Project Submission 1
pdf
keyboard_arrow_up
School
Carleton University *
*We aren’t endorsed by this school
Course
1046
Subject
Mechanical Engineering
Date
Jan 9, 2024
Type
Pages
14
Uploaded by DeanOyster2527
ECOR 1046 Mechanics Submission 1 1 ECOR 1046 Mechanics Roof Truss Design (Submission 1) Submission 1 shall be submitted by 11:30 am November 24
th
. It shall consist of: 1.
Calculations of the point loads acting on the Truss
2.
An Engineering drawing showing the geometry of the truss, the point loads acting on the truss, and clearly labeled joints.
3.
A full analysis showing the forces acting on each truss member. All calculations and Free body diagrams of each analysis must be shown.
4.
A table and a second engineering drawing summarizing all the forces acting on each truss member. Drawing Guidelines: Two engineering drawings are required and must be completed using drawing tools such as AutoCAD or a similar software (SketchUp, LibreCAD, Google Documents drawing tool). All the drawings must show the dimensions of the truss. The two required engineering drawings are: I.
The truss with the external applied loads and reactions; and II.
The truss with the internal tension and compression forces acting on the members See the example drawings in Appendix B of this document. A title block is not required. Format the engineering drawings on 8.5x11” paper in landscape orientation
. Drawings should be laid out to make effective use of the entire page
. The drawings should include the drawing name, the course name and number, the names of group members, and the group name. Group Specified Variables and Input Parameters Each group will be assigned a different combination of 5 parameters: span length, spacing between trusses, spacing between open web steel joists, concrete slab thickness and snow accumulation on the roof. It is important that you design for the assigned variables and parameters. The assigned group parameters will be available on Brightspace. Figure 1: Standard Hockey Arena
ECOR 1046 Mechanics Submission 1 2 Figure 1 above shows that the standard width of ice in a hockey arena is 25.9 m. The span of the roof truss you will be designing must be greater than the width of the hockey rink and bleachers, to prevent obstructions on the rink and prevent obstructions to the view of spectators. For this project, different spans will be assigned to each group. The standard length of the ice surface in a hockey arena is 61 m. The length of the roof depends on the spacing between the 11 trusses supporting the roof. The spacing between the roof trusses will be different for each group. Open web steel joists span the spacing between the trusses. A plan view of the structure supporting the roof is shown in Figure 2 below. Your objective is to design the interior truss along column line D. Figure 2: Plan View of Arena Technical Considerations Truss Design During the design process, designers often estimate the results of calculations before performing the calculations. Critical thinking of the outcomes helps designers achieve the most effective design faster and allows them to notice errors. Geometry The variables that determine the geometry of the truss include the truss type, the support orientation, the span, and spacing between trusses. The support orientation, span length, spacing between trusses and spacing between open web steel joists will be provided. Each group must independently determine which truss type is optimal for their design. Each group will design one of the several trusses supporting the roof of the hockey arena. No group will have the same design, although multiple groups will be designing a truss with Truss Open web steel joist
ECOR 1046 Mechanics Submission 1 3 some of the same variables. Refer to Lectures on methods of truss analysis (Method of Joints and Method of Sections) to analyze and determine the forces in the members of your truss. Supports For this project, assume the roof truss is simply supported
, i.e. one end of the roof truss is supported by a pin-support, and the other end is supported by a roller-support. Loads There are several different loads that act on structures. The different loads can be categorized as follows: •
Dead Loads: Permanent loads that act on the structure over its entire lifetime. Dead loads are the self-weight of structural members.
•
Live Loads: Live loads are due to the use and occupancy of structure.
•
Snow Loads: Are due to the accumulation of snow or ice on structure.
•
Wind Loads: Loads applied to structures due to high wind pressures.
•
Earthquake Loads: These loads are due to seismic and earthquake events.
Snow Load The snow load is calculated based on the anticipated maximum snow load that may occur every 1 in 50 years. The NBCC specifies the weight of snow to be approximately 3.2 ?𝑁 ?
3
⁄
.
For this project, the anticipated snow accumulation on the roof will be provided as one of the design variables for the project. The NBCC also states that rainwater accumulation in snow must be accounted for as well, as wet snow is heavier. Wet snow has contributed to the collapse of structures in the past, such as the Listowel Arena in Orangeville (Figure 3). Figure 3: Listowel Arena Collapse.
Your preview ends here
Eager to read complete document? Join bartleby learn and gain access to the full version
- Access to all documents
- Unlimited textbook solutions
- 24/7 expert homework help
ECOR 1046 Mechanics Submission 1 4 The NBCC accounts for the accumulation of rainwater in snow. For this this project the additional load due to rain will be 0.4 ?𝑁 ?
2
⁄
. The load per unit area of snow can be calculated using the following equation: 𝑆
?
= 𝛾
?
ℎ
?
Where: •
𝑆
?
: Snow load due to accumulation of snow (KPa). •
𝛾
?
= 3.2 ?𝑁 ?
3
⁄
: Unit weight of snow. •
ℎ
?
: Anticipated height of snow accumulation (m). The total snow load per unit area acting on the roof of the arena is a combination of the accumulation of snow and the additional load due to rain: 𝑆 = 𝑆
?
+ 𝑆
?
Where: •
𝑆
: Total snow load (kPa). •
𝑆
?
: Snow load due to accumulation of snow (kPa). •
𝑆
?
= 0.4 ?𝑁 ?
2
⁄
: Load due to accumulation of water (kPa). Concrete Slab, Steel Deck, and Roof Insulation A corrugated steel deck is used to support roof finishes and the snow load on the roof. Sometimes, the steel deck on also has a layer of concrete as shown in Figure 4. This layer of concrete is known as a concrete slab. The concrete slab increases the strength of the roof but adds cost and weight. For this project, a steel deck with a concrete slab will be used. The concrete slab thickness will be assigned to each group as a design variable. Figure 4: Steel Deck with Concrete Slab.
ECOR 1046 Mechanics Submission 1 5 To calculate the weight of the concrete slab and the steel deck, the slab-deck system can be divided into three separate components as follows: 1.
Steel Deck: Steel decks are often light due to the thickness of the steel deck being between 0.76 mm –
1.21 mm. The weight of the steel deck to be used in this project can be taken as 𝑊
??
= 0.10 ?𝑁 ?
2
⁄
. 2.
Concrete Cover: Is the portion of concrete that is above the top of the steel deck profile (i.e. steel deck flute) highlighted in Figure 5. Figure 5: Concrete Slab and Steel Deck Dimensions. The weight of the concrete slab can be calculated as follows: 𝑊
??
= (?
?
− ℎ
?
) × 𝛾
?
Where: •
𝑊
??
: Weight of concrete cover (?𝑁 ?
2
⁄
)
•
?
?
: Thickness of the concrete slab in (mm). •
ℎ
?
= 38??
: Height of the steel deck flute •
𝛾
?
= 24 ?𝑁 ?
3
⁄
: The unit weight of concrete 3.
Concrete Between Flutes: This is the portion of the slab that is contained in the flutes highlighted in Figure 6. Figure 6: Concrete Contained in Flute. A good approximation to obtain the weight per unit area of concrete contained in the flutes is to use half the height of the flute. 𝑊
?𝑓
= (
ℎ
?
2
) × 𝛾
?
Where: •
𝑊
?𝑓
= Weight of concrete between steel deck flutes (?𝑁 ?
2
⁄
)
. •
ℎ
?
= 38??
: Height of the steel deck flute •
𝛾
?
= 24 ?𝑁 ?
3
⁄
: The unit weight of concrete
ECOR 1046 Mechanics Submission 1 6 In addition to the steel deck and concrete slab weights, we must also account for the weight of roof finishes. Roof finishes are used to protect the roof from the elements (snow, rain, wind, UV, etc.). For this project, assume the use of built-up roof (Figure 7) with a weight of 𝑊
?
= 0.31(?𝑁 ?
2
⁄
)
.
Figure 7: Built-up roof The total weight of the concrete slab and steel deck is the summation of all the above components: 𝑊
?
= 𝑊
??
+ 𝑊
??
+ 𝑊
?𝑓
+ 𝑊
?
Where: •
𝑊
?
= The total weight of all roof components (?𝑁 ?
2
⁄
)𝑜? ?𝑃𝑎
. •
𝑊
??
= Weight of steel deck (?𝑁 ?
2
⁄
)𝑜? ?𝑃𝑎
. •
𝑊
??
= Weight of concrete cover (?𝑁 ?
2
⁄
) 𝑜? ?𝑃𝑎
. •
𝑊
?𝑓
= Weight of concrete between steel deck flutes (?𝑁 ?
2
⁄
) 𝑜? ?𝑃𝑎
. Load Factors To account for the variability in loads acting on structures, the National Building Code of Canada (NBCC) uses load factors to magnify applied loads. This design philosophy is known as limit states design. Limit states used to prevent the collapse or failures of structures are known as ultimate limit states (ULS). Structural failures may include rupture, instability, or buckling. To determine the internal loads developed in the truss members, the snow and dead loads, calculated as shown above, need to be multiplied by load factors to determine the total factored loads. The NBCC outlines several load factors and load combinations which can be used in structures depending on different loading conditions. For this project we will only
Your preview ends here
Eager to read complete document? Join bartleby learn and gain access to the full version
- Access to all documents
- Unlimited textbook solutions
- 24/7 expert homework help
ECOR 1046 Mechanics Submission 1 7 be focused on the load combination that magnifies dead and snow loads. In this load combination, the dead and snow loads applied to the truss are multiplied by the following factors to determine the factored load per unit area 𝑤
𝑓
: 𝑤
𝑓
= 1.25𝐷 + 1.5𝑆
•
𝑤
𝑓
: Factored load per unit area applied on the roof •
Dead load (D): 1.25 (self-weight of concrete slab and other roofing materials) •
Snow Load (S): 1.5 (accumulated snow and rain) Since the design of the roof truss is an iterative process, do not account for the weight of the truss members or the open web steel joists in this iteration of your design. The self-weight of the truss and the weight of the open web steel joists is often accounted for in a later iteration of the design, and will be outside the scope of this project. Load Path The load path is the sequence in which loads are transferred through various members from the location where they are applied until they reach the foundation of the structure. The load path for the arena roof is as follows: The snow rests on the built-up roof. The weight of the snow and built-up roof is supported by the presence of a steel deck with a concrete cover. The steel deck distributes the loads to the open-web steel joists. Open web steel joists are supported at each end by roof trusses. There elements are the main components of the roof system shown in Figure 8 below. Roof trusses are supported at their ends by columns which transfer that load to the foundation of the structure. Figure 8: Components of Arena Roof. Loads Transferred to Open Web Steel Joists and Tributary Area Each open web steel joist is designed to resist loads applied to the area that it directly supports. This area is referred to as the “Tributary Area” of the joist. Consider the floor plan shown in Figure 9 where the open web steel joists span east to west and the main trusses
ECOR 1046 Mechanics Submission 1 8 span north to south. The spacing between joists is 4 m and the spacing between trusses is 9 m. Figure 9: Arena Floor Plan. The typical tributary area supported by each joist is as shown in Figure 10 below. Figure 10: Tributary Area Acting on Open Web Steel Joist. To design the open web steel joists as 2D members, the loads applied on this tributary area need to be converted to a uniformly distributed load (UDL). The uniformly distributed load can be calculated by multiplying the load per unit area by the width of the area that the joist supports, referred to as the tributary width. In this project, the tributary width of the joists is simply the spacing between the joists ?
𝑗
. This gives us the following equation for calculating the factored uniformly distributed load acting on the joists: 𝑈𝐷𝐿
𝑓𝑗
= 𝑤
𝑓
× (𝑆
𝑗
)
Where: •
𝑈𝐷𝐿
𝑓𝑗
: Factored uniform distributed load acting on the joist (?𝑁 ?
⁄
)
•
𝑤
𝑓
: Factored load per unit area applied on the roof (?𝑁 ?
2
⁄
)
•
?
𝑗
: Spacing between joists (?)
ECOR 1046 Mechanics Submission 1 9 The free body diagram of the open web steel joist is shown in fugure 11 below. Figure 11: FBD of open web steel joist Load Transfer from Open Web Steel Joists to Truss Open web steel joists are supported by a truss at each of its ends. Since joists are symmetric about their midspan, the factored support reaction at each joist end 𝑃
𝑓𝑗
is equal to the factored uniformly distributed load on the joist 𝑈𝐷𝐿
𝑓𝑗
, multiplied by the length of each joist and divided by 2. Since the length of the joist is equal to the spacing between the trusses ?
?
, we can arrive at the following expression for calculating the factored reaction at joist ends 𝑃
𝑓𝑗
: 𝑃
𝑓𝑗
= 𝑈𝐷𝐿
𝑓𝑗
× ?
?
/2
𝑃
𝑓𝑗
= 𝑤
𝑓
?
𝑗
?
?
/2
The load applied at the connection between the OWSJ and the truss is equal to 2 times the factored support reaction of the joists 𝑃
𝑓𝑗
, and that is simply because interior trusses support pairs of open web steel joists, a joist to the left and a joist to the right of the truss. This is shown in Figure 12 below. Figure 12: Interior
trusses often support OWSJ in pairs
Your preview ends here
Eager to read complete document? Join bartleby learn and gain access to the full version
- Access to all documents
- Unlimited textbook solutions
- 24/7 expert homework help
ECOR 1046 Mechanics Submission 1 10 Accordingly, the factored load applied to the truss from the joists 𝑃
𝑓
can be calculated as follows: 𝑃
𝑓
= 2 × 𝑃
𝑓𝑗
= 2 × 𝑤
𝑓
?
𝑗
?
?
/2
𝑃
𝑓
= 𝑤
𝑓
?
𝑗
?
?
Where: •
𝑃
𝑓
: Factored load applied to the truss from the joists •
𝑤
𝑓
: Factored load per unit area applied on the roof (?𝑁 ?
2
⁄
)
•
?
𝑗
: Spacing between joists (?)
•
?
?
: Spacing between trusses (?)
The open web steel joists should be placed at the joints of the main truss. This is done to ensure the truss members do not have to resists any internal shear or moment. Accordingly, the FBD of a truss would be similar to the one shown in Figure 13 below. Figure 13: FBD of truss supported by columns at each end Truss properties (Truss span, truss spacing, truss depth and joist spacing) For this project different groups will be assigned different span lengths varying between 35 m and 42 m, and different truss spacings ranging from 7 m to 11 m. The height of the truss, also commonly referred to as the depth of the truss, is dependent on the total span of the truss and how much load the truss carries. A good estimate for the design depth of the truss ranges between 𝒍
??
≤ 𝒉 ≤
𝒍
𝟗
(shown in Figure 14)
.
For heavy loaded trusses use a depth closer to 𝑙
9
, for lighter loads use a depth closer to 𝑙
12
.
ECOR 1046 Mechanics Submission 1 11 Figure 14: Truss depth Another important truss property is the spacing of joists, which in turn sets the points of applications of the load on the truss. In structural design, it is efficient to space the joists relatively close to each other. Another reason to keep joist spacing low is to ensure steel decking is long enough to span between the joists. For this project, use an equal spacing between joists equal to 𝒍
?𝟒
where ? is the span of the truss. This should result in 13 equally spaced point loads along the span of the truss. Truss Types Each group must determine an appropriate truss type for their design. Some truss types to choose from include Pratt, Howe, warren without verticals and Warren-with-verticals as shown in Table 1 below. Table 1: Some suggested truss types Pratt Truss Howe Truss Warren without verticals Warren with verticals Truss Analysis Internal Forces Determine the internal forces
acting on the truss members based on the loads you determined previously. Choose either the Method of Joints or the Method of Sections to analyze your truss.
ECOR 1046 Mechanics Submission 1 12 Draw a free body diagram
of the internal forces acting on the members of the truss, showing which members are in tension and which members are in compression. See the example engineering drawing in Appendix B.
Recall: Internal tension forces pull on the member ends while internal compression forces push on the member ends as shown in Figure 15. Figure 15: Sign convention for internal forces in truss members.
Your preview ends here
Eager to read complete document? Join bartleby learn and gain access to the full version
- Access to all documents
- Unlimited textbook solutions
- 24/7 expert homework help
ECOR 1046 Mechanics Submission 1 13 Appendix A:
Example Results Table
Member Factored Internal Force (kN) Selected Member Designation Member Resistance (kN) AB ex: 570 kN (T) ex: HSS 152 X 102 X 11 ex: 1100 kN (T) AD ex: 470 kN (C) ex: 500 kN (C) BD BC CD CE DE
ECOR 1046 Mechanics Submission 1 14 Appendix B: Example Engineering Drawings (please note each drawing should take up one full page and must
have a clear title block at the bottom right corner) Figure 1A: Sample Internal Forces Diagram without a title block
Related Documents
Related Questions
Help!!! Please answer part B correctly!!! Please
arrow_forward
Please write clearly / legibly. Thanks!
arrow_forward
Part 1:
up a study about types of trusses and its importance and applications.
Perform a design and structural analysis for the forces acting on the members of the truss
shown in the figure below using the method of joints and the method of sections
Make a critical comparison between the two methods
Estimate the load in each member of the trusses shown in the figure below
Show the detailed calculations and computation of the estimated load.
Explain the impact of these calculations on the design of different constructions.
Set
Part 2
A Pratt roof truss is loaded as shown. Using the method of joints and the method of
sections, determine the force in all members.
for the force P =171
80 kN
P kN
60 kN
в
8 m
60 kN
A
G-
MATHaling.com
6 m
600 C
6 m
E
6 m
40 kN
100 kN
6 m
arrow_forward
Help!!! Answer part B correctly
arrow_forward
Learning Goal:
To apply the condition of equilibrium to three-
dimensional systems and solve for unknown forces.
Part A - Finding the tension in cable AC
▼
As shown, a mass is being lifted by a strut that is
supported by two cables AC and CD. The dimensions
given are a
d = 3.70 ft, and e = 4.70 ft.(Figure 1)
A weight of 125 lb acts at C on the strut. Find the magnitude of the tension in cable AC.
= 7.30 ft, 6 = 4.70 ft, c = 8.10 ft,
Express your answer to three significant figures and include the appropriate units.
• View Available Hint(s)
HẢ
?
ТАС
Value
Units
Submit
Part B - Finding the unknown weight
▼
Figure
1 of 1
What is the weight of an unknown hanging mass when the compressive force
strut BC is 615
Express your answer to three significant figures and include the appropriate units.
• View Available Hint(s)
HẢ
?
E
B
y
W =
Value
Units
a
Submit
arrow_forward
Help!!! Answer this correctly!! Please
arrow_forward
Just a small explanation only please and the correct answer thanks
arrow_forward
Question 2:
For part a), analyze the rectangular truss in Sl units. For part b), analyze the triangular truss in
FPS units.
10 kN
8 kN
4 kN
a) Use the method of joints to find the forces
in members AB, AC, and AF. State whether
each member is in tension (T) or
compression (C).
3 kN-
1.5 m
2 m
2 m
-9 ft-6 ft--6 ft--9 ft-
tontont
b) Using the method of sections, find the forces in
members DC, HI, and JI using the cuts s-s and t-t.
State whether each is in tension (T) or
compression (C).
6 ft
1200 lb
1600 lb
6 ft
12 ft
A
B
|- 6 ft-+-6 ft --|
arrow_forward
Determine the force in members BG, BC, and HG of the truss and state if the members are in tension or compression.
arrow_forward
Q1. For a 2D truss with 10 nodes, what is the associated total number of Degrees of Freedom?
arrow_forward
1. True or False: If only two forces act on a body that is in equilibrium, then the two forces must be equal in magnitude, co-linear and opposite in sense. True or False? ______
2. True or False: Frictionless 2D Pins and 2D Hinges have reactions in both the x and y directions.
True or False? _________.
3. Under certain loading conditions, can a Truss ever include a two-force member that experiences zero force? Yes or No? _______
4. A force of 5.5 “kips” in the US Customary System is just an abbreviation for this number of US pounds. 5.5 kips = ________ pounds.
5. What are the two common numerical/analytical methods that we use for in Engineering Mechanics: Statics courses for analyzing trusses? The Methods are: _______ and ______.
6. True or false: It is generally safe to assume that the 2D reaction forces that occur at single-track rollers and/or rockers are reversible. In other words, a roller support such as this: can pull downward on a free body. True or False? ________.
arrow_forward
View Policies
Current Attempt in Progress
Determine the force in each member of the loaded truss. The force is positive if in tension, negative if in compression.
70°
35°
11°
W
Answers:
AB =
AC =
W
BC =
eTextbook and Media
Save for Later
Attempts: unlimited
Submit A
arrow_forward
Can someone please help me to solve this problem following all directions using the “method of joints” and drawing all needed diagrams highlighted in yellow and show neat hand written work with all formulas. PLEASE AND THANK YOU!!!!!!
arrow_forward
1)Calculate force in each member using method of joints.
2)Calculate force in each member using method of sections.
3)Summary of calculations for proposed truss design
arrow_forward
Which of the following most nearly gives the force in
member DE for the truss loaded as shown?
B
a) DE = 15,942.86 lb (T)
6200 lb
b) DE = 14,704.60 lb (C)
4 ft
D
DE = 17,672.72 lb (T)
13 ft
d)
DE = 2,524.67 lb (C)
A
e) DE = 9,300 lb (C)
9 ft-
9 ft
f)
None of the choices
arrow_forward
Calculate the forces in members FH, FI and GI using the method of sections.
arrow_forward
SEE MORE QUESTIONS
Recommended textbooks for you
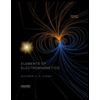
Elements Of Electromagnetics
Mechanical Engineering
ISBN:9780190698614
Author:Sadiku, Matthew N. O.
Publisher:Oxford University Press
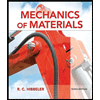
Mechanics of Materials (10th Edition)
Mechanical Engineering
ISBN:9780134319650
Author:Russell C. Hibbeler
Publisher:PEARSON
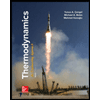
Thermodynamics: An Engineering Approach
Mechanical Engineering
ISBN:9781259822674
Author:Yunus A. Cengel Dr., Michael A. Boles
Publisher:McGraw-Hill Education
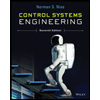
Control Systems Engineering
Mechanical Engineering
ISBN:9781118170519
Author:Norman S. Nise
Publisher:WILEY
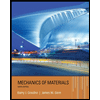
Mechanics of Materials (MindTap Course List)
Mechanical Engineering
ISBN:9781337093347
Author:Barry J. Goodno, James M. Gere
Publisher:Cengage Learning
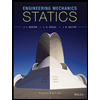
Engineering Mechanics: Statics
Mechanical Engineering
ISBN:9781118807330
Author:James L. Meriam, L. G. Kraige, J. N. Bolton
Publisher:WILEY
Related Questions
- Help!!! Please answer part B correctly!!! Pleasearrow_forwardPlease write clearly / legibly. Thanks!arrow_forwardPart 1: up a study about types of trusses and its importance and applications. Perform a design and structural analysis for the forces acting on the members of the truss shown in the figure below using the method of joints and the method of sections Make a critical comparison between the two methods Estimate the load in each member of the trusses shown in the figure below Show the detailed calculations and computation of the estimated load. Explain the impact of these calculations on the design of different constructions. Set Part 2 A Pratt roof truss is loaded as shown. Using the method of joints and the method of sections, determine the force in all members. for the force P =171 80 kN P kN 60 kN в 8 m 60 kN A G- MATHaling.com 6 m 600 C 6 m E 6 m 40 kN 100 kN 6 marrow_forward
- Help!!! Answer part B correctlyarrow_forwardLearning Goal: To apply the condition of equilibrium to three- dimensional systems and solve for unknown forces. Part A - Finding the tension in cable AC ▼ As shown, a mass is being lifted by a strut that is supported by two cables AC and CD. The dimensions given are a d = 3.70 ft, and e = 4.70 ft.(Figure 1) A weight of 125 lb acts at C on the strut. Find the magnitude of the tension in cable AC. = 7.30 ft, 6 = 4.70 ft, c = 8.10 ft, Express your answer to three significant figures and include the appropriate units. • View Available Hint(s) HẢ ? ТАС Value Units Submit Part B - Finding the unknown weight ▼ Figure 1 of 1 What is the weight of an unknown hanging mass when the compressive force strut BC is 615 Express your answer to three significant figures and include the appropriate units. • View Available Hint(s) HẢ ? E B y W = Value Units a Submitarrow_forwardHelp!!! Answer this correctly!! Pleasearrow_forward
- Just a small explanation only please and the correct answer thanksarrow_forwardQuestion 2: For part a), analyze the rectangular truss in Sl units. For part b), analyze the triangular truss in FPS units. 10 kN 8 kN 4 kN a) Use the method of joints to find the forces in members AB, AC, and AF. State whether each member is in tension (T) or compression (C). 3 kN- 1.5 m 2 m 2 m -9 ft-6 ft--6 ft--9 ft- tontont b) Using the method of sections, find the forces in members DC, HI, and JI using the cuts s-s and t-t. State whether each is in tension (T) or compression (C). 6 ft 1200 lb 1600 lb 6 ft 12 ft A B |- 6 ft-+-6 ft --|arrow_forwardDetermine the force in members BG, BC, and HG of the truss and state if the members are in tension or compression.arrow_forward
- Q1. For a 2D truss with 10 nodes, what is the associated total number of Degrees of Freedom?arrow_forward1. True or False: If only two forces act on a body that is in equilibrium, then the two forces must be equal in magnitude, co-linear and opposite in sense. True or False? ______ 2. True or False: Frictionless 2D Pins and 2D Hinges have reactions in both the x and y directions. True or False? _________. 3. Under certain loading conditions, can a Truss ever include a two-force member that experiences zero force? Yes or No? _______ 4. A force of 5.5 “kips” in the US Customary System is just an abbreviation for this number of US pounds. 5.5 kips = ________ pounds. 5. What are the two common numerical/analytical methods that we use for in Engineering Mechanics: Statics courses for analyzing trusses? The Methods are: _______ and ______. 6. True or false: It is generally safe to assume that the 2D reaction forces that occur at single-track rollers and/or rockers are reversible. In other words, a roller support such as this: can pull downward on a free body. True or False? ________.arrow_forwardView Policies Current Attempt in Progress Determine the force in each member of the loaded truss. The force is positive if in tension, negative if in compression. 70° 35° 11° W Answers: AB = AC = W BC = eTextbook and Media Save for Later Attempts: unlimited Submit Aarrow_forward
arrow_back_ios
SEE MORE QUESTIONS
arrow_forward_ios
Recommended textbooks for you
- Elements Of ElectromagneticsMechanical EngineeringISBN:9780190698614Author:Sadiku, Matthew N. O.Publisher:Oxford University PressMechanics of Materials (10th Edition)Mechanical EngineeringISBN:9780134319650Author:Russell C. HibbelerPublisher:PEARSONThermodynamics: An Engineering ApproachMechanical EngineeringISBN:9781259822674Author:Yunus A. Cengel Dr., Michael A. BolesPublisher:McGraw-Hill Education
- Control Systems EngineeringMechanical EngineeringISBN:9781118170519Author:Norman S. NisePublisher:WILEYMechanics of Materials (MindTap Course List)Mechanical EngineeringISBN:9781337093347Author:Barry J. Goodno, James M. GerePublisher:Cengage LearningEngineering Mechanics: StaticsMechanical EngineeringISBN:9781118807330Author:James L. Meriam, L. G. Kraige, J. N. BoltonPublisher:WILEY
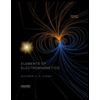
Elements Of Electromagnetics
Mechanical Engineering
ISBN:9780190698614
Author:Sadiku, Matthew N. O.
Publisher:Oxford University Press
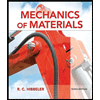
Mechanics of Materials (10th Edition)
Mechanical Engineering
ISBN:9780134319650
Author:Russell C. Hibbeler
Publisher:PEARSON
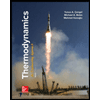
Thermodynamics: An Engineering Approach
Mechanical Engineering
ISBN:9781259822674
Author:Yunus A. Cengel Dr., Michael A. Boles
Publisher:McGraw-Hill Education
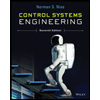
Control Systems Engineering
Mechanical Engineering
ISBN:9781118170519
Author:Norman S. Nise
Publisher:WILEY
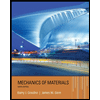
Mechanics of Materials (MindTap Course List)
Mechanical Engineering
ISBN:9781337093347
Author:Barry J. Goodno, James M. Gere
Publisher:Cengage Learning
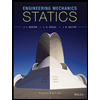
Engineering Mechanics: Statics
Mechanical Engineering
ISBN:9781118807330
Author:James L. Meriam, L. G. Kraige, J. N. Bolton
Publisher:WILEY