Laboratory #3 - Manual (1)
pdf
keyboard_arrow_up
School
Palo Alto College *
*We aren’t endorsed by this school
Course
4312
Subject
Mechanical Engineering
Date
Apr 3, 2024
Type
Pages
10
Uploaded by LieutenantBookOpossum46
ME 4312 - Thermal and Fluids Laboratory | Page 1
of 10
The University of Texas at San Antonio (UTSA) Klesse College of Engineering and Integrated Design Department of Mechanical Engineering ME 4312 - Thermal and Fluids Laboratory Laboratory Assignment #3 - Analysis of Two-Dimensional Airfoil Aerodynamics Manual and Supplementary Materials
The objective of this laboratory assignment is to determine the experimental and theoretical/simulation lift force (and the pressure and lift force coefficients) experienced by an airfoil (a National Advisory Committee for Aeronautics
, NACA 4415), that is subject to different free-stream wind speeds and angles of attack. For such purpose, a wind tunnel and a set of manometers installed on both the wind tunnel and a model NACA 4415 will be considered. In general, the two-dimensional aerodynamics of a body consist of three different forces: the lift force (which always acts perpendicular to the direction of the free stream flow), the drag force (which always acts in the direction of the free stream flow), and a moment force (torque), which acts clockwise or counterclockwise and with respect to a reference position on the airfoil (usually at the aerodynamic center). Each of these forces has two components: (1) a viscous component, and (2) a pressure-based component. On the one hand, the viscous component results from the shear stresses developed between the free-stream flow and the surface of the object, and require detailed descriptions of the near-wall velocity profile and the flow condition (e.g., laminar vs turbulent). On the other hand, the pressure component depends on the pressure distribution around the surface of the object. In this laboratory assignment, only the pressure component will be investigated. It is worth nothing that, viscous contributions to the lift force are usually small and, thus, often neglected. However, the viscous component is usually important when analyzing drag and moment forces. In this laboratory assignment, only the pressure component of the lift force will be analyzed for different free-stream flow speeds (Reynolds numbers) and angles of attack. Experimental Procedures:
The wind tunnel has two 8-tube manometers (16 tubes total) that are used to measure the pressure at different points along the surface of the NACA 4415 airfoil (Figure 1 shows one 8-tube manometer to measure pressure along the upper surface of the airfoil, the other 8-tube manometer is to measure pressure along the lower surface of the airfoil). Each tube has a black ring on it that can slide up and down. Use these rings to mark the baseline water level on each tube (when the airfoil is at an angle of attack of 0 degrees and the wind tunnel is turned off) to later measure pressure changes on the surface due to changes in flow speed or the angle of attack. The baseline water levels are shown in Figure 2. The water is dyed to make it easier to read, and the dye has a negligible effect on the water’s density. Figure 1.
Airfoil Manometers. Figure 2.
Slide Black Ring to Baseline Water Level. The angle of attack (AOA) is shown by a black arrow attached to the airfoil (Figures 3 and 4) and a protractor taped to the back window (Figure 4). The AOA is controlled by turning an orange handle located beneath the wind tunnel, as shown in Figure 5.
ME 4312 - Thermal and Fluids Laboratory | Page 2
of 10
Figure 3.
NACA 4415 Airfoil. Figure 4.
Protractor. Figure 5.
Orange Handle. The key on the control unit should be turned to RUN
(see Figure 6). The green button labeled FAN ENABLE
will turn on the wind tunnel when pressed. The red button above it will stop it. The black dial below the display controls fan speed, and the display shows the wind tunnel’s fan rotational speed in RPM. The rotational speed of the fan is NOT an appropriate measurement of the wind tunnel’s wind speed and should not be referred to as such in your report. Instead, you need to determine the wind tunnel wind speed using the measurements of a Pitot tube that is installed in the upwind section of the tunnel (before the airfoil). The Pitot tube is connected to a “red” manometer located on top of the wind tunnel and shown in Figure 7. The manometer reads the dynamic pressure in the wind tunnel in “inches of water”. This pressure can later be converted into wind speed using equations presented later in this document (make sure to conduct appropriate review of how manometers work, using your lecture notes of the class fluid mechanics, and measurements and instrumentation). The wind speed (for a fixed fan speed in RPM) should always be recorded at an AOA of 0° to prevent blockage effects between the airfoil and the Pitot tube. Figure 6.
Wind Tunnel Controls. Figure 7.
Manometer to Measure Wind Speed (Pressure Readings Collected from Pitot Tube). Using the supplied ruler, measure the change in pressure (i.e., the change in water level with respect to the baseline water level marked with the black rings) for each of the 16 tubes (8 tubes are for measuring the change in pressure along the upper surface of the airfoil, and 8 tubes are for measuring the change in pressure along the lower surface of the airfoil, see figure 8). The manometer tubes start at #1 on the far right and increase from right to left to tube #16. Note that if the water is sucked up the tube it indicates a vacuum pressure (negative gage pressure). Once all 16 measurements are taken, change the AOA and repeat the measurements. The sixteen pressure measurements will be taken for 9 AOA (-15°, -10°, -6°, -4°, 0°, 4°, 6°, 10°, and 15°) values and at 4 different wind speeds (defined by the instructor in terms of the fan’s RPM) for a total of 576 measurements.
ME 4312 - Thermal and Fluids Laboratory | Page 3
of 10
Figure 8.
Measuring Manometer Water Levels. Airfoil Physical Dimensions Using a measuring device, record the chord length and airfoil width (wingspan, which is perpendicular to the chord length). From the leading edge of the airfoil, make precise measurements to each of the pressure sensing ports for both the upper and lower surfaces of the airfoil. Use a flexible tape for measuring the distances along the surface of the airfoil. Denote each dimension of the upper surface as X
U and subscript each of the X
U dimensions with respect to pressure sensing ports starting with the port nearest to the leading edge. X
U1
, X
U2
, X
U3
, and so on are examples of the subscripting process (see Figure 9 for example). The dimensions for the lower surface shall be identified the same as described for the upper surface except the symbol shall be X
L in place of X
U
. The table shown in page 6 reports the results of such measurements. Figure 9.
Example of Model Airfoil Dimensions (Upper Surface Only). Figure 10.
Pressure Port Distribution Along the Surface of the Airfoil.
Your preview ends here
Eager to read complete document? Join bartleby learn and gain access to the full version
- Access to all documents
- Unlimited textbook solutions
- 24/7 expert homework help
ME 4312 - Thermal and Fluids Laboratory | Page 4
of 10
Theoretical Analysis:
The airfoil used in this laboratory assignment is the NACA 4415 (normally used on the Lake Amphibious aircraft). The NACA 4415 is a very high lift airfoil designed to lift aircraft out of water quickly. Nomenclature
C Chord Lengh L Lift Force S Scale 𝐶𝐶
𝑀𝑀𝑀𝑀𝑀𝑀𝑀𝑀𝑀𝑀
Model Chrod Length 𝐶𝐶
𝑃𝑃𝑃𝑃𝑀𝑀𝑃𝑃𝑀𝑀𝑃𝑃𝑃𝑃𝑃𝑃𝑀𝑀
Prototype Chrod Length A Surface Area 𝐴𝐴
𝑀𝑀𝑀𝑀𝑀𝑀𝑀𝑀𝑀𝑀
Model Surface Area 𝐴𝐴
𝑃𝑃𝑃𝑃𝑀𝑀𝑃𝑃𝑀𝑀𝑃𝑃𝑃𝑃𝑃𝑃𝑀𝑀
Prototype Surface Area 𝐿𝐿
𝑀𝑀𝑀𝑀𝑀𝑀𝑀𝑀𝑀𝑀
Model Lift 𝐿𝐿
𝑃𝑃𝑃𝑃𝑀𝑀𝑃𝑃𝑀𝑀𝑃𝑃𝑃𝑃𝑃𝑃𝑀𝑀
Prototype Lift 𝑉𝑉
∞
Relative (Freestream) Wind Velocity 𝜌𝜌
∞
Frestream Fluid Density 𝐶𝐶
𝐿𝐿
Lift Coefficient 𝐶𝐶
𝑃𝑃
Pressure Coefficient 𝑃𝑃
Pressure at Evaluation Point 𝑃𝑃
∞
Freestream Pressure Due to the high cost of testing full size prototype airfoils in a wind tunnel, such testing is usually accomplished by use of scale models of the prototype. In scaling an airfoil, the parameters scaled from the prototype are its chord, its surface area, and its “lift force”. Figure 11 provides the basic dimensional nomenclature of the airfoil, i.e., the chord, the chord line, the mean camber line, the camber, the thickness, the leading edge, and the trailing edge. Figure 11.
Airfoil Nomenclature. The scale factor for a model is determined by dividing the chord length of the model by the chord length of the full-sized airfoil (often referred to as the prototype). This relation is shown in equation 1. 𝑆𝑆
=
𝐶𝐶
𝑀𝑀𝑀𝑀𝑀𝑀𝑀𝑀𝑀𝑀
𝐶𝐶
𝑃𝑃𝑃𝑃𝑀𝑀𝑃𝑃𝑀𝑀𝑃𝑃𝑃𝑃𝑃𝑃𝑀𝑀
(1) Model scale typically ranges from 1/5 scale to as small as 1/48 scale. The aerodynamic area of the model is also related to the aerodynamic area of the prototype by use of the scale factor, as shown in equation 2. 𝐴𝐴
𝑀𝑀𝑀𝑀𝑀𝑀𝑀𝑀𝑀𝑀
=
𝐴𝐴
𝑃𝑃𝑃𝑃𝑀𝑀𝑃𝑃𝑀𝑀𝑃𝑃𝑃𝑃𝑃𝑃𝑀𝑀
∗ 𝑆𝑆
(2) And finally, the lift force of the prototype can be estimated by using the scale factor and the lift force of the model as shown in equation 3. 𝐿𝐿
𝑃𝑃𝑃𝑃𝑀𝑀𝑃𝑃𝑀𝑀𝑃𝑃𝑃𝑃𝑃𝑃𝑀𝑀
=
𝐿𝐿
𝑀𝑀𝑀𝑀𝑀𝑀𝑀𝑀𝑀𝑀
𝑆𝑆
(3)
ME 4312 - Thermal and Fluids Laboratory | Page 5
of 10
The air speed in a wind tunnel (also known as freestream wind speed) acts as a simulation of the speed of a moving airfoil. The velocity of the tunnel air speed is referred to as the relative wind speed or freestream wind speed (V
∞
). The airfoil reacts to the V
∞
by experiencing lift force (L), a drag force (D), and a moment force (M), the magnitude of such being also highly dependent on the angle of attack. A sketch showing the definitions of lift, drag, relative wind velocity V
∞
, and angle of attack is provided in Figure 12. Figure 12.
Two-Dimensional Airfoil Aerodynamics. The equation used for determining the lift force on an airfoil is shown in equation 4. 𝐿𝐿
= 1
2
𝜌𝜌
∞
𝐴𝐴𝑉𝑉
∞
2
𝐶𝐶
𝐿𝐿
(4) The lift coefficient (
C
L
) can be considered a function of all the simple and complex factors such as: (1) body shape, (2) inclination (e.g., angle of attack), (3) surface roughness, and (4) flow conditions (flow velocity, fluid viscosity, etc.), among others. This value is usually determined experimentally for different airfoils, and is correlated with the angle of attack and the Reynolds number Re =
𝜌𝜌
∞
𝑉𝑉
∞
𝐶𝐶
/
𝜇𝜇
, where 𝜌𝜌
∞
is the air density, 𝑉𝑉
∞
is the wind tunnel air speed, 𝐶𝐶
is the chord length of the airfoil, and 𝜇𝜇
is the dynamic viscosity of air. Since the air velocity varies in magnitude over the surface of the airfoil, so does the pressure. Thus, to establish the pressure component of the lift force of the airfoil, a measure of the dynamic pressure at many locations over the top and bottom surfaces of the airfoil is required. The air stream velocity profile can be assumed constant over the wingspan (i.e., direction perpendicular to the airfoil), the flow stream will essentially be two-
dimensional. Therefore, the pressure distribution over the airfoil can be established by way of multiple pressure sensors aligned along the top and bottom surface of the airfoil in a direction tangential to the direction of airflow. It is common practice to express pressure distribution measurements in terms of a pressure coefficient defined by the dimensionless ratio, as indicated in Equation 5. 𝐶𝐶
𝑃𝑃
=
𝑃𝑃 − 𝑃𝑃
∞
1
2
(
𝜌𝜌
∞
𝑉𝑉
∞
2
)
(5) It should be noted that, for each different air stream velocity, the pressure coefficient profile over the airfoil surface should not substantially change. To establish the magnitude of the pressure-based lift force from model test data (i.e., from pressure measurements along the airfoil surface), the product of measured pressure times the airfoil segment area A
n
(i.e., the segment of area where the pressure is exerted by the freestream air) must be calculated for both the upper surface of the airfoil and for the lower surface of the airfoil. The absolute difference between the absolute force in the lower section (
𝐿𝐿
𝑀𝑀𝑙𝑙
) and the absolute force in the upper section (
𝐿𝐿
𝑢𝑢𝑙𝑙
) leads to the magnitude of the pressure-based lift force. Since there are many pressure measurements along the airfoil surface, the total airfoil surface area has to be apportioned into a number of areas A
n
associated with the location of each pressure sensing port. The boundaries of each area shall be the length of the wingspan and the half way distances along the curve between each pressure sensing port
. The magnitude of the pressure-based lift force shall then be established as indicated in Equations 6, 7, and 8. 𝐿𝐿
𝑀𝑀𝑙𝑙
= |
𝑝𝑝
9
𝐴𝐴
9
+
𝑝𝑝
10
𝐴𝐴
10
+
𝑝𝑝
11
𝐴𝐴
11
+
𝑝𝑝
12
𝐴𝐴
12
+
𝑝𝑝
13
𝐴𝐴
13
+
𝑝𝑝
14
𝐴𝐴
14
+
𝑝𝑝
15
𝐴𝐴
15
+
𝑝𝑝
16
𝐴𝐴
16
|
(6) 𝐿𝐿
𝑢𝑢𝑙𝑙
= |
𝑝𝑝
1
𝐴𝐴
1
+
𝑝𝑝
2
𝐴𝐴
2
+
𝑝𝑝
3
𝐴𝐴
3
+
𝑝𝑝
4
𝐴𝐴
4
+
𝑝𝑝
5
𝐴𝐴
5
+
𝑝𝑝
6
𝐴𝐴
6
+
𝑝𝑝
7
𝐴𝐴
7
+
𝑝𝑝
8
𝐴𝐴
8
|
(7) 𝐿𝐿
= |
𝐿𝐿
𝑀𝑀𝑙𝑙
− 𝐿𝐿
𝑢𝑢𝑙𝑙
|
(8)
ME 4312 - Thermal and Fluids Laboratory | Page 6
of 10
Note that the direction of the lift force can be upwards (when 𝐿𝐿
𝑀𝑀𝑙𝑙
>
𝐿𝐿
𝑢𝑢𝑙𝑙
) or downwards (when 𝐿𝐿
𝑀𝑀𝑙𝑙
<
𝐿𝐿
𝑢𝑢𝑙𝑙
). Analysis and Summary of Findings: 1.
Starting from the leading edge of the airfoil to each of the pressure sensing ports, divide the X
U and X
L dimensions by the chord length C
. Below a summary of the results:
Chord Length:
6 inches
Wingspan (perpendicular to chord length c):
11.75 inches Refer to Figures 9 and 10 for a visual representation of the data provided in the next tables: Upper Airfoil Surface Pressure Port # X
u
/C (Normalized Distance Along Chord Line) Starting Point to Ending Point Distance along curve (inches) 1 0.04 Leading edge to port 1 0.4 2 0.09 Port 1 to 2 0.33 3 0.16 2 to 3 0.44 4 0.25 3 to 4 0.55 5 0.34 4 to 5 0.54 6 0.48 5 to 6 0.84 7 0.64 6 to 7 0.97 8 0.8 7 to 8 0.98 Distance from port 8 to trailing edge along the curve of the airfoil is 1.25 inches Lower Airfoil Surface Pressure Port # X
L
/C (Normalized Distance Along Chord Line) Starting Point to Ending Point Distance along curve (inches) 9 0.01 Leading edge to port 9 0.1 10 0.06 Port 9 to 10 0.39 11 0.13 10 to 11 0.47 12 0.21 11 to 12 0.51 13 0.31 12 to 13 0.55 14 0.45 13 to 14 0.87 15 0.62 14 to 15 0.98 16 0.79 15 to 16 0.98 Distance from port 16 to trailing edge along the curve of the airfoil is 1.25 inches
Your preview ends here
Eager to read complete document? Join bartleby learn and gain access to the full version
- Access to all documents
- Unlimited textbook solutions
- 24/7 expert homework help
ME 4312 - Thermal and Fluids Laboratory | Page 7
of 10
2.
Calculate the airfoil surface area A
n associated with each pressure sensing port. Boundaries of each area shall be the length of the wingspan and the halfway distances between each pressure sensing port (see image below for an example). The areas can be obtained by taking the product of the wingspan and the length “along the curve” (use the data provided in the previous table to find the appropriate length along the curve).
3.
Calculate the total surface area of the airfoil and check to see if the sum of the areas determined in step 2 equals the total surface area (calculated as wing span times distance along the curve from leading edge to trailing edge for both upper and lower surfaces).
4.
Procedures to calculate the air velocity in the wind tunnel using experimental data from red manometer:
https://en.wikipedia.org/wiki/Pitot_tube Note that: • Stagnation (or total) pressure (pt) = static pressure (ps) + dynamic pressure (pd). The manometer reads dynamic pressure, which can be expressed as pd = (pt-ps). • 1 in of H2O equals 248.84 Pa. So, for example, if the dynamic pressure read by the manometer is 0.36 in of H2O, then, the value (pt-ps) is equal to 89.5824 Pa. • Estimate the air density at a height of 200 m above the sea level (altitude of the city of san Antonio) and for a temperature of about 22 degrees Celsius. Alternatively, assume the sea level value 1.2254 kg/m
3
. • The wind tunnel air speed is v = sqrt(2*(pt-ps)/rho_air).
5.
Calculate the pressure coefficient C
p (equation 5) for each of the recorded airfoil pressures 𝑝𝑝
. Remember that p-p
∞
is obtained from the height difference measured from the green tube manometers (measured displacement minus baseline).
https://en.wikipedia.org/wiki/Pressure_coefficient
6.
Prepare two sets of tables for each of the four wind velocities 𝑉𝑉
∞
(
specified by your instructor in terms of fan RPM)
. The tables shall consist of the non-dimensional tap locations X
U
/C and X
L
/C as the first column of data followed by columns of their corresponding (1) airfoil pressures 𝑝𝑝
, (2) surface areas A
n established in Step 2 above, and (3) the lift forces L
ls and L
us for each angle of attack. One table set shall apply to data corresponding to the airfoil upper surface and the second table set shall apply to the lower surface. The total airfoil surface area A and the total lift force L shall be included at the bottom of each of their respective columns. The column headings shall appear as denoted in the following example:
X
U
/C Airfoil Pressure p (Units) at Various AOA A
U
2
Lift Force L
U -15
o
-10
o
-6
o
-4
o
0
o
+4
o
+6
o
+10
o
+15
o
•
There will be a total of 8 tables for this step (lower surface and upper surface for each of the three wind velocities). •
Refer to Equations 6 and 7. •
Calculate pressure values. Multiply each pressure value by corresponding area. Add down the column for a lift
ME 4312 - Thermal and Fluids Laboratory | Page 8
of 10
force per angle of attack. The values in the table below are not the correct values
for the data provided to you; only use the table as an example. 7.
Prepare two tables consisting of tap locations X
U
/C and X
L
/C as the first column of data followed by columns Wind Velocity 𝑉𝑉
∞
and pressure coefficients C
p
. One table shall apply to data corresponding to the airfoil upper surface and the second table shall apply to the lower surface. The “average” C
p shall be established for each Angle of Attack (AOA) as indicated in the following table. Cite what you observe from this data, especially regarding the significance of C
p. For each angle of attack, establish the “average” C
p over the range of wind velocity.
Column headings should appear as in the following example: X
U/C Wind
Velocity
(ft/sec) Pressure Coefficient (C
p
) at Various AOA -15
o
-10
o
-6
o
-4
o
0
o
+4
o
+6
o
+10
o
-15
o
(1) (2)
(3)
(4) AVERAGE C
P
The values in the table below are not the correct values
; only use the table as an example. 8.
Prepare a plot of the “average” pressure coefficient C
p versus the chord position X/C for each angle of attack. Differentiate which C
p applies to the top surface and that of the lower surface. Apply the chord position X/C as the abscissa.
ME 4312 - Thermal and Fluids Laboratory | Page 9
of 10
Note:
To make the data easier to interpret, it would be best for the ordinate to include negative C
p
’s above the abscissa and positive C
p
’s below the abscissa as illustrated below. A sample plot
is shown below: •
For the upper and lower surface, you will plot the average pressure coefficients obtained for each angle of attack. •
You can switch the negative and positive numbers as in the plot above if it helps to interpret the data. 9.
Prepare tables and Compute the total lift L = |L
l
- L
u
| for each Angle of attack and for each wind velocity. Prepare a plot of L versus angle of attack, with angle of attack as the abscissa. All four wind velocities should be included on a single plot (overlay). Comment on your observations in your data analysis, especially with regard to “stalling”. A useful reference of 2D steady-state airfoil aerodynamics is: https://www.hindawi.com/journals/mpe/2015/854308/ A sample plot
is shown below: 10.
Discuss all tables and plots as they are presented in the report. Questions to guide discussion: •
What is the significance of the pressure coefficient and lift force? •
What is the relationship to angle of attack? •
What effects occur on the upper and lower surface of the airfoil? •
What effects occur at the leading edge vs. the trailing edge? •
Does the data make sense? Why or why not? •
What sources of error could affect the data collected?
Your preview ends here
Eager to read complete document? Join bartleby learn and gain access to the full version
- Access to all documents
- Unlimited textbook solutions
- 24/7 expert homework help
ME 4312 - Thermal and Fluids Laboratory | Page 10
of 10
Simulation Data: Below information for the simulation data component of this laboratory assignment: 1.
Using the coordinate data provided, recreate the NACA 4415 airfoil in your desired simulation software (For S
olid
W
orks
tutorial
: https://www.youtube.com/watch?v=6kXwoe6KMR0
)
.
2.
For the simulation boundary condition, you will need to choose one of the four (4) velocities considered during the experiment and for all angles of attack
calculate the lift force.
For this you will need to set an external flow simulation with the chosen velocity boundary condition and adjust the airfoil orientation towards the airflow for each angle of attack. (For S
olid
W
orks
tutorial
: https://www.youtube.com/watch?v=4ltTTYbmQkY
)
3.
Calculate the simulation lift force for the chosen velocity and all angles of attack and compare with the lift force calculated for those conditions with experimental data.
4.
During the experiment it is not possible to visualize the conditions of the flow surrounding the airfoil
and identify any areas of stagnated flow, flow separation, etc. Please include in your flow analysis the differences in the flow for the different angles of attack and what happens when the angle of attack is +/- 15 degrees.
(For this analysis you should create velocity cut plots and using contours or isolines for each angle of attack. The velocity condition chosen should be in the direction of the flow you set for your simulation).
Related Documents
Related Questions
Drop-load (I)This exercise is part of a series of problems aimed at modelling a situation by progressively refining our model to consider more and more parameters. This progressive approach is very close to what professional scientists do!
Context
We want to lower a suspended load in a controlled way so that it hits the ground with a speed whose modulus is not too great. To do this, the suspended load (B) is connected by a rope passing through a pulley to another mass (A), which can move on a horizontal surface.
Information
The masses of the charges A and B are known.The pulley is a ring of mass mp and radius R that can rotate without friction.The surface on which mass A is placed is horizontal.There is no friction between mass A and the surface on which it is placed.The string attached to mass A is perfectly parallel to the surface on which the mass rests.
SchematizationDraw a diagram of each object that interests us. Draw x- and y-axes for each object. Draw and name each force…
arrow_forward
You have been shortlisted for a job vacancy in the aerodynamic section of Airbus Industries. As part of the selection process, you are invited to participate in an online examination in order to evaluate your suitability for the advertised position. The set of the questions that has been sent to you are listed below. Your answer to each part should follow the corresponding word limit and guideline.
a- How does the Reynolds number affect the drag characteristics of the landing gear and the wing of an aircraft? Provide clear reasoning and use a sketch or sketches to illustrate your answer. Your answer should be limited to around 60-80 words.
b- In what ways do turbulent boundary layers affect the production of lift and drag on a typical civilian aircraft? Provide clear reasoning and limit your answer to around 60-80 words.
c- How does the position of the maximum thickness of an uncambered symmetrical aerofoil affect its drag? Use sketches to explain your answer. Your answer…
arrow_forward
Wind tunnel test section
km/h
Model
FD
Moving belt Drag balance
The aerodynamic drag of a new Volvo FH truck is to be predicted at a speed of 85 km/h at an air
temperature of 25°C (p=1.184 kg/m³, u=1.849x10-5kg/m-s). Volvo engineers build a 1/2 scale
model of the FH to test in a wind tunnel. The temperature of the wind tunnel is also 25°C. The drag
force is measured with a drag balance, and the moving belt is used to simulate the moving ground.
Determine how fast the engineers should run the wind tunnel to achieve similarity between
the model and the prototype.
arrow_forward
2. A student team is to design a human-powered submarine for a design competition. The overall
length of the prototype submarine is 4.85 m, and its student designers hope that it can travel fully
submerged through water at 0.440 m/s. The water is freshwater (a lake) at T = 15 °C. The design
team builds a one-fifth scale model to test in their university's wind tunnel, as shown in the Fig. A
shield surrounds the drag balance strut so that the aerodynamic drag of the strut itself does not
influence the measured drag. The air in the wind tunnel is at 25 °C and at one standard atmosphere
pressure. At what air speed do they need to run the wind tunnel in order to achieve similarity?
Take for water at T = 15 °C and atmospheric pressure, p = 999.1 kg/m³ and µ = 1.138 × 10-³ Pa.s.
Take for air at T = 25 °C and atmospheric pressure, p = 1.184 kg/m³ and µ = 1.849 × 105 Pa.s.
Wind tunnel test section
V
Poo, P
Model
Shield
FD
Drag balance
Strut
arrow_forward
2. A student team is to design a human-powered submarine for a design competition. The overall
length of the prototype submarine is 4.85 m, and its student designers hope that it can travel fully
submerged through water at 0.440 m/s. The water is freshwater (a lake) at T = 15 °C. The design
team builds a one-fifth scale model to test in their university's wind tunnel, as shown in the Fig. A
shield surrounds the drag balance strut so that the aerodynamic drag of the strut itself does not
influence the measured drag. The air in the wind tunnel is at 25 °C and at one standard atmosphere
pressure. At what air speed do they need to run the wind tunnel in order to achieve similarity?
Take for water at T = 15 °C and atmospheric pressure, p = 999.1 kg/m³ and µ = 1.138 × 10-³ Pa.s.
Take for air at T = 25 °C and atmospheric pressure, p = 1.184 kg/m³ and µ = 1.849 × 10-³ Pa.s.
V
Por P
Wind tunnel test section
Model
Shield
FD
Drag balance
Strut
arrow_forward
You are tasked with designing the runway on an aircraft carrier. The minimum speed for the F/A-18 Hornet is 193.8 mph. The Hornet weighs 40,000 lbf and its twin engines provide a thrust of ~40,000 lbf combined, providing a max acceleration of 1g. How long must the deck be to takeoff unassisted in feet?
arrow_forward
Fluid Mechanics Problem
Note: Fluids are assumed to be at 20oC.
arrow_forward
The following equation may be used to estimate the take-off ground run for an aircraft: Equation has been attached as an image.
Calculate the take-off ground run, from a runway at ISA-SL conditions, for a twin engine aircraft for which the following data may be assumed
Aircraft lift-off speed
155 knots
Max take-off gross weight
220 tonnes
Wing planform area (S)
358 m
Wing CL (t/o flaps deployed, a = 0)
1.1
Wing span
53.18 m
Oswald efficiency factor, e
0.7
KGE = CD(IGE) / Co(OGE)
0.4
Co sum (fuselage, wing, tailplane and nacelle)
0.015
Co for undercarriage
0.021
Co for flaps at taking-off setting
0.0073
Coefficient of rolling friction, u
0.02
Engine thrust (assumed constant)
310 kN per engine
It may be assumed that 1knot = 0.51444 m/s
It may be assumed that 1knot = 0.51444 m/s
arrow_forward
2. Outcomes 1 and 4.Show and explain all work. You must show and explain all work. The drag
on the hull of a sailboat can be shown to depend on the boat velocity V, the water density p and viscosity
μ, the length of the hull f, and the acceleration due to gravity g.
JIH
Class 40 Racing Yacht.
30
arrow_forward
Given:
The plane accelerates in its current trajectory with a= 100 m/s^2
Farag
Angle theta= 5°
W=105 kips
F_drag= 80 kips
m= 1000 lbs
Find: F_thrust, F_lift
Please include the KD.
Fthrust
Futel t Fueight
000
BY NC SA
2013 Michael Swanbom
arrow_forward
If your lift to drag ratio is 15 for airline A flight and the airplane weighs 15,000-lb for L/Dmax, what’s the speed for L/Dmax at 22,500 lbs.?
arrow_forward
Fluid mechanics / please find the attached file.
arrow_forward
Stage Design
A cable is used to support an actor as he swings onto the stage. Now suppose the tension in the cable is 920 N as the actor reaches
the lowest point. What diameter should an 11-m-long steel cable have if we do not want it to stretch more than 0.50 cm under
these conditions?
R.
Actor
Sandbag
SOLUTION
Conceptualize Look back at the Example "A Grand Entrance," where we analyzed a cable used to support an actor as he swung
onto the stage. We ignored any stretching of the cable there, but we wish to address this phenomenon in this example.
Categorize We perform a simple calculation involving the equation
F
A
Y =
AL
Li
so we categorize this example as
--Select---
v problem.
Solve the Young's modulus equation for the cross-sectional area of the cable:
FL;
A =
YAL
Assuming the cross section is circular, find the diameter of the cable from d = 2r and A = ar (Use the following as necessary: F, Y,
Li, AL, and r.):
FL
A
d = 2r = 2 - = 2
Substitute numerical values. (Enter your answer…
arrow_forward
M Inbox - wep10@zips.uakron.edu
O My Akron Experience - The Univ
B Homepage - Statics 801
O Pearson MyLab and Mastering
b The equivalent resultant force, di x
Course Home
A https://openvellum.ecollege.com/course.html?courseld=16245503&OpenVellumHMAC=67fab398401alafde96db3b49e605db9#10001
O My Courses
KAssignment 10o
Course Home
Problem 4.137
3 of 4
Syllabus
I Review
Scores
Replace the three forces acting on the plate by a wrench. Suppose
that FA = {450i}N, FB = {-350k} N, and Fc = {300j} N.
(Figure 1)
Part B
eТext
Determine the couple moment of the wrench.
Express your answer to three significant figures and include the appropriate units. Enter positive value if the sense of direction of the couple moment is the
same as that of the resultant force and negative value if the sense of direction of the couple moment is opposite to that of the resultant force.
Study Area
Document Sharing
TH HẢ
?
User Settings
Value
Units
Course Tools
>
Submit
Previous Answers Request Answer
X Incorrect; Try…
arrow_forward
I need help with my MATLAB code. There is an error in the following code. The error says my orbitaldynamics function must return a column vector. Can you help me fix it?
mu_earth = 398600.4418; % Earth's gravitational parameter (km^3/s^2)
R_earth = 6378.137; % Earth's radius (km)
C_d = 0.3; % Drag coefficient (assumed)
A = 0.023; % Cross-sectional area of ISS (km^2)
m = 420000; % Mass of ISS (kg)
% Initial conditions: position and velocity (ISS state vector)
% ISS initial state vector (km and km/s) - sample data
state_ISS =[-2.1195e+03, 3.9866e+03, 5.0692e+03, -5.3489, -5.1772, 1.8324];
% Time span for 10 revolutions
T_orbit = 2 * pi * sqrt((norm(state_ISS(1:3))^3) / mu_earth);
time_span = [0, 10 * T_orbit];
% Step 3: Numerical integration using ODE solver
options = odeset('RelTol', 1e-12, 'AbsTol', 1e-12);
[t, state] = ode45(@orbitalDynamics, time_span, state_ISS, options);
% Step 4: Plot the results
figure;
plot3(state(:, 1), state(:, 2), state(:, 3));
xlabel('X…
arrow_forward
>
| E9
docs.google.com/form
تبديل الحساب
Questions
7 نقاط
Q1/ The power of 6-blade flat blade turbine agitator in a tank is a function of diameter of impeller, number of
rotations of the impeller per unit time, viscosity and density of liquid. From a dimensional analysis, obtain a
relation between the power and the four variables.
3.
صفحة 2 من
arrow_forward
The figure shows two cables AB and AC. Using the tabulated values for the parameters, calculate the
magnitude of the projection of FAC onto AB. Also, determine the angle 0 formed by BAC. NOTE: the
magnitude of the projection may be positive or negative (or zero). Also, point C lies on the y axis.
В
L6
FAB
A
L2
FAC
y
L3
X
2021 Cathy Zupke
parameter
value
units
3
m
L2
L3
L4
3
m
3
m
1
m
3
L6
FAB
2
80
N
FAC
100
The magnitude of the projection of FAC on AB is
N
The angle AB makes with AC is 0-
arrow_forward
= 3570
T AC
=144
Example:
1.5 ft
It is desired to determine the drag force at a given
speed on a prototype sailboat hull. A model is
placed in a test channel and three cables are used
to align its bow on the channel centerline. For a
given speed, the tension is 40 lb in cable AB and
60 lb in cable AE.
Flow
4 ft
Determine the drag force exerted on the hull and
the tension in cable AC.
Choc
ug the h-
as the free hod-
DApress the
arrow_forward
SEE MORE QUESTIONS
Recommended textbooks for you
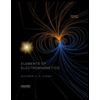
Elements Of Electromagnetics
Mechanical Engineering
ISBN:9780190698614
Author:Sadiku, Matthew N. O.
Publisher:Oxford University Press
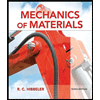
Mechanics of Materials (10th Edition)
Mechanical Engineering
ISBN:9780134319650
Author:Russell C. Hibbeler
Publisher:PEARSON
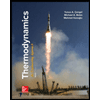
Thermodynamics: An Engineering Approach
Mechanical Engineering
ISBN:9781259822674
Author:Yunus A. Cengel Dr., Michael A. Boles
Publisher:McGraw-Hill Education
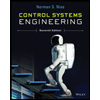
Control Systems Engineering
Mechanical Engineering
ISBN:9781118170519
Author:Norman S. Nise
Publisher:WILEY
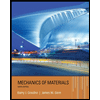
Mechanics of Materials (MindTap Course List)
Mechanical Engineering
ISBN:9781337093347
Author:Barry J. Goodno, James M. Gere
Publisher:Cengage Learning
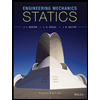
Engineering Mechanics: Statics
Mechanical Engineering
ISBN:9781118807330
Author:James L. Meriam, L. G. Kraige, J. N. Bolton
Publisher:WILEY
Related Questions
- Drop-load (I)This exercise is part of a series of problems aimed at modelling a situation by progressively refining our model to consider more and more parameters. This progressive approach is very close to what professional scientists do! Context We want to lower a suspended load in a controlled way so that it hits the ground with a speed whose modulus is not too great. To do this, the suspended load (B) is connected by a rope passing through a pulley to another mass (A), which can move on a horizontal surface. Information The masses of the charges A and B are known.The pulley is a ring of mass mp and radius R that can rotate without friction.The surface on which mass A is placed is horizontal.There is no friction between mass A and the surface on which it is placed.The string attached to mass A is perfectly parallel to the surface on which the mass rests. SchematizationDraw a diagram of each object that interests us. Draw x- and y-axes for each object. Draw and name each force…arrow_forwardYou have been shortlisted for a job vacancy in the aerodynamic section of Airbus Industries. As part of the selection process, you are invited to participate in an online examination in order to evaluate your suitability for the advertised position. The set of the questions that has been sent to you are listed below. Your answer to each part should follow the corresponding word limit and guideline. a- How does the Reynolds number affect the drag characteristics of the landing gear and the wing of an aircraft? Provide clear reasoning and use a sketch or sketches to illustrate your answer. Your answer should be limited to around 60-80 words. b- In what ways do turbulent boundary layers affect the production of lift and drag on a typical civilian aircraft? Provide clear reasoning and limit your answer to around 60-80 words. c- How does the position of the maximum thickness of an uncambered symmetrical aerofoil affect its drag? Use sketches to explain your answer. Your answer…arrow_forwardWind tunnel test section km/h Model FD Moving belt Drag balance The aerodynamic drag of a new Volvo FH truck is to be predicted at a speed of 85 km/h at an air temperature of 25°C (p=1.184 kg/m³, u=1.849x10-5kg/m-s). Volvo engineers build a 1/2 scale model of the FH to test in a wind tunnel. The temperature of the wind tunnel is also 25°C. The drag force is measured with a drag balance, and the moving belt is used to simulate the moving ground. Determine how fast the engineers should run the wind tunnel to achieve similarity between the model and the prototype.arrow_forward
- 2. A student team is to design a human-powered submarine for a design competition. The overall length of the prototype submarine is 4.85 m, and its student designers hope that it can travel fully submerged through water at 0.440 m/s. The water is freshwater (a lake) at T = 15 °C. The design team builds a one-fifth scale model to test in their university's wind tunnel, as shown in the Fig. A shield surrounds the drag balance strut so that the aerodynamic drag of the strut itself does not influence the measured drag. The air in the wind tunnel is at 25 °C and at one standard atmosphere pressure. At what air speed do they need to run the wind tunnel in order to achieve similarity? Take for water at T = 15 °C and atmospheric pressure, p = 999.1 kg/m³ and µ = 1.138 × 10-³ Pa.s. Take for air at T = 25 °C and atmospheric pressure, p = 1.184 kg/m³ and µ = 1.849 × 105 Pa.s. Wind tunnel test section V Poo, P Model Shield FD Drag balance Strutarrow_forward2. A student team is to design a human-powered submarine for a design competition. The overall length of the prototype submarine is 4.85 m, and its student designers hope that it can travel fully submerged through water at 0.440 m/s. The water is freshwater (a lake) at T = 15 °C. The design team builds a one-fifth scale model to test in their university's wind tunnel, as shown in the Fig. A shield surrounds the drag balance strut so that the aerodynamic drag of the strut itself does not influence the measured drag. The air in the wind tunnel is at 25 °C and at one standard atmosphere pressure. At what air speed do they need to run the wind tunnel in order to achieve similarity? Take for water at T = 15 °C and atmospheric pressure, p = 999.1 kg/m³ and µ = 1.138 × 10-³ Pa.s. Take for air at T = 25 °C and atmospheric pressure, p = 1.184 kg/m³ and µ = 1.849 × 10-³ Pa.s. V Por P Wind tunnel test section Model Shield FD Drag balance Strutarrow_forwardYou are tasked with designing the runway on an aircraft carrier. The minimum speed for the F/A-18 Hornet is 193.8 mph. The Hornet weighs 40,000 lbf and its twin engines provide a thrust of ~40,000 lbf combined, providing a max acceleration of 1g. How long must the deck be to takeoff unassisted in feet?arrow_forward
- Fluid Mechanics Problem Note: Fluids are assumed to be at 20oC.arrow_forwardThe following equation may be used to estimate the take-off ground run for an aircraft: Equation has been attached as an image. Calculate the take-off ground run, from a runway at ISA-SL conditions, for a twin engine aircraft for which the following data may be assumed Aircraft lift-off speed 155 knots Max take-off gross weight 220 tonnes Wing planform area (S) 358 m Wing CL (t/o flaps deployed, a = 0) 1.1 Wing span 53.18 m Oswald efficiency factor, e 0.7 KGE = CD(IGE) / Co(OGE) 0.4 Co sum (fuselage, wing, tailplane and nacelle) 0.015 Co for undercarriage 0.021 Co for flaps at taking-off setting 0.0073 Coefficient of rolling friction, u 0.02 Engine thrust (assumed constant) 310 kN per engine It may be assumed that 1knot = 0.51444 m/s It may be assumed that 1knot = 0.51444 m/sarrow_forward2. Outcomes 1 and 4.Show and explain all work. You must show and explain all work. The drag on the hull of a sailboat can be shown to depend on the boat velocity V, the water density p and viscosity μ, the length of the hull f, and the acceleration due to gravity g. JIH Class 40 Racing Yacht. 30arrow_forward
- Given: The plane accelerates in its current trajectory with a= 100 m/s^2 Farag Angle theta= 5° W=105 kips F_drag= 80 kips m= 1000 lbs Find: F_thrust, F_lift Please include the KD. Fthrust Futel t Fueight 000 BY NC SA 2013 Michael Swanbomarrow_forwardIf your lift to drag ratio is 15 for airline A flight and the airplane weighs 15,000-lb for L/Dmax, what’s the speed for L/Dmax at 22,500 lbs.?arrow_forwardFluid mechanics / please find the attached file.arrow_forward
arrow_back_ios
SEE MORE QUESTIONS
arrow_forward_ios
Recommended textbooks for you
- Elements Of ElectromagneticsMechanical EngineeringISBN:9780190698614Author:Sadiku, Matthew N. O.Publisher:Oxford University PressMechanics of Materials (10th Edition)Mechanical EngineeringISBN:9780134319650Author:Russell C. HibbelerPublisher:PEARSONThermodynamics: An Engineering ApproachMechanical EngineeringISBN:9781259822674Author:Yunus A. Cengel Dr., Michael A. BolesPublisher:McGraw-Hill Education
- Control Systems EngineeringMechanical EngineeringISBN:9781118170519Author:Norman S. NisePublisher:WILEYMechanics of Materials (MindTap Course List)Mechanical EngineeringISBN:9781337093347Author:Barry J. Goodno, James M. GerePublisher:Cengage LearningEngineering Mechanics: StaticsMechanical EngineeringISBN:9781118807330Author:James L. Meriam, L. G. Kraige, J. N. BoltonPublisher:WILEY
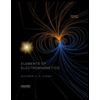
Elements Of Electromagnetics
Mechanical Engineering
ISBN:9780190698614
Author:Sadiku, Matthew N. O.
Publisher:Oxford University Press
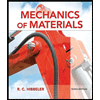
Mechanics of Materials (10th Edition)
Mechanical Engineering
ISBN:9780134319650
Author:Russell C. Hibbeler
Publisher:PEARSON
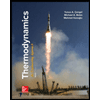
Thermodynamics: An Engineering Approach
Mechanical Engineering
ISBN:9781259822674
Author:Yunus A. Cengel Dr., Michael A. Boles
Publisher:McGraw-Hill Education
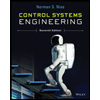
Control Systems Engineering
Mechanical Engineering
ISBN:9781118170519
Author:Norman S. Nise
Publisher:WILEY
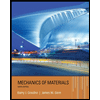
Mechanics of Materials (MindTap Course List)
Mechanical Engineering
ISBN:9781337093347
Author:Barry J. Goodno, James M. Gere
Publisher:Cengage Learning
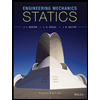
Engineering Mechanics: Statics
Mechanical Engineering
ISBN:9781118807330
Author:James L. Meriam, L. G. Kraige, J. N. Bolton
Publisher:WILEY