FINAL REPORT - MD1
docx
keyboard_arrow_up
School
University of Technology Sydney *
*We aren’t endorsed by this school
Course
48600
Subject
Mechanical Engineering
Date
Dec 6, 2023
Type
docx
Pages
46
Uploaded by ericnzioka11
WARMAN DESIGN REPORT
ERIC KIOKO - 13555887
UTS – COORDINATOR: Dr. Mickey Clemon
MECHANICAL DESIGN 1 – AUTUMN 2020
Warman Design Report
Mechanical Design 1 – Autumn 2021
CERTIFICATE
I certify that the work in this report has not previously been submitted except as fully acknowledged
within the text.
I also certify the report has been written by myself. In addition, I certify that all information sources
and literature used are indicated in the report.
Signature of student:
Eric Nzioka Kioko
Date: 24/05/2021
Group 02, Monday, 9:00am.
1 |
P a g e
Warman Design Report
Mechanical Design 1 – Autumn 2021
ABSTRACT
This report outlines group Mon_02’s design and the manufacturing process of the whole robot. The
report also gives details of the FRDPARRC analysis of the personal artefacts that I was in charge of for
this project. The personal artefacts consist of fasteners, mechanical adapters, navigation path and for
the electrical artefact; motor driver/motor shield H bridge. The project was to build an autonomous
robot according to the Warman competition. The group tried to reach all the required functional
requirements and made necessary countermeasures to avoid any risks that might occur.
2 |
P a g e
Your preview ends here
Eager to read complete document? Join bartleby learn and gain access to the full version
- Access to all documents
- Unlimited textbook solutions
- 24/7 expert homework help
Warman Design Report
Mechanical Design 1 – Autumn 2021
Contents
CERTIFICATE
..........................................................................................................................................
1
ABSTRACT
..............................................................................................................................................
2
Acronyms and abbreviations
.................................................................................................................
5
INTRODUCTION
.....................................................................................................................................
6
Warman Competition
........................................................................................................................
6
Objectives/Requirements/Goals
........................................................................................................
6
Outline of the report
.........................................................................................................................
6
Literature Review
...............................................................................................................................
7
Acknowledgements
...........................................................................................................................
7
RESEARCH AND PLANNING
...................................................................................................................
8
FRDPARRC
..........................................................................................................................................
8
Design and Development
.................................................................................................................
12
Analysis
............................................................................................................................................
12
Designs and Analysis Criteria
...........................................................................................................
12
Gantt chart
.......................................................................................................................................
13
Risk Assessment
...............................................................................................................................
14
Group Tasks and Performance
.........................................................................................................
14
OVERALL SYSTEM DESIGN
....................................................................................................................
15
Mechanical Components
.................................................................................................................
15
Base/Chassis
................................................................................................................................
15
Motor and controller Mounts
......................................................................................................
15
Wheels
.........................................................................................................................................
15
Payload/Collection Basket
...........................................................................................................
15
Electrical Components
.....................................................................................................................
16
Control unit (Arduino)
..................................................................................................................
16
Motors
.........................................................................................................................................
16
Motor Drive
.................................................................................................................................
16
Battery
.........................................................................................................................................
17
Power Regulator
..........................................................................................................................
17
ARTEFACT 1: FASTENERS
.....................................................................................................................
18
Functional Requirements
.................................................................................................................
18
Design Parameters (morphology)
....................................................................................................
19
Analysis
............................................................................................................................................
19
References
.......................................................................................................................................
19
3 |
P a g e
Warman Design Report
Mechanical Design 1 – Autumn 2021
Risks
.................................................................................................................................................
19
Countermeasures
............................................................................................................................
20
CONCLUSION
...................................................................................................................................
20
ARTEFACT 2: MECHANICAL ADAPTERS
...............................................................................................
21
Functional Requirements
.................................................................................................................
21
Design Parameters (morphology)
....................................................................................................
21
Analysis
............................................................................................................................................
21
References
.......................................................................................................................................
21
Risks
.................................................................................................................................................
21
Countermeasures
............................................................................................................................
21
ARTEFACT 3; NAVIGATION PATH
.........................................................................................................
22
Functional Requirements
.................................................................................................................
22
Design Parameters (morphology)
....................................................................................................
22
Analysis
............................................................................................................................................
22
References
.......................................................................................................................................
22
Risks
.................................................................................................................................................
22
Countermeasures
............................................................................................................................
22
ARTEFACT 4: MOTOR DRIVER
..............................................................................................................
23
Functional Requirements
.................................................................................................................
23
Design Parameters (morphology)
....................................................................................................
23
Analysis
............................................................................................................................................
23
References
.......................................................................................................................................
24
Risks
.................................................................................................................................................
24
Countermeasures
............................................................................................................................
24
CONCLUSION
...................................................................................................................................
24
COST ANALYSIS/ECONOMIC FEASIBILITY
............................................................................................
25
CONCLUSION/DISCUSSION
.................................................................................................................
26
APPENDIX
............................................................................................................................................
27
REFERENCES
........................................................................................................................................
43
4 |
P a g e
Warman Design Report
Mechanical Design 1 – Autumn 2021
Acronyms and abbreviations
FRDPARRC – Functional Requirements, Design Parameters, Analysis, References, Risks,
Countermeasures
SHS – Square Hollow Section
MDF – Medium-Density Fibreboard
5 |
P a g e
Your preview ends here
Eager to read complete document? Join bartleby learn and gain access to the full version
- Access to all documents
- Unlimited textbook solutions
- 24/7 expert homework help
Warman Design Report
Mechanical Design 1 – Autumn 2021
INTRODUCTION
Warman Competition
The Warman competition aims to solve a problem where engineers are meant drop neutralising
pellets onto mined ore, this is to separate the mined ore from the metals. Before this, a prototype is
made, and the competition is to make a prototype that demonstrates how this can be achieved. The
prototype requires the engineers to drop 10 tennis balls that represent the neutralising pellets into 4
different silos, the different amount of tennis balls that are dropped represent the higher quality of
neutralising agent required for that specific silo.
Objectives/Requirements/Goals
To design, build and demonstrate through the prototype, a proof of concept for the robot that will be
used as a pellet deployment system. This prototype needs to go from the start/end zone and needs
to drop a specific number of the ten balls into one of the 4 silos and then needs to come back to the
start/end zone. This needs to be done autonomously and for the most points to be earned, the
correct number of pellets need to be dropped into the right silos as demonstrated in Figure 1 below.
The system is also required to have the 10 balls pre-loaded onto the robot in the beginning and must
complete all operations within 120 seconds. Additionally, the robot must be able to fit in a 500 x 500
x 500 mm box without payload and must not have a mass greater than 6kg.
Figure 1. Schematic view of the competition track showing silo tube location and the number of
pellets targeted to be in each tube at the competition of the run. Tubes (silos) are shown transparent
for clarity.
Outline of the report
The purpose of this report is to cover the technical and theoretical details of the Warman
competition robot. It also includes the design and ideation processes, research stages. The overall
system designs and the personal artefacts assigned to me. Additionally, the cost analysis/economic
feasibility report is included with reasoning behind each part. Lastly, the conclusion summarises the
whole report and the learning experiences from undertaking this project.
6 |
P a g e
Warman Design Report
Mechanical Design 1 – Autumn 2021
Literature Review
For this project, we started by thinking about what would be the easiest design to accomplish the
projects’ objectives. After consulting and researching previous groups’ ideas as well, we decided to
do the telescopic arm which requires less movement of the whole robot and more focus on the arm
deployment system. This idea was better to us because it required less movement of the whole robot
and rather more focus on the arm and the lifting mechanism.
Acknowledgements
For this Warman project, it was done in groups and it was only due to the groups collective hard
work that the robot was able to work. Each group member contributed to their specific artefacts and
the group communicated effectively on a weekly basis to efficiently build the prototype that meets
all the required objectives. Many thanks to our subject coordinator Dr. Lee ‘Mickey’ Clemon and to
our tutor Dr. Mohammed Adwadallah. Also not forgetting my group members who all put in a lot of
effort; our group leader Leon Agalawatta, Toby Marchant as our manufacturing engineer 1, Max
Mckern as our manufacturing engineer 2, our mechanical engineer as Sam Lawson and I as the
mechatronics engineer.
7 |
P a g e
Warman Design Report
Mechanical Design 1 – Autumn 2021
RESEARCH AND PLANNING
FRDPARRC
FUNCTIONAL
REQUIREMENT
DESIGN
PARAMET
ERS
ANALYSIS
REFERENCES
RISK
COUNTER-
MEASURES
BASE CHASSIS
“Give precise
linear motion”
to accurately
place the
payload into
the storage
area.
“Omnidirection
al load
capability with
long life” to be
stable enough
to place loads
on it within a
500x500x500
mm^3 area.
“Rapid
acceleration”
to complete
the proposed
task in under
120 seconds
and
subsequently,
rapid
acceleration
must occur to
maximise time
for other
tasks.
Accurately
place the
payload into
the storage
area.
Must be
stable
enough to
place loads
on it within
a
500x500x50
0mm^3
area.
“Rapid
acceleration
”.
The whole
robot needs
to complete
the
proposed
task in
under 120
seconds.
1. These wheels were
considered the most
appropriate as they allowed
for linear motion and were
easy to implement. The
addition of pillow bearings
(Appendix C.3) for the axle
to pass through allowed for
little resistance and easy
motion. The use of YG2900
Arduino Wheels (appendix
1) to drive the chassis
completes the system and
should allow for the
completion of the task within
120 seconds. The rubber
outside of all the wheels
also provide enough grip to
move the robot so no time
will be wasted with slippage.
2.
The wheels used also
allow for motion in either
direction. The use of non-
direction specific pillow
bearings attached to the
underside of the frame allow
for easy motion in either
direction and don’t require
any maintenance due to the
closed nature of the
bearings used. Similarly, the
use of 2 YG2900 Arduino
Wheels placed at either end
of the robot, control how fast
and far the robot travels in
either direction. This design
was chosen due to the ease
of access to the parts and
the overall construction
Anon, 2021, viewed 15
April 2021,
<https://www.bunnings.c
om.au/ambassador-
100mm-white-plastic-
centre-wheel-and-
rubber-tyre_p3942885>.
Anon, 2021, viewed 15
April 2021,
<https://www.bunnings.c
om.au/metal-mate-25-4-
x-25-4-x-1-2mm-3m-
aluminium-square-box-
tube_p1079488>.
Datasheets - Aluminium
Alloy - Commercial Alloy
- 6063 - '0' Extrusions |
Dalsteel Metals 2021,
Dalsteel.com.au. viewed
15 April 2021,
<http://www.dalsteel.co
m.au/technical-
information/datasheets/
Aluminium-Alloy-6063-0-
Extrusion
s_
160.asmx>.
Driving
wheels not
powerful
enough/ov
er-
encumber
ed
Bolts used
to hold
parts on
loosen
with use
Bolts used
to hold
parts on
loosen
with use
Switch out for
ones with a
higher torque
rating.
Potentially
redesign
elements above
the base chassis
to be lighter.
Use locktite to
secure bolts on,
particularly the
ones holding the
wheels on
Have spare
parts or choose
plastics with a
higher modulus
of elasticity,
potentially 3d
print the parts
instead of
buying.
8 |
P a g e
Your preview ends here
Eager to read complete document? Join bartleby learn and gain access to the full version
- Access to all documents
- Unlimited textbook solutions
- 24/7 expert homework help
Warman Design Report
Mechanical Design 1 – Autumn 2021
being simple to reduce any
chance of faults.
LIFTING MECHANISM
1. Supply an
upwards force
on the loading
mechanism
2. Have a large
enough
effective stroke
that's enough
so the loading
mechanism
can reach the
shortest and
tallest tube
3. Must not
exceed size
requirements
of Warman
competition
1. Supply
an upwards
force of
approximate
ly 34N to lift
the loading
mechanism
which is
expected to
weight up to
3.5kg
2. Have an
effective
stroke of
400mm to
to able to
reach all the
tubes
3. Robot
must be to
fit into a
500x500x50
0 (mm) box
at its
smallest
state
Calculations in Appendix 2.
-Collins, D. (2020,
February 7). What
options are there for
integrated motor and
screw designs?
Linear Motion Tips.
https://www.linearmo
tiontips.com/what-
options-are-there-
for-integrated-motor-
and-sc
rew-designs/
-Instructables, &
Ben1998. (2017,
December 28).
Linear Actuator
Stepper Motor.
Instructables.
https://www.instructa
bles.com/Linear-
Actuator-Stepper-
Motor/
-Instructables, &
farmerkeith. (2019,
February 25). DIY
Linear Actuator.
Instructables.
https://www.instructa
bles.com/DIY-Linear-
Actuator/
1.
Insufficient
upwards
force
2.
Insufficient
stroke
length
3. Too
large and
fails to
meet the
maximum
size
requireme
nts
-For [1] &
[2] ensure that
extensive testing
is done on the
lifting
mechanism.
- For risk [1] is to
put into place a
factor of safety
(FoS) of 1.5
-For risk [3] the
countermeasure
put in place is to
test fit the linear
actuator onto
the chassis and
measure the
height of the
system and
ensure it is not
taller than the
500mm height
restriction.
PAYLOAD DISPENSER
Dispenses
payloads
smoothly and
accurately and
complies with
weight and
Material is
lightweight
but can
withstand a
weight of
approximate
Using PVC piping with
diameter of 90mm. Any less
and the balls from the top
storage part would not be
able to roll down the bend
connecting to the arm due
Bunnings’s warehouse,
drawer slides, viewed
2 April 2021,
https://www.bunnings.c
om.au/our-
Balls fall
out of the
pipe
Anything less than
90mm, the balls
could possibly fall
out. Calculations
show that 90mm
9 |
P a g e
Warman Design Report
Mechanical Design 1 – Autumn 2021
volume
restrictions.
A number of
dispensing
options are no
longer
available. They
must comply
with the weight
and volume
requirements
outlined in the
introduction.
ly 4kg.
Payload
unloading is
controlled
as we need
the system
to move
before
releasing
more
payloads.
The cost of
the
materials is
less than
$150,
preferably
around
$100.
All
components
are secure
and rigid.
The delivery
system
must be
within
H340x
W450x
D500mm at
the start
and
completion
of the timed
run.
to the decrease in internal
size at the bend. This could
have been counteracted by
cutting the pipe however
this would mean the balls
were more likely to fall out.
The PVC on the telescopic
arm was cut in half as the
ball would easily stay inside
the pvc. The bottom of the
telescopic arm will point
towards the middle guiding
the ball out in the exact spot
we would like it to go.
The drawer slides are steel
and zinc plated. This will be
the heaviest part of the
robot weighing 3kg for 4
sets of drawer slides. Each
drawer slide extends 40mm
and will be connected to the
top and bottom of each
piece of PVC.
The cuts of pvc will be
raised using another piece
of MDF, they will be cut to
the shape of the pvc and
glued to both the MDF plate
and the pvc pipe.
Calculations have shown
that the balls will easily go
through the system and into
the track pipes totalling
30seconds. This leaves 1
minute 30 seconds for the
robot to move down the
track, extend and retract the
arm and allow the rack and
pinion to move the MDF.
range/building-
hardware/door-
window-gate-
hardware/cabinet/draw
er-slides?
page=1&facets=Categ
oryIdPath
%3D8dedf25d-58b7-
430e-a87c-
e889b570bc90%2CSu
bCategoryIdPath
%3Dc175764f-6e57-
4bcd-a7a8-
d0627a89047b&sort=B
oostOrder&pageSize=
60
MDF properties,
viewed 10 April 2021,
https://civiltoday.com/ci
vil-engineering-
materials/timber/166-
mdf-definition-types-
properties-manufacture
Rack and Pinion,
viewed 7 April 2021,
https://www.britannica.
com/technology/rack-
and-pinion
MDF can’t
hold the
weight
Rack and
Pinion too
slow
will stop the balls
from going out
the sides. The
only problem
would be
bouncing but at
the angle and
speed, it will not
bounce enough to
fall out.
The MDF has a
density of
600kg/m^3
making it
extremely strong.
It is also stiff and
rigid which is
needed for this
task.
The rack and
pinion can be
going while the
robot is moving in
any direction.
Telescopic Arm
The furthest
tube is 1.8
metres, and as
-
To reach
1.8 metres,
we will have
-
As the arm is going to be
heavy, we will have to make
sure that the robot will be
Anon, 2021, viewed
15 April
2021<
https://www.bunnin
-
If the
telescopic
arm is too
If the arm is
too heavy and
we cannot put
10 |
P a g e
Warman Design Report
Mechanical Design 1 – Autumn 2021
such the
deposit system
will have to
bridge that
distance
without failing.
The other
tubes, which
are closer are
all different
lengths away
thus needing a
way to control
the length of
the tube.
As per the
design
requirements,
the robot must
fit into a
50x50x50cm
box, thus it
needs a way to
extend out.
drawn
sliders
connected
to PVC
pipes in
order to
reach the
distance.
We need a
lightweight
material due
to the draws
sliders
weighing a
net total of 3
kg.
-
To control
the length of
the deposit
system, we
will have a
string
connected
to the
bottom of
the system,
this string
will be
reeled in. In
order to reel
it in and out
we will
connect a
motor to the
reel. Thus,
will help us
reel it in.
able to support the weight
without tipping over or the
arm falling off the robot. we
will have to find the force
and moments acting on the
robot when the arm is fully
extended.
-
The calculations around
the arm will focus on how
strong the motor needs to
be to reel in the arm when
at its furthest point. We will
also need to find the tension
in the string to see the force
acting on it. Once we find
this, we will be able to
choose a string that will be
appropriate.
-
The calculations for the
arm will reveal the angle
which the system has to be
at. Once we find the angle
that the telescopic arm sits
at, we will be able to use
this information to find the
length that the robot will be
lifted up.
gs.com.au/holman-
100mm-x-6m-pvc-
dwv-pipe_p4770346
>
Anon, 2021,
viewed 15 April
2021<
https://www.bunnin
gs.com.au/goliath-
standard-drawer-
slide-pair-
400mm_p4020969?
gclid=Cj0KCQjw6-
SDBhCMARIsAGbI
7Ui4cD49Wk0ajiug
PcCEdC10XU77Up
wpxKdkODvmqWrb
MzSvRVVVdzoaAh
GxEALw_wcB&gcl
src=aw.ds
>
Anon, 2021, viewed
15 April
2021<
https://www.jaycar.
com.au/standard-
high-power-d-c-
motors-20000-
rpm/p/YM2772
>
heavy, we
may not
be able to
add
enough
counterwei
ghts while
staying
under the
6kg limit.
enough
counterweights
on the vehicle
without
exceeding the
6kg limit we will
have to try and
find lighter draw
sliders, or a
different method
to extend the
telescopic arm,
but as we do not
have it built at
this stage, we
won’t be able to
test if it is too
heavy.
FASTENERS
-Affix two or
more
components of
the robot
together for a
smooth and
firm robot
-Withstand the
load when the
-Joiners to
affix the
chassis and
the screws
to fasten
them
together.
-Wheels
held down
- We have wood screws
which we could have used,
however, since our base
was metallic, we decided to
use the machine screws
since the wood screws work
better with wood or softer
materials.
- Used the Phillips and
•CUBII Industrial
Solutions. (2020,
May). Fasteners and
its importance in
industry.
https://cubii.co/en/fas
teners-and-its-
importance-in-
industry/
-Nuts
might not
be tight
enough
since
they’re
pressing
onto the
bearing
which is a
moving
To mitigate this
risk is by using
washers
together with the
nuts to allow for
the nuts not to
be loosely held.
11 |
P a g e
Your preview ends here
Eager to read complete document? Join bartleby learn and gain access to the full version
- Access to all documents
- Unlimited textbook solutions
- 24/7 expert homework help
Warman Design Report
Mechanical Design 1 – Autumn 2021
robot is in
application.
-Allow for the
different
components to
be easily
removed/dism
antled when
necessary,
without
damaging the
joining
components.
by the 8
machine
screws 4
which are
slotted drive
types and 4
which are
Phillips’
drive types.
-M6 nuts to
hold the
bearing in
wheels at
the end of
the rod.
slotted drives since they are
the most common and
easily available.
•Bolt Depot. (2018).
Fastener Basics.
https://www.boltdepo
t.com/fastener-
information/printable-
tools/Fastener-
Basics.pdf
part.
However,
the
likelihood
of this
happening
is small
since
there were
3 nuts
used.
Design and Development
12 |
P a g e
Warman Design Report
Mechanical Design 1 – Autumn 2021
Analysis
The group discussed about different pros and cons of the different prototypes we had and decided to
analyse using the PUGH evaluation as well as a Gantt chart and by the provided data we made some
minor changes to our prototype.
Designs and Analysis Criteria
PUGH EVALUATION
Excavator
Arm
Swiveling
Arm
Telescopic
Arm
COG/Stability
7
9
5
Mechanical
Complexity
2
8
3
Software
Complexity
1
8
2
Manufacturing
Complexity
2
8
3
Payload
Accuracy/Delivery
8
4
10
Cost
6
8
7
Size
7
7
7
Range of Motion
10
5
5
13 |
P a g e
Warman Design Report
Mechanical Design 1 – Autumn 2021
SCORE
43
57
49
Table 1 – PUGH evaluation
Gantt chart
Table 2. Gantt Chart
Risk Assessment
The risks associated with the robot are assessed to ensure that the requirements are not
compromised. Therefore, to solve any of these risks, countermeasures are put in place. The risks are
as stated in the FRDPARRC table as well as the countermeasures. The following table would look in
more detail about how risks on parameters such as safety, functionality, cost and time.
Type of risk
Risk rating
Likelihood of
occurrence
Cause
Consequence
Safety
Medium
Medium
An error in the coding which
would make the heavy arm
swing rapidly.
Temporary injury to a
person, probably to the
lower body, might also
cause the robot break.
Functionality
High
Medium
Not knowing clearly about the
design parameters as well as,
low analysis in design stages
The robot isn’t able to
reach all the PVC pipe and
thus doesn’t meet the
specified requirements.
Cost
Low
Low
Low future thinking when in
design stages as well as
Due to too high costs, it
becomes hard to finish the
14 |
P a g e
Your preview ends here
Eager to read complete document? Join bartleby learn and gain access to the full version
- Access to all documents
- Unlimited textbook solutions
- 24/7 expert homework help
Warman Design Report
Mechanical Design 1 – Autumn 2021
overengineering of functional
issues that may be faced.
robot and thus may cause
the group to have an
unfinished final robot.
Time
Medium
Medium
Lack of group meetings and
group communication and
allocation of tasks
Due to lack of good
planning, building the
robot will become a heavy
task due to undone tasks.
Group Tasks and Performance
Leon – creating the Gantt chart, create a final sketch, analysis of system containers, FEA analysis of
materials, cost analysis and finalise CAD parts and assembly.
Max – Draw CAD models, analysis of system wheels, create CAD of base, finalise system hardware.
Eric – create presentation 1, analysis of System Motors, analysis of Software, finalise System
software.
Sam – Create Presentation 1, analysis of System Arms, create CAD of Arms, Finalise & Edit
Presentation 2, Finalise System Design.
Toby - create presentation 1, Draw CAD models, Analysis of System Base, Create CAD of Wheels w/
motor, Finalise System Hardware.
Everyone contributed to; Identify Functional Requirements, Individual Idea Generation, Identify
Design Parameters, Analyse & Research/References, Group Discussion, Reach Design Decision,
Finalise & Edit Presentation 1, Presentation of Presentation 1, Create Presentation 2, Finalise & Edit
Presentation 2, Create Final Presentation, Finalise System Requirements, CAD drawings, Testing and
Validation, Finalise & Edit final Presentation, Present Final Presentations.
The group worked together communicating and solving the issues as a group.
OVERALL SYSTEM DESIGN
Below are the mechanical and electronic components which work in conjunction to make the whole
robot work.
Mechanical Components
Base/Chassis
The base is made up of 4 steel bars joined together with tubing joiners and a MDF base on top of it
which allows for a housing for the electronic components and other components.
15 |
P a g e
Warman Design Report
Mechanical Design 1 – Autumn 2021
Motor and controller Mounts
The motors and controllers will be mounted with 3D printed bases and stuck onto the base/chassis.
Wheels
We used 4 100cm diameter wheels however, these were used only as a guide and support but two
DC powered wheels were used to move the robot.
Payload/Collection Basket
The robot will have an MDF at the top and using PVC tubes as the storage system and will use gravity
to allow the balls to drop into the silos.
Electrical Components
Control unit (Arduino)
The controller used was the Arduino Uno which is used to allow for the mechatronic components of
the whole robot. The Arduino is what allows us to move the arm back after it has been extended and
released the balls into the silos. Additionally, it is used to control the L298 motor drivers which allow
the linear actuator to move to the desired height and the desired distance for the DC powered
wheels.
Motors
DC
-
The Robot is 2 using DC powered wheels to move the robot and both wheels will be placed
at the front to allow for the robot to move.
16 |
P a g e
Warman Design Report
Mechanical Design 1 – Autumn 2021
Stepper
-
The robot uses a servo motor for the lifting mechanism to allow for the robot to be able to
reach the height of the high silos.
Motor Drive
An L298N stepper motor module was used to control the height of the stepper motor powered linear
actuator as well as the length for the wheels to move the robot.
Battery
The group used a small 9V battery to power the Arduino Uno. However, a LIPO battery from an RC
car is used to power the L298N stepper motor controller. The LIPO battery has 7.2V and 6800mAh.
17 |
P a g e
Your preview ends here
Eager to read complete document? Join bartleby learn and gain access to the full version
- Access to all documents
- Unlimited textbook solutions
- 24/7 expert homework help
Warman Design Report
Mechanical Design 1 – Autumn 2021
Power Regulator
The L298N stepper motor controller has its own 5V power regulator in-built. This is to allow for the
Arduino and controller not to overheat.
18 |
P a g e
Warman Design Report
Mechanical Design 1 – Autumn 2021
ARTEFACT 1: FASTENERS
Functional Requirements
The function of these fasteners is;
To be able to affix two or more components of the robot together for a smooth and firm
robot
Must be able to withstand the load when the robot is in application.
Allow for the different components to be easily removed/dismantled, when necessary,
without damaging the joining components.
Keep all the components safe from damage
19 |
P a g e
Warman Design Report
Mechanical Design 1 – Autumn 2021
Design Parameters (morphology)
The design has multiple components. Each component used as a fastener is specifically chosen with
the fitting dimensions. The fasteners consist of;
o
M6 nuts – 4 used for each of the wheels
o
8 Machine screws 4 slotted drive type and 4 Phillips drive type
o
6mm miniature ball bearing – 4 used for the 4 wheels
o
4 box tubing joiners
For the wheels, connected to the wheel axle we used a bracket that was held down by the 8 machine
screws 4 which are slotted drive types and 4 which are Phillips’ drive types. The bracket is screwed
down to the base chassis of the robot to hold down the box tubing joiners as well as the wheel axle
in order for the base to be firmly connected and for the wheel axle to be held in an unmoving
position to allow for the wheels to move around the bearing that is held down by the bracket.
Additionally, we used m6 nuts for the wheels 3 each to hold the bearing in and an extra one for each
wheel to hold out the outside of the wheels at the end of the rod.
We will also use 8 more screws and nuts to hold together our arm that will be able to go in and out.
These will allow them to be connected to each other and also for the storage system above which
will be made of PVC we have 4 screws and nuts to hold them to the top base.
Analysis
We also had wood screws which we could have used, however, since our base was metallic, we
decided to use the machine screws since the wood screws work better with wood or softer materials.
Furthermore, we used the Phillips and slotted drives since they are the most common and easily
available. For the box tubing joiners, we decided to use these since they had good grip together with
the metallic base. We used ball bearings for the wheels however to improve it we could use washers
to help prevent loosening by spreading the load over a great surface area.
References
Through some research I got to see some advantages and disadvantages of fasteners which helped
the group decide which fasteners to use.
CUBII Industrial Solutions. (2020, May).
Fasteners and its importance in industry
.
<
https://cubii.co/en/fasteners-and-its-importance-in-industry/
>
Bolt Depot. (2018).
Fastener Basics
. https://www.boltdepot.com/fastener-
information/printable-tools/Fastener-Basics.pdf
Risks
For risks that might happen is that the nuts might not be tight enough since they’re pressing onto the
bearing which is a moving part. This could lead to the wheels not working due to the nuts not being
tight enough, however the likelihood of this happening is small since there was 3 nuts used.
20 |
P a g e
Your preview ends here
Eager to read complete document? Join bartleby learn and gain access to the full version
- Access to all documents
- Unlimited textbook solutions
- 24/7 expert homework help
Warman Design Report
Mechanical Design 1 – Autumn 2021
Countermeasures
The plan to mitigate this risk is by using washers together with the nuts to allow for the nuts not to
be loosely held. So, what we will do is just add washers and may also get rid of the extra nut if not
necessary.
CONCLUSION
Through the choices made we were able to apply the SLOs below;
4. Apply the principles of mechanism analysis and design.
5. Apply good mechanical design practice to design and build a mechanical device.
21 |
P a g e
Your preview ends here
Eager to read complete document? Join bartleby learn and gain access to the full version
- Access to all documents
- Unlimited textbook solutions
- 24/7 expert homework help
Warman Design Report
Mechanical Design 1 – Autumn 2021
ARTEFACT 2: MECHANICAL ADAPTERS
Functional Requirements
The mechanical adapters’ functional requirements include;
Transforming rotational to linear motion for the threaded rod in the linear actuator
Transforming linear to rotational motion for the rack and pinion used for the
telescopic arm
Design Parameters (morphology)
The design parameters met through this is that through the threaded rod in the linear actuator, the
robot is able to reach the tall silos and thus drop all the balls into the silos as required for this
Warman competition. Furthermore, the rack and pinion also make the robot able to reach the silos
and thus able to meet the requirement of dropping the balls in each of the pellets.
Analysis
The rack and pinion were a good choice for the telescopic arm, however, the arms we used were the
drawer ones, and they were the heaviest components, weighing up to 3kgs which is half of the
maximum weight allowed for the whole robot. Furthermore, the threaded rod and lead screw was a
good choice as it lifted the robot well, however, it was an expensive choice.
References
Macsim. 2021.
Threaded Rod
. https://www.macsim.com.au/category/1854-threaded-rod
Risks
If the threaded rod breaks, then it would be dangerous since it would be holding the top part of the
robot where the tennis balls will be stored.
Countermeasures
As a countermeasure, the top part of the arm will be held by string in order for it not to fall on
someone’s foot
CONCLUSION
Through the choices made we were able to apply the SLOs below;
4. Apply the principles of mechanism analysis and design.
5. Apply good mechanical design practice to design and build a mechanical device.
22 |
P a g e
Your preview ends here
Eager to read complete document? Join bartleby learn and gain access to the full version
- Access to all documents
- Unlimited textbook solutions
- 24/7 expert homework help
Warman Design Report
Mechanical Design 1 – Autumn 2021
ARTEFACT 3; NAVIGATION PATH
Functional Requirements
The navigation path needs to allow for the robot to complete the task in the fastest time as possible.
Design Parameters (morphology)
The navigation path needs to allow for the required 2mins time therefore it should be the shortest
distance to allow time for the other tasks such as extending of the arm and dropping of the balls in
the silos. As calculated, the best path for our robot is only sideways along the start/end zone line.
This allows for the best time compared to moving the robot along the line.
Analysis
By doing this the robot is estimated to take approximately 1min 35 seconds at max. compared to
going through the track, this would make the robot take longer due to our arm taking time to drop
the balls.
References
Weir. 2021.
Advice from a Warman Winner
. https://www.global.weir/brands/warman/warman-
design-and-build-campaign/advice-from-a-warman-d-and-b-winner/
Risks
The robot could fail to move which would make the robot fail since the arm cannot rotate and the
wheels therefore need to move to the precise line of the silos in order for the telescopic arm to drop
the balls.
Countermeasures
As a backup, we could use the weight of the arm to make the arm to move in one direction and drop
a counterweight on the other side of the robot in order to stop the robot.
CONCLUSION
Through the choices made we were able to apply the SLOs below;
4. Apply the principles of mechanism analysis and design.
5. Apply good mechanical design practice to design and build a mechanical device.
23 |
P a g e
Your preview ends here
Eager to read complete document? Join bartleby learn and gain access to the full version
- Access to all documents
- Unlimited textbook solutions
- 24/7 expert homework help
Warman Design Report
Mechanical Design 1 – Autumn 2021
ARTEFACT 4: MOTOR DRIVER
Functional Requirements
The motor drivers we used is the L298N Dual Motor Driver which;
Interface between the stepper motor and the Arduino for our lifting mechanism which
allows the robot to reach the taller silos (delivery tubes) in order to drop the tennis balls.
This is also used for the DC motor wheels and allows for the robot to move from side to side
autonomously.
Design Parameters (morphology)
To meet the requirement for the vehicle to be autonomous
Allow for the robot to be able to reach all the balls
To be able to reach move to the different locations for the arm to drop the balls.
Analysis
Component
Specifications
Image
Motor driver module;
L298N dual motor driver
Type: module
Logic voltage: 5V
Operating voltage: 3-30V
Max current: 4A
Power: 25W
Cost: $11.95
Dimensions: 69 x 56 x 36 mm
24 |
P a g e
Your preview ends here
Eager to read complete document? Join bartleby learn and gain access to the full version
- Access to all documents
- Unlimited textbook solutions
- 24/7 expert homework help
Warman Design Report
Mechanical Design 1 – Autumn 2021
References
Jaycar, 2021, ‘Dual/stepper motor controller module’. Viewed 23/05/2021
<https://www.jaycar.com.au/medias/sys_master/images/images/9526468673566/XC4492-
dataSheetMain.pdf>
Risks
The heat sink of the L298N motor driver heats up really quickly especially with the stepper
motor thus, it dangerous if someone touches it while in operation or soon after operation
ends. This could cause serious burns to the person’s hand.
Using the weak type of wiring to connect the Arduino to the motor drivers could also cause
the wires to burn quickly.
Countermeasures
Only one person will be operating the L298N and the heat sink will not be touched until it
cools off. Furthermore, the group members and others will be informed of the risk in order
to avoid anyone touching it.
By using thicker wires that can withstand high amps of current, this avoids the risk of the
wires getting hot and degrading
CONCLUSION
Through the choices made we were able to apply the SLOs below;
4. Apply the principles of mechanism analysis and design.
6. Apply good mechatronics principles to develop a mechatronic system to control a mechanical
device.
25 |
P a g e
Your preview ends here
Eager to read complete document? Join bartleby learn and gain access to the full version
- Access to all documents
- Unlimited textbook solutions
- 24/7 expert homework help
Warman Design Report
Mechanical Design 1 – Autumn 2021
COST ANALYSIS/ECONOMIC FEASIBILITY
For the completion of the Warman competition robot, the group had to source parts to construct the
robot. The materials that were used were all sourced locally from stores such as Bunnings, core
electronics and Jaycar. Below are the parts, the store sourced from and their costs.
Part
Store
Cost
65mm 1m PVC
Bunnings
$13
32mm 1m PVC
Bunnings
$8
20mm 1m PVC
Bunnings
$4.35
90mm 1m PVC
Bunnings
$9.85
MDF 900x600
Bunnings
$4.50
Nylon Line
Bunnings
$5
Linear Actuator (stepper motor
and lead screw)
Core Electronics
$87.95
L298N dual/stepper motor
driver
Jaycar
$14.95
Multipin Nylon 2Pin
Jaycar
$3.25
12VDC Motor
Jaycar
$18.95
Stepper Motor
Jaycar
$9.95
5-10V DC Wheel
Jaycar
$9.95
5-10V DC Wheel
Jaycar
$9.95
Total cost
$214.14
26 |
P a g e
Your preview ends here
Eager to read complete document? Join bartleby learn and gain access to the full version
- Access to all documents
- Unlimited textbook solutions
- 24/7 expert homework help
Warman Design Report
Mechanical Design 1 – Autumn 2021
CONCLUSION/DISCUSSION
This report analyses the 2 mechanical artefacts and 2 electrical artefacts for group 2 Monday class for
the Warman competition. Each components used is explained and the process through which the
robot was made is explained. The report also justifies the choices made.
However, since we have not completed the robot yet, some content may change and but the overall
design of the robot will remain the same. The project overall has helped me understand more about
how to work as a team as well as how to improve through research and constant review in order to
increase the likelihood of success in a project. It is very useful and will be able to help me transfer
this in the workplace.
27 |
P a g e
Your preview ends here
Eager to read complete document? Join bartleby learn and gain access to the full version
- Access to all documents
- Unlimited textbook solutions
- 24/7 expert homework help
Warman Design Report
Mechanical Design 1 – Autumn 2021
APPENDIX
Appendix
Appendix A: Internet multimedia -
?
links of all Videos
-
Link to video of robot’s mechanism
https://teams.microsoft.com/_?culture=en-
au&country=AU&lm=deeplink&lmsrc=NeutralHomePageWeb&cmpid=
WebSignIn#/mp4/viewer/teams/https:~2F~2Fstudentutsedu.sha
repoint.com~2Fsites~2F48600MechanicalDesign1-MD1Monday-
MohamedAwadallah~2FShared%20Documents~2FMD1%20Monday%20-
%20Mohamed%20Awadallah~2FVideos~2FMonday%20Group%202.mp4?
threadId=19:0dc9381176bb4539b7efad50241deed0@thread.tacv2
&baseUrl=https:~2F~2Fstudentutsedu.sharepoint.com~2Fsites
~2F48600MechanicalDesign1-MD1Monday-
MohamedAwadallah&fileId=681f0bc9-b887-49cd-b5b1-
7f524bd58ca3&ctx=files&rootContext=items_view&viewerActio
n=view
Appendix B: Calculations
28 |
P a g e
Your preview ends here
Eager to read complete document? Join bartleby learn and gain access to the full version
- Access to all documents
- Unlimited textbook solutions
- 24/7 expert homework help
Warman Design Report
Mechanical Design 1 – Autumn 2021
Appendix C: CAD
29 |
P a g e
Your preview ends here
Eager to read complete document? Join bartleby learn and gain access to the full version
- Access to all documents
- Unlimited textbook solutions
- 24/7 expert homework help
Warman Design Report
Mechanical Design 1 – Autumn 2021
30 |
P a g e
Your preview ends here
Eager to read complete document? Join bartleby learn and gain access to the full version
- Access to all documents
- Unlimited textbook solutions
- 24/7 expert homework help
Warman Design Report
Mechanical Design 1 – Autumn 2021
31 |
P a g e
Your preview ends here
Eager to read complete document? Join bartleby learn and gain access to the full version
- Access to all documents
- Unlimited textbook solutions
- 24/7 expert homework help
Warman Design Report
Mechanical Design 1 – Autumn 2021
32 |
P a g e
Your preview ends here
Eager to read complete document? Join bartleby learn and gain access to the full version
- Access to all documents
- Unlimited textbook solutions
- 24/7 expert homework help
Warman Design Report
Mechanical Design 1 – Autumn 2021
Made by group leader - Leon
33 |
P a g e
Your preview ends here
Eager to read complete document? Join bartleby learn and gain access to the full version
- Access to all documents
- Unlimited textbook solutions
- 24/7 expert homework help
Warman Design Report
Mechanical Design 1 – Autumn 2021
Appendix D: Team Meetings, data sheet of motor drive and code
CODE:
FOR THE WHEELS:
// connect motor controller pins to Arduino digital pins
// motor one
int enA = 10;
int in1 = 9;
int in2 = 8;
// motor two
int enB = 5;
int in3 = 7;
int in4 = 6;
void setup()
{
// set all the motor control pins to outputs
pinMode(enA, OUTPUT);
pinMode(enB, OUTPUT);
pinMode(in1, OUTPUT);
pinMode(in2, OUTPUT);
pinMode(in3, OUTPUT);
pinMode(in4, OUTPUT);
}
void demoOne()
{
// this function will run the motors in both directions at a fixed speed
// turn on motor A
digitalWrite(in1, HIGH);
digitalWrite(in2, LOW);
// set speed to 200 out of possible range 0~255
analogWrite(enA, 200);
// turn on motor B
digitalWrite(in3, HIGH);
digitalWrite(in4, LOW);
34 |
P a g e
Your preview ends here
Eager to read complete document? Join bartleby learn and gain access to the full version
- Access to all documents
- Unlimited textbook solutions
- 24/7 expert homework help
Warman Design Report
Mechanical Design 1 – Autumn 2021
// set speed to 200 out of possible range 0~255
analogWrite(enB, 200);
delay(2000);
// now change motor directions
digitalWrite(in1, LOW);
digitalWrite(in2, HIGH);
digitalWrite(in3, LOW);
digitalWrite(in4, HIGH);
delay(2000);
// now turn off motors
digitalWrite(in1, LOW);
digitalWrite(in2, LOW);
digitalWrite(in3, LOW);
digitalWrite(in4, LOW);
}
void demoTwo()
{
// this function will run the motors across the range of possible speeds
// note that maximum speed is determined by the motor itself and the operating voltage
// the PWM values sent by analogWrite() are fractions of the maximum speed possible
// by your hardware
// turn on motors
digitalWrite(in1, LOW);
digitalWrite(in2, HIGH);
digitalWrite(in3, LOW);
digitalWrite(in4, HIGH);
// accelerate from zero to maximum speed
for (int i = 0; i < 256; i++)
{
analogWrite(enA, i);
analogWrite(enB, i);
delay(20);
}
// decelerate from maximum speed to zero
for (int i = 255; i >= 0; --i)
{
analogWrite(enA, i);
analogWrite(enB, i);
delay(20);
}
// now turn off motors
digitalWrite(in1, LOW);
digitalWrite(in2, LOW);
digitalWrite(in3, LOW);
digitalWrite(in4, LOW);
}
void loop()
{
demoOne();
delay(1000);
demoTwo();
35 |
P a g e
Your preview ends here
Eager to read complete document? Join bartleby learn and gain access to the full version
- Access to all documents
- Unlimited textbook solutions
- 24/7 expert homework help
Warman Design Report
Mechanical Design 1 – Autumn 2021
delay(1000);
}
FOR THE STEPPER MOTOR
/*
Stepper Motor Control - one revolution
This program drives a unipolar or bipolar stepper motor.
The motor is attached to digital pins 8 - 11 of the Arduino.
The motor should revolve one revolution in one direction, then
one revolution in the other direction.
Created 11 Mar. 2007
Modified 30 Nov. 2009
by Tom Igoe
*/
#include <Stepper.h>
const int stepsPerRevolution = 200;
// change this to fit the number of steps per revolution
// for your motor
// initialize the stepper library on pins 8 through 11:
Stepper myStepper(stepsPerRevolution, 8, 9, 10, 11);
void setup() {
// set the speed at 60 rpm:
myStepper.setSpeed(60);
// initialize the serial port:
Serial.begin(9600);
}
void loop() {
// step one revolution
in one direction:
Serial.println("clockwise");
myStepper.step(stepsPerRevolution);
delay(500);
// step one revolution in the other direction:
Serial.println("counterclockwise");
myStepper.step(-stepsPerRevolution);
delay(500);
}
36 |
P a g e
Your preview ends here
Eager to read complete document? Join bartleby learn and gain access to the full version
- Access to all documents
- Unlimited textbook solutions
- 24/7 expert homework help
Warman Design Report
Mechanical Design 1 – Autumn 2021
37 |
P a g e
Your preview ends here
Eager to read complete document? Join bartleby learn and gain access to the full version
- Access to all documents
- Unlimited textbook solutions
- 24/7 expert homework help
Warman Design Report
Mechanical Design 1 – Autumn 2021
38 |
P a g e
Your preview ends here
Eager to read complete document? Join bartleby learn and gain access to the full version
- Access to all documents
- Unlimited textbook solutions
- 24/7 expert homework help
Warman Design Report
Mechanical Design 1 – Autumn 2021
39 |
P a g e
Your preview ends here
Eager to read complete document? Join bartleby learn and gain access to the full version
- Access to all documents
- Unlimited textbook solutions
- 24/7 expert homework help
Warman Design Report
Mechanical Design 1 – Autumn 2021
40 |
P a g e
Your preview ends here
Eager to read complete document? Join bartleby learn and gain access to the full version
- Access to all documents
- Unlimited textbook solutions
- 24/7 expert homework help
Warman Design Report
Mechanical Design 1 – Autumn 2021
41 |
P a g e
Your preview ends here
Eager to read complete document? Join bartleby learn and gain access to the full version
- Access to all documents
- Unlimited textbook solutions
- 24/7 expert homework help
Warman Design Report
Mechanical Design 1 – Autumn 2021
42 |
P a g e
Your preview ends here
Eager to read complete document? Join bartleby learn and gain access to the full version
- Access to all documents
- Unlimited textbook solutions
- 24/7 expert homework help
Warman Design Report
Mechanical Design 1 – Autumn 2021
43 |
P a g e
Your preview ends here
Eager to read complete document? Join bartleby learn and gain access to the full version
- Access to all documents
- Unlimited textbook solutions
- 24/7 expert homework help
Warman Design Report
Mechanical Design 1 – Autumn 2021
44 |
P a g e
Your preview ends here
Eager to read complete document? Join bartleby learn and gain access to the full version
- Access to all documents
- Unlimited textbook solutions
- 24/7 expert homework help
Warman Design Report
Mechanical Design 1 – Autumn 2021
REFERENCES
Anon, 2021, viewed 15 April 2021, <https://www.bunnings.com.au/ambassador-100mm-
white-plastic-centre-wheel-and-rubber-tyre_p3942885>.
Anon, 2021, viewed 15 April 2021, <https://www.bunnings.com.au/metal-mate-25-4-x-25-4-
x-1-2mm-3m-aluminium-square-box-tube_p1079488>.
Supplies, S. 2021,
Square Tube Joiner Two Way Corner
, Shapealuminium.net.au. viewed 15
April 2021, <https://www.shapealuminium.net.au/square-box-tube-joiners/square-tube-
joiner-two-way-corner>.
Collins, D. (2020, February 7). What options are there for integrated motor and
screw designs? Linear Motion Tips. <https://www.linearmotiontips.com/what-options-are-
there-for-integrated-motor-and-screw-designs/>
Instructables, & Ben1998. (2017, December 28). Linear Actuator Stepper Motor.
Instructables. <https://www.instructables.com/Linear-Actuator-Stepper-Motor/>
Bunnings’s
warehouse,
drawer
slides,
viewed
2
April
2021,
<
https://www.bunnings.com.au/our-range/building-hardware/door-window-gate-
hardware/cabinet/drawer-slides?page=1&facets=CategoryIdPath%3D8dedf25d-58b7-430e-
a87c-e889b570bc90%2CSubCategoryIdPath%3Dc175764f-6e57-4bcd-a7a8-
d0627a89047b&sort=BoostOrder&pageSize=60
>
MDF properties, viewed 10 April 2021, <
https://civiltoday.com/civil-engineering-
materials/timber/166-mdf-definition-types-properties-manufacture
>
CUBII Industrial Solutions. (2020, May). Fasteners and its importance in industry.
<https://cubii.co/en/fasteners-and-its-importance-in-industry/>
45 |
P a g e
Your preview ends here
Eager to read complete document? Join bartleby learn and gain access to the full version
- Access to all documents
- Unlimited textbook solutions
- 24/7 expert homework help
Related Documents
Related Questions
I need answers to questions 10, 11, and 12 pertaining to the print provided.
Note: A tutor keeps putting 1 question into 3 parts and wasted so many of my questions. Never had a issue before until now, please allow a different tutor to answer because I was told I am allowed 3 of these questions.
arrow_forward
I need answers to questions 1, 2, and 3 pertaining to the print provided.
Note: A tutor keeps putting 1 question into 3 parts and wasted so many of my questions. Never had a issue before until now, please allow a different tutor to answer because I was told I am allowed 3 of these questions.
arrow_forward
I need answers for problems 13, 14, and 15 pertaining to the print provided.
NOTE: If you refuse to answers all 3 parts and insist on wasting my question by breaking down 1 simple question into 3 parts, then just leave it for someone else to answer. Thank you.
arrow_forward
I asked for problems 6 and 7 to be answered, but I did not get a properly structured answered as the example shows on problem number 1. Here is the link to the questions I already had answered, could you please rewrite the answer so its properly answered as the example shows (Problem 1)?
https://www.bartleby.com/questions-and-answers/it-vivch-print-reading-for-industry-228-class-date-name-review-activity-112-for-each-local-note-or-c/cadc3f7b-2c2f-4471-842b-5a84bf505857
arrow_forward
Question 2
You are a biomedical engineer working for a small orthopaedic firm that fabricates rectangular shaped fracture
fixation plates from titanium alloy (model = "Ti Fix-It") materials. A recent clinical report documents some problems with the plates
implanted into fractured limbs. Specifically, some plates have become permanently bent while patients are in rehab and doing partial
weight bearing activities.
Your boss asks you to review the technical report that was generated by the previous test engineer (whose job you now have!) and used to
verify the design. The brief report states the following... "Ti Fix-It plates were manufactured from Ti-6Al-4V (grade 5) and machined into
solid 150 mm long beams with a 4 mm thick and 15 mm wide cross section. Each Ti Fix-It plate was loaded in equilibrium in a 4-point bending
test (set-up configuration is provided in drawing below), with an applied load of 1000N. The maximum stress in this set-up was less than the
yield stress for the…
arrow_forward
I need help solving this problem.
arrow_forward
You are a biomedical engineer working for a small orthopaedic firm that fabricates rectangular shaped fracture
fixation plates from titanium alloy (model = "Ti Fix-It") materials. A recent clinical report documents some problems with the plates
implanted into fractured limbs. Specifically, some plates have become permanently bent while patients are in rehab and doing partial
weight bearing activities.
Your boss asks you to review the technical report that was generated by the previous test engineer (whose job you now have!) and used to
verify the design. The brief report states the following... "Ti Fix-It plates were manufactured from Ti-6Al-4V (grade 5) and machined into
solid 150 mm long beams with a 4 mm thick and 15 mm wide cross section. Each Ti Fix-It plate was loaded in equilibrium in a 4-point bending
test (set-up configuration is provided in drawing below), with an applied load of 1000N. The maximum stress in this set-up was less than the
yield stress for the Ti-6Al-4V…
arrow_forward
A Team of Engineers asked for an internal combustion engine to use it in a designed car. Your role is to describe the operation sequence of different types of available engines, explain their mechanical efficiency, and deliver a detailed technical report to show your approach in solving and discussing the following tasks and issues.
You must follow the following steps to help the team:
STEP 1
Describe the operational sequence of four-stroke spark ignition and four-stroke compression ignition engines with the aid of sketches by constructing simple sketch representing the operation and plotting the P-V diagrams for each process during the cycle to show the following:
The input and output heat and net output work
The expansion and compression strokes
The air-fuel mixture intake and exhaust gasses
The spark plug when it is in the active mode
The complete cycle of ideal Otto and Diesel cycles that shows the input and output heat and net output work.
STEP 2
Explain the mechanical…
arrow_forward
Case Study – The New Engineer
Jeff was just hired by GSI, Inc. to be their Environmental and Safety Coordinator. This is Jeff's first position after completing his engineering degree. He had taken a course in safety engineering as part of his studies and felt confident that he could handle the job.
Management at GSI, Inc. has assured him that they are committed to maintaining a safe workplace. They have never had an individual dedicated to this task full-time. They will implement his recommendations if he can justify them.
As Jeff begins to get familiar with the operations, he spends considerable time on the production floor. He notices workers clean their tools before break with a liquid from an unmarked 55-gallon drum. They also use this liquid to clean residue from their skin. They use paper towels to dry their tools and hands, throw these towels in the trash, and head to the break room for a snack and/or smoke.
In talking with the workers, Jeff learns of some of…
arrow_forward
Case Study – The New Engineer
Jeff was just hired by GSI, Inc. to be their Environmental and Safety Coordinator. This is Jeff's first position after completing his engineering degree. He had taken a course in safety engineering as part of his studies and felt confident that he could handle the job.
Management at GSI, Inc. has assured him that they are committed to maintaining a safe workplace. They have never had an individual dedicated to this task full-time. They will implement his recommendations if he can justify them.
As Jeff begins to get familiar with the operations, he spends considerable time on the production floor. He notices workers clean their tools before break with a liquid from an unmarked 55-gallon drum. They also use this liquid to clean residue from their skin. They use paper towels to dry their tools and hands, throw these towels in the trash, and head to the break room for a snack and/or smoke.
In talking with the workers, Jeff learns of some of…
arrow_forward
Please give a complete solution in Handwritten format.
Strictly don't use chatgpt,I need correct answer.
Engineering dynamics
arrow_forward
I want to talks about this paragraph very briefly (pen heads)
arrow_forward
I need parts 1, 2, and 3 answered pertaining to the print provided.
NOTE: If you refuse to answers all 3 parts and insist on wasting my question, then just leave it for someone else to answer. I've never had an issue until recently one single tutor just refuses to even read the instructions of the question and just denies it for a false reasons or drags on 1 part into multiple parts for no reason.
arrow_forward
I need parts 4, 5, and 6 answered pertaining to the print provided.
arrow_forward
I need answers to questions 4, 5, and 6 pertaining to the print provided.
arrow_forward
est 2 (copy) (page 4 of 9)
A wiseup.wsu.acza/mod/quiz/attempt.php7attempt=610918cmid 148960&page=3
ops
O YouTube
M Gmail
Maps
O GENERAL MATHEM.
O New Tab
:WSU WiSeUp
1 MONLO GOA
ashboard / My courses / FLM15B2_KF_WS6222 2021 / Tests / Test 2 (copy)
uestion 4
Quz navigation
Gate AB in Figure below is 1.0 m long and 0.9 wide. Calculate force F on the gate and position X of its centre of
Not yet
answered
pressure.
Marked out of
Finish attempt
10,000
Rag question
3m
Oil,
s.g.=Q81
7m
1.0m
B
50
Answer
arrow_forward
I need parts 2 and 3 answered please and thank you.
arrow_forward
I need problems 6 and 7 solved.
I got it solved on 2 different occasions and it is not worded correctly.
NOTE: Problem 1 is an example of how it should be answered. Below are 2 seperate links to same question asked and once again it was not answered correctly. 1. https://www.bartleby.com/questions-and-answers/it-vivch-print-reading-for-industry-228-class-date-name-review-activity-112-for-each-local-note-or-c/cadc3f7b-2c2f-4471-842b-5a84bf505857
2. https://www.bartleby.com/questions-and-answers/it-vivch-print-reading-for-industry-228-class-date-name-review-activity-112-for-each-local-note-or-c/bd5390f0-3eb6-41ff-81e2-8675809dfab1
arrow_forward
Please show work in a handwritten format.
Don't use chatgpt.
Mechanics of materials/design.
arrow_forward
Please give me the answers for this i been looking at this for a hour and my head hurts
arrow_forward
Chrome
File
Edit
View
History
Bookmarks
People
Tab
Window
Help
McGraw-Hill Campus - ALEKS Science - CHM1045 GEN CHEM 1 BLENDED 669113
A bconline.broward.edu/d21/le/content/466883/fullscreen/12868783/View
McGraw-Hill Campus - ALEKS Science
O GASES
Interconverting pressure and force
A chemistry graduate student is designing a pressure vessel for an experiment. The vessel will contain gases at pressures up to 470.0 MPa. The student's
design calls for an observation port on the side of the vessel (see diagram below). The bolts that hold the cover of this port onto the vessel can safely withstand
a force of 2.80 MN.
pressure vessel
bolts
side
View
port
Calculate the maximum safe diameter w of the port. Round your answer to the nearest 0.1 cm.
O cm
Explanation
Check
O2021 McGraw-Hill Education. All Rights Reserved. Terms of Use
FEB
arrow_forward
I need answers to questions 13, 14, and 15 pertaining to the print provided.
Note: A tutor keeps putting 1 question into 3 parts and wasted so many of my questions. Never had a issue before until now, please allow a different tutor to answer because I was told I am allowed 3 of these questions.
arrow_forward
I Blackboard @ Texas Tech Uni x
Bb MasteringEngineering - Spri x
E MasteringEngineering Maste X
C Suppose That H = 3.8 M . (Fi x
X Mathway | Calculus Problem x
y! how to take a full page scree
A session.masteringengineering.com/myct/itemView?assignmentProblemID=12360392&offset=next
ABP O
Tp E
G
KAssignment #3
Fundamental Problem 2.29
5 of 6
>
I Review
Part A
Find the magnitude of the projected component of the force along the pipe AO.
(Figure 1)
Express your answer to three significant figures and include the appropriate units.
µA
FAO =
Value
Units
Submit
Request Answer
Figure
4 m
F = 400 N
6 m
5 m
B
4 m
10:31 PM
O Type here to search
2/7/2021
arrow_forward
Please solve, engineering econ
arrow_forward
The question and data are in pictures.
Please answer properly with each steps and explanation.
Best of luck.
Thank you so much in advance.
arrow_forward
SEE MORE QUESTIONS
Recommended textbooks for you
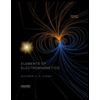
Elements Of Electromagnetics
Mechanical Engineering
ISBN:9780190698614
Author:Sadiku, Matthew N. O.
Publisher:Oxford University Press
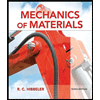
Mechanics of Materials (10th Edition)
Mechanical Engineering
ISBN:9780134319650
Author:Russell C. Hibbeler
Publisher:PEARSON
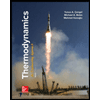
Thermodynamics: An Engineering Approach
Mechanical Engineering
ISBN:9781259822674
Author:Yunus A. Cengel Dr., Michael A. Boles
Publisher:McGraw-Hill Education
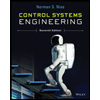
Control Systems Engineering
Mechanical Engineering
ISBN:9781118170519
Author:Norman S. Nise
Publisher:WILEY
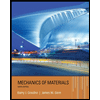
Mechanics of Materials (MindTap Course List)
Mechanical Engineering
ISBN:9781337093347
Author:Barry J. Goodno, James M. Gere
Publisher:Cengage Learning
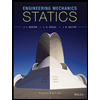
Engineering Mechanics: Statics
Mechanical Engineering
ISBN:9781118807330
Author:James L. Meriam, L. G. Kraige, J. N. Bolton
Publisher:WILEY
Related Questions
- I need answers to questions 10, 11, and 12 pertaining to the print provided. Note: A tutor keeps putting 1 question into 3 parts and wasted so many of my questions. Never had a issue before until now, please allow a different tutor to answer because I was told I am allowed 3 of these questions.arrow_forwardI need answers to questions 1, 2, and 3 pertaining to the print provided. Note: A tutor keeps putting 1 question into 3 parts and wasted so many of my questions. Never had a issue before until now, please allow a different tutor to answer because I was told I am allowed 3 of these questions.arrow_forwardI need answers for problems 13, 14, and 15 pertaining to the print provided. NOTE: If you refuse to answers all 3 parts and insist on wasting my question by breaking down 1 simple question into 3 parts, then just leave it for someone else to answer. Thank you.arrow_forward
- I asked for problems 6 and 7 to be answered, but I did not get a properly structured answered as the example shows on problem number 1. Here is the link to the questions I already had answered, could you please rewrite the answer so its properly answered as the example shows (Problem 1)? https://www.bartleby.com/questions-and-answers/it-vivch-print-reading-for-industry-228-class-date-name-review-activity-112-for-each-local-note-or-c/cadc3f7b-2c2f-4471-842b-5a84bf505857arrow_forwardQuestion 2 You are a biomedical engineer working for a small orthopaedic firm that fabricates rectangular shaped fracture fixation plates from titanium alloy (model = "Ti Fix-It") materials. A recent clinical report documents some problems with the plates implanted into fractured limbs. Specifically, some plates have become permanently bent while patients are in rehab and doing partial weight bearing activities. Your boss asks you to review the technical report that was generated by the previous test engineer (whose job you now have!) and used to verify the design. The brief report states the following... "Ti Fix-It plates were manufactured from Ti-6Al-4V (grade 5) and machined into solid 150 mm long beams with a 4 mm thick and 15 mm wide cross section. Each Ti Fix-It plate was loaded in equilibrium in a 4-point bending test (set-up configuration is provided in drawing below), with an applied load of 1000N. The maximum stress in this set-up was less than the yield stress for the…arrow_forwardI need help solving this problem.arrow_forward
- You are a biomedical engineer working for a small orthopaedic firm that fabricates rectangular shaped fracture fixation plates from titanium alloy (model = "Ti Fix-It") materials. A recent clinical report documents some problems with the plates implanted into fractured limbs. Specifically, some plates have become permanently bent while patients are in rehab and doing partial weight bearing activities. Your boss asks you to review the technical report that was generated by the previous test engineer (whose job you now have!) and used to verify the design. The brief report states the following... "Ti Fix-It plates were manufactured from Ti-6Al-4V (grade 5) and machined into solid 150 mm long beams with a 4 mm thick and 15 mm wide cross section. Each Ti Fix-It plate was loaded in equilibrium in a 4-point bending test (set-up configuration is provided in drawing below), with an applied load of 1000N. The maximum stress in this set-up was less than the yield stress for the Ti-6Al-4V…arrow_forwardA Team of Engineers asked for an internal combustion engine to use it in a designed car. Your role is to describe the operation sequence of different types of available engines, explain their mechanical efficiency, and deliver a detailed technical report to show your approach in solving and discussing the following tasks and issues. You must follow the following steps to help the team: STEP 1 Describe the operational sequence of four-stroke spark ignition and four-stroke compression ignition engines with the aid of sketches by constructing simple sketch representing the operation and plotting the P-V diagrams for each process during the cycle to show the following: The input and output heat and net output work The expansion and compression strokes The air-fuel mixture intake and exhaust gasses The spark plug when it is in the active mode The complete cycle of ideal Otto and Diesel cycles that shows the input and output heat and net output work. STEP 2 Explain the mechanical…arrow_forwardCase Study – The New Engineer Jeff was just hired by GSI, Inc. to be their Environmental and Safety Coordinator. This is Jeff's first position after completing his engineering degree. He had taken a course in safety engineering as part of his studies and felt confident that he could handle the job. Management at GSI, Inc. has assured him that they are committed to maintaining a safe workplace. They have never had an individual dedicated to this task full-time. They will implement his recommendations if he can justify them. As Jeff begins to get familiar with the operations, he spends considerable time on the production floor. He notices workers clean their tools before break with a liquid from an unmarked 55-gallon drum. They also use this liquid to clean residue from their skin. They use paper towels to dry their tools and hands, throw these towels in the trash, and head to the break room for a snack and/or smoke. In talking with the workers, Jeff learns of some of…arrow_forward
- Case Study – The New Engineer Jeff was just hired by GSI, Inc. to be their Environmental and Safety Coordinator. This is Jeff's first position after completing his engineering degree. He had taken a course in safety engineering as part of his studies and felt confident that he could handle the job. Management at GSI, Inc. has assured him that they are committed to maintaining a safe workplace. They have never had an individual dedicated to this task full-time. They will implement his recommendations if he can justify them. As Jeff begins to get familiar with the operations, he spends considerable time on the production floor. He notices workers clean their tools before break with a liquid from an unmarked 55-gallon drum. They also use this liquid to clean residue from their skin. They use paper towels to dry their tools and hands, throw these towels in the trash, and head to the break room for a snack and/or smoke. In talking with the workers, Jeff learns of some of…arrow_forwardPlease give a complete solution in Handwritten format. Strictly don't use chatgpt,I need correct answer. Engineering dynamicsarrow_forwardI want to talks about this paragraph very briefly (pen heads)arrow_forward
arrow_back_ios
SEE MORE QUESTIONS
arrow_forward_ios
Recommended textbooks for you
- Elements Of ElectromagneticsMechanical EngineeringISBN:9780190698614Author:Sadiku, Matthew N. O.Publisher:Oxford University PressMechanics of Materials (10th Edition)Mechanical EngineeringISBN:9780134319650Author:Russell C. HibbelerPublisher:PEARSONThermodynamics: An Engineering ApproachMechanical EngineeringISBN:9781259822674Author:Yunus A. Cengel Dr., Michael A. BolesPublisher:McGraw-Hill Education
- Control Systems EngineeringMechanical EngineeringISBN:9781118170519Author:Norman S. NisePublisher:WILEYMechanics of Materials (MindTap Course List)Mechanical EngineeringISBN:9781337093347Author:Barry J. Goodno, James M. GerePublisher:Cengage LearningEngineering Mechanics: StaticsMechanical EngineeringISBN:9781118807330Author:James L. Meriam, L. G. Kraige, J. N. BoltonPublisher:WILEY
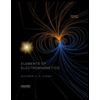
Elements Of Electromagnetics
Mechanical Engineering
ISBN:9780190698614
Author:Sadiku, Matthew N. O.
Publisher:Oxford University Press
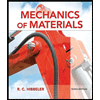
Mechanics of Materials (10th Edition)
Mechanical Engineering
ISBN:9780134319650
Author:Russell C. Hibbeler
Publisher:PEARSON
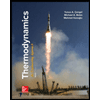
Thermodynamics: An Engineering Approach
Mechanical Engineering
ISBN:9781259822674
Author:Yunus A. Cengel Dr., Michael A. Boles
Publisher:McGraw-Hill Education
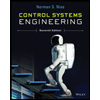
Control Systems Engineering
Mechanical Engineering
ISBN:9781118170519
Author:Norman S. Nise
Publisher:WILEY
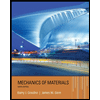
Mechanics of Materials (MindTap Course List)
Mechanical Engineering
ISBN:9781337093347
Author:Barry J. Goodno, James M. Gere
Publisher:Cengage Learning
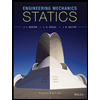
Engineering Mechanics: Statics
Mechanical Engineering
ISBN:9781118807330
Author:James L. Meriam, L. G. Kraige, J. N. Bolton
Publisher:WILEY