OPSCB574-Assessment1-2nd
docx
keyboard_arrow_up
School
University of Phoenix *
*We aren’t endorsed by this school
Course
OPSCB/574
Subject
Management
Date
Jan 9, 2024
Type
docx
Pages
11
Uploaded by DukeArtSpider34
Jenifer Kephart
OPSCB/574
November 25, 2023
Competency 1 Assessment
Jenifer Kephart
OPSCB/574
November 25, 2023
Competency 1 Assessment (2
nd
Attempt)
Jenifer Kephart
OPSCB/574
November 25, 2023
Competency 1 Assessment
Competency 1 Assessment
Process Evaluation:
Current pest control service flow chart:
I am the office manager for a local pest control called Hydrex Pest Control. In my evaluation of the pest control service process using Lean concepts, the focus is on eliminating waste and enhancing overall efficiency in order to be able to provide more services per day. One key area of improvement lies in the scheduling of pest control visits. By ensuring that services are provided just in time and avoiding excessive treatments or inspections, we can eliminate overproduction and optimize resource utilization. Office schedules service/plans route
tech drives to location
tech speaks with customer
tech evaluates areas of concern
tech gathers needed materials
tech spends time looking for needed material
tech treats yard and structure for target pests
tech speaks to customer again
Collects payment
Posts job in PestPac
Turns paperwork into office
Jenifer Kephart
OPSCB/574
November 25, 2023
Competency 1 Assessment
A critical aspect to address is inventory management. Minimizing the stock of pesticides and equipment reduces carrying costs and the risk of obsolescence. A careful balance is required to meet customer demand without maintaining unnecessary inventory levels. This not only streamlines the process but also contributes to cost savings.
In the realm of customer experience, minimizing wait times is paramount. By optimizing technician routing and scheduling, we can reduce the time customers have to wait for appointments, enhancing overall satisfaction. Additionally, centralizing scheduling may be considered to minimize unnecessary travel and transportation costs.
Efficiency in motion is essential during inspections or treatments. Streamlining technician
movement and ensuring that equipment is efficiently positioned in service vehicles can significantly reduce unnecessary steps. This contributes to a more agile and responsive pest control service.
Quality control is a key component in the Lean approach. Implementing a robust system to identify and address defects during inspections or treatments is crucial. Ongoing training for technicians further reduces the likelihood of errors, enhancing the overall quality of the service provided.
Lastly, recognizing and fully utilizing the talent of technicians is essential. Ensuring they are well-trained and equipped to handle a variety of pest control issues contributes to a more versatile and adaptable workforce. Encouraging continuous improvement and feedback from technicians fosters a culture of innovation within the team, leading to a more effective and efficient pest control service process.
Your preview ends here
Eager to read complete document? Join bartleby learn and gain access to the full version
- Access to all documents
- Unlimited textbook solutions
- 24/7 expert homework help
Jenifer Kephart
OPSCB/574
November 25, 2023
Competency 1 Assessment
Flow chart showing proposed changes:
Evaluation Of The Control Chart And Process Metrics My process is for pest control services. I’m measuring how many services are performed
per 8 hour work day. The target is 12 jobs per day. Forty-five sample daily service numbers are
recorded in Column B.
Day
# of Jobs
Average UCL
LCL
1
13
12
16.91288
7.087123
2
14
12
16.91288
7.087123
3
10
12
16.91288
7.087123
4
12
12
16.91288
7.087123
5
12
12
16.91288
7.087123
6
12
12
16.91288
7.087123
7
12
12
16.91288
7.087123
8
10
12
16.91288
7.087123
9
8
12
16.91288
7.087123
10
15
12
16.91288
7.087123
Office schedules service/plans route
tech drives to location
tech speaks with customer
tech evaluates areas of concern
tech gathers needed materials more quickly due to new organization methods
tech treats yard and structure for target pests more efficiently
tech speaks to customer and collects payment/provides invoice
tech posts job in PestPac, and paperwork is eliminated with new online software for technicians.
Jenifer Kephart
OPSCB/574
November 25, 2023
Competency 1 Assessment
11
14
12
16.91288
7.087123
12
12
12
16.91288
7.087123
13
12
12
16.91288
7.087123
14
12
12
16.91288
7.087123
15
12
12
16.91288
7.087123
16
12
12
16.91288
7.087123
17
10
12
16.91288
7.087123
18
8
12
16.91288
7.087123
19
16
12
16.91288
7.087123
20
12
12
16.91288
7.087123
21
12
12
16.91288
7.087123
22
10
12
16.91288
7.087123
23
11
12
16.91288
7.087123
24
12
12
16.91288
7.087123
25
12
12
16.91288
7.087123
26
10
12
16.91288
7.087123
27
12
12
16.91288
7.087123
28
12
12
16.91288
7.087123
29
12
12
16.91288
7.087123
30
11
12
16.91288
7.087123
31
12
12
16.91288
7.087123
32
12
12
16.91288
7.087123
33
12
12
16.91288
7.087123
34
11
12
16.91288
7.087123
35
10
12
16.91288
7.087123
36
12
12
16.91288
7.087123
37
14
12
16.91288
7.087123
38
12
12
16.91288
7.087123
39
12
12
16.91288
7.087123
40
13
12
16.91288
7.087123
41
12
12
16.91288
7.087123
42
13
12
16.91288
7.087123
43
15
12
16.91288
7.087123
44
15
12
16.91288
7.087123
45
13
12
16.91288
7.087123
Average:
12
STDEV:
1.637626
Jenifer Kephart
OPSCB/574
November 25, 2023
Competency 1 Assessment
1
3
5
7
9
11
13
15
17
19
21
23
25
27
29
31
33
35
37
39
41
43
45
0
2
4
6
8
10
12
14
16
18
Control Chart
Series1
Series2
Series3
Series4
The control chart shows that the process is stable or in statistical control as there are no points occurring beyond the limits, and there are no patterns. The control chart displays the upper specification limit (USL) as the maximum number of
service jobs completed in a day and the lower specification limit (LSL) as the minimum number of jobs completed in a day. The upper limit is set at 17 jobs, while the lower limit is set at 7 jobs. To achieve a minimum of 12 jobs per day, each job must be completed within 30 minutes, and the average drive time between job locations should be less than 10 minutes.
Being "in control" is indicated when all data points fall between the lower and upper control limits. This suggests that we are successfully meeting the project's goal. Variability, representing the spread of data points, is acceptable as long as it remains within the control limits.
Your preview ends here
Eager to read complete document? Join bartleby learn and gain access to the full version
- Access to all documents
- Unlimited textbook solutions
- 24/7 expert homework help
Jenifer Kephart
OPSCB/574
November 25, 2023
Competency 1 Assessment
0
5
10
15
20
25
USL=17
LSL=7
Capability Analysis
Measurement
Frequency
Chart
Cp
Cpk
Cpu
Cpl
Est. Sigma
PPM > USL
PPM < LSL
To
CPK
0.34331494
0.34296568
0.34296568
0.34366419
4.772
151764
151272
Total PPM
Sigma Level
Average
Count
Out of Spec
Actual
169423
1.37266452
12.00
180
45 (25.00%)
Descriptive Statistics
Variable
13
Mean
12.00
Standard Error
0.244
Mode
12
Jenifer Kephart
OPSCB/574
November 25, 2023
Competency 1 Assessment
Standard Deviation
1.638
Variance
2.682
Coefficient of Variation
13.65
Kurtosis
0.993
Skewness
-
0.0325
Range
8
Minimum
8
Maximum
16
Sum
540
Count
45
First Quartile
12
Median
12
Third Quartile
12
95% Lower Conf. Limit
11.51
95% Upper Conf. Limit
12.49
Executive Summary Hydrex Pest Control, a leading service provider in the pest management industry, has undergone a comprehensive process evaluation using Lean principles and Statistical Process Control (SPC) methods. This evaluation aimed to identify opportunities for waste elimination, process improvement, and enhanced overall efficiency.
Summary of the Process Evaluation using Lean Concepts:
In the Lean evaluation, the focus was on identifying and eliminating waste in the pest control service process. Overproduction, excess inventory, waiting times, unnecessary transportation times, inefficient motion, over-processing, and underutilized talent were scrutinized. The scheduling of pest control visits was optimized to ensure services are provided at the necessary times, minimizing overproduction. Inventory management practices were refined to strike a balance between meeting customer demand and minimizing carrying costs.
Efforts by our staff in the office have been made to minimize customer wait times by optimizing technician routing and scheduling, reducing unnecessary transportation and
Jenifer Kephart
OPSCB/574
November 25, 2023
Competency 1 Assessment
enhancing overall customer satisfaction. Motion efficiency was addressed by streamlining technician movement during inspections and treatments. Quality control measures are being reinforced to identify and address areas of applicator error during the process, and ongoing training is being emphasized to reduce the likelihood of errors.
The evaluation highlighted the need for continuous improvement and the importance of recognizing and utilizing the full potential of the talent within the workforce. This Lean approach resulted in a more streamlined and efficient pest control service process, with a focus on delivering enhanced value to the customers.
Summary of the Evaluation of Control Chart and Process Metrics based on SPC Methods:
Control charts provided a visual representation of the stability of the pest control service process. Any significant variations or outliers were identified, allowing for timely intervention and
corrective actions. By monitoring these metrics, Hydrex Pest Control gained insights into the process's inherent variability and its ability to meet predefined quality standards. Looking at the Control chart there is no significant patterns or points where the data fell below the lower limit or
went above the upper limit.
Evaluation of whether the process would benefit from Six Sigma, Lean, or other tools:
The combined Lean and SPC evaluation demonstrated significant improvements in the pest control service process. However, there are areas where Six Sigma methodologies could be integrated to further enhance efficiency and reduce defects. Six Sigma's focus on minimizing
process variations aligns seamlessly with the SPC analysis findings.
By implementing Six Sigma, Hydrex Pest Control can systematically identify and eliminate the root causes of variations, resulting in a more consistent and predictable service delivery. This methodology, coupled with Lean principles, would provide a comprehensive approach to process improvement, ensuring that the pest control service not only meets but consistently exceeds customer expectations. The two main variables in why more or less jobs are completed in a day are the routing done by office staff, and the time spent at each location.
DMAIC:
Define: Ensuring that a proper number of pest service jobs are completed daily.
Measure: Collecting data over a period of 45 days to gather information about the number of jobs being completed daily.
Analyze: Using control charts analyze the information of how many jobs are being completed daily, and what the variables are that cause these numbers to fluctuate.
Your preview ends here
Eager to read complete document? Join bartleby learn and gain access to the full version
- Access to all documents
- Unlimited textbook solutions
- 24/7 expert homework help
Jenifer Kephart
OPSCB/574
November 25, 2023
Competency 1 Assessment
Improve: Train office staff how to better route jobs based on customer locations, and train technicians on how to utilize time most effectively while completing each job. Control: Use of Standard Operating Procedures to ensure jobs are being scheduled and serviced as efficiently as possible. Six Sigma is particularly effective in situations where reducing variation is critical to achieving process stability and consistency. The primary goal is to minimize defects and errors, Six Sigma's emphasis on statistical analysis and control may be more beneficial. Six Sigma relies heavily on data analysis and statistical tools to identify root causes of problems and make informed decisions. The process improvement initiative requires a rigorous and data-driven approach to problem-solving, Six Sigma provides a structured methodology for this purpose. A primary concern is customer satisfaction and minimizing defects, Six Sigma's DMAIC (Define, Measure, Analyze, Improve, Control) methodology is designed to identify and eliminate defects and improve overall process performance.
Description of the SPC Project and Recommendations for Improvements:
The SPC project involves the development and implementation of control charts to monitor critical process metrics. The control charts facilitate real-time monitoring, enabling the identification of trends and variations in the number of jobs being completed each day.
Recommendations for improvements include:
Implementing enhanced, targeted training programs and detail Standard Operating Procedures to further enhance technician skills, reducing variations in inspection accuracy and treatment effectiveness, as well as for office staff when scheduling service appointments.
Establishing a system for collecting and analyzing customer feedback to identify areas for improvement and ensure ongoing customer satisfaction. This can be done with surveys sent out to customers via text and/or email shortly after services have been provided. Integrate advanced data analytics tools to gain deeper insights into process performance, enabling proactive adjustments and continuous improvement.
Foster collaboration between different departments such as technicians and office staff to address process variations holistically and ensure a unified approach to quality control.
In conclusion, the integration of Lean concepts and SPC methods has significantly improved the pest control service process at Hydrex Pest Control. The recommendation is to further leverage Six Sigma methodologies to drive continuous improvement, reduce process variations, and elevate the overall quality of service delivery. This approach will position Hydrex Pest Control as an industry leader in providing efficient, consistent, and customer-centric pest management solutions.
Jenifer Kephart
OPSCB/574
November 25, 2023
Competency 1 Assessment
References:
https://www.spcforexcel.com/thank-you-for-requesting-our-demo-software/
Gérard Cachon, & Terwiesch, C. (2020). Operations management
. Mcgraw-Hill.
https://www.hydrexbugs.com/
Related Documents
Recommended textbooks for you
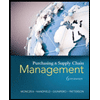
Purchasing and Supply Chain Management
Operations Management
ISBN:9781285869681
Author:Robert M. Monczka, Robert B. Handfield, Larry C. Giunipero, James L. Patterson
Publisher:Cengage Learning
Marketing
Marketing
ISBN:9780357033791
Author:Pride, William M
Publisher:South Western Educational Publishing
Recommended textbooks for you
- Purchasing and Supply Chain ManagementOperations ManagementISBN:9781285869681Author:Robert M. Monczka, Robert B. Handfield, Larry C. Giunipero, James L. PattersonPublisher:Cengage LearningMarketingMarketingISBN:9780357033791Author:Pride, William MPublisher:South Western Educational Publishing
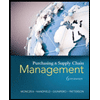
Purchasing and Supply Chain Management
Operations Management
ISBN:9781285869681
Author:Robert M. Monczka, Robert B. Handfield, Larry C. Giunipero, James L. Patterson
Publisher:Cengage Learning
Marketing
Marketing
ISBN:9780357033791
Author:Pride, William M
Publisher:South Western Educational Publishing