E29 Spring 2023 - HW4 - Forming processes
pdf
keyboard_arrow_up
School
University of California, Berkeley *
*We aren’t endorsed by this school
Course
29
Subject
Mechanical Engineering
Date
Apr 3, 2024
Type
Pages
4
Uploaded by MagistrateTarsier1791
1 University of California, Berkeley Department of Mechanical Engineering E 29: Manufacturing and Design Communication Spring 2023 Homework 4 Forming processes Due: Friday March 10, 11.59pm on Gradescope In all questions, please show your working or reasoning clearly. Responses showing only a final answer with no working or explanation will not receive full credit. Important note: uploads to Gradescope must be in image (e.g. .png) or .pdf format, and not .docx format (which is very cumbersome to download and grade). Also, we require that you use the Gradescope interface to identify the location of each part of your solutions in the file(s) you upload, so the reader does not have to scroll through a large document to find each of your answers. The instructions on how to do this are here
. Total points: 40 1. Lego bricks [10 points] In this question we consider the design and manufacture of Lego bricks. The photographs below show some bricks that have suffered from certain defects during the injection molding process. (A) (B)
(C)
(D)
http://bricksetforum.com/discussion/16396/marbled-lego-bricks-and-other-parts
2 1.1. Briefly name and describe the possible cause of any manufacturing defect(s) that you can identify in each photograph (A) to (D) above (some defect types may occur in more than one photo) [4 points]. An example of a drawing showing a typical Lego assembly is below: https://www.toysperiod.com/lego-set-reference/universal-building-set/basic/lego-507-1-basic-building-set/ 1.2. From a fit and tolerancing perspective, explain how Lego bricks work. What type of fit do you think exists between assembled Lego bricks? You do not need to give a specific numbered tolerance grade like “RC4”; we are looking for the general category of fit, like clearance, interference, transition, snap, shrink, or expansion. [3 points] 1.3. By considering fit and manufacturing issues, explain why the features on the underside of the bricks shown in photo B above are tubes rather than solid cylinders. [3 points] 2. Design for manufacture (DfM) by injection molding [6 points] In this question you will explore some key elements of a Solidworks tutorial on mold design for injection molding. Completing the whole tutorial would take longer than you are expected to take on this homework, so we have selected a few key steps to focus on below. You are welcome to work through the tutorial in detail if you have the time and interest. Steps: •
Load Solidworks (you can use the CAD labs computers if needed; also, the whole class has had remote ME CAD computer enabled) •
Click on the help icon (question mark in top right), then Tutorials, All SOLIDWORKS Tutorials, scroll down and click on Mold Design. •
Advance to the page on “Opening the model”, and click on the link to open a 3D model of half of a telephone handset that could be injection-molded. •
Save a local copy of the .sldpart file. •
Skip over the “Inserting mounting bosses” section to the “Checking for Draft” section.
3 •
To activate the Draft Analysis tool, click on the “Evaluate” ribbon above the view window, and then Draft Analysis (the tutorial says it is on the “mold tools toolbar” which has changed in this version of Solidworks). •
Follow the instructions in the tutorial for checking for draft angles in the design (the tutorial tells you to set a draft angle criterion of 0.5 degrees: i.e., edges that have a draft angle less than 0.5 degrees will be flagged as needing draft). •
After analysis parameters have been set in Step 4, you need to click the green tick in the Draft Analysis panel to run the analysis. •
The 3D model will be colored with regions with positive, negative, and missing draft. Rotate the model so you can see some of each category of draft, and place a screenshot of this view in your responses [2 points]
•
Suppose that the minimum acceptable draft for the process is now increased to 1 degree. Update this criterion in the draft analysis panel, update the analysis, and capture a new screenshot clearly showing any new surfaces that require draft. Place this screenshot in your responses [2 points]. •
Briefly describe which additional features require draft, when the required draft is increased to 1 degree [2 points] •
If you advance to the “Adding Draft” tutorial section, you will see instructions for adding draft to the zero-draft region of the design around the edge of the casing. I have found that following the instructions here yields the error “could not construct draft”, so I recommend skipping over this section and noting the general principle that draft can automatically be added to features that need it. •
Advance to “Applying Scaling”. Because the polymer contracts as it cools, the mold needs to be slightly larger than the intended final size of the component. Follow the instructions to scale up the dimensions by a factor of 1.05. (Step 2 says to select ‘Draft2’ under Solid Bodies(1) in the design tree. Assuming that you did not generate draft in the previous topic, ‘Draft2’ may not appear here; simply select whatever item appears under Solid Bodies(1) instead). 3. Sand casting [8 points] A sand mold has a downsprue of length = 15 cm. The cross-sectional area at the bottom of the sprue is 3.125 cm
2
. The sprue leads into a horizontal runner which feeds the mold cavity, whose volume is 1172 cm
3
. Determine: 3.1. the velocity of the molten metal flowing through the base of the downsprue, assuming that it is poured starting from a stationary state at the top of the downsprue, [4 points] 3.2. the volume rate of flow [2 points], and 3.3. the time required to fill the mold cavity, assuming continuity is preserved in the runner and gate system, and ignoring the time taken to fill runners and risers [2 points]. 4. Solidification in casting [6 points] A flat plate is to be cast in an open mold whose base has a square shape that is 200 mm × 200 mm. The mold is 40 mm deep. A total of 1,000,000 mm
3
of molten aluminum is poured into the mold. Volumetric solidification shrinkage is known to be 6.0%. The linear shrinkage due to thermal contraction after solidification is 1.3%. If the availability of molten metal in the mold allows the square shape of the cast plate to maintain its 200 mm × 200 mm dimensions until just after solidification is completed, determine the final dimensions of the plate. Show your calculations step-by-step.
Your preview ends here
Eager to read complete document? Join bartleby learn and gain access to the full version
- Access to all documents
- Unlimited textbook solutions
- 24/7 expert homework help
4 5. Solidification and Chvorinov’s rule [8 points] In a sand-casting process, the total solidification times of three potential riser shapes are to be compared: •
a sphere with diameter 10 cm, •
a cylinder with diameter and length both of 10 cm, and •
a cube with side length 10 cm. Mold constant = 3.5 min/cm
2
in Chvorinov's rule. The same casting alloy is used in the three cases. 5.1. Determine the solidification time for each geometry. [6 points] 5.2. Based on the results of part 4.1 and any other practical considerations that you consider relevant (e.g. how the pattern interacts with the packed sand), which geometric element do you think would make the best riser? Explain your reasoning. [2 points] 6. Casting defects [2 points] Study the photo below of some sand-cast components: Name a processing defect visible in these castings and explain how it could be eliminated, either by modifying the casting process or via secondary processing.
Related Documents
Related Questions
I need problems 6 and 7 solved.
I got it solved on 2 different occasions and it is not worded correctly.
NOTE: Problem 1 is an example of how it should be answered. Below are 2 seperate links to same question asked and once again it was not answered correctly. 1. https://www.bartleby.com/questions-and-answers/it-vivch-print-reading-for-industry-228-class-date-name-review-activity-112-for-each-local-note-or-c/cadc3f7b-2c2f-4471-842b-5a84bf505857
2. https://www.bartleby.com/questions-and-answers/it-vivch-print-reading-for-industry-228-class-date-name-review-activity-112-for-each-local-note-or-c/bd5390f0-3eb6-41ff-81e2-8675809dfab1
arrow_forward
Help me solve this ENGINEERING GRAPHICS question
Use 0.25 cartesian paper or 0.25 Isometric paper please.
arrow_forward
You are a biomedical engineer working for a small orthopaedic firm that fabricates rectangular shaped fracture
fixation plates from titanium alloy (model = "Ti Fix-It") materials. A recent clinical report documents some problems with the plates
implanted into fractured limbs. Specifically, some plates have become permanently bent while patients are in rehab and doing partial
weight bearing activities.
Your boss asks you to review the technical report that was generated by the previous test engineer (whose job you now have!) and used to
verify the design. The brief report states the following... "Ti Fix-It plates were manufactured from Ti-6Al-4V (grade 5) and machined into
solid 150 mm long beams with a 4 mm thick and 15 mm wide cross section. Each Ti Fix-It plate was loaded in equilibrium in a 4-point bending
test (set-up configuration is provided in drawing below), with an applied load of 1000N. The maximum stress in this set-up was less than the
yield stress for the Ti-6Al-4V…
arrow_forward
I need answers for problems 13, 14, and 15 pertaining to the print provided.
NOTE: If you refuse to answers all 3 parts and insist on wasting my question by breaking down 1 simple question into 3 parts, then just leave it for someone else to answer. Thank you.
arrow_forward
Please do not copy other's work and do not use ChatGPT or Gpt4,i will be very very very appreciate!!!
Thanks a lot!!!!!
arrow_forward
Please solve, engineering econ
arrow_forward
Please make the charts for the questions. Please refer to Successful Project Management (7th Edition). Attached is the example
Thank you.
arrow_forward
The class I'm taking is physics for scientists and engineers!
**** I need help with part D only*****
Can you please write out the solution and not type out the solution? I had to reask this question because the last tutor typed out the solution and it was very hard for me to follow . Please and thank you for the special request.
I have attached the problem. Please view attachment before answering. Thank you!
arrow_forward
Don't use chatgpt will upvote
arrow_forward
Please show work in a handwritten format.
Don't use chatgpt.
Mechanics of materials/design.
arrow_forward
I need parts 8, 9, and 10 answered. Number 1 is an example of how it should be answered.
NOTE: Read the instructions, no where does it say any drawing is required. It is really frustrating when I wait all this time for an answer to a question and some tutor does even read the instructions and just declines it...its ridicilous.
arrow_forward
Help!!! Answer all parts correctly!! Please
arrow_forward
The first photo is the question, where the 2nd shows some problem solving strategies
arrow_forward
I need answers to questions 13, 14, and 15 pertaining to the print provided.
Note: A tutor keeps putting 1 question into 3 parts and wasted so many of my questions. Never had a issue before until now, please allow a different tutor to answer because I was told I am allowed 3 of these questions.
arrow_forward
I need parts 1, 2, and 3 answered pertaining to the print provided.
NOTE: If you refuse to answers all 3 parts and insist on wasting my question, then just leave it for someone else to answer. I've never had an issue until recently one single tutor just refuses to even read the instructions of the question and just denies it for a false reasons or drags on 1 part into multiple parts for no reason.
arrow_forward
Chrome
File
Edit
View
History
Bookmarks
People
Tab
Window
Help
McGraw-Hill Campus - ALEKS Science - CHM1045 GEN CHEM 1 BLENDED 669113
A bconline.broward.edu/d21/le/content/466883/fullscreen/12868783/View
McGraw-Hill Campus - ALEKS Science
O GASES
Interconverting pressure and force
A chemistry graduate student is designing a pressure vessel for an experiment. The vessel will contain gases at pressures up to 470.0 MPa. The student's
design calls for an observation port on the side of the vessel (see diagram below). The bolts that hold the cover of this port onto the vessel can safely withstand
a force of 2.80 MN.
pressure vessel
bolts
side
View
port
Calculate the maximum safe diameter w of the port. Round your answer to the nearest 0.1 cm.
O cm
Explanation
Check
O2021 McGraw-Hill Education. All Rights Reserved. Terms of Use
FEB
arrow_forward
I need answers to questions 1, 2, and 3 pertaining to the print provided.
Note: A tutor keeps putting 1 question into 3 parts and wasted so many of my questions. Never had a issue before until now, please allow a different tutor to answer because I was told I am allowed 3 of these questions.
arrow_forward
I need answers to problems 7, 8, and 9.
NOTE: Please stop wasting my time and yours by rejecting my question because it DOES NOT REQUIRE YOU TO DRAW anything at all. They are simple questions pertaining to the print provided. READ THE INSTRUCTIONS of the assignment before you just reject it for a FALSE reason or leave it for someone to answer that actually wants to do their job. Thanks.
arrow_forward
Handwritten solution required.
Strictly don't use chatgpt.
If you use chatgpt ,I will report the answer for sure.
Mechanical engineering dynamics.
arrow_forward
[Engineering Thermodynamics]
Please finish the answer with a diagram for reference to me (if needed).
Show the answer step by step and clear to see.
If you need to answer with words, please type directly. (to avoid cant see clear by handwriting)
Thank you.
P.S. Use the online software http://www.peacesoftware.de/einigewerte/r134a_e.html
or property table and p-h diagram for R134a where necessary.
arrow_forward
A Team of Engineers asked for an internal combustion engine to use it in a designed car. Your role is to describe the operation sequence of different types of available engines, explain their mechanical efficiency, and deliver a detailed technical report to show your approach in solving and discussing the following tasks and issues.
You must follow the following steps to help the team:
STEP 1
Describe the operational sequence of four-stroke spark ignition and four-stroke compression ignition engines with the aid of sketches by constructing simple sketch representing the operation and plotting the P-V diagrams for each process during the cycle to show the following:
The input and output heat and net output work
The expansion and compression strokes
The air-fuel mixture intake and exhaust gasses
The spark plug when it is in the active mode
The complete cycle of ideal Otto and Diesel cycles that shows the input and output heat and net output work.
STEP 2
Explain the mechanical…
arrow_forward
I just need help with part D, thanks
arrow_forward
In a hypothetical scenario respond to the following email to reasuure the owner and in an informative and professional way.
Dear Project Manager-
I am so excited to have broken ground on the new mixed use space. As I watch the underground utilities such as water, storm drain, and sewer get installed I find myself worrying about failures. What steps are you taking to ensure those systems will not have to be dug up and repaired later in the construction process? We cannot afford a delay of any kind. Could you please explain how you plan to prevent any delays and ensure that the systems are functional and leak free.
The other concern that has come up that I would like to address now is the comfort of the office staff. Our current building is not comfortable. I am wondering why. We have the temperature appropriately set and it is easily maintained, but people still complain. What can we do to ensure they will be comfortable in the new building? A few months ago I asked one of our…
arrow_forward
J 6
arrow_forward
SEE MORE QUESTIONS
Recommended textbooks for you
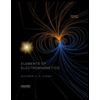
Elements Of Electromagnetics
Mechanical Engineering
ISBN:9780190698614
Author:Sadiku, Matthew N. O.
Publisher:Oxford University Press
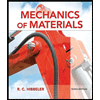
Mechanics of Materials (10th Edition)
Mechanical Engineering
ISBN:9780134319650
Author:Russell C. Hibbeler
Publisher:PEARSON
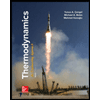
Thermodynamics: An Engineering Approach
Mechanical Engineering
ISBN:9781259822674
Author:Yunus A. Cengel Dr., Michael A. Boles
Publisher:McGraw-Hill Education
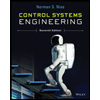
Control Systems Engineering
Mechanical Engineering
ISBN:9781118170519
Author:Norman S. Nise
Publisher:WILEY
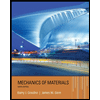
Mechanics of Materials (MindTap Course List)
Mechanical Engineering
ISBN:9781337093347
Author:Barry J. Goodno, James M. Gere
Publisher:Cengage Learning
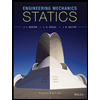
Engineering Mechanics: Statics
Mechanical Engineering
ISBN:9781118807330
Author:James L. Meriam, L. G. Kraige, J. N. Bolton
Publisher:WILEY
Related Questions
- I need problems 6 and 7 solved. I got it solved on 2 different occasions and it is not worded correctly. NOTE: Problem 1 is an example of how it should be answered. Below are 2 seperate links to same question asked and once again it was not answered correctly. 1. https://www.bartleby.com/questions-and-answers/it-vivch-print-reading-for-industry-228-class-date-name-review-activity-112-for-each-local-note-or-c/cadc3f7b-2c2f-4471-842b-5a84bf505857 2. https://www.bartleby.com/questions-and-answers/it-vivch-print-reading-for-industry-228-class-date-name-review-activity-112-for-each-local-note-or-c/bd5390f0-3eb6-41ff-81e2-8675809dfab1arrow_forwardHelp me solve this ENGINEERING GRAPHICS question Use 0.25 cartesian paper or 0.25 Isometric paper please.arrow_forwardYou are a biomedical engineer working for a small orthopaedic firm that fabricates rectangular shaped fracture fixation plates from titanium alloy (model = "Ti Fix-It") materials. A recent clinical report documents some problems with the plates implanted into fractured limbs. Specifically, some plates have become permanently bent while patients are in rehab and doing partial weight bearing activities. Your boss asks you to review the technical report that was generated by the previous test engineer (whose job you now have!) and used to verify the design. The brief report states the following... "Ti Fix-It plates were manufactured from Ti-6Al-4V (grade 5) and machined into solid 150 mm long beams with a 4 mm thick and 15 mm wide cross section. Each Ti Fix-It plate was loaded in equilibrium in a 4-point bending test (set-up configuration is provided in drawing below), with an applied load of 1000N. The maximum stress in this set-up was less than the yield stress for the Ti-6Al-4V…arrow_forward
- I need answers for problems 13, 14, and 15 pertaining to the print provided. NOTE: If you refuse to answers all 3 parts and insist on wasting my question by breaking down 1 simple question into 3 parts, then just leave it for someone else to answer. Thank you.arrow_forwardPlease do not copy other's work and do not use ChatGPT or Gpt4,i will be very very very appreciate!!! Thanks a lot!!!!!arrow_forwardPlease solve, engineering econarrow_forward
- Please make the charts for the questions. Please refer to Successful Project Management (7th Edition). Attached is the example Thank you.arrow_forwardThe class I'm taking is physics for scientists and engineers! **** I need help with part D only***** Can you please write out the solution and not type out the solution? I had to reask this question because the last tutor typed out the solution and it was very hard for me to follow . Please and thank you for the special request. I have attached the problem. Please view attachment before answering. Thank you!arrow_forwardDon't use chatgpt will upvotearrow_forward
- Please show work in a handwritten format. Don't use chatgpt. Mechanics of materials/design.arrow_forwardI need parts 8, 9, and 10 answered. Number 1 is an example of how it should be answered. NOTE: Read the instructions, no where does it say any drawing is required. It is really frustrating when I wait all this time for an answer to a question and some tutor does even read the instructions and just declines it...its ridicilous.arrow_forwardHelp!!! Answer all parts correctly!! Pleasearrow_forward
arrow_back_ios
SEE MORE QUESTIONS
arrow_forward_ios
Recommended textbooks for you
- Elements Of ElectromagneticsMechanical EngineeringISBN:9780190698614Author:Sadiku, Matthew N. O.Publisher:Oxford University PressMechanics of Materials (10th Edition)Mechanical EngineeringISBN:9780134319650Author:Russell C. HibbelerPublisher:PEARSONThermodynamics: An Engineering ApproachMechanical EngineeringISBN:9781259822674Author:Yunus A. Cengel Dr., Michael A. BolesPublisher:McGraw-Hill Education
- Control Systems EngineeringMechanical EngineeringISBN:9781118170519Author:Norman S. NisePublisher:WILEYMechanics of Materials (MindTap Course List)Mechanical EngineeringISBN:9781337093347Author:Barry J. Goodno, James M. GerePublisher:Cengage LearningEngineering Mechanics: StaticsMechanical EngineeringISBN:9781118807330Author:James L. Meriam, L. G. Kraige, J. N. BoltonPublisher:WILEY
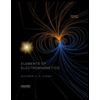
Elements Of Electromagnetics
Mechanical Engineering
ISBN:9780190698614
Author:Sadiku, Matthew N. O.
Publisher:Oxford University Press
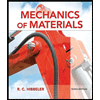
Mechanics of Materials (10th Edition)
Mechanical Engineering
ISBN:9780134319650
Author:Russell C. Hibbeler
Publisher:PEARSON
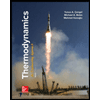
Thermodynamics: An Engineering Approach
Mechanical Engineering
ISBN:9781259822674
Author:Yunus A. Cengel Dr., Michael A. Boles
Publisher:McGraw-Hill Education
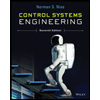
Control Systems Engineering
Mechanical Engineering
ISBN:9781118170519
Author:Norman S. Nise
Publisher:WILEY
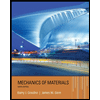
Mechanics of Materials (MindTap Course List)
Mechanical Engineering
ISBN:9781337093347
Author:Barry J. Goodno, James M. Gere
Publisher:Cengage Learning
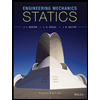
Engineering Mechanics: Statics
Mechanical Engineering
ISBN:9781118807330
Author:James L. Meriam, L. G. Kraige, J. N. Bolton
Publisher:WILEY