Mack’s guitar fabrication shop produces low-cost, highly durable guitars for beginners. Typically, out of the 100 guitars that begin production each month, only 80 percent are considered good enough to sell. The other 20 percent are scrapped due to quality problems that are identified after they have completed the production process. Each guitar sells for $250. Because some of the production process is automated, each guitar only requires 10 labor hours. Each employee works an average 160 hours per month. Labor is paid at $10/hour, materials cost is $40/guitar, and overhead is $4,000.
Mack’s guitar fabrication shop produces low-cost, highly durable guitars for beginners. Typically, out of the 100 guitars that
begin production each month, only 80 percent are considered
good enough to sell. The other 20 percent are scrapped due to
quality problems that are identified after they have completed
the production process. Each guitar sells for $250. Because
some of the production process is automated, each guitar only
requires 10 labor hours. Each employee works an average
160 hours per month. Labor is paid at $10/hour, materials cost
is $40/guitar, and overhead is $4,000.
a. Calculate the labor and multifactor productivity ratios.
b. After some study, the operations manager Darren Funk
recommends three options to improve the company’s
multifactor productivity: (1) increase the sales price by
10 percent, (2) improve quality so that only 10 percent
are defective, or (3) reduce labor, material, and overhead
costs by 10 percent. Which option has the greatest impact
on the multifactor productivity measure?

Step by step
Solved in 7 steps with 30 images

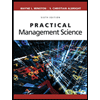
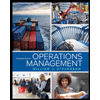
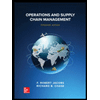
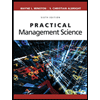
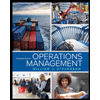
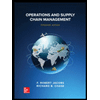
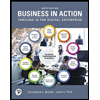
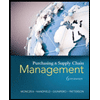
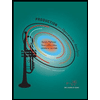