Thermo-Module-problem-set_v3
docx
keyboard_arrow_up
School
University of Wisconsin, Madison *
*We aren’t endorsed by this school
Course
460
Subject
Mechanical Engineering
Date
Dec 6, 2023
Type
docx
Pages
8
Uploaded by DukeStarRaven27
CALPHAD Lab
First step is to download Thermocalc. To get most recent Thermocalc demo go here:
https://www.thermocalc.com/academia/students/educational-package-for-
students/
Useful links:
1.
Thermocalc help:
file:///Applications/Thermo-Calc-academic-
2017b.app/Contents/Resources/HTML5/Content/Welcome.htm
2.
Save projects often. Mine tend to freeze and I need to restart the Thermo-calc
software.
3.
Use “Project” pane features to reuse settings and “Clone” feature to perform
similar actions. Right clicking gives options. All of problem 1 and 2 can each be in
their own projects, giving two projects that contain the whole lab.
1.
Martensitic stainless steels offer a combination of high mechanical strength and
corrosion resistance. To increase the hardness of the surface, the process of
“carburization”, or annealing in the presence of a carbon-rich gas, can be
performed, which will increase the carbon concentration in the steel near the
surface. However, the increase in hardness must be balanced against a loss of
corrosion resistance. This exercise will help understand the reasons for this
trade-off.
The most basic martensitic stainless steel is Type 410, which has a
nominal composition of (by mass percent)
Cr 13.5
C
0.15.
Fe 86.35
Usually when specifying steel compositions this would be written Fe-13.5Cr-
0.15C, where composition is written prior to each element, and the Fe
composition is omitted since it is the main constituent. 410 steels may also
include a small amount of Mn which is primarily used to combine with and
remove oxygen impurities; it can be neg
lected
for the purposes of this exercise. Carburization causes an increase in carbon
concentration near the surface, leading to the formation of chromium-rich
carbide phases within the FCC matrix, including M
23
C
6
, M
7
C
3
, and M
3
C (where M
stands for metal). M
23
C
6
and M
7
C
3
increase hardness, but the formation of M
3
C
(also called cementite) reduces strength. In the following, you can label phases in
picture by right-clicking but it takes a lot of time as you need to do each one
separately so don’t worry about labeling them unless I ask explicitly.
1.1. Using Thermo-calc with the database FEDEMO do the following.
1.1.1.
Plot an isopleth of this steel for mass percent carbon varying from 0-5
mass-%. An isopleth keeps all compositions constant except one alloying
element and the host, in this case C and Fe, respectively. You can do this
with the “Property Model” tool and select “Phase Diagram” in the
“Equilibrium Calculator” to do this. Put plot below as Figure 1.1.1. Please
label the phases that occur at 1230K. Note that the FCC Fe phase forms
at this temperature.
1.1.2.
Plot the phase fractions as a function of mass percent carbon at 1230
K in the range 0-5 mass-% carbon. You can do this with “Property
Model” in the “Equilibrium Calculator”. Put plot below as Figure 1.1.2.
1.2. Using the results of part (a), at a temperature of 1230 K, determine the range
of mass percent carbon that allows M
23
C
6
and/or M
7
C
3
to form, but prevents
cementite from forming (carburization will not raise C content dramatically
which is why you can limit your search to <5 mass % C). Put text below as
Response 1.2.
From about 0.2% C to 3.5% C.
1.3. Corrosion resistance in stainless steels is significantly enhanced by the
presence of Cr in the FCC matrix phase.
After carburization, it has been
found that corrosion resistance at the surface decreases. Explain why this
occurs using a plot of Cr content of the FCC phase versus carbon
concentration. Again use a temperature of 1230 K and up to 5 mass % C. You
can get Cr content as the output variable with a “Property Model” in the
“Equilibrium Calculator” but you must set the output in the “Plot Renderer
Y-axis tab. Put plot below as Figure 1.3. Put text below as Response 1.3.
The corrosion resistance decreases because as the carbon
concentration increases, the Cr content in FCC matrix decreases as
seen in the plot.
2.
Kinetics of carbide precipitation in steels. Open example: P_03_Precipitation_Fe-
C-Cr_TTT_Cementite-M7C3-M23C6.tcu. You can find this under File/Example
Files/Precipitation Module – TC-Prisma.
2.1. First, write down the composition of this example. Put text below as
Response 2.1.
Fe-12Cr-0.1C
2.2. Perform a calculation at thermodynamic equilibrium (use the
“Project Pane” to find the preset “Equilibrium Calculation”) to determine
Your preview ends here
Eager to read complete document? Join bartleby learn and gain access to the full version
- Access to all documents
- Unlimited textbook solutions
- 24/7 expert homework help
what phases are present at 1000K. Put the plot below as Figure 2.2. Put text
below as Response 2.2. Note that the point of this is to understand where
our kinetic simulation should end up when we run for long enough time,
which is equilibrium.
Figure 2.2
BCC_A2 and M23C6 are present at 1000K
2.3. Calculate a TTT diagram and determine how long it takes to form M23C6 at
1000K (try to be accurate within a factor of 2x or so but don’t worry about
being precise) (use the “Project Pane” to find the preset “Precipitation
Calculation”). Keep all the precipitate phases even though we are just asking
about M23C6 as they could influence the behavior of M23C6. Set the
temperature step size to 50 to make the calculation faster. Set all the
interfacial energies to be “user defined” (somewhat strangely, this calculates
defaults and please use these defaults. This gives a value of 0.252 J/m2 for
M23C6). Set the max time to 10
5
seconds. Put the TTT plot below as Figure
2.3. Put text below as Response 2.3. Note that this calculation can take 2-
10min to run depending on the computer.
Figure 2.3
About 860 seconds.
2.4. Change the interfacial E by ~10% (reduce by 0.02 J/m2) for M23C6 to see
impact on time. Determine how long it takes to form M23C6 at 1000K with
the new interfacial energy (try to be accurate within a factor of 2x or so but
don’t worry about being precise)? This demonstrates how sensitive the
results are to the exact interfacial energy. Why do you think the results are so
sensitive? Put plot
below as Figure 2.4. Put text below as Response 2.4.
Figure 2.4
About 43.4 seconds with the new interfacial energy.
2.5. Perform an isothermal annealing simulation at 1000 K for10
5
s.
Use the
original interfacial energies, Adjust plot renderer settings to get clear plots
of average radius and number density and volume fraction vs. time for all 3
precipitates.
Set axes to log if needed to see all data.
Put plots below as
Figure 2.5a (radius), 2.5b (number density), and 2.5c (volume fraction).
Please put results for each precipitate type on the same plot, e.g., Figure 2.5a
should have radius of cementite, M7C3, M27C6). What is happening over
long times to these precipitates? Put text below as Response 2.5.
Figure 2.5a
Your preview ends here
Eager to read complete document? Join bartleby learn and gain access to the full version
- Access to all documents
- Unlimited textbook solutions
- 24/7 expert homework help
Figure 2.5b
Figure 2.5c
Over a long period of time, both cementite and M7C3 reduced in size
while M23C6 becomes the primary precipitate.
Related Documents
Related Questions
https://drive.google.com/file/d/1X0Sk9U2pT7lwJ9IB--kLkGngHm46SywH/view?usp=sharing
arrow_forward
kamihq.com/web/viewer.html?state%=D%7B"ids"%3A%5B"1vSrSXbH_6clkKyVVKKAtzZb_GOMRwrCG"%5D%...
lasses
Gmail
Copy of mom it for..
Маps
OGOld Telephone Ima.
Preview attachmen...
Kami Uploads ►
Sylvanus Gator - Mechanical Advantage Practice Sheet.pdf
rec
Times New Roman
14px
1.5pt
BIUSA
A Xa x* 三三
To find the Mechanical Advantage of ANY simple machine when given the force, use MA = R/E.
1.
An Effort force of 30N is appliled to a screwdriver to pry the lid off of a can of paint. The
screwdriver applies 90N of force to the lid. What is the MA of the screwdriver?
MA =
arrow_forward
A VẬT LÝ ĐẠI CƯƠ X
A TongHopTailieul x
A DaoHam.pdf - Go X
A Chương 1 - Good x
The position vec
My Tutoring | ba x
QUIZ 1: MOTION X
f (2) Facebook
O X
Slide 1
O YouTube
(66) YouTube
+ → C D
A Không bảo mật e-learning.hcmut.edu.vn/pluginfile.php?file=%2F1499051%2Fmod_resource%2Fcontent%2F8%2FChapter%201-%20Kinematics.pdf
A YouTube to MP3 C.
M Hộp thư đến (41) -...
Khóa học: Soft Skill.
O Audio Cambridge 1.
A TẠI LIEU WRITING.
t Link tải Cam 1- 15..
iot IELTS Simulation Te.
A (HV] Chương trình...
A BTC OISP GALA 202..
A GĐ2: OISP YOUTH...
A Tổng hợp đề writin.
A REPORT DE THI IEL.
>>
QUIZ 1: MOTION IN TWO AND THREE DIMENSIONS
1 / 5
195%
in meters and t is in seconds. At t = 3.00 s, find (a) the position of the particle, (b) its velocity, and
(c) its acceleration.
1.2. A motorist drives south at 20.0 m/s for 3.00 min, then turns west and travels at 25.0 m/s for 2.00
min, and finally travels northwest at 30.0 m/s for 1.00 min. For this 6.00-min trip, find (a) the total
vector displacement,…
arrow_forward
dated metncpdf
Thermodynamics An Engineering X
E Module2-chap2propertiesofpure x
O File
C:/Users/DANIEL/Desktop/300L%202ND%20SEMESTER%20MATERIALS/Module2-chap2propertiesofpuresubstances-130703012604 phpap.
ID Page view
A Read aloud
V Draw
H Highlight
O Erase
40
MEC 451 - THERMODYNAMICS
Faculty of Mechanical Engineering, UITM
Supplementary Problems
The pressure in an automobile tire depends on the temperature of the air
in the tire. When the air temperature is 25°C, the pressure gage reads 210
kRa. If the volume of the tire is 0.025 m3, Cetermine the pressure rise in
the tire when the air temperature in the tire rises to 50°C. Also, determine
the amount of air that must be bled off to restore pressure to its original
value at this temperature. Assume the atmospheric pressure is 100 kPa.
[ 26 kPa, 0.007 kg]
1.
A 6 4 2:57 PM
Lucky CORER
144
Tum lock
314
%
8
1/2
24
6
1/4
23
T
K
F
pause
B
arrow_forward
https://drive.google.com/file/d/1X0Sk9U2pT7lwJ9IB--kLkGngHm46SywH/view?usp=sharing
arrow_forward
As shown in figure a Pepsi can and a plastic Pepsi bottle. Describe how they were manufactured
arrow_forward
Newton’s 2nd Law Lab (Modeling friendly lab)
Go to the PhET simulation Forces & Motion. https://phet.colorado.edu/sims/html/forcesandmotionbasics/latest/forcesandmotionbasics_en.html
Select “Acceleration”
Click to show Forces, Sum of Forces, Values, Mass, and Acceleration.
There are two experiments for this activity – make sure you include both.
Experiment #1: Acceleration vs. Force
In this lab you will determine the relationship between acceleration and net force.
Choose a mass at the beginning, and keep it constant for this entire experiment.
Set the friction to zero. This will make your Applied Force equal to the net force.
Record data for five different values of Applied Force.
Graph Acceleration vs. Net Force.
Graph this in Google sheets(you want a line graph - it should only have one line).
Make sure that Applied Force information is used as the x value
Make sure that Acceleration information is used as the y value
Add a trendline – see what fits best –…
arrow_forward
Chrome
File
Edit
View
History
Bookmarks
People
Tab
Window
Help
McGraw-Hill Campus - ALEKS Science - CHM1045 GEN CHEM 1 BLENDED 669113
A bconline.broward.edu/d21/le/content/466883/fullscreen/12868783/View
McGraw-Hill Campus - ALEKS Science
O GASES
Interconverting pressure and force
A chemistry graduate student is designing a pressure vessel for an experiment. The vessel will contain gases at pressures up to 470.0 MPa. The student's
design calls for an observation port on the side of the vessel (see diagram below). The bolts that hold the cover of this port onto the vessel can safely withstand
a force of 2.80 MN.
pressure vessel
bolts
side
View
port
Calculate the maximum safe diameter w of the port. Round your answer to the nearest 0.1 cm.
O cm
Explanation
Check
O2021 McGraw-Hill Education. All Rights Reserved. Terms of Use
FEB
arrow_forward
Thermodynamics
Please READ THE PROBLEM! I’m tired of posting the same problem over and over. please Read.
This is what the asking for please:
-1. sketch and label all your answers on the nozzle
-2. Sketch and label all your answers on the process on a P-V diagram....
Thank you
arrow_forward
https://pubmed.ncbi.nlm.nih.gov/32521345/
I want to know what them came up with in this project? using link to know that pls veryyyy urgent i will give u like
arrow_forward
I need help solving this problem.
arrow_forward
my project will be thermal analysis of a Swirler Combustor Engine of range extender Using Hydrogen as Fuel,
mainly in the combustor chamber, the engine supported by a turbocharger.
i need a help to start this project.
what i need to use as a tool for my work?
any geometry design availble i could improve it?
methodology?
some rferencess to use.
yhank you
arrow_forward
Mail-Castro Alvarez, Flavio-Cu x W Project Paper.docx
X
arn-us-east-1-prod-fleet02-xythos.content.blackboardcdn.com/5u1270dbb5a74/28581879?X-Blackboard-Expiration-1665014400000&X-Blackboard-Signature-NIkW%28dvWFpbWGe3%28tdPHIz8DWa0asAf2MVdll iOSt0%3D&X Blackboard-Cl... Q @
Bb 28581878
Type here to search
F2
The assembly shown starts from rest when a constant 15-N
force T is applied at time t = 0. Find the speed of the 3-kg
balls when t = 10 s. You can assume that friction is negligible
and that the mass of the rods and disk that T attaches to are
very small compared to the balls.
F3
O
F4
2
n
F6
F6
9
F7
2/3
W
M
A
x (1) Glomb, Zach | Microsoft Team x +
F8
250% + 1 BO
Fo
F10
F11
F12
Prick
Screen
Sys Riq
Scroll
Lock
m
00
400 mm
Pause
Break
3 kg
T
100 mm
70°F Sunny
400
10/4
arrow_forward
I need help coding in MATLAB. I have a .txt file containing the following data. That data is saved in a file named data.txt. I am wondering how I could extract all or some of that data into another .m file. Can you show me the code.
[[5.0018696581196584, 17.863820207570207, -13.086858974358975], [5.0018696581196584, 17.863820207570207, -13.086858974358975], [5.0018696581196584, 17.863820207570207, -13.086858974358975]]
arrow_forward
SEE MORE QUESTIONS
Recommended textbooks for you
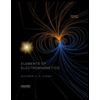
Elements Of Electromagnetics
Mechanical Engineering
ISBN:9780190698614
Author:Sadiku, Matthew N. O.
Publisher:Oxford University Press
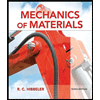
Mechanics of Materials (10th Edition)
Mechanical Engineering
ISBN:9780134319650
Author:Russell C. Hibbeler
Publisher:PEARSON
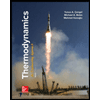
Thermodynamics: An Engineering Approach
Mechanical Engineering
ISBN:9781259822674
Author:Yunus A. Cengel Dr., Michael A. Boles
Publisher:McGraw-Hill Education
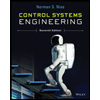
Control Systems Engineering
Mechanical Engineering
ISBN:9781118170519
Author:Norman S. Nise
Publisher:WILEY
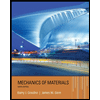
Mechanics of Materials (MindTap Course List)
Mechanical Engineering
ISBN:9781337093347
Author:Barry J. Goodno, James M. Gere
Publisher:Cengage Learning
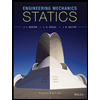
Engineering Mechanics: Statics
Mechanical Engineering
ISBN:9781118807330
Author:James L. Meriam, L. G. Kraige, J. N. Bolton
Publisher:WILEY
Related Questions
- https://drive.google.com/file/d/1X0Sk9U2pT7lwJ9IB--kLkGngHm46SywH/view?usp=sharingarrow_forwardkamihq.com/web/viewer.html?state%=D%7B"ids"%3A%5B"1vSrSXbH_6clkKyVVKKAtzZb_GOMRwrCG"%5D%... lasses Gmail Copy of mom it for.. Маps OGOld Telephone Ima. Preview attachmen... Kami Uploads ► Sylvanus Gator - Mechanical Advantage Practice Sheet.pdf rec Times New Roman 14px 1.5pt BIUSA A Xa x* 三三 To find the Mechanical Advantage of ANY simple machine when given the force, use MA = R/E. 1. An Effort force of 30N is appliled to a screwdriver to pry the lid off of a can of paint. The screwdriver applies 90N of force to the lid. What is the MA of the screwdriver? MA =arrow_forwardA VẬT LÝ ĐẠI CƯƠ X A TongHopTailieul x A DaoHam.pdf - Go X A Chương 1 - Good x The position vec My Tutoring | ba x QUIZ 1: MOTION X f (2) Facebook O X Slide 1 O YouTube (66) YouTube + → C D A Không bảo mật e-learning.hcmut.edu.vn/pluginfile.php?file=%2F1499051%2Fmod_resource%2Fcontent%2F8%2FChapter%201-%20Kinematics.pdf A YouTube to MP3 C. M Hộp thư đến (41) -... Khóa học: Soft Skill. O Audio Cambridge 1. A TẠI LIEU WRITING. t Link tải Cam 1- 15.. iot IELTS Simulation Te. A (HV] Chương trình... A BTC OISP GALA 202.. A GĐ2: OISP YOUTH... A Tổng hợp đề writin. A REPORT DE THI IEL. >> QUIZ 1: MOTION IN TWO AND THREE DIMENSIONS 1 / 5 195% in meters and t is in seconds. At t = 3.00 s, find (a) the position of the particle, (b) its velocity, and (c) its acceleration. 1.2. A motorist drives south at 20.0 m/s for 3.00 min, then turns west and travels at 25.0 m/s for 2.00 min, and finally travels northwest at 30.0 m/s for 1.00 min. For this 6.00-min trip, find (a) the total vector displacement,…arrow_forward
- dated metncpdf Thermodynamics An Engineering X E Module2-chap2propertiesofpure x O File C:/Users/DANIEL/Desktop/300L%202ND%20SEMESTER%20MATERIALS/Module2-chap2propertiesofpuresubstances-130703012604 phpap. ID Page view A Read aloud V Draw H Highlight O Erase 40 MEC 451 - THERMODYNAMICS Faculty of Mechanical Engineering, UITM Supplementary Problems The pressure in an automobile tire depends on the temperature of the air in the tire. When the air temperature is 25°C, the pressure gage reads 210 kRa. If the volume of the tire is 0.025 m3, Cetermine the pressure rise in the tire when the air temperature in the tire rises to 50°C. Also, determine the amount of air that must be bled off to restore pressure to its original value at this temperature. Assume the atmospheric pressure is 100 kPa. [ 26 kPa, 0.007 kg] 1. A 6 4 2:57 PM Lucky CORER 144 Tum lock 314 % 8 1/2 24 6 1/4 23 T K F pause Barrow_forwardhttps://drive.google.com/file/d/1X0Sk9U2pT7lwJ9IB--kLkGngHm46SywH/view?usp=sharingarrow_forwardAs shown in figure a Pepsi can and a plastic Pepsi bottle. Describe how they were manufacturedarrow_forward
- Newton’s 2nd Law Lab (Modeling friendly lab) Go to the PhET simulation Forces & Motion. https://phet.colorado.edu/sims/html/forcesandmotionbasics/latest/forcesandmotionbasics_en.html Select “Acceleration” Click to show Forces, Sum of Forces, Values, Mass, and Acceleration. There are two experiments for this activity – make sure you include both. Experiment #1: Acceleration vs. Force In this lab you will determine the relationship between acceleration and net force. Choose a mass at the beginning, and keep it constant for this entire experiment. Set the friction to zero. This will make your Applied Force equal to the net force. Record data for five different values of Applied Force. Graph Acceleration vs. Net Force. Graph this in Google sheets(you want a line graph - it should only have one line). Make sure that Applied Force information is used as the x value Make sure that Acceleration information is used as the y value Add a trendline – see what fits best –…arrow_forwardChrome File Edit View History Bookmarks People Tab Window Help McGraw-Hill Campus - ALEKS Science - CHM1045 GEN CHEM 1 BLENDED 669113 A bconline.broward.edu/d21/le/content/466883/fullscreen/12868783/View McGraw-Hill Campus - ALEKS Science O GASES Interconverting pressure and force A chemistry graduate student is designing a pressure vessel for an experiment. The vessel will contain gases at pressures up to 470.0 MPa. The student's design calls for an observation port on the side of the vessel (see diagram below). The bolts that hold the cover of this port onto the vessel can safely withstand a force of 2.80 MN. pressure vessel bolts side View port Calculate the maximum safe diameter w of the port. Round your answer to the nearest 0.1 cm. O cm Explanation Check O2021 McGraw-Hill Education. All Rights Reserved. Terms of Use FEBarrow_forwardThermodynamics Please READ THE PROBLEM! I’m tired of posting the same problem over and over. please Read. This is what the asking for please: -1. sketch and label all your answers on the nozzle -2. Sketch and label all your answers on the process on a P-V diagram.... Thank youarrow_forward
- https://pubmed.ncbi.nlm.nih.gov/32521345/ I want to know what them came up with in this project? using link to know that pls veryyyy urgent i will give u likearrow_forwardI need help solving this problem.arrow_forwardmy project will be thermal analysis of a Swirler Combustor Engine of range extender Using Hydrogen as Fuel, mainly in the combustor chamber, the engine supported by a turbocharger. i need a help to start this project. what i need to use as a tool for my work? any geometry design availble i could improve it? methodology? some rferencess to use. yhank youarrow_forward
arrow_back_ios
SEE MORE QUESTIONS
arrow_forward_ios
Recommended textbooks for you
- Elements Of ElectromagneticsMechanical EngineeringISBN:9780190698614Author:Sadiku, Matthew N. O.Publisher:Oxford University PressMechanics of Materials (10th Edition)Mechanical EngineeringISBN:9780134319650Author:Russell C. HibbelerPublisher:PEARSONThermodynamics: An Engineering ApproachMechanical EngineeringISBN:9781259822674Author:Yunus A. Cengel Dr., Michael A. BolesPublisher:McGraw-Hill Education
- Control Systems EngineeringMechanical EngineeringISBN:9781118170519Author:Norman S. NisePublisher:WILEYMechanics of Materials (MindTap Course List)Mechanical EngineeringISBN:9781337093347Author:Barry J. Goodno, James M. GerePublisher:Cengage LearningEngineering Mechanics: StaticsMechanical EngineeringISBN:9781118807330Author:James L. Meriam, L. G. Kraige, J. N. BoltonPublisher:WILEY
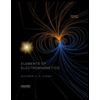
Elements Of Electromagnetics
Mechanical Engineering
ISBN:9780190698614
Author:Sadiku, Matthew N. O.
Publisher:Oxford University Press
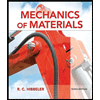
Mechanics of Materials (10th Edition)
Mechanical Engineering
ISBN:9780134319650
Author:Russell C. Hibbeler
Publisher:PEARSON
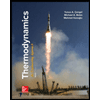
Thermodynamics: An Engineering Approach
Mechanical Engineering
ISBN:9781259822674
Author:Yunus A. Cengel Dr., Michael A. Boles
Publisher:McGraw-Hill Education
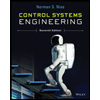
Control Systems Engineering
Mechanical Engineering
ISBN:9781118170519
Author:Norman S. Nise
Publisher:WILEY
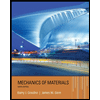
Mechanics of Materials (MindTap Course List)
Mechanical Engineering
ISBN:9781337093347
Author:Barry J. Goodno, James M. Gere
Publisher:Cengage Learning
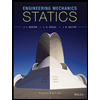
Engineering Mechanics: Statics
Mechanical Engineering
ISBN:9781118807330
Author:James L. Meriam, L. G. Kraige, J. N. Bolton
Publisher:WILEY