Lab_3_Report_Olsowski (1)
docx
keyboard_arrow_up
School
Florida Atlantic University *
*We aren’t endorsed by this school
Course
4730L
Subject
Mechanical Engineering
Date
Dec 6, 2023
Type
docx
Pages
7
Uploaded by ChancellorHummingbirdMaster103
Department of Ocean and Mechanical Engineering
Lab subject: DEFLECTION OF SIMPLE AND COMPOSED BEAMS
Submission Date: September 21, 2023
Submitted to: Dr. Oren Masory
Team # R7
Team members:
1. Scott Olsowski
2. Michael Micele
Abstract:
This experiment aimed to determine the Young's Modulus,
(
E
)
, for individual beams labeled
as A and B, and their combined configurations. Using a simple support setup, deflections were
measured at two distinct positions, L2 (16 inches) and L3 (22 inches), under a constant applied
force of 5 pounds at a distance L1 (10 inches) from the support. Using the deflection formula, we
could derive and calculate Young's Modulus for each configuration. Preliminary results showed
varied
(
E
)
values for different beam setups and positions. These findings were compared
with standard Young's Modulus values for known materials to deduce the beams' probable
material compositions. The experiment provides insights into the mechanical properties of
materials under load and emphasizes the importance of accurate measurements and calculations
in determining material characteristics. Moreover, the juxtaposition of individual and combined
beam configurations highlighted the complexities introduced when materials interact under load.
The derived values from this experiment were foundational in understanding material behavior
and could be pivotal for more complex mechanical applications.
List of Symbols:
(
E
)
- Young's Modulus
(
L
)
- Length of the span
(
L
1,
L
2,
L
3)
- Measurement distances along the beam
(
P
)
- Applied force (5 pounds)
List of Tables
:
Table 1: Inertia Values for Beam A and B
Table 2: Deflection values for Beam A and B with calculated
(
E
)
Introduction:
The deflection of beams under applied loads is a foundational concept in mechanical and civil
engineering. Understanding the behavior of materials under stress is crucial for predicting the
performance of structures and ensuring their safety and longevity. This lab experiment was
designed to evaluate the Young's Modulus (often called the modulus of elasticity) of two
different beams and their composite forms. By examining individual beams and their combined
configurations, we aim to comprehensively understand their mechanical properties and the
impact of composite configurations on these properties.
Theoretical Background:
Beam Deflection
: When a load is applied to a beam supported at its ends, it deflects. This
deflection depends on several factors: the applied load, the method of load application, the shape
of the beam (its cross-sectional area and moment of inertia), the span length of the beam, and the
material's properties. The amount a beam bends is directly related to its ability to bear the loads it
will experience, making this an essential aspect of structural and mechanical design.
Young's Modulus (E)
: One of the material properties that significantly influence beam
deflection is the Young's Modulus, denoted as
E
. It measures a material's stiffness and is defined
as the stress ratio (force per unit area) to strain (proportional deformation). A higher
E
value
indicates a stiffer material. In this lab,
E
is determined experimentally by measuring beam
deflection under known loads and using the relationship:
E
=
{
6
×δ ×I
}
{
(
P× L
1
2
×
20
)
}
(
L
+
L
1
)
here
P
is the applied load,
L
1 is the distance to the load,
δ
is the deflection, and
I
is the moment
of inertia of the beam.
Moment of Inertia (I)
: The moment of inertia,
I
, of a beam's cross-sectional area about a given
axis describes the beam's ability to resist bending. It depends on both the size and shape of the
beam's cross-sectional area. For a rectangular cross-section, the moment of inertia is given by:
I
=
{
b×h
3
}
{
12
}
Where
b
is the width and
h
is the height of the cross-section.
Composite Beams
: Composite beams are made of more than one material or a single material in
various configurations. In this lab, beams A and B are combined in various configurations to
understand how their combined properties influence deflection and, consequently, the calculated
Young's Modulus.
I
eff
=
I
a
+
I
b
Apparatus:
- Beams: A (1" x .25") and B (1" x .125")
- Simple Support Structure
- Precision Dial on a magnetic-based arm
- Tape Measure
Procedure:
1.
Mount the respective beam with a span of L (30 inches).
2.
A force, P (5 pounds), is applied at L1 (10 inches).
3.
Measure the deflection at L2 (16 inches) and L3 (22 inches).
4.
As outlined in the lab manual, The above steps are repeated for different beams A and B
configurations
Your preview ends here
Eager to read complete document? Join bartleby learn and gain access to the full version
- Access to all documents
- Unlimited textbook solutions
- 24/7 expert homework help
Results:
All calculations were done using Microsoft Excel.
Inertia of a Bar:
I=bh^3/12
b
a
=
1
h
a
=
0.25
I
a
=
0.0013
b
b
=
1
h
b
=
0.125
I
b
=
0.0002
I
ef
=
0.0015
Table 1: Inertia Values for Beam A and B
Table 2: Deflection values for Beam A
Error Analysis Discussion:
It's important to compare the calculated Young's Modulus (E) values against known standards for
the materials in question to critically analyze the results obtained from the experiment. For this
experiment, we will assume standard values for aluminum and brass, and the error will be
computed accordingly.
1. Comparative Analysis:
Assuming standard Young's Modulus for:
- Aluminum:
(
E
{
standard, Al
}
)
= 10,000,000 psi
- Brass:
(
E
{
standard, Brass
}
)
= 15,000,000 psi
From the experiment, the calculated values were:
- Beam A:
(
E
{
calculated, A
}
)
= 142,222,222.2 psi at L2 and 204,800,000 psi at L3.
- Beam B:
(
E
{
calculated, B
}
)
= 512,000,000 psi at L2 and 744,727,272.7 psi at L3.
The percentage error is given by:
¿
[%
Error
=
(
{
|
E
{
calculated
}
−
E
{
standard
}
|
}
{
E
{
standard
}
}
)
×
100
Using the above formula, the percentage errors are:
- For Beam A (assuming aluminum):
- At L2: 1,322.22%
- At L3: 1,948.00%
- For Beam B (assuming brass):
- At L2: 3,413.33%
- At L3: 4,964.85%
2. Potential Sources of High Errors:
- Inaccurate Measurements: Any inaccuracies in the deflection measurements, beam
dimensions, or applied load can lead to significant discrepancies in the calculated Young's
Modulus.
- Assumptions about Material: It's possible that the beams might not be pure aluminum or
brass but alloys with slightly different mechanical properties.
- Beam Imperfections: Any imperfections, inconsistencies, or residual stresses within the beam
can alter its behavior under load, leading to deviations from expected deflection values.
- Methodological Errors: Any inconsistency in the setup, like uneven support or slight
variations in load application, can affect the results.
3. Recommendations for Improvement:
- Ensure measurement tools are correctly calibrated and are of high precision.
- Verify the purity or exact composition of the beam materials.
- Conduct repeated trials to check for consistency in results and average out random errors.
- Ensure the setup is as per the theoretical assumptions to reduce methodological errors.
Conclusions and Recommendations:
Conclusions:
1. Young's Modulus Values:
- The Young's Modulus (E) for Beam A was determined to be
approximately
(
E
{
calculated , A
}
)
=
142,222,222.2 psi at L2 and 204,800,000 psi at L3.
- For Beam B, the corresponding values were
(
E
{
calculated, B
}
)
= 512,000,000 psi at L2 and
744,727,272.7 psi at L3.
- In layered and bolted configurations, the composite beams demonstrated different Young's
Modulus values, indicating the influence of combined properties and the interaction between
Beam A and Beam B.
2. Comparison to Theoretical Values:
- The lab results provided valuable insights into the behavior of both individual and composite
beams under a load. The actual behavior might slightly deviate from theoretical predictions,
emphasizing the importance of real-world testing.
3. Composite Beam Analysis:
- The experiment showcased the complex nature of composite materials, which do not merely
manifest properties as a direct combination of their components. The interactions between the
two beams, especially in the bolted configuration, produced intriguing results.
Recommendations:
1. Repeated Trials:
Your preview ends here
Eager to read complete document? Join bartleby learn and gain access to the full version
- Access to all documents
- Unlimited textbook solutions
- 24/7 expert homework help
- To improve the accuracy and reliability of results, it's recommended to conduct repeated
trials. This not only helps to validate the obtained results but also averages random errors that
might occur in a single trial.
2. Enhanced Measurement Tools:
- Using digital measurement tools, especially for measuring deflections, can increase the
accuracy of the readings, leading to more precise calculated values.
3. Benchmark Comparisons:
- If possible, future experiments should include benchmark tests using materials with known
Young's Modulus values. This will provide a reference point and aid in assessing the accuracy of
the experimental setup and methodology.
4. Review of Experimental Setup:
- Regularly check the experimental setup for alignment, wear, and calibration. This ensures
consistency across trials and reduces systematic errors.
5. Further Study:
- It's advisable to delve deeper into the properties of composite materials in different
configurations. Exploring different bolting techniques or layering sequences could lead to
varying results and provide more insights into the behavior of composite materials.
In conclusion, this experiment provided essential hands-on experience and understanding of
beam deflections and the factors influencing them. It's an excellent foundation for further
exploration in the field of material science and mechanical engineering.
References:
[1] Ugural, A. C., and Saul K. Fenster. “5.”
Advanced Mechanics of Materials and Applied
Elasticity
, Pearson, 2020.
Related Documents
Related Questions
slove 1,2 and 3
arrow_forward
Engineering Computation. Please show all work! EI=2,900,000k-in^2
arrow_forward
A long steel rod is placed horizontally between two supports, one at each end. The rod bends a little in the center. Which property of this rod can be used to estimate how much the rod should bend at the center?
1.
Its Shear Modulus
2.
Its Young's Modulus
3.
All of these Moduli can be used to compute how much it bends.
4.
Its Bulk Modulus.
arrow_forward
Deform hw. Please help
arrow_forward
You are a structural Engineer who works in Dar Al Handasah company. Your manager has
called for a meeting and provided you with the below schematic design of a concrete beam that
might be implemented at one of the sites. You were requested to calculate the
following: (make 15 KN bold)
40
KN
15
KN
20
KN
45
30
KN
40
KN
16
20
Figure 1: Concrete Beam
1. Find the equivalent forces of the disturbed loads.
2. Sketch the beam showing all the applied forces (reaction and equivalent
forces) and allocate them into their suitable locations proper points.
3. Apply the moment equations in the equilibrium state to find the value of the reaction
forces at points A and B.
4. If the given beam in Figure 1 compressed shrank to be 19.98 meter where the
original temperature was at the given temperature T1=200 K, find the
temperature (T2) after the compression shrinking.
arrow_forward
In order to determine the magnitude of the internal forces, a FBD must be cut.
It is difficult to determine where a cut should be made in order to reveal the Maximum Internal Forces, thus we have put the distance to the cut in terms of 'x', and plot the equation.
In my lecture we took a generic portion of a Beam and applied equilibrium and saw that Loading, Shear and Moment are related to each through differential equations. Change in Shear is the Area under the Loading diagram. Change in Moment is the Area under the Shear Diagram.
Using Graphic Integration draw the shear and moment diagrams for the given beams and loading.
arrow_forward
Please Provide correct solution, correct Method.
No Missing steps / calculations.
No Handwriting please
arrow_forward
5) Calculations for the red dog food can rolling down the slope in the Rube Goldberg design are
as follows (we will name it Step 1):
Step 1 (calculations are given):
Coefficient of friction → μ = 0.14
Mass of the object → m = 368 gm = 0.368kg
Initial height of the object (red can on top of books) → h=8.89, cm = 0.0889 m
Slope of the file folder → 0= 14°
Travelling Distance by the object = 11.5 inch = 0.292 m
And length that the object will travel = h/sin 0 = 0.0889/ sin14° = 0.367 m
So, the radius of the object → R = 0.367 -0.292 = 0.075 m
Initial Velocity of red can → u = 0
Velocity and Force Calculations for Step 1:
-From total mechanical energy conservation: → Initial mechanical energy = final mechanical energy →
mg
- In case of pure rolling, the velocity of the center of mass: →V=Roo= 0.075 x 14.28 = 1.07 m/s.
-Hence the change in force acting on the object for the travel: →F=mgsine = 0.368 x 9.81 × sin14°
=0.89 N
Step 2: The Selective Step (Step 2) in this design and for the…
arrow_forward
QUESTION 17
A design engineer is considering the application of a square box beam for a component of a bridge. A schematic of the beam is included in Figure Q17. The
beams are to be produced from a structural steel with shear modulus 81 GPa. The thickness of the section t is equal to 0.017 m and its breadth b 0.2 m.
Give your answer to 3 significant figures in Pa m4 and non-scientific notation e.g. 10000 rather than 10e05. Do not include units in your answer
where:
4A²
JT =
$7/ds
Torsional stiffness = GJT
b
Figure Q17: Cross-section of a square box-beam
arrow_forward
I need correct solution only handwritten listen again only handwritten
arrow_forward
SHOW YOUR SOLUTIONS PLS
INSTRUCTIONS:
A beam having a tee-shaped cross section is subjected to equal 18 kN-m bending moments, as shown. Assume bf = 125 mm, tf = 25 mm, d = 185 mm, tw = 20 mm. The cross-sectional dimensions of the beam are also shown.
Use these information to answer questions 1-5.
QUESTIONS:
1) Determine the centroid location (measured upward from the bottom), in mm rounded to the nearest tenths.
2) With reference to problem 2, determine the moment of inertia about the z axis. Express your answer in (106) mm4 rounded to three significant figures.
3) With reference to problem 2, determine the controlling section modulus about the z axis. Express your answer in (103) mm3 rounded to three significant figures.
4) With reference to problem 2, determine the bending stress at point H (positive if tensile and negative if compressive). Express your answer in MPa rounded to the nearest hundredths.
5) With reference to problem 2, determine the maximum bending stress…
arrow_forward
Hi i need to carry out a propagation of Young's modulus to find the overall error for it. I have the readings and I have calculated the overall error for E (for Cantilever beam) but I'm not sure if it is correct. Pls could it be checked or could I have some help with it please. Thanks.
arrow_forward
Draw the shear force, bending moment and normal force diagram for the simple beam loading given below.
Do not copy paste this answer as it is incomplete and not clear
https://www.bartleby.com/questions-and-answers/a-a-20cm-200n-40cm-200n-45-60cm-ib-y/a5a940f9-2e4f-4826-8c8c-65bdb1039b9a
arrow_forward
Could I get this question explained step for step thanks
arrow_forward
Formulate the boundary-value problem for a beam (thin beam)
arrow_forward
True or False
arrow_forward
Just don't plot on excel just solve it
arrow_forward
A manufacturing company (Company X) that manufactures rigging equipment such as steel wire rope,lifting chains, synthetic slings…etc, outsources all their equipment load testing jobs to external clients.Company X is looking to perform all equipment load testing in-house. To accommodate the expansion, theowner decides to utilize existing equipment which consists of an overhead I-beam (10m long, 553 x 210 x138) and hoist. As an Engineer, he has requested your assistance to determine if the existing beam iscapable of performing the intended function, if not, advise on a suitable beam for the task.
1. Sketch a free-body diagram of the simply supported beam with loads applied. By assessing the sketch,evaluate the slope and deflection on the beam when the maximum load is lifted, By using the data fromthe attached excel file “LO2 Data”2. Determine the suitability of this beam for the given application If the maximum allowable deflection isset at 23mm.
arrow_forward
Do not provide handwritten solution,Maintain accuracy and quality in your answer,Take care of plagiarism,Answer completely,You will get up vote for sure.
arrow_forward
03 Question (1 point)
question? It is worth 1 point/ You have unlimited attempts/There is no
Calculate the value of K at 25°C for the reaction:
5Fe2+(aq) + MnO4(aq) + 8H+ (aq)
5Fe3+ (aq) + Mn2+(aq) + 4H₂O(1)
Use the standard reduction potentials below to complete the calculation:
MnO4(aq) +8H+ (aq) +5e¯ →→→ Mn²+ (aq) +4H₂O(1) E° = 1.507 V
Fe2+ (aq) E° = 0.770 V
Fe3+ (aq) +le
1st attempt
K=
See Period
arrow_forward
SEE MORE QUESTIONS
Recommended textbooks for you
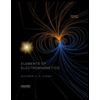
Elements Of Electromagnetics
Mechanical Engineering
ISBN:9780190698614
Author:Sadiku, Matthew N. O.
Publisher:Oxford University Press
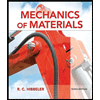
Mechanics of Materials (10th Edition)
Mechanical Engineering
ISBN:9780134319650
Author:Russell C. Hibbeler
Publisher:PEARSON
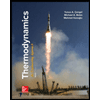
Thermodynamics: An Engineering Approach
Mechanical Engineering
ISBN:9781259822674
Author:Yunus A. Cengel Dr., Michael A. Boles
Publisher:McGraw-Hill Education
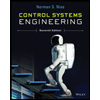
Control Systems Engineering
Mechanical Engineering
ISBN:9781118170519
Author:Norman S. Nise
Publisher:WILEY
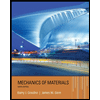
Mechanics of Materials (MindTap Course List)
Mechanical Engineering
ISBN:9781337093347
Author:Barry J. Goodno, James M. Gere
Publisher:Cengage Learning
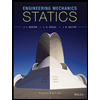
Engineering Mechanics: Statics
Mechanical Engineering
ISBN:9781118807330
Author:James L. Meriam, L. G. Kraige, J. N. Bolton
Publisher:WILEY
Related Questions
- slove 1,2 and 3arrow_forwardEngineering Computation. Please show all work! EI=2,900,000k-in^2arrow_forwardA long steel rod is placed horizontally between two supports, one at each end. The rod bends a little in the center. Which property of this rod can be used to estimate how much the rod should bend at the center? 1. Its Shear Modulus 2. Its Young's Modulus 3. All of these Moduli can be used to compute how much it bends. 4. Its Bulk Modulus.arrow_forward
- Deform hw. Please helparrow_forwardYou are a structural Engineer who works in Dar Al Handasah company. Your manager has called for a meeting and provided you with the below schematic design of a concrete beam that might be implemented at one of the sites. You were requested to calculate the following: (make 15 KN bold) 40 KN 15 KN 20 KN 45 30 KN 40 KN 16 20 Figure 1: Concrete Beam 1. Find the equivalent forces of the disturbed loads. 2. Sketch the beam showing all the applied forces (reaction and equivalent forces) and allocate them into their suitable locations proper points. 3. Apply the moment equations in the equilibrium state to find the value of the reaction forces at points A and B. 4. If the given beam in Figure 1 compressed shrank to be 19.98 meter where the original temperature was at the given temperature T1=200 K, find the temperature (T2) after the compression shrinking.arrow_forwardIn order to determine the magnitude of the internal forces, a FBD must be cut. It is difficult to determine where a cut should be made in order to reveal the Maximum Internal Forces, thus we have put the distance to the cut in terms of 'x', and plot the equation. In my lecture we took a generic portion of a Beam and applied equilibrium and saw that Loading, Shear and Moment are related to each through differential equations. Change in Shear is the Area under the Loading diagram. Change in Moment is the Area under the Shear Diagram. Using Graphic Integration draw the shear and moment diagrams for the given beams and loading.arrow_forward
- Please Provide correct solution, correct Method. No Missing steps / calculations. No Handwriting pleasearrow_forward5) Calculations for the red dog food can rolling down the slope in the Rube Goldberg design are as follows (we will name it Step 1): Step 1 (calculations are given): Coefficient of friction → μ = 0.14 Mass of the object → m = 368 gm = 0.368kg Initial height of the object (red can on top of books) → h=8.89, cm = 0.0889 m Slope of the file folder → 0= 14° Travelling Distance by the object = 11.5 inch = 0.292 m And length that the object will travel = h/sin 0 = 0.0889/ sin14° = 0.367 m So, the radius of the object → R = 0.367 -0.292 = 0.075 m Initial Velocity of red can → u = 0 Velocity and Force Calculations for Step 1: -From total mechanical energy conservation: → Initial mechanical energy = final mechanical energy → mg - In case of pure rolling, the velocity of the center of mass: →V=Roo= 0.075 x 14.28 = 1.07 m/s. -Hence the change in force acting on the object for the travel: →F=mgsine = 0.368 x 9.81 × sin14° =0.89 N Step 2: The Selective Step (Step 2) in this design and for the…arrow_forwardQUESTION 17 A design engineer is considering the application of a square box beam for a component of a bridge. A schematic of the beam is included in Figure Q17. The beams are to be produced from a structural steel with shear modulus 81 GPa. The thickness of the section t is equal to 0.017 m and its breadth b 0.2 m. Give your answer to 3 significant figures in Pa m4 and non-scientific notation e.g. 10000 rather than 10e05. Do not include units in your answer where: 4A² JT = $7/ds Torsional stiffness = GJT b Figure Q17: Cross-section of a square box-beamarrow_forward
- I need correct solution only handwritten listen again only handwrittenarrow_forwardSHOW YOUR SOLUTIONS PLS INSTRUCTIONS: A beam having a tee-shaped cross section is subjected to equal 18 kN-m bending moments, as shown. Assume bf = 125 mm, tf = 25 mm, d = 185 mm, tw = 20 mm. The cross-sectional dimensions of the beam are also shown. Use these information to answer questions 1-5. QUESTIONS: 1) Determine the centroid location (measured upward from the bottom), in mm rounded to the nearest tenths. 2) With reference to problem 2, determine the moment of inertia about the z axis. Express your answer in (106) mm4 rounded to three significant figures. 3) With reference to problem 2, determine the controlling section modulus about the z axis. Express your answer in (103) mm3 rounded to three significant figures. 4) With reference to problem 2, determine the bending stress at point H (positive if tensile and negative if compressive). Express your answer in MPa rounded to the nearest hundredths. 5) With reference to problem 2, determine the maximum bending stress…arrow_forwardHi i need to carry out a propagation of Young's modulus to find the overall error for it. I have the readings and I have calculated the overall error for E (for Cantilever beam) but I'm not sure if it is correct. Pls could it be checked or could I have some help with it please. Thanks.arrow_forward
arrow_back_ios
SEE MORE QUESTIONS
arrow_forward_ios
Recommended textbooks for you
- Elements Of ElectromagneticsMechanical EngineeringISBN:9780190698614Author:Sadiku, Matthew N. O.Publisher:Oxford University PressMechanics of Materials (10th Edition)Mechanical EngineeringISBN:9780134319650Author:Russell C. HibbelerPublisher:PEARSONThermodynamics: An Engineering ApproachMechanical EngineeringISBN:9781259822674Author:Yunus A. Cengel Dr., Michael A. BolesPublisher:McGraw-Hill Education
- Control Systems EngineeringMechanical EngineeringISBN:9781118170519Author:Norman S. NisePublisher:WILEYMechanics of Materials (MindTap Course List)Mechanical EngineeringISBN:9781337093347Author:Barry J. Goodno, James M. GerePublisher:Cengage LearningEngineering Mechanics: StaticsMechanical EngineeringISBN:9781118807330Author:James L. Meriam, L. G. Kraige, J. N. BoltonPublisher:WILEY
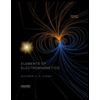
Elements Of Electromagnetics
Mechanical Engineering
ISBN:9780190698614
Author:Sadiku, Matthew N. O.
Publisher:Oxford University Press
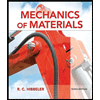
Mechanics of Materials (10th Edition)
Mechanical Engineering
ISBN:9780134319650
Author:Russell C. Hibbeler
Publisher:PEARSON
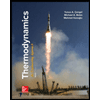
Thermodynamics: An Engineering Approach
Mechanical Engineering
ISBN:9781259822674
Author:Yunus A. Cengel Dr., Michael A. Boles
Publisher:McGraw-Hill Education
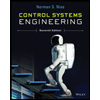
Control Systems Engineering
Mechanical Engineering
ISBN:9781118170519
Author:Norman S. Nise
Publisher:WILEY
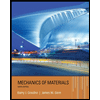
Mechanics of Materials (MindTap Course List)
Mechanical Engineering
ISBN:9781337093347
Author:Barry J. Goodno, James M. Gere
Publisher:Cengage Learning
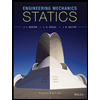
Engineering Mechanics: Statics
Mechanical Engineering
ISBN:9781118807330
Author:James L. Meriam, L. G. Kraige, J. N. Bolton
Publisher:WILEY