Group 4, Lab 10
docx
keyboard_arrow_up
School
California State University, Northridge *
*We aren’t endorsed by this school
Course
317
Subject
Mechanical Engineering
Date
Feb 20, 2024
Type
docx
Pages
10
Uploaded by moops02
Fall 2023
California State University, Northridge
Experiment 10
Dynamic Imbalance
Mechanics Lab
AM 317
Written By:
Abstract: In engineering, dynamic imbalance delves into the realm of analyzing machinery with rotation parts. Dynamic imbalance is when the mass of a rotating member in a machine is not equally distributed about the axis of rotation. This imbalance is certainly an issue to be wary of, especially with machinery that operates at high speeds. Some common devices that experience dynamic imbalance are engines, turbines, shafts, and fans. It is important to try to minimize dynamic imbalance wherever possible as it can lead to many different issues in the future if left alone.
Some things to consider when analyzing systems to find dynamic imbalances are its causes, its effects, its remedies, and its applications. There are various causes for dynamic imbalances. It could be caused by uneven material distribution when the part was manufactured or even normal wear and tear. The effects of dynamic imbalance are also numerous. Dynamic imbalances can lead to vibrations in the system which create noise, reduces the overall efficiency, and lead to increased stress on the rotating machinery. When left untreated, excessive vibration can lead to compromised safety of the system. When treating dynamic imbalance, there
are two ways to approach it. One method is static balancing, where the components are stationary and seeing where the center of mass lines up in the vertical plane. Another method is dynamic balancing where the same types of balancing techniques as static balancing are applied but, in all planes, not just the vertical plane.
We expect to see an exponential growth graph for both the experimental and theoretical values, and for the most part that is what we saw, with a small degree of error, but a consistent error, letting us know that our values were precise.
Introduction:
Dynamic imbalance is when the mass of a rotating member in a machine is not equally distributed about the axis of rotation. This imbalance is certainly an issue to be wary of, especially with machinery that operates at high speeds. Some common devices that experience dynamic imbalance are engines, turbines, shafts, and fans.
Some things to consider when analyzing systems to find dynamic imbalances are its causes, its effects, its remedies, and its applications. There are various causes for dynamic imbalances. It could be caused by uneven material distribution when the part was manufactured or even normal wear and tear. The effects of dynamic imbalance are also numerous. Dynamic imbalances can lead to vibrations in the system which create noise, reduces the overall efficiency, and lead to increased stress on the rotating machinery. When left untreated, excessive vibration can lead to compromised safety of the system. When treating dynamic imbalance, there
are two ways to approach it. One method is static balancing, where the components are stationary and seeing where the center of mass lines up in the vertical plane. Another method is dynamic balancing where the same types of balancing techniques as static balancing are applied but, in all planes, not just the vertical plane.
In this lab, using the rotor mounted in bearings, the 12” steel scale, charge amplifier, multi-meter (voltmeter), and wheel balance. Using this equipment, we hope to be able to find an exponential growth graph between the reaction force and the angular frequency.
Your preview ends here
Eager to read complete document? Join bartleby learn and gain access to the full version
- Access to all documents
- Unlimited textbook solutions
- 24/7 expert homework help
Theory:
There are a few things to know when analyzing dynamic unbalance in systems. One of which is the force that the eccentric mass gives off. This is used in order to find the maximum reaction force at the different locations on the balance wheel. Once we know that, we can do a more detailed study on systems that experience dynamic unbalance. The formula for finding the force of the eccentric mass is m, the mass of the weight, times r, the distance of the weight to the center of the shaft, times the angular velocity, also referred as angular frequency of the motor, squared, is equal to the force of the eccentric mass. The next equation that we need is the force in the y direction. These forces are the forces that act in the y plane that occur when the balance wheel is spinning. The force in the y direction is a result of the forces that the motor puts on the wheel. The equation is as follows, m, the mass of the weight, times r, the distance of the weight to the center of the shaft, times b, the distance from the bearing to the unbalanced disk, over L, the length of the shaft between the bearings, all times the angular velocity, also referred as angular frequency of the motor, squared, is equal to the peak force at the location of the force transducer. We also need to calculate the percent error between two values in order to compare the difference between the calculated value and the experimental value.
Procedures:
To begin the lab, we had to measure various dimensions of the shaft and balanced wheels.
Once those dimensions were recorded, we went on and found the balance, which consisted of a bolt, a nut, and a washer. We weighed those in ounces and recorded those values into its subsequent table. We then made sure that all the equipment was plugged into the outlet, plugged into each other, and turned on. Once we made sure of that, we were then ready to perform the actual testing for the lab.
For the first part of the lab, we placed the weight in one of the holes on the balance wheel
and set the machine to run at 700 rpm. Once we got a steady reading of force, we recorded the value into our table. There were 8 different holes throughout the balance wheel, and we repeated the steps of installing and reading the force for each hole. During this whole first process, we did not change the motor speed in order to get a consistent reading across all the holes. When looking at our table, we found one hole whose value had the highest reaction force. We took note
of the hole that experienced the highest reaction force, as we will need it for the second stage of the experiment.
For the second part of the lab, we first took out the weight from the balance wheel. We started the motor at 300 rpm’s. From there, we increased the speed by 100 rpms until we reached 700 rpms. Then, we inserted the weight back into the hole that we found the highest reaction force into and started the testing over back at 300 rpm. We found that we were getting much higher loads with the weight in compared to without the weight. Once we completed the lab, we turned off all the equipment and cleaned everything up.
Results:
Table 1: System Specifications.
Measured Data
L (in.)
11.50
b (in.) 10.00
r (in.)
4.50
m (lb-s2/in.)
0.000161825
Table 2: Reaction Force for Different Mass Locations at 700 RPM.
Hole Number
1
2
3
4
5
6
7
8
Force (lb)
2.75 3.25 3.55 3.47 3.08 2.48 2.21 2.40
Table 3: Experimental Data
FREQUENC
Y
(rpm)
FREQUENCY
ω (rad/sec)
FORCE
READINGS
w/o mass
w/ mass*
FORCE (lb)
Exp. Theory
% Error
300
31.4159265
0.6
1.09
0.5
0.62496996
13.5958477
400
41.8879021
0.6
1.6
1
1.11105771
13.5958477
500
52.3598776
0.6
2.13
1.5
1.73602768
14.1718754
600
62.8318531
0.7
2.8
2.2
2.49987986
13.9958669
700
73.3038286
0.7
3.74
3.1
3.40261425
9.18747254
800
83.7758041
0
4.44423086
100
900
94.2477796
0
5.62472968
100
1000
104.719755
0
6.94411071
100
1100
115.191731
0
8.40237396
100
1200
125.663706
0
9.99951943
100
1300
136.135682
0
11.7355471
100
1400
146.607657
0
13.610457
100
Your preview ends here
Eager to read complete document? Join bartleby learn and gain access to the full version
- Access to all documents
- Unlimited textbook solutions
- 24/7 expert homework help
Graph 1: Experimental Reaction Force vs. Angular Frequency 250
300
350
400
450
500
550
600
650
700
750
0
0.5
1
1.5
2
2.5
3
3.5
f(x) = 0.01 x − 1.5
R² = 0.98
Experimental Reaction Force vs. Angular Frequency
Angular Frequency (rpm)
Reaction Force (lb)
Graph 2: Theoretical Reaction Force vs. Angular Frequency
200
400
600
800
1000
1200
1400
1600
0
2
4
6
8
10
12
14
16
f(x) = 0.01 x − 4.19
R² = 0.97
Theoretical Reaction Force vs. Angular Frequency
Angular Frequency (rpm)
Reaction Force (lb)
Discussions and Conclusions:
There were a lot of different values that go into play when analyzing dynamic imbalance. The first things that we had to get were the system specifications, or the measurements of the system. We recorded the total length of the system, the length of the balance to the motor, the radius of the balance wheel, and the mass of the washer, bolt, and nut. These values were used to find other values later in the experiment. In Table 2, we recorded our reaction forces for different mass locations at 700 rpm instead of the recommended 900 rpm. There, we started the seeing values starting at 2.75 lb for the first hole and ended with 2.4 lb on the eighth hole. The values rose and fell, with the highest value being on the third hole that we tested. The third hole was determined to be the one that the highest reaction force occurs at. In Table 3, we recorded our calculated values and our recorded values. Using the values that we obtained in Table 1; we were able to get our values. We only performed tests from 300 rpm to 700 rpm but calculated our values from 300 rpm to 1400 rpm. We found that our forces in
theory were always slightly higher than the force that we got from experimentation, but not by a large amount, the error between the two ranged from 9.19% to 14.17%.
In Graph 1, you can see that the experimental values seem to form an exponential growth graph, had the experimentation been continued we would have seen results that would reflect a more noticeable exponential growth. In Graph 2, because we were able to calculate more values the exponential growth graph was more obvious to see.
Overall, we saw the values that we expected to see from the experiment.
Appendix:
Your preview ends here
Eager to read complete document? Join bartleby learn and gain access to the full version
- Access to all documents
- Unlimited textbook solutions
- 24/7 expert homework help
Related Documents
Related Questions
lail - Ahmed Amro Hussein Ali A x n Course: EN7919-Thermodynamic x
Homework Problerns(First Law)_S x
noodle/pluginfile.php/168549/mod_resource/content/1/Homework%20Problems%28First%20Law%29_SOLUTIONS.pdf
UTIONS.pdf
4 / 4
100%
Problem-4: When a system is taken from a state-a to a state-b,
the figure along path a-c-b, 84 kJ of heat flow into the system,
and the system does 32 kJ of work.
(i) How much will the heat that flows into the system along the
path a-d-b be, if the work done is 10.5 kJ? (Answer: 62.5 kJ)
(ii) When the system is returned from b to a along the curved path, the work done on
the system is 21 kJ. Does the system absorb or liberate heat, and how much?
(Answer:-73 k])
(iii) If Ua = 0 andU, = 42kJ , find the heat absorbed in the processes ad and db.
(Answer: 52.5 kJ, 10 kJ)
arrow_forward
A physics lab Consist of a large bowl attached to wire. Students hold onto one of the wire the whirl the ball around in circles and count the number of rotations per second. One group finds these numbers: ball mass=320g, wire length=1.3m, number of rotations/second=2.5. The wire is made of steel with a diameter of 1mm and a Young’s modulus of 20x10^10 N/m^2. How much does the wire stretch due to the tension on it? Should the students correct their data for the wire stretching?
arrow_forward
Given:
The plane accelerates in its current trajectory with a= 100 m/s^2
Farag
Angle theta= 5°
W=105 kips
F_drag= 80 kips
m= 1000 lbs
Find: F_thrust, F_lift
Please include the KD.
Fthrust
Futel t Fueight
000
BY NC SA
2013 Michael Swanbom
arrow_forward
Manufacturing process with two variables x1,x2 described by the empirical model:
y=bo +b1 x1 + b2 x2 + b12 x1 x2 + b3 (x1)^2 +b4 (x2)^2
please refere to the image attached
arrow_forward
22°F
Clear
DDÈ DDE MMMBU BU ► ► ► 2GQ==§¤¤✰=aaa=Û¤ı1 × PDF PDF PDF PDF PDE
File | C:/Users/ignor/Downloads/Assignment%203%20(2).pdf
T❘ Read aloud
Draw
Ask Copilot
a) Use Newton's second law
b) Use the Torque equation
a
Search
TWO
Particle P is sliding along a circular path of radius r . The circular path is placed on top of a
truck that is moving to the left with a velocity of v and an acceleration of a. The friction is
negligible. Find the EOM of particle P.
O
0
2
r
of 6
| CD
P
eac
СО da | +
o
ENG
60
T
6L
N
{0}
7:39 PM
1/17/2024
x
arrow_forward
is a mass hanging by a spring under the influence of gravity. The force due to gravity, Fg, is acting
in the negative-y direction. The dynamic variable is y. On the left, the system is shown without spring deflection.
On the right, at the beginning of an experiment, the mass is pushed upward (positive-y direction) by an amount y₁.
The gravitational constant g, is 9.81 m/s².
No Deflection
m
k
Fg = mg
Initial Condition
m
k
Fg = mg
Figure 3: System schematic for Problem 4.
Yi
8
Your tasks:
A Write down, in terms of the variables given, the total potential energy stored in the system when it is held in
the initial condition, relative to the system with no deflection.
B Write down an expression for the total energy H as the sum of potential and kinetic energy in terms of y, y, yi
and element parameters. Will H change as the mass moves?
C After the system is released, it will start to move. Write down an expression for the kinetic energy of the
system, T, in terms of position, y, the initial…
arrow_forward
Thermodynamics
Answer the following problem with complete solutions. Write legibly
A balloon is filled with pure oxygen at 10 ℃. The balloon is released from the bottom of a water-filled testing pool and floats 30 m to the water surface (where the atmospheric pressure is standard). The volume of the balloon is 3,000 cm^3. The temperature is 25 ℃ at the surface of the water, and the water temperature at the bottom of the pool is 10 ℃. What is the volume of the balloon at the surface after it has come into thermal equilibrium with the surroundings
arrow_forward
is a mass hanging by a spring under the influence of gravity. The force due to gravity, Fg, is acting
in the negative-y direction. The dynamic variable is y. On the left, the system is shown without spring deflection.
On the right, at the beginning of an experiment, the mass is pushed upward (positive-y direction) by an amount y₁.
The gravitational constant g, is 9.81 m/s².
DO
C.D
Frontly
у
Your tasks:
No Deflection
m
k
Fg = mg
Initial Condition
y
m
k
Write down an expression for the total energy If as the sum
Write down an expression for the total energy H
Fg = mg
Figure 3: System schematic for Problem 4.
Yi
&
X
Write down, in terms of the variables given, the total potential energy stored in the system when it is held in
the initial condition, relative to the system with no deflection.
as the sum of potential and kinetic energy in terms of y, y, yi
C After the system is released, it will start to move. Write down an expression for the kinetic energy of the
system, T, in terms of…
arrow_forward
22°F
Clear
1MMBU BU ► ► ► 20°HD®°°*EqqaHÛDin × ODE DDE DE DE
File C:/Users/ignor/Downloads/Assignment%203%20(2).pdf
T❘ Read aloud Ask Copilot
Draw
a) Use Newton's second law
b) Use the Torque equation
///
Collar A is free to slide with negligible friction on the circular guide mounted in a vertical frame.
Find the EOM of collar A if the frame is given a velocity v and a constant horizontal acceleration
a to the right.
Search
1
A
www
of 6
TTTT
| CD
a
laaa
8
o
+
ENG
60
T
N
7:35 PM
1/17/2024
x
arrow_forward
dated metncpdf
Thermodynamics An Engineering X
E Module2-chap2propertiesofpure x
O File
C:/Users/DANIEL/Desktop/300L%202ND%20SEMESTER%20MATERIALS/Module2-chap2propertiesofpuresubstances-130703012604 phpap.
ID Page view
A Read aloud
V Draw
H Highlight
O Erase
40
MEC 451 - THERMODYNAMICS
Faculty of Mechanical Engineering, UITM
Supplementary Problems
The pressure in an automobile tire depends on the temperature of the air
in the tire. When the air temperature is 25°C, the pressure gage reads 210
kRa. If the volume of the tire is 0.025 m3, Cetermine the pressure rise in
the tire when the air temperature in the tire rises to 50°C. Also, determine
the amount of air that must be bled off to restore pressure to its original
value at this temperature. Assume the atmospheric pressure is 100 kPa.
[ 26 kPa, 0.007 kg]
1.
A 6 4 2:57 PM
Lucky CORER
144
Tum lock
314
%
8
1/2
24
6
1/4
23
T
K
F
pause
B
arrow_forward
23:38 Fri 22 Jul
Q6.
4 of 6
Q6. Cont.
library.qol.qub.ac.uk - Private
Q7.
An engineer is designing a pressure vessel, and selects an initial concept design consisting of a
cylinder or length L, and radius r, both measured in metres, as shown in figure Q6. The volume
of the vessel should be 1200 litres. The wall of the vessel will be a constant thickness throughout.
The engineer wants to minimise the amount of material used in order to minimise the cost.
4% 1
[1 marks]
Figure Q6
(a) Determine expressions for the surface area and the volume of the tank in
L. Hence find an expression for surface area in terms of r only.
Q6. Cont./
MEE1001/2021
rms of r and
[4 marks]
(b) Determine the combination of radius and length that will require the minimum amount of
material to be used. You should use an appropriate method to verify that it is a minimum.
[10 marks]
arrow_forward
Help please I'm stuck on these two problems.
arrow_forward
Anasayfam Ders Kataloğu ME2005 54954 ME 2005 Dynamics- Midterm Exam 05.12.2020 @18:00 KTÜ Department of Mechanical Engineering Fall 2020 ME 2005 Dynamics Midterm Exam
01
Genel
Önceki Etkinlik
7.
Lecture 1 (08.10 2020)
2.
Lecture 2 (15,10.2020)
Lecture 3 (22.10.2020)
Soru 10
If the motion of one particle is dependent on that of another particle, each coordinate axis system for the particles
3.
Lecture 4 (05.11.2020)
Cevap kaydedildi
Lütfen birini seçin:
4.
3,00 üzerinden
a. should have the same origin.
Make-up Lecture- Lectu
işaretlenmiş
b. None
6 Lecture 6 (12.11.2020)
P Soruyu işaretle
c. can be directed anywhere,
7.
Lecture 7 (19.11.2020)
d. should be directed along the path of motion.
Lecture 8 (25.11 2020)
O e. should be directed perpendicular to the path of motion.
9.
Lecture 9 (26.11.2020)
10 Lecture 10 (27.11.2020)
Önceki sayfa
11 ME 2005 Dynamics-M
Sonraki sayfa
O KTU Department of
arrow_forward
Return to
Required information
Sometimes equations can be developed and practical problems solved by knowing nothing more than the dimensions of
the key parameters. For example, consider the heat loss through a window in a building. Window efficiency is rated in
terms of R value, which has the unit of ft2-hr-F/Btu. A certain manufacturer offers a double-pane window with R=2.5 and
also a triple-pane window with R=3.4. Both windows are 3.5 ft by 5 ft. On a given winter day, the temperature difference
between the inside and outside is 45°F.
Assume that a homeowner buys 20 such triple-pane windows for the house. A typical winter equals about 120 heating days at AT =
45°F. Each triple-pane window costs $85 more than a double-pane window. Ignoring interest and inflation, how many years will it take
the homeowner to make up the additional cost of the triple-pane windows from heating bill savings?
9.5 years
S
MacBook Air
!
arrow_forward
SEE MORE QUESTIONS
Recommended textbooks for you
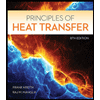
Principles of Heat Transfer (Activate Learning wi...
Mechanical Engineering
ISBN:9781305387102
Author:Kreith, Frank; Manglik, Raj M.
Publisher:Cengage Learning
Related Questions
- lail - Ahmed Amro Hussein Ali A x n Course: EN7919-Thermodynamic x Homework Problerns(First Law)_S x noodle/pluginfile.php/168549/mod_resource/content/1/Homework%20Problems%28First%20Law%29_SOLUTIONS.pdf UTIONS.pdf 4 / 4 100% Problem-4: When a system is taken from a state-a to a state-b, the figure along path a-c-b, 84 kJ of heat flow into the system, and the system does 32 kJ of work. (i) How much will the heat that flows into the system along the path a-d-b be, if the work done is 10.5 kJ? (Answer: 62.5 kJ) (ii) When the system is returned from b to a along the curved path, the work done on the system is 21 kJ. Does the system absorb or liberate heat, and how much? (Answer:-73 k]) (iii) If Ua = 0 andU, = 42kJ , find the heat absorbed in the processes ad and db. (Answer: 52.5 kJ, 10 kJ)arrow_forwardA physics lab Consist of a large bowl attached to wire. Students hold onto one of the wire the whirl the ball around in circles and count the number of rotations per second. One group finds these numbers: ball mass=320g, wire length=1.3m, number of rotations/second=2.5. The wire is made of steel with a diameter of 1mm and a Young’s modulus of 20x10^10 N/m^2. How much does the wire stretch due to the tension on it? Should the students correct their data for the wire stretching?arrow_forwardGiven: The plane accelerates in its current trajectory with a= 100 m/s^2 Farag Angle theta= 5° W=105 kips F_drag= 80 kips m= 1000 lbs Find: F_thrust, F_lift Please include the KD. Fthrust Futel t Fueight 000 BY NC SA 2013 Michael Swanbomarrow_forward
- Manufacturing process with two variables x1,x2 described by the empirical model: y=bo +b1 x1 + b2 x2 + b12 x1 x2 + b3 (x1)^2 +b4 (x2)^2 please refere to the image attachedarrow_forward22°F Clear DDÈ DDE MMMBU BU ► ► ► 2GQ==§¤¤✰=aaa=Û¤ı1 × PDF PDF PDF PDF PDE File | C:/Users/ignor/Downloads/Assignment%203%20(2).pdf T❘ Read aloud Draw Ask Copilot a) Use Newton's second law b) Use the Torque equation a Search TWO Particle P is sliding along a circular path of radius r . The circular path is placed on top of a truck that is moving to the left with a velocity of v and an acceleration of a. The friction is negligible. Find the EOM of particle P. O 0 2 r of 6 | CD P eac СО da | + o ENG 60 T 6L N {0} 7:39 PM 1/17/2024 xarrow_forwardis a mass hanging by a spring under the influence of gravity. The force due to gravity, Fg, is acting in the negative-y direction. The dynamic variable is y. On the left, the system is shown without spring deflection. On the right, at the beginning of an experiment, the mass is pushed upward (positive-y direction) by an amount y₁. The gravitational constant g, is 9.81 m/s². No Deflection m k Fg = mg Initial Condition m k Fg = mg Figure 3: System schematic for Problem 4. Yi 8 Your tasks: A Write down, in terms of the variables given, the total potential energy stored in the system when it is held in the initial condition, relative to the system with no deflection. B Write down an expression for the total energy H as the sum of potential and kinetic energy in terms of y, y, yi and element parameters. Will H change as the mass moves? C After the system is released, it will start to move. Write down an expression for the kinetic energy of the system, T, in terms of position, y, the initial…arrow_forward
- Thermodynamics Answer the following problem with complete solutions. Write legibly A balloon is filled with pure oxygen at 10 ℃. The balloon is released from the bottom of a water-filled testing pool and floats 30 m to the water surface (where the atmospheric pressure is standard). The volume of the balloon is 3,000 cm^3. The temperature is 25 ℃ at the surface of the water, and the water temperature at the bottom of the pool is 10 ℃. What is the volume of the balloon at the surface after it has come into thermal equilibrium with the surroundingsarrow_forwardis a mass hanging by a spring under the influence of gravity. The force due to gravity, Fg, is acting in the negative-y direction. The dynamic variable is y. On the left, the system is shown without spring deflection. On the right, at the beginning of an experiment, the mass is pushed upward (positive-y direction) by an amount y₁. The gravitational constant g, is 9.81 m/s². DO C.D Frontly у Your tasks: No Deflection m k Fg = mg Initial Condition y m k Write down an expression for the total energy If as the sum Write down an expression for the total energy H Fg = mg Figure 3: System schematic for Problem 4. Yi & X Write down, in terms of the variables given, the total potential energy stored in the system when it is held in the initial condition, relative to the system with no deflection. as the sum of potential and kinetic energy in terms of y, y, yi C After the system is released, it will start to move. Write down an expression for the kinetic energy of the system, T, in terms of…arrow_forward22°F Clear 1MMBU BU ► ► ► 20°HD®°°*EqqaHÛDin × ODE DDE DE DE File C:/Users/ignor/Downloads/Assignment%203%20(2).pdf T❘ Read aloud Ask Copilot Draw a) Use Newton's second law b) Use the Torque equation /// Collar A is free to slide with negligible friction on the circular guide mounted in a vertical frame. Find the EOM of collar A if the frame is given a velocity v and a constant horizontal acceleration a to the right. Search 1 A www of 6 TTTT | CD a laaa 8 o + ENG 60 T N 7:35 PM 1/17/2024 xarrow_forward
- dated metncpdf Thermodynamics An Engineering X E Module2-chap2propertiesofpure x O File C:/Users/DANIEL/Desktop/300L%202ND%20SEMESTER%20MATERIALS/Module2-chap2propertiesofpuresubstances-130703012604 phpap. ID Page view A Read aloud V Draw H Highlight O Erase 40 MEC 451 - THERMODYNAMICS Faculty of Mechanical Engineering, UITM Supplementary Problems The pressure in an automobile tire depends on the temperature of the air in the tire. When the air temperature is 25°C, the pressure gage reads 210 kRa. If the volume of the tire is 0.025 m3, Cetermine the pressure rise in the tire when the air temperature in the tire rises to 50°C. Also, determine the amount of air that must be bled off to restore pressure to its original value at this temperature. Assume the atmospheric pressure is 100 kPa. [ 26 kPa, 0.007 kg] 1. A 6 4 2:57 PM Lucky CORER 144 Tum lock 314 % 8 1/2 24 6 1/4 23 T K F pause Barrow_forward23:38 Fri 22 Jul Q6. 4 of 6 Q6. Cont. library.qol.qub.ac.uk - Private Q7. An engineer is designing a pressure vessel, and selects an initial concept design consisting of a cylinder or length L, and radius r, both measured in metres, as shown in figure Q6. The volume of the vessel should be 1200 litres. The wall of the vessel will be a constant thickness throughout. The engineer wants to minimise the amount of material used in order to minimise the cost. 4% 1 [1 marks] Figure Q6 (a) Determine expressions for the surface area and the volume of the tank in L. Hence find an expression for surface area in terms of r only. Q6. Cont./ MEE1001/2021 rms of r and [4 marks] (b) Determine the combination of radius and length that will require the minimum amount of material to be used. You should use an appropriate method to verify that it is a minimum. [10 marks]arrow_forwardHelp please I'm stuck on these two problems.arrow_forward
arrow_back_ios
SEE MORE QUESTIONS
arrow_forward_ios
Recommended textbooks for you
- Principles of Heat Transfer (Activate Learning wi...Mechanical EngineeringISBN:9781305387102Author:Kreith, Frank; Manglik, Raj M.Publisher:Cengage Learning
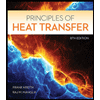
Principles of Heat Transfer (Activate Learning wi...
Mechanical Engineering
ISBN:9781305387102
Author:Kreith, Frank; Manglik, Raj M.
Publisher:Cengage Learning