Olsowski_Scott_Lab2_10052023 (1)
docx
keyboard_arrow_up
School
Florida Atlantic University *
*We aren’t endorsed by this school
Course
4730L
Subject
Mechanical Engineering
Date
Dec 6, 2023
Type
docx
Pages
11
Uploaded by ChancellorHummingbirdMaster103
Department of Ocean and Mechanical Engineering
Lab subject: Pressure Drop in Pipes and Fittings
Submission Date: October 5th, 2023
Submitted to: Dr. Oren Masory
Team # R7
Team members:
1. Scott Olsowski
2. Michael Micele
Abstract: In Lab #2 of the Mechanical Systems course, we sought to understand the relationship between the friction coefficient and Reynolds number in rough and smooth pipes while also analyzing the pressure drop across various elbow fittings. Employing a hydraulic bench with labeled components, we meticulously measured the pressure drop for distinct flow rates on specified components: 17mm & 23mm diameter rough pipes and three types of elbows (90°, double 90°, and 45°). In addition, the Venturi tube was employed, with an input nozzle diameter of
(
D
1
=
1
”
)
and an exit diameter (
D
2
=
0.5
”
)
.
The Moody chart was utilized to verify theoretical concepts to determine the friction coefficient in pipes. As for the loss coefficient, (
K
)
, for the elbow fittings, it was derived using the relation (
K
=
{
2
ΔP
}
{
ρv
2
}
)
, wherein (
ΔP
)
is the pressure drop, (
ρ
)
is the fluid density, and
(
v
)
is the fluid velocity. Different fittings, like 90° versus 45° elbows, inherently have additional resistance to flow and, thus, different (
K
)
values.
Furthermore, we compared results from individual components to combined pipes, dissecting any deviations observed. As a comprehensive approach, error analysis was executed for the coefficient of friction and the output velocity from the nozzle using the given formula. The insights from this experiment provide a practical perspective on fluid mechanics concepts, aiding
in real-world applications where precise control and understanding of fluid flow are pivotal.
Introduction:
Fluids, when in motion, generate losses due to their inherent viscous nature, and this phenomenon is amplified when they flow through complex networks like pipes and fittings. Studying these losses is pivotal in hydraulic engineering, HVAC design, and many other industries where fluid flow is critical. Lab #2 aims to delve deep into this phenomenon by focusing on the relationship between the friction coefficient and the Reynolds number in rough and smooth pipes and evaluating the pressure drop in various elbow fittings.
Theoretical Background: 1. Reynolds Number (Re):
The Reynolds number is a dimensionless quantity given by (
ℜ=
{
ρvD
}
{
μ
}
)
, where (
ρ
)
is the fluid density, (
v
)
is the average fluid velocity,
(
D
)
is the characteristic length (usually the diameter of the pipe), and (
μ
)
is the fluid's dynamic viscosity. It represents the ratio of inertial forces to viscous forces. A higher Reynolds number indicates a turbulent flow, while a lower one suggests a laminar flow. The transition between laminar and turbulent flow typically occurs around (
ℜ=
2300)
.
2. Friction Factor and the Moody Chart:
The friction factor measures the resistance caused by fluid viscosity during flow. In pipes, it's often determined using the Moody chart, a graphical representation correlating the friction factor,
Reynolds number, and the relative roughness of the pipe. The Moody chart simplifies finding the
friction factor, which can then be used to determine the pressure drop due to friction in pipes using Darcy's equation.
3. Pressure Drop in Fittings (K - Loss Coefficient):
As fluids move through pipe fittings like elbows, bends, or tees, they face changes in direction and velocity, leading to energy losses. These losses are often quantified using a loss coefficient,
(
K
)
,
which is then used to calculate the pressure drop as (
ΔP
=
{
1
}
{
2
}
Kρ v
2
)
.
Different fittings have different (
K
)
values due to their distinct geometries and effects on flow patterns. The higher the (
K
)
value, the higher the energy loss in that fitting.
4. Venturi Effect and Velocity Calculation:
The Venturi effect is a phenomenon in fluid dynamics where a fluid's velocity increases as it passes through a constricted section, decreasing static pressure. This behavior is captured by the energy conservation principle, as articulated in Bernoulli's equation.
For the specific context of this lab, the Venturi tube, a device with varying cross-sectional areas, is utilized to measure flow rates based on pressure changes. As fluid moves from a more comprehensive section (with diameter (
D
1
)
) to a narrower section (with diameter (
D
2
)
), its velocity increases, leading to a reduction in pressure. To determine the fluid's velocity at the exit of the nozzle (or the narrower section), the equation provided in the lab is employed:
[
v
2
=
C
√
{
{
2
g
(
h
2
−
h
1
)
}
{
1
−
(
{
D
2
}
{
D
1
}
)
2
}
}
]
Here, - (
v
2
)
is the exit velocity.
- (
C
)
is the discharge constant, accounting for real-world deviations from the ideal behavior. This can be determined empirically by plotting (
v
2
)
as a function of the square root term in the equation.
- (
g
)
is the acceleration due to gravity.
- (
h
1
)
and (
h
2
)
represent fluid heights, or equivalently, pressure heads in the broader and narrower sections, respectively.
Using this equation, one can derive valuable insights into the fluid's velocity characteristics as it moves through different sections of the Venturi tube.
Apparatus: The primary tool for Lab #2 is a hydraulic bench, used to study fluid flow through different pipes
and fittings:
1.
Hydraulic Bench: Central platform that controls fluid flow, with adjustable flow rate options.
2.
Pipes: - 17mm and 23mm diameter rough pipes (components 2 & 3): Used to study the effects of surface roughness and diameter on frictional losses.
3.
Elbow Fittings: - 90° and Double 90° elbows (component 22 & 17): Assess flow losses during abrupt direction changes.
- 45° elbow (component 20): Analyze flow losses during gentler direction shifts.
4.
Venturi Tube (component 13): With input diameter (
D
1
)
of 1 inch and exit diameter
(
D
2
)
of 0.5 inches, it's critical for studying the Venturi effect and velocity measurements based on pressure differentials.
5.
Pressure Instruments: Devices attached at strategic points to measure pressure drops crucial for calculating friction and loss coefficients.
6.
Flow Rate Measurement: Ensures desired flow conditions and aids in computing Reynolds numbers.
Your preview ends here
Eager to read complete document? Join bartleby learn and gain access to the full version
- Access to all documents
- Unlimited textbook solutions
- 24/7 expert homework help
7.
Valves: Control fluid flow through the two pipes, allowing variation in flow rates.
The hydraulic bench and its components provide a comprehensive setup for analyzing fluid flow characteristics in pipes and fittings.
Procedure:
1.
Setup:
- Position the hydraulic bench on a level surface.
- Attach the venturi tube, pipes, and elbow fittings securely.
2.
Flow Rate Measurements:
- Turn on the bench, set the first flow rate, and close all valves.
3.
Pipe Measurements:
- For the 17mm and 23mm rough pipes, open their respective valves, measure, and record the pressure drop at five different flow rates.
4.
Elbow Measurements:
- Record the pressure drop for the 90°, double 90°, and 45° elbows at five flow rates.
5.
Venturi Tube:
- Measure the pressure drop across the tube at five flow rates, noting input and exit pressures.
6.
Combined Pipe Analysis:
- Open valves for both rough pipes, recording the combined pressure drop at five flow rates.
Results: 0.000E+00
5.000E-04
1.000E-03
1.500E-03
2.000E-03
2.500E-03
0
0.1
0.2
0.3
0.4
0.5
0.6
0.7
0.8
0.9
1
f(x) = 277.84 x + 0.35
Value of C
v2
Square root term
Figure 1: Graph showing the function of exit velocity vs the square root term in the Venturi equation to obtain C.
Venturi Tube
Venturi Tube Ext.
v2
h2-h1
Square root
term
Pipe Diameter
(in)
A
4.244E-04
1.500E-
02
0.469813793
D1
1
0.785398163
8.488E-04
2.100E-
02
0.555891176
D2
0.5
0.196349541
1.273E-03
3.800E-
02
0.747776705
1.698E-03
4.300E-
02
0.795452701
2.122E-03
6.000E-
02
0.939627586
Table 1: Results of the analysis for the Venturi Tube
Error Analysis Discussion: (
Error Analysis of Fluid Flow Through Pipe Setups and Fittings)
Our experiments examining fluid flow through diverse pipe configurations and fittings noted specific errors. This section briefs these sources of error, their potential impacts, and measures to mitigate them.
1. Measurement Uncertainties:
- Pressure Drop: Uncertainties arise from the manometer's least count and human reading errors.
- Flow Rate: Calibration and response time of flow meters can vary results.
- Velocity: Derived from flow rate and pipe area, errors in either propagate here.
2. Physical Factors:
- Pipe Roughness: Over time, scaling or wear can alter pipe roughness.
- Pipe Diameter: A minor inconsistency in diameter significantly affects outcomes.
3. Reynolds Number (Re):
- Being derived, it's sensitive to velocity, viscosity, and diameter errors.
4. Coefficients (K and f):
- Determined experimentally, they're influenced by flow disturbances, temperature, and pipe geometry changes.
5. Fittings and Instruments:
- Precise dimensions of fittings like elbows are vital. Instruments like manometers must be calibrated.
6. Assumptions:
- The flow is considered steady, fully developed, and either laminar or turbulent. Deviations affect results.
- Fluid properties, like density and viscosity, were assumed constant.
Minimizing Errors:
1. Calibration: Instruments' frequent calibration ensures accuracy.
2. Multiple Readings: Averaging multiple readings reduces random errors.
3. Setup & Environment: Ensure a consistent, leak-free setup and, if possible, a controlled environment.
Conclusions:
The experiments provided informative results on fluid dynamics. However, understanding potential errors is crucial. Results should be cross-checked with theoretical models
and further research. Our experiment compared the fluid flow dynamics in rough pipes with diameters of 17mm and 23mm and their combined configuration. Here are the summarized observations from the results:
1. Flow Rate at 25 l/min:
- Combined rough pipes: 4.167E-04 m^3/s with a pressure drop of 5.682E+03 Pa.
- 17mm rough pipe: 4.167E-04 m^3/s with a pressure drop of 4.415E+03 Pa.
- 23mm rough pipe*: 4.167E-04 m^3/s with a pressure drop of 1.275E+03 Pa.
2. Friction Coefficient at 25 l/min:
- Combined rough pipes: 2.400E-02.
- 17mm rough pipe: 2.800E-02.
- 23mm rough pipe: 2.750E-02.
From the observations:
- Flow Rate Comparisons: At the same flow rate, the pressure drop for the combined rough pipes was higher than that of the individual 17mm and 23mm pipes. This implies that when pipes of two different diameters are combined, they produce a more significant resistance to flow than when operating individually.
- Friction Coefficient: The friction coefficient for the combined pipes was slightly lower than the individual 17mm and 23mm pipes. This suggests that while the combined configuration may
Your preview ends here
Eager to read complete document? Join bartleby learn and gain access to the full version
- Access to all documents
- Unlimited textbook solutions
- 24/7 expert homework help
lead to more significant pressure drops, the extent of frictional resistance per unit length, characterized by the friction coefficient, is somewhat reduced.
The apparent discrepancies in pressure drops and friction coefficients between the combined and individual configurations underscore the complex nature of fluid dynamics in different pipe geometries. The combined layout, intriguingly, doesn't mirror the behavior of its constituent pipes, indicating that pipe combinations can lead to unique fluid flow profiles.
References: [1] White, F. M. Fluid Mechanics. 8th ed., McGraw-Hill Education, 2016.
Appendix:
1. Flow rate conversion:
[
Q
(
m
3
s
)
=
Q
(
l
min
)
×
{
1
m
3
}
{
1000
l
}
×
{
1
}
{
60
s
}
]
ere: −
(
Q
(
m
3
s
)
)
is the flow rate in cubic meters per second.
- (
Q
(
l
min
)
)
the flow rate in liters per minute.
2. Flow Velocity:
[
V
=
{
Q
(
m
3
s
)
}
{
A
(
m
2
)
}
]
Where:
- (
V
)
is the flow velocity.
- (
Q
(
m
3
s
)
)
is the flow rate in cubic meters per second.
- (
A
(
m
2
)
)
is the cross-sectional area of the pipe.
3. Reynolds Number:
[
ℜ=
{
ρ×V ×d
}
{
μ
}
]
Where:
- (
ℜ
)
is the Reynolds Number.
- (
ρ
)
is the fluid density.
- (
V
)
is the flow velocity.
- (
d
)
is the diameter of the pipe.
- (
μ
)
is the dynamic viscosity of the fluid.
4. Loss Coefficient:
[
K
=
{
2
×Δ P
}
{
ρ×V
2
}
]
Where:
- (
K
)
is the loss coefficient.
- (
ΔP
)
is the pressure drop across the pipe section.
5. Friction Coefficient:
Was found using Moody chart in reference [1]
6. List of Symbols: - (
ℜ
)
: Reynolds number, a dimensionless quantity representing the ratio of inertial forces to viscous forces in fluid flow.
- (
ΔP
)
: Pressure drop across a component or section of pipe.
- (
K
)
: Loss coefficient, used to quantify losses in various pipe fittings.
- (
D
1)
: Input diameter of the nozzle in the Venturi tube.
-
(
D
2)
: Exit diameter of the nozzle in the Venturi tube.
- (
ρ
)
: Fluid density, mass per unit volume.
- (
v
)
: Fluid velocity, representing the rate of fluid flow.
- (
g
)
: Acceleration due to gravity.
- (
C
)
: Discharge constant, utilized in the context of the Venturi effect for the determination of fluid exit velocity.
7. List of Tables and Figures
:
Figure 1: Graph showing the function of exit velocity vs. the square root term in the Venturi equation to obtain C.
Table 1: Results of the analysis for the Venturi Tube.
Table 2: Results of all configurations
8. Measurements & Calculations
17mm diameter rough pipe
Q (l/min)
Q (m^3
/s)
DP (mmH2
O)
DP (Pa)
V (flow velocity)
Re (Reynol
ds)
K (loss coefficient)
f (friction coefficient)
5.000E
+00
8.333
E-05
2.000E
+01
1.962E
+02
3.673E-01
6.232E+
03
2.908E+00
3.800E-02
1.000E
+01
1.667
E-04
5.000E
+01
4.905E
+02
7.347E-01
1.246E+
04
1.818E+00
3.500E-02
1.500E
+01
2.500
E-04
1.450E
+02
1.422E
+03
1.102E+0
0
1.870E+
04
2.343E+00
3.200E-02
2.000E
+01
3.333
E-04
2.900E
+02
2.845E
+03
1.469E+0
0
2.493E+
04
2.636E+00
3.000E-02
2.500E
+01
4.167
E-04
4.500E
+02
4.415E
+03
1.837E+0
0
3.116E+
04
2.617E+00
2.800E-02
23mm diameter rough pipe
Q (l/min)
Q (m^3
/s)
DP (mmH2
O)
DP (Pa)
V (flow velocity)
Re (Reynol
ds)
K (loss coefficient)
f (friction coefficient)
5.000E
+00
8.333
E-05
7.000E
+00
6.867E
+01
2.007E-01
4.606E+
03
3.410E+00
4.000E-02
1.000E
+01
1.667
E-04
1.900E
+01
1.864E
+02
4.014E-01
9.213E+
03
2.314E+00
3.400E-02
1.500E
+01
2.500
E-04
4.000E
+01
3.924E
+02
6.020E-01
1.382E+
04
2.165E+00
3.100E-02
2.000E
+01
3.333
E-04
8.000E
+01
7.848E
+02
8.027E-01
1.843E+
04
2.436E+00
2.900E-02
2.500E
+01
4.167
E-04
1.300E
+02
1.275E
+03
1.003E+0
0
2.303E+
04
2.533E+00
2.750E-02
90° Elbow
Q (l/min)
Q (m^3
DP (mmH2
DP (Pa)
V (flow velocity)
Re (Reynol
K (loss coefficient)
f (friction coefficient)
Your preview ends here
Eager to read complete document? Join bartleby learn and gain access to the full version
- Access to all documents
- Unlimited textbook solutions
- 24/7 expert homework help
/s)
O)
ds)
5.000E
+00
8.333
E-05
3.000E
+00
2.943E
+01
3.673E-01
6.232E+
03
4.362E-01
3.600E-02
1.000E
+01
1.667
E-04
4.000E
+00
3.924E
+01
7.347E-01
1.246E+
04
1.454E-01
3.000E-02
1.500E
+01
2.500
E-04
7.000E
+00
6.867E
+01
1.102E+0
0
1.870E+
04
1.131E-01
2.700E-02
2.000E
+01
3.333
E-04
3.000E
+01
2.943E
+02
1.469E+0
0
2.493E+
04
2.726E-01
2.550E-02
2.500E
+01
4.167
E-04
4.400E
+01
4.316E
+02
1.837E+0
0
3.116E+
04
2.559E-01
2.400E-02
Double 90° Elbow
Q (l/min)
Q (m^3
/s)
DP (mmH2
O)
DP (Pa)
V (flow velocity)
Re (Reynol
ds)
K (loss coefficient)
f (friction coefficient)
5.000E
+00
8.333
E-05
8.000E
+00
7.848E
+01
3.673E-01
6.232E+
03
1.163E+00
3.600E-02
1.000E
+01
1.667
E-04
2.000E
+01
1.962E
+02
7.347E-01
1.246E+
04
7.271E-01
3.000E-02
1.500E
+01
2.500
E-04
3.200E
+01
3.139E
+02
1.102E+0
0
1.870E+
04
5.170E-01
2.700E-02
2.000E
+01
3.333
E-04
5.600E
+01
5.494E
+02
1.469E+0
0
2.493E+
04
5.089E-01
2.550E-02
2.500E
+01
4.167
E-04
7.700E
+01
7.554E
+02
1.837E+0
0
3.116E+
04
4.479E-01
2.400E-02
45° Elbow
Q (l/min)
Q (m^3
/s)
DP (mmH2
O)
DP (Pa)
V (flow velocity)
Re (Reynol
ds)
K (loss coefficient)
f (friction coefficient)
5.000E
+00
8.333
E-05
7.000E
+00
6.867E
+01
3.673E-01
6.232E+
03
1.018E+00
3.600E-02
1.000E
+01
1.667
E-04
1.000E
+01
9.810E
+01
7.347E-01
1.246E+
04
3.635E-01
3.000E-02
1.500E
+01
2.500
E-04
1.300E
+01
1.275E
+02
1.102E+0
0
1.870E+
04
2.100E-01
2.700E-02
2.000E
+01
3.333
E-04
2.300E
+01
2.256E
+02
1.469E+0
0
2.493E+
04
2.090E-01
2.550E-02
2.500E
+01
4.167
E-04
3.700E
+01
3.630E
+02
1.837E+0
0
3.116E+
04
2.152E-01
2.400E-02
Venturi Tube
Q (l/min)
Q (m^3
DP (mmH2
DP (Pa)
V (flow velocity)
Re (Reynol
K (loss coefficient)
f (friction coefficient)
/s)
O)
ds)
5.000E
+00
8.333
E-05
1.500E
+01
1.472E
+02
3.673E-01
6.232E+
03
2.181E+00
3.600E-02
1.000E
+01
1.667
E-04
2.100E
+01
2.060E
+02
7.347E-01
1.246E+
04
7.634E-01
3.000E-02
1.500E
+01
2.500
E-04
3.800E
+01
3.728E
+02
1.102E+0
0
1.870E+
04
6.140E-01
2.700E-02
2.000E
+01
3.333
E-04
4.300E
+01
4.218E
+02
1.469E+0
0
2.493E+
04
3.908E-01
2.550E-02
2.500E
+01
4.167
E-04
6.000E
+01
5.886E
+02
1.837E+0
0
3.116E+
04
3.490E-01
2.400E-02
Combined rough pipes
Q (l/min)
Q (m^3
/s)
DP (mmH2
O)
DP (Pa)
V (flow velocity)
Re (Reynol
ds)
K (loss coefficient)
f (friction coefficient)
5.000E
+00
8.333
E-05
2.600E
+01
2.551E
+02
3.673E-01
6.232E+
03
3.781E+00
3.600E-02
1.000E
+01
1.667
E-04
7.000E
+01
6.867E
+02
7.347E-01
1.246E+
04
2.545E+00
3.000E-02
1.500E
+01
2.500
E-04
1.835E
+02
1.800E
+03
1.102E+0
0
1.870E+
04
2.965E+00
2.700E-02
2.000E
+01
3.333
E-04
3.705E
+02
3.635E
+03
1.469E+0
0
2.493E+
04
3.367E+00
2.550E-02
2.500E
+01
4.167
E-04
5.793E
+02
5.682E
+03
1.837E+0
0
3.116E+
04
3.369E+00
2.400E-02
Table 2: Results of all configurations
Related Documents
Related Questions
Note:
Please deliver a clear, step-by-step handwritten calculation (without any explanations!), ensuring it is created without any AI assistance. I expect a top-quality, expert-level handwritten solution, and I will evaluate and rate it based on its accuracy and precision. Double-check every detail for correctness before submission. Appreciate your time and effort!.
Question is down below:
In Figure 3, when y = 160 mm, the piston rod of the hydraulic cylinder C imparts a
vertical motion to the pin B consisting of y = 400 mm/s and ÿ = -100 mm/s'. For this instant determine the angular velocity w and the angular acceleration a of link OA.
Members OA and AB make equal angles with the horizontal at this instant.
arrow_forward
The crux of the problem asks you to compute the elastic modulus of a pancake--for this we give you numbers that we got from our own measurements of the pancakes. The last question asks you to hypothesize about which ingredients are playing the role of flour in the gluten free recipes. If you find this topic interesting, you may want to consider exploring something like this for your final project, and design an experiment to understand the difference between the normal and gluten free recipe and try to manipulate the gluten free recipe to better resemble the normal pancakes.If you choose to make the two recipes and compare them in your own kitchen, make sure you use exactly the same protocol for each recipe: In our trials, we made the batter, and then cooked on a skillet, using 1/4 cup of batter per pancake, and flipped when the edges were firm and golden, about 4-5 minutes on each side.Consider a stack of six pancakes. Each pancake is made of 1/4 cup (approximately 60 mL) of batter,…
arrow_forward
Mechanical engineering aircon topic. Please help to solve the problem asap. Will upvote for your answer
arrow_forward
Determine the resistance in each scenario presented. Explain whether the resistance is linear or not,
and if not describe the relation, finally, explain how it can be linearized about a specific condition.
Be sure to state the units and demonstrate that they are correct using the appropriate pressure/flow
relation.
a) Laminar flow
An aqueous solution of 50% glycerol / 50% water is flowing through a pipe with the following system
parameters:
System_Parameters = (L = 100.0 D= 0.2 u= 0.022 p= 1150.0 9m=7.0 g = 9.81)
units : L ~ m; D~ m; µ ~ Pa · s; p~
kg: 4. ~ 8:
Confirm that this is laminar flow and then calculate the resistance.
b) Pump Resistance from Pump Curve
Consider the following pump curve:
[Feet) (Meters]
30어
Find the pump resistance if the pump is
supporting 15 meters of discharge head
pressure, at a flow rate of 300 L/minute.
80-
250
7어 100 PSI
L/min
Determine the pump resistance in
Pa
20어 6어85 PST
50 SCFM
5어 75 PST
Note that standard pump curves are
oriented opposite to the…
arrow_forward
Task 1
You are employed as a mechanical engineer within an unnamed research center, specializing in the development.
of innovative air conditioning systems. Your division is tasked with providing computer-based modeling and
design solutions using computational fluid dynamics through ANSYS software. Your primary responsibilities.
involve the analysis of horizontal channel dynamics to meet specific criteria. Under the guidance of your
immediate supervisor, you have been assigned unique responsibilities within an ongoing project. As a member of
the research team, your role includes constructing an appropriate model and executing a sequence of simulation.
iterations to explore and enhance channel performance. Figure 1 provides a visualization of the horizontal channel
under consideration. Consider 2D, incompressible, steady flowin a horizontal channel at a Reynolds number of
150. The schematic below illustrates the channel flow, not drawn to scale. For simplicity, neglect gravity. The…
arrow_forward
Question 4
A team of engineers tasked with the design of a pipe system is currently sizing
some of the different subsections. The team has started by identifying two types
of pipes, each of them involving different fluids (water and glycerin) as shown in
Figure 4 below. Material roughness is e = 10μm for both.
D₁ = 0.1m
D₂ = 0.15m
(a)
(b)
V₂
Section 1
Pw=999 kg/m³
P = 0.00112 N-s/m²
P₁ = 1260 kg/m³
#₂ = 1.5 N-s/m²
Figure 4
Section 2
Pipe 1 (water)
Pipe 2 (glycerin)
1.1D₂
1.1D ₂
Consider only Section 1, where pipe diameter is respectively Di and D2, and
estimate the head loss per meter when the volume flow rate within each
pipe is Q=0.05 m³/s. Refer to the given values of density (p) and dynamic
viscosity (u) indicated in the figure as well as to the Moody chart in the next
page where appropriate.
As also shown in the figure above, the diameter of the pipe increases by 10%
across a sudden expansion for both cases. What is the head loss per meter
over Section 2?
In order to account for…
arrow_forward
Question No. 17
arrow_forward
Task 1
You are employed as a mechanical engineer within an unnamed research center, specializing in the
development of innovative air conditioning systems. Your division is tasked with providing computer-based
modeling and design solutions using computational fluid dynamics through ANSYS software. Your primary
responsibilities involve the analysis of horizontal channel dynamics to meet specific criteria. Under the
guidance of your immediate supervisor, you have been assigned unique responsibilities within an ongoing
project. As a member of the research team, your role includes constructing an appropriate model and
executing a sequence of simulation iterations to explore and enhance channel performance. Figure 1
provides a visualization of the horizontal channel under consideration. Consider 2D, incompressible, steady
flow in a horizontal channel at a Reynolds number of 150. The schematic below illustrates the channel flow,
not drawn to scale. For simplicity, neglect gravity. The…
arrow_forward
Please go for all in handwritten format.
[All these are easy one's ,So Solve all]
arrow_forward
Fluid mechanics
arrow_forward
Find the viscosity of Water @ 25oC and @37oC
arrow_forward
Fluid Mechanics Laboratory (a report on this experiment is required) Experiment No.1 Reynolds number
arrow_forward
Develop a summary of a report on a fluid pumping system project, which, in addition to the summary, contains:
Project objective: To experimentally determine the characteristic curves of a pump as a function of its flow rate and pressure loss;
Methodology used: measurement of the flow of the pump and its head for the assembly of the graph;
Results: Graphs resulting from the pump curves
Conclusion: Conclusion that the project was able to determine reliable curves, even with a small number of data
arrow_forward
CS) Flow through a heat exchanger tube is to be studied by means of a 1/10 scale model. If the tmateaangeraarmall, carries widecreme de ratio of pressure losses between the model and the prototype if water is used in the model.
arrow_forward
Subject: Mechanical Measurements
Do not copy other answers
arrow_forward
Note:-
• Do not provide handwritten solution. Maintain accuracy and quality in your answer. Take care of plagiarism.
• Answer completely.
• You will get up vote for sure.
arrow_forward
Im needed the solve max 30-45 minutes and please send Im very needed. Thank u
Manufacture and design a U-pipe in an open state with a minimum of 7 different fluids with a datum.
NOTE
Examples of answers such as the available images and there are also problems from the 2 available images. The answer does not need to use numbers as in the example answer
arrow_forward
Problem 1: HD-based Ch 7 & MSH-based Ch 3:
a solution of unknown origin. Based on the shear rate and shear stress characteristics,
determine the type of fluid. A) Mark your answer by placing the Capital Letter corresponding to
the correct term in the box. B) What is the viscosity of the solution when the shear stress is
sufficient for movement? Remember units. Answers must be supported by an appropriately
labeled and hand drawn graph (practice for exams).
The following data was obtained for
Shear rate (s)
Shear Stress (Pa)
11
200
22
325
470
34
41
600
45
A. Newtonian
B. Pseudoplastic
C. Dilatant
D. Bingham plastic
E. Rheopectic
A:
B:
arrow_forward
Give an example of an interconnected system of two tanks so that:
the system is homogeneous
the system is nonhomogeneous
the systems has constant coefficients
the systems has at least one non-constant coefficient
Solve one of the systems you gave (use a constant-coefficient, homogeneous system)
arrow_forward
SEE MORE QUESTIONS
Recommended textbooks for you
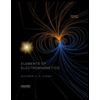
Elements Of Electromagnetics
Mechanical Engineering
ISBN:9780190698614
Author:Sadiku, Matthew N. O.
Publisher:Oxford University Press
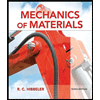
Mechanics of Materials (10th Edition)
Mechanical Engineering
ISBN:9780134319650
Author:Russell C. Hibbeler
Publisher:PEARSON
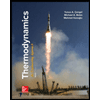
Thermodynamics: An Engineering Approach
Mechanical Engineering
ISBN:9781259822674
Author:Yunus A. Cengel Dr., Michael A. Boles
Publisher:McGraw-Hill Education
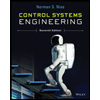
Control Systems Engineering
Mechanical Engineering
ISBN:9781118170519
Author:Norman S. Nise
Publisher:WILEY
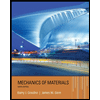
Mechanics of Materials (MindTap Course List)
Mechanical Engineering
ISBN:9781337093347
Author:Barry J. Goodno, James M. Gere
Publisher:Cengage Learning
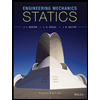
Engineering Mechanics: Statics
Mechanical Engineering
ISBN:9781118807330
Author:James L. Meriam, L. G. Kraige, J. N. Bolton
Publisher:WILEY
Related Questions
- Note: Please deliver a clear, step-by-step handwritten calculation (without any explanations!), ensuring it is created without any AI assistance. I expect a top-quality, expert-level handwritten solution, and I will evaluate and rate it based on its accuracy and precision. Double-check every detail for correctness before submission. Appreciate your time and effort!. Question is down below: In Figure 3, when y = 160 mm, the piston rod of the hydraulic cylinder C imparts a vertical motion to the pin B consisting of y = 400 mm/s and ÿ = -100 mm/s'. For this instant determine the angular velocity w and the angular acceleration a of link OA. Members OA and AB make equal angles with the horizontal at this instant.arrow_forwardThe crux of the problem asks you to compute the elastic modulus of a pancake--for this we give you numbers that we got from our own measurements of the pancakes. The last question asks you to hypothesize about which ingredients are playing the role of flour in the gluten free recipes. If you find this topic interesting, you may want to consider exploring something like this for your final project, and design an experiment to understand the difference between the normal and gluten free recipe and try to manipulate the gluten free recipe to better resemble the normal pancakes.If you choose to make the two recipes and compare them in your own kitchen, make sure you use exactly the same protocol for each recipe: In our trials, we made the batter, and then cooked on a skillet, using 1/4 cup of batter per pancake, and flipped when the edges were firm and golden, about 4-5 minutes on each side.Consider a stack of six pancakes. Each pancake is made of 1/4 cup (approximately 60 mL) of batter,…arrow_forwardMechanical engineering aircon topic. Please help to solve the problem asap. Will upvote for your answerarrow_forward
- Determine the resistance in each scenario presented. Explain whether the resistance is linear or not, and if not describe the relation, finally, explain how it can be linearized about a specific condition. Be sure to state the units and demonstrate that they are correct using the appropriate pressure/flow relation. a) Laminar flow An aqueous solution of 50% glycerol / 50% water is flowing through a pipe with the following system parameters: System_Parameters = (L = 100.0 D= 0.2 u= 0.022 p= 1150.0 9m=7.0 g = 9.81) units : L ~ m; D~ m; µ ~ Pa · s; p~ kg: 4. ~ 8: Confirm that this is laminar flow and then calculate the resistance. b) Pump Resistance from Pump Curve Consider the following pump curve: [Feet) (Meters] 30어 Find the pump resistance if the pump is supporting 15 meters of discharge head pressure, at a flow rate of 300 L/minute. 80- 250 7어 100 PSI L/min Determine the pump resistance in Pa 20어 6어85 PST 50 SCFM 5어 75 PST Note that standard pump curves are oriented opposite to the…arrow_forwardTask 1 You are employed as a mechanical engineer within an unnamed research center, specializing in the development. of innovative air conditioning systems. Your division is tasked with providing computer-based modeling and design solutions using computational fluid dynamics through ANSYS software. Your primary responsibilities. involve the analysis of horizontal channel dynamics to meet specific criteria. Under the guidance of your immediate supervisor, you have been assigned unique responsibilities within an ongoing project. As a member of the research team, your role includes constructing an appropriate model and executing a sequence of simulation. iterations to explore and enhance channel performance. Figure 1 provides a visualization of the horizontal channel under consideration. Consider 2D, incompressible, steady flowin a horizontal channel at a Reynolds number of 150. The schematic below illustrates the channel flow, not drawn to scale. For simplicity, neglect gravity. The…arrow_forwardQuestion 4 A team of engineers tasked with the design of a pipe system is currently sizing some of the different subsections. The team has started by identifying two types of pipes, each of them involving different fluids (water and glycerin) as shown in Figure 4 below. Material roughness is e = 10μm for both. D₁ = 0.1m D₂ = 0.15m (a) (b) V₂ Section 1 Pw=999 kg/m³ P = 0.00112 N-s/m² P₁ = 1260 kg/m³ #₂ = 1.5 N-s/m² Figure 4 Section 2 Pipe 1 (water) Pipe 2 (glycerin) 1.1D₂ 1.1D ₂ Consider only Section 1, where pipe diameter is respectively Di and D2, and estimate the head loss per meter when the volume flow rate within each pipe is Q=0.05 m³/s. Refer to the given values of density (p) and dynamic viscosity (u) indicated in the figure as well as to the Moody chart in the next page where appropriate. As also shown in the figure above, the diameter of the pipe increases by 10% across a sudden expansion for both cases. What is the head loss per meter over Section 2? In order to account for…arrow_forward
- Question No. 17arrow_forwardTask 1 You are employed as a mechanical engineer within an unnamed research center, specializing in the development of innovative air conditioning systems. Your division is tasked with providing computer-based modeling and design solutions using computational fluid dynamics through ANSYS software. Your primary responsibilities involve the analysis of horizontal channel dynamics to meet specific criteria. Under the guidance of your immediate supervisor, you have been assigned unique responsibilities within an ongoing project. As a member of the research team, your role includes constructing an appropriate model and executing a sequence of simulation iterations to explore and enhance channel performance. Figure 1 provides a visualization of the horizontal channel under consideration. Consider 2D, incompressible, steady flow in a horizontal channel at a Reynolds number of 150. The schematic below illustrates the channel flow, not drawn to scale. For simplicity, neglect gravity. The…arrow_forwardPlease go for all in handwritten format. [All these are easy one's ,So Solve all]arrow_forward
arrow_back_ios
SEE MORE QUESTIONS
arrow_forward_ios
Recommended textbooks for you
- Elements Of ElectromagneticsMechanical EngineeringISBN:9780190698614Author:Sadiku, Matthew N. O.Publisher:Oxford University PressMechanics of Materials (10th Edition)Mechanical EngineeringISBN:9780134319650Author:Russell C. HibbelerPublisher:PEARSONThermodynamics: An Engineering ApproachMechanical EngineeringISBN:9781259822674Author:Yunus A. Cengel Dr., Michael A. BolesPublisher:McGraw-Hill Education
- Control Systems EngineeringMechanical EngineeringISBN:9781118170519Author:Norman S. NisePublisher:WILEYMechanics of Materials (MindTap Course List)Mechanical EngineeringISBN:9781337093347Author:Barry J. Goodno, James M. GerePublisher:Cengage LearningEngineering Mechanics: StaticsMechanical EngineeringISBN:9781118807330Author:James L. Meriam, L. G. Kraige, J. N. BoltonPublisher:WILEY
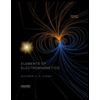
Elements Of Electromagnetics
Mechanical Engineering
ISBN:9780190698614
Author:Sadiku, Matthew N. O.
Publisher:Oxford University Press
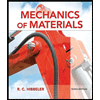
Mechanics of Materials (10th Edition)
Mechanical Engineering
ISBN:9780134319650
Author:Russell C. Hibbeler
Publisher:PEARSON
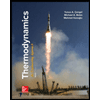
Thermodynamics: An Engineering Approach
Mechanical Engineering
ISBN:9781259822674
Author:Yunus A. Cengel Dr., Michael A. Boles
Publisher:McGraw-Hill Education
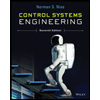
Control Systems Engineering
Mechanical Engineering
ISBN:9781118170519
Author:Norman S. Nise
Publisher:WILEY
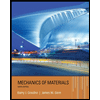
Mechanics of Materials (MindTap Course List)
Mechanical Engineering
ISBN:9781337093347
Author:Barry J. Goodno, James M. Gere
Publisher:Cengage Learning
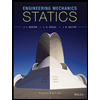
Engineering Mechanics: Statics
Mechanical Engineering
ISBN:9781118807330
Author:James L. Meriam, L. G. Kraige, J. N. Bolton
Publisher:WILEY