lab 2 report
pdf
keyboard_arrow_up
School
The City College of New York, CUNY *
*We aren’t endorsed by this school
Course
461
Subject
Mechanical Engineering
Date
Jan 9, 2024
Type
Pages
12
Uploaded by smuntah000
Objective
The experiment's main purpose was to determine the maximum load the material withstands before
breaking. Also, we determined the force-elongation of the materials after necking. This experiment
helped us determine several mechanical properties such as Youn
g’s Modulus, Poisson’s ratio,
yield strength, ultimate tensile strength, failure tensile strain, etc. All these mechanical properties
can be obtained by the graphs plotted in excel with the results from the ‘BlueHill’ software used
during the Tensile testing. The stress-strain curves were obtained for different types of Steel,
Aluminum, and Iron. These materials were tested under different loads to experience real-life
necking and deformation and eventually breaking. Different materials react differently to similar
loads which signify the different properties of each material consists of.
Equipment
•
An instron testing machine connected to a desktop with ‘Bluehill’ software
•
Extensometer
•
Caliper, micrometer, and a ruler
Experimental Procedures
Three materials were used in the experiment; Al 2024, HR steel, and Cast Iron, while Al 2024 and
HR steel had two specimens each as they were tested at two different speeds of 5mm/min and
50mm/min. The specimens were measured before and after the tensile loading to determine the
deformation. The length was measured by a ruler and the diameter was measured by a caliper.
Then, the specifications of each specimen such as the material type, displacement rate, length, and
1
diameter were input into the ‘Bluehill software on the desktop. The extensometer was mounted in
the middle of the specimen to determine the extension of the material and to measure the strain.
Then, the fractured specimen was removed, and the length and diameter were measured after the
tensile loading. The extensometer was only used for the displacement of 5mm/min as 50mm/min
is very fast. ‘Table 1’ below represents the materials used, along with the displacement rates and
the extensometer specifications.
Table 1: Testing matrix
Results
Specimen
Displacement
rate
(mm/min)
Initial
gage
length
(mm)
Final
gage
length
(mm)
Initial
diameter
(mm)
Final
diameter
(fracture)
(mm)
Final
diameter
(unbroken)
(mm)
HR Steel
5
103
124
8.52
7.05
7.91
Aluminum
6061
5
102
115
8.45
7.25
8.25
Cast Iron
-
101
101
8.53
8.53
-
Table 2: Measurements of specimen parameters at a displacement rate of 5 mm/min
2
Specimen
Displacement
rate
(mm/min)
Initial
gage
length
(mm)
Final
gage
length
(mm)
Initial
diameter
(mm)
Final
diameter
(fracture)
(mm)
Final
diameter
(unbroken)
(mm)
HR Steel
50
102
123
8.54
7.17
7.98
Aluminum
6061
50
103
114
8.52
7.85
8.19
Cast Iron
-
-
-
-
-
-
Table 3: Measurements of specimen parameters at a displacement rate of 50 mm/min
The parameters of the graphs were calculated using the following formulas.
Engineering Stress:
Engineering Strain:
True Stress:
True Strain:
Here,
F: Load Applied
A
0:
Cross-sectional area of specimen before deformation has taken place
A:
Cross-sectional area of specimen at which the load is applied
𝛿:
Total elongation
L
0:
Original value of the gage length
L:
Successive values of the length as it changes
Your preview ends here
Eager to read complete document? Join bartleby learn and gain access to the full version
- Access to all documents
- Unlimited textbook solutions
- 24/7 expert homework help
3
Figure 1: Engineering stress vs. Engineering strain graphs for the three specimens at low displacement
rate
Figure 2: True stress vs. True strain graphs for the three specimens at low displacement rate
4
Figure 3: Engineering stress vs. Engineering strain graphs for the Aluminum and HR Steel specimens at
high displacement rate
Figure 4: True stress vs. True strain graphs for aluminum and HR steel at low displacement rate
5
Figure 5: Load-extension graph to calculate total energy for aluminum
Figure 6: Load-extension graph to calculate total energy for HR steel
Your preview ends here
Eager to read complete document? Join bartleby learn and gain access to the full version
- Access to all documents
- Unlimited textbook solutions
- 24/7 expert homework help
6
Figure 7: Load-extension graph to calculate total energy for cast iron
Note: The areas under the load-extension curves are a measure of the Reiman sum of the individual
areas of rectangles formed by consecutive load and extension values. The rule used was the
Trapezoid rule.
Specimen
Ultimate
Tensile
Stress (Mpa)
Young’s
Modulus, E
Failure
Tensile
Stress (MPa)
Aluminum
346.4041
19068
273.48
HR Steel
600.9009
18934
422.42
Cast Iron
280.8143
22089
280.02
Table 4: Comparison of specimen properties at low displacement rate
7
Specimen
Ultimate Tensile
Stress (MPa)
Young’s Modulus, E
Failure Tensile
Stress (MPa)
Aluminum
309.08
19639
245.23
HR Steel
452.54
19333
368.47
Table 5: Comparison of specimen properties at high displacement rate
Discussions
The elongation of steel is the highest, while the lowest is cast iron which means that steel is the
most ductile among all the specimens. Elongation helps us choose the material type according to
the project. The gradient of the elastic region
provides Young’s Modulus which affects the
deflection of material under different loads. Necking is more in steel than aluminum, while cast
iron has no necking. Hence, steel has higher yield strength than aluminum. True strains are of
higher values than engineering strains as true strains take place in transverse directions of the gage
length.
It can be noticed that steel requires the most stress and strain before fracture which proves that
steel withstands the highest load before breaking and is the strongest of the specimens. This means
that more energy is required to break steel than aluminum and cast iron. The engineering stress-
strain curve shows the deformation specifications of the specimen, while the true stress-strain
curve shows the true values of the changing deformation. HR steel has a lower and upper yield
point as its local transitions from elastic to plastic behavior while aluminum has a gradual
transition. The specimen’s fractures other than cast iron were at an angle of approximately 45
degrees like a cup cone as the specimens experienced rupture while breaking. Furthermore, to
reduce error, I think it would be more accurate to obtain the stress-strain data by the machine
directly.
Conclusion
8
This tensile testing helped us know about different material properties using the tensile testing
machine. The ductile fracture can be proved when our results show that the area of the specimen
is reduced at the breaking point. Elastic and plastic deformation can be seen when the material is
stretched in the machine. This experiment helped me with a better understanding of how materials
react under different conditions such as speed and load.
Review Questions
1.
What divides the engineering stress-strain curve into two regions, namely, the elastic and
plastic regions?
-
The Yield strength or yield point
2.
What is the difference between the behavior of the material in the elastic and plastic regions
of the engineering stress-strain curve?
-
Under elastic region, the material regains its original form after the load is removed.
In plastic region, deformation becomes permanent.
3.
What measurement should you have taken in order to be able to plot the true stress-true
strain curve?
-
Load and the corresponding deformation parameters.
4.
Why does low carbon steel have clear upper and lower yield points? Why doesn't the
aluminum have the same? Explain the differences using your knowledge of the alloying
and dislocation theories.
-
The reason is the presence of interstitial atoms. The dislocations are due to plastic
deformation in carbon. The same is not true for aluminum since steel has a higher
modulus of rigidity than aluminum.
Your preview ends here
Eager to read complete document? Join bartleby learn and gain access to the full version
- Access to all documents
- Unlimited textbook solutions
- 24/7 expert homework help
9
5.
Did you observe parallel lines inclined about 45
o
with the horizontal on the surface of the
steel specimen, and in the area where necking later took place? What are those lines called?
What do they reveal about the mechanism of deformation? Apply Schmid
’
s Law, see S
LIP
IN
S
INGLE
C
RYSTALS
(Sec 7.5) of Ch 7:
Dislocation and Strengthening Mechanisms
.
-
The lines are called dislocation lines. The angle of 45 degrees implies maximum
shear stress has reached.
6.
Could you observe any similar lines on the aluminum specimen? What is the mechanism
of deformation in this latter case?
-
Yes, the lines were visible in aluminum as well and the mechanism of deformation
is the same.
7.
Obtain the area under the load-extension curve (i.e., energy) for each specimen and divide
it by the volume between the gage length in order to obtain the modulus of toughness.
Compare the value of plain carbon steel and that of aluminum. Can you draw any
conclusion?
-
Refer to the results section. It can be concluded that the amount of energy associated
with each specimen revolves around the same value.
8.
Looking at the curve indicating the distribution of elongation along the gage length, where
did the maximum localized elongation take place?
-
In the middle of the specimen where necking occurred.
9.
How do you interpret the shape of the above-mentioned curve?
- High strain rate breaks the specimen faster.
10.
What effect does the high strain rate have on the mechanical properties mentioned in
Problem 8?
10
- High strain rate breaks the specimen faster.
10.
Did the high strain rate have any effect on the mode of failure of any of the specimens?
Why?
- High strain rate caused faster elongation and, hence, failure.
12
. What effect does the high strain rate have on the mechanical properties mentioned below?
-
High strain rate, increases the Young’s modulus and
failure strength of the specimens.
13.
Design for Experiments
: Rather than using the extensometer/change in gage length and
change in diameter, the axial and lateral strains of the test can also be measured directly using
a “T” strain rosette shown at
right. If the strain-rosette mounted tensile test needs to be
conducted under water, what additional step(s), if any, should be taken to ensure the success
of the test.
Hint
:
Refer
to
the
Vishay
Precision
Group,
Micro-Measurements
website:
http://www.vishaypg.com/micro-measurements/
.
-
For under-water testing, ultra-thins films and van-der walls adhesion will be needed.
11
References
Li, J.
Lab Manuals
. CUNY Blackboard Website
“Engineering
Stress/Strain
VS
True
Stress/Strain.”
Yasin
APAR
,
https://yasincapar.com/engineering-stress-strain-vs-true-stress-
strain/#:~:text=Engineering%20strain%20is%20the%20amount,length%20over%20the%2
0original%20length
Erhart, Angela. “Engineering Stress
-Strain vs. True Stress-
Strain.”
AHSS Guidelines
, 24 Mar.
2021,
https://ahssinsights.org/forming/formability/engineering-stress-strain-true-stress-
strain/
Your preview ends here
Eager to read complete document? Join bartleby learn and gain access to the full version
- Access to all documents
- Unlimited textbook solutions
- 24/7 expert homework help
Related Documents
Related Questions
In your summer internship, you are tasked with measuring the ultimate tensile strength of a material to determine if it meets your company’s (Superior Super Ships Inc) specification. Your boss is worried that the new low-cost supplier, Shoddy Alloys Inc, may not be reliable but it is the only way to source on-time the SS304 needed to make finishings for Jeff Bezos’ new yacht, the Black Pearl. You collect several load versus displacement curves, as illustrated below. The initial diameter of the round gauge section is 0.25 in.
You also collect the instantaneous diameter of the specimen during the test using a laser.
Using the provided data, calculate what is the ultimate tensile strength measured in this test?
arrow_forward
1. A tensile test was conducted on a metal "505" specimen and the following stress-strain curves
were generated, both curves generated from the same set of data. Use the graphs to fill in the
mechanical properties of the material tested in the box below. Don't forget units!
Stress vs Strain
Stress, psi
Stress, psi
80000
70000
60000
50000
40000
30000
20000
10000
0
0.00
80000
70000
60000
50000
40000
30000
20000
10000
0.02
0
0.000 0.002
0.04
0.004
0.06
0.006
0.08
0.10
Strain
Stress vs Strain
0.008
0.12
Elastic Modulus, E:
0.2% Offset Yield Strength, oo:
Tensile Strength, ou:
Breaking Strength, of:
% Elongation:
0.14
0.010 0.012 0.014
Strain
0.16
0.18
0.016 0.018
0.20
0.020
arrow_forward
Please can you plot the Mohr's strain circle using the above inform
arrow_forward
Calculate the young’s modulus from one of these two graphs?
arrow_forward
Consider the graph below for 3 test samples A, B and C of the same metal
composition which have been cold-worked, but to different extents. If you had to
sort the samples by the degree of cold-working they have undergone, how would
you rank them?
Stress (MPa)
600
500
4006
300
200
100
0
A
B
0.05
1
0.1
0.15
Strain
Select the correct answer:
a. A
arrow_forward
You are a comparative evolutionary biologist that studies biomechanics. In particular, you are interested in how bone cross sectional shapes have evolved. You have discovered a rare (hypothetical) animal that has bone shapes similar to ours, but has solid, rectangular cross sectional areas. You conduct mechanical testing according to the parameters below and want to determine the:
(A) moment of inertia;
(B) reaction forces and moments at the fixed end O;
(C) the stresses at points A, B, and C designated below, including the contributions of the different types of stresses at each point
arrow_forward
The graph below shows the yield stress for a polycrystalline metal as a function of the grain size of the metal. The point A is (10 microns, 100 MPa) and B is
(1000 microns, 28 MPa). Using this data, calculate what is the closest numerical match to the yield stress at 2 microns.
yield stress (MPa)
8 8 8 8 8 8 8
80
70
50
40
30
A
200
Select one:
O a. 198.9 MPa
O b. 310.9 MPa
O C.
O d. 80.5 MPa
252.6 MPa
O e. 165.2 MPa
400
600
grain size d (microns)
800
B
●
1000
arrow_forward
UzNDU3NTYyMjk0/a/MjYOMzAwMjMOOTM5/details
Further questions
4.The graphs show how the extension changes with stretching force for four different materials.
a. Which two graphs show materials that follow Hooke's law?
A
B
b. Which two graphs show materials that become less stiff as
they are stretched?
force
force
D
C. Which graph shows a material that maintains the same
stiffness throughout?
force
force
1. A force of 20N stretches a spring by 0.5m. The spring obeys Hooke's law.
a. Calculate the spring constant including a suitable unit.
b. How much force must a man use to stretch it by 1.5m?
5. A car has a weight of 240OON which is distributed equally over all four wheels. Each wheel has a spring of
spring constant 400N/cm.
a.
Determine the force through the spring on each wheel.
b. Calculate the compression of each spring when the car rests on the ground.
6.In a spring experiment the results were as follows:
Force (N)
Length (mpm
1
2
4
6.
7
50
58
70
74
82
9n
102
125
LELL
arrow_forward
The graph below gives a plot of force versus total sample length in a tensile test of a polymer. The sample is cylindrical, with an initial diameter of 1 cm and an initial length of 10 cm. From the data below, calculate the modulus, yield stress, yield strain, tensile strength, and % elongation.
arrow_forward
No wrong answer please , i could downvote
The piece of suture is tested for its stress relaxation properties after cutting 3 cm long sample with a diameter of 1mm. The initial force recorded after stretching 0.1 cm between grips was 5 Newtons. Assume the suture material behave as if it has one relaxation time. The gage length was 1 cm.
a. Calculate the initial stress.
b. Calculate the initial strain.
c. Calculate the modulus of elasticity of the suture if the initial stretching can be considered as linear and elastic.
d. Calculate the relaxation time if the force recorded after 10 hours is 4 Newtons.
arrow_forward
please solve part b, this is past paper and just iam studying, mechanical engineering
arrow_forward
6. State your answers to the following questions.Strain Gauge represents the deformation of a material through a change in resistance. If so, explain how temperature will affect the strain gauge in the experimental environment.①:In this experiment, the Strain Gauge measures the strain in micro units. Explain one possible error factor when applying a load by hanging a weight on the material with the strain gauge attached. (Hint: It is easy to shake by hanging the weight using a thread)①:
arrow_forward
i need the answer quickly
arrow_forward
Calculate the young’s modulus from one of these two graphs?
arrow_forward
SEE MORE QUESTIONS
Recommended textbooks for you
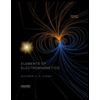
Elements Of Electromagnetics
Mechanical Engineering
ISBN:9780190698614
Author:Sadiku, Matthew N. O.
Publisher:Oxford University Press
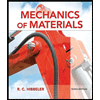
Mechanics of Materials (10th Edition)
Mechanical Engineering
ISBN:9780134319650
Author:Russell C. Hibbeler
Publisher:PEARSON
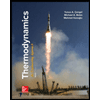
Thermodynamics: An Engineering Approach
Mechanical Engineering
ISBN:9781259822674
Author:Yunus A. Cengel Dr., Michael A. Boles
Publisher:McGraw-Hill Education
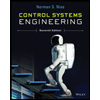
Control Systems Engineering
Mechanical Engineering
ISBN:9781118170519
Author:Norman S. Nise
Publisher:WILEY
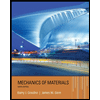
Mechanics of Materials (MindTap Course List)
Mechanical Engineering
ISBN:9781337093347
Author:Barry J. Goodno, James M. Gere
Publisher:Cengage Learning
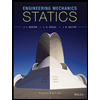
Engineering Mechanics: Statics
Mechanical Engineering
ISBN:9781118807330
Author:James L. Meriam, L. G. Kraige, J. N. Bolton
Publisher:WILEY
Related Questions
- In your summer internship, you are tasked with measuring the ultimate tensile strength of a material to determine if it meets your company’s (Superior Super Ships Inc) specification. Your boss is worried that the new low-cost supplier, Shoddy Alloys Inc, may not be reliable but it is the only way to source on-time the SS304 needed to make finishings for Jeff Bezos’ new yacht, the Black Pearl. You collect several load versus displacement curves, as illustrated below. The initial diameter of the round gauge section is 0.25 in. You also collect the instantaneous diameter of the specimen during the test using a laser. Using the provided data, calculate what is the ultimate tensile strength measured in this test?arrow_forward1. A tensile test was conducted on a metal "505" specimen and the following stress-strain curves were generated, both curves generated from the same set of data. Use the graphs to fill in the mechanical properties of the material tested in the box below. Don't forget units! Stress vs Strain Stress, psi Stress, psi 80000 70000 60000 50000 40000 30000 20000 10000 0 0.00 80000 70000 60000 50000 40000 30000 20000 10000 0.02 0 0.000 0.002 0.04 0.004 0.06 0.006 0.08 0.10 Strain Stress vs Strain 0.008 0.12 Elastic Modulus, E: 0.2% Offset Yield Strength, oo: Tensile Strength, ou: Breaking Strength, of: % Elongation: 0.14 0.010 0.012 0.014 Strain 0.16 0.18 0.016 0.018 0.20 0.020arrow_forwardPlease can you plot the Mohr's strain circle using the above informarrow_forward
- Calculate the young’s modulus from one of these two graphs?arrow_forwardConsider the graph below for 3 test samples A, B and C of the same metal composition which have been cold-worked, but to different extents. If you had to sort the samples by the degree of cold-working they have undergone, how would you rank them? Stress (MPa) 600 500 4006 300 200 100 0 A B 0.05 1 0.1 0.15 Strain Select the correct answer: a. Aarrow_forwardYou are a comparative evolutionary biologist that studies biomechanics. In particular, you are interested in how bone cross sectional shapes have evolved. You have discovered a rare (hypothetical) animal that has bone shapes similar to ours, but has solid, rectangular cross sectional areas. You conduct mechanical testing according to the parameters below and want to determine the: (A) moment of inertia; (B) reaction forces and moments at the fixed end O; (C) the stresses at points A, B, and C designated below, including the contributions of the different types of stresses at each pointarrow_forwardThe graph below shows the yield stress for a polycrystalline metal as a function of the grain size of the metal. The point A is (10 microns, 100 MPa) and B is (1000 microns, 28 MPa). Using this data, calculate what is the closest numerical match to the yield stress at 2 microns. yield stress (MPa) 8 8 8 8 8 8 8 80 70 50 40 30 A 200 Select one: O a. 198.9 MPa O b. 310.9 MPa O C. O d. 80.5 MPa 252.6 MPa O e. 165.2 MPa 400 600 grain size d (microns) 800 B ● 1000arrow_forwardUzNDU3NTYyMjk0/a/MjYOMzAwMjMOOTM5/details Further questions 4.The graphs show how the extension changes with stretching force for four different materials. a. Which two graphs show materials that follow Hooke's law? A B b. Which two graphs show materials that become less stiff as they are stretched? force force D C. Which graph shows a material that maintains the same stiffness throughout? force force 1. A force of 20N stretches a spring by 0.5m. The spring obeys Hooke's law. a. Calculate the spring constant including a suitable unit. b. How much force must a man use to stretch it by 1.5m? 5. A car has a weight of 240OON which is distributed equally over all four wheels. Each wheel has a spring of spring constant 400N/cm. a. Determine the force through the spring on each wheel. b. Calculate the compression of each spring when the car rests on the ground. 6.In a spring experiment the results were as follows: Force (N) Length (mpm 1 2 4 6. 7 50 58 70 74 82 9n 102 125 LELLarrow_forwardThe graph below gives a plot of force versus total sample length in a tensile test of a polymer. The sample is cylindrical, with an initial diameter of 1 cm and an initial length of 10 cm. From the data below, calculate the modulus, yield stress, yield strain, tensile strength, and % elongation.arrow_forwardNo wrong answer please , i could downvote The piece of suture is tested for its stress relaxation properties after cutting 3 cm long sample with a diameter of 1mm. The initial force recorded after stretching 0.1 cm between grips was 5 Newtons. Assume the suture material behave as if it has one relaxation time. The gage length was 1 cm. a. Calculate the initial stress. b. Calculate the initial strain. c. Calculate the modulus of elasticity of the suture if the initial stretching can be considered as linear and elastic. d. Calculate the relaxation time if the force recorded after 10 hours is 4 Newtons.arrow_forwardplease solve part b, this is past paper and just iam studying, mechanical engineeringarrow_forward6. State your answers to the following questions.Strain Gauge represents the deformation of a material through a change in resistance. If so, explain how temperature will affect the strain gauge in the experimental environment.①:In this experiment, the Strain Gauge measures the strain in micro units. Explain one possible error factor when applying a load by hanging a weight on the material with the strain gauge attached. (Hint: It is easy to shake by hanging the weight using a thread)①:arrow_forwardarrow_back_iosSEE MORE QUESTIONSarrow_forward_ios
Recommended textbooks for you
- Elements Of ElectromagneticsMechanical EngineeringISBN:9780190698614Author:Sadiku, Matthew N. O.Publisher:Oxford University PressMechanics of Materials (10th Edition)Mechanical EngineeringISBN:9780134319650Author:Russell C. HibbelerPublisher:PEARSONThermodynamics: An Engineering ApproachMechanical EngineeringISBN:9781259822674Author:Yunus A. Cengel Dr., Michael A. BolesPublisher:McGraw-Hill Education
- Control Systems EngineeringMechanical EngineeringISBN:9781118170519Author:Norman S. NisePublisher:WILEYMechanics of Materials (MindTap Course List)Mechanical EngineeringISBN:9781337093347Author:Barry J. Goodno, James M. GerePublisher:Cengage LearningEngineering Mechanics: StaticsMechanical EngineeringISBN:9781118807330Author:James L. Meriam, L. G. Kraige, J. N. BoltonPublisher:WILEY
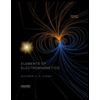
Elements Of Electromagnetics
Mechanical Engineering
ISBN:9780190698614
Author:Sadiku, Matthew N. O.
Publisher:Oxford University Press
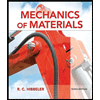
Mechanics of Materials (10th Edition)
Mechanical Engineering
ISBN:9780134319650
Author:Russell C. Hibbeler
Publisher:PEARSON
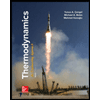
Thermodynamics: An Engineering Approach
Mechanical Engineering
ISBN:9781259822674
Author:Yunus A. Cengel Dr., Michael A. Boles
Publisher:McGraw-Hill Education
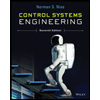
Control Systems Engineering
Mechanical Engineering
ISBN:9781118170519
Author:Norman S. Nise
Publisher:WILEY
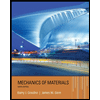
Mechanics of Materials (MindTap Course List)
Mechanical Engineering
ISBN:9781337093347
Author:Barry J. Goodno, James M. Gere
Publisher:Cengage Learning
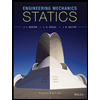
Engineering Mechanics: Statics
Mechanical Engineering
ISBN:9781118807330
Author:James L. Meriam, L. G. Kraige, J. N. Bolton
Publisher:WILEY