Group 4, Lab 6
docx
keyboard_arrow_up
School
California State University, Northridge *
*We aren’t endorsed by this school
Course
317
Subject
Mechanical Engineering
Date
Feb 20, 2024
Type
docx
Pages
15
Uploaded by moops02
Fall 2023
California State University, Northridge
Experiment 6
Springs in Series and Parallel
Mechanics Lab
AM 317
Written By:
Abstract:
Understanding springs is imperative for engineers because they can release and store energy. There are three types of spring loadings that engineers must understand, those are series, parallel, and a combination of both. These different loading cases are used in different applications, so it is important that an engineer understands all of them to properly account for the situation.
Springs in series store energy independently. The way that springs are loaded in series gives it an effective stiffness that is overall reduced. This configuration is useful when the goal is
to produce a system that can take into account sharp movements. An example of this is the suspensions of a car. The springs in the car’s suspension act to counter the bumps in the road. Springs in parallel story energy in redundancy. The way that the springs are loaded in parallel allows each spring to bear a portion of the load. This configuration is useful when load distribution in a system is desired over the ability to account for sharp movements. An example of springs in parallel is anti-vibration mounts. The springs act in parallel in order to reduce the amount of movement that the system experiences. Some things that we expect to see in this lab is a linear relationship between deflection and load for all the singular spring loading cases. As for the more intricate loading cases we expect to see effective spring constants similar to what we calculate for them in the later theory section of the lab.
For the most part we saw a perfect linear relationship for all the singular spring loading cases as well as for the series and balanced parallel loading cases. We did see different behavior
for the unbalanced parallel loading case and for the series and parallel loading which we concluded came from the springs not completely coming into contact with the bars as more and more springs were added to the system.
Your preview ends here
Eager to read complete document? Join bartleby learn and gain access to the full version
- Access to all documents
- Unlimited textbook solutions
- 24/7 expert homework help
Introduction:
The lab this week seeks to introduce us to the concept of springs, spring constants, springs in series, springs in parallel, and a combination of the two. These conditions need to be known by an engineer that is working with springs because springs behave in different ways depending on how the springs are loaded.
Individual springs are the most simple type of loading condition. Individual springs only have one formula to work with and only have one spring constant to be wary of. Individual springs make up parts of other spring systems like series and parallel and bring their spring constants to the greater system. Springs in series is a slightly more complicated loading condition. Series springs store energy independently and the overall stiffness is reduced. These are good in applications where springs are used to absorb sudden forces like the suspensions on a car. The springs’ stiffness is reduced in order to reduce the bumpiness felt by the driver of the car.
Springs in parallel are another loading condition. The energy stored in parallel springs is distributed amongst all the springs in the system. These are good in applications where a larger force acts on the system and the springs can more effectively reduce the force, take for example the earthquake protection you see on large buildings in California. The large springs at the base are used to counteract the motion of the earthquake.
The things we are using in the lab to test spring loading conditions are a steel frame to hang the springs from, the springs, hooks, and aluminum bars in order to hold the springs to the steel frame, and a ruler to measure the displacement of the springs as loads are applied.
Theory:
Springs are devices that can store and release energy. They have different behaviors depending on how the springs are arranged, their spring constants, and their positioning. Springs are used in a wide array of applications, so knowing these properties is very important for engineers. There are three types of spring loadings, series, parallel, and a combination of both. Springs connected in series share the same force or load. Effectively, the spring constant is reduced compared to an individual spring’s spring constant. Springs connected in parallel share the total force. Effectively, the springs distribute the load that is applied on them. In either case, the spring constant can be determined with the following use of Hooke’s Law, where F, the applied force, is equal to ∆
, the resulting displacement, times k, the spring constant. F
=
∆ k
The different arrangements of springs warrant different equations to find the equivalent spring constant, k
eq
. One of the cases we will be testing is of two springs attached at each other’s ends. This arrangement is a series arrangement. The k
eq
calculation for this arrangement is as shown, where the different k values indicate springs if different spring constants.
k
eq
=
1
1
k
1
+
1
k
2
The next case that we wanted to test was when the springs were loaded in parallel. To do this, attached two springs of different constants to a bar and proceeded with loading weight on them. The spring constant calculation is as follows.
k
eq
=
k
1
+
k
2
The next case was similar to the previous case, except the loading was unbalanced, meaning that the springs were unevenly spaced from the center. This equation has 3 new variables, L, which is the vertical length of the loading bar between the springs, a, which is the vertical distance between the left springs and the weight, and b, which is the vertical distance between the weight and the right spring. k
eq
=
L
2
b
2
k
1
+
a
2
k
2
The last case that we tested was a combination of series and parallel. It used 2 loading bars and 2 sets of 2 springs that had similar spring constants, and 1 with a different spring constant. The formula for calculating the spring constant for that case is as follows. k
eq
=
1
1
k
1
+
k
2
+
k
1
+
1
k
3
+
k
3
Your preview ends here
Eager to read complete document? Join bartleby learn and gain access to the full version
- Access to all documents
- Unlimited textbook solutions
- 24/7 expert homework help
Procedures:
The procedures of the lab were quite repetitive for the initial identification but were necessary for the later part of the lab. For the lab, we gathered 7 different springs from the box in order to start testing. In order to test the springs, we laid them in order right to left. There is no definite way that the lab has us order them in, so long as we can keep track of them throughout the experiment. To start the test, we attached a hook to the top of the steel frame so that we can attach the spring easier. We then attached the spring to the hook and the weight pan to the bottom of the spring. When we loaded the springs, we had to make sure that the springs could experience a dead load, meaning that the spring would slightly stretch, enough to be visibly seen. This ensures that the spring will decompress as weight is added so we can calculate the spring constant. During testing we found several springs that had gone past elastic deformation and had experienced plastic deformation. When we encountered springs like this, we dug through the box and found a suitable replacement. Once the dead load was taken account of, we slowly added more and more weight until we had 4 readings to find the spring constant with. Once we had the measurements, we moved onto the next portion of the lab.
The next portion of the lab builds on the first half with more variables. We first attached a
bar with hooks to two springs that had equal spring constants. Referring to the previous table we were able to find two springs that were equal spring constants and place them on either side. For the next test, we repeated the previous steps but instead of having 2 springs that had the same constant, we made sure that the springs had different spring constants. For the third and final test,
we constructed a system that had 2 sets of springs that had similar spring constants and 1 that
was different from the rest. We arranged them so in series and parallel so that on the first row, 2 springs that had the same spring constant would surround 1 spring that had a different spring constant and the second row would have two springs of equal spring constant, with the weight pan at the bottom of the whole system. As always, we found the dead load and added weight in 4 equal increments after the dead load was reached.
Results:
Spring #
Initial
Position (in)
Force (lb)
Reading (in)
Deflection (in)
Preload
(lb)
k
(lb/in)
1
11.9
1
12.2
0.3
1
2.9437
2294
2
12.6
0.7
3
13
1.1
4
13.3
1.4
2
11.8
1
12.2
0.4
2
2.6877
7056
2
12.5
0.7
3
12.9
1.1
4
13.3
1.5
3
12.5
1
13.1
0.6
2
1.6666
6667
2
13.7
1.2
3
14.3
1.8
4
14.9
2.4
4
12.8
1
13.5
0.7
2
1.6071
4286
2
14
1.2
3
14.6
1.8
4
15.2
2.4
5
11.9
1
12.1
0.2
5
5.6071
4286
2
12.25
0.35
3
12.4
0.5
4
12.6
0.7
6
15
1
15.2
0.2
5
5
2
15.4
0.4
3
15.6
0.6
4
15.8
0.8
7
13.3
1
13.9
0.6
1
1.5466
5242
2
14.6
1.3
3
15.3
2
4
16
2.7
Table 1: Spring Data
Your preview ends here
Eager to read complete document? Join bartleby learn and gain access to the full version
- Access to all documents
- Unlimited textbook solutions
- 24/7 expert homework help
Graph 1: Spring 1, Deflection versus load.
0.2
0.4
0.6
0.8
1
1.2
1.4
1.6
0
0.5
1
1.5
2
2.5
3
3.5
4
4.5
f(x) = 2.69 x + 0.15
R² = 1
Spring 1 (preload 1lb)
Load (lb.)
Defelction (in.)
Graph 2: Spring 2, Deflection versus load.
0.2
0.4
0.6
0.8
1
1.2
1.4
1.6
0
0.5
1
1.5
2
2.5
3
3.5
4
4.5
f(x) = 2.69 x + 0.01
R² = 1
Spring 2 (preload 2 lb)
Graph 3: Spring 3, Deflection versus load.
0.5
1
1.5
2
2.5
0
0.5
1
1.5
2
2.5
3
3.5
4
4.5
f(x) = 1.67 x
R² = 1
Spring 3 (preload 2lb)
Graph 4: Spring 4, Deflection versus load.
0.6
0.8
1
1.2
1.4
1.6
1.8
2
2.2
2.4
2.6
0
0.5
1
1.5
2
2.5
3
3.5
4
4.5
f(x) = 1.75 x − 0.17
R² = 1
Spring 4 (preload 2lb)
Graph 5: Spring 5, Deflection versus load.
0.1
0.2
0.3
0.4
0.5
0.6
0.7
0.8
0
0.5
1
1.5
2
2.5
3
3.5
4
4.5
f(x) = 6.03 x − 0.14
R² = 0.99
Spring 5 (preload 5lb)
Graph 6: Spring 6, Deflection versus load.
0.1
0.2
0.3
0.4
0.5
0.6
0.7
0.8
0.9
0
0.5
1
1.5
2
2.5
3
3.5
4
4.5
f(x) = 5 x
R² = 1
Spring 6 (preload 5lb)
Graph 7: Spring 7, Deflection versus load.
0
0.5
1
1.5
2
2.5
3
0
0.5
1
1.5
2
2.5
3
3.5
4
4.5
f(x) = 1.43 x + 0.14
R² = 1
Spring 7 (preload 1lb)
Table 2: Measured Data
Spring
System
Initial
Position
(in)
Force
(lb)
Reading
(in)
Deflection
(in)
Preload
(lb)
Measure
d
k (lb/in)
Calculated
K (lb/in.)
Series
15.6
1
16.3
0.7
2
1.443729
1.401993
2
16.9
1.3
3
17.7
2.1
4
18.5
2.9
Parallel
Balanced
6.9
1
7.2
0.3
4
3.333333
3.274
2
7.5
0.6
3
7.8
0.9
4
8.1
1.2
Parallel
Unbalanced
6.6
1
6.7
0.1
7
10
5.170214
2
6.8
0.2
3
6.9
0.3
4
7
0.4
Series and
Parallel
4.8
1
5.1
0.3
7
3.214286
2.535161
2
5.4
0.6
3
5.7
0.9
4
6.2
1.4
Your preview ends here
Eager to read complete document? Join bartleby learn and gain access to the full version
- Access to all documents
- Unlimited textbook solutions
- 24/7 expert homework help
Discussion and Conclusions:
The results that we saw from this week’s lab were similar in some ways to what we expected to see but differed in a few major ways. For table 1, we first took note of which spring was which, making sure that we did not mix them up while we were testing the original spring constant. We took note of the initial position using a ruler that was mounted along the side of the frame. We took note of the preloading condition and the readings we got from each additional pound added to the spring. Using that, we were able to calculate the spring constants for each of the springs.
For graphs 1 to 7, we plotted the deflection versus the load for each of the 7 springs that we tested. As you can see from the data, most of the graphs had a perfect linear growth, just as we expected to observe. Others that were not an exact regression analysis of 1 were very close to
1. For the different cases of series, balanced parallel, unbalanced parallel, and series and parallel, we got mixed results. For the springs loaded in series and balanced parallel, we got observed values that were close to the calculated values. For the unbalanced parallel and the series and parallel loading cases, we observed values that were very different from the values that we calculated. When investigating why this may be the case, we took note that all the springs in the later configurations did not always contract when the load was applied. Sometimes
the springs on the ends would contract first while springs in the middle of the arrangement wouldn’t compress. Knowing this, this should account for the disparity that we saw in the loading conditions that use multiple springs of different spring constants.
Appendix:
Your preview ends here
Eager to read complete document? Join bartleby learn and gain access to the full version
- Access to all documents
- Unlimited textbook solutions
- 24/7 expert homework help
Related Documents
Related Questions
PHYS X PHYS X
印 PHYS X
PHYS X
POTPHYS X
PHYS X
E PHYS X E PHYS
top/semester2/physics%20for%20engineers/PHYS220_CH15_Lecture%20Notes_Problems%2015 19,15.29 S
(D Page view
A Read aloud
V Draw
Problem-15-19: page-475
A 0.500-kg object attached to a spring with a force constant of 8.00 N/m vibrates in simple harmonic motion
with an amplitude of 10.0 cm. Calculate the maximum value of its
(a) speed, and acceleration.
(b) the speed and the acceleration when the object is 6.00 em from the equilibrium position, and
(c) the time interval required for the object to move from.r50 to r5 8.O0 cm.
Solution:
arrow_forward
account_circle
Science
PhysicsQ&A LibraryA child’s toy consists of a m = 31 g monkey suspended from a spring of negligible mass and spring constant k. When the toy monkey is first hung on the spring and the system reaches equilibrium, the spring has stretched a distance of x = 17.6 cm, as shown in the diagram. This toy is so adorable you pull the monkey down an additional d = 7.6 cm from equilibrium and release it from rest, and smile with delight as it bounces playfully up and down. 1. Calculate the speed of the monkey, ve, in meters per second, as it passes through equilibrium. 2. Derive an expression for the total mechanical energy of the system as the monkey reaches the top of the motion, Etop, in terms of m, x, d, k, the maximum height above the bottom of the motion, hmax, and the variables available in the palette. 3. Calculate the maximum displacement, h, in centimeters, above the equilibrium position, that the monkey reaches.
A child’s toy consists of a…
arrow_forward
Physics 121 Spring 2021 - Document #11: Homework #04 & Reading Assignment page 4 of 8
Problem 1: Gnome Ride - This from a Previous Exam
I.
A Gnome of given mass M goes on the Gnome Ride as follows: He stands on a horizontal
platform that is connected to a large piston so that the platform is driven vertically with a position
as a function of time according to the following equation:
y(t) = C cos(wt)
Here w is a constant given angular frequency, C is a given constant (with appropriate physical
units) and y represents the vertical position, positive upward as indicated.
Part (a) - What is the velocity of the Gnome at time t = 0? Explain your work. Present your
answer in terms of the given parameters
Part (b) – What is the net force on the Gnome at time t = 0? Explain your work. Present your
answer in terms of the given parameters
Part (c) – What is the Normal Force on the Gnome at time t = 0? Explain your work. Present
your answer in terms of the given parameters
Some Possibly Useful…
arrow_forward
i just need part 3
arrow_forward
Hello Good Evening Sir,I have a question in my homework related structural mechanics lesson. The following below is my question. Please advice. Thank you so much
Regards,
Yusuf
arrow_forward
Q1 A and B
arrow_forward
1. The development of thermodynamics since the 17th century, which was pioneered by the invention of the steam engine in England, and was followed by thermodynamic scientists such as Willian Rankine, Rudolph Clausius, and Lord Kelvin in the 19th century. explain what the findings or theories of the 3 inventors are!
Please answer fast max 25-30.minutes thank u
arrow_forward
Q1 please
arrow_forward
Question 1b
arrow_forward
Why differential equations and matlab important in engineering study
arrow_forward
62. •A 5-kg object is constrained to move along a straight
line. Its initial speed is 12 m/s in one direction, and its final
speed is 8 m/s in the
opposite
Complete the graph of
force versus time with
direction.
F (N)
(s)
appropriate values for
both variables (Figure
7-26). Several answers
are correct, just be sure
that your answer is
internally consistent.
Figure 7-26 Problem 62
arrow_forward
Thermodynamics
Please READ THE PROBLEM! I’m tired of posting the same problem over and over. please Read.
This is what the asking for please:
-1. sketch and label all your answers on the nozzle
-2. Sketch and label all your answers on the process on a P-V diagram....
Thank you
arrow_forward
C
Dynamic Analysis and Aeroelasticity
SECTION B
Answer TWO questions from this section
ENG2012-N
The moment of inertia of a helicopter's rotor is 320kg. m². The rotor starts from rest
and at t = 0, the pilot begins by advancing the throttle so that the torque exerted on
the rotor by the engine (in N.m) is modelled by as a function of time (in seconds) by
T = 250t.
a) How long does it take the rotor to turn ten revolutions?
b) What is the rotor's angular velocity (in RPM) when it has turned ten
revolutions?
arrow_forward
22°F
Clear
1MMBU BU ► ► ► 20°HD®°°*EqqaHÛDin × ODE DDE DE DE
File C:/Users/ignor/Downloads/Assignment%203%20(2).pdf
T❘ Read aloud Ask Copilot
Draw
a) Use Newton's second law
b) Use the Torque equation
///
Collar A is free to slide with negligible friction on the circular guide mounted in a vertical frame.
Find the EOM of collar A if the frame is given a velocity v and a constant horizontal acceleration
a to the right.
Search
1
A
www
of 6
TTTT
| CD
a
laaa
8
o
+
ENG
60
T
N
7:35 PM
1/17/2024
x
arrow_forward
is a mass hanging by a spring under the influence of gravity. The force due to gravity, Fg, is acting
in the negative-y direction. The dynamic variable is y. On the left, the system is shown without spring deflection.
On the right, at the beginning of an experiment, the mass is pushed upward (positive-y direction) by an amount y₁.
The gravitational constant g, is 9.81 m/s².
DO
C.D
Frontly
у
Your tasks:
No Deflection
m
k
Fg = mg
Initial Condition
y
m
k
Write down an expression for the total energy If as the sum
Write down an expression for the total energy H
Fg = mg
Figure 3: System schematic for Problem 4.
Yi
&
X
Write down, in terms of the variables given, the total potential energy stored in the system when it is held in
the initial condition, relative to the system with no deflection.
as the sum of potential and kinetic energy in terms of y, y, yi
C After the system is released, it will start to move. Write down an expression for the kinetic energy of the
system, T, in terms of…
arrow_forward
Please show everything step by step in simplest form.
Please provide the right answer exactly as per the Question.
Please go through the Question very accurately.
arrow_forward
the question is in the picture
arrow_forward
SEE MORE QUESTIONS
Recommended textbooks for you
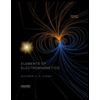
Elements Of Electromagnetics
Mechanical Engineering
ISBN:9780190698614
Author:Sadiku, Matthew N. O.
Publisher:Oxford University Press
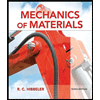
Mechanics of Materials (10th Edition)
Mechanical Engineering
ISBN:9780134319650
Author:Russell C. Hibbeler
Publisher:PEARSON
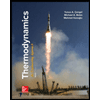
Thermodynamics: An Engineering Approach
Mechanical Engineering
ISBN:9781259822674
Author:Yunus A. Cengel Dr., Michael A. Boles
Publisher:McGraw-Hill Education
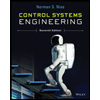
Control Systems Engineering
Mechanical Engineering
ISBN:9781118170519
Author:Norman S. Nise
Publisher:WILEY
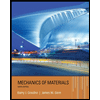
Mechanics of Materials (MindTap Course List)
Mechanical Engineering
ISBN:9781337093347
Author:Barry J. Goodno, James M. Gere
Publisher:Cengage Learning
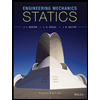
Engineering Mechanics: Statics
Mechanical Engineering
ISBN:9781118807330
Author:James L. Meriam, L. G. Kraige, J. N. Bolton
Publisher:WILEY
Related Questions
- PHYS X PHYS X 印 PHYS X PHYS X POTPHYS X PHYS X E PHYS X E PHYS top/semester2/physics%20for%20engineers/PHYS220_CH15_Lecture%20Notes_Problems%2015 19,15.29 S (D Page view A Read aloud V Draw Problem-15-19: page-475 A 0.500-kg object attached to a spring with a force constant of 8.00 N/m vibrates in simple harmonic motion with an amplitude of 10.0 cm. Calculate the maximum value of its (a) speed, and acceleration. (b) the speed and the acceleration when the object is 6.00 em from the equilibrium position, and (c) the time interval required for the object to move from.r50 to r5 8.O0 cm. Solution:arrow_forwardaccount_circle Science PhysicsQ&A LibraryA child’s toy consists of a m = 31 g monkey suspended from a spring of negligible mass and spring constant k. When the toy monkey is first hung on the spring and the system reaches equilibrium, the spring has stretched a distance of x = 17.6 cm, as shown in the diagram. This toy is so adorable you pull the monkey down an additional d = 7.6 cm from equilibrium and release it from rest, and smile with delight as it bounces playfully up and down. 1. Calculate the speed of the monkey, ve, in meters per second, as it passes through equilibrium. 2. Derive an expression for the total mechanical energy of the system as the monkey reaches the top of the motion, Etop, in terms of m, x, d, k, the maximum height above the bottom of the motion, hmax, and the variables available in the palette. 3. Calculate the maximum displacement, h, in centimeters, above the equilibrium position, that the monkey reaches. A child’s toy consists of a…arrow_forwardPhysics 121 Spring 2021 - Document #11: Homework #04 & Reading Assignment page 4 of 8 Problem 1: Gnome Ride - This from a Previous Exam I. A Gnome of given mass M goes on the Gnome Ride as follows: He stands on a horizontal platform that is connected to a large piston so that the platform is driven vertically with a position as a function of time according to the following equation: y(t) = C cos(wt) Here w is a constant given angular frequency, C is a given constant (with appropriate physical units) and y represents the vertical position, positive upward as indicated. Part (a) - What is the velocity of the Gnome at time t = 0? Explain your work. Present your answer in terms of the given parameters Part (b) – What is the net force on the Gnome at time t = 0? Explain your work. Present your answer in terms of the given parameters Part (c) – What is the Normal Force on the Gnome at time t = 0? Explain your work. Present your answer in terms of the given parameters Some Possibly Useful…arrow_forward
- 1. The development of thermodynamics since the 17th century, which was pioneered by the invention of the steam engine in England, and was followed by thermodynamic scientists such as Willian Rankine, Rudolph Clausius, and Lord Kelvin in the 19th century. explain what the findings or theories of the 3 inventors are! Please answer fast max 25-30.minutes thank uarrow_forwardQ1 pleasearrow_forwardQuestion 1barrow_forward
- Why differential equations and matlab important in engineering studyarrow_forward62. •A 5-kg object is constrained to move along a straight line. Its initial speed is 12 m/s in one direction, and its final speed is 8 m/s in the opposite Complete the graph of force versus time with direction. F (N) (s) appropriate values for both variables (Figure 7-26). Several answers are correct, just be sure that your answer is internally consistent. Figure 7-26 Problem 62arrow_forwardThermodynamics Please READ THE PROBLEM! I’m tired of posting the same problem over and over. please Read. This is what the asking for please: -1. sketch and label all your answers on the nozzle -2. Sketch and label all your answers on the process on a P-V diagram.... Thank youarrow_forward
arrow_back_ios
SEE MORE QUESTIONS
arrow_forward_ios
Recommended textbooks for you
- Elements Of ElectromagneticsMechanical EngineeringISBN:9780190698614Author:Sadiku, Matthew N. O.Publisher:Oxford University PressMechanics of Materials (10th Edition)Mechanical EngineeringISBN:9780134319650Author:Russell C. HibbelerPublisher:PEARSONThermodynamics: An Engineering ApproachMechanical EngineeringISBN:9781259822674Author:Yunus A. Cengel Dr., Michael A. BolesPublisher:McGraw-Hill Education
- Control Systems EngineeringMechanical EngineeringISBN:9781118170519Author:Norman S. NisePublisher:WILEYMechanics of Materials (MindTap Course List)Mechanical EngineeringISBN:9781337093347Author:Barry J. Goodno, James M. GerePublisher:Cengage LearningEngineering Mechanics: StaticsMechanical EngineeringISBN:9781118807330Author:James L. Meriam, L. G. Kraige, J. N. BoltonPublisher:WILEY
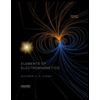
Elements Of Electromagnetics
Mechanical Engineering
ISBN:9780190698614
Author:Sadiku, Matthew N. O.
Publisher:Oxford University Press
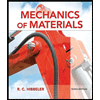
Mechanics of Materials (10th Edition)
Mechanical Engineering
ISBN:9780134319650
Author:Russell C. Hibbeler
Publisher:PEARSON
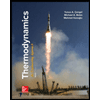
Thermodynamics: An Engineering Approach
Mechanical Engineering
ISBN:9781259822674
Author:Yunus A. Cengel Dr., Michael A. Boles
Publisher:McGraw-Hill Education
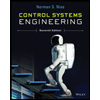
Control Systems Engineering
Mechanical Engineering
ISBN:9781118170519
Author:Norman S. Nise
Publisher:WILEY
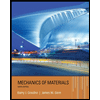
Mechanics of Materials (MindTap Course List)
Mechanical Engineering
ISBN:9781337093347
Author:Barry J. Goodno, James M. Gere
Publisher:Cengage Learning
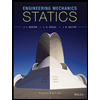
Engineering Mechanics: Statics
Mechanical Engineering
ISBN:9781118807330
Author:James L. Meriam, L. G. Kraige, J. N. Bolton
Publisher:WILEY