Examples and Solved Problems; Author: Dr. Bharatendra Rai;https://www.youtube.com/watch?v=2n9NLZTIlz8;License: Standard YouTube License, CC-BY