MECH 351 Lab 1
docx
keyboard_arrow_up
School
Concordia University *
*We aren’t endorsed by this school
Course
351
Subject
Mechanical Engineering
Date
Apr 3, 2024
Type
docx
Pages
21
Uploaded by AgentSnail2002
Lab Report on Experiment 1
EXPANSION OF A PERFECT GAS
MECH-351 Lab Section WI-X
Group B
January 23
rd
, 2024
Dr. Lyes Kadem & Dr. Charles Kiyanda
Concordia University
Montreal, QC, Canada
OBJECTIVE
This lab contains 3 distinct experiments with different objectives which all use
temperature and pressure sensors [1]. Experiment 1 aims to show the relation between
temperature and pressure by using a short depressurization period [1]. Experiment 2 aims to use
the same short depressurization technique to simulate a reversible, adiabatic expansion, which
will then be used to calculate the specific heat capacity ratio of the surrounding air through
pressure readings [1]. Experiment 3 aims to use a longer depressurization period to simulate an
irreversible, adiabatic expansion which will then be used to calculate the specific heat capacity
ratio of air by using the pressure readings [1].
INTRODUCTION
The behavior of a gas is difficult to perfectly predict, or calculate under most conditions,
as there are numerous parameters to take into account. To avoid measuring and calculating many
of these parameters, one can use the ideal gas equation along with the assumption that the gas
behaves ideally to calculate approximate values for the gas’ state [1]. A gas that behaves ideally
is referred to as a perfect gas and the four following assumptions are made about it: gas particles
hold negligible volume, gas particles are equally sized and have no intermolecular forces, gas
particles move in accordance to Newton’s Laws of Motion, and gas particle experience no
energy loss due to perfect elastic collision [2]. Using these assumptions, one can now relate the
pressure, temperature, and volume of the gas through the following equation referred to as the
ideal gas equation:
PV = nRT
where “P” is pressure in kPa, “V” is volume in m
3
, “n” is number of moles, “R” is the gas
constant in kJ/(mol*K), and “T” is the temperature in K [1]. A real gas can be described by:
PV = znRT
where “z” is the compressibility factor which has no units [1]. The compressibility factor
remains close to one when pressures are below 300 kPa, and thus a real gas can be said to behave
ideally under those conditions [1].
The amount of energy required to increase one unit mass by one degree is referred to as
the specific heat capacity [1]. The specific heat capacity of a gas varies based on whether the gas
is at constant volume, or constant pressure [1]. These are referred to as “C
V
” and “C
P
”
respectively. By taking the ratio of C
P
/C
V
, the specific heat capacity ratio, “
”
𝘠
can be found [1].
This new variable has no units and allows one to relate pressure, temperature and volume during
simple expansion or compression of gasses [3]. More applications of this variable exist, but this
experiment focuses on the compression and expansion of air.
An isothermal process is one in which the temperature remains constant, while an
adiabatic process means that no heat energy is added or removed during the process [1]. An
isothermal process is not necessarily adiabatic as a system can remain the same temperature if
equivalent energy is lost through work as is added through heat [1]. Reversible and irreversible processes refer to the ability of the system to return to its
original state with no change to its surrounding environment through heat or work [1]. Processes
tend to be irreversible as they often encompass a change in entropy [1]. A process is only said to
be reversible if there is no change in entropy due to the process [1]. The following formula is
used to calculate the change in entropy for processes done on ideal gasses:
s
2
- s
1
= C
V
ln(T
2
/T
1
) + Rln(V
2
/V
1
)
where “s” is the entropy of the gas [1]. To achieve such a reversible process, a technique named
“Clément Desormes Method” will be employed [1]. This two step method takes an initial state
and puts it through a reversible, adiabatic process to an intermediate state [1]. The intermediate
state is then left at constant volume until it has stabilized [1]. This process allows one to calculate
the specific heat capacity ratio through the following equation:
Figure 1: Equation 1.13 [1]
The same method can also be applied to an irreversible, adiabatic process and yields the
following formula:
Figure 2:Equation 1.17 [1]
Your preview ends here
Eager to read complete document? Join bartleby learn and gain access to the full version
- Access to all documents
- Unlimited textbook solutions
- 24/7 expert homework help
This experiment uses a pressurized vessel with internal pressure and temperature sensors,
along with software which allows one to visualize the values of the pressure and/or temperature
[1]. The vessel has a constant volume and the change in mass is negligible, and therefore treated
as a constant [1]. This means that the pressure and temperature are expected to be directly
proportional, according to the ideal gas equation. Using this relationship, a reversible and non-
reversible, adiabatic process will be done to explore different aspects of the first and second laws
of thermodynamics [1]. PROCEDURE
Equipment Information
The three experiments for lab 1 use an apparatus called “The Expansion of a Perfect Gas
TD1004V” [1]. This machine consists of two pressurized vessels, a pressure and a vacuum
vessel, with pressure and temperature sensors, along with a connecting bore pipe fitted with ball
valves to either transfer, or empty the gasses in the vessels from the top [1]. Both vessels can
have a small tube with a valve connected through the bottom to allow the connection of an air
pump to control the pressure within the vessels [1]. Below, Figure 1 will show the full apparatus
used for the three experiments:
Figure 3: Front View of Expansion of a Perfect Gas Apparatus [1]
The three experiments use the pressure vessel, along with valve 1, in conjunction with a
diaphragm pump to increase pressure within the vessel [1]. The pump can be controlled via the
apparatus’ control box where the various sensors are also connected to [1]. The control box can
be seen below in Figure 3:
Figure 4: Expansion of a Perfect Gas Apparatus Control Box [1]
Various configurations of how the sensors are plugged will have their own distinct advantages
and disadvantages which will be briefly seen in the experiments [1]. The final equipment is a
software named Versatile Data Acquisition System (VDAS
®) [1]. The software receives the data
from the sensors and plots it so that the user may visualize and use the data [1].
Experiment 1
Run VDAS
® and select “Experiment 1” on the computer [1]. Ensure that the pressure
vessel is selected and input the ambient pressure [1]. From Figure 1, insert “P1” and “T1” into
Figure 2’s “P” and “T” slots under the “Fast Inputs” label [1]. Connect both “Pressure Ports”
from Figures 1 and 2 and start communications on VDAS
® [1]. Turn on the air pump, let the
pressure rise to approximately 30kPa, and then turn off the air pump [1]. Wait for the
temperature and pressure to stabilize within +/- 0.5 and kPa, and then quickly open and close
℃
Figure 1’s “V1” valve [1]. Wait for the temperature and pressure to stabilize within +/- 0.5 ℃
and kPa, and stop VDAS
® communications [1]. Scroll through the acquired data graph until the
offset is found and right click the graph and select “Save analogue traces to File” [1]. Ensure that
a copy of this file is acquired for use in the lab report and then open “V1” to completely empty
the vessel [1].
Experiment 2
Run VDAS
® and select “Experiment 2” on the computer. Ensure that the pressure vessel
is selected and input the ambient pressure [1]. From Figure 1, insert “P1” and “T1” into Figure
2’s “P” and “T1” [1]. Connect both “Pressure Ports” from Figures 1 and 2 and start
communications on VDAS
® [1]. Run the air pump until the pressure reaches approximately
30KPa and then stop the air pump [1]. Wait for the pressure and temperature to stabilize within
+/- 0.5 and kPa, and record the pressure in the allotted spot on the data sheet [1]. Quickly
℃
open and close valve “V1” and then allow pressure and temperature to stabilize within +/- 0.5 ℃
and kPa, [1]. Stop VDAS
® communications and record the final pressure in the allotted spot on
the data sheet [1]. Scroll back on the data graph until the offset is reached and record the lowest
pressure into its allotted spot on the data sheet [1]. Right click the graph and select “Save
analogue traces to File” [1]. Ensure that a copy of this file is acquired for use in the lab report
and then open “V1” to completely empty the vessel [1]. Repeat the entire process, excluding
saving and copying the file, two more times, and then another 3 times each for 40kPa, 50kPa,
and 60kPa [1].
Experiment 3
Run VDAS
® and select “Experiment 2” on the computer. Ensure that the pressure vessel
is selected and input the ambient pressure [1]. From Figure 1, insert “P1” and “T1” into Figure
2’s “P” and “T1” [1]. Connect both “Pressure Ports” from Figures 1 and 2 and start
communications on VDAS
® [1]. Run the air pump until the pressure reaches approximately
30KPa and then stop the air pump [1]. Wait for the pressure and temperature to stabilize within
+/- 0.5 and kPa, and record the pressure in the allotted spot on the data sheet [1]. Open valve
℃
“V1” and then close after 1 second then allow pressure and temperature to stabilize within +/-
0.5 and kPa, [1]. Stop ℃
VDAS
® communications and record the final pressure in the allotted
spot on the data sheet [1]. Scroll back on the data graph until the offset is reached and record the
lowest pressure into its allotted spot on the data sheet [1]. Right click the graph and select “Save
analogue traces to File” [1]. Ensure that a copy of this file is acquired for use in the lab report
and then open “V1” to completely empty the vessel [1]. Repeat the process two more times,
excluding the saving of the file [1].
Your preview ends here
Eager to read complete document? Join bartleby learn and gain access to the full version
- Access to all documents
- Unlimited textbook solutions
- 24/7 expert homework help
RESULTS
Experiment 1
Figure 5: Temperature (top blue line) and pressure (bottom yellow line) readings from Experiment 1 on “P vs t”
and “T vs t” Graph
Experiment 2
Sample Calculations
Formulas used:
P
abs
= P
atm
+P
gauge
where P
atm is 102 kPa
and
Figure 6: Equation 1.13 [1]
P
abs
= 102 kPa + 31.79 kPa = 133.79 kPa
rev= [ln(119.47 kPa) - ln(133.79 kPa)] / [ln(123.3 kPa) - ln(133.79 kPa)] = 1.386
𝘠
0.3 bars
0.4 bars
0.5 bars
0.6 bars
Trial
1
Trial
2
Trial
3
Trial
1
Trial
2
Trial
3
Trial
1
Trial
2
Trial
3
Trial
1
Trial
2
Trial
3
P
abs initial
(kPa)
133.
79
131.
12
130.
66
141.
08
141.
23
141.
92
150.
67
150.
82
150.
51
161.
50
160.
84
161.
10
P
abs inter
(kPa)
119.
47
121.
58
123.
09
125.
20
130.
81
136.
96
139.
80
140.
50
133.
35
151.
66
151.
97
141.
70
P
abs Final (kPa)
123.
30
123.
72
124.
83
129.
07
133.
17
137.
50
142.
03
142.
64
137.
44
150.
04
150.
14
145.
77
Table 1: Measured values from experiment 2 converted into the absolute pressure values P(abs). The formula used
was P
abs
= P
atm
+P
gauge
0.3 bars
0.4 bars
0.5 bars
0.6 bars
rev=
𝘠
1.331
1.257
1.291
0.987
Table 2: Using the values from the figure 5, we calculated the mean specific heat capacity ratio for each pressure
(we use the sum∑ of all Trials for each P).
Your preview ends here
Eager to read complete document? Join bartleby learn and gain access to the full version
- Access to all documents
- Unlimited textbook solutions
- 24/7 expert homework help
Figure 7: Pressure (yellow line) readings from Experiment 2 on a “P vs t” Graph
Experiment 3
Sample Calculations
Formulas used:
P
abs
= P
atm
+P
gauge
where P
atm is 102 kPa
and
Figure 8:Equation 1.17 [1]
P
abs
= 102 kPa + 29.27 kPa = 131.27 kPa
𝘠
irrev
= ((131.27 kPa/102 kPa) - 1)/((131.27 kPa/108.40 kPa) - 1) = 1.36
Figure 9: Pressure (yellow line) readings from Experiment 3 on a “P vs t” Graph
0.3 bars
Trial 1
Trial 2
Trial 3
P
abs initial
(kPa)
131.27
131.42
131.28
P
abs inter (kPa)
102.76
102.73
102.75
P
abs Final
108.40
108.40
108.41
Your preview ends here
Eager to read complete document? Join bartleby learn and gain access to the full version
- Access to all documents
- Unlimited textbook solutions
- 24/7 expert homework help
(kPa)
Table 3: Measured values from experiment 3 converted into the absolute pressure values P(abs). The formula used
was P
abs
= P
atm
+P
gauge
0.3 bars
Trial 1 Trial 2
Trial 3
𝘠
irrev
=
1.360
1.358
1.361
Table 4: Specific Heat Capacity Ratio from each Trial on Table 3
DISCUSSION
Experiment 1
During the brief depressurization of the pressure vessel, changes in both temperature and
pressure were observed. The internal pressure of the vessel, initially stable at 0.3 bars (30kPa),
dipped below the 0.25 bars (25kPa) and began augmenting until it stabilized at 0.25 bars (25kPa)
(+/- 0.05 bars). A dip in the form of a reciprocal function was observed for the temperature line
and a gradual increase was noted. The temperature stabilized once it matched that of the ambient
temperature (23.4
).
℃
Due to the atmospheric temperature of the room being higher than that of
the vessel after the brief depressurization, the increase of internal temperature of the vessel can
be explained by the second law of thermodynamics which states that the entropy of an isolated
system always increases. In other words, the system is attempting to reach equilibrium with that
of the system surrounding it (we consider the entire lab room to be the latter). Because
temperature and pressure are directly proportional, the increase of temperature causes the
increase in pressure. From the specific heat capacity at constant pressure formula (
u
=
U
/
m
)
where u
is specific heat capacity at constant pressure, U
is enthalpy and m
is the mass of the
system, we know that “heat energy [...] added at constant pressure [...] causes gas to expand,
[thus] expanding the container” [1]. In this lab the container was rigid and could not expand,
therefore no expansion of volume occurred (constant volume). We can also prove this using the
first law of a closed system formula: dE
/
dt
=
Q
−
W
+
m
1
(
h
1
+(
v
1
2
/
2
)+
g
1
z
1...
)−
m
(
h
2
+(
v
2
2
/
2
)+
g
2
z
2...
)
dE/dt= change of internal energy over time Q= internal heat W= work
m= mass of the system
h= enthalpy
v= velocity
g= gravitational constant
z= height
For experiment 1 of this lab, all but Q and h cancel out which in turn leaves us with Q
=
h
2
−
h
1
.
This formula, for an ideal gas becomes Q
=
Cv
(
T
2
−
T
1
)
. Experiment 2
Calculating the average specific heat ratios yielded 1.331, 1.257, 1.291, and 0.987 for 30
KPa, 40 KPa, 50 KPa, and 60 KPa respectively. The given reference value for the specific heat
ratio of air at room temperature was 1.401 [1]. Figure 8 shows the variation of the specific heat
ratio given different ambient temperatures [1]:
Your preview ends here
Eager to read complete document? Join bartleby learn and gain access to the full version
- Access to all documents
- Unlimited textbook solutions
- 24/7 expert homework help
Figure 10: Relationship Between Specific Heat Ratio and Temperature of Ambient Air [1]
The lowest deviation was found at 30 KPa with a 5.00% offset compared to 10.28% at 40 KPa,
7.85% at 50 KPa, and 29.55% at 60 KPa. This is to be expected as our point of reference remains
the same while the system experiences changes in pressure which, from figure 4, we see is the
driving variable for the specific heat capacity ratio. The offsets can also be explained by the
increase in intermolecular activity as the pressure increases [1]. As the pressure increases, the
compressibility factor will vary further from ideal gas behaviors and thus higher offsets are
expected at higher pressures. Despite this, the offsets are minor and the pressures are still at low
enough levels to consider the calculated values as valuable approximations.
In this lab, no heat is added or removed from the closed system, therefore this process is
by definition adiabatic. We consider the pressure vessel (see figure 1
) system to be isolated.
When the ball valve goes from open to closed, the temperature goes down and the gas expands
out of the vessel and into the lab room [1]. Because the system’s change is that of volume, we
use the Work= ∫
PdV to demonstrate that Work = P (pressure) * (V2-V1). By definition, an
adiabatic system is one which is isolated and in which energy is transferred through work [1]. No
heat is applied or taken from the system, t
herefore, the system is adiabatic. Experiment 3
The 𝘠
rev
(mean specific heat capacity ratio) result obtained in Experiment 2 for the 0.3 bar
trial using the formula from figure 7 was 1.331, whereas the result obtained from the experiment
3 using the formula from figure 11
was 1.360. There is a difference of 0.0310 units or 2.132%
from the first to the second result for the specific heat capacity ratios. We can assume the reason
for the lower results in experiment 2 is a bigger drop in temperature from the first to the second
result which was to be expected as the specific heat capacity ratio is a property of the gas under specific conditions, in which these
conditions were very similar. Experiment 2’s results had a 5.00% difference from the theoretical
value of 1.401, whereas experiment 3 had a 2.93% difference. The offset between the two
experiments is likely due the fluctuations in initial, intermediate, and final pressures as well as
air leaks or issues with the sensors. The offset from the theoretical value is likely largely due to
the differences in the ambient conditions used for the experiment versus the theoretical value.
A reversible process is one during which the initial and final conditions of the system end
up the same (volume, internal energy, etc.) all while not affecting the surrounding environment.
To help us explain this, we considered the initial state values to have been 0 bars of pressure,
ambient temperature and a rigid container (we do not have the dimensions of the Perfect Gas
Expansion Apparatus but the rigidity of the vessel implies that initial volume= final volume).
Furthermore, we considered the state during which the apparatus was filled with air at 0.3 bars to
be the intermediary state
. We considered the final state to be that of the vessel after having fully
opened the ball valve and closed it again. The final state therefore contained the values of 0 bars
of pressure, ambient temperature and the same volume as the initial volume (
see figure 6
). We
can also prove this using the first law of a closed system equation: dE
/
dt
=
Q
−
W
+
m
1
(
h
1
+(
v
1
2
/
2
)+
g
1
z
1...
)−
m
(
h
2
+(
v
2
2
/
2
)+
g
2
z
2...
)
dE/dt= change of internal energy over time Q= internal heat
W= work
m= mass of the system
h= enthalpy
v= velocity
g= gravitational constant
z= height
We cancel out the change of internal energy as the system is in a steady state; no work is done
(volume remains constant); the mass of the system remains the same, and all other energies
cancel out. This leaves us with the formula Q
=
h
2
−
h
1
. This formula, for an ideal gas becomes
Q
=
Cv
(
T
2
−
T
1
)
. In this case, because the initial temperatures are both the ambient temperature,
Q= 0. This demonstrates equilibrium in the initial and final states. Although expansion of a gas is never truly reversible, due to adiabatic expansion against
atmospheric pressure possibly causing a change in entropy, experiment 3 shows that the results
of the irreversible process are are similar enough to the reversible process results that one can
satisfactorily conclude that it is also a reversible process [1].
CONCLUSION
Experiment 1:
●
Brief depressurization of the pressure vessel causing changes in temperature and pressure (in vessel).
●
The temperature stabilizes when it reaches the ambient temperature (23.4
). This ℃
follows the second law of thermodynamics.
●
In this experiment, the vessel was rigid, so there was no change in volume.
●
Therefore, in the first law of thermodynamics, we are left with Q
=
Cv
(
T
2
−
T
1
)
.
Your preview ends here
Eager to read complete document? Join bartleby learn and gain access to the full version
- Access to all documents
- Unlimited textbook solutions
- 24/7 expert homework help
Experiment 2:
●
From Figure 4, we see pressure is the driving variable for the specific heat capacity ratio.
●
Offsets explained by increase in molecular activity when the pressure increases.
●
Higher offsets are expected at higher pressures.
●
Pressure vessel is isolated.
●
The ball valve goes from open to close causing the temperature to go down and the gas to
expand out of the vessel.
●
There is a change in volume, so W=
P (pressure) * (V2-V1).
●
In this system, there is no heat change, it is therefore adiabatic.
Experiment 3:
.
●
We assume the reason for lower results is a bigger drop in temperature.
●
Experiment 2’s results had a 5.00% difference from 1.401.
●
Experiment 3 had a 2.93% difference. ●
The offset between the two is likely due to fluctuations in pressures and air leaks or issues with sensors.
●
The offset from the theoretical value is likely due to differences in the ambient conditions
used for the experiment vs the theoretical value.
●
The formula becomes Q
=
Cv
(
T
2
−
T
1
)
but in this case, Q=0. This demonstrates equilibrium. in the initial and final states.
●
Due to adiabatic expansion against atmospheric pressure, experiment 3 shows that the results of the irreversible process are are similar enough to the reversible process results that one can satisfactorily conclude that it is also a reversible process.
SOURCES OF MEASUREMENT ERRORS
One of the main sources of error could be attributed to the fluctuations of the pressure
and temperature displayed by the hardware. Due to having a time limit, the values recorded may
not have been fully stabilized before proceeding with further steps. To compound that, the ball
valve may have been slowly releasing pressure due to imperfect sealing, thus not only making
stabilizing difficult, but impossible.
Even if no relative percentage error was mentioned on the machine used, it is known that
for those types of experiment, there is always a relative error percentage. Since this was a
modern lab with computer technology, it is assumed that the relative error percentage would be
small. Nevertheless, due to significant figures not always being carried over, the final results
may have significant errors.
Finally, it was not possible to get the same pressure values for the different trials, which
may have led to results being a little less accurate.
REFERENCES
[1]
Department of Mechanical, Industrial and Aerospace Engineering. THERMODYNAMICS II MECH 351 LABORATORY MANUAL (WINTER 2024). CONCORDIA UNIVERSITY; Engineering and Computer Science
[2]
K. M. Tenny and J. S. Cooper, “Ideal Gas Behavior,” in StatPearls
, Treasure Island (FL):
StatPearls Publishing, 2024. Accessed: Jan. 26, 2024. [Online]. Available: http://www.ncbi.nlm.nih.gov/books/NBK441936/
[3]
“Specific Heats.” Accessed: Jan. 30, 2024. [Online]. Available: https://www.grc.nasa.gov/www/k-12/airplane/specheat.html
Your preview ends here
Eager to read complete document? Join bartleby learn and gain access to the full version
- Access to all documents
- Unlimited textbook solutions
- 24/7 expert homework help
Related Documents
Related Questions
Subject: Mechanical Measurements
Do not copy online solutions. It's different value
arrow_forward
Part III Capstone Problem
Interactive Physics - [Lab7Part3.IP]
Eile Edit World View Object Define Measure Script Window Help
Run StoplI Reset
圖|& 品凸?
Time
Length of Spring 22
6.00
dx
Center of Mass of Rectangle 2
5.000
Tension of Rope 3
Jain@
IFI
... N
ot
rot
***lad
Split
4.000
Velocity of Center of Mass of Rectangle 2
Vx Vx
V Vy
MM
Ve
- m/s
m/s
3.00
*** m/s
Vo
..* lad/s
2 00
Center of Mass of Rectangle 1
1.000
tol
rot
*.* rad
EVelocity of Center of Mass of Rectangle 1
Vx Vx
VVy
M
0.000
-m/s
w 30
m/s
w..
MI
Ve
母100
*** m/s
Vo
... rad/s
+
EAcceleration of Center of Mass of Rectangle 1
Ax Ax
A Ay
AUJAI
Ae
--- m/s^2
... m/s^2
-- m/s^2
.-- rad/s^2
3.00
Aø
Mass M1 = 2.25 kg is at the end of a rope that is 2.00 m in length. The initial angle with
respect to the vertical is 60.0° and M1 is initially at rest. Mass M1 is released and strikes M2
= 4.50 kg exactly horizontally. The collision is elastic. After collision, mass M2 is moving on
a frictionless surface, but runs into a rough patch 2.00…
arrow_forward
Subject: Mechanical Measurements
Do not copy other online answers
arrow_forward
mylabmastering.pearson.com
Chapter 12 - Lecture Notes.pptx: (MAE 272-01) (SP25) DY...
P Pearson MyLab and Mastering
Scores
arrow_forward
Chapter 12 - Lecture Notes.pptx: (MAE 272-01) (SP25) DY...
Scores
arrow_forward
K
mylabmastering.pearson.com
Chapter 12 - Lecture Notes.pptx: (MAE 272-01) (SP25) DY...
P Pearson MyLab and Mastering
Mastering Engineering
Back to my courses
Course Home
Scores
Course Home
arrow_forward
Answer Q1 and Q2 (thermofluids)
arrow_forward
Not Ai generated please show all steps
arrow_forward
https://drive.google.com/file/d/1X0Sk9U2pT7lwJ9IB--kLkGngHm46SywH/view?usp=sharing
arrow_forward
Geochemical Box Models - please use same terminology found in question
Consider an element X exchanging between two geochemical reservoirs A and B. Let MA and MB be the masses of X in reservoirs A and B, respectively; let tA and tB be the residence times of X in reservoirs A and B, respectively. Further let M = MA + MB be the total mass of X in the two reservoirs combined.
Consider a situation where additional mass M' is injected into reservoir A at time t=0 increasing the total amount of element X in the system from M0 to M1, with no further injection at later times; further assume that tA >> tB, that the total mass in the altered system is M1 = M0 + M', and that M0 << M'. Give an expression for MB(t) as a function of M1, tA, tB, and t. What is the characteristic time for MB to approach steady state? What is the characteristic time for MA to approach steady state?
arrow_forward
otoring:
MITO
R
(Motor)
=
VAPPL
Torque [N*m]
60
T 0₁ V
200 rad/s
W₁
Viscous Friction
b₁
N₁
J₁
2
N₂
b₂
Viscous Friction
J₂
VMOTOR K, W₁
T=K₁ i
0₂
ta from the steady state dynamometer test and the given values: J₁
², b₁
2N, b2 = 12N, N₁ = 50 teeth, N₂ = 100 teeth (R should
rad'
arrow_forward
K
mylabmastering.pearson.com
Chapter 12 - Lecture Notes.pptx: (MAE 272-01) (SP25) DY...
P Pearson MyLab and Mastering
Mastering Engineering
Back to my courses
Course Home
Scores
Course Home
arrow_forward
Pearson eText
Study Area
mylabmastering.pearson.com
Access Pearson
P Pearson MyLab and Mastering
Problem 14.78
P Course Home
b Answered: HW_02.pdf EE 213-01 > Assignments HW_#...
2 of 8
Document Sharing
User Settings
The spring has a stiffness k = 200 N/m and an
unstretched length of 0.5 m. It is attached to the 4.6-kg
smooth collar and the collar is released from rest at A.
Neglect the size of the collar. (Figure 1)
Part A
Determine the speed of the collar when it reaches B.
Express your answer to three significant figures and include the appropriate units.
Figure
1 of 1
με
VB = Value
Units
Submit
Request Answer
Provide Feedback
?
Review
Next >
arrow_forward
SEE MORE QUESTIONS
Recommended textbooks for you
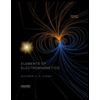
Elements Of Electromagnetics
Mechanical Engineering
ISBN:9780190698614
Author:Sadiku, Matthew N. O.
Publisher:Oxford University Press
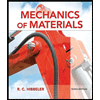
Mechanics of Materials (10th Edition)
Mechanical Engineering
ISBN:9780134319650
Author:Russell C. Hibbeler
Publisher:PEARSON
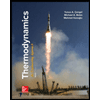
Thermodynamics: An Engineering Approach
Mechanical Engineering
ISBN:9781259822674
Author:Yunus A. Cengel Dr., Michael A. Boles
Publisher:McGraw-Hill Education
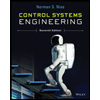
Control Systems Engineering
Mechanical Engineering
ISBN:9781118170519
Author:Norman S. Nise
Publisher:WILEY
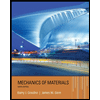
Mechanics of Materials (MindTap Course List)
Mechanical Engineering
ISBN:9781337093347
Author:Barry J. Goodno, James M. Gere
Publisher:Cengage Learning
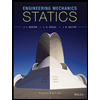
Engineering Mechanics: Statics
Mechanical Engineering
ISBN:9781118807330
Author:James L. Meriam, L. G. Kraige, J. N. Bolton
Publisher:WILEY
Related Questions
- Subject: Mechanical Measurements Do not copy online solutions. It's different valuearrow_forwardPart III Capstone Problem Interactive Physics - [Lab7Part3.IP] Eile Edit World View Object Define Measure Script Window Help Run StoplI Reset 圖|& 品凸? Time Length of Spring 22 6.00 dx Center of Mass of Rectangle 2 5.000 Tension of Rope 3 Jain@ IFI ... N ot rot ***lad Split 4.000 Velocity of Center of Mass of Rectangle 2 Vx Vx V Vy MM Ve - m/s m/s 3.00 *** m/s Vo ..* lad/s 2 00 Center of Mass of Rectangle 1 1.000 tol rot *.* rad EVelocity of Center of Mass of Rectangle 1 Vx Vx VVy M 0.000 -m/s w 30 m/s w.. MI Ve 母100 *** m/s Vo ... rad/s + EAcceleration of Center of Mass of Rectangle 1 Ax Ax A Ay AUJAI Ae --- m/s^2 ... m/s^2 -- m/s^2 .-- rad/s^2 3.00 Aø Mass M1 = 2.25 kg is at the end of a rope that is 2.00 m in length. The initial angle with respect to the vertical is 60.0° and M1 is initially at rest. Mass M1 is released and strikes M2 = 4.50 kg exactly horizontally. The collision is elastic. After collision, mass M2 is moving on a frictionless surface, but runs into a rough patch 2.00…arrow_forwardSubject: Mechanical Measurements Do not copy other online answersarrow_forward
- mylabmastering.pearson.com Chapter 12 - Lecture Notes.pptx: (MAE 272-01) (SP25) DY... P Pearson MyLab and Mastering Scoresarrow_forwardChapter 12 - Lecture Notes.pptx: (MAE 272-01) (SP25) DY... Scoresarrow_forwardK mylabmastering.pearson.com Chapter 12 - Lecture Notes.pptx: (MAE 272-01) (SP25) DY... P Pearson MyLab and Mastering Mastering Engineering Back to my courses Course Home Scores Course Homearrow_forward
- Geochemical Box Models - please use same terminology found in question Consider an element X exchanging between two geochemical reservoirs A and B. Let MA and MB be the masses of X in reservoirs A and B, respectively; let tA and tB be the residence times of X in reservoirs A and B, respectively. Further let M = MA + MB be the total mass of X in the two reservoirs combined. Consider a situation where additional mass M' is injected into reservoir A at time t=0 increasing the total amount of element X in the system from M0 to M1, with no further injection at later times; further assume that tA >> tB, that the total mass in the altered system is M1 = M0 + M', and that M0 << M'. Give an expression for MB(t) as a function of M1, tA, tB, and t. What is the characteristic time for MB to approach steady state? What is the characteristic time for MA to approach steady state?arrow_forwardotoring: MITO R (Motor) = VAPPL Torque [N*m] 60 T 0₁ V 200 rad/s W₁ Viscous Friction b₁ N₁ J₁ 2 N₂ b₂ Viscous Friction J₂ VMOTOR K, W₁ T=K₁ i 0₂ ta from the steady state dynamometer test and the given values: J₁ ², b₁ 2N, b2 = 12N, N₁ = 50 teeth, N₂ = 100 teeth (R should rad'arrow_forwardK mylabmastering.pearson.com Chapter 12 - Lecture Notes.pptx: (MAE 272-01) (SP25) DY... P Pearson MyLab and Mastering Mastering Engineering Back to my courses Course Home Scores Course Homearrow_forwardarrow_back_iosSEE MORE QUESTIONSarrow_forward_ios
Recommended textbooks for you
- Elements Of ElectromagneticsMechanical EngineeringISBN:9780190698614Author:Sadiku, Matthew N. O.Publisher:Oxford University PressMechanics of Materials (10th Edition)Mechanical EngineeringISBN:9780134319650Author:Russell C. HibbelerPublisher:PEARSONThermodynamics: An Engineering ApproachMechanical EngineeringISBN:9781259822674Author:Yunus A. Cengel Dr., Michael A. BolesPublisher:McGraw-Hill Education
- Control Systems EngineeringMechanical EngineeringISBN:9781118170519Author:Norman S. NisePublisher:WILEYMechanics of Materials (MindTap Course List)Mechanical EngineeringISBN:9781337093347Author:Barry J. Goodno, James M. GerePublisher:Cengage LearningEngineering Mechanics: StaticsMechanical EngineeringISBN:9781118807330Author:James L. Meriam, L. G. Kraige, J. N. BoltonPublisher:WILEY
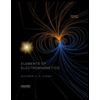
Elements Of Electromagnetics
Mechanical Engineering
ISBN:9780190698614
Author:Sadiku, Matthew N. O.
Publisher:Oxford University Press
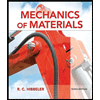
Mechanics of Materials (10th Edition)
Mechanical Engineering
ISBN:9780134319650
Author:Russell C. Hibbeler
Publisher:PEARSON
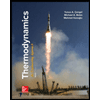
Thermodynamics: An Engineering Approach
Mechanical Engineering
ISBN:9781259822674
Author:Yunus A. Cengel Dr., Michael A. Boles
Publisher:McGraw-Hill Education
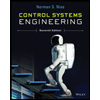
Control Systems Engineering
Mechanical Engineering
ISBN:9781118170519
Author:Norman S. Nise
Publisher:WILEY
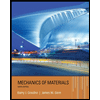
Mechanics of Materials (MindTap Course List)
Mechanical Engineering
ISBN:9781337093347
Author:Barry J. Goodno, James M. Gere
Publisher:Cengage Learning
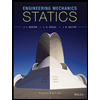
Engineering Mechanics: Statics
Mechanical Engineering
ISBN:9781118807330
Author:James L. Meriam, L. G. Kraige, J. N. Bolton
Publisher:WILEY