Laboratory #1 - Supplemental Guide (1)
pdf
keyboard_arrow_up
School
Palo Alto College *
*We aren’t endorsed by this school
Course
4312
Subject
Mechanical Engineering
Date
Apr 3, 2024
Type
Pages
4
Uploaded by LieutenantBookOpossum46
ME 4312 - Thermal and Fluids Laboratory | Page 1
of 4
The University of Texas at San Antonio (UTSA) Klesse College of Engineering and Integrated Design
Department of Mechanical Engineering ME 4312 - Thermal and Fluids Laboratory Laboratory Assignment #
1
: Analysis of Pumps in Series and Parallel Configurations Supplemental Guide
Experimental Procedures:
The descriptions presented below are supplemental of the descriptions presented in the condensed manual. The switch in Figure 1 is the mains isolator switch. There are two of these switches. The one on the left of the apparatus powers pump 1, as well as the pressure sensors and readouts. This switch should be on for the duration of the lab. The switch on the right of the apparatus powers pump 2 and should only be on when testing series and parallel pump configurations. Figure 1.
Mains isolator switch. Before starting any pump, make sure to zero out the pressure transducers (Figure 2). There is also a button to zero out the torque input on both motors. These should also be pressed before starting the motors attached to the pumps. To start the motor, press the green button (at left), and stop it with the red button (at right) shown in Figure 3. The black knob controls motor rotational speed in RPM and is very sensitive. For all tests, you need to run the motors at 3,000 RPM (or as close as 3,000 RPM as possible). If you get within +/- 10 rpm you can record your results as long as you note your exact measurement of rotational speed in RPM. Figure 2.
Zero out pressure transducers. Figure 3.
Motor controls. Before actually running each experiment, you will need to turn the speed controls on the motors you are using for the current test to max RPM. You will look at the pressures in the system to determine if the system is properly bled. On the two motor control panels, you can find the expected pressure readings for each pump configuration (see Figure 4). The actual pressures should match these values (see Figure 5); if they don’t, let your TA know so they can prop
erly bleed the system.
ME 4312 - Thermal and Fluids Laboratory | Page 2
of 4
Figure 4.
Expected pressure readings. Figure 5.
Actual pressure readings. The outlet valve in Figure 6 should be handled slowly and with both hands. It is PVC on PVC and does have a tendency to bind because of this. For the single, series, and parallel tests this valve should be closed in 0.1 bar increments (read as pressure P4). This should be done up to 1.5 bar (again, read as pressure P4). DO NOT EXCEED 1.5 BAR WITH THE OUTLET VALVE! Figure 6.
Outlet valve. Due to inappropriate handling of equipment by students in the past, part of the inlet valve for pump 2 broke off. This part was responsible for limiting how far the valve can be opened. To avoid further damage to the valve, stop opening the valve when the threads on the shaft are flush with the end of the pipe, as shown in Figure 7. Do not do as in Figure 8. The inlet valves require many turns to fully open or close. Figure 7.
Good way to open valve. Figure 8.
Bad way to open valve.
ME 4312 - Thermal and Fluids Laboratory | Page 3
of 4
Theoretical Data:
Theoretical formulations and information can be found in: (1) the lab manual, and (2) your notes from Measurements & Instrumentation, Fluid Mechanics, and Thermodynamics I (review the course schedule for information on textbook chapters). An additional source of information is presented below: https://www.youtube.com/watch?v=iDRoSxZKKz8 Summary of Findings:
The following is a checklist of what should appear in the “data analysis”
section of your report. None of this information is new or different from what was asked in the manual. It is simply included here in a list with some clarification based on common questions. Your “data analysis”
section should be written in report form, not as responses to the checklist. The checklist should be used only to guide your discussion. Steps: 1.
Table similar to Table 2 on page 39 (last page on PDF file) of the lab manual for each of the following:
a.
Single pump
b.
Parallel pumps
c.
Series pumps
a.
Data for ΔP
1
, P
2
, P
3
, P
4
are provided for you.
b.
Data for pump mechanical power input, W, (and for the second pump where applicable) are provided for you.
For two pumps, you must calculate the total power input as the sum of the individual power inputs. Make sure to
avoid mixing nomenclature (W
2
is the hydraulic power of the pump).
c.
Data for pump rotational speed (N) is provided. Note that although the speed was set to 3,000 RPM (revolutions
per min), small deviations were recorded.
d.
All other values should be calculated using equations on pages 25 –
28 of the lab manual.
e.
As stated in the video, make sure to take a look at Venturi dimensions on page 15 of the lab manual (page 13 on
the PDF file) when determining flow rates.
f.
PAY CLOSE ATTENTION TO UNITS!
2.
Summary tables for each of the tables created in Step 1 that will help you see the relationships and compare/contrast
the different pump configurations.
a.
In the summary tables, include flow rate, efficiency, total head, and total input power for 3 flow rates
(columns should appear in this order)
b.
The 3 flow rates should be the following:
i.
minimum flow rate.
ii.
flow rate at max efficiency (if the max efficiency is at an endpoint, use an approximate midpoint for
the 2
nd
flow rate.)
iii.
maximum flow rate.
3.
For each pump configuration, construct a single
plot of efficiency, total power input, and total head against flow
rate.
a.
Flow rate will be on the x-axis.
b.
Axes should appear as shown in the example plot below.
c.
Plot labels should match your table labels.
d.
For more information on how to create secondary axis on Excel plots, see the following link:
https://support.microsoft.com/en-us/topic/add-or-remove-a-secondary-axis-in-a-chart-in-excel-91da1e2f-5db1-
41e9-8908-e1a2e14dd5a9
Your preview ends here
Eager to read complete document? Join bartleby learn and gain access to the full version
- Access to all documents
- Unlimited textbook solutions
- 24/7 expert homework help
ME 4312 - Thermal and Fluids Laboratory | Page 4
of 4
4.
Discuss tables and plots by answering the following questions in your discussion:
a.
For the single pump test, describe the relationship between efficiency, head, and flow rate.
b.
What is the best efficiency for the single pump?
c.
Compare the results for the series and parallel pump tests against the single pump test at the same pump
rotational speed.
d.
Use your summary tables to compare the different tests. For example, compare the flow rates at which the
maximum efficiency occurs.
e.
What can you observe about flow rate, total head, and efficiency among the different tests?
The efficiency of large industrial pumps is normally about 75%. Why is the efficiency of the pumps in this experiment different from that of a large industrial pump? Discuss specific reasons.
Related Documents
Related Questions
FLUID POWER SYSTEMS
arrow_forward
Name
Section 5-2: Line Diagrams-Signals,
Decisions, and Actions
In the following application, a temperature switch controls a heating contactor and a flow switch is used to
ensure there is enough air flow. If there is not enough air flow, an alarm is sounded. Complete the required
information.
1. List all the signal devices in the circuit.
2. List all the action devices in the circuit.
3. List the decision part of the circuit that automatically sounds the alarm if there is a problem.
4. When the heating element is on during normal operation, is the flow switch open or closed?
CIRCULATING
2
L1
FAN
TEMPERATURE
SWITCH
TR
HEATING
ELEMENTS
FLOW
SWITCH
-HOT AIR
PADDLE
AIR FILTER
NORMALLY CLOSED
FLOW SWITCH
65
ALARM
(SOUNDS IF NO FLOW FOR
15 SECONDS OR MORE)
Date
HEATING
CONTACTOR
TR
ON-DELAY
TIMER
SUPPLY AIR
COLD AIR
(3) TIME SET= 15 SEC
© 2014 American Technical Publishers, Inc.
All rights reserved
arrow_forward
can you please find the solution for this?
arrow_forward
I need part 7 answered pertaining to the print and instructions.
arrow_forward
What does it mean to shift the patient into the treatment position? Could you describe the coordinate system used to shift the patient into treatment position.
arrow_forward
Circuit Problem and Description: Using the given components, design a pneumatic circuit
which will operate a double acting cylinder (A) from any one of two identical valves. The
double acting cylinder will move out when either push button (M1) or (M2) is pressed, or
when they are pressed at the same time. When the buttons are released, the cylinder will
return to the initial position.
Materials:
Part #
Component Description
Quantity
SAI 2026 Double acting cylinder
SAI 2015 Normally closed 3/2 way valves operated by push button
SAI 2023 Pneumatically piloted 5/2 way monostable valve
SAI 2007
2
1
"OR" logic function valve
1
Teske
Circuit Problem and Description: Using the given components, design a pneumatic circuit
which will correctly and safely operate this machine control application. WWith this circuit, it
must be possible to regulate the delay of a double acting cylinder (A). The cylinder will be
driven by a valve, actuated by two pneumatic push buttons. One of the two push buttons…
arrow_forward
III.Question and Answer
1.Understand the given Physical process control diagram
and explain the working of the system.
Actual
level
Reference
Controller
Measurement
level
System
H
Pump
Tank
Liquid Level Control System
Electronics Coach
2. Understand the given Industrial process control system
and convert it in to Block diagram (draw neatly)
4-20 mA signal
FC
4-20 mA signal
FY
FT
3-15 PSI signal
FV
Pump
Pipe
InstrumentationTools.com
arrow_forward
Circuit Design - aircraft system application
Draw the circuit of the flap and aileron actuation system of a small aircraft.
The hydraulic system uses a variable engine driven pump as power supply. The
pump takes flow from a reservoir. The circuit is protected against overload by a
pressure relief valve.
The speed and the direction of rotation of the flap motor are controlled using
an electrically operated proportional valve. The aileron actuator contains a
double acting cylinder, which is also controlled by an electrically operated
proportional valve. Draw the circuit using ISO standard!
Use the following symbol for the electrically operated proportional valve
THEL
arrow_forward
I need parts 1, 2, and 3, answered pertaining to the print and instructions.
arrow_forward
13) Write a program to implement the process illustrated in the figure below. The sequence
of operation is to be as follows:
• Normally open start and normally closed stop pushbuttons are used to start and stop the
process.
• When the start button is pressed, solenoid A energizes to start filling the tank.
• As the tank fills, the empty level sensor switch closes.
• When the tank is full, the full level sensor switch closes.
• Solenoid A is de-energized.
• The agitate motor starts automatically and runs for 3 min to mix the liquid.
15
• When the agitate motor stops, solenoid B is energized to empty the tank.
• When the tank is completely empty, the empty sensor switch opens to de-energize
solenoid B
• The start button is pressed to repeat the sequence.
SOL A
Motor
Full
sensor
switch
Empty
sensor
switch
+SOL B
Start/stop
control station
arrow_forward
What is the required diameter in meters of a cylindrical tank which has a length of 3 meters used for oil storage that will supply the engine for 5 days having a fuel consumption of 60Kg/hour at 27 degrees
API? Please Answer # 9. If you can answer # 10 it will be appreciated much and rated high. Thanks!
arrow_forward
Chapter 18 Controlling a Pneumatic System
451
To circuit section
operated at maximum
workstation pressure
Motor operated at
a pressure below the
workstation setting
Goodheart-Willcox Publisher
Figure 18-12. A pressure lower than that selected as the workstation pressure may be easily provided by the addition of a
second pressure regulator.
arrow_forward
Instrumentation & Measurements
This homework measures your capability to design/analyze various components/variables of ameasurement system based on what you have studied.
Question 1 Attached.
arrow_forward
use red parameters
arrow_forward
Chapter 18 Controlling a Preumatic System
461
Timing volume reservoir
Goodheart-Willcox Publisher
Figure 18-31, Timing-volume reservoirs allow ontrol of the sequence of a circuit using pilot-activated directional control valves.
arrow_forward
SEE MORE QUESTIONS
Recommended textbooks for you
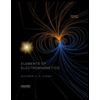
Elements Of Electromagnetics
Mechanical Engineering
ISBN:9780190698614
Author:Sadiku, Matthew N. O.
Publisher:Oxford University Press
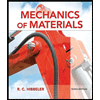
Mechanics of Materials (10th Edition)
Mechanical Engineering
ISBN:9780134319650
Author:Russell C. Hibbeler
Publisher:PEARSON
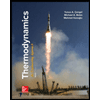
Thermodynamics: An Engineering Approach
Mechanical Engineering
ISBN:9781259822674
Author:Yunus A. Cengel Dr., Michael A. Boles
Publisher:McGraw-Hill Education
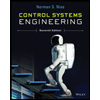
Control Systems Engineering
Mechanical Engineering
ISBN:9781118170519
Author:Norman S. Nise
Publisher:WILEY
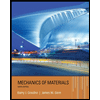
Mechanics of Materials (MindTap Course List)
Mechanical Engineering
ISBN:9781337093347
Author:Barry J. Goodno, James M. Gere
Publisher:Cengage Learning
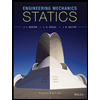
Engineering Mechanics: Statics
Mechanical Engineering
ISBN:9781118807330
Author:James L. Meriam, L. G. Kraige, J. N. Bolton
Publisher:WILEY
Related Questions
- FLUID POWER SYSTEMSarrow_forwardName Section 5-2: Line Diagrams-Signals, Decisions, and Actions In the following application, a temperature switch controls a heating contactor and a flow switch is used to ensure there is enough air flow. If there is not enough air flow, an alarm is sounded. Complete the required information. 1. List all the signal devices in the circuit. 2. List all the action devices in the circuit. 3. List the decision part of the circuit that automatically sounds the alarm if there is a problem. 4. When the heating element is on during normal operation, is the flow switch open or closed? CIRCULATING 2 L1 FAN TEMPERATURE SWITCH TR HEATING ELEMENTS FLOW SWITCH -HOT AIR PADDLE AIR FILTER NORMALLY CLOSED FLOW SWITCH 65 ALARM (SOUNDS IF NO FLOW FOR 15 SECONDS OR MORE) Date HEATING CONTACTOR TR ON-DELAY TIMER SUPPLY AIR COLD AIR (3) TIME SET= 15 SEC © 2014 American Technical Publishers, Inc. All rights reservedarrow_forwardcan you please find the solution for this?arrow_forward
- I need part 7 answered pertaining to the print and instructions.arrow_forwardWhat does it mean to shift the patient into the treatment position? Could you describe the coordinate system used to shift the patient into treatment position.arrow_forwardCircuit Problem and Description: Using the given components, design a pneumatic circuit which will operate a double acting cylinder (A) from any one of two identical valves. The double acting cylinder will move out when either push button (M1) or (M2) is pressed, or when they are pressed at the same time. When the buttons are released, the cylinder will return to the initial position. Materials: Part # Component Description Quantity SAI 2026 Double acting cylinder SAI 2015 Normally closed 3/2 way valves operated by push button SAI 2023 Pneumatically piloted 5/2 way monostable valve SAI 2007 2 1 "OR" logic function valve 1 Teske Circuit Problem and Description: Using the given components, design a pneumatic circuit which will correctly and safely operate this machine control application. WWith this circuit, it must be possible to regulate the delay of a double acting cylinder (A). The cylinder will be driven by a valve, actuated by two pneumatic push buttons. One of the two push buttons…arrow_forward
- III.Question and Answer 1.Understand the given Physical process control diagram and explain the working of the system. Actual level Reference Controller Measurement level System H Pump Tank Liquid Level Control System Electronics Coach 2. Understand the given Industrial process control system and convert it in to Block diagram (draw neatly) 4-20 mA signal FC 4-20 mA signal FY FT 3-15 PSI signal FV Pump Pipe InstrumentationTools.comarrow_forwardCircuit Design - aircraft system application Draw the circuit of the flap and aileron actuation system of a small aircraft. The hydraulic system uses a variable engine driven pump as power supply. The pump takes flow from a reservoir. The circuit is protected against overload by a pressure relief valve. The speed and the direction of rotation of the flap motor are controlled using an electrically operated proportional valve. The aileron actuator contains a double acting cylinder, which is also controlled by an electrically operated proportional valve. Draw the circuit using ISO standard! Use the following symbol for the electrically operated proportional valve THELarrow_forwardI need parts 1, 2, and 3, answered pertaining to the print and instructions.arrow_forward
- 13) Write a program to implement the process illustrated in the figure below. The sequence of operation is to be as follows: • Normally open start and normally closed stop pushbuttons are used to start and stop the process. • When the start button is pressed, solenoid A energizes to start filling the tank. • As the tank fills, the empty level sensor switch closes. • When the tank is full, the full level sensor switch closes. • Solenoid A is de-energized. • The agitate motor starts automatically and runs for 3 min to mix the liquid. 15 • When the agitate motor stops, solenoid B is energized to empty the tank. • When the tank is completely empty, the empty sensor switch opens to de-energize solenoid B • The start button is pressed to repeat the sequence. SOL A Motor Full sensor switch Empty sensor switch +SOL B Start/stop control stationarrow_forwardWhat is the required diameter in meters of a cylindrical tank which has a length of 3 meters used for oil storage that will supply the engine for 5 days having a fuel consumption of 60Kg/hour at 27 degrees API? Please Answer # 9. If you can answer # 10 it will be appreciated much and rated high. Thanks!arrow_forwardChapter 18 Controlling a Pneumatic System 451 To circuit section operated at maximum workstation pressure Motor operated at a pressure below the workstation setting Goodheart-Willcox Publisher Figure 18-12. A pressure lower than that selected as the workstation pressure may be easily provided by the addition of a second pressure regulator.arrow_forward
arrow_back_ios
SEE MORE QUESTIONS
arrow_forward_ios
Recommended textbooks for you
- Elements Of ElectromagneticsMechanical EngineeringISBN:9780190698614Author:Sadiku, Matthew N. O.Publisher:Oxford University PressMechanics of Materials (10th Edition)Mechanical EngineeringISBN:9780134319650Author:Russell C. HibbelerPublisher:PEARSONThermodynamics: An Engineering ApproachMechanical EngineeringISBN:9781259822674Author:Yunus A. Cengel Dr., Michael A. BolesPublisher:McGraw-Hill Education
- Control Systems EngineeringMechanical EngineeringISBN:9781118170519Author:Norman S. NisePublisher:WILEYMechanics of Materials (MindTap Course List)Mechanical EngineeringISBN:9781337093347Author:Barry J. Goodno, James M. GerePublisher:Cengage LearningEngineering Mechanics: StaticsMechanical EngineeringISBN:9781118807330Author:James L. Meriam, L. G. Kraige, J. N. BoltonPublisher:WILEY
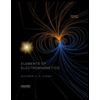
Elements Of Electromagnetics
Mechanical Engineering
ISBN:9780190698614
Author:Sadiku, Matthew N. O.
Publisher:Oxford University Press
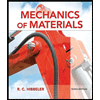
Mechanics of Materials (10th Edition)
Mechanical Engineering
ISBN:9780134319650
Author:Russell C. Hibbeler
Publisher:PEARSON
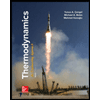
Thermodynamics: An Engineering Approach
Mechanical Engineering
ISBN:9781259822674
Author:Yunus A. Cengel Dr., Michael A. Boles
Publisher:McGraw-Hill Education
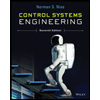
Control Systems Engineering
Mechanical Engineering
ISBN:9781118170519
Author:Norman S. Nise
Publisher:WILEY
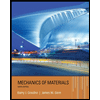
Mechanics of Materials (MindTap Course List)
Mechanical Engineering
ISBN:9781337093347
Author:Barry J. Goodno, James M. Gere
Publisher:Cengage Learning
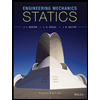
Engineering Mechanics: Statics
Mechanical Engineering
ISBN:9781118807330
Author:James L. Meriam, L. G. Kraige, J. N. Bolton
Publisher:WILEY