ME495 Lab 01_ Brayton Cycle
pdf
keyboard_arrow_up
School
San Diego State University *
*We aren’t endorsed by this school
Course
495
Subject
Mechanical Engineering
Date
Apr 3, 2024
Type
Pages
19
Uploaded by ChiefDeerMaster1083
Brayton Cycle
ME 495: Mechanical and Thermal Systems Lab
Section 05: Thursday
Group D
Authors: Soeung Khanitha, Smith Emilee, Sichantha Jack, Taylor Charles
Instructor: Dr. Hamid Nourollahi
Experiment Performed, Date: Thursday, March 14th, 2024
Report Due, Date: Thursday, March 21, 2024
1
Table of Contents
Objective of Experiment (Khanitha Soeung)
.................................................................................................
2
Equations and Symbols (Emilee Smith)
....................................................................................
3
Equipment (Khanitha Soeung)
.......................................................................................................................
3
Experimental Setup (Khanitha Soeung, Jack Sichantha)
...............................................................................
5
Experimental Procedure (Khanitha Soeung & Jack Sichantha)
.....................................................................
5
Experimental Results (Jack Sichantha & Emilee Smith & Charles Taylor)
..................................................
6
Discussion of Results (Charles Taylor)
........................................................................................................
14
Conclusion (Charles Taylor )
.......................................................................................................................
14
References ( Khanitha Soeung )
...................................................................................................................
15
Appendix
......................................................................................................................................................
15
List of Figures
Brayton Cycle
..........................................................................................................................
0
Figure 1: Axial flow gas turbine manufactured by Armfield Tech. Ltds
................................................
5
Figure 2: Actual Brayton P-V for Sample 1
..............................................................................
7
Figure 3: Actual Brayton T-S for Sample 1
..............................................................................
7
Figure 5: Actual Brayton T-S for Sample 2
..............................................................................
8
Figure 7: Actual Brayton T-S for Sample 3
..............................................................................
9
Figure 9: Actual Brayton T-S for Sample 4
............................................................................
10
Figure 11: Actual Brayton T-S for Sample 5
...........................................................................
11
Figure 12: Ideal Brayton T-S
..................................................................................................
12
Figure 13: Ideal Brayton P-V
.................................................................................................
12
List of Tables
Table 1: Equations
.............................................................................................................................
3
Table 2: Thermal Efficiency of Brayton Cycle for Each Engine Speed
.........................................
12
Table 3: First law analysis of each section at each engine speed
...................................
13
Table 4: Back Work Ratio for each engine speed
............................................................
13
2
Objective of Experiment (Khanitha Soeung)
The objective of this laboratory exercise is to acquire hands-on experience with the Brayton
cycle, a thermodynamic cycle that describes the operation of gas turbines, by using empirical data from a
Model CM14 Axial Flow gas turbine as well as referencing Lab 01 procedure and guides provide by
Dr.Nourollahi The Brayton cycle is comprised of four main processes: compression, combustion,
expansion, and exhaust.
During the compression process, air is compressed by the compressor section of the gas turbine.
The compressed air then enters the combustion chamber where fuel is added and combustion occurs,
leading
to
a
significant
increase
in
temperature
and
pressure.
Subsequently,
the
high-pressure,
high-temperature gas expands through the turbine section, producing thrust or shaft work. Finally, the
exhaust gasses are expelled from the system.
The cold-air-standard assumption is often used in the analysis of gas turbine cycles, assuming that
the air behaves as an ideal gas with constant specific heats throughout the cycle and neglecting any heat
transfer with the surroundings.
The team aims to validate the theoretical Brayton cycle model against empirical measurements
obtained from the gas turbine, thereby affirming the cycle's applicability in practical gas turbine systems.
By comparing the theoretical predictions with actual experimental data, the team can assess the accuracy
of the Brayton cycle model and gain insights into the performance characteristics of the gas turbine under
various operating conditions. This validation process contributes to a deeper understanding of gas turbine
operation and enhances the ability to design, optimize, and analyze such systems for various applications,
including aircraft and ship propulsion and power generation. The team hypothesizes that the errors will be
primarily systematic during this process because the data is driven primarily by machine instead of
human. The team also hypothesizes that data will be most efficient in the section of no pressure change,
e.i. between points 2,3 and 1,4.
Your preview ends here
Eager to read complete document? Join bartleby learn and gain access to the full version
- Access to all documents
- Unlimited textbook solutions
- 24/7 expert homework help
3
Equations and Symbols (Emilee Smith)
Table 1: Equations
Equation 1: Thermal Efficiency
η
?ℎ,???𝑦???
= 1 −
1
?
?
(𝑘−1)/𝑘
Equation 2: Pressure Ratio
?
?
= ?
2
/?
1
Equation 3: Specific Heat Ratio
𝑘 = 1. 4
Equation 4: Back work ratio
?
?𝑤
=
𝑤
??𝑀?,𝑖?
𝑊
??𝑅?,???
Equation 5: First Law for Compressor
− 𝑤
?
= ?
?,?
(?
?,???
− ?
?,𝑖?
)
Equation 6: Efficiency of the Compressor
η
?
=
?
???,?
−?
𝑖?
?
???,?
−?
𝑖?
Equation 7
?
?
= ?
?,?
(?
?,???
− ?
?,𝑖?
)
Equation 8: First Law for Turbine
− 𝑤
?
= ?
?,?
(?
?,???
− ?
?,𝑖?
)
Equation 9: Efficiency of Turbine
η
?
=
?
???,?
−?
𝑖?
?
???,?
−?
𝑖?
Equipment (Khanitha Soeung)
●
Model CM14 Axial Flow Gas Turbine
○
Main component of the experiment, representing a simple gas turbine engine to study the
Brayton cycle.
●
Transparent Polycarbonate Safety Screen
○
Provides protection by enclosing the engine and preventing contact with moving parts.
4
●
Fuel Tank with Aeroshell 500 Turbine Oil Mixture
○
Supplies fuel to the engine for combustion during operation.
●
Electronic Console
○
Controls the engine operation and facilitates data acquisition for analysis.
●
PC with Armfield Software
○
Monitors engine performance, collects data, and aids in analysis of experimental results.
●
Sensors
○
Measure various parameters such as temperature, pressure, shaft speed, and thrust to
provide data for analysis.
●
Ear Protection Gear
○
Ensures safety by reducing exposure to loud engine noise during operation.
●
Power Outlet and Cord
○
Supplies electrical power to the Electronic Console for operation.
●
Data Recording Tools (Manual Sampling Button, Integrated Spreadsheet)
○
Facilitate data collection during engine operation for analysis.
5
Experimental Setup (Khanitha Soeung)
Figure 1: Axial flow gas turbine manufactured by Armfield Tech. Ltds.
Experimental Procedure (Khanitha Soeung & Jack Sichantha)
This procedure is entirely in reference to the lab guide manual in combination with the team’s experience
during the lab experiment. This manual is referenced in the references section of this report as reference
[1]. In the laboratory experiment, the Professor and TA guided the team through the inspection procedure.
They inspected the compressor/turbine for free rotation and ensured no obstructions were present in front
of the CM-14 engine's intake or exhaust. Fuel and oil levels were checked, and the transparent
polycarbonate safety screen was securely fitted and clamped. Any spilled fuel around the plinth was also
checked and cleared. The red button on the Electronic Console was kept off, and the console was
connected to a power outlet using the supplied cord, with a USB cable connected to the PC. The full fuel
tank was positioned appropriately, and the Armfield software was activated on the PC, displaying useful
Your preview ends here
Eager to read complete document? Join bartleby learn and gain access to the full version
- Access to all documents
- Unlimited textbook solutions
- 24/7 expert homework help
6
engine readings. Before starting the engine, the "zero buttons" were clicked on all sensor edit fields to
compensate for any residual sensor errors. Following the correct sequence, the engine was started by
clicking the 'Power On', 'Enable', and 'Start' buttons on the PC screen. The startup sequence was initiated,
and upon clicking the 'Start' button, the electric starter attempted to start the engine after a delay. Samples
were taken using the manual sampling button in the Armfield software, and subsequent runs were
conducted as per the professor's instructions. Specific graphs were displayed using the 'View Graph'
button, and after data collection, the engine was powered down using the appropriate controls. Results
were collected and recorded in the 'Table' section of the Armfield software for analysis.
Experimental Results (Jack Sichantha & Emilee Smith & Charles Taylor)
1.
Provide a T – s diagram and a P – v diagram for the ideal and actual Brayton cycle for each test
speed.
7
Figure 2: Actual Brayton P-V for Sample 1
Figure 3: Actual Brayton T-S for Sample 1
Figure 4: Actual Brayton P-V for Sample 2
8
Figure 5: Actual Brayton T-S for Sample 2
Figure 6: Actual Brayton P-V for Sample 3
Your preview ends here
Eager to read complete document? Join bartleby learn and gain access to the full version
- Access to all documents
- Unlimited textbook solutions
- 24/7 expert homework help
9
Figure 7: Actual Brayton T-S for Sample 3
Figure 8: Actual Brayton P-V for Sample 4
10
Figure 9: Actual Brayton T-S for Sample 4
Figure 10: Actual Brayton P-V for Sample 5
11
Figure 11: Actual Brayton T-S for Sample 5
Ideal Plots:
Your preview ends here
Eager to read complete document? Join bartleby learn and gain access to the full version
- Access to all documents
- Unlimited textbook solutions
- 24/7 expert homework help
12
Figure 12: Ideal Brayton T-S
Figure 13: Ideal Brayton P-V
2.
Calculate the thermal efficiency for the Brayton cycle for each engine speed.
a.
η
?ℎ,???𝑦???
= 1 −
1
?
?
(𝑘−1)/𝑘
Table 2: Thermal Efficiency of Brayton Cycle for Each Engine Speed
Sample
Thermal Efficiency
1
0.560
2
0.547
3
0.557
4
0.553
5
0.550
Example Calculation
Run 1:
?
?
= ?
2
/?
1
= 46. 39/2. 6 = 17. 72
13
η
?ℎ,???𝑦???
= 1 −
1
?
?
(𝑘−1)/𝑘
= 1 −
1
17.72
(1.4−1)/1.4
= 0. 560
3.
Perform a first law analysis of each section of the CM-14 engine at each engine speed.
Table 3: First law analysis of each section at each engine speed
4.
Calculate the efficiency of the compressor section and turbine section for each engine speed. This
experiment must be carried out with the engine and the flow in stationary condition. To facilitate
the capture of data with meaningful value of the efficiency for all the engine stages the mimic
diagram has been modified.
Table 4: Efficiencies for each speed
5.
Calculate the back work ratio for each engine speed.
14
Table 5: Back Work Ratio for each engine speed
Back work ratio:
?
?𝑤
=
𝑤
??𝑀?,𝑖?
𝑊
??𝑅?,???
Discussion of Results (Charles Taylor)
The diagrams for T-S and P-V as shown represent the analytical solution to the actual data for each of the
plots made. When these are compared to figures 12 and 13, the ideal P-V and T-S diagrams, many
extrapolations can be made. This includes the fact that these plots show a large amount of systematic error
within the data, because they show repeated error that manifests in the same way at each engine speed.
The thermal efficiency table, Table 2, shows the different thermal efficiency at each engine speed and
sample number. The first law analysis of each system for the compressor, combustion and the turbine are
represented in the first law work equations shown in table 1. These values are calculated for each dataset
within the points 1 and 2 for compressor, 2 and 3 for combustion and 3 and 4 for turbine.
The back work ratio is a function of the work outputs for the turbine and the compressor. This is then
calculated by dividing these works to achieve a ratio.
There are many possible sources of error within this experiment. Based on the data discussed above it is
likely that this experiment involves more systematic errors than human errors. This is because most of the
errors are repeated as opposed to random, inconsistent errors. Some examples of these errors in the data
are the T-S and P-V diagrams when compared to the ideal diagrams. Possible reasons for these systematic
Your preview ends here
Eager to read complete document? Join bartleby learn and gain access to the full version
- Access to all documents
- Unlimited textbook solutions
- 24/7 expert homework help
15
errors include the software only being the academic version of the data taking program, only performing 1
trial for each sample engine speed, and not performing the experiment in a temperature controlled
environment. These factors may have affected the data drastically and systematically throughout the
entire experiment. The team’s hypothesis stated that the error will be primarily systematic which is
absolutely proven true. The team also hypothesized that the areas without pressure change would have the
highest efficiencies, this was true.
Conclusion (Charles Taylor )
Based on the data collected within this experiment the team’s hypothesis held true for both
statements. The data also showed a large congregation of systematic error within the areas
primarily regarding the compression and turbine chambers. These likely had high amounts of
error due to the academic level of software used to extract this data from the turbine and
compressor. The objective of this experiment was to determine the efficiencies and back work
ratios for each of the different engine speeds tested for within the dataset. This was accomplished
both in the report and in the experiment itself. The team concludes that if this experiment were to
be done again, it is recommended that the team spends more time discussing the theory around
finding the efficiencies and the ideal values of the data with the lab guide, professor and TA. This
would aid in the team’s expression of the dataset and likely allow them to understand the data
which is being reduced more.
References ( Khanitha Soeung )
[1]
Nourollahi, A. (2024). ME-495 Laboratory Exercise – Number 1 Brayton Cycle
In ME Dept,
SDSU – Nourollahi. SDSU Publishing
16
[2]
Nourollahi, A. (2024). ME-495 Course Introduction_and Syllabus Spring 2024-1. In ME Dept,
SDSU – Nourollahi. SDSU Publishing
17
Appendix
N/A
Your preview ends here
Eager to read complete document? Join bartleby learn and gain access to the full version
- Access to all documents
- Unlimited textbook solutions
- 24/7 expert homework help
18
Related Documents
Related Questions
answer and feedback attached, can show steps more clearly please
arrow_forward
I asked bartleby to solve this question earlier, it gave me AI answer which is completely different to what's shown in this answer. I don't know which one is correct now. I have attached screenshots of the AI answer. Can you clarify which is correct. Also I previously asked about pv diagram and you said ' the curve in the explanation is correct', did you mean in your explanation or the one I showed as an example? Please advice
arrow_forward
Problem Statement
=
You install a heat pump to heat a cottage during the winter using the outside air as the heat
source. You wish to maintain the interior temperature of the cottage at 22°C. A simplified
model of the heat loss through the walls indicates that heat will need to be supplied at a
rate of 0.14(Tinterior - Texterior) where Q is the rate at which heat must be supplied to
the cottage (in kW), Tinterior is the interior air temperature (in C), and Texterior is the exterior
air temperature (in C). You have a 1kW electric motor available to run the heat pump.
What is the coldest winter day when the heat pump will be able to keep up to the heating
demand?
Answer Table
Stage
Description
Your Answer
Correct
Answer *
Due Date
Grade
(%)
Part
Weight Attempt Action/Message.
Type
1
Coldest outdoor temperature (°C)
Nov 7, 2024 11:59 pm
0.0
1
1/5
Submit
* Correct answers will only show after due date has passed.
arrow_forward
Answer the following questions fully
arrow_forward
Needs Complete typed solution with 100 % accuracy.
arrow_forward
Please I want a detailed explanation of the energy method rule placed in the first line and how these numbers appeared to us. I want a detailed explanation please urgent .
arrow_forward
bliuzodt to mopolb
9. If machine parts are degreased by means of kerosene as shown in the diagram,
how much kerosene make-up is needed per day? How much kerosene has to enter
the degreasing vat per day? There are about 3 lb of grease per 100 lb of machine
parts, and 60 tons of machine parts are processed each day. Five thousand pounds
of kerosene (the 10% solution) are carried away by the machine parts each day
but drip off and are caught and put back in the degreasing vat. Two hundred
pounds of the 10% solution are lost each day from the vat by evaporation, spillage,
or by being carried away.
arrow_forward
D2L MCG3740_Final_2018 - MC...
D2L Accueil - Université d'Ottaw...
← Homework 6 - Fall 2024
Τρ
Question 3 of 4
<
סוי
education.wiley.com
Sephora
G formule vitesse angulaire en...
WP Homework 6 - Fall 2024
X WP Question 3 of 4 - Homewor...
Mail - Pierre Sarr - Outlook
- / 10
0
Current Attempt in Progress
For the instant represented, crank OB has a clockwise angular velocity w = 1.22 rad/sec and is passing the horizontal position.
Determine the corresponding magnitudes of the velocity of the guide roller A in the 22° slot and the velocity of point C midway
between A and B.
15"
7
C. 32"
AO
22%
B
Answers:
VA =
VC =
-
eTextbook and Media
Save for Later
in./sec
in./sec
Attempts: 0 of 1 used
Submit Answer
arrow_forward
Which of the following formulas describe the thermal efficiency of a cycle?
Select all that applies.
1 - qin/qout
worknet/qout
worknet/qin
1 - qout/qin
arrow_forward
Algenib
Sherately
Alpher
Sche
M
فرع واحد
/ تدلا سؤال/
Q1/Write a notes on heat balance sheet, draw that on the energy flow and enhance your answers
with equations.
2:2
Q2/An indicator diagram taken from a single cylinder four stroke, compression ignition engine has
a length of 100/mm and an area of 2045 mm². The indicator pointer deflects a distance of 10 mm for
a pressure increment of 2 bar in the cylinder. If the bore and stroke of the engine cylinder are both
100 mm and the engine speed is 900 rev/min, calculate the mean effective pressure and the indicated
power. If the mechanical efficiency is 0.75, what is the brake power developed. Draw the indicator
diagram.)
ip or bif
03 A diesel engine develops 5kW. Its indicated thermal efficiency is 0.3 and mechanical efficiency
0.75. Estimate the fuel consumption of engine in (a) Kg/hr (b) liters/hr (c) indicated specific fuel
consumption and (d) brake specific fuel consumption. Take heat value of fuel 42000 kJ/Kg and
density of fuel 0.87…
arrow_forward
Solve show all steps and solution. Energy systems engineering
arrow_forward
Please solve this question
arrow_forward
Part I : Analysis of heat exchangers in engineering applications(max. 5 pages)Select any thermal energy system you are interested. Describe the system and statehow the system works. The system should have at least one heat exchanger.Analyse the design of the heat exchangers and their functions in the system. Part Iand Part II are connected. Select a system you are able to complete the exergyanalysis in Part II.Part II: Exergy analysis & performance optimisation of heat exchangersfor a thermal energy system (max. 5 pages)Perform exergy analysis and performance optimization of the thermal energy systemin Part I. For the above question, the thermal energy system i have chosen is a steam rankine cycle, so for part II, i would like exergy analysis and performance optimistaion to be done 3 times over for a steam rankine cycle, show full working calculations for each and explanations. Provide references for any values used.
arrow_forward
Part I : Analysis of heat exchangers in engineering applications(max. 5 pages)Select any thermal energy system you are interested. Describe the system and statehow the system works. The system should have at least one heat exchanger.Analyse the design of the heat exchangers and their functions in the system. Part Iand Part II are connected. Select a system you are able to complete the exergyanalysis in Part II.Part II: Exergy analysis & performance optimisation of heat exchangersfor a thermal energy system (max. 5 pages)Perform exergy analysis and performance optimization of the thermal energy systemin Part I.
arrow_forward
An electric hot water heater consumes 3.1 kilowatts of electricity and converts it to heat. How long will it take the water heater to heat a 67 gallon tank of water from 10 degrees Celsius to 50 degrees Celsius? (1 kilogram of water is 0.37 gallons, 1 Calorie = 4200 J). It may be helpful to refer back to the weekly handout for guidance on this problem.
Your final answer should be in minutes (rounded to the nearest 10 minutes).
arrow_forward
SCH 08 HW
PSS 8.1: Static equilibrium problems
To practice Problem Solving Strategy 8.1 Static
equilibrium problems.
When you at an object by moving only your forearm, the
main lining muscle in your arm is the biceps. Suppose
the mass of a forearm is 1.20 kg. If the biceps is
connected to the forearm a distance du-3.50 cen
from the elbow, how much force F must the biceps
exert to hold a 750 g bal at the end of the forearm at
distance du 30.0 ctn from the elbow, with the
torearm parallel to the floor? How much force F
must the elbow exert? (Doute 1)
Figure
dap
Biceps
Soull
1 of 1
Evaluate whether the answer you obtained for the force exerted by the biceps is reasonable
▾
Part J
VAX
Although it is uncommon, orthopedic surgeons have seen patients who have tom their biceps tendon
when forces of greater than 390 N have been exeded on the tendon with the arm bent at the elbow so
that the forearm is parallel to the ground. What is the minimum mass of a ball Af such a patient might
have held…
arrow_forward
Handwritten solution required.
Strictly don't use chatgpt.
If you use chatgpt ,I will report the answer for sure.
Mechanical engineering dynamics.
arrow_forward
SEE MORE QUESTIONS
Recommended textbooks for you
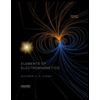
Elements Of Electromagnetics
Mechanical Engineering
ISBN:9780190698614
Author:Sadiku, Matthew N. O.
Publisher:Oxford University Press
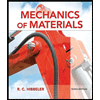
Mechanics of Materials (10th Edition)
Mechanical Engineering
ISBN:9780134319650
Author:Russell C. Hibbeler
Publisher:PEARSON
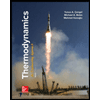
Thermodynamics: An Engineering Approach
Mechanical Engineering
ISBN:9781259822674
Author:Yunus A. Cengel Dr., Michael A. Boles
Publisher:McGraw-Hill Education
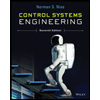
Control Systems Engineering
Mechanical Engineering
ISBN:9781118170519
Author:Norman S. Nise
Publisher:WILEY
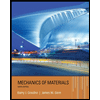
Mechanics of Materials (MindTap Course List)
Mechanical Engineering
ISBN:9781337093347
Author:Barry J. Goodno, James M. Gere
Publisher:Cengage Learning
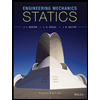
Engineering Mechanics: Statics
Mechanical Engineering
ISBN:9781118807330
Author:James L. Meriam, L. G. Kraige, J. N. Bolton
Publisher:WILEY
Related Questions
- answer and feedback attached, can show steps more clearly pleasearrow_forwardI asked bartleby to solve this question earlier, it gave me AI answer which is completely different to what's shown in this answer. I don't know which one is correct now. I have attached screenshots of the AI answer. Can you clarify which is correct. Also I previously asked about pv diagram and you said ' the curve in the explanation is correct', did you mean in your explanation or the one I showed as an example? Please advicearrow_forwardProblem Statement = You install a heat pump to heat a cottage during the winter using the outside air as the heat source. You wish to maintain the interior temperature of the cottage at 22°C. A simplified model of the heat loss through the walls indicates that heat will need to be supplied at a rate of 0.14(Tinterior - Texterior) where Q is the rate at which heat must be supplied to the cottage (in kW), Tinterior is the interior air temperature (in C), and Texterior is the exterior air temperature (in C). You have a 1kW electric motor available to run the heat pump. What is the coldest winter day when the heat pump will be able to keep up to the heating demand? Answer Table Stage Description Your Answer Correct Answer * Due Date Grade (%) Part Weight Attempt Action/Message. Type 1 Coldest outdoor temperature (°C) Nov 7, 2024 11:59 pm 0.0 1 1/5 Submit * Correct answers will only show after due date has passed.arrow_forward
- bliuzodt to mopolb 9. If machine parts are degreased by means of kerosene as shown in the diagram, how much kerosene make-up is needed per day? How much kerosene has to enter the degreasing vat per day? There are about 3 lb of grease per 100 lb of machine parts, and 60 tons of machine parts are processed each day. Five thousand pounds of kerosene (the 10% solution) are carried away by the machine parts each day but drip off and are caught and put back in the degreasing vat. Two hundred pounds of the 10% solution are lost each day from the vat by evaporation, spillage, or by being carried away.arrow_forwardD2L MCG3740_Final_2018 - MC... D2L Accueil - Université d'Ottaw... ← Homework 6 - Fall 2024 Τρ Question 3 of 4 < סוי education.wiley.com Sephora G formule vitesse angulaire en... WP Homework 6 - Fall 2024 X WP Question 3 of 4 - Homewor... Mail - Pierre Sarr - Outlook - / 10 0 Current Attempt in Progress For the instant represented, crank OB has a clockwise angular velocity w = 1.22 rad/sec and is passing the horizontal position. Determine the corresponding magnitudes of the velocity of the guide roller A in the 22° slot and the velocity of point C midway between A and B. 15" 7 C. 32" AO 22% B Answers: VA = VC = - eTextbook and Media Save for Later in./sec in./sec Attempts: 0 of 1 used Submit Answerarrow_forwardWhich of the following formulas describe the thermal efficiency of a cycle? Select all that applies. 1 - qin/qout worknet/qout worknet/qin 1 - qout/qinarrow_forward
- Algenib Sherately Alpher Sche M فرع واحد / تدلا سؤال/ Q1/Write a notes on heat balance sheet, draw that on the energy flow and enhance your answers with equations. 2:2 Q2/An indicator diagram taken from a single cylinder four stroke, compression ignition engine has a length of 100/mm and an area of 2045 mm². The indicator pointer deflects a distance of 10 mm for a pressure increment of 2 bar in the cylinder. If the bore and stroke of the engine cylinder are both 100 mm and the engine speed is 900 rev/min, calculate the mean effective pressure and the indicated power. If the mechanical efficiency is 0.75, what is the brake power developed. Draw the indicator diagram.) ip or bif 03 A diesel engine develops 5kW. Its indicated thermal efficiency is 0.3 and mechanical efficiency 0.75. Estimate the fuel consumption of engine in (a) Kg/hr (b) liters/hr (c) indicated specific fuel consumption and (d) brake specific fuel consumption. Take heat value of fuel 42000 kJ/Kg and density of fuel 0.87…arrow_forwardSolve show all steps and solution. Energy systems engineeringarrow_forwardPlease solve this questionarrow_forward
arrow_back_ios
SEE MORE QUESTIONS
arrow_forward_ios
Recommended textbooks for you
- Elements Of ElectromagneticsMechanical EngineeringISBN:9780190698614Author:Sadiku, Matthew N. O.Publisher:Oxford University PressMechanics of Materials (10th Edition)Mechanical EngineeringISBN:9780134319650Author:Russell C. HibbelerPublisher:PEARSONThermodynamics: An Engineering ApproachMechanical EngineeringISBN:9781259822674Author:Yunus A. Cengel Dr., Michael A. BolesPublisher:McGraw-Hill Education
- Control Systems EngineeringMechanical EngineeringISBN:9781118170519Author:Norman S. NisePublisher:WILEYMechanics of Materials (MindTap Course List)Mechanical EngineeringISBN:9781337093347Author:Barry J. Goodno, James M. GerePublisher:Cengage LearningEngineering Mechanics: StaticsMechanical EngineeringISBN:9781118807330Author:James L. Meriam, L. G. Kraige, J. N. BoltonPublisher:WILEY
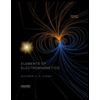
Elements Of Electromagnetics
Mechanical Engineering
ISBN:9780190698614
Author:Sadiku, Matthew N. O.
Publisher:Oxford University Press
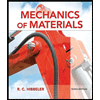
Mechanics of Materials (10th Edition)
Mechanical Engineering
ISBN:9780134319650
Author:Russell C. Hibbeler
Publisher:PEARSON
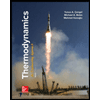
Thermodynamics: An Engineering Approach
Mechanical Engineering
ISBN:9781259822674
Author:Yunus A. Cengel Dr., Michael A. Boles
Publisher:McGraw-Hill Education
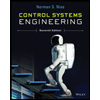
Control Systems Engineering
Mechanical Engineering
ISBN:9781118170519
Author:Norman S. Nise
Publisher:WILEY
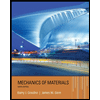
Mechanics of Materials (MindTap Course List)
Mechanical Engineering
ISBN:9781337093347
Author:Barry J. Goodno, James M. Gere
Publisher:Cengage Learning
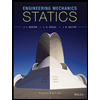
Engineering Mechanics: Statics
Mechanical Engineering
ISBN:9781118807330
Author:James L. Meriam, L. G. Kraige, J. N. Bolton
Publisher:WILEY