CEE 377 HW5 SOLUTION
pdf
keyboard_arrow_up
School
University of Washington *
*We aren’t endorsed by this school
Course
377
Subject
Mechanical Engineering
Date
Dec 6, 2023
Type
Pages
10
Uploaded by Alexkarlbrown
Homework 5
CEE 377 - Introduction to Structural Design
Problem 1
This problem involves some additional calculations involving PACCAR Hall. Consider again the W24
×
55
beam examined in Lab 3 (i.e., beam B.8/11-B.8/13).
a.
In lab we determined that the equivalent uniform
D
+
L
load corresponding to the 38 k reactions for
this beam would be 1.73 k/ft.
Use the dead and live floor load values from the floor load map to
calculate the dead load portion of this 1.73 k/ft loading (i.e.,
D/
(
D
+
L
)). Don’t forget to subtract
the member’s self weight first, then add it back in later once you’ve done a proportional split on the
dead and live floor loads.
The weight of the beam is 55 lb/ft, so we can first remove that from the total load,
leaving w = 1.675 kip/ft.
In the lab exercises, we determined that the total dead load
consisted of 58.1 psf from the 4.5 inch thick slab and 30 psf from the combined ceiling
(15 psf) and floor finish (15 psf) associated with dead load label ”4”, and that the live
load is 100 psf associated with lobby/assembly/stairs, labeled ”F”. If the ratio of dead to
total load is D/(D+L) = 88/188 = 0.468, we can assume that the dead load contributes
0.468(1.675 kip/ft) = 0.784 kip/ft.
Adding back the self-weight of the beam, we arrive
at a distributed dead load of w
D
=
0
.
839 kip/ft
.
b.
Use this uniform dead load,
w
D
, to determine the maximum displacement at the center of this beam
due to dead load only, again assuming the connections act like simple supports.
To determine the displacement, we need the stiffness terms E = 29,000 ksi and I =
1350
in
4
. For a simply supported beam under uniform loading, the maximum deflection
occurs at midspan and is of magnitude
v
max
=
5wL
4
384EI
=
(
0
.
839
k
/
ft
×
1
ft
/
12
in)(
44
ft
×
12
in
/
1
ft)
4
384
(
29000
ksi)(
1350
in
4
)
=
1
.
81
in
c.
In a simple sense, camber can be used to accommodate dead loads so that floors are close to flat prior
to live loading. Compare your dead load displacement to the specified camber of this beam. It won’t
match particularly well in this case, so see if you can identify some reasons why this might be so.
The camber for the beam of interest, as shown in the plans, is 1 inch, much lower that
what we see here. This is most likely due to overestimation of our loads and the conser-
vatism associated with the tributary area method we assumed. It could also be a function
of connection type and the system stiffness not matching a perfectly pinned-pinned as-
sumption.
d.
The 38 kip end reactions shown for the W24
×
55 girder in the plans (shown again in the figure below).
What end reactions would you get using each of the three methods presented in class (tributary area
method and alternative methods 1 and 2)? Recall that for this floor area, using ASD load combinations,
D
+
L
= 188 psf.
Because we have a simply supported beam, we can quickly determine the end reactions
by summing the total area for which the load will travel through the girders. The three
options are shown below.
Tributary Area
Method 1 (Two-Way Slab)
Method 2 (One-Way Slab)
Now we can calculate the total area and subsequent total load that will move into the
girder by multiplying the associated areas by 188 psf:
Method
A
blue
,
ft
2
D
+
L
,
kip
Reaction, kip
Tributary Area
484
91.0
45.5
Method 1
393.25
73.9
37.0
Method 2
363
68.2
34.1
e.
Find the end reactions using the area shown in the figure below as the tributary area. Note that the
floor surface on the right is about 6 inches narrower due to the wall thickness. Does this get you closer
to the 38 kip value shown in the plans?
This part of the problem is essentially the same as we solved for Method 1 above. In this
case, we got 37.0 kips, which nearly matches the 38 kip reactions provided. If we add the
self weight back, we end up with an additional reaction of (0.055 kip/ft)(44 ft)/2 = 1.2
kips, and that basically gets us to the 38 kip reactions. The 6 inch wall thickness would
make the spacing in the right most span equal to 10.5, which would reduce the total area
by
[(
5
.
5
ft)(
11
ft) + (
0
.
5
)(
5
.
5
ft)(
5
.
5
ft)]
−
[(
5
.
25
ft)(
11
ft) +
0
.
5
(
5
.
25
ft)(
5
.
25
ft)] =
4
.
1
ft
2
This results in a reduction of approximately 0.4 kips in the reactions. All of this gets us
to 37.8 kips, which is a pretty close result.
Your preview ends here
Eager to read complete document? Join bartleby learn and gain access to the full version
- Access to all documents
- Unlimited textbook solutions
- 24/7 expert homework help
f.
Instead of ASD, assume that you are using LRFD to check the design of the W24
×
55 girder. Using
the tributary area provided in part [e.] and the dead and live loads you found in part [a.], determine
i.
The maximum shear in the beam
ii.
The maximum moment in the beam
iii.
The maximum bending stress in the beam
iv.
The maximum deflection in the beam
Here we find that the distributed area load 1.2D + 1.6L = 1.2(88 psf) + 1.6(100 psf) =
266 psf. Applying the area as a distributed load, we get
1.46 klf
2.93 klf
Analyzing this beam, we can find that the end reactions are
R
left
=
R
right
=
1
2
[
0
.
5
(
1
.
46
k
/
ft)(
11
ft) + (
2
.
93
k
/
ft)(
33
ft)] =
52
.
4
kip
We know that, because this is a simply supported member, the maximum shear occurs
at the pinned supports, thus we have V
max
=
52
.
4
kip
. We also know that, for a simply
supported beam with symmetric loading, the maximum moment will occur at midspan.
We can calculate the maximum moment as
M
max
=
(
52
.
4
kip)(
22
ft)
−
(
0
.
5
)(
1
.
46
k
/
ft)(
5
.
5
ft)(
18
.
333
ft)
−
(
2
.
93
k
/
ft)(
16
.
5
ft)(
8
.
25
ft)
=
680
k
·
ft
The maximum bending stress in the beam can then be calculated by finding the seciton
modulus for the W24
×
55, which is S
=
114
in
3
, thus the maximum bending stress is
σ
max
=
M
max
/
S
=
71
.
6
ksi
. This is very high, way over the typical yield stress for a beam
of 50 ksi. There are a few reasons for this, the primary one being that this is composite
construction.
In composite construction, the moment capacity can grow quite a bit as
the steel beam and the concrete slab work together.
If you notice, there are 24 shear
studs on the W24
×
55, which justifies our assumption. The actual analysis here is quite
complex and will be left for future study.
Finally, for the deflection, this is a complicated beam to solve, and I am happy if you
used some judgment. The exact displacment calculation, based on dead and live service
loads, is 4.235 inches.
A more reasonable approach would be to use the conservative
tributary approach, which gives us an upper bound of 5wL
4
/
384EI
=
4
.
46 inches, which
represents a total displacement of L
/
118, a value that is going to be too high for any
reasonable limit state. Again, however, the composite nature of the beam will help with
this tremendously, and that’s how the beam can be properly designed.
Problem 2
For the frame below, assume that a unit load can move from point
A
to point
E
along the horizontal member.
Draw the influence lines for the vertical reactions at the supports
D
and
F
and for the shear and bending
moment at point
C
.
A
B
C
D
E
F
10 ft
15 ft
15 ft
10 ft
20 ft
Here we first need to determine the influence lines for the reactions.
The reaction at F will
behave the same as if it were at point B because this is a statically determinate frame and
the force in the direction is zero. We can use the same concept where the influence lines for
the reactions equal one directly above the joint in question and zero at other joints, with a
straight line connecting all points. Once we solve for the reactions, we consider the scenarios
when the point load is to the left and to the right of point C:
Unit load to the right of point C (cutting and looking to the left)
V
C
=
−
R
D
M
C
= 15
R
D
Unit load to the left of point C (cutting and looking to the right)
V
C
=
R
F
M
C
= 15
R
F
This gives us the following influence lines:
1.333
-0.333
(
IL
)
R
D
-0.333
1.333
(
IL
)
R
F
0.333
-0.333
-0.5
0.5
(
IL
)
V
C
-5
-5
7.5
(
IL
)
M
C
Problem 3
Using the influence lines you developed in Problem 2, determine the maximum shear and moment at point
C
assuming a uniformly distributed dead load of 1.25 kips/ft from points
A
to
E
and both a 0.640 kips/ft
uniformly distributed live load and a 40 kip concentrated live load placed to maximize shear, positive moment,
and negative moment at point
C
.
We can use the influence lines directly to solve this problem.
For maximum shear, the
dead load provides zero shear at point C due to symmetry so we can maximize either positive
or negative shear.
To maximize positive shear, we place the point load at midspan and the
distributed loads on the left cantilever and to the right of point C within the simple span.
For maximizing positive moment, the point load goes at midspan and the distributed load is
between the supports.
For maximizing negative moment, the point load goes at either free
end and the distributed load spans both cantilever sections. We can check the values for both
load combinations to see which controls. We can use the following values to help us use the
influence lines to determine the shear and moment:
A
total
A
positive
A
negative
(
IL
)
+
max
(
IL
)
−
max
V
C
, kips
0
5.417
-5.417
0.5
-0.5
M
C
, kip
·
ft
62.5
112.5
-50
7.5
-5
LC1: 1.4D
–
w
D
= 1
.
4(1
.
25 k
/
ft) = 1
.
75 k
/
ft
–
w
L
=
P
L
= 0
–
V
C
=
w
D
A
total
+
w
L
A
positive
+
P
L
(
IL
max
) = (1
.
75)(0) + (0)(5
.
417) + (0)(0
.
5) = 0
–
M
+
C
=
w
D
A
total
+
w
L
A
positive
+
P
L
(
IL
+
max
) = (1
.
75)(62
.
5) + (0)(112
.
5) + (0)(7
.
5) = 109 k
·
ft
–
M
−
C
= 0 because the dead load only results in positive moment at C
LC2: 1.2D + 1.6L
–
w
D
= 1
.
2(1
.
25 k
/
ft) = 1
.
50 k
/
ft
–
w
L
= 1
.
6(0
.
64 k
/
ft) = 1
.
024 k
/
ft
–
P
L
= 1
.
6(40 kip) = 64 kip
–
V
C
=
w
D
A
total
+
w
L
A
positive
+
P
L
(
IL
max
) = (1
.
50)(0) + (1
.
024)(5
.
417) + (64)(0
.
5) = 37
.
5 kip
–
M
+
C
=
w
D
A
total
+
w
L
A
positive
+
P
L
(
IL
+
max
) = (1
.
50)(62
.
5)+(1
.
024)(112
.
5)+(64)(7
.
5) = 689 k
·
ft
–
M
−
C
=
w
D
A
total
+
w
L
A
negative
+
P
L
(
IL
−
max
) = (1
.
50)(62
.
5)+(1
.
024)(
−
50)+(64)(
−
5) =
−
277 k
·
ft
And the 1.2D + 1.6L combination controls for all three values.
Your preview ends here
Eager to read complete document? Join bartleby learn and gain access to the full version
- Access to all documents
- Unlimited textbook solutions
- 24/7 expert homework help
Problem 4
Consider the hoist crane shown.
Stringers transfer the moving crane load to panel points on the truss.
Determine the influence line diagrams for Member
AC
and
CD
. If the max concentrated live load is 25 k,
and the normal stress is not to exceed 36 ksi, determine the truss diameter assuming each member is circular
rod with the same area. Hint: this problem can be simplified by using the method of sections to determine
the force in
CD
as a function of the reaction at the right pin, then using the method of joints at joint
C
to
calculate the force in
AC
as a function of the same reaction.
C
D
A
B
4 @ 20 ft = 80 ft
15 ft
25 kip
The influence lines for the reactions will be the same as we have had before since the truss is
simply supported. The influence lines and corresponding equations are shown below.
1
(
IL
)
R
left
= 1
−
x
80
1
(
IL
)
R
right
=
x
80
Now we can solve the two member forces as functions of the reactions. Using the method of sections, we
can cut the truss as shown below, then
C
D
A
B
1
R
left
R
right
When the unit load is to the left of member
CD
, we can look to the right, and we get
X
M
B
= 40
R
right
−
15
F
CD
= 0
⇒
F
CD
=
8
3
R
right
=
x
30
X
F
y
=
R
right
−
3
5
F
BC
= 0
⇒
F
BC
=
5
3
R
right
=
x
48
When the unit load is to the right of member
CD
, we can look to the left, and we get
X
F
y
=
R
left
+
3
5
F
BC
= 0
⇒
F
BC
=
−
5
3
R
left
=
−
5
3
1
−
x
80
=
x
−
80
48
X
M
A
=
−
20
R
left
+ 15
F
CD
+ 15
4
5
F
BC
= 0
⇒
F
CD
=
1
15
(20 + 20)
R
left
=
8
3
R
left
=
8
3
1
−
x
80
=
80
−
x
30
Then we separately consider member
AC
by solving the method of joints at joint
C
. In this case, we will
consider the unit load to the left or to the right of point
C
. When the unit load is to the left of joint
C
, we
can look to the right, and we get
X
F
y
=
F
AC
+
3
5
F
BC
= 0
⇒
F
AC
=
−
3
5
F
BC
=
−
R
right
=
−
x
80
When the unit load is to the right of joint
C
, we can look to the left, and we get
X
F
y
=
F
AC
+
3
5
F
BC
= 0
⇒
F
AC
=
−
3
5
F
BC
=
R
left
=
1
−
x
80
So this gets us here:
1
(
IL
)
F
AC
1
(
IL
)
F
CD
We have two things left to check. First, we can connect the dots for the force in member
CD
. We need
to actually think about what is happening in the missing section. For a truss, the load can only appear at
a joint, which has the implication that there is no discontinuity as shown in the result for member
CD
. For
the influence line for member
AC
, we have an inconsistency because this member is in the same direction
as the loads. The values shown in the figure above are just to the right or just to the left of point
C
, but in
fact we cannot be just to the left or right, only directly at point
C
. If we place the load at point
C
, then our
assumption that the ”load is to the left of member
CD
so we look to the right” neglects to actually include
the unit load at point
C
, so if we add it back, we get
X
F
y
=
F
AC
+
3
5
F
BC
−
1 = 0
⇒
F
AC
=
−
3
5
F
BC
= 1
−
R
right
= 1
−
x
80
= 0
.
75
This confirms that the correct selection for the influence line is 0.75 at that point. Thus, our final influence
lines are shown below.
0.75
(
IL
)
F
AC
4/3
(
IL
)
F
CD
Problem 5
Determine the moment envelope for the AASHTO design tandem (two 25 kip loads spaced 4 ft apart)
traveling across a 30 foot simply supported beam.
We did a problem very similar to this in the examples.
A
B
30 ft
25
k
25
k
4
′
1
.
0
(
I.L.
)
R
A
1
.
0
(
I.L.
)
R
B
We will construct an influence line for the moment at an arbitrary point
C
, located a distance
a
from the
left support. Taking cuts at point
C
and looking to either side as the load moves from one side to the other,
we again find that
M
C
=
bR
B
when the unit load is to the left of point
C
and
M
C
=
aR
A
when the unit
load is to the right. ,
L
= 30 ft
a
b
A
B
C
bR
B
aR
A
(
I.L.
)
M
C
ab/L
C
It doesn’t matter which load we choose to place at point
C
, so I will place the left load there. Again,
we will take advantage of symmetry and it does not matter which direction we assume for our analysis here.
The magnitude of the moment influence line needs to be found at each load. We can use the right side of
the influence line, where we find:
(
I.L.
)
M
C
=
a
(
I.L.
)
R
A
=
a
1
−
x
L
@
x
=
a
:
(
I.L.
)
M
C
=
a
1
−
a
L
=
a
(
L
−
a
)
L
=
ab
L
@
x
=
a
+ 4 :
(
I.L.
)
M
C
=
a
1
−
a
+ 4
L
=
a
(
L
−
a
−
4)
L
=
a
(
b
−
4)
L
bR
B
aR
A
(
I.L.
)
M
C
ab/L
a
(
b
−
4)
/L
C
25
k
25
k
a
4
′
b
−
4 ft
This allows us to calculate the moment at point
C
directly as a function of
a
M
C
=
ab
L
(25 kip) +
a
(
b
−
4)
L
(25 kip) =
25
a
(
L
−
a
)
L
+
25
a
(
L
−
a
−
4)
L
Now we can plug in
L
= 30 feet and simplify, and we get
M
C
=
5
a
6
(2(30)
−
2
a
−
4) =
5
a
3
(28
−
a
) =
−
5
a
2
3
+
140
a
3
This represents the equation for the maximum moment at each location
a
for all potential load locations.
We can find the location of the absolute maximum moment by taking the derivative of
M
C
with respect to
a
and finding the local maximum
dM
C
dx
=
140
−
10
a
3
= 0
⇒
a
= 14 ft
Your preview ends here
Eager to read complete document? Join bartleby learn and gain access to the full version
- Access to all documents
- Unlimited textbook solutions
- 24/7 expert homework help
This tells us that the maximum moment occurs 14 feet from the left support, or just slightly to the left of
midspan. The corresponding maximum value of the moment at
C
for
a
= 14 ft is
M
C
= 327 k
·
ft. Because
of symmetry, we can also invert this equation and find that a second location provides the same maximum
moment 14 feet from the right support. The entire moment envelope is shown below. Note that the dashed
lines inside of the envelope represent the moment envelope for the truck driving in a direction that does not
control at that location, and the two curves represent the two directions of travel.
M
max
= 327 k
·
ft
As a note, in the case of the simply supported beam, when one load is larger than all others in a load
train, the absolute maximum moment occurs when the load train is placed so the midspan of the beam is
halfway between the largest load and the centroid. For the problem above, we calculate the centroid of the
load train as directly in the middle, or ¯
x
= 2 ft. Placing point
C
so that it is halfway between the centroid
and the load train and the maximum load, we would place the load where an axle is one foot from point
C
.
Related Documents
Related Questions
SOLVE STEP BY STEP IN DIGITAL FORMAT
arrow_forward
A) Calculate the stress in each link when a force of 600 lbs is applied to the rigid element AF, employing manual calculations and finite element methods.
B) Determine the corresponding deflection at point A, manually applying the finite element penalty method to model and solve the constraints effectively.
Available Data:
The links BC and DE are made of steel.
Each link has dimensions of 1/2 inch in width and 1/4 inch in thickness.
Modulus of elasticity (E): 29 x 10^6 psi.
Instructions: For this problem, manual calculation is crucial. Utilize the finite element method with the penalty approach to handle boundary conditions and constraints effectively. This method involves incorporating penalty factors into the system equations to enforce the constraints strictly.
arrow_forward
In order to determine the magnitude of the internal forces, a FBD must be cut.
It is difficult to determine where a cut should be made in order to reveal the Maximum Internal Forces, thus we have put the distance to the cut in terms of 'x', and plot the equation.
In my lecture we took a generic portion of a Beam and applied equilibrium and saw that Loading, Shear and Moment are related to each through differential equations. Change in Shear is the Area under the Loading diagram. Change in Moment is the Area under the Shear Diagram.
Using Graphic Integration draw the shear and moment diagrams for the given beams and loading.
arrow_forward
You are a structural Engineer who works in Dar Al Handasah company. Your manager has
called for a meeting and provided you with the below schematic design of a concrete beam that
might be implemented at one of the sites. You were requested to calculate the
following: (make 15 KN bold)
40
KN
15
KN
20
KN
45
30
KN
40
KN
16
20
Figure 1: Concrete Beam
1. Find the equivalent forces of the disturbed loads.
2. Sketch the beam showing all the applied forces (reaction and equivalent
forces) and allocate them into their suitable locations proper points.
3. Apply the moment equations in the equilibrium state to find the value of the reaction
forces at points A and B.
4. If the given beam in Figure 1 compressed shrank to be 19.98 meter where the
original temperature was at the given temperature T1=200 K, find the
temperature (T2) after the compression shrinking.
arrow_forward
Use answer from first part without spring to build onto next part, thanks.
arrow_forward
Help!!! Please answer all Correctly!!! Please
arrow_forward
I need correct solution only handwritten listen again only handwritten
arrow_forward
> Next question You can retry this question below
A triangular distributed load of max intensity w-490 N/m acts on beam AB.
The beam is supported by a pin at A and member CD, which is connected by
pins at C and D respectively. Determine the reaction forces at A and C.
Enter your answers in Cartesian components. Assume the masses of both beam
AB and member CD are negligible.
cc 030
BY NC SA
2016 Eric Davishahl
Variable Value
6.6 m
a
b
C
D
11.88 m
4.95 m
Values for dimensions on the figure are given in the following table. Note the
figure may not be to scale.
The reaction at A is A = -11268.69
N.
The reaction at Cis C= 11268.69
N.
20
Submit Question Jump to Answer
X2-3923.92
B
X2+ -8451.52
H
X
X
arrow_forward
TEXT: A five (5) metre long beam is stored in A, B and C, as indicated on the sketch. The beam has ajoints in point D. The beam has an outer downward directed evenly distributed load q=4kN/m and a concentratedhorizontal load N=20kN , as indicated on the sketch.
a) Calculate the bearing reactions of the beam for the external given load effect.b) Calculate the joint force in the joint D.
arrow_forward
For the beam and loading shown in Figure 5, determine the value of (r) at the point of action of the resuitant force of the distributed load using
point B as the origin.
Parabola
Vertex
2000 N/m
900 N/m
B
6 m
A Figure 5: A parabolic distributed load on a beam AB.
Answer:
If the loading were analysed using point A as the origin, would the value of w at the location of the resultant change?
Select one:
a. No
b. Yes
arrow_forward
Help me answer this please
arrow_forward
Problem 1: (Please solve parts A and B of problem)
A) A uniformly distributed load is subjected on the clamped-clamped beam and it is supported by a spring in the middle of the beam. Using Castigliano’s theorem, find the deflection in the spring. (Please use only Castigliano’s theorem to solve this part)
B) Remove the spring in part A and use the Rayleigh-Ritz method to solve for the deflection at the middle of the beam.
Assume that v(x) = C (1- Cos((2Pi*x)/L)) (Please use only Rayleigh-Ritz method for this part)
arrow_forward
solve, show all steps and fbd. do not provide copied answer or I will report
Do problem 12 -22 using double integration. Also find how much additional deflection is added (to the max) if we account for the beam self-weight. Find this additional deflection using the table in appendix C.
mechanics of materials chapter 12 (integration of moment)= theta, and integration of theta = v
arrow_forward
B
X-SeT
Problem Statement:
Consider an S203x34 beam under self-weight loading only with a length of 11.4 m. Find the following, assuming the beam is composed of structural steel.
(a) The deflection of the beam at B.
(b) The slope of the beam at point B.
(c) The factor of safety against yielding for the beam. (Use the sectional modulus for this question.)
(d) The maximum length of the beam given a factor of safety of 2.02 against yielding.
(e) The deflection of the beam at point B using the length calculated from part (d).
Answers:
(Denote upward deflections with positive values, and downward deflections with negative values. Denote positive slopes with positive values and negative
slopes with negative values.)
(а) ув -
(b) OB =
(c) FS =
(d) anew =
(е) ув,леш
be sure to include units with your answers
arrow_forward
calculate the theoretical stress using the flexure or bending stress formula. The experimental se
is shown in Figure 1:
•
L
LB 10 inches
w = 1.5 inches
t = 0.25 inches
LB
Take a few minutes to solve the following pre-lab exercise problems before continuing with the
background unit:
Problem 1:
An experiment was set up according to Figure 1 with the following:
L=12 inches
Figure 1: Simple cantilever beam
with single longitudinal strain gage
Search
t
P = 4 lbs
With the load applied, the longitudinal strain gage reading was recorded as 83 us
(microstrain). Determine the elastic modulus of the beam material. What material is it?
MEXY
arrow_forward
The question answer includes 4 pages with 2 diagrams if u don't know the solution or is there a slight mistake i will downvote and will report to bartleby for revocation. Here is the question :
A cantilever beam of length 1m carries a point load of 2000N at the free end. The cross-section of the cantilever is an unequal angle of dimensions 100mm by 60mm and 10 mm thick. The small leg of angle (i.e 60 mm) is horizontal. The load passes through the centroid of the cross-section. Determine: (i) Position of neutral axis; (ii) The magnitude of maximum stress set up at the fixed section of the cantilever.
arrow_forward
SEE MORE QUESTIONS
Recommended textbooks for you
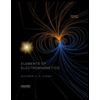
Elements Of Electromagnetics
Mechanical Engineering
ISBN:9780190698614
Author:Sadiku, Matthew N. O.
Publisher:Oxford University Press
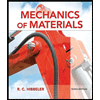
Mechanics of Materials (10th Edition)
Mechanical Engineering
ISBN:9780134319650
Author:Russell C. Hibbeler
Publisher:PEARSON
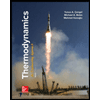
Thermodynamics: An Engineering Approach
Mechanical Engineering
ISBN:9781259822674
Author:Yunus A. Cengel Dr., Michael A. Boles
Publisher:McGraw-Hill Education
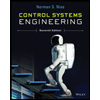
Control Systems Engineering
Mechanical Engineering
ISBN:9781118170519
Author:Norman S. Nise
Publisher:WILEY
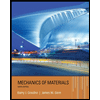
Mechanics of Materials (MindTap Course List)
Mechanical Engineering
ISBN:9781337093347
Author:Barry J. Goodno, James M. Gere
Publisher:Cengage Learning
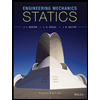
Engineering Mechanics: Statics
Mechanical Engineering
ISBN:9781118807330
Author:James L. Meriam, L. G. Kraige, J. N. Bolton
Publisher:WILEY
Related Questions
- SOLVE STEP BY STEP IN DIGITAL FORMATarrow_forwardA) Calculate the stress in each link when a force of 600 lbs is applied to the rigid element AF, employing manual calculations and finite element methods. B) Determine the corresponding deflection at point A, manually applying the finite element penalty method to model and solve the constraints effectively. Available Data: The links BC and DE are made of steel. Each link has dimensions of 1/2 inch in width and 1/4 inch in thickness. Modulus of elasticity (E): 29 x 10^6 psi. Instructions: For this problem, manual calculation is crucial. Utilize the finite element method with the penalty approach to handle boundary conditions and constraints effectively. This method involves incorporating penalty factors into the system equations to enforce the constraints strictly.arrow_forwardIn order to determine the magnitude of the internal forces, a FBD must be cut. It is difficult to determine where a cut should be made in order to reveal the Maximum Internal Forces, thus we have put the distance to the cut in terms of 'x', and plot the equation. In my lecture we took a generic portion of a Beam and applied equilibrium and saw that Loading, Shear and Moment are related to each through differential equations. Change in Shear is the Area under the Loading diagram. Change in Moment is the Area under the Shear Diagram. Using Graphic Integration draw the shear and moment diagrams for the given beams and loading.arrow_forward
- You are a structural Engineer who works in Dar Al Handasah company. Your manager has called for a meeting and provided you with the below schematic design of a concrete beam that might be implemented at one of the sites. You were requested to calculate the following: (make 15 KN bold) 40 KN 15 KN 20 KN 45 30 KN 40 KN 16 20 Figure 1: Concrete Beam 1. Find the equivalent forces of the disturbed loads. 2. Sketch the beam showing all the applied forces (reaction and equivalent forces) and allocate them into their suitable locations proper points. 3. Apply the moment equations in the equilibrium state to find the value of the reaction forces at points A and B. 4. If the given beam in Figure 1 compressed shrank to be 19.98 meter where the original temperature was at the given temperature T1=200 K, find the temperature (T2) after the compression shrinking.arrow_forwardUse answer from first part without spring to build onto next part, thanks.arrow_forwardHelp!!! Please answer all Correctly!!! Pleasearrow_forward
- I need correct solution only handwritten listen again only handwrittenarrow_forward> Next question You can retry this question below A triangular distributed load of max intensity w-490 N/m acts on beam AB. The beam is supported by a pin at A and member CD, which is connected by pins at C and D respectively. Determine the reaction forces at A and C. Enter your answers in Cartesian components. Assume the masses of both beam AB and member CD are negligible. cc 030 BY NC SA 2016 Eric Davishahl Variable Value 6.6 m a b C D 11.88 m 4.95 m Values for dimensions on the figure are given in the following table. Note the figure may not be to scale. The reaction at A is A = -11268.69 N. The reaction at Cis C= 11268.69 N. 20 Submit Question Jump to Answer X2-3923.92 B X2+ -8451.52 H X Xarrow_forwardTEXT: A five (5) metre long beam is stored in A, B and C, as indicated on the sketch. The beam has ajoints in point D. The beam has an outer downward directed evenly distributed load q=4kN/m and a concentratedhorizontal load N=20kN , as indicated on the sketch. a) Calculate the bearing reactions of the beam for the external given load effect.b) Calculate the joint force in the joint D.arrow_forward
- For the beam and loading shown in Figure 5, determine the value of (r) at the point of action of the resuitant force of the distributed load using point B as the origin. Parabola Vertex 2000 N/m 900 N/m B 6 m A Figure 5: A parabolic distributed load on a beam AB. Answer: If the loading were analysed using point A as the origin, would the value of w at the location of the resultant change? Select one: a. No b. Yesarrow_forwardHelp me answer this pleasearrow_forwardProblem 1: (Please solve parts A and B of problem) A) A uniformly distributed load is subjected on the clamped-clamped beam and it is supported by a spring in the middle of the beam. Using Castigliano’s theorem, find the deflection in the spring. (Please use only Castigliano’s theorem to solve this part) B) Remove the spring in part A and use the Rayleigh-Ritz method to solve for the deflection at the middle of the beam. Assume that v(x) = C (1- Cos((2Pi*x)/L)) (Please use only Rayleigh-Ritz method for this part)arrow_forward
arrow_back_ios
SEE MORE QUESTIONS
arrow_forward_ios
Recommended textbooks for you
- Elements Of ElectromagneticsMechanical EngineeringISBN:9780190698614Author:Sadiku, Matthew N. O.Publisher:Oxford University PressMechanics of Materials (10th Edition)Mechanical EngineeringISBN:9780134319650Author:Russell C. HibbelerPublisher:PEARSONThermodynamics: An Engineering ApproachMechanical EngineeringISBN:9781259822674Author:Yunus A. Cengel Dr., Michael A. BolesPublisher:McGraw-Hill Education
- Control Systems EngineeringMechanical EngineeringISBN:9781118170519Author:Norman S. NisePublisher:WILEYMechanics of Materials (MindTap Course List)Mechanical EngineeringISBN:9781337093347Author:Barry J. Goodno, James M. GerePublisher:Cengage LearningEngineering Mechanics: StaticsMechanical EngineeringISBN:9781118807330Author:James L. Meriam, L. G. Kraige, J. N. BoltonPublisher:WILEY
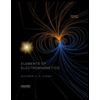
Elements Of Electromagnetics
Mechanical Engineering
ISBN:9780190698614
Author:Sadiku, Matthew N. O.
Publisher:Oxford University Press
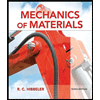
Mechanics of Materials (10th Edition)
Mechanical Engineering
ISBN:9780134319650
Author:Russell C. Hibbeler
Publisher:PEARSON
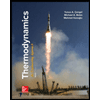
Thermodynamics: An Engineering Approach
Mechanical Engineering
ISBN:9781259822674
Author:Yunus A. Cengel Dr., Michael A. Boles
Publisher:McGraw-Hill Education
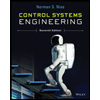
Control Systems Engineering
Mechanical Engineering
ISBN:9781118170519
Author:Norman S. Nise
Publisher:WILEY
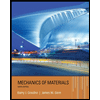
Mechanics of Materials (MindTap Course List)
Mechanical Engineering
ISBN:9781337093347
Author:Barry J. Goodno, James M. Gere
Publisher:Cengage Learning
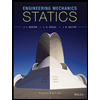
Engineering Mechanics: Statics
Mechanical Engineering
ISBN:9781118807330
Author:James L. Meriam, L. G. Kraige, J. N. Bolton
Publisher:WILEY