lab 10 report
pdf
keyboard_arrow_up
School
The City College of New York, CUNY *
*We aren’t endorsed by this school
Course
461
Subject
Mechanical Engineering
Date
Jan 9, 2024
Type
Pages
8
Uploaded by smuntah000
Objective
As in laboratory experiment #2 (Tensile test in metals) the objective of this
experiment is to study the effect of temperature and displacement rate on polymers when put
under tensile force. And compare results with those obtained in experiment #2.
Materials and equipment
•
Instron tensile testing machine.
•
Environmental chamber.
•
Test specimens:
-
Acrylic /PMMA (Poly (methyl methacrylate)) Nylon 6.6 (Polyamide) or PE
(Polyethylene)
-
Experimental Procedure
•
Take the initial measurements of the specimens (gage length, diameter). Record them
in table 2. Use a permanent marker to mark the middle 2-
inch span of the specimen’s
narrow section to specify where to mount the arms of the extensometer.
•
Input the data (material name, displacement rate, gage length, diameter, and geometry
of the specimen) of the test into Merlin software. Follow the tensile testing matrix shown
in Table1.
•
Mount the specimen into the threaded grips enclosed by the environmental chamber.
•
Keep the acrylic specimen at 60°C in the environmental chamber for 1 hour.
1
•
Remove the fractured test specimen from the grips and measure the final gage length
on the specimen. Also, measure the diameter of the specimen at the fracture (the neck).
•
Record the final measurements (gage length, diameter) in table 2.
•
Follow the same procedure described above for Nylon 6.6 (Polyamide) & PE
(Polyethylene) without using environmental chamber and utilize the extensometer.
Results
Table 1: Measurements for the specimens tested
Specimen
Young’s
Modulus/MPa
Yield
Strength/MPa
Yield
Strain
Ultimate
Tensile/MPa
PMMA (60
°C)
700.6
35.09
0.05
52.73
PMMA (low
rate)
2236.9
43.01
0.03
79.82
PMMA
(high rate)
2380.6
57.03
0.03
73.02
PE (low
rate)
810.82
12.48
0.05
17.67
PE (high
rate)
1143
22.10
0.05
27.58
Nylon (low
rate)
2976.1
16.16
0.05
22.51
2
Nylon (high
rate)
3247.5
69.99
0.05
78.98
Table 2: A comparison of the mechanical properties of the specimens. The values are obtained from
MIcrosoft Excel
Specimen
Failure
Tensile
Stress
Failure
Tensile
Strain
Elongation
(%)
Area
Reduction
(%)
Poisson’s
Ratio
PMMA
(60°C)
43.69
0.63
53.57
61.32
0.71
PMMA (low
rate)
79.78
0.08
1.72
0.44
0.13
PMMA (high
rate)
73.01
0.05
1.67
0.44
0.13
PE (low rate)
17.56
1.78
46.03
73.4
1.19
PE (high
rate)
14.01
2.15
86.15
70.65
0.74
Nylon (low
rate)
19.31
0.33
33.85
79.58
1.43
Nylon (high
rate)
28.11
0.68
31.75
87.06
1.44
Table 3: A comparison of the mechanical properties of the specimens. The values are obtained from
MIcrosoft Excel
Following are the engineering stress vs engineering strain graphs for all the specimens tested
Your preview ends here
Eager to read complete document? Join bartleby learn and gain access to the full version
- Access to all documents
- Unlimited textbook solutions
- 24/7 expert homework help
3
Discussion
The data obtained at room temperature for Acrylic in low displacement and plexiglass in high displacement
is incoherent because we did not have enough data points to work with, which lead to inadequate leading
curves. Based on the plots, we see that acrylic at room temperature in low displacement has the second
highest yield strength and ultimate strength. The difference between low and high displacement rate is the
change in strain. Nylon at room temperature has less yield strength in low displacement rate compared to
4
the high displacement rate. The plots of Nylon in low & high displacement rate are similar but after 1-strain
units, the graph of the high rate decreases and has a greater ultimate strength than the low rate. Nevertheless,
the Stress vs. Strain curve for plexiglass demonstrates that strain is more apparent at room temperature than
in high displacement rate at 60 °C. The yield strength is also greater at room temperature than at 60°C.
Since there is more deformation going on in the higher temperature, the failure occurs faster (at low strain)
at room temperature than at 60°C.
Review Questions
1.
Determine the yield, maximum, and failure values of load and displacement from the load
displacement data provided by the machine.
-
Refer to the “Results” section
2.
Plots of Engineering Stress vs Strain are required for each specimen. Overplot stress strain
data of the tested specimens in a figure.
-
Refer to the “Results” section.
3.
Determine the mechanical properties of each tested specimen (Young’s Modulus, yield
stress, yield strain, Poisson’s ratio, failure stress, failure strain, ductility (%EL)), and show
your calculations explicitly. Compare your calculations with the literature and compute the
percentage error.
-
Refer to the “Results” section.
4.
Did fracture occur at the neck for the nylon or PE?
-
The Facture did not take place at the necking of Nylon at low displacement rate and PE
in both cases
–
the specimens were only stretched and elongated.
5.
After necking of the nylon or PE specimen, did further deformation occur at the neck area?
5
-
After necking further deformation took place at the neck area, it can only be drawn a
similarity with PMMA at high temperature.
6.
Were similar phenomena observed when testing the PMMA specimen?
-
PMMA specimens tested at room temperature have a brittle mode of failure while
PMMA at high temperature the largest plastic deformation. The strain of PMMA at
high temperature showed the largest ductility compared to the other PMMA specimens.
7.
Are the modes of failure of the PMMA and nylon or PE specimens similar? Why?
-
The failure modes of PMMA and nylon are similar because high strain rate leads to
greater yield strength and ultimate strength but decreases ductility.
8.
What are the effects of high strain rate on the failure mode and on the mechanical properties
of each of the PMMA and nylon or PE specimen? Did you observe a similar phenomenon
for metals you tested at lab 2?
-
In the nylon material, greater strain rate causes the plastic deformation rate to increase.
The mode of failure was around the same for acrylic at high strain rate.
9.
Does the failure mode of polymers differ from that of metals? Explain in detail.
-
Failure more in polymers are different from metals as they have weak intermolecular
interactions. The reversible deformation in the material causes the modulus of elasticity
to be less. Nonetheless, polymers experience additional strain in the elastic region than
metals.
10.
What is the elastic deformation mechanism for nylon or PE? Is it different from that of
metals? In what way?
-
Nylon has more reversible deformation and can experience more strain than metals
because the material has more necking and went through crazing.
Your preview ends here
Eager to read complete document? Join bartleby learn and gain access to the full version
- Access to all documents
- Unlimited textbook solutions
- 24/7 expert homework help
6
11.
What is the plastic deformation mechanism for nylon? How does it affect the shape of the
engineering stress-strain curve?
-
In Nylon, the necking spreads which causes a lot of crazing. The strain is also increased
in the plastic region of the stress-strain curve.
12.
Discuss how the microstructures of polymers and metals make their behavior under
mechanical loading different.
-
Metals do not go through crazing because their microstructure is not composed of
chains that can be straightened into units. The microstructure of metals is not very
ductile compared to polymers. This is because the interior of metals is constructed of
crystal material. However, polymers contain lower tensile strength.
13.
What is the temperature effect on stress-strain curves on PMMA? Do you expect to have
similar effects on aluminum or steel you tested at lab 2?
-
The stress-strain curve for PMMA is greatly impacted by temperature. According to
the plots, strain varies with temperature.
14.
What effect does temperature have on the rupture stress?
-
Higher temperatures decrease rupture stress.
15.
What effect does temperature have on the rupture strain?
-
Higher temperatures increase the rupture strain.
Conclusions
7
The experiment allowed us to analyze and compare the properties of different polymers
under tensile loading at different displacement rates and temperatures. A further goal achieved was
to compare the results with those of metals. It was observed that displacement rate and
temperatures affect Young’s modulus, yield strength and strain, as well as modes of failure of the
materials tested.
References
Callister, William D. Rethwisch, David G. “Materials Science & Engineering”. 2010 edition.
Li, J.
Lab Manuals
. CUNY Blackboard Website.
Related Documents
Related Questions
A polymer has creep behaviour that can be represented as a power law equation:
e = 0 (Jo + Jit")
where J, is 0.5 GPa1, J1 is 0.45 GPa's 0.3 and n is 0.3 (with t in seconds).
A component of this material has the following applied stress history:
There is no stress before t = 0
A positive (tensile) stress of 8 MPa is applied from t = 0 for 4 hours
From t = 4 hours to 6 hours, the stress is compressive stress of 2 MPa
The stress is then removed.
What will the strain in the material be at t = 9 hours?
Enter your value as a number to 4 decimal places. You have a 2% error margin with this.
arrow_forward
An unknown polymer sample was found to have the following molecular weight distribution:
Molecular weight range
8,000 - 20,000
20,000 - 32,000
32,000 - 44,000
44,000 - 56,000
56,000 -68,000
68,000 -80,000
80,000 - 92,000
Having a DP=763, which of the following common polymers is this sample?
Xi
0.05
0.15
0.21
0.28
0.18
0.10
0.03
Wi
0.02
0.08
0.17
0.29
0.23
0.16
0.05
Select one:
O a. Polymethylmethacrylate with a monomer molecular weight of 100.121 g/mol
O b.
Polystyrene with a monomer molecular weight of 104.15 g/mol
Polycarbonate with a monomer molecular weight of 61.0168 g/mol
O c.
O d.
Polyvinyl chloride with a monomer molecular weight of 62.498 g/mol
Polypropylene with a monomer molecular weight of 42.08 g/mol
O e.
arrow_forward
At room temperature, most polymers have
similar fracture toughness compared to metals.
O True
False
arrow_forward
Which of the statements below are accurate regarding the stress-strain behavior of polymers:
(This question has more than one correct answer)
а.
Strain softening happens in elastomers where the deformation gradually leads to a decrease in stress under constant strain
rate
b.
As temperature is reduced, the necking behavior of plastic tensile bars completely disappears
C- The slope of the stress-strain curve for totally elastic and brittle polymers is always positive
d.
The stress-strain curve for vulcanized elastomers has a greater slope than unvulcanized polymers throughout
arrow_forward
Thermoplastics are stronger than thermoset plastics.
True
False
Yield strength, ultimate tensile strength, linear coefficient of thermal expansion, modulus of elasticity (E), proportional limit, and rupture strength are all examples of mechanical properties of engineering materials.
True
False
arrow_forward
An unknown polymer sample was found to have the following molecular weight distribution:
Molecular weight range
xi
8,000 -20,000
0.05
20,000 - 32,000
0.15
32,000 44,000
0.21
44,000 56,000
0.28
56,000 -68,000
0.18
68,000 - 80,000
0.10
80,000 - 92,000
0.03
Having a DP=763, which of the following common polymers is this sample?
Select one:
wi
0.02
0.08
0.17
0.29
0.23
0.16
0.05
a. Polymethylmethacrylate with a monomer molecular weight of 100.121 g/mol
b. Polyvinyl chloride with a monomer molecular weight of 62.498 g/mol
c. Polycarbonate with a monomer molecular weight of 61.0168 g/mol
d. Polypropylene with a monomer molecular weight of 42.08 g/mol
e. Polystyrene with a monomer molecular weight of 104.15 g/mol
arrow_forward
The graph below gives a plot of force versus total sample length in a tensile test of a polymer. The sample is cylindrical, with an initial diameter of 1 cm and an initial length of 10 cm. From the data below, calculate the modulus, yield stress, yield strain, tensile strength, and % elongation.
arrow_forward
There are 4 classifications of structural molecular characteristics of polymers - Linear, Network, Crosslinked. What is the
final type?
Answer:
arrow_forward
Draw stress-strain graphs for two polymers: one is stiffer than the other and exhibits ayield point and the other shows no clear yield point but is much tougher.
arrow_forward
Compression molding is a manufacturing process in which the molding material is preheated then placed in an open mold cavity where the
compressive action of the punch forces the polymer into the desired shape as shown in the figure below. Based on your understanding of the
behavior of polymers, which of the statements below regarding compression molding of polymers are accurate?
Punch
Cavity
C.
-Upper mold half
Charge
41
(1)
-Lower mold half
Knock-out pin
V, F
|x.F
(2) and (3)
Molded part
a. Lower operating temperatures are more desirable as they reduce viscosity making it easier to fill the cavity
b. This process can only be used for thermosets as they can thermally cure from monomer state
This process can be used for both thermosets and thermoplastics as they can both be thermally shaped
d. This process is suitable for rubber, PVC and polymethyl methacrylate
arrow_forward
An unknown polymer sample was found to have the following molecular weight distribution:
Molecular weight range
Wi
8,000 - 20,000
0.05
0.02
20,000 – 32,000
0.15
0.08
32,000 - 44,000
0.21
0.17
44,000 – 56,000
0.28
0.29
56,000 - 68,000
0.18
0.23
68,000 - 80,000
0.10
0.16
80,000 - 92,000
0.03
0.05
Which of the following common polymers is this sample?
(This question has only one correct answer)
arrow_forward
For an application of high strength components including gears cams and rollers the desired properties in a plastic would be high tensile and impact strength, stability at high temperature, and machine ability. Potential materials which are suitable for these applications are nylon phenolics, TFE filled acetals, PET, and poly carbonate. True or false.
arrow_forward
An unknown polymer sample was found to have the following molecular weight distribution:
Molecular weight range
8,000 - 20,000
20,000 - 32,000
32,000 - 44,000
44,000 - 56,000
56,000 - 68,000
68,000 -80,000
80,000 - 92,000
0.03
Knowing that the monomer is methyl methacrylate, which of the below is the number average degree of polymerization for this polymer sample?
Select one:
O a.
O b. DP 476
O C.
DP = 338
DP = 664
O d. DP 544
O e. DP = 801
Xi
0.05
0.15
0.21
0.28
0.18
0.10
Wi
0.02
0.08
0.17
0.29
0.23
0.16
0.05
arrow_forward
Which statements are correct regarding the mechanical properties of polymers?
a.
Drawing increases alignment and strength, and decreases ductility (% elongation)
b.
Annealing increases alignment, strength and elastic modulus
c.
Increasing temperature results in increased elastic modulus and strength, and decreased elongation
d.
Decreasing strain rate causes decreased strength and elastic modulus and increased elongation
e.
A higher degree of crosslinking generally results in decreased percent elongation at break, and increases strength
arrow_forward
When a viscoelastic material is loaded and unloaded, the unloading curve is different to the loading curve, i.e. it takes more energy to displace
the material than it does to return the material to its original configuration. This is known as:
Select one:
O a. creep
O b. stress relaxation
O c. hysteresis
d. strain-rate dependance
arrow_forward
A continuous and aligned fiber-reinforced composite is to be produced consisting of 30%
vol aramid fibers and 70% vol of a polycarbonate matrix. Mechanical characteristics from
the test are given below. The composite is characterized by mechanical testing in both
longitudinal and transverse loading. Calculate the longitudinal and transverse elastic
modulus.
30% vol aramid fibers (Modulus of Elasticity - 121.68 GPa)
70% vol of a polycarbonate matrix (Modulus of Elasticity - 3.42 GPa)
arrow_forward
An unknown polymer sample was found to have the following molecular weight distribution:
Molecular weight range
Xi
Wi
8,000 – 20,000
0.05
0.02
20,000 – 32,000
0.15
0.08
32,000 – 44,000
0.21
0.17
44,000 – 56,000
0.28
0.29
56,000 – 68,000
0.18
0.23
68,000 – 80,000
0.10
0.16
80,000 - 92,000
0.03
0.05
What would the weight average molecular weight of the sample be if, we had filtered the monomer mixture with a 44 kDa dialysis
tubing before preparation? (Hint: a dialysis tubing of a known molecular weight, only keeps molecules larger than that size)
arrow_forward
Kindly solve it completely by hand if possible.
arrow_forward
Molecular weight data for some polymer are tabulated here. Compute (a) the number-average
molecular weight, (b) the weight-average molecular weight. (c) If it is known that this material's degree of
polymerization is 710, which one of the polymers listed in Table 14.3 is this polymer? Why?
Molecular Weight
Range g/mol
15,000-30,000
Xi
Wi
0.04
0.01
30,000-45,000
0.07
0.04
45,000-60,000
0.16
0.11
60,000-75,000
0.26
0.24
75,000-90,000
0.24
0.27
90,000 105,000
0.12
0.16
105,000-120,000
0.08
0.12
120,000-135,000
0.03
0.05
arrow_forward
SEE MORE QUESTIONS
Recommended textbooks for you
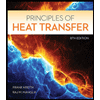
Principles of Heat Transfer (Activate Learning wi...
Mechanical Engineering
ISBN:9781305387102
Author:Kreith, Frank; Manglik, Raj M.
Publisher:Cengage Learning
Related Questions
- A polymer has creep behaviour that can be represented as a power law equation: e = 0 (Jo + Jit") where J, is 0.5 GPa1, J1 is 0.45 GPa's 0.3 and n is 0.3 (with t in seconds). A component of this material has the following applied stress history: There is no stress before t = 0 A positive (tensile) stress of 8 MPa is applied from t = 0 for 4 hours From t = 4 hours to 6 hours, the stress is compressive stress of 2 MPa The stress is then removed. What will the strain in the material be at t = 9 hours? Enter your value as a number to 4 decimal places. You have a 2% error margin with this.arrow_forwardAn unknown polymer sample was found to have the following molecular weight distribution: Molecular weight range 8,000 - 20,000 20,000 - 32,000 32,000 - 44,000 44,000 - 56,000 56,000 -68,000 68,000 -80,000 80,000 - 92,000 Having a DP=763, which of the following common polymers is this sample? Xi 0.05 0.15 0.21 0.28 0.18 0.10 0.03 Wi 0.02 0.08 0.17 0.29 0.23 0.16 0.05 Select one: O a. Polymethylmethacrylate with a monomer molecular weight of 100.121 g/mol O b. Polystyrene with a monomer molecular weight of 104.15 g/mol Polycarbonate with a monomer molecular weight of 61.0168 g/mol O c. O d. Polyvinyl chloride with a monomer molecular weight of 62.498 g/mol Polypropylene with a monomer molecular weight of 42.08 g/mol O e.arrow_forwardAt room temperature, most polymers have similar fracture toughness compared to metals. O True Falsearrow_forward
- Which of the statements below are accurate regarding the stress-strain behavior of polymers: (This question has more than one correct answer) а. Strain softening happens in elastomers where the deformation gradually leads to a decrease in stress under constant strain rate b. As temperature is reduced, the necking behavior of plastic tensile bars completely disappears C- The slope of the stress-strain curve for totally elastic and brittle polymers is always positive d. The stress-strain curve for vulcanized elastomers has a greater slope than unvulcanized polymers throughoutarrow_forwardThermoplastics are stronger than thermoset plastics. True False Yield strength, ultimate tensile strength, linear coefficient of thermal expansion, modulus of elasticity (E), proportional limit, and rupture strength are all examples of mechanical properties of engineering materials. True Falsearrow_forwardAn unknown polymer sample was found to have the following molecular weight distribution: Molecular weight range xi 8,000 -20,000 0.05 20,000 - 32,000 0.15 32,000 44,000 0.21 44,000 56,000 0.28 56,000 -68,000 0.18 68,000 - 80,000 0.10 80,000 - 92,000 0.03 Having a DP=763, which of the following common polymers is this sample? Select one: wi 0.02 0.08 0.17 0.29 0.23 0.16 0.05 a. Polymethylmethacrylate with a monomer molecular weight of 100.121 g/mol b. Polyvinyl chloride with a monomer molecular weight of 62.498 g/mol c. Polycarbonate with a monomer molecular weight of 61.0168 g/mol d. Polypropylene with a monomer molecular weight of 42.08 g/mol e. Polystyrene with a monomer molecular weight of 104.15 g/molarrow_forward
- The graph below gives a plot of force versus total sample length in a tensile test of a polymer. The sample is cylindrical, with an initial diameter of 1 cm and an initial length of 10 cm. From the data below, calculate the modulus, yield stress, yield strain, tensile strength, and % elongation.arrow_forwardThere are 4 classifications of structural molecular characteristics of polymers - Linear, Network, Crosslinked. What is the final type? Answer:arrow_forwardDraw stress-strain graphs for two polymers: one is stiffer than the other and exhibits ayield point and the other shows no clear yield point but is much tougher.arrow_forward
- Compression molding is a manufacturing process in which the molding material is preheated then placed in an open mold cavity where the compressive action of the punch forces the polymer into the desired shape as shown in the figure below. Based on your understanding of the behavior of polymers, which of the statements below regarding compression molding of polymers are accurate? Punch Cavity C. -Upper mold half Charge 41 (1) -Lower mold half Knock-out pin V, F |x.F (2) and (3) Molded part a. Lower operating temperatures are more desirable as they reduce viscosity making it easier to fill the cavity b. This process can only be used for thermosets as they can thermally cure from monomer state This process can be used for both thermosets and thermoplastics as they can both be thermally shaped d. This process is suitable for rubber, PVC and polymethyl methacrylatearrow_forwardAn unknown polymer sample was found to have the following molecular weight distribution: Molecular weight range Wi 8,000 - 20,000 0.05 0.02 20,000 – 32,000 0.15 0.08 32,000 - 44,000 0.21 0.17 44,000 – 56,000 0.28 0.29 56,000 - 68,000 0.18 0.23 68,000 - 80,000 0.10 0.16 80,000 - 92,000 0.03 0.05 Which of the following common polymers is this sample? (This question has only one correct answer)arrow_forwardFor an application of high strength components including gears cams and rollers the desired properties in a plastic would be high tensile and impact strength, stability at high temperature, and machine ability. Potential materials which are suitable for these applications are nylon phenolics, TFE filled acetals, PET, and poly carbonate. True or false.arrow_forward
arrow_back_ios
SEE MORE QUESTIONS
arrow_forward_ios
Recommended textbooks for you
- Principles of Heat Transfer (Activate Learning wi...Mechanical EngineeringISBN:9781305387102Author:Kreith, Frank; Manglik, Raj M.Publisher:Cengage Learning
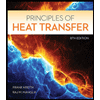
Principles of Heat Transfer (Activate Learning wi...
Mechanical Engineering
ISBN:9781305387102
Author:Kreith, Frank; Manglik, Raj M.
Publisher:Cengage Learning