ME495 Lab 10_ Ratio of Volumes
pdf
keyboard_arrow_up
School
San Diego State University *
*We aren’t endorsed by this school
Course
495
Subject
Mechanical Engineering
Date
Apr 3, 2024
Type
Pages
13
Uploaded by ChiefDeerMaster1083
Ratio of Volumes
ME 495: Mechanical and Thermal Systems Lab
Section 05: Thursday
Group D
Authors: Soeung Khanitha, Smith Emilee, Sichantha Jack, Taylor Charles
Instructor: Dr. Hamid Nourollahi
Wednesday, March 13, 2024
1
Table of Contents
Objective of Experiment (Khanitha Soeung)
...................................................................................
2
List of Symbols and Equations (Charles Taylor)
.............................................................................
2
Equipment (Khanitha Soeung & Jack Sichantha)
............................................................................
3
Experimental Setup (Khanitha Soeung, Jack Sichantha)
.................................................................
4
Experimental Procedure (Emilee Smith)
.........................................................................................
6
Experimental Results(Charles Taylor)
....................................................................................
8
Discussion of Results (Charles Taylor)
............................................................................................
9
Lab Guide Questions (Emilee Smith)
............................................................................................
10
Conclusion (Jack Sichantha)
..........................................................................................................
11
References ( Khanitha Soeung )
....................................................................................................
12
Appendix (Khanitha Soeung)
........................................................................................................
12
List of Figures
Figure 1: Illustrates the TH5 apparatus for expansion processes of a perfect gas, developed
by Armfield Limited
..................................................................................................................
4
Figure 2: Electrical Console; (A) Front Perspective, (B) Rear Perspective…………………..5
Figure 3: Equipment Diagrams
…………………………………………………………….6
List of Tables
Table 2: Figure 2 Equipment Diagram reference from lab manual
.....................................
7
Table 2: Experimental Data Two pressure sensors are employed, both utilizing
piezoresistive technology, generating a voltage output that varies linearly with pressure
fluctuations from lab manual
...............................................................................................
8
Table 3: Pressure Sensors
...................................................................................................
8
2
Objective of Experiment (Khanitha Soeung)
The objective of this experiment is to determine the ratio of volumes for air in two
vessels through an isothermal expansion process, providing students with practical insight into
ideal gas behavior, adiabatic processes, and thermodynamics' first law. Utilizing the TH5-B
equipment, which introduces basic thermodynamic processes using air as a working fluid, the
setup comprises interconnected rigid vessels—one for pressurized operation and the other for
vacuum
operation—allowing
for
independent
or
combined
evaluation
of thermodynamic
processes. Constructed from clear rigid plastic, the vessels maintain moderate insulation to
minimize external temperature influences while permitting rapid return to ambient temperature.
The teams hypothesize that the volume ratio of air in the vessels will remain constant throughout
the expansion, in accordance with Boyle's Law and ideal gas principles. The team also
hypothesized that, when calculating the ratio of volumes, error should be less than 10%.
List of Symbols and Equations (Charles Taylor)
Table 1: Symbols and Equations
PARAMETER
SYMBOL / EQUATION
UNIT
Constant Temperature for both
vessels
T
°C
Atmospheric Pressure
P
atm
101325 N/m
2
Initial Pressure for first vessel
(Measured)
P
s
N/m
2
Initial Pressure for first vessel
(Absolute)
P1abs
s
= P
atm
+ P
s
N/m
2
Initial
Vacuum
for
second
vessel (Measured)
V
s
N/m
2
Initial
Pressure
for
second
vessel (Absolute)
P2abs
s
= P
atm
- V
s
N/m
2
Final pressure (Measured)
P
f
= -V
f
N/m
2
Final Pressure (Absolute)
P1abs
f
= P
f
+ P
atm
N/m
2
Ratio of Volumes
R=Vol1/Vol2
𝑉𝑜𝑙1/𝑉𝑜𝑙2 = (𝑃2???, ? − 𝑃𝑓)/(𝑃𝑓 − 𝑃1???, ?)
Ratio of Volumes From Data
Logger
Ro
Percent Error
𝐸??𝑜? = |𝑅 − 𝑅𝑜|/𝑅
%
Your preview ends here
Eager to read complete document? Join bartleby learn and gain access to the full version
- Access to all documents
- Unlimited textbook solutions
- 24/7 expert homework help
3
Note: A majority of this table is directly cited from the lab guide manual
This is given in the references of this report as reference number [1]
Equipment (Khanitha Soeung & Jack Sichantha)
●
Temperature Probes (T1 & T2)
○
Miniature semiconductor thermistor beads with fine connecting leads, installed
between support wires at the tip of the probe assembly; exhibit nonlinear negative
resistance characteristics; fast response to temperature changes.
●
Air Pump
○
Supplies air for evaluating thermodynamic properties of a perfect gas; inlet
connected to tapping on top of evacuated vessel, outlet connected to tapping on
top of pressurized vessel.
●
Electrical Console
○
Simple console with power supplies and necessary connections for air pump and
sensors; displays pressure (P), vacuum (V), and temperatures (T1 & T2) on a
digital meter with rotator selector switch.
●
IFD5
○
Interface device allowing voltage signals from measurements to be connected to a
PC; connects to console via 50-way data cable and to PC via USB cable; features
red 'Power' LED indicating connection to PC and green 'Active' LED indicating
recognition by PC.
4
Experimental Setup (Khanitha Soeung, Jack Sichantha)
5
Figure 1: Illustrates the TH5 apparatus for expansion processes of a perfect gas, developed by
Armfield Limited.
Figure 2: Electrical Console; (A) Front Perspective, (B) Rear Perspective
The setup procedure began with ensuring that the Mains on/off switch on the electrical
console was in the OFF position, along with the air pump switch. Ball valves V1, V2, and V3 on
top of the vessels were fully opened, and isolating valves V4 and V7 from the air pump to the
pressurized and evacuated vessels were also opened entirely. Following this, the inlet of the air
pump was connected to the tapping on top of the evacuated vessel, while the outlet was
connected to the tapping on the top of the pressurized vessel. Leads from the sensors were
connected to the appropriate sockets at the rear of the electrical console. After ensuring the mains
electrical supply was connected and switched on, the operation of the RCD was tested, and the
miniature circuit breakers were confirmed to be in the ON position. The mains on/off switch on
the front of the electrical console was set to the ON position, and the digital panel meter was
observed to be illuminated. The rotary selector switch was set to each position in turn to check
Your preview ends here
Eager to read complete document? Join bartleby learn and gain access to the full version
- Access to all documents
- Unlimited textbook solutions
- 24/7 expert homework help
6
the readings. Ball valves V1 and V2, along with isolating valve V6, were closed, and isolating
valve V4 was opened to allow the air pump to pressurize the pressurized vessel. The selector
switch was set to position P to observe the pressure inside the pressurized vessel, and the air
pump was switched ON. Once the pressure reached approximately 30 kN/m2, isolating valve V4
was closed, and the air pump was switched OFF. Similar procedures were followed for observing
the vacuum inside the evacuated vessel. Finally, valves V1, V2, and V3 were opened to return
the vessels to atmospheric pressure, and the equipment was switched OFF using the mains
switch on the electrical console.
Experimental Procedure (Emilee Smith)
Figure 3: Equipment Diagrams
Before commencing the exercise, it was ensured that both rigid vessels were at
atmospheric pressure by opening valves V1 and V3 on top of the vessels and closing all other
valves. The atmospheric pressure (Patm) was assumed to be 760 mm of Hg (or 10130 N/m2).
Ball-valves V1, V3, and V5 were closed, while V4 and V7 were opened. The large vessel was
pressurized by switching ON the air pump, and when the pressure (P) reached approximately 30
kN/m2, the air pump was switched OFF, and valves V4 and V7 were closed. After allowing the
7
pressure in the large vessel to stabilize, the starting pressure (Ps) and ambient temperature (Ts)
were recorded. The software was configured to take samples at 1-second intervals, and data
logging was initiated by pressing the green 'Go' button. Needle valve V5 was fully closed, and
isolating valve V6 was opened, with V5 opened slightly to allow air to leak from the pressurized
vessel to the evacuated vessel. V5 was adjusted to ensure a slow decrease in P without any
change in T1 or T2. Once the vessel contents stabilized in pressure and temperature, the final
pressure (Pf) was recorded. Data logging was stopped by pressing the red 'Stop' button, and the
data for each trial was saved as an Excel file on a portable USB drive.
Table 2: Figure 2 Equipment Diagram reference from lab manual
8
Table 2: Experimental Data Two pressure sensors are employed, both utilizing piezoresistive
technology, generating a voltage output that varies linearly with pressure fluctuations from lab
manual
Table 3: Pressure Sensors
Experimental Results (Charles Taylor)
Table 4: Experimental Pressure Values
Trial
Initial Pressure
Final Pressure
Ps (kN/m^s)
P1abss
(kN/m^s)
Vs
(kN/m^s)
P2abss
(kN/m^s)
Pf (kN/m^s)
P1absf
(kN/m^s)
1
34.46
134.46
34.46
65.54
114.48
14.48
2
34.46
134.46
34.46
65.54
112.96
12.96
3
34.46
134.46
34.46
65.54
112.56
12.56
4
34.46
134.46
34.46
65.54
114.29
14.29
5
34.46
134.46
34.46
65.54
114.82
14.82
Table 5: Experimental R Values and Error
R
Ro (From Data Logger)
Error (%)
2.449
2.36
3.651
2.205
2.15
2.520
2.147
2.12
1.259
2.416
2.36
2.356
2.509
2.41
3.952
Your preview ends here
Eager to read complete document? Join bartleby learn and gain access to the full version
- Access to all documents
- Unlimited textbook solutions
- 24/7 expert homework help
9
Sample Calculations: Trial 1
First, initial pressures are recorded and noted. These are all found in table 4.
Now calculate Pf:
Pf = -Vf + Patm, Vf is recorded to be -14.48 kN/m^2. Hence, Pf = 114.48 kN/m^2
Now calculate P1abs,f:
P1abs,f = Pf - Patm, Pf = 114.48 kN/m^2. Hence, P1abs,f = 14.48 kN/m^2
Now calculate R:
,
P2abs,s, Pf, and P1 abs,s are found above
𝑅 = 𝑉𝑜𝑙1/𝑉𝑜𝑙2 = (𝑃2???, ? − 𝑃𝑓)/(𝑃𝑓 − 𝑃1???, ?)
in table 4. R = 2.449
Now calculate Error:
,
R and Ro are found in table 4, Error = 3.952%
𝐸??𝑜? = |𝑅 − 𝑅𝑜|/𝑅
Discussion of Results (Charles Taylor)
Table 4: Experimental Pressure Values represent the comparison of the data points for all the
pressure found experimentally throughout the experiment. All initial pressures are taken directly
from the data logger trials. The Ps represents the initial pressure for the first vessel, and P1abs,s
is the absolute pressure for the first vessel. Vs and P2abs,s represent the initial pressures and
vacuums for the second vessel. Pf was a calculated value using Vf and P1abs, and f is the
absolute final pressure which is calculated using Pf and Patm. Table 5: Experimental R-Value
and Error shows the experimental and theoretical values for R, Ro. R is calculated using the ratio
of the volumes of the two containers, this equation can be shown in the lab guide. It is then
compared to the Ro value shown in the data logger. This table also shows the error between these
10
two values. It is important to note that the calculated R-value is generally greater than its Ro
counterpart. This shows that the error is likely a result of systematic error rather than random
error, however, small random errors are likely still present. For example, a few systematic errors
are the calibration of the machine or the wear of the pressure sensor. Random error should be
uncommon in this experiment since the computer logs a majority of the data, however, turning
the valve open too fast may cause excess pressure loss and could alter the data for each trial.
The team’s hypothesis was that, when measuring the ratio volumes, the error found should be
less than 10%. This turned out to be true in all cases and all trials. The error shown in table 4
proves that it was consistently less than 10% and even less than 4% in all cases.
Lab Guide Questions (Emilee Smith)
1.
Why is this an isothermal process?
a.
An isothermal process occurs when the temperature of a system remains constant.
The temperature of this system remained roughly the same, fluctuating by tenths
of a degree Celcius with a maximum temperature difference of 2.4°C in Trial 2.
2.
How well does the result obtained compare to the expected result? Give possible
reasons for any difference.
a.
The results from the experiment compared to the expected results were relatively
close with a maximum percent error of 7.05% and a minimum percent error of
0.13%. Human error would be the most likely cause for any type of error because
manually turning the knob will never be at the same rate each time and would also
11
change depending on the person turning it. Other reasons may involve any gas
escaping from the vessels via worn seals/valves/etc.
3.
Comment on the effect if the rate of change of pressure was sufficient to affect the
temperature of the air inside the vessels.
a.
There was no effect from the rate of change of the pressure on the temperature of
the air inside the vessels, which was expected since the experiment is an
isothermal process.
Conclusion (Jack Sichantha)
Based on the data presented in Tables 3 and 4, it can be concluded that the experimental
method employed to measure pressure and calculate the ratio of volumes between the two
containers was effective and reliable. The systematic error observed, likely stemming from
factors such as machine calibration and pressure sensor wear, was consistently small and below
the threshold of 10% as hypothesized by the team. The low percentage of error, often less than
4%, indicates a high degree of precision in the experimental measurements.
Furthermore, the rarity of random errors, attributed to the automated data logging
process, underscores the robustness of the experimental setup. Nevertheless, precautions were
taken to mitigate potential sources of random error, such as controlled valve operation.
Overall, these findings validate the team's hypothesis and affirm the accuracy of the
experimental procedure in determining the ratio of volumes between the containers. This not
only contributes to the understanding of the physical properties under investigation but also
highlights the importance of meticulous experimental design and execution in scientific research.
Your preview ends here
Eager to read complete document? Join bartleby learn and gain access to the full version
- Access to all documents
- Unlimited textbook solutions
- 24/7 expert homework help
12
References ( Khanitha Soeung )
[1]
Nourollahi, A. (2024). ME-495 Laboratory Exercise – Number 10 – Ratio of Volumes In
ME Dept, SDSU – Nourollahi. SDSU Publishing
[2]
Nourollahi, A. (2024). ME-495 Course Introduction_and Syllabus Spring 2024-1. In ME
Dept, SDSU – Nourollahi. SDSU Publishing
Appendix (Khanitha Soeung)
The
correlation
between resistance and temperature for thermistors employed in TH5-B
(Nominal Values) is as follows:
Related Documents
Related Questions
Thermodynamics
Please READ THE PROBLEM! I’m tired of posting the same problem over and over. please Read.
This is what the asking for please:
-1. sketch and label all your answers on the nozzle
-2. Sketch and label all your answers on the process on a P-V diagram....
Thank you
arrow_forward
HEAT TRANSFER
CASE: I want to know what temperature in (°F) the cylinder will have inside. It's a heat transfer problem.
what is T2 ?
HEAT TRANSFER
They gave me an answer all squashed together that i can't make sense of it. If you could help me makes sense of it thank you!
arrow_forward
An electric hot water heater consumes 3.1 kilowatts of electricity and converts it to heat. How long will it take the water heater to heat a 67 gallon tank of water from 10 degrees Celsius to 50 degrees Celsius? (1 kilogram of water is 0.37 gallons, 1 Calorie = 4200 J). It may be helpful to refer back to the weekly handout for guidance on this problem.
Your final answer should be in minutes (rounded to the nearest 10 minutes).
arrow_forward
I want to briefly summarize what he is talking about and what you conclude.
pls very urgent
arrow_forward
Topics:
Statics of Rigid Bodies, Equilibrium of Rigid Bodies, Equilibrium in Two Dimensions, etc.
I will rate you with “LIKE/UPVOTE," if it is COMPLETE STEP-BY-STEP SOLUTION.
If it is INCOMPLETE SOLUTION and there are SHORTCUTS OF SOLUTION, I will rate you with “DISLIKE/DOWNVOTE.”
THANK YOU FOR YOUR HELP.
PS: If you have answered this already, don’t answer it again; give chance to other experts to answer it. I want to verify if all of you will arrive in the same final answer; thats why I ask it multiple times. If you answer it again, i'll dislike all your entries/answers.
arrow_forward
Topics:
Statics of Rigid Bodies, Equilibrium of Rigid Bodies, Equilibrium in Two Dimensions, etc.
I will rate you with “LIKE/UPVOTE," if it is COMPLETE STEP-BY-STEP SOLUTION.
If it is INCOMPLETE SOLUTION and there are SHORTCUTS OF SOLUTION, I will rate you with “DISLIKE/DOWNVOTE.”
THANK YOU FOR YOUR HELP.
PS: If you have answered this already, don’t answer it again; give chance to other experts to answer it. I want to verify if all of you will arrive in the same final answer; thats why I ask it multiple times. If you answer it again, i'll dislike all your entries/answers.
arrow_forward
1. The development of thermodynamics since the 17th century, which was pioneered by the invention of the steam engine in England, and was followed by thermodynamic scientists such as Willian Rankine, Rudolph Clausius, and Lord Kelvin in the 19th century. explain what the findings or theories of the 3 inventors are!
Please answer fast max 25-30.minutes thank u
arrow_forward
Show work
Part 1 website: https://ophysics.com/r5.html
PArt 2 website: https://ophysics.com/r3.html
arrow_forward
The left side of this equation tells how much energy Q the cylinder gives to the water while it cools. The right
side of this equation tells how much energy Q the water and aluminum cup absorb from the cylinder to warm
up. Because it is the same energy, they are equal.
What is known in this equation?
Mcyl
411.7 g, malum
46.5 g, malum+water
= 175 g
Can you find: mwater =? g
Twater = Talum = 20°C (water and cup of room temperature)
90°C, T; = 35°C (hot cylinder and cool "cylinder+cup+water" temperatures)
Tcyl
kCal
Calum = 0.22, Cwater
1 (specific heat of water and aluminum, measured in units
kg-°C
What are we looking for is Ccul - How we find it? Plug all the numbers into the equation (1), Ccul will be one
unknown which you can calculate from the equation. Important, convert all the masses from grams to kilograms!
After
you find Ccyl, compare it to known value for the copper 0.093(our cylinder is made out of copper).
|Ceyl -0.093|
% :
· 100%
0.093
arrow_forward
Newton's Law of cooling states that the rate at which heat is lost by a heated body is
proportional to the difference in temperature between the body and the surrounding
medium. Match the following statements/phrases with the corresponding item in the
drop down box. Choices in the box
1. In accordance with the stated law obove, we have the equation?
2. If a thermometer is taken outdoors where the temperoture is 5 deg C, from a
room in which the temperature is 20 deg C and the reading drops 10 deg C in one
minute, the working equation is?
3. In the obove problem, separoting the variables and integrating will result to?
4. In the obove problem, how long, in minutes, after its removal from the room will
the reading be 6 deg C?
5. In the obove problem, ofter 30 seconds, whot will be the thermometer reading?
5.2
dT(body temp)/dt = k(Temp of medium - 5)
dr(body temp)/dt = k(Temp of body - Temp of medium)
Temp of body = Cenkt +5
2.5
13.7
dr(body temp)/dt = k(Temp of medium - Temp of body)…
arrow_forward
Problem Statement
=
You install a heat pump to heat a cottage during the winter using the outside air as the heat
source. You wish to maintain the interior temperature of the cottage at 22°C. A simplified
model of the heat loss through the walls indicates that heat will need to be supplied at a
rate of 0.14(Tinterior - Texterior) where Q is the rate at which heat must be supplied to
the cottage (in kW), Tinterior is the interior air temperature (in C), and Texterior is the exterior
air temperature (in C). You have a 1kW electric motor available to run the heat pump.
What is the coldest winter day when the heat pump will be able to keep up to the heating
demand?
Answer Table
Stage
Description
Your Answer
Correct
Answer *
Due Date
Grade
(%)
Part
Weight Attempt Action/Message.
Type
1
Coldest outdoor temperature (°C)
Nov 7, 2024 11:59 pm
0.0
1
1/5
Submit
* Correct answers will only show after due date has passed.
arrow_forward
Handwritten solution required.
Strictly don't use chatgpt.
If you use chatgpt ,I will report the answer for sure.
Mechanical engineering dynamics.
arrow_forward
Help!!! Please answer all Correctly!!! Please
arrow_forward
Do not provide handwritten solution,Maintain accuracy and quality in your answer,Take care of plagiarism,Answer completely,You will get up vote for sure.
arrow_forward
SEE MORE QUESTIONS
Recommended textbooks for you
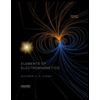
Elements Of Electromagnetics
Mechanical Engineering
ISBN:9780190698614
Author:Sadiku, Matthew N. O.
Publisher:Oxford University Press
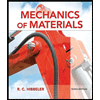
Mechanics of Materials (10th Edition)
Mechanical Engineering
ISBN:9780134319650
Author:Russell C. Hibbeler
Publisher:PEARSON
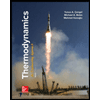
Thermodynamics: An Engineering Approach
Mechanical Engineering
ISBN:9781259822674
Author:Yunus A. Cengel Dr., Michael A. Boles
Publisher:McGraw-Hill Education
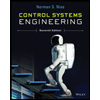
Control Systems Engineering
Mechanical Engineering
ISBN:9781118170519
Author:Norman S. Nise
Publisher:WILEY
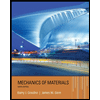
Mechanics of Materials (MindTap Course List)
Mechanical Engineering
ISBN:9781337093347
Author:Barry J. Goodno, James M. Gere
Publisher:Cengage Learning
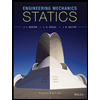
Engineering Mechanics: Statics
Mechanical Engineering
ISBN:9781118807330
Author:James L. Meriam, L. G. Kraige, J. N. Bolton
Publisher:WILEY
Related Questions
- Thermodynamics Please READ THE PROBLEM! I’m tired of posting the same problem over and over. please Read. This is what the asking for please: -1. sketch and label all your answers on the nozzle -2. Sketch and label all your answers on the process on a P-V diagram.... Thank youarrow_forwardHEAT TRANSFER CASE: I want to know what temperature in (°F) the cylinder will have inside. It's a heat transfer problem. what is T2 ? HEAT TRANSFER They gave me an answer all squashed together that i can't make sense of it. If you could help me makes sense of it thank you!arrow_forwardAn electric hot water heater consumes 3.1 kilowatts of electricity and converts it to heat. How long will it take the water heater to heat a 67 gallon tank of water from 10 degrees Celsius to 50 degrees Celsius? (1 kilogram of water is 0.37 gallons, 1 Calorie = 4200 J). It may be helpful to refer back to the weekly handout for guidance on this problem. Your final answer should be in minutes (rounded to the nearest 10 minutes).arrow_forward
- I want to briefly summarize what he is talking about and what you conclude. pls very urgentarrow_forwardTopics: Statics of Rigid Bodies, Equilibrium of Rigid Bodies, Equilibrium in Two Dimensions, etc. I will rate you with “LIKE/UPVOTE," if it is COMPLETE STEP-BY-STEP SOLUTION. If it is INCOMPLETE SOLUTION and there are SHORTCUTS OF SOLUTION, I will rate you with “DISLIKE/DOWNVOTE.” THANK YOU FOR YOUR HELP. PS: If you have answered this already, don’t answer it again; give chance to other experts to answer it. I want to verify if all of you will arrive in the same final answer; thats why I ask it multiple times. If you answer it again, i'll dislike all your entries/answers.arrow_forwardTopics: Statics of Rigid Bodies, Equilibrium of Rigid Bodies, Equilibrium in Two Dimensions, etc. I will rate you with “LIKE/UPVOTE," if it is COMPLETE STEP-BY-STEP SOLUTION. If it is INCOMPLETE SOLUTION and there are SHORTCUTS OF SOLUTION, I will rate you with “DISLIKE/DOWNVOTE.” THANK YOU FOR YOUR HELP. PS: If you have answered this already, don’t answer it again; give chance to other experts to answer it. I want to verify if all of you will arrive in the same final answer; thats why I ask it multiple times. If you answer it again, i'll dislike all your entries/answers.arrow_forward
- 1. The development of thermodynamics since the 17th century, which was pioneered by the invention of the steam engine in England, and was followed by thermodynamic scientists such as Willian Rankine, Rudolph Clausius, and Lord Kelvin in the 19th century. explain what the findings or theories of the 3 inventors are! Please answer fast max 25-30.minutes thank uarrow_forwardShow work Part 1 website: https://ophysics.com/r5.html PArt 2 website: https://ophysics.com/r3.htmlarrow_forwardThe left side of this equation tells how much energy Q the cylinder gives to the water while it cools. The right side of this equation tells how much energy Q the water and aluminum cup absorb from the cylinder to warm up. Because it is the same energy, they are equal. What is known in this equation? Mcyl 411.7 g, malum 46.5 g, malum+water = 175 g Can you find: mwater =? g Twater = Talum = 20°C (water and cup of room temperature) 90°C, T; = 35°C (hot cylinder and cool "cylinder+cup+water" temperatures) Tcyl kCal Calum = 0.22, Cwater 1 (specific heat of water and aluminum, measured in units kg-°C What are we looking for is Ccul - How we find it? Plug all the numbers into the equation (1), Ccul will be one unknown which you can calculate from the equation. Important, convert all the masses from grams to kilograms! After you find Ccyl, compare it to known value for the copper 0.093(our cylinder is made out of copper). |Ceyl -0.093| % : · 100% 0.093arrow_forward
- Newton's Law of cooling states that the rate at which heat is lost by a heated body is proportional to the difference in temperature between the body and the surrounding medium. Match the following statements/phrases with the corresponding item in the drop down box. Choices in the box 1. In accordance with the stated law obove, we have the equation? 2. If a thermometer is taken outdoors where the temperoture is 5 deg C, from a room in which the temperature is 20 deg C and the reading drops 10 deg C in one minute, the working equation is? 3. In the obove problem, separoting the variables and integrating will result to? 4. In the obove problem, how long, in minutes, after its removal from the room will the reading be 6 deg C? 5. In the obove problem, ofter 30 seconds, whot will be the thermometer reading? 5.2 dT(body temp)/dt = k(Temp of medium - 5) dr(body temp)/dt = k(Temp of body - Temp of medium) Temp of body = Cenkt +5 2.5 13.7 dr(body temp)/dt = k(Temp of medium - Temp of body)…arrow_forwardProblem Statement = You install a heat pump to heat a cottage during the winter using the outside air as the heat source. You wish to maintain the interior temperature of the cottage at 22°C. A simplified model of the heat loss through the walls indicates that heat will need to be supplied at a rate of 0.14(Tinterior - Texterior) where Q is the rate at which heat must be supplied to the cottage (in kW), Tinterior is the interior air temperature (in C), and Texterior is the exterior air temperature (in C). You have a 1kW electric motor available to run the heat pump. What is the coldest winter day when the heat pump will be able to keep up to the heating demand? Answer Table Stage Description Your Answer Correct Answer * Due Date Grade (%) Part Weight Attempt Action/Message. Type 1 Coldest outdoor temperature (°C) Nov 7, 2024 11:59 pm 0.0 1 1/5 Submit * Correct answers will only show after due date has passed.arrow_forwardHandwritten solution required. Strictly don't use chatgpt. If you use chatgpt ,I will report the answer for sure. Mechanical engineering dynamics.arrow_forward
arrow_back_ios
SEE MORE QUESTIONS
arrow_forward_ios
Recommended textbooks for you
- Elements Of ElectromagneticsMechanical EngineeringISBN:9780190698614Author:Sadiku, Matthew N. O.Publisher:Oxford University PressMechanics of Materials (10th Edition)Mechanical EngineeringISBN:9780134319650Author:Russell C. HibbelerPublisher:PEARSONThermodynamics: An Engineering ApproachMechanical EngineeringISBN:9781259822674Author:Yunus A. Cengel Dr., Michael A. BolesPublisher:McGraw-Hill Education
- Control Systems EngineeringMechanical EngineeringISBN:9781118170519Author:Norman S. NisePublisher:WILEYMechanics of Materials (MindTap Course List)Mechanical EngineeringISBN:9781337093347Author:Barry J. Goodno, James M. GerePublisher:Cengage LearningEngineering Mechanics: StaticsMechanical EngineeringISBN:9781118807330Author:James L. Meriam, L. G. Kraige, J. N. BoltonPublisher:WILEY
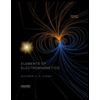
Elements Of Electromagnetics
Mechanical Engineering
ISBN:9780190698614
Author:Sadiku, Matthew N. O.
Publisher:Oxford University Press
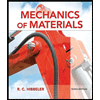
Mechanics of Materials (10th Edition)
Mechanical Engineering
ISBN:9780134319650
Author:Russell C. Hibbeler
Publisher:PEARSON
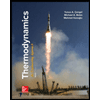
Thermodynamics: An Engineering Approach
Mechanical Engineering
ISBN:9781259822674
Author:Yunus A. Cengel Dr., Michael A. Boles
Publisher:McGraw-Hill Education
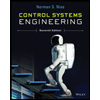
Control Systems Engineering
Mechanical Engineering
ISBN:9781118170519
Author:Norman S. Nise
Publisher:WILEY
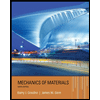
Mechanics of Materials (MindTap Course List)
Mechanical Engineering
ISBN:9781337093347
Author:Barry J. Goodno, James M. Gere
Publisher:Cengage Learning
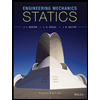
Engineering Mechanics: Statics
Mechanical Engineering
ISBN:9781118807330
Author:James L. Meriam, L. G. Kraige, J. N. Bolton
Publisher:WILEY