MECH 351 Lab 2
docx
keyboard_arrow_up
School
Concordia University *
*We aren’t endorsed by this school
Course
351
Subject
Mechanical Engineering
Date
Apr 3, 2024
Type
docx
Pages
18
Uploaded by AgentSnail2002
Lab Report on Experiment 2
DWSIM
MECH-351 Lab Section WI-X
Group B
February 19th, 2024
Dr. Lyes Kadem & Dr. Charles Kiyanda
Concordia University
Montreal, QC, Canada
SECTION 1
Figure 1: Rankine Cycle Diagram from Experiment 1
Figure 2: Results from Experiment 1
A)
Compute the actual Carnot and thermal efficiencies a.1.) Carnot efficiency: 50.98%
a.2.) Thermal efficiency: 29.20%
B)
Plot the T-S diagram for the actual Rankine cycle
Your preview ends here
Eager to read complete document? Join bartleby learn and gain access to the full version
- Access to all documents
- Unlimited textbook solutions
- 24/7 expert homework help
C)
Plot the variations for the following Inlet Turbine Temperatures:
Figure 3: Diagram Containing Variations for Inlet Turbine Temperatures
Temperature (Celsius)
450
500
550
600
Carnot Efficiency
50.98%
54.15%
56.94%
59.40%
Thermal Efficiency
29.20%
30.05%
30.94%
31.86%
Steam Quality
0.9219
0.9450
0.9667
0.9873
Table 1: Table Containing Variations for Inlet Turbine Temperatures
DISCUSSION: Both the Carnot and Thermal efficiencies of the system increases with the
increase of heat at the turbine inlet. This can be explained by the formulas 1-(Tc/Th) (Carnot)
and W/Qin (Thermal). Both efficiencies generally increase with an increase in the heat
supplied to the turbine inlet, but the Carnot efficiency benefits from the increase in
temperature difference between the heat source while the thermal efficiency benefits from the
increased net work output. The steam quality inches closer to the saturated vapor line (x= 1)
with the increase of heat because more heat entails that the quality of the water at the same
given pressure will come closer to dry vapor and further away from the saturated vapor line
(x=0).
D)
Plot the variations for the following Condenser Pressures: Figure 4: Diagram Containing Variations for Condenser Pressures
Your preview ends here
Eager to read complete document? Join bartleby learn and gain access to the full version
- Access to all documents
- Unlimited textbook solutions
- 24/7 expert homework help
Condenser
Pressures (kPa)
50
40
30
20
10
Carnot Efficiency
50.98%
51.74%
52.67%
53.92%
55.89%
Thermal
Efficiency
29.20%
30.07%
31.14%
32.57%
34.83%
Steam Quality
0.9219
0.9121
0.9000
0.8838
0.8582
Table 2: Table Containing Variations for Condenser Pressures
DISCUSSION: As the pressure of the condenser decreases, the efficiencies increase. By
decreasing the pressure at the condenser, the condenser temperature decreases. This, in turn,
increases the temperature difference between the boiler and the condenser. According to the
Carnot efficiency formula, a larger temperature difference leads to higher efficiency. When
the pressure at the condenser decreases, the pressure difference decreases as well, resulting in
reduced pump work. This reduction in pump work improves the overall efficiency of the
cycle.The steam quality is also reduced because lower pressures yield lower temperatures
which in turn, yield steam that is less “dry”.
E)
Plot the variations for the following Condenser Exit Temperatures: Figure 5: Diagram Containing Variations for Condenser Exit Temperatures
Figure 6: Diagram Containing Variations for Condenser Outlet Temperatures Back Work Ratio
Your preview ends here
Eager to read complete document? Join bartleby learn and gain access to the full version
- Access to all documents
- Unlimited textbook solutions
- 24/7 expert homework help
Temperature
(Celsius)
80
70
60
50
20
Carnot Efficiency
51.17%
52.55%
53.93%
55.31%
59.46%
Thermal
Efficiency
29.15%
28.75%
28.36%
27.98%
26.90%
Back Work Ratio
(work pump /
Work turbine)
3.45e-3
3.43e-3
3.41e-3
3.40e-3
3.36e-3
Table 3: Table Containing Variations for Condenser Exit Temperatures DISCUSSION:
By decreasing the condenser exit temperature, the temperature difference
between the boiler and the condenser increases. According to the Carnot efficiency formula, a
larger temperature difference leads to a higher Carnot efficiency. Therefore, lowering the
condenser exit temperature would increase the Carnot efficiency. The thermal efficiency on
the other hand, is determined by the ratio of net work output to the heat input. Decreasing the
condenser exit temperature can reduce the temperature at which heat is rejected from the
cycle. As a result, the heat rejected in the condenser decreases. However, the work output
from the turbine remains relatively constant, leading to a reduction in the ratio of work output
to heat input and thus a decrease in thermal efficiency. The work of the pump in this ideal
rankine cycle is negligible. The average value of percentage of work in, in comparison with
that of the value of work out, is less than 1%.
F)
Plot the variations for the following Turbine Pressures : Figure 7: Diagram Containing Variations for Turbine Inlet Pressures
Pressure (MPa)
2
5
10
15
20
Carnot Efficiency
50.98%
50.98%
50.98%
50.98%
50.98%
Thermal
Efficiency
27.18%
31.65%
34.65%
36.09%
36.82%
Steam Quality 0.9528
0.8812
0.8199
0.7770
0.7402
Table 4: Table Containing Variations for Turbine Pressures
DISCUSSION: Increasing the inlet turbine pressure doesn't directly impact the Carnot
efficiency, as long as the temperatures of the heat source (boiler) and the heat sink
(condenser) remain the same. Higher turbine inlet pressure means higher enthalpy of the
steam entering the turbine. This results in more work output for the same mass flow rate of
steam passing through the turbine, increasing the cycle's efficiency. With increased turbine
inlet pressure, the turbine expands the steam to a lower pressure, which can lead to increased
expansion work output. This is because the larger pressure drop across the turbine results in
more work extracted from the steam. Additionally, higher turbine inlet pressure can allow for
a reduction in the amount of superheating needed in the boiler, reducing energy losses
associated with superheating and improving overall efficiency. The quality of the steam
inevitably inches closer to x=1 due to the increase in pressure which in turn, increases
temperature. The quality will always inch closer to x=1 (saturated vapor line) as temperature
increases.
Your preview ends here
Eager to read complete document? Join bartleby learn and gain access to the full version
- Access to all documents
- Unlimited textbook solutions
- 24/7 expert homework help
SECTION 2
Figure 2: Ideal Regeneration Rankine Cycle on DWSIM
Thermal Efficiency
Feed Water Heater Pressure (kPa)
30.00%
200
29.84%
400
29.73%
600
29.65%
800
29.59%
1000
Table 2: Thermal Efficiency Vs Feed Water Heater Pressure for an Ideal Regeneration Rankine Cycle Data
Figure 3: Thermal Efficiency Vs Feed Water Heater Pressure for an Ideal Regeneration Rankine Cycle
Question 2 Discussion
As seen above, the thermal efficiency decreases as the feed water heater (FWH)
pressure increases. Mathematically, this can be seen from the data in the appendix. As FWH
pressure increases, the “Q_in” value decreases and the “Q_out” value remains stable, while
thermal efficiency can be calculated as:
ղ
Th
= 1 - Q_out/Q_in
showing that the ratio “Q_out/Q_in” increases. The same can be said for the ratio “Net
Work/Q_in”. Both values decrease with the increased pressure of the FWH, but the “Net
Work” decreases at a higher rate than “Q_in”. However, theoretically this does not make sense as a FWH should increase the
efficiency of a rankine system as the FWH temperature approaches closer to the average of
the outlet temperature of the boiler and the outlet temperature of the condenser. The FWH
being at a higher pressure means the temperature should be higher as well. Looking at the
data, the expected outcome would be an increase in thermal efficiency from 200 kPa to 600
kPa and then a decrease until 1000 kPa as temperature starts to become further from the
average. This discrepancy with the expected trend may be due to many factors. One factor
may be the fraction split between the FWH and the second turbine. No fraction was specified
and so only 5.00% of the mass flow went to the FWH. Another issue may be that the mass
split was done after the turbines work whereas, generally, FWH’s take some of the flow
directly from the turbine, before the work is finished, as it allows for it to use higher pressure
steam while also allowing the first turbine to complete more work. This however, should not
be the issue as the calculations were done under the assumption of ideal parameters with
100% efficiency.
Although the values were not as expected, the FWH still increased the efficiency of
the system compared to if no FWH was involved. The thermal efficiency at 200 kPa without
a FWH would have been:
ղ
Th
= 1 - Q_out/Q_in → ղ
Th
= 1 - 2124.7946kW/3001.1445kW = 0.2920 = 29.20%
compared to the 30.00% that was calculated instead.
SECTION 3
a)
Your preview ends here
Eager to read complete document? Join bartleby learn and gain access to the full version
- Access to all documents
- Unlimited textbook solutions
- 24/7 expert homework help
Figure 4: Three Turbine, Reheat and Regeneration Cycle
b)
Choice 1
: We need the pressure at point 16, which is where the steam is extracted for the water heating.
Choice2
: We need the temperature at point 14. This is right after the throttling process and before the open feedwater heater.
c)
Choice 1 (Pressure at Point 4): This pressure is typically chosen to maximize the efficiency of
the turbine cycle while still providing sufficient energy for the extraction process.
Since the steam is being extracted for feedwater heating, the pressure should be high enough to ensure a significant temperature difference between the extracted steam and the feedwater.
However, it shouldn't be too high to avoid excessive energy loss in the extraction process.
A reasonable range for the pressure at point 4 could be between 0.7 MPa to 1 MPa {0.7, 0.8, 0.9, 1.0}.
Choice 2 (Temperature at Point 8): This temperature is typically slightly above the saturation temperature corresponding to the pressure at point 4, as it is right after the throttling process.
The throttling process results in a small decrease in temperature due to the Joule-Thomson effect, but it should remain close to the saturation temperature. A reasonable range for the temperature at point 8 could be 350ºC to 400ºC {350, 375, 400, 425, 450}.
d)
Figure 5: Thermal Efficiency vs Pressure for Three Turbine Cycle
The parameter we chose is Pressure. There are 3 stages to what we observe:
1.
When the steam is bleeding at a low pressure, it has a low thermal efficiency, as we can see on the graph, if we plot a value of low pressure, the thermal efficiency will be Thermal
efficiency
P
low. We can also say that there is very low heat sent to the feed water heater, so the thermal efficiency is low.
2.
When pressure is bleeding at a high pressure, it has a high thermal efficiency because the heat required by the boiler is less, so the thermal efficiency increases.
3.
When the pressure starts being too high, the thermal efficiency decreases because the work output of the turbine will be less.
4.
Values: At 0.6MPa: Thermal efficiency is 28.87%
At 0.7MPa: Thermal efficiency is 31.83%
At 0.8MPa: Thermal efficiency is 34.66%
At 0.9MPa: Thermal efficiency is 36.37%
At 1.0MPa: Thermal efficiency is 34.98%
Your preview ends here
Eager to read complete document? Join bartleby learn and gain access to the full version
- Access to all documents
- Unlimited textbook solutions
- 24/7 expert homework help
Related Documents
Related Questions
Submit correct and complete solutions.
give propriate Explanation.
Provide step-by-step detailed explanations.
arrow_forward
OBB
Occ
ODD
QUESTION 7
What is the entropy change for an energy reservoir at 700°C that transfers 1500KJ of heat to a heat engine? (5 Points) Please include your calculations in the PDE submission and mark your answer on Blackboard.
QUESTION 8
Calculate the entropy change, in kJ/K, of 10 kg of silver when its temperature increases from 20°C to 100°C (cy of silver 0 235 kJkgk) (5 Points) Please include your calculations in the PDE submission and mark your answer.on
Blackboard.
QUESTION 9
An engineer claims that they designed a nozzle that increases the velocity of air flow from 50 m/s to 100 m/s. However, due to unforeseen issues, the exit velocity is measured as 75 m/s Find the isentropic efficiency of this nozzle. (5
Points) Please include your calculations in the PDF submission and mark your answer on Blackboard,
QUESTION 10
Steam enters in an adiabatic turbine steadily at 4 MPa and 85% quality, Steam leaves the turbine as saturated vapor at 10°C If the mass flow rate of the steam is…
arrow_forward
Combined Gas-Vapor Power Cycle.
Thermodynamics
Trying to find T7 using the following equation. Don't understand how to get Ta, Tb, cp,a or (dp/dt)sat. No need to solve for values, but if you can explain how to get them I will appreciate it.
arrow_forward
Hi please show calculations or diagrams if required thank you
arrow_forward
I am having a hard time understanding C-E on this problem. For C, I know that Th>Ti>Tc. Does that mean that since ec= 1-Tc/Th and Tc is the lowest temp of the system, that it is indeed more efficient with both engines?
The other ones, I just don't know where to start.
Any help or explantions would be appreciated!
arrow_forward
Given:
=
refueling Powertran
SOURCE EMISSIONS
vehide
eff
eff
gasoline 266g co₂/kwh-
HEV
0.90
0.285
FLgrid 411ilg Co₂/kWh
41111gCo₂/kWh
EV
0.85
0.80
Production
11x10% og CO₂
13.7 x 10°g CO₂
A) Calculate the breakeven pont (in km driven) for a EV
against on HEV in Florida
of 0.1kWh/kM
Use a drive cycle conversion
5) How efficient would the powertrain of the HEV in this
example have to be to break even with an EV in Florida
after 150,000 Miles of service (240,000) km
Is it plausible to achieve the answer from pert b
Consideans the HaXINERY theoretical efficiency of
the Carnot cycle is 5020 and there are additional
losses of the transMISSION :- 90% efficiency
?
c
A what do
you conclude is the leading factor in why
EVs are less emissive than ICE,
arrow_forward
I need a rules used in the ventilation system for the report "air quality and safe entertainment in sports halls" like this photo below but for ventilation system formulas
arrow_forward
Show incorrect Only
Ford: Attempt 5
Qin
Qout
System
Hot Rody
1.
Win
Consider the heat pump cycle outlined above. If the C.O.P. of the cycle is reported to
be Y = 6.0 and the work input to the system is found to be Win = 10.30 Btu,
determine the heat transferred into the system during cycle, Qin (Btu).
!!
%3D
Your Answer:
Answer
units
37°F Clear
bp
17
f8
f9
ho
16
10
14
fs
%24
&
4.
8
近
arrow_forward
What would be the type of filter (model) used in a steam turbine cogeneration plant in a thermal power plant?
*Exemplify with a cataloged model with data such as pressure drop, for example.
arrow_forward
Please solve and read question carefully the answer is not 11977.487.
arrow_forward
University of Basrah - College of Engineering
Department of Mechanical Engineering
Subject: Power Plant I
Class: Fourth
Examiner: Dr. Ahmad A. M Alsahlani
Notes: Giving Sketches is compulsory wherever needed (Total Ma
Q1] Answer the following que
Exam: Final-Exam
Date: 11/09/2023
Time: 2 Hours
1- Explain how the Geothermal Energy can be utilized to generate electricity.
2- State the two classifications of energy sources and give three examples for each.
3- State three advantages and three disadvantages of using Gas Turbine Power Plant.
4- What are the reasons that lead to a deviation in the ideal gas turbine cycle?
5- Draw a block diagram for a regenerative Rankin Cycle using one open feed water
heater.
Q2]
A closed cycle gas-turbine power plant has a pressure ratio of 10. The air temperature is
35 C at the compressor inlet and 1127 C at the turbine inlet. The received energy at the Qi
combustion chamber is 794 kJ/kg. Assume the isentropic efficiency of the turbine is
95%. Determine…
arrow_forward
Pls. refer to the answer keys so that I will know if my solution is wrong
arrow_forward
| As a mechanical engineering technician, you are asked by your building manager to investigate the
performance of a steam turbine at the main university building. Criticaly compare how heat transfer
efficiency will affect the lifetime of the turbine.
arrow_forward
[MO31] THERMODYNAMIC CYCLES
It is proposed to build a 1000 MWelectric power plant with steam as the working fluid. The condensers
are to be cooled with river water. The maximum steam temperature is 550 C, and the pressure in the condensers
will be 10 kPa. Estimate the temperature rise of the river downstream from the power plant.
A. AT = 4.9 deg C
Power
B. AT = 3.9 deg C
plant
C. AT = 2.9 deg C
D. AT = 1.9 deg C
Discharge
Intake
60 m-
8 m deep
River mean speed
10m/minute
arrow_forward
SEE MORE QUESTIONS
Recommended textbooks for you
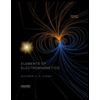
Elements Of Electromagnetics
Mechanical Engineering
ISBN:9780190698614
Author:Sadiku, Matthew N. O.
Publisher:Oxford University Press
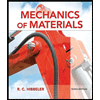
Mechanics of Materials (10th Edition)
Mechanical Engineering
ISBN:9780134319650
Author:Russell C. Hibbeler
Publisher:PEARSON
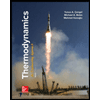
Thermodynamics: An Engineering Approach
Mechanical Engineering
ISBN:9781259822674
Author:Yunus A. Cengel Dr., Michael A. Boles
Publisher:McGraw-Hill Education
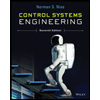
Control Systems Engineering
Mechanical Engineering
ISBN:9781118170519
Author:Norman S. Nise
Publisher:WILEY
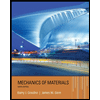
Mechanics of Materials (MindTap Course List)
Mechanical Engineering
ISBN:9781337093347
Author:Barry J. Goodno, James M. Gere
Publisher:Cengage Learning
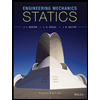
Engineering Mechanics: Statics
Mechanical Engineering
ISBN:9781118807330
Author:James L. Meriam, L. G. Kraige, J. N. Bolton
Publisher:WILEY
Related Questions
- Submit correct and complete solutions. give propriate Explanation. Provide step-by-step detailed explanations.arrow_forwardOBB Occ ODD QUESTION 7 What is the entropy change for an energy reservoir at 700°C that transfers 1500KJ of heat to a heat engine? (5 Points) Please include your calculations in the PDE submission and mark your answer on Blackboard. QUESTION 8 Calculate the entropy change, in kJ/K, of 10 kg of silver when its temperature increases from 20°C to 100°C (cy of silver 0 235 kJkgk) (5 Points) Please include your calculations in the PDE submission and mark your answer.on Blackboard. QUESTION 9 An engineer claims that they designed a nozzle that increases the velocity of air flow from 50 m/s to 100 m/s. However, due to unforeseen issues, the exit velocity is measured as 75 m/s Find the isentropic efficiency of this nozzle. (5 Points) Please include your calculations in the PDF submission and mark your answer on Blackboard, QUESTION 10 Steam enters in an adiabatic turbine steadily at 4 MPa and 85% quality, Steam leaves the turbine as saturated vapor at 10°C If the mass flow rate of the steam is…arrow_forwardCombined Gas-Vapor Power Cycle. Thermodynamics Trying to find T7 using the following equation. Don't understand how to get Ta, Tb, cp,a or (dp/dt)sat. No need to solve for values, but if you can explain how to get them I will appreciate it.arrow_forward
- Hi please show calculations or diagrams if required thank youarrow_forwardI am having a hard time understanding C-E on this problem. For C, I know that Th>Ti>Tc. Does that mean that since ec= 1-Tc/Th and Tc is the lowest temp of the system, that it is indeed more efficient with both engines? The other ones, I just don't know where to start. Any help or explantions would be appreciated!arrow_forwardGiven: = refueling Powertran SOURCE EMISSIONS vehide eff eff gasoline 266g co₂/kwh- HEV 0.90 0.285 FLgrid 411ilg Co₂/kWh 41111gCo₂/kWh EV 0.85 0.80 Production 11x10% og CO₂ 13.7 x 10°g CO₂ A) Calculate the breakeven pont (in km driven) for a EV against on HEV in Florida of 0.1kWh/kM Use a drive cycle conversion 5) How efficient would the powertrain of the HEV in this example have to be to break even with an EV in Florida after 150,000 Miles of service (240,000) km Is it plausible to achieve the answer from pert b Consideans the HaXINERY theoretical efficiency of the Carnot cycle is 5020 and there are additional losses of the transMISSION :- 90% efficiency ? c A what do you conclude is the leading factor in why EVs are less emissive than ICE,arrow_forward
- I need a rules used in the ventilation system for the report "air quality and safe entertainment in sports halls" like this photo below but for ventilation system formulasarrow_forwardShow incorrect Only Ford: Attempt 5 Qin Qout System Hot Rody 1. Win Consider the heat pump cycle outlined above. If the C.O.P. of the cycle is reported to be Y = 6.0 and the work input to the system is found to be Win = 10.30 Btu, determine the heat transferred into the system during cycle, Qin (Btu). !! %3D Your Answer: Answer units 37°F Clear bp 17 f8 f9 ho 16 10 14 fs %24 & 4. 8 近arrow_forwardWhat would be the type of filter (model) used in a steam turbine cogeneration plant in a thermal power plant? *Exemplify with a cataloged model with data such as pressure drop, for example.arrow_forward
- Please solve and read question carefully the answer is not 11977.487.arrow_forwardUniversity of Basrah - College of Engineering Department of Mechanical Engineering Subject: Power Plant I Class: Fourth Examiner: Dr. Ahmad A. M Alsahlani Notes: Giving Sketches is compulsory wherever needed (Total Ma Q1] Answer the following que Exam: Final-Exam Date: 11/09/2023 Time: 2 Hours 1- Explain how the Geothermal Energy can be utilized to generate electricity. 2- State the two classifications of energy sources and give three examples for each. 3- State three advantages and three disadvantages of using Gas Turbine Power Plant. 4- What are the reasons that lead to a deviation in the ideal gas turbine cycle? 5- Draw a block diagram for a regenerative Rankin Cycle using one open feed water heater. Q2] A closed cycle gas-turbine power plant has a pressure ratio of 10. The air temperature is 35 C at the compressor inlet and 1127 C at the turbine inlet. The received energy at the Qi combustion chamber is 794 kJ/kg. Assume the isentropic efficiency of the turbine is 95%. Determine…arrow_forwardPls. refer to the answer keys so that I will know if my solution is wrongarrow_forward
arrow_back_ios
SEE MORE QUESTIONS
arrow_forward_ios
Recommended textbooks for you
- Elements Of ElectromagneticsMechanical EngineeringISBN:9780190698614Author:Sadiku, Matthew N. O.Publisher:Oxford University PressMechanics of Materials (10th Edition)Mechanical EngineeringISBN:9780134319650Author:Russell C. HibbelerPublisher:PEARSONThermodynamics: An Engineering ApproachMechanical EngineeringISBN:9781259822674Author:Yunus A. Cengel Dr., Michael A. BolesPublisher:McGraw-Hill Education
- Control Systems EngineeringMechanical EngineeringISBN:9781118170519Author:Norman S. NisePublisher:WILEYMechanics of Materials (MindTap Course List)Mechanical EngineeringISBN:9781337093347Author:Barry J. Goodno, James M. GerePublisher:Cengage LearningEngineering Mechanics: StaticsMechanical EngineeringISBN:9781118807330Author:James L. Meriam, L. G. Kraige, J. N. BoltonPublisher:WILEY
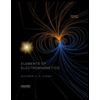
Elements Of Electromagnetics
Mechanical Engineering
ISBN:9780190698614
Author:Sadiku, Matthew N. O.
Publisher:Oxford University Press
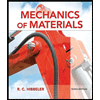
Mechanics of Materials (10th Edition)
Mechanical Engineering
ISBN:9780134319650
Author:Russell C. Hibbeler
Publisher:PEARSON
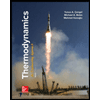
Thermodynamics: An Engineering Approach
Mechanical Engineering
ISBN:9781259822674
Author:Yunus A. Cengel Dr., Michael A. Boles
Publisher:McGraw-Hill Education
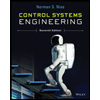
Control Systems Engineering
Mechanical Engineering
ISBN:9781118170519
Author:Norman S. Nise
Publisher:WILEY
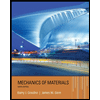
Mechanics of Materials (MindTap Course List)
Mechanical Engineering
ISBN:9781337093347
Author:Barry J. Goodno, James M. Gere
Publisher:Cengage Learning
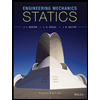
Engineering Mechanics: Statics
Mechanical Engineering
ISBN:9781118807330
Author:James L. Meriam, L. G. Kraige, J. N. Bolton
Publisher:WILEY