E29 Spring 2023 - HW3 - Additive processes
pdf
keyboard_arrow_up
School
University of California, Berkeley *
*We aren’t endorsed by this school
Course
29
Subject
Mechanical Engineering
Date
Apr 3, 2024
Type
Pages
6
Uploaded by MagistrateTarsier1791
1 University of California, Berkeley Department of Mechanical Engineering E 29: Manufacturing and Design Communication Spring 2023 Homework 3 Additive processes Due: Friday February 24, 11.59pm on Gradescope (This week, you can have a penalty-free extension of up to five days past this date without needing to request one; if you find you need a longer extension, please inform your GSI.) Important note: uploads to Gradescope must be in image (e.g. .png) or .pdf format, and not .docx format (which is very cumbersome to download and grade). Also, we require that you use the Gradescope interface to identify the location of each part of your solutions in the file(s) you upload, so the reader does not have to scroll through a large document to find each of your answers. The instructions on how to do this are here
. Total points: 40 1. Applications of additive manufacturing [12 points] Below are listed four objects that are regularly manufactured: 1.1. The body of a space rocket 1.2. Food eaten by astronauts on the Space Station 1.3. Transparent dental aligner 1.4. Heat exchanger for an air conditioning system For each item, do the following: (a) Ask ChatGPT whether or not additive manufacturing is suitable for manufacturing the object, and why. Abridge ChatGPT’s answer to not more than 100 words and quote it at the start of your response. Make it clear which part of your answer came from ChatGPT. [1 point per object] (b) In your own words, discuss whether or not you agree with the response you obtained above. Include in your answer [2 points per object]: •
A brief discussion of the relative merits of using an additive process for this product, as opposed to using a “traditional” process such as machining, injection molding, casting, stamping, etc. •
If you think additive manufacturing could be appropriate, briefly explain why (as inspiration, you can use the list of possible motivations for using additive processing in the lecture notes).
2 •
If you believe additive manufacturing could be appropriate, suggest which
additive process(es) of the ones we have studied in lecture would be most appropriate, and why. •
If you think an additive process would not be warranted, briefly say why not. 2. Carbon fiber-reinforced FDM extrusion path planning [12 points] The Markforged X7 printer combines an FDM thermoplastic extrusion printer with the ability to incorporate continuous fiber reinforcement, producing extremely stiff, strong, and lightweight composite components. 2.1. Study the Jacobs online training materials for the Markforged X7 printer (
here
), then take the online quiz at the end of the training materials and upload a screenshot showing that you have successfully completed it with a score of 7/7. [3 points] Notes: •
The section of the Jacobs training entitled “Eiger File Setup Process” asks you to “Log in to the Jacobs Institute’s Eiger Organization”. For this homework, you will not be printing directly to the Institute’s physical printer, so, instead, simply create a free online Markforged account at https://eiger.io to enable you to use their proprietary cloud-based slicer software, Eiger. You will be invited to activate a free trial of the simulation features within the Markforged software. Simulation is not necessary for this homework, and you may want to wait to activate the simulation trial in case you end up wanting to use it for your project. •
You do not need to schedule any in-person/hands-on training for this homework, though are welcome to do so if interested. Next, we will load, slice, and analyze an example object in the interface. •
Import the RepRap extruder mount .stl file from Lab 3. Accept the default orientation of the part as imported. •
Go to Part View. •
In Part Settings (right hand of screen), select Onyx FR material (the chopped carbon fiber-reinforced Nylon material), and Carbon Fiber reinforcement material (the material for the continuous fibers to be woven into the print). The printer Type should then appear as “Industrial Series (X3, X5, X7)”. •
Click Save, and the software will slice the object and generate print paths (this will take a couple of minutes). •
Click on Internal View (bottom right), then select 2D mode.
3 2.2. Scan through the layers using the slider at the bottom of the screen. At which layer numbers (as displayed above the slider) does continuous reinforcement fiber appear? [1 point] 2.3. Upload a screenshot of one of the layers containing continuous fibers. [1 point] 2.4. Describe the pattern traced out by the continuous fibers in these layers. How are fibers near the edges of the part laid down, compared to those in the center of the part? [1 point] 2.5. Why do you think the slicer has placed continuous fibers at these layers and not others? [2 points] 2.6. Record the projected material cost from the left hand of the screen. [0.5 point] 2.7. Suppose that the component is anchored at the two locations shown by the yellow arrows in the diagram below, and that it is loaded in the direction and location shown by the red arrow. If maximizing the flexural rigidity of this component in this loading state is important, suggest, in words, one modification to the placement of continuous fiber that could be made, within the physical constraints of the printer’s capabilities, to increase the rigidity. [2 points] 2.8. Use the “Create new override” function to implement your proposed change. (If you want to add fibers to multiple layers at once, you will need to switch into 3D view, and click and drag on the layer bar to select the range of layers to which fibers are to be added.) Include a 3D screenshot of your modified toolpath plan in Internal View. [1 point] 2.9. Report the change in projected cost associated with this modification. [0.5 point]
Your preview ends here
Eager to read complete document? Join bartleby learn and gain access to the full version
- Access to all documents
- Unlimited textbook solutions
- 24/7 expert homework help
4 Stereolithography [12 points] As introduced in class, some stereolithography printers use an oxygen-permeable window at the bottom of the resin tray to create a ‘dead zone’ of resin in which photocrosslinking is inhibited by the presence of oxygen. The purpose is to prevent the printed part from sticking to the tray. As the part being printed is drawn upwards out of the tray, liquid resin is sucked into the space vacated by the part. In this question we consider how the thickness of the dead zone and the design being printed affects the vertical force that needs to be exerted on the component. Below is a figure taken from the Science
paper that introduced the Continuous Liquid Interface Production (CLIP) process (Tumbleston et al., Science
vol. 347, no. 6228, p 1349):
5 Consider the following simple model for the pressures in a thin disk of liquid between two rigid surfaces that is being made thinner or thicker at a specified rate. The printed feature illustrated is a cylindrical post with radius a
: The pressure distribution across the fluid disk is parabolic, falling to zero at the edges and peaking at the center. The average suction pressure across the disk is given by: 𝑝𝑝
0
=
3
𝜂𝜂𝑎𝑎
2
2ℎ
3
�
d
ℎ
d
𝑡𝑡
�
Where 𝜂𝜂
is the viscosity of the resin, h
is the thickness of the dead zone, and t
is time. The vertical force associated with the suction pressures within this resin disk is 𝐹𝐹
𝑓𝑓𝑓𝑓𝑓𝑓𝑓𝑓𝑓𝑓𝑓𝑓𝑓𝑓
=
π
a
2
p
0
. Note the inverse cubic dependence of pressure on dead zone thickness for a given printing speed. In the printer, the lower rigid plate corresponds to the oxygen-permeable window, and the upper plate, with radius a
, is a single feature that is being printed. A printed object will contain many features distributed across the window. 2.10. Suppose that the viscosity of the resin is 0.35 Pa.s (Pascal-seconds), which is typical for a stereolithography resin. Take a
= 1 mm, and the dead zone thickness to be h
= 50 µm. Also suppose that 100 of these features are arrayed across the part being printed. The print speed, d
h
/d
t
, is 100 mm/hour. Showing your working, compute the total force that would need to be applied to the part during printing to overcome viscous forces in the resin. [6 points] 2.11. Now suppose that instead of printing 100, 1 mm-radius pillars, a single pillar with radius 10 mm is printed. It has the same area as the 100 smaller pillars. Find the printing force for this single, larger, pillar. [4 points]
6 2.12. Compare your value from 3.2 with the value you found in part 3.1, and comment on your findings and any implications for the application of dead zones and geometric freedom in stereolithography printing. [2 points] 3. Gathering your opinions on computer programming in ME [4 points] In the ME Department we are currently reviewing how we teach computer programming at the undergraduate level. We would like to give you an opportunity to provide your perspective and influence the development of our curriculum in this area. Please complete the following short survey as part of this homework: https://forms.gle/iaXS8GAZsTgitQL66 We will award 4 points when your response is logged by the Google Form. There is no need to upload anything specific to Gradescope for this part of the homework.
Your preview ends here
Eager to read complete document? Join bartleby learn and gain access to the full version
- Access to all documents
- Unlimited textbook solutions
- 24/7 expert homework help
Related Documents
Related Questions
Help!!! Answer all parts correctly!! Please
arrow_forward
Help me solve this ENGINEERING GRAPHICS question
Use 0.25 cartesian paper or 0.25 Isometric paper please.
arrow_forward
Please write solution on paper, thank you. No typing, it's hard to follow. I''l give positive feedback.
arrow_forward
AutoSave
STATICS - Protected View• Saved to this PC -
O Search (Alt+Q)
Off
ERIKA JOY DAILEG
EJ
File
Home
Insert
Draw
Design
Layout
References
Mailings
Review
View
Help
Acrobat
O Comments
E Share
PROTECTED VIEW Be careful-files from the Internet can contain viruses. Unless you need to edit, it's safer to stay in Protected View.
Enable Editing
Situation 9 - A 6-m long ladder weighing 600 N is shown in the Figure. It is required to determine
the horizontal for P that must be exerted at point C to prevent the ladder from sliding. The
coefficient of friction between the ladder and the surface at A and B is 0.20.
25. Determine the reaction at A.
26. Determine the reaction at B.
27. Determine the required force P.
4.5 m
1.5 m
H=0.2
30°
Page 5 of 5
671 words
D. Focus
100%
C
ЕPIC
GAMES
ENG
7:24 pm
w
US
16/02/2022
IZ
arrow_forward
J 6
arrow_forward
No gpt,solve in paper sheet.
Free body diagram is must and should.
arrow_forward
I just need help with part D, thanks
arrow_forward
Chrome
File
Edit
View
History
Bookmarks
People
Tab
Window
Help
McGraw-Hill Campus - ALEKS Science - CHM1045 GEN CHEM 1 BLENDED 669113
A bconline.broward.edu/d21/le/content/466883/fullscreen/12868783/View
McGraw-Hill Campus - ALEKS Science
O GASES
Interconverting pressure and force
A chemistry graduate student is designing a pressure vessel for an experiment. The vessel will contain gases at pressures up to 470.0 MPa. The student's
design calls for an observation port on the side of the vessel (see diagram below). The bolts that hold the cover of this port onto the vessel can safely withstand
a force of 2.80 MN.
pressure vessel
bolts
side
View
port
Calculate the maximum safe diameter w of the port. Round your answer to the nearest 0.1 cm.
O cm
Explanation
Check
O2021 McGraw-Hill Education. All Rights Reserved. Terms of Use
FEB
arrow_forward
I need problems 6 and 7 solved.
I got it solved on 2 different occasions and it is not worded correctly.
NOTE: Problem 1 is an example of how it should be answered. Below are 2 seperate links to same question asked and once again it was not answered correctly. 1. https://www.bartleby.com/questions-and-answers/it-vivch-print-reading-for-industry-228-class-date-name-review-activity-112-for-each-local-note-or-c/cadc3f7b-2c2f-4471-842b-5a84bf505857
2. https://www.bartleby.com/questions-and-answers/it-vivch-print-reading-for-industry-228-class-date-name-review-activity-112-for-each-local-note-or-c/bd5390f0-3eb6-41ff-81e2-8675809dfab1
arrow_forward
You are a biomedical engineer working for a small orthopaedic firm that fabricates rectangular shaped fracture
fixation plates from titanium alloy (model = "Ti Fix-It") materials. A recent clinical report documents some problems with the plates
implanted into fractured limbs. Specifically, some plates have become permanently bent while patients are in rehab and doing partial
weight bearing activities.
Your boss asks you to review the technical report that was generated by the previous test engineer (whose job you now have!) and used to
verify the design. The brief report states the following... "Ti Fix-It plates were manufactured from Ti-6Al-4V (grade 5) and machined into
solid 150 mm long beams with a 4 mm thick and 15 mm wide cross section. Each Ti Fix-It plate was loaded in equilibrium in a 4-point bending
test (set-up configuration is provided in drawing below), with an applied load of 1000N. The maximum stress in this set-up was less than the
yield stress for the Ti-6Al-4V…
arrow_forward
arrow_forward
Oh no! Our expert couldn't answer your question.
Don't worry! We won't leave you hanging. Plus, we're giving you back one question for the inconvenience.
Here's what the expert had to say:
Hi and thanks for your question! Unfortunately we cannot answer this particular question due to its complexity. We've credited a question back to your account. Apologies for the inconvenience.
Ask Your Question Again
5 of 10 questions left
until 8/10/20
Question
Asked Jul 13, 2020
1 views
An air conditioning unit uses Freon (R-22) to adapt an office room at temperature 25 oC in the summer, if the temperature of the evaporator is 16 oC and of the condenser is 48 oC. The reciprocating compressor is single acting, number of cylinders are 2, the volumetric efficiency is 0.9, number of revolutions are 900 r.p.m. and L\D= 1.25. If the compressor consumes a power of 3 kW and its mechanical efficiency is 0.9. Find the following:
(A) Flow rate of the refrigerant per…
arrow_forward
Please do one through 3
arrow_forward
Hartley Electronics, Inc., in Nashville, producesshort runs of custom airwave scanners for the defense industry.The owner, Janet Hartley, has asked you to reduce inventory byintroducing a kanban system. After several hours of analysis, youdevelop the following data for scanner connectors used in onework cell. How many kanbans do you need for this connector?Daily demand 1,000 connectorsLead time 2 daysSafety stock 12 dayKanban size 500 connectors
arrow_forward
1. Use the collision theory to explain why a lump of sugar is better to use in hot cup of tea ,but granulated sugar is better to use in iced tea.
2.suppose you held a lighted match to a solid pieces of wood and another match to a pile of wood shavings .which form of wood catch fire more easily and why?
arrow_forward
Handwritten solution required.
Strictly don't use chatgpt.
If you use chatgpt ,I will report the answer for sure.
Mechanical engineering dynamics.
arrow_forward
Don't use chatgpt will upvote
arrow_forward
The first photo is the question, where the 2nd shows some problem solving strategies
arrow_forward
I drew it but I don't know where I have to connect it. Where do I put dashed lines (if needed) where are the solid lines? Did I do it right?
arrow_forward
Home
Insert
Draw
Design
Layout
References
Maili
OLYTECH
Calibri (Bo...
11
v A A
Aa v
m Air. Ma
Paste
в I
U v ab x,
x | A
Name:
ID No.:
rm Air. M
Date:
CRN:
Course Code: JACV 506E
Aircraft Mechanical Mainte
Practice.
ces ( CRI
Page
Originated By
Mark awarded -
Instructor/Assessor:
Assignment: Interpret engineering drawings and diagrams
bus
se Mat
hing Pl
Questions: -
1. Write 2 differences between isometric and oblique projections?
ssment
2. Write 5 details found on the drawing title block?
Feedba
3. Write 4 types of sectional views?
4. Name 3 methods how drawings are stored in?
5. Name 3 types of fits?
arrow_forward
Please show work in a handwritten format.
Don't use chatgpt.
Mechanics of materials/design.
arrow_forward
Don't Use Chat GPT Will Upvote And Give Handwritten Solution Please
arrow_forward
SEE MORE QUESTIONS
Recommended textbooks for you
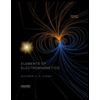
Elements Of Electromagnetics
Mechanical Engineering
ISBN:9780190698614
Author:Sadiku, Matthew N. O.
Publisher:Oxford University Press
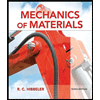
Mechanics of Materials (10th Edition)
Mechanical Engineering
ISBN:9780134319650
Author:Russell C. Hibbeler
Publisher:PEARSON
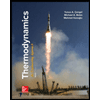
Thermodynamics: An Engineering Approach
Mechanical Engineering
ISBN:9781259822674
Author:Yunus A. Cengel Dr., Michael A. Boles
Publisher:McGraw-Hill Education
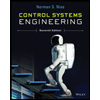
Control Systems Engineering
Mechanical Engineering
ISBN:9781118170519
Author:Norman S. Nise
Publisher:WILEY
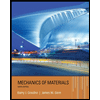
Mechanics of Materials (MindTap Course List)
Mechanical Engineering
ISBN:9781337093347
Author:Barry J. Goodno, James M. Gere
Publisher:Cengage Learning
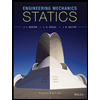
Engineering Mechanics: Statics
Mechanical Engineering
ISBN:9781118807330
Author:James L. Meriam, L. G. Kraige, J. N. Bolton
Publisher:WILEY
Related Questions
- AutoSave STATICS - Protected View• Saved to this PC - O Search (Alt+Q) Off ERIKA JOY DAILEG EJ File Home Insert Draw Design Layout References Mailings Review View Help Acrobat O Comments E Share PROTECTED VIEW Be careful-files from the Internet can contain viruses. Unless you need to edit, it's safer to stay in Protected View. Enable Editing Situation 9 - A 6-m long ladder weighing 600 N is shown in the Figure. It is required to determine the horizontal for P that must be exerted at point C to prevent the ladder from sliding. The coefficient of friction between the ladder and the surface at A and B is 0.20. 25. Determine the reaction at A. 26. Determine the reaction at B. 27. Determine the required force P. 4.5 m 1.5 m H=0.2 30° Page 5 of 5 671 words D. Focus 100% C ЕPIC GAMES ENG 7:24 pm w US 16/02/2022 IZarrow_forwardJ 6arrow_forwardNo gpt,solve in paper sheet. Free body diagram is must and should.arrow_forward
- I just need help with part D, thanksarrow_forwardChrome File Edit View History Bookmarks People Tab Window Help McGraw-Hill Campus - ALEKS Science - CHM1045 GEN CHEM 1 BLENDED 669113 A bconline.broward.edu/d21/le/content/466883/fullscreen/12868783/View McGraw-Hill Campus - ALEKS Science O GASES Interconverting pressure and force A chemistry graduate student is designing a pressure vessel for an experiment. The vessel will contain gases at pressures up to 470.0 MPa. The student's design calls for an observation port on the side of the vessel (see diagram below). The bolts that hold the cover of this port onto the vessel can safely withstand a force of 2.80 MN. pressure vessel bolts side View port Calculate the maximum safe diameter w of the port. Round your answer to the nearest 0.1 cm. O cm Explanation Check O2021 McGraw-Hill Education. All Rights Reserved. Terms of Use FEBarrow_forwardI need problems 6 and 7 solved. I got it solved on 2 different occasions and it is not worded correctly. NOTE: Problem 1 is an example of how it should be answered. Below are 2 seperate links to same question asked and once again it was not answered correctly. 1. https://www.bartleby.com/questions-and-answers/it-vivch-print-reading-for-industry-228-class-date-name-review-activity-112-for-each-local-note-or-c/cadc3f7b-2c2f-4471-842b-5a84bf505857 2. https://www.bartleby.com/questions-and-answers/it-vivch-print-reading-for-industry-228-class-date-name-review-activity-112-for-each-local-note-or-c/bd5390f0-3eb6-41ff-81e2-8675809dfab1arrow_forward
- You are a biomedical engineer working for a small orthopaedic firm that fabricates rectangular shaped fracture fixation plates from titanium alloy (model = "Ti Fix-It") materials. A recent clinical report documents some problems with the plates implanted into fractured limbs. Specifically, some plates have become permanently bent while patients are in rehab and doing partial weight bearing activities. Your boss asks you to review the technical report that was generated by the previous test engineer (whose job you now have!) and used to verify the design. The brief report states the following... "Ti Fix-It plates were manufactured from Ti-6Al-4V (grade 5) and machined into solid 150 mm long beams with a 4 mm thick and 15 mm wide cross section. Each Ti Fix-It plate was loaded in equilibrium in a 4-point bending test (set-up configuration is provided in drawing below), with an applied load of 1000N. The maximum stress in this set-up was less than the yield stress for the Ti-6Al-4V…arrow_forwardarrow_forward Oh no! Our expert couldn't answer your question. Don't worry! We won't leave you hanging. Plus, we're giving you back one question for the inconvenience. Here's what the expert had to say: Hi and thanks for your question! Unfortunately we cannot answer this particular question due to its complexity. We've credited a question back to your account. Apologies for the inconvenience. Ask Your Question Again 5 of 10 questions left until 8/10/20 Question Asked Jul 13, 2020 1 views An air conditioning unit uses Freon (R-22) to adapt an office room at temperature 25 oC in the summer, if the temperature of the evaporator is 16 oC and of the condenser is 48 oC. The reciprocating compressor is single acting, number of cylinders are 2, the volumetric efficiency is 0.9, number of revolutions are 900 r.p.m. and L\D= 1.25. If the compressor consumes a power of 3 kW and its mechanical efficiency is 0.9. Find the following: (A) Flow rate of the refrigerant per…arrow_forwardPlease do one through 3arrow_forward
arrow_back_ios
SEE MORE QUESTIONS
arrow_forward_ios
Recommended textbooks for you
- Elements Of ElectromagneticsMechanical EngineeringISBN:9780190698614Author:Sadiku, Matthew N. O.Publisher:Oxford University PressMechanics of Materials (10th Edition)Mechanical EngineeringISBN:9780134319650Author:Russell C. HibbelerPublisher:PEARSONThermodynamics: An Engineering ApproachMechanical EngineeringISBN:9781259822674Author:Yunus A. Cengel Dr., Michael A. BolesPublisher:McGraw-Hill Education
- Control Systems EngineeringMechanical EngineeringISBN:9781118170519Author:Norman S. NisePublisher:WILEYMechanics of Materials (MindTap Course List)Mechanical EngineeringISBN:9781337093347Author:Barry J. Goodno, James M. GerePublisher:Cengage LearningEngineering Mechanics: StaticsMechanical EngineeringISBN:9781118807330Author:James L. Meriam, L. G. Kraige, J. N. BoltonPublisher:WILEY
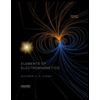
Elements Of Electromagnetics
Mechanical Engineering
ISBN:9780190698614
Author:Sadiku, Matthew N. O.
Publisher:Oxford University Press
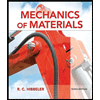
Mechanics of Materials (10th Edition)
Mechanical Engineering
ISBN:9780134319650
Author:Russell C. Hibbeler
Publisher:PEARSON
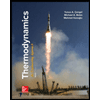
Thermodynamics: An Engineering Approach
Mechanical Engineering
ISBN:9781259822674
Author:Yunus A. Cengel Dr., Michael A. Boles
Publisher:McGraw-Hill Education
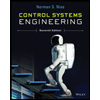
Control Systems Engineering
Mechanical Engineering
ISBN:9781118170519
Author:Norman S. Nise
Publisher:WILEY
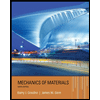
Mechanics of Materials (MindTap Course List)
Mechanical Engineering
ISBN:9781337093347
Author:Barry J. Goodno, James M. Gere
Publisher:Cengage Learning
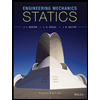
Engineering Mechanics: Statics
Mechanical Engineering
ISBN:9781118807330
Author:James L. Meriam, L. G. Kraige, J. N. Bolton
Publisher:WILEY