CEE 377 HW3 SOLUTION
pdf
keyboard_arrow_up
School
University of Washington *
*We aren’t endorsed by this school
Course
377
Subject
Mechanical Engineering
Date
Dec 6, 2023
Type
Pages
7
Uploaded by Alexkarlbrown
Homework 3 Solution
Problem 1
A new downtown Seattle restaurant is framed as shown
25
ft
8
ft
12
ft
12
ft
12
ft
A
A
B
B
8
×
8 Timber
Support Column (Typ.)
Indoor
Restaurant Area
Outdoor
Patio
Plan View
Elevation View
Simple
Connection (Typ.)
Supporting 2
×
12
Supporting 2
×
12
Full Height
Glass Window
Full Height
Glass Window
2
×
10 Wood Beam
2
×
10 Wood Beam
The beam along line A that supports the second story may be analyzed as pin-supported at the left
end and propped on a roller at the locaton of the 2
×
12 supporting beam. The dead and live loads are
calculated as shown below. Using the LRFD load combinations from ASCE 7, determine the maximum
positive and negative moments for use in design of the beam (assume both loads at in full)
D
= 1
.
5
kip
/
ft
25
ft
8
ft
L
= 0
.
8
kip
/
ft
25
ft
8
ft
Since both beams have the same layout, we’ll start this problem by solving the moment diagram for
an arbitrary uniform distributed load of
w
.
w
25
ft
8
ft
Solving for reactions (and acknowledging that there are no forces in the
x
-direction), we get
X
M
pin
= 0
⟲
+
R
roller
(25
ft)
−
(
w
)(33
ft)(33
ft
/
2) = 0
→
R
roller
= 21
.
78
w
X
F
y
= 0
↑
+ :
R
pin
+
R
roller
−
w
(33
ft) = 0
→
R
pin
= 11
.
22
w
Note that the units above are in feet, but once we add the dimensional load it will convert to a force.
Now we can get the moment diagram. I’m going to work through the shear and moment diagram by
observation from the free body diagram below.
For the shear, we know (1) the reactions represent
a discontinuity in the shear diagram, and (2) the distributed load represents to slope of the shear
diagram. For the moment, we have zero moment at the pin support by definition, then we can use the
magnitudes
from the shear diagram to give us the
slopes
of the moment diagram. To determine the
magnitudes of the moment diagram at a point
x
, we can take the area of the shear diagram from
x
= 0
to
x
=
x
.
FBD
11
.
22
w
21
.
78
w
25
ft
8
ft
w
V
(
x
) (kip)
11
.
22
w
−
13
.
78
w
8
.
0
w
11
.
22
ft
M
(
x
) (k-ft)
62
.
9
w
−
32
w
So we see here that the maximum positive moment occurs 11.22 feet from the pin support and is
going to be equal to 62.9
w
, while the maximum negative moment occurs at the roller support with a
magnitude of
−
32
w
. Specifically, we find that
D
= 1
.
5
kip
/
ft
→
M
+
D,max
= 94
.
4
kip ft
,
M
−
D,max
=
−
48
kip ft
D
= 0
.
8
kip
/
ft
→
M
+
L,max
= 50
.
4
kip ft
,
M
−
L,max
=
−
25
.
6
kip ft
Finally we consider the load combinations. We only have a live and a dead load, so wwe will only need
to consider two load combinations: 1
.
4
D
and 1
.
2
D
+ 1
.
6
L
.
M
+
max
: max [1
.
4
D
= 1
.
4(94
.
4) = 132
.
2
kip ft
,
1
.
2
D
+ 1
.
6
L
= 1
.
2(94
.
4) + 1
.
6(50
.
4) = 193
.
9
kip ft]
M
−
max
: max [1
.
4
D
=
−
67
.
2
kip ft
,
1
.
2
D
+ 1
.
6
L
=
−
98
.
6
kip ft]
Thus, the maximum factored moments are
M
+
max
= 193
.
9
kip ft
M
−
max
=
−
98
.
6
kip ft
If the live load may instead be placed either on the 25 ft or the 8 ft spans (cases 1 and 2 below),
determine the maximum factored positive and negative moments.
L
= 0
.
8
kip
/
ft
25
ft
8
ft
Live Load Case 1
L
= 0
.
8
kip
/
ft
25
ft
8
ft
Live Load Case 2
We are going to approach the problem the same way as we did previously by solving the moment
diagram. The dead load does not change, so we need to consider the modified live load.
–
Live Load Case 1
X
M
pin
= 0
⟲
+
R
roller
(25
ft)
−
(0
.
8
kip
/ft
)(25
ft)(25
ft
/
2) = 0
→
R
roller
= 10
kip
X
F
y
= 0
↑
+ :
R
pin
+
R
roller
−
(0
.
8
kip
/
ft)(25
ft) = 0
→
R
pin
= 10
kip
FBD
10
kip
10
kip
25
ft
8
ft
0
.
8
kip
/
ft
V
(
x
) (kip)
10
−
10
12
.
5
ft
M
(
x
) (k-ft)
62
.
5
kip ft
–
Live Load Case 2
X
M
pin
= 0
⟲
+
R
roller
(25
ft)
−
(0
.
8
kip
/ft
)(8
ft)(29
ft) = 0
→
R
roller
= 7
.
42
kip
X
F
y
= 0
↑
+ :
R
pin
+
R
roller
−
(0
.
8
kip
/
ft)(8
ft) = 0
→
R
pin
=
−
1
.
02
kip
FBD
1
.
02
kip
7
.
42
kip
25
ft
8
ft
0
.
8
kip
/
ft
V
(
x
) (kip)
−
1
.
02
6
.
4
M
(
x
) (k-ft)
−
25
.
6
kip ft
Your preview ends here
Eager to read complete document? Join bartleby learn and gain access to the full version
- Access to all documents
- Unlimited textbook solutions
- 24/7 expert homework help
Now we have the maximum positive and negative live loads from the modified scenarios
–
Live Load Case 1:
M
+
L,max
= 62
.
5
kip ft,
M
−
L,max
= 0
–
Live Load Case 2:
M
+
L,max
= 0,
M
−
L,max
=
−
25
.
6
kip ft
It is obvious that Live Load Case 1 may modify the maximum positive moment while Live Load Case
2 may modify the maximum negative moment.
The maximum negative moment is straightforward
because the maximum negative moment still occurs at the roller support and has the same magntude
as before, so nothing will change and
M
−
max
=
−
98
.
6
kip ft.
The maximum positive moment will certainly change, and the location will change as well since the
two systems no longer provide the same location for the maximum moment. The most accurate way
to do this is to combine the two systems and find the actual maximum moment. Below we see the free
body diagram with the
factored
distributed loads. We can accomplish this by simply factoring the free
body diagrams above with the appropriate load combinations.
R
pin
= 1
.
2(11
.
22(1
.
5)) + 1
.
6(10) = 36
.
2
kip
R
roller
= 1
.
2(21
.
78(1
.
5)) + 1
.
6(10) = 55
.
2
kip
w
D
= 1
.
2(1
.
5) = 1
.
8
kip
/
ft
w
L
= 1
.
6(0
.
8) = 1
.
28
kip
ft
FBD
36
.
2
kip
55
.
2
kip
25
ft
8
ft
3
.
08
kip
/
ft
1
.
8
kip
/
ft
V
(
x
) (kip)
36
.
2
−
40
.
8
14
.
4
11
.
75
ft
M
(
x
) (k-ft)
212
.
7
−
57
.
6
Looking at these results, we see that the maximum factored positive moment is thus
M
+
max
= 212
.
7 kip ft.
If you were designing this wood beam that has the same resistance for positive and negative moment,
what value of moment would you design it for?
Clearly here we would be looking for the maximum magnitude of the moment if the beam provides equal
tensile and compressive resistance. In this case, we would choose
M
max
= 212
.
7
kip ft.
It is interesting to point out that, as engineers, we often simplify our problem in ways that ensure a
conservative solution (one that will make our design more safe).
The answer above is th exact solution,
but a more conservative approach would be to simply take the two maximum values and use them as they
are while acknowledging that (1) you the engineer are aware that these values do not occur at the same
location on the beam, and (2) given the distribution of the moment, the maximum values occur within a
reasonable proximity to one another. In this case, we would have estimated that the maximum moment is
simply 1
.
2(94
.
4)+1
.
6(62
.
5) = 213
.
3 kip ft. Given the exact solution, this results in an error of 0.28%. From
an engineering perspective, these are the same.
Problem 2
The lateral force resisting system for the restaurant in Problem 1 is located along line B-B in the plan view
shown above. An elevation view for that lateral force resisting system, which consists of tension-only steel
strap bracing, is shown below. The beams at each story in this end-wall frame are assumed to be subject to
the same dead and live load as the beam in Problem 1a. Wind loading is calculated and found to be 20 kips
at the top story and 10 kips at the bottom story, and is distributed as shown. Assume that these are the
only loads acting on this end-wall frame (you do not need to consider the load from the 2
×
12 supporting
beam that runs perpendicular to the end-wall frame). This structure is statically determinate and can be
solved by hand. Remember a couple of things. First, the tension-only straps do not resist compression, so
only one strap will be loaded per floor at a time.
Second, because the beams are simply supported and
braces are treated like truss elements, the entire frame can be analyzed in a manner similar to a truss.
25
ft
12
ft
12
ft
B
B
Simple
Connection (Typ.)
Simple Column
Support (Typ.)
Tension-Only Steel
Strap Bracing (Typ.)
10
kip
5
kip
10
kip
5
kip
Use the LRFD load combinations from ASCE 7-16 to determine:
a. The maximum factored compression in the first and second story columns.
b. The maximum factored uplift that the connection of frame to foundation must be designed to resist.
c. The maximum factored tension in the steel strap bracing. Assume that the steel strap bracing does
not carry any gravity loads.
The combination of steel strap bracing, which behaves like a truss member, and the simple connections
for the beams means that this frame will behave very much like a truss in that it will not transfer moment
from the beams/braces to the columns. In fact, because we assume that all of the lateral load moves into
the braces, no members are subject to any transverse loading, so we can model this as a truss. For a truss
problem, it is often easier to solve the entire truss for each loading type and factor any required values at the
end, so that’s what we will do here.
Note: because the strap braces are tension only, we remove
the braces in compression, as shown below in the dashed lines
.
Dead Load
1
.
5
kip
/
ft (typ.)
Live Load
0
.
8
kip
/
ft (typ.)
Wind Load
5
kip
10
kip
5
kip
10
kip
We can solve each of these systems in a rather straightforward manner.
For the dead and live loads,
because they are gravity loads, they do not move into the braces and only travel through the beams and
into the columns. As a result, the column compressive forces are equal to the reactions from the beams, and
because of symmetry, each of the pin reactions resists half of the total force.
37
.
5
kip
37
.
5
kip
37.5 (C) 18.8 (C)
37.5 (C)
18.8 (C)
0
0
0
0
Dead Load
20
kip
20
kip
20 (C)
10 (C)
20 (C)
10 (C)
0
0
0
0
Live Load
24
kip
24
kip
9.6 (T)
0
24 (C)
9.6 (C)
25 (C)
10 (C)
33.3 (T)
22.2 (T)
Wind Load
Now we can answer our questions directly. We have three load types, so we will need load combinations
for live, dead, and wind loads. The table below shows the factored load in the individual members, in kips.
The controlling values are shown in bold.
LC 1
LC 2
LC 3
LC 4
LC 5
1.4D
1.2D+1.6L
1.2D+(L or 0.5W)
1.2D+1.0W+L
0.9D+1.0W
Column AC
52.5
77
65
55.4
24.2
Column BD
52.5
77
65
89
57.8
Column CE
26.3
38.5
32.5
32.5
16.9
Column DF
26.3
38.5
32.5
42.2
26.5
Uplift Force
No Uplift
No Upllift
No Uplift
No Uplift
No Uplift
(
R
y,left
)
(
R
y
>
0)
(
R
y
>
0)
(
R
y
>
0)
(
R
y
>
0)
(
R
y
>
0)
1st Story Brace
0
0
33.3
33.3
33.3
2nd Story Brace
0
0
22.2
22.2
22.2
Your preview ends here
Eager to read complete document? Join bartleby learn and gain access to the full version
- Access to all documents
- Unlimited textbook solutions
- 24/7 expert homework help
Problem 3
The beam below is the same beam that is statically indeterminate with a roller support at midspan. If the
beam is a 40 foot W18x50 steel wide flange beam, determine the maximum compressive stress you would
have to design for in the cross section. Assume that the roller support and the point load are both located
at the center of the span.
D
= 1
.
15
kip
/
ft
L
= 1
.
85
kip
/
ft
D
= 8
.
0
kip
L
r
= 4
.
8
kip
S
= 10
.
0
kip
W
= 15
.
0
kip
E
= 25
.
0
kip
20
ft
20
ft
First, let’s consider what we are looking for. This problem asks us for the maximum compressive stress.
The equation for the compressive stress for a beam under both transverse and axial loads is
σ
=
My
I
+
P
A
We can look up the geometric values that we need for a W18
×
50.
Specifically, we have
A
= 14
.
7
in
2
,
I
= 800
in
4
and
y
= 9
.
0
in. In the case of a steel W section,
y
top
=
y
bottom
=
y
. We only need to use
the loads and load combinations to find the maximum moment and axial force. Note that the point loads
at midspan do not contribute at all to either value, since a point load directly above a support will move
directly into the support reaction but does not cause any deformation in the beam.
We can rigorously solve this problem with a lot of math, but there are simpler ways to do this.
The
axial force is constant through the entire structure. Beam tables tell us that a two span beam with span
length
L
, subjected to a uniformly distributed load,
w
, has a maximum positive moment of 9
wL
2
/
128 and
a maximum negative moment
−
wL
2
/
8. Because we have a symmetric section, the tensile and compressive
stresses are equal within the section, thus we only neeed the higher magnitude of
M
max
=
wL
2
/
8.
We can also consider load combinations
1
.
4
D
1
.
2
D
+ 1
.
6
L
+ 0
.
5(
L
r
or
S
or
R
)
1
.
2
D
+ 1
.
6(
L
r
or
S
or
R
) + (
L
or 0
.
5
W
)
1
.
2
D
+ 1
.
0
W
+
L
+ 0
.
5(
L
r
or
S
or
R
)
0
.
9
D
+ 1
.
0
W
1
.
2
D
+
E
v
+
E
h
+
L
+ 0
.
2
S
0
.
9
D
−
E
v
+
E
h
Combination
w
( kip
/
ft)
P
( kip)
M
( kip ft)
My/I
( ksi)
P/A
( ksi)
σ
comp
( ksi)
LC 1: 1.4D
1.61
0
80.5
10.9
0
10.9
LC 2: 1.2D + 1.6L
4.34
0
217
29.3
0
29.3
LC 3a: 1.2D + L
3.23
0
161.5
21.8
0
21.8
LC 3b: 1.2D + 0.5W
1.38
7.5
69
9.32
0.51
9.83
LC 4: 1.2D + 1.0W + L
3.23
7.5
161.5
21.8
0.51
22.3
LC 5: 0.9D + 1.0W
1.04
7.5
51.8
6.99
0.51
7.50
LC 6: 1.2D + E + L
3.23
12.5
161.5
21.8
0.85
22.7
LC 7: 0.9 + E
1.04
12.5
51.8
6.99
0.85
7.84
As we see, load combination 2 provides the maximum compressive stress of 29.3 ksi.
Related Questions
Please include a free body diagram in your handwritten solution.
No Chatgpt.
Mechanical engineering
arrow_forward
Pls.help with 24.
arrow_forward
6 please answer the problems, the answer is already given i just need the solution
please type your answer if you can because i can't view written answers
arrow_forward
Z3
arrow_forward
Live load on the deck = 70 psf
Deck weight = 6 psf
Beam weight = 8 lb/ft
Column weight = 80 lb
Please round to the nearest one.
Foundation reaction at 2-A column=
lb
16'
2
12'
Time left 0:33:26
3
arrow_forward
Fig. 1 shows a simply supported beam structure. It exhibits a cross-section as per Fig. 2.
20 kN
A
- 5 m
C
Fig. 1
150 mm
4 kN/m
B
5 m
30 mm
60 mm
60 mm
100 mm
30 mm
Fig. 2
2
arrow_forward
pleace, I want FULL answer for this question with ALL ateps. in addition to neat handwriting or electronic writing.
arrow_forward
Part B
Draw the moment diagram for the beam.
Click on "add vertical line off" to add discontinuity lines. Then click on "add segment" button to add functions between the lines.
Note - Make sure you place only one vertical line at places that require a vertical line. If you inadvertently place two vertical lines at the same place, it will appear visually correct because the
lines overlap, but the system will mark it wrong.
No elements selected
M (kip.ft)
80
70
60
50
40
30
20
10-
00
-10
-20-
-30-
-40-
-50
-60
-70-
-80
-12 ft-
3 kip/ft
14
6 ft
z (ft)
Press TAB to navigate between elements on the canvas. Press (ALT+M) to get to the main menu. Press [ALT+A to
modify the attributes. Press (ALT+Q) to quit the application.
Revic
Wrang
arrow_forward
18
please answer the problems, the answer is already given i just need the solution
please type your answer if you can because i can't view written answers
arrow_forward
Required information
NOTE: This is a multi-part question. Once an answer is submitted, you will be unable to return to this part.
A power line pole is subjected to two cable forces of 250 N and 218 N as shown, with each force lying completely in the x-
z plane. There is also a supporting guy wire that runs from the ground to the top of the pole and is connected to a small
horizontal extension arm at A that extends from the pole. The diameter of the pole is 0.3 m, and the y-axis runs directly
along the centerline of the pole. The point where the two cables are attached, point C, is located on the outer perimeter of
the pole (i.e., the x-coordinate of point C is 0.15 m) and is in the x-y plane. You want to determine the components of the
reactions at the fixed base of the pole, O. The tension in the guy wire that supports the pole is 344 N.
Given X1= 250 N
X2 = 218 N
X1 N
40°
X2 N 1
12 m
3 m
0.9 m
The reaction couple at O, expressed in vector component form, is as follows:
Mo = (-26.47…
arrow_forward
Question 6- SFD & BMD- Simply Beam (Point)
From the beam shown below,
i) Draw the Free Body Diagram (FBD) & Find R1 & R2
ii) Draw Shear Force Diagram (SFD), clearly show all the shear force the beam is
experiencing at each point.
iii) Draw the Bending Moment Diagram (BMD), clearly show all the bending moment the
beam is experiencing at each point.
800 N
400 N 600 N
200 N
0.4 m-
0.8 m
t0.3 m--0.3 m-0.4 m-
he
C
A.
0.9 m
0.5 m-.2 m-
R2
R1
arrow_forward
Question 6 - SFD & BMD-Simply Beam (Point)
From the beam shown below,
i) Draw the Free Body Diagram (FBD) & Find R1 & R2
ii) Draw Shear Force Diagram (SFD), clearly show all the shear force the beam is
experiencing at each point.
iii) Draw the Bending Moment Diagram (BMD), clearly show all the bending moment the
beam is experiencing at each point.
400 N 600 N
200 N
800 N
0.8 m
0.3 m--0.3 m-
0.4 m
0.4 m
C
0.9 m
0.5 mo.2 m-
arrow_forward
force, the sign convention is same as that used in lectures and seminars).
A simply supported beam is loaded as shown in the Figure. The corresponding SFD and BMD would be:
20 kN
10 kN/m
2 m
2 m
30 kN
(a)
40 kN m
30 kN
30 kN
10 kN
(b)
40 kN.m
10 kN
30 kN
30 kN
Click Save and Submit to save and submit. Click Save All Answers to save all answvers.
arrow_forward
QUESTION #1
A beam AB is simply supported at the ends and carries two points having a magnitude of 5 kN
each. The beam length is 10 m, the point loads are 3 m and 7 m from end A support. In addition.
the beam carries a UDL of 1.000 N/m between the two point loads. Draw the SF and BM diagrams.
(Show each section of the beam and each section equation for each diagram).
UDL
w 1000 N/m
5 kN
A
5 kN
B
arrow_forward
Part A
Draw the shear diagram for the beam. Follow the sign convention. (Figure 1)
Click on "add vertical line off" to add discontinuity lines. Then click on "add segment" button to add functions between the lines.
Note - Make sure you place only one vertical line at places that require a vertical line. If you inadvertently place 2 vertical lines at the same place, it will
appear correct visually because the lines overlap, but the system will mark it wrong.
4 + D
800 N
600 N
1200 N- m
B
-1m.
1m
1 m
1 m
No elements selected
V (N)
1000
500
I (m)
3
-500
-1000
Add discontinuity lines and select segments to add to the canvas.
arrow_forward
SEE MORE QUESTIONS
Recommended textbooks for you
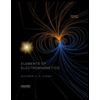
Elements Of Electromagnetics
Mechanical Engineering
ISBN:9780190698614
Author:Sadiku, Matthew N. O.
Publisher:Oxford University Press
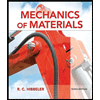
Mechanics of Materials (10th Edition)
Mechanical Engineering
ISBN:9780134319650
Author:Russell C. Hibbeler
Publisher:PEARSON
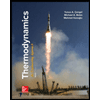
Thermodynamics: An Engineering Approach
Mechanical Engineering
ISBN:9781259822674
Author:Yunus A. Cengel Dr., Michael A. Boles
Publisher:McGraw-Hill Education
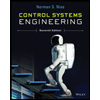
Control Systems Engineering
Mechanical Engineering
ISBN:9781118170519
Author:Norman S. Nise
Publisher:WILEY
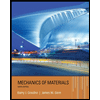
Mechanics of Materials (MindTap Course List)
Mechanical Engineering
ISBN:9781337093347
Author:Barry J. Goodno, James M. Gere
Publisher:Cengage Learning
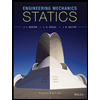
Engineering Mechanics: Statics
Mechanical Engineering
ISBN:9781118807330
Author:James L. Meriam, L. G. Kraige, J. N. Bolton
Publisher:WILEY
Related Questions
- Please include a free body diagram in your handwritten solution. No Chatgpt. Mechanical engineeringarrow_forwardPls.help with 24.arrow_forward6 please answer the problems, the answer is already given i just need the solution please type your answer if you can because i can't view written answersarrow_forward
- Z3arrow_forwardLive load on the deck = 70 psf Deck weight = 6 psf Beam weight = 8 lb/ft Column weight = 80 lb Please round to the nearest one. Foundation reaction at 2-A column= lb 16' 2 12' Time left 0:33:26 3arrow_forwardFig. 1 shows a simply supported beam structure. It exhibits a cross-section as per Fig. 2. 20 kN A - 5 m C Fig. 1 150 mm 4 kN/m B 5 m 30 mm 60 mm 60 mm 100 mm 30 mm Fig. 2 2arrow_forward
- pleace, I want FULL answer for this question with ALL ateps. in addition to neat handwriting or electronic writing.arrow_forwardPart B Draw the moment diagram for the beam. Click on "add vertical line off" to add discontinuity lines. Then click on "add segment" button to add functions between the lines. Note - Make sure you place only one vertical line at places that require a vertical line. If you inadvertently place two vertical lines at the same place, it will appear visually correct because the lines overlap, but the system will mark it wrong. No elements selected M (kip.ft) 80 70 60 50 40 30 20 10- 00 -10 -20- -30- -40- -50 -60 -70- -80 -12 ft- 3 kip/ft 14 6 ft z (ft) Press TAB to navigate between elements on the canvas. Press (ALT+M) to get to the main menu. Press [ALT+A to modify the attributes. Press (ALT+Q) to quit the application. Revic Wrangarrow_forward18 please answer the problems, the answer is already given i just need the solution please type your answer if you can because i can't view written answersarrow_forward
- Required information NOTE: This is a multi-part question. Once an answer is submitted, you will be unable to return to this part. A power line pole is subjected to two cable forces of 250 N and 218 N as shown, with each force lying completely in the x- z plane. There is also a supporting guy wire that runs from the ground to the top of the pole and is connected to a small horizontal extension arm at A that extends from the pole. The diameter of the pole is 0.3 m, and the y-axis runs directly along the centerline of the pole. The point where the two cables are attached, point C, is located on the outer perimeter of the pole (i.e., the x-coordinate of point C is 0.15 m) and is in the x-y plane. You want to determine the components of the reactions at the fixed base of the pole, O. The tension in the guy wire that supports the pole is 344 N. Given X1= 250 N X2 = 218 N X1 N 40° X2 N 1 12 m 3 m 0.9 m The reaction couple at O, expressed in vector component form, is as follows: Mo = (-26.47…arrow_forwardQuestion 6- SFD & BMD- Simply Beam (Point) From the beam shown below, i) Draw the Free Body Diagram (FBD) & Find R1 & R2 ii) Draw Shear Force Diagram (SFD), clearly show all the shear force the beam is experiencing at each point. iii) Draw the Bending Moment Diagram (BMD), clearly show all the bending moment the beam is experiencing at each point. 800 N 400 N 600 N 200 N 0.4 m- 0.8 m t0.3 m--0.3 m-0.4 m- he C A. 0.9 m 0.5 m-.2 m- R2 R1arrow_forwardQuestion 6 - SFD & BMD-Simply Beam (Point) From the beam shown below, i) Draw the Free Body Diagram (FBD) & Find R1 & R2 ii) Draw Shear Force Diagram (SFD), clearly show all the shear force the beam is experiencing at each point. iii) Draw the Bending Moment Diagram (BMD), clearly show all the bending moment the beam is experiencing at each point. 400 N 600 N 200 N 800 N 0.8 m 0.3 m--0.3 m- 0.4 m 0.4 m C 0.9 m 0.5 mo.2 m-arrow_forward
arrow_back_ios
SEE MORE QUESTIONS
arrow_forward_ios
Recommended textbooks for you
- Elements Of ElectromagneticsMechanical EngineeringISBN:9780190698614Author:Sadiku, Matthew N. O.Publisher:Oxford University PressMechanics of Materials (10th Edition)Mechanical EngineeringISBN:9780134319650Author:Russell C. HibbelerPublisher:PEARSONThermodynamics: An Engineering ApproachMechanical EngineeringISBN:9781259822674Author:Yunus A. Cengel Dr., Michael A. BolesPublisher:McGraw-Hill Education
- Control Systems EngineeringMechanical EngineeringISBN:9781118170519Author:Norman S. NisePublisher:WILEYMechanics of Materials (MindTap Course List)Mechanical EngineeringISBN:9781337093347Author:Barry J. Goodno, James M. GerePublisher:Cengage LearningEngineering Mechanics: StaticsMechanical EngineeringISBN:9781118807330Author:James L. Meriam, L. G. Kraige, J. N. BoltonPublisher:WILEY
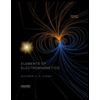
Elements Of Electromagnetics
Mechanical Engineering
ISBN:9780190698614
Author:Sadiku, Matthew N. O.
Publisher:Oxford University Press
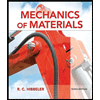
Mechanics of Materials (10th Edition)
Mechanical Engineering
ISBN:9780134319650
Author:Russell C. Hibbeler
Publisher:PEARSON
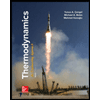
Thermodynamics: An Engineering Approach
Mechanical Engineering
ISBN:9781259822674
Author:Yunus A. Cengel Dr., Michael A. Boles
Publisher:McGraw-Hill Education
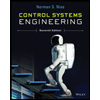
Control Systems Engineering
Mechanical Engineering
ISBN:9781118170519
Author:Norman S. Nise
Publisher:WILEY
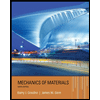
Mechanics of Materials (MindTap Course List)
Mechanical Engineering
ISBN:9781337093347
Author:Barry J. Goodno, James M. Gere
Publisher:Cengage Learning
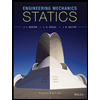
Engineering Mechanics: Statics
Mechanical Engineering
ISBN:9781118807330
Author:James L. Meriam, L. G. Kraige, J. N. Bolton
Publisher:WILEY