Group 4 , Lab 7
docx
keyboard_arrow_up
School
California State University, Northridge *
*We aren’t endorsed by this school
Course
317
Subject
Mechanical Engineering
Date
Feb 20, 2024
Type
docx
Pages
14
Uploaded by moops02
Fall 2023
California State University, Northridge
Experiment 7
Vibration of a Rigid Beam with a Dashpot
Damper
Mechanics Lab
AM 317
Written By:
Abstract:
Vibrations are the oscillatory motion or periodic movement of a mechanical system about
its equilibrium position. There are various types of vibrations. Free vibrations occur when a system oscillates without any external forces or excitation. Forced vibrations occur when an external force is applied to the system. Resonance occurs when a forced frequency matches the system’s natural frequency. Finally, damped vibrations occur when a damping mechanism, such as a viscous damper, is introduced into a system. The damper acts to reduce the amplitude of vibrations and control the system’s response. Dampers are devices designed to reduce the amplitude of vibrations and dissipate energy in mechanical systems. These devices are critical for controlling vibrations in engineering applications. There are many different types of dampers. Friction dampers use friction between surfaces to dissipate energy. When a system with a friction damper vibrates, the friction forces absorb and dissipate energy and reduce the amplitude of motion. Pneumatic dampers use gases to
absorb energy. When a system with a pneumatic damper vibrates, the compression and expansion of gases within the damper reduce the amplitude of motion. Finally, Viscous dampers use a fluid to resist motion. When a system with a viscous damper vibrates, the fluid in the damper experiences shear and reduces the amplitude of motion. For the most part we saw what we expected to see in this lab. For the tables that we made
from the data collected, we saw a sharp increase of magnification factor around 6.8 HZ for both the fully opened damper and the fully closed damper. This sharp increase in magnification factor indicates that the vibrations matched the beam’s resonance frequency.
Your preview ends here
Eager to read complete document? Join bartleby learn and gain access to the full version
- Access to all documents
- Unlimited textbook solutions
- 24/7 expert homework help
Introduction:
Vibrations represent the periodic or oscillatory movement of a mechanical system around
its equilibrium position. Dampers are used to help reduce the vibrations that occur in various systems. There are various types of dampers that an engineer can use in order to reduce the vibrations in a system. Dampers that most people know about are in one’s car. The dampers in one’s car act as shock absorbers to give the driver and passengers a smoother ride. Other places that have a big affect on people is dampers in buildings and bridges. Dampers in buildings and bridges serve to reduce the vibrations caused by wind in order to reduce the risk of structural damage. Of the different applications and different types of dampers, the one that we will be testing is a viscous damper that uses a fluid to dampen vibrations, most commonly found in automotive applications. For this lab, we made use of newer equipment. The testing machine is called the TQ TM1016 Free and Forced Vibrations Apparatus. This machine let us set the acceleration and displacements of the motor, as well as the motor’s speed, and recorded the data onto one of the lab computers. We also made use of the accompanying software, TecQuipment VDAS Hardware
and Software in order to record what the testing machine was reading out. Lastly, we used a tape measure to get measurements of the equipment that we were testing. There are a few things that we expect to see in this lab, one of which is a bell-shaped graph. As the frequency gets closer and closer to the material’s natural frequency, the more the beam will vibrate.
Theory:
Because there are so many different variables in this lab, there are also many different equations to consider when performing this lab. The first of which is the mass inertia of the system. The four different mass inertia terms that we need are the mass inertia of the beam, exciter, spring unit, and dashpot. For the following equations, m is the mass, and L is the length.
MoI, beam: I
b
=
1
3
m
b
L
b
2
MoI, exciter: I
e
=
m
e
L
e
2
MoI, spring unit: I
s
=
(
1
3
m
s
+
m
fixing
)
L
s
2
MoI, dashpot: I
d
=
m
d
L
d
2
The moment of inertia of the system is all the moments of inertia added together.
MoI, system: I
A
=
I
b
+
I
e
+
I
s
+
I
d
The next equation that we need is the angular natural frequency. The angular natural frequency is calculated by multiplying the spring constant k, in this case the spring constant is given as 3800, times L
s
, the length from the pivot to the center of the spring fixing squared, over the I
A
., the moment of inertia of the system, all under the square root.
ω
n
=
√
k L
s
2
I
A
Next, we need the excitation speed, ω
0
. The excitation speed is a simple calculation, which is the motor speed in hertz, times 2π.
Next, the β of the system needs to be calculated. It is also a simple calculation of the natural frequency,
ω
n
, over the excitation speed ω
0
.
The next equation we need uses parts from all the previous equations. The magnification factor uses the moment of inertia of the whole system, I
A
, over the product of l, the length from the pivot to the displacement sensor, times the L
E
, the length from the pivot to the center of the exciter, times the m
0
, the eccentric mass added to the rotating unit of the exciter, times r, the distance from the center of the exciter to the eccentric mass, that fraction, times y
adj
the y value found during the experimental phase minus the y
shift
.
MF
=
I
A
l L
E
m
0
r
y
adj
Your preview ends here
Eager to read complete document? Join bartleby learn and gain access to the full version
- Access to all documents
- Unlimited textbook solutions
- 24/7 expert homework help
Procedures:
For the most part the procedures of the lab this week were done on the computer that was gathering data from the free and forced vibrations machine.
First, we had to make sure that the vibrations machine was on. There is a switch on the surge protector as well as a switch on the machine that when switched on, a green light would appear and the screen on the machine would turn on. We then had to change the acceleration dial
and displacement dials to zero. The lights above those dials would turn off when they were in the
zero position. Once we were sure that the machine was properly set up, we logged onto the computer with one of our CSUN credentials. We opened “TecQuipment VDAS” and changed the settings to what was given detailed in the lab. We tested to see if the vibration machine was properly outputting data to the computer by exciting the cantilever bar with our hand. In our case, the vibration machine did not output the readings to the computer. We decided to turn everything off, restart the computer and restart the lab procedures. This worked and we were able
to proceed with the rest of the lab.
The next part of the lab was the data collection portion. We set the VDAS software to the
appropriate settings, made sure that the oil damper was open, and pressed the green start button on the machine to start the motor. When looking at the computer we saw a sine graph. The scaling on the computer can be changed in order to see the full graph. To start testing we adjusted the exciter motor dial until it was at 5.25 Hz. We waited for the reading to steady out before we took the displacement amplitude. We adjusted the exciter motor’s dial until we recorded all the readings that we needed for the first portion of the lab. The next part was to
repeat the same steps except with the damper disk closed. When we were done, we closed the VDAS software and exited the computer.
Results:
Table 1: Specific Measurements and Calculations
Component Rigid Beam
Dashpot Exciter Eccentric Mass Displacement
Sensor Spring and fixing
Spring constant k= 3800 N/m)
Table 2: Experimental Records and Calculations for Fully-Open Damping Condition
Recommended Motor Speed (Hz)
Excitation
Speed
ω
0
(rad/s)
β =ω
0
/ω
n
Measured y
(10
-3
m)
Adjusted y*
(10
-3 m)
MF = (
I
A
/
l
L
e
m
0
r
)*y
adj
5.25
32.987
0.741
0.488
0.039
561.833
5.50
34.558
0.777
0.510
0.061
878.765
5.75
36.128
0.812
0.568
0.119
1714.311
6.00
37.699
0.847
0.625
0.176
2535.452
6.20
38.956
0.875
0.727
0.278
4004.862
6.40
40.212
0.904
0.864
0.415
5978.480
6.50
40.841
0.918
0.979
0.530
7635.168
6.60
41.469
0.932
1.321
0.872
12562.012
6.70
42.097
0.946
2.086
1.637
23582.584
6.80
42.726
0.960
3.470
3.021
43520.457
6.90
43.354
0.974
2.340
1.891
27241.703
7.00
43.982
0.988
1.390
0.941
13556.024
7.10
44.611
1.003
1.127
0.678
9767.252
7.30
45.867
1.031
0.864
0.415
5978.480
7.50
47.124
1.059
0.727
0.278
4004.862
7.75
48.695
1.094
0.659
0.210
3025.255
8.50
53.407
1.200
0.556
0.107
1541.440
9.00
56.549
1.271
0.533
0.084
1210.102
Your preview ends here
Eager to read complete document? Join bartleby learn and gain access to the full version
- Access to all documents
- Unlimited textbook solutions
- 24/7 expert homework help
9.25
58.119
1.306
0.522
0.073
1051.636
Table 3: Damping Ratio and Viscous Damping Coefficient Calculations for Fully-Open, Minimum, Damping Condition.
ζ using Eq.
(7.10)
0.0155
ζ using Eq.
(7.11)
0.0000
Average ζ
0.0078
Viscous
Damping Coefficient 17.3991
Table 4: Experimental Records and Calculations for Fully-Shut Damping Condition
Recommended Motor Speed (Hz)
Excitation
Speed
ω
0
(rad/s)
β =ω
0
/ω
n
Measured y
(10
-3
m)
Adjusted y*
(10
-3 m)
MF = (
I
A
/
l
L
e
m
0
r
)*y
adj
5.25
32.9867
0.7413
0.4990
0.0500
720.2989
5.50
34.5575
0.7766
0.5220
0.0730
1051.6363
5.75
36.1283
0.8119
0.5790
0.1300
1872.7770
6.00
37.6991
0.8472
0.6130
0.1640
2362.5802
6.20
38.9557
0.8755
0.6930
0.2440
3515.0584
6.40
40.2124
0.9037
0.7730
0.3240
4667.5366
6.50
40.8407
0.9178
0.8190
0.3700
5330.2115
6.60
41.4690
0.9320
0.9100
0.4610
6641.1554
6.70
42.0973
0.9461
1.0130
0.5640
8124.9711
6.80
42.7257
0.9602
1.0360
0.5870
8456.3085
6.90
43.3540
0.9743
1.0130
0.5640
8124.9711
7.00
43.9823
0.9884
0.9330
0.4840
6972.4929
7.10
44.6106
1.0026
0.8990
0.4500
6482.6897
7.30
45.8673
1.0308
0.8070
0.3580
5157.3398
7.50
47.1239
1.0590
0.7160
0.2670
3846.3959
7.75
48.6947
1.0943
0.6700
0.2210
3183.7209
8.50
53.4071
1.2002
0.5680
0.1190
1714.3113
9.00
56.5487
1.2708
0.5560
0.1070
1541.4395
9.25
58.1195
1.3061
0.5450
0.0960
1382.9738
Table 5: Damping Ratio and Viscous Damping Coefficient Calculations for Fully-Open, Minimum, Damping Condition.
ζ using Eq.
(7.10)
0.05102040
8
ζ using Eq.
(7.11)
5.91275E-05
Average ζ
0.02553976
8
Viscous
Damping Coefficient 57.1333135
7
Graph 1: Magnification factor versus frequency ratio, fully opened damper
0.600
0.700
0.800
0.900
1.000
1.100
1.200
1.300
1.400
0.000
5000.000
10000.000
15000.000
20000.000
25000.000
30000.000
35000.000
40000.000
45000.000
50000.000
MF versus β Fully Open Frequency Ratio, β
Magnification Factor, MF
Graph 2: Magnification factor versus frequency ratio, fully closed damper
0.6000
0.7000
0.8000
0.9000
1.0000
1.1000
1.2000
1.3000
1.4000
0.0000
1000.0000
2000.0000
3000.0000
4000.0000
5000.0000
6000.0000
7000.0000
8000.0000
9000.0000
MF versus β Fully Closed Frequency Ratio, β
Magnification Factor, MF
Conclusions and Discussion:
For the most part, we saw in our graphs and tables the results that we expected to see from the lab.
In Table 1, we took measurements of length of different points of the system. The table also came with values for mass given. Using both the length measurements and the given mass values, we were able to calculate the moments of inertia for the beam, exciter, spring unit, and dashpot. Using those values, we were able to calculate the moment of inertia for the whole system.
In Table 2 and 4, we recorded our measured values of y. There we also calculated the excitation speed, calculated the β, found the y adjusted value, and calculated the magnitude factor. For the magnitude factor column, we also took note of the highest value that we calculated. For table 2 we calculated the highest magnitude factor to be 43,520.457, which happened when we tested the system at 6.8 Hz. For table 4 we calculated the highest magnitude factor to be 8,456.3085, which also happened when we tested the system at 6.8 Hz. For Table 3 and 5, we calculated the ζ of each of the systems using two different methods
as well as calculating the viscous damping coefficient. We found that the viscous damping coefficient was much higher for the fully closed damper, which makes sense because more fluid was affecting the damper.
For our graphs, we found that the values we calculated produced a bell curve graph, where our highest value was the highest point on the graph. This is similar to the sample graph that was provided in the lab manual.
Your preview ends here
Eager to read complete document? Join bartleby learn and gain access to the full version
- Access to all documents
- Unlimited textbook solutions
- 24/7 expert homework help
Appendix:
Related Documents
Related Questions
Vibrations
arrow_forward
Vibration Engineering
arrow_forward
Which of these statements are correct?
arrow_forward
Vibration Engineering. Please help to provide solution for the problem below. Thank you.
arrow_forward
E and 5 v X
O file:///C:/Users/Hp/Desktop/mm/OUTCOME%20NO.2%20and%205%20with%20Problems.pdf
+
O Fit to page
D Page view
A Read aloud
1 Add notes
Problems
1. A brass rod of diameter 25 mm and length 250 mm is
subjected to a tensile load of 50 kN and the extension of
the rod is equal to 0.3 mm. Find the Young's Modulus or
Modulus of Elasticity.
99+
to search
hp
delete
prt sc
14 DI
backs
&
7
8
24
4
P
EJR
-0
J
K
H
D.
F
arrow_forward
122
1.17 The tripod shown in Fig. 1.73 is used for mounting an electronic instrument that finds the
distance between two points in space. The legs of the tripod are located symmetrically
about the mid-vertical axis, each leg making an angle a with the vertical. If each leg has a
length / and axial stiffness k, find the equivalent spring stiffness of the tripod in the verti-
cal direction.
CHAPTER 1 FUNDAMENTALS OF VIBRATION
FIGURE 1.73 A tripod carrying an electronic instrument.
arrow_forward
Subject: mechanical engineering
arrow_forward
APPLICATIONS OF FIRST ORDER DIFFERENTIAL EQUATIONS
Newton’s Law of Cooling and Joint Proportions
At 4:00pm, a thermometer reading of 28 deg C is taken outside where the ambient temperature is –11 deg C. At 4:05 pm, the thermometer reads 8 deg above zero. After a while, the thermometer is returned to the room maintained at 28 deg C. At 4:12pm, the thermometer reads 15 deg C. When was the thermometer returned to the room?
arrow_forward
Alert for not submit AI generated answer. I need unique and correct answer. Don't try to copy from anywhere. Do not give answer in image formet and hand writing
arrow_forward
Can you please show the complete solution of the image below. Thanks!
Subject: Mechanical Vibration
arrow_forward
Find the differential equation of the mechanical system in Figure 1(a)
To obtain the differential equation of motion of the mass and spring system given in Fig. 1. (a)
one may utilize the Newton's law for mass and spring relations defined as shown in Fig. 1. (b)
and (c) use f = cv for viscous friction, where v is the velocity of the motion and c is a constant.
Z///////
k
M
F.
F,
F
F
F,
F,
k
EF=ma
F = k(x, - x,) = kx
(b)
(c)
Figure 1: Mass-spring system (a), Force relations of mass (b) and spring (c)
arrow_forward
Please solve the following problem showing every single step and all the work, I'm trying to get through some good practice on these dynamics and vibrations problems while I have some time off before finals in a few weeks, need some really good help on this problem though. I really appreciate it!
arrow_forward
.ll alfa ?
1:09 PM
@ 27% 4
PHYS220_Exam-1 Pr...
PHYS220 _ Spring/20-21 _ Practice Sheet-1_ Keys
1) A0.1 kg object oscillates as a simple harmonic motion along the x -axis with a frequency f = 3.185 Hz.
At a position x1, the object has a kinetic energy of 0.7 J and a potential energy 0.3 J. The amplitude of
oscillation, A, is:
(a) 0.12 m
(b) 0.22 m
(c) 0.31 m
(d)0.42 m
2) A block of mass m is attached to a spring with force constant, k and oscillate at a frequency f. If the
mass is changed to m' = m/2, and the spring force is changed to k' = 2k, then the new frequency f' of
the oscillation would be,
(a) f' = 2f
(b) f' = f
(c) f' = f/2
(d) f' = 4f
The following given is for questions 3 and 4:
A block of mass m = 2 kg is attached to a spring with spring constant k = 200 N/m, and set to
oscillates on a frictionless horizontal surface. At time t = 0 its position is xo = 0 and its velocity is
vo = +5 m/s.
3) Which of the following is true about the oscillation amplitude and the phase…
arrow_forward
answer fast
arrow_forward
Note:
Please provide a detailed, step-by-step handwritten solution (no explanations) created entirely without AI involvement. The work must reflect expert-level precision, as I will assess and rate it based on accuracy and quality. Ensure every calculation is thoroughly double-checked before submitting.
Question:
In Figure 6, a 2-kg block is subjected to a harmonic force F = 30 cos 5t. Given that if k1 = 40 N/m, k2 = 60 N/m, k3 = 76N/m, and c = 50 N.s/m, derive the equation describing its steady-state motion.
arrow_forward
Need help with C as I’ve got an answer for x^1 but it’s not correct due to it not being from the 0 time point.
So can you help find the answer from 0 Time Point to when the wave reaches -2 next
arrow_forward
SEE MORE QUESTIONS
Recommended textbooks for you
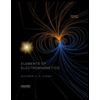
Elements Of Electromagnetics
Mechanical Engineering
ISBN:9780190698614
Author:Sadiku, Matthew N. O.
Publisher:Oxford University Press
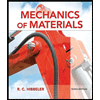
Mechanics of Materials (10th Edition)
Mechanical Engineering
ISBN:9780134319650
Author:Russell C. Hibbeler
Publisher:PEARSON
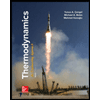
Thermodynamics: An Engineering Approach
Mechanical Engineering
ISBN:9781259822674
Author:Yunus A. Cengel Dr., Michael A. Boles
Publisher:McGraw-Hill Education
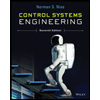
Control Systems Engineering
Mechanical Engineering
ISBN:9781118170519
Author:Norman S. Nise
Publisher:WILEY
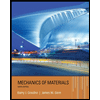
Mechanics of Materials (MindTap Course List)
Mechanical Engineering
ISBN:9781337093347
Author:Barry J. Goodno, James M. Gere
Publisher:Cengage Learning
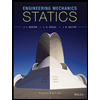
Engineering Mechanics: Statics
Mechanical Engineering
ISBN:9781118807330
Author:James L. Meriam, L. G. Kraige, J. N. Bolton
Publisher:WILEY
Related Questions
- Vibration Engineering. Please help to provide solution for the problem below. Thank you.arrow_forwardE and 5 v X O file:///C:/Users/Hp/Desktop/mm/OUTCOME%20NO.2%20and%205%20with%20Problems.pdf + O Fit to page D Page view A Read aloud 1 Add notes Problems 1. A brass rod of diameter 25 mm and length 250 mm is subjected to a tensile load of 50 kN and the extension of the rod is equal to 0.3 mm. Find the Young's Modulus or Modulus of Elasticity. 99+ to search hp delete prt sc 14 DI backs & 7 8 24 4 P EJR -0 J K H D. Farrow_forward122 1.17 The tripod shown in Fig. 1.73 is used for mounting an electronic instrument that finds the distance between two points in space. The legs of the tripod are located symmetrically about the mid-vertical axis, each leg making an angle a with the vertical. If each leg has a length / and axial stiffness k, find the equivalent spring stiffness of the tripod in the verti- cal direction. CHAPTER 1 FUNDAMENTALS OF VIBRATION FIGURE 1.73 A tripod carrying an electronic instrument.arrow_forward
- Subject: mechanical engineeringarrow_forwardAPPLICATIONS OF FIRST ORDER DIFFERENTIAL EQUATIONS Newton’s Law of Cooling and Joint Proportions At 4:00pm, a thermometer reading of 28 deg C is taken outside where the ambient temperature is –11 deg C. At 4:05 pm, the thermometer reads 8 deg above zero. After a while, the thermometer is returned to the room maintained at 28 deg C. At 4:12pm, the thermometer reads 15 deg C. When was the thermometer returned to the room?arrow_forwardAlert for not submit AI generated answer. I need unique and correct answer. Don't try to copy from anywhere. Do not give answer in image formet and hand writingarrow_forward
- Can you please show the complete solution of the image below. Thanks! Subject: Mechanical Vibrationarrow_forwardFind the differential equation of the mechanical system in Figure 1(a) To obtain the differential equation of motion of the mass and spring system given in Fig. 1. (a) one may utilize the Newton's law for mass and spring relations defined as shown in Fig. 1. (b) and (c) use f = cv for viscous friction, where v is the velocity of the motion and c is a constant. Z/////// k M F. F, F F F, F, k EF=ma F = k(x, - x,) = kx (b) (c) Figure 1: Mass-spring system (a), Force relations of mass (b) and spring (c)arrow_forwardPlease solve the following problem showing every single step and all the work, I'm trying to get through some good practice on these dynamics and vibrations problems while I have some time off before finals in a few weeks, need some really good help on this problem though. I really appreciate it!arrow_forward
arrow_back_ios
SEE MORE QUESTIONS
arrow_forward_ios
Recommended textbooks for you
- Elements Of ElectromagneticsMechanical EngineeringISBN:9780190698614Author:Sadiku, Matthew N. O.Publisher:Oxford University PressMechanics of Materials (10th Edition)Mechanical EngineeringISBN:9780134319650Author:Russell C. HibbelerPublisher:PEARSONThermodynamics: An Engineering ApproachMechanical EngineeringISBN:9781259822674Author:Yunus A. Cengel Dr., Michael A. BolesPublisher:McGraw-Hill Education
- Control Systems EngineeringMechanical EngineeringISBN:9781118170519Author:Norman S. NisePublisher:WILEYMechanics of Materials (MindTap Course List)Mechanical EngineeringISBN:9781337093347Author:Barry J. Goodno, James M. GerePublisher:Cengage LearningEngineering Mechanics: StaticsMechanical EngineeringISBN:9781118807330Author:James L. Meriam, L. G. Kraige, J. N. BoltonPublisher:WILEY
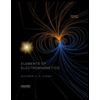
Elements Of Electromagnetics
Mechanical Engineering
ISBN:9780190698614
Author:Sadiku, Matthew N. O.
Publisher:Oxford University Press
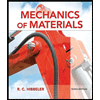
Mechanics of Materials (10th Edition)
Mechanical Engineering
ISBN:9780134319650
Author:Russell C. Hibbeler
Publisher:PEARSON
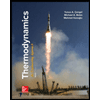
Thermodynamics: An Engineering Approach
Mechanical Engineering
ISBN:9781259822674
Author:Yunus A. Cengel Dr., Michael A. Boles
Publisher:McGraw-Hill Education
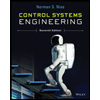
Control Systems Engineering
Mechanical Engineering
ISBN:9781118170519
Author:Norman S. Nise
Publisher:WILEY
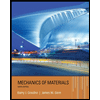
Mechanics of Materials (MindTap Course List)
Mechanical Engineering
ISBN:9781337093347
Author:Barry J. Goodno, James M. Gere
Publisher:Cengage Learning
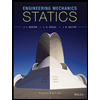
Engineering Mechanics: Statics
Mechanical Engineering
ISBN:9781118807330
Author:James L. Meriam, L. G. Kraige, J. N. Bolton
Publisher:WILEY