ME495 Lab 06_ Vibration Analysis Lab
pdf
keyboard_arrow_up
School
San Diego State University *
*We aren’t endorsed by this school
Course
495
Subject
Mechanical Engineering
Date
Apr 3, 2024
Type
Pages
14
Uploaded by ChiefDeerMaster1083
Heat Plate Exchanger
ME 495: Mechanical and Thermal Systems Lab
Section 05: Thursday
Group D
Authors: Soeung Khanitha, Smith Emilee, Sichantha Jack, Taylor Charles
Instructor: Dr. Hamid Nourollahi
Thursday, February 15, 2024
1
Table of Contents ( Khanitha Soeung )
Objective of Experiment ( Jack Sichantha )
..............................................................................
1
Equations and Symbols ( Khanitha Soeung & Jack Sichantha )
...........................................
2
Equipment ( Khanitha Soeung )
.................................................................................................
2
Experimental Procedure ( Khanitha Soeung )
..........................................................................
3
Experimental Results (Charles Taylor)
......................................................................................
6
Discussion of Results (Charles Taylor)
.....................................................................................
7
Lab Guide Questions (Emilee Smith)
.........................................................................................
9
Conclusion (Emilee Smith)
.......................................................................................................
10
References ( Khanitha Soeung )
..............................................................................................
10
Appendix ( Khanitha Soeung )
..................................................................................................
11
Table of Figures and Tables( Khanitha Soeung )
Figure 1: Vibration Analysis Unit (95-ME5 AI)
...........................................................................
2
Figure 2: Belt Drive Setup
...........................................................................................................
3
Figure 3: Belt Tension
.................................................................................................................
3
Figure 4: Sensor Placement
.......................................................................................................
6
Figure 5: Velocity of Vibrations for Motor
.................................................................................
7
Figure 6: Velocity of Vibrations for Bearing Support
...............................................................
7
Table 1: Lab Data
.........................................................................................................................
8
Objective of Experiment ( Jack Sichantha )
This lab experiment aims to introduce students to the 95-MEAI Vibration Analysis
Learning System. This demonstrates the use of vibration analysis for maintaining power
transmission components. Students will acquire practical skills such as using a vibration meter to
measure vibration, identifying measurement points on various power transmission systems,
analyzing the results, and minimizing the vibrations. Primarily this experiment will focus on
using the vibration meter to monitor the condition of a belt drive, enabling a timely correction to
prevent system failure. Both the horizontal and vertical readings are needed to detect any worn or
. stretched belts. The axial readings will help identify belt or shave misalignments. The main
2
objective is to establish a correlation between vibration direction as well as the underlying
effects. Velocity measurements are recommended due to the low rotational speeds of belt drives.
When measuring the belt drive vibration, readings should be taken on the bearing nearest to the
sheave, or if needed, on the motor, to ensure consistent sensor placement per measurement. The
team states that, for the motor and bearing alike, the defective belt will cause more vibrations
along the vertical and horizontal axes, while the sheave misalignment will likely increase the
vibration velocity in the axial direction.
Equations and Symbols ( Khanitha Soeung & Jack Sichantha )
No equations used throughout this experiment.
Equipment ( Khanitha Soeung )
Figure 1:
Vibration Analysis Unit (95-ME5 AI)
●
Amatrol 95-ME5-AI Vibration Analysis
○
Analyzes Vibrations in machinery and equipment.
○
Detects and measures the amplitude, frequency, as well as imbalance, misalignment, or
bearing wear as potential issues.
●
Vistec Hand-held Vibration Meter
○
Used for on the spot vibration measurement and analysis. This tool provides real time
readings of vibration levels.
●
Assorted Wrenches
Your preview ends here
Eager to read complete document? Join bartleby learn and gain access to the full version
- Access to all documents
- Unlimited textbook solutions
- 24/7 expert homework help
3
○
Basic tools used to tighten or loosen nuts & bolts during maintenance or repair task.
These tools vary in size to accommodate different fastener types.
●
Assorted Allen Wrenches
○
These tools are used for driving bolts & screws with hexagonal sockets. These are needed
to access and tighten fasteners in small spaces.
●
Extech 41893 Non-contact Digital Tachometer
○
This tool measures the rotational speed of machinery by using non-contact method, such
as laser, to help monitor machinery performance or diagnose issues related to speed
variations or any other abnormalities.
Experimental Procedure ( Khanitha Soeung )
Figure 2:
Belt Drive Setup
Figure 3:
Belt Tension
Before the setup, all loose clothing was tucked in, watches, and jewelry were removed.
Long hair was tied back and safety glasses were worn when the belt was in operation. The belt
drive was installed & aligned using an 18 inch straight edge to ensure the alignment of the two
4
sheaves, while ensuring the zerk fitting on the pillow block bearing closest to the sheave faced
away from the motor. An alignment check was performed by looking down the side of the
machine to ensure alignment of the two sheaves. With adjustments made if needed by loosening
the motor sheave, aligning it w/the bearing sheave by hand, and then retightening it. The belt
tension was set to 3-4 lbs using a tension tester and a straight edge for reference. All nuts & bolts
were securely fastened to prevent anything from coming loose during operation. The vibration
meter was configured by obtaining it from the storage location. Installing the magnet to the
accelerometer, pressing the ‘select’ button to turn it on, scrolling to select ‘ALL’ and ‘mm/s’ as
the units, and holding the button until the reading stabilized around a constant number, which
served as the recorded data. These steps ensured the safe and effective operation of the
machinery.
Baseline Directions
The lockout tag-out, which was a lock guarding the ‘ON’ switch, was removed from the
Amatrol device, and everyone was ensured to stand clear before starting the motor. The sensor of
the vibration meter was placed on the motor to measure horizontal vibration, and a velocity
(mm/s) reading was taken, ensuring that the sensor was parallel to the centerline of the two shafts
as shown in Figure 4 of the lab guide provided by Dr. Hamid Nourollahi. Measurements were
recorded on Table 2, with three runs conducted (n=3). This process was repeated for the sensor in
an almost vertical position on the motor. Then conducted again for both horizontal and vertical
positions on the bearing. An additional step involved converting the axial position
(perpendicular) of the bearing by placing the vibration meter ‘ON’ the bearing pillow block,
NOT the rotating sheave, with the measurement recorded on Table 2 as seen in the lab guide.
RPM readings were recorded one time (n=1) each for the motor and bearing sheaves using the
5
non-contact digital tachometer, by holding it steady and parallel to the ground while pointing it at
the reflective tape placed on each of the sheaves. The motor was then stopped, and the
lockout/tagout was installed as it must be when adjusting the belt or the sheaves.
Defective Belt
A plastic zip tie was installed around the belt, and any excess tail was trimmed off using a
pair of scissors. It was ensured that the knob of the zip tie was residing on top of the belt,
avoiding the placement on the belt’s side to prevent excessive vibration. In the event that the zip
tie snapped off the belt during operation, the belt drive was shut down, and then a new zip tie
was installed, ensuring all safety procedures were followed.
Parallel Misaligned Sheaves (with defective belt)
A ruler was used to misalign the sheaves very slightly ( less than one inch ) following
steps 3a and 3b in the lab guide. Ensuring they remained parallel it was ensured that the
misaligned motor sheave was not overhung the end of the rotating axle nor was it pushed flush
with the motor casting.
Parallel Misaligned Sheaves
The plastic tie was previously removed from the belt. Step 8b was repeated as instructed
in the lab guide. Once the experiment was completed, the belt was then removed from the
sheaves, all tools used were replaced, and the work area was cleaned up.
Your preview ends here
Eager to read complete document? Join bartleby learn and gain access to the full version
- Access to all documents
- Unlimited textbook solutions
- 24/7 expert homework help
6
Data Reduction
Figure 4:
Sensor Placement
After completing all the readings, the data was graphed and compared to analyze the
significance of the numbers obtained. Two separate graphs were created, one for the motor and
one for the bearing. The independent variable, representing the belt condition (baseline, zip tie,
zip tie w/misaligned, and misaligned), was plotted on the x-axis, while the dependent variable,
represented the vibrations, was plotted on the y-axis. For each graph, bars were added for each
direction measured. For instance, the bearing graph included bars for the x, y, and z direction.
Upon comparing all the graphs, various patterns and trends were observed indicating the impact
of different belt conditions on vibration levels. Detailed analysis was conducted to interpret these
findings and understand the implications.
7
Experimental Results (Charles Taylor)
Figure 5:
Velocity of Vibrations for Motor
Figure 6:
Velocity of Vibrations for Bearing Support
8
Table 1:
Lab Data
NOTE: No sample calculations were needed for this experiment’s data reduction. All data
analysis was done directly from the experimental results.
Discussion of Results (Charles Taylor)
Figure 5: Velocity of Vibrations for the Motor shows the magnitude of the vibrations in
both horizontal (parallel with belt) and vertical (perpendicular to belt) planes for the motor. Four
different sets of data were collected, one with a normal belt, one with a defect in the belt, one
with a misaligned belt, and one with both a misalignment and a defect. The data indicates that
the vertical and horizontal vibrations both saw a dramatic increase in magnitude in both tests
with the defective belt. Both vibration directions increased by about 5 or 6 mm/s to compare
data. As for the misalignment, this seemed to cause a slight increase in horizontal vibration,
while causing a slight decrease in vertical vibration.
Figure 6: Velocity of Vibrations for the Bearing Support shows the magnitude of the
vibrations in the horizontal (parallel with belt), vertical (perpendicular to belt), and axial (out of
Your preview ends here
Eager to read complete document? Join bartleby learn and gain access to the full version
- Access to all documents
- Unlimited textbook solutions
- 24/7 expert homework help
9
the plane from belt) planes for the bearing. Four sets of data were collected, one with a normal
belt, one with a defect in the belt, one with a misaligned belt, and one with both a misalignment
and a defect. The data indicates that the vertical vibrations saw a dramatic increase in magnitude
in both tests with the defective belt, increasing by about 7 mm/s to comparable trials. The defect
also seemed to slightly increase the vibrations along the horizontal axis. The misalignment
seemed to have little effect on either the vertical or horizontal vibrations. As for the axial
vibration, the misalignment, surprisingly, caused a decrease in the vibration magnitude. The
defect-only data showed a significantly higher axial vibration than any other data set. Using
Table 1.A from the Lab guide handout for Vibration Analysis, we can see that any Vibration
Velocity above 10.7 is considered severe. This means that, for the bearing and the motor, having
a defective belt will make the system unsafe and severely vibrational. This said the baseline (no
defect, properly aligned) for a majority of the data shown above indicates that the machine itself
already operates at a level between 5.4mm/s and 10.7mm/s which is still a very rough and
potentially damaging amount of vibration. The data shown above does not necessarily show a
large indication of error, however, the axial loading data shown in Figure 2, indicates that some
error may have occurred while measuring the vibration for the defect belt. Some sources of
possible errors are human error, including misreading the vibration meter or not tightening the
motor well enough. Some errors may also be systematic from the calibration of the machine or
the vibration meter. These results generally conclude that the axial vibration is more of a product
of the sheave misalignment, while the vertical and horizontal vibrations are more of a result of a
defect in the belt. This partially confirms the hypothesis stated in the objective. The hypothesis
stated that the defective belt would cause more vibrations along the vertical and horizontal axes,
while the sheave misalignment would likely engender more vibration in the axial direction.
10
While the data suggest that the correlations between these directions of vibration and belt issue
are true, the data inversely proves that misalignment causes additional vibration in the axial
direction, instead it causes a decrease in vibration velocity along the axial loading.
Lab Guide Questions (Emilee Smith)
1.
What are some potential causes of belt drive vibration?
The movement of the motor while it is running as well as the rotational speed can cause belt drive
vibration. A deviation of vibration from the baseline can indicate a problem with either the motor,
bearing, or belt, along with other parts of the system. Potential issues with misaligned shafts, an
unbalanced system, bearings that have been worn down or overstretched, can all cause more or less belt
drive vibration.
2.
Why is it important to measure vibration on a belt drive? Explain each direction.
Measuring the vibration on a belt drive regularly will allow for regular maintenance to prevent issues
before the system fails. This regular measurement can be compared to overall velocity guidelines and will
show whether the system is well aligned, has minor faults, or even whether it is unsafe to run altogether.
Measuring in different directions can help to indicate where the problem is coming from and what might
need to be checked or repaired. The readings taken vertically and horizontally can detect issues with the
belt, such as wear or excessive stretching. The measurements of vibration in the axial direction that are
taken on the bearing will show whether or not the belt of sheave is misaligned.
3.
Which measurement direction yielded the highest vibrations on the motor? Explain.
Overall, the highest vibrations on the motor were recorded in the horizontal direction. This is most likely
because the system is set up along the x-axis and the belt is pulling in the horizontal direction.
11
4.
Which measurement direction yielded the highest vibrations on the bearing? Explain.
The bearing, on average, yielded the highest vibration readings in the vertical direction. This could
potentially be due to the installation of the belt drive and the fittings holding down the sheave, putting a
vertical force on it.
5.
What are possible sources of error in your experiment?
The baseline measurement wouldn’t necessarily provide readings that would be similar to a well
balanced, well aligned system because it is used consistently for this experiment (unless routine
maintenance is done). Other sources of error include the vibration recordings as they were usually in a
range each time and a single number wasn’t always what was shown on the device, so the number it
stayed near the longest was the number that was recorded. Finally, the added defect (the zip tie) may be
put on differently by different people, possibly causing the vibration analysis to change slightly. However,
with the baseline reading, it was possible to still see a trend in the data and what types of affects different
defects or alignments might have on the vibration.
6.
Are the vibration readings on the motor and the bearings what you expected? If not, what
do you think the cause is?
Most of the readings were as I would expect, higher vibration readings for the different circumstances.
However, some readings were below or roughly the same as the baseline readings which was not what I
was expecting. The cause for a slightly lower, or similar vibration result with a misaligned sheave makes
sense now, because with the misalignment, the direction mostly affected is the axial direction. The
readings for the motor were done vertically and horizontally.
Conclusion (Emilee Smith)
The main objective of the experiment was to become familiar with the process of
vibration analysis for maintaining components of power transmission systems such as belt
Your preview ends here
Eager to read complete document? Join bartleby learn and gain access to the full version
- Access to all documents
- Unlimited textbook solutions
- 24/7 expert homework help
12
drives, sheaves, bearings, and other machine components. Measuring vibrations provides
information on the functionality of a system and the technique can be used to determine what
part of the system might need maintenance. The results of vibrational analysis can be compared
to the guidelines for vibration severity to determine functionality - whether the belt, sheaves, or
other various components of the system can be repaired or completely decommissioned. Per this
experiment, a defective belt or misaligned sheaves with a belt defect can be determined easily by
observing an increase in vibrational velocity on the bearing in the vertical direction. For
misaligned sheaves, the vibration analysis left little deviation in all directions for both the motor
and bearing measurements making it difficult to determine what direction the change in vibration
velocity correlates to this system component.
References ( Khanitha Soeung )
[1]
Nourollahi, A. (2024). ME-495 Laboratory Exercise – Number 6 –Vibration Analysis In
ME Dept, SDSU – Nourollahi. SDSU Publishing
[2]
Nourollahi, A. (2024). ME-495 Course Introduction_and Syllabus Spring 2024-1. In ME
Dept, SDSU – Nourollahi. SDSU Publishing
13
Appendix ( Khanitha Soeung )
Related Documents
Related Questions
Please solve this question
arrow_forward
Use Matlab
arrow_forward
dated metncpdf
Thermodynamics An Engineering X
E Module2-chap2propertiesofpure x
O File
C:/Users/DANIEL/Desktop/300L%202ND%20SEMESTER%20MATERIALS/Module2-chap2propertiesofpuresubstances-130703012604 phpap.
ID Page view
A Read aloud
V Draw
H Highlight
O Erase
40
MEC 451 - THERMODYNAMICS
Faculty of Mechanical Engineering, UITM
Supplementary Problems
The pressure in an automobile tire depends on the temperature of the air
in the tire. When the air temperature is 25°C, the pressure gage reads 210
kRa. If the volume of the tire is 0.025 m3, Cetermine the pressure rise in
the tire when the air temperature in the tire rises to 50°C. Also, determine
the amount of air that must be bled off to restore pressure to its original
value at this temperature. Assume the atmospheric pressure is 100 kPa.
[ 26 kPa, 0.007 kg]
1.
A 6 4 2:57 PM
Lucky CORER
144
Tum lock
314
%
8
1/2
24
6
1/4
23
T
K
F
pause
B
arrow_forward
Part I : Analysis of heat exchangers in engineering applications(max. 5 pages)Select any thermal energy system you are interested. Describe the system and statehow the system works. The system should have at least one heat exchanger.Analyse the design of the heat exchangers and their functions in the system. Part Iand Part II are connected. Select a system you are able to complete the exergyanalysis in Part II.Part II: Exergy analysis & performance optimisation of heat exchangersfor a thermal energy system (max. 5 pages)Perform exergy analysis and performance optimization of the thermal energy systemin Part I. For the above question, the thermal energy system i have chosen is a steam rankine cycle, so for part II, i would like exergy analysis and performance optimistaion to be done 3 times over for a steam rankine cycle, show full working calculations for each and explanations. Provide references for any values used.
arrow_forward
Part I : Analysis of heat exchangers in engineering applications(max. 5 pages)Select any thermal energy system you are interested. Describe the system and statehow the system works. The system should have at least one heat exchanger.Analyse the design of the heat exchangers and their functions in the system. Part Iand Part II are connected. Select a system you are able to complete the exergyanalysis in Part II.Part II: Exergy analysis & performance optimisation of heat exchangersfor a thermal energy system (max. 5 pages)Perform exergy analysis and performance optimization of the thermal energy systemin Part I.
arrow_forward
HEAT TRANSFER
CASE: I want to know what temperature in (°F) the cylinder will have inside. It's a heat transfer problem.
what is T2 ?
HEAT TRANSFER
They gave me an answer all squashed together that i can't make sense of it. If you could help me makes sense of it thank you!
arrow_forward
answer and feedback attached, can show steps more clearly please
arrow_forward
Part d-f
arrow_forward
You are working in a biology lab during your summer break. Your supervisor asks you to perform an experiment to find the effective spring constant
(in N/m) of a partial molecule of DNA (deoxyribonucleic acid). You perform experiments and find that a single straight portion of a DNA molecule is
2.19 μm long. You then perform an activity that charges the ends of the molecule; each end becomes singly ionized: negative on one end, positive on
the other. After the ends are charged, the molecule shrinks by 1.31% of its length.
1.21e-9
arrow_forward
answer the questions and explain all of it in words. Ignore where it says screencast and in class explanation
arrow_forward
This problem is (16.23) from a book "Thermodynamics and Statistical Mechanics An Integrated Approach by M. Scott Shell"
arrow_forward
Answer the following questions fully
arrow_forward
I asked bartleby to solve this question earlier, it gave me AI answer which is completely different to what's shown in this answer. I don't know which one is correct now. I have attached screenshots of the AI answer. Can you clarify which is correct. Also I previously asked about pv diagram and you said ' the curve in the explanation is correct', did you mean in your explanation or the one I showed as an example? Please advice
arrow_forward
V:01
Expert Q&A
Done
Question 1: In your own words, write down the differences
between thermodynamic and heat transfer. (3 Marks)
Question 2: Estimate the heat loss per square metre of surface
through a brick wall 0.5 m thick when the inner surface is at 400
K and the outside surface is at 300 K. The thermal conductivity
of the brick may be taken as 0.7 W/mK. (2 Marks)
Question 3: A furnace is constructed with 0.20 m of firebrick,
0.10 m of insulating brick, and 0.20 m of building brick. The
inside temperature is 1200 K and the outside temperature is 330
K. If the thermal conductivities are as shown in the figure below,
estimate the heat loss per unit area. (5 Marks)
1200 K
330 K
Insulating
brick
X-0.10m
k= 0.21
Ordinary
brick
X=0.20 m
Fire brick
X= 0.20 m
k= 1.4
k= 0.7
(W/mK)
arrow_forward
Τρ
סוי
D2L Notes de cours 2 - MA...
D2L Solutions d'examen -...
B https://uottawa.brights...
ChatGPT
← Homework 4 - Fall 2024
Question 6 of 6
<
View Policies
education.wiley.com
ELG 3736 - Google Docs
On mesure la traînée s...
WP Homework 4 - Fall 2024
X W Question 6 of 6 - Hom...
- / 20
0
Current Attempt in Progress
A small ball is projected horizontally toward an incline as shown. Determine the slant range R. The initial speed is vo = 18 m/s, and the
coefficient of restitution for the impact at A is e = 0.85.
VO
Answer: R =
34°
eTextbook and Media
Save for Later
R
m
B
Attempts: 0 of 1 used
Submit Answer
arrow_forward
Τρ
סוי
D2L Notes de cours 2 - MA...
D2L Solutions d'examen -...
B https://uottawa.brights...
ChatGPT
← Homework 4 - Fall 2024
Question 5 of 6
<
View Policies
education.wiley.com
ELG 3736 - Google Docs
On mesure la traînée s...
WP Homework 4 - Fall 2024
X W Question 5 of 6 - Hom...
- / 20
0
Current Attempt in Progress
If the center of the ping-pong ball is to clear the net as shown, at what height h should the ball be horizontally served? Also determine
h2. The coefficient of restitution for the impacts between ball and table is e = 0.71, and the radius of the ball is r = 0.75 in.
T
✓
Answers:
h =
in.
h2=
eTextbook and Media
Save for Later
in.
Attempts: 0 of 1 used
Submit Answer
arrow_forward
Τρ
סוי
D2L Notes de cours 2 - MA...
D2L Solutions d'examen -...
B https://uottawa.brights...
ChatGPT
← Homework 4 - Fall 2024
Question 2 of 6
<
View Policies
education.wiley.com
ELG 3736 - Google Docs
On mesure la traînée s...
WP Homework 4 - Fall 2024
X W Question 2 of 6 - Hom...
- / 20
0
Current Attempt in Progress
The force P, which is applied to the 15.6-kg block initially at rest, varies linearly with the time as indicated. If the coefficients of static
and kinetic friction between the block and the horizontal surface are 0.38 and 0.30, respectively, determine the velocity of the block
when t = 3.7 s.
15.6 kg
93
P
P. N
Hg=
= 0.38
=0.30
0
S
3.7
Answer: v= i
eTextbook and Media
Save for Later
m/s
Attempts: 0 of 1 used
Submit Answer
Π
-120
arrow_forward
SEE MORE QUESTIONS
Recommended textbooks for you
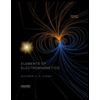
Elements Of Electromagnetics
Mechanical Engineering
ISBN:9780190698614
Author:Sadiku, Matthew N. O.
Publisher:Oxford University Press
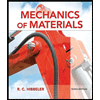
Mechanics of Materials (10th Edition)
Mechanical Engineering
ISBN:9780134319650
Author:Russell C. Hibbeler
Publisher:PEARSON
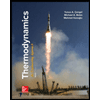
Thermodynamics: An Engineering Approach
Mechanical Engineering
ISBN:9781259822674
Author:Yunus A. Cengel Dr., Michael A. Boles
Publisher:McGraw-Hill Education
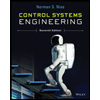
Control Systems Engineering
Mechanical Engineering
ISBN:9781118170519
Author:Norman S. Nise
Publisher:WILEY
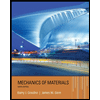
Mechanics of Materials (MindTap Course List)
Mechanical Engineering
ISBN:9781337093347
Author:Barry J. Goodno, James M. Gere
Publisher:Cengage Learning
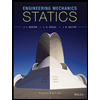
Engineering Mechanics: Statics
Mechanical Engineering
ISBN:9781118807330
Author:James L. Meriam, L. G. Kraige, J. N. Bolton
Publisher:WILEY
Related Questions
- Please solve this questionarrow_forwardUse Matlabarrow_forwarddated metncpdf Thermodynamics An Engineering X E Module2-chap2propertiesofpure x O File C:/Users/DANIEL/Desktop/300L%202ND%20SEMESTER%20MATERIALS/Module2-chap2propertiesofpuresubstances-130703012604 phpap. ID Page view A Read aloud V Draw H Highlight O Erase 40 MEC 451 - THERMODYNAMICS Faculty of Mechanical Engineering, UITM Supplementary Problems The pressure in an automobile tire depends on the temperature of the air in the tire. When the air temperature is 25°C, the pressure gage reads 210 kRa. If the volume of the tire is 0.025 m3, Cetermine the pressure rise in the tire when the air temperature in the tire rises to 50°C. Also, determine the amount of air that must be bled off to restore pressure to its original value at this temperature. Assume the atmospheric pressure is 100 kPa. [ 26 kPa, 0.007 kg] 1. A 6 4 2:57 PM Lucky CORER 144 Tum lock 314 % 8 1/2 24 6 1/4 23 T K F pause Barrow_forward
- Part I : Analysis of heat exchangers in engineering applications(max. 5 pages)Select any thermal energy system you are interested. Describe the system and statehow the system works. The system should have at least one heat exchanger.Analyse the design of the heat exchangers and their functions in the system. Part Iand Part II are connected. Select a system you are able to complete the exergyanalysis in Part II.Part II: Exergy analysis & performance optimisation of heat exchangersfor a thermal energy system (max. 5 pages)Perform exergy analysis and performance optimization of the thermal energy systemin Part I. For the above question, the thermal energy system i have chosen is a steam rankine cycle, so for part II, i would like exergy analysis and performance optimistaion to be done 3 times over for a steam rankine cycle, show full working calculations for each and explanations. Provide references for any values used.arrow_forwardPart I : Analysis of heat exchangers in engineering applications(max. 5 pages)Select any thermal energy system you are interested. Describe the system and statehow the system works. The system should have at least one heat exchanger.Analyse the design of the heat exchangers and their functions in the system. Part Iand Part II are connected. Select a system you are able to complete the exergyanalysis in Part II.Part II: Exergy analysis & performance optimisation of heat exchangersfor a thermal energy system (max. 5 pages)Perform exergy analysis and performance optimization of the thermal energy systemin Part I.arrow_forwardHEAT TRANSFER CASE: I want to know what temperature in (°F) the cylinder will have inside. It's a heat transfer problem. what is T2 ? HEAT TRANSFER They gave me an answer all squashed together that i can't make sense of it. If you could help me makes sense of it thank you!arrow_forward
- answer and feedback attached, can show steps more clearly pleasearrow_forwardPart d-farrow_forwardYou are working in a biology lab during your summer break. Your supervisor asks you to perform an experiment to find the effective spring constant (in N/m) of a partial molecule of DNA (deoxyribonucleic acid). You perform experiments and find that a single straight portion of a DNA molecule is 2.19 μm long. You then perform an activity that charges the ends of the molecule; each end becomes singly ionized: negative on one end, positive on the other. After the ends are charged, the molecule shrinks by 1.31% of its length. 1.21e-9arrow_forward
- answer the questions and explain all of it in words. Ignore where it says screencast and in class explanationarrow_forwardThis problem is (16.23) from a book "Thermodynamics and Statistical Mechanics An Integrated Approach by M. Scott Shell"arrow_forwardAnswer the following questions fullyarrow_forward
arrow_back_ios
SEE MORE QUESTIONS
arrow_forward_ios
Recommended textbooks for you
- Elements Of ElectromagneticsMechanical EngineeringISBN:9780190698614Author:Sadiku, Matthew N. O.Publisher:Oxford University PressMechanics of Materials (10th Edition)Mechanical EngineeringISBN:9780134319650Author:Russell C. HibbelerPublisher:PEARSONThermodynamics: An Engineering ApproachMechanical EngineeringISBN:9781259822674Author:Yunus A. Cengel Dr., Michael A. BolesPublisher:McGraw-Hill Education
- Control Systems EngineeringMechanical EngineeringISBN:9781118170519Author:Norman S. NisePublisher:WILEYMechanics of Materials (MindTap Course List)Mechanical EngineeringISBN:9781337093347Author:Barry J. Goodno, James M. GerePublisher:Cengage LearningEngineering Mechanics: StaticsMechanical EngineeringISBN:9781118807330Author:James L. Meriam, L. G. Kraige, J. N. BoltonPublisher:WILEY
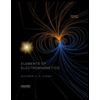
Elements Of Electromagnetics
Mechanical Engineering
ISBN:9780190698614
Author:Sadiku, Matthew N. O.
Publisher:Oxford University Press
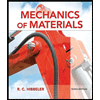
Mechanics of Materials (10th Edition)
Mechanical Engineering
ISBN:9780134319650
Author:Russell C. Hibbeler
Publisher:PEARSON
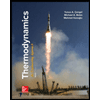
Thermodynamics: An Engineering Approach
Mechanical Engineering
ISBN:9781259822674
Author:Yunus A. Cengel Dr., Michael A. Boles
Publisher:McGraw-Hill Education
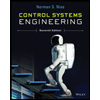
Control Systems Engineering
Mechanical Engineering
ISBN:9781118170519
Author:Norman S. Nise
Publisher:WILEY
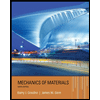
Mechanics of Materials (MindTap Course List)
Mechanical Engineering
ISBN:9781337093347
Author:Barry J. Goodno, James M. Gere
Publisher:Cengage Learning
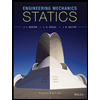
Engineering Mechanics: Statics
Mechanical Engineering
ISBN:9781118807330
Author:James L. Meriam, L. G. Kraige, J. N. Bolton
Publisher:WILEY