PS4S30_Week 7_Ethical-Audits_Information-Sheet
docx
keyboard_arrow_up
School
Meru University College of Science and Technology (MUCST) *
*We aren’t endorsed by this school
Course
CCS3476
Subject
Management
Date
Nov 24, 2024
Type
docx
Pages
4
Uploaded by ChefMaskWolf17
Codes of Conduct and Audits for (more) sustainable supply chains Debate Information Sheet (2022)
Instructions
This document contains some relevant information (in fhe form of brief summaries of research and research findings and quoted extracts from relevant publications, such as commercial organizations’ reports and consultancy research reports) to help you to further investigate and assess the issue of codes of conduct and ethical audits as mechanisms for enhancing sustainable practices in supply chains. The information is presented in no particular order.
You may draw on these, alongside your own additional ideas, arguments and evidence to build your case(s) for the debate. ____________________________________________________________________________
“An audit [at IKEA] typically takes one or two days and is conducted using a checklist covering the approximately 90 issues of the code. During the audit, a number of randomly selected employees and management representatives are interviewed. Apart from conducting interviews, the auditors go through relevant documents, such as employment contracts and payslips, and make observations about the working conditions around the factory. Issues that need to be improved are noted in an audit report” (Andersen and Skjoett-Larsson 2009, p.80)
LeBaron and Lister (2016) suggest that deception in the audit regime is widespread, and known to corporations. A focus on Tier 1 suppliers may help a buying firm to avoid reputational damage, but it doesn’t necessarily work to eliminate social/environmental harm.
They highlight the ineffectiveness by citing an example of a fire at a garment factory in Karachi, Pakistan, in 2012, which killed approximately 300 workers and yet had recently achieved SA 8000 accreditation (
SA 8000 is
an international certification standard that encourages organizations to develop, maintain and apply socially acceptable practices in the workplace). They conclude that, “ultimately, the audit regime is ‘working’ for corporations, but failing workers and the planet. Labour abuses, poor working conditions and environmental degradation within global supply chains remain widespread. ..Audits are ineffective tools for detecting, reporting, or correcting environmental and labour problems in supply chains. They reinforce existing business models and preserve the global production status quo.”
Short et al. (2015) analyzed 16,000 codes of conduct audits across around 6000 factories globally to investigate factors that affect the quality of the audit. Their key findings suggest that there are numerous factors that affect the efficacy of audits carried out by private auditors: 1.
Who pays for the audit? If the factory pays, fewer violations are flagged, than if the brand
pays.
2.
Audit team – all new, or some return auditors? Return auditors leads to flagging fewer violations.
3.
Gender composition of the team – mixed, or only women flag more violations than male only teams.
1
4.
Level of training – higher level of training leads to flagging more violations.
Short et al. (2015) suggest that these are all key challenges in assuring the quality of private auditors and the quality of their assessments. They suggest firms that use private
auditors aren’t necessarily getting complete and accurate information from their supply chain monitors.
Jiang (2009) investigated the conditions for suppliers in developing countries’ compliance with Codes of Conduct imposed on them by Western buying firms. They made the following
conclusions and recommendations for management. 1.
Relying on audits to check suppliers’ compliance with codes of conduct, with associated threats of lost business, means audits can in some circumstances drive dishonesty as suppliers feel forced to provide the ‘right’ answer, or face serious business consequences. 2.
Level of management ‘know-how’ in developing countries’ factories can be low regarding
CSR, and this must be taken in to account: “Open and honest communication at buyer, supplier, and factory-worker level is essential if progress is to be made in building SCC compliance, so suppliers can have information about buyers’ expectations and are able to receive feedback about where or how to get improvements started”. 3.
Sometimes buying firms are ‘part of the problem’, with unfair buying practices driving the
conditions that do not comply with the buying firms’ code of conduct, such as excessive overtime, low pay, poor working conditions: “A responsible buyer should see itself as part of the problem and solution of the supplier’s…compliance, rather than as an independent authority demanding better behavior from the supplier”
When a large customer commits to extended responsibility for its supply chain, the current trend is for it to engage in a programme of monitoring suppliers taking the form of audits (Spence and Bourlakis, 2009).
Based on a review of a wide range of literature, Benstead et al. (2021, p.1138) summarized a standard audit in the following way: “A standard social audit applies public or private standards by investigating working conditions within a factory by touring the site, reviewing documents, and interviewing workers to further understand employee wages and benefits, working hours, harassment, health and safety, and the use of child labour…These can be announced or unannounced to uncover the real conditions in a factory and conducted by brands internally, NGOs or third-party auditors”
In a 2021 interview with CIPS Supply Magazine, the senior manager for Corporate Social Responsibility at John Lewis Partnership (JLP) said that while it acknowledges audits are not always the best way to monitor supply chain risks, they can still be a valuable way to build better relationships with suppliers (CIPS, 2021). In conducting their audits at JLP suppliers, the consider the following as good practices that help to increase the efficacy of audits:
o
Have a pre-audit conversation: “Being clear about what you want to investigate and why is helpful. We had pre-audit conversations just to say ‘this is what we’re going to
do’. We were asking them not to alert people or change the way they behave because what we were going to do is to share things openly. There’s no risk to 2
people, it’s not as if we’re going to use it to penalise anyone. You should have that really open engagement early.”
o
See auditing as a collaborative process based on shared values. For this reason, they do not put contractual rewards in place for doing the right thing, nor do they penalize based on gaps in compliance (CIPS, 2021).
Some extracts from Apple’s 2022 Supplier Responsibility Report:
1.
“Through every challenge [this year], we’ve continued to push forward in our work to raise standards across industries and support people across our global supply chain. That begins with the high standards we set in our Supplier Code of Conduct — grounded
in internationally recognised principles, Apple’s Human Rights Policy, and the values that have always guided our company. To uphold those standards, this year, our teams and independent auditors conducted 1,177 assessments of our supplier facilities in 52 countries. We engaged more than 350,000 supplier employees about their workplace experiences. And for new suppliers, we conducted extensive onboarding to be sure they abide by our Supplier Code — in their respect for people’s rights and for the planet” (Apple, 2022, p.3). 2.
“As we make progress towards our goal to use only recycled and renewable materials in our products and packaging, we continue to source primary materials responsibly. 100 per cent of the identified tin, tungsten, tantalum, and gold (3TG), cobalt and lithium smelters and refiners in our supply chain have participated in independent, third-party audits to assess and identify social, environmental, human rights and governance risks.” (Apple, 2022, p.11)
3.
As a result of our responsible procurement process, 9 per cent of prospective suppliers evaluated for Code-related risks have been prevented from entering our supply chain since fiscal year (FY) 2020 for being unable or unwilling to meet our Apple Supplier Code of Conduct (“the Code”) and the Apple Supplier Responsibility Standards (“the Standards”). We continued to extend our support to help prospective suppliers correct compliance issues found during the supplier selection process. Since FY2020, 68 per cent of companies who were not awarded our business opted in to receive this additional
support, helping to protect people and the planet beyond the reach of our business and supply chain (Apple, 2022, p. 8)
“While there is no specific set of information that is required in a code of conduct, several significant United Nations guidelines have outlined what a code should include. Organisations can use codes to bind their employees and suppliers to their expectations for how to manage labour, human rights, anti-corruption, and environmental impact. A code of conduct should, in essence, identify company standards, and follow a clear plan of action to address grievances within the organisation and the supply chain… In response to globalisation, the United Nations has provided several guidelines that influence business responsibility in the absence of adequate local law. These guidelines directly and indirectly address the content of a code of conduct” (Theron et al., 2020, p.5).
Theron et al. (2020) suggest that two key things must be taken in to account in order to enhance the effectiveness of audits, particularly in the context of global supply chains: 3
Your preview ends here
Eager to read complete document? Join bartleby learn and gain access to the full version
- Access to all documents
- Unlimited textbook solutions
- 24/7 expert homework help
power dynamics between the buying firm and the supplier, and the culture and socio-
economic environment of the supplier. Failure to acknowledge these factors can lead to ‘risk-shifting’ : which is the process of “shifting the responsibilities outlined in the code of conduct from the buyer down the supply chain without assessing the feasibility of implementation based on economic means. This creates a trickle-down effect in which the responsibility to uphold human, labour, and environmental rights is passed to the people who need protecting” (Theron et al., 2020, p. 9).
References
Andersen, M. and Skjoett-Larsen (2009), ‘Corporate social responsibility in global supply chains’, Supply Chain Management: an International Journal, 14(2), pp.75-86
Apple (2022) Annual Progress Report: People and Environment in our Supply Chain, Available at: https://www.apple.com/euro/supplier-responsibility/l/titles_en/pdf/
Apple_ESCI_2022_Progress_Report_UK_IE.pdf
(Accessed 21 Oct 2022). Benstead, A.V.,Hendry, L. C. & Stevenson, M. (2021) ‘Detecting and remediating modern slavery in supply chains: a targeted audit approach’, Production Planning & Control, 32:13
CIPS (2021), ‘How to conduct meaningful supplier audits’, CIPS Supply Magazine, Available at: https://www.cips.org/supply-management/analysis/2021/may/how-to-conduct-meaningful-
supplier-audits/
(Accessed: 14 Oct 2022).
Helin, S., and Babri, M (2015). “Travelling with a Code of Ethics: A Contextual Study of a Swedish MNC Auditing a Chinese Supplier.” Journal of Cleaner Production 107: 41–53. Jiang, B. (2009), “Implementing Supplier Codes of Conduct in Global Supply Chains: Process Explanations from Theoretic and Empirical Perspectives.” Journal of Business Ethics 85 (1): 77–
92. LeBaron, G. and Lister, J. (2016), ‘Ethical Audits and the Supply Chains of Global Corporations,
Report. SPERI Global Political Economy Briefs. Sheffield Political Economy Research Institute, University of Sheffield.
Short, J.L., Toffel, M.W. and Huguill, A.R. (2015), ‘Monitoring global supply chains’, Strategic Management Journal, 37, pp.1878-1897
Spence, L., and Bourlakis, M. (2009), ‘The evolution from corporate social responsibility to supply chain responsibility: the case of Waitrose’, Supply Chain Management: an International Journal, 14(4), pp. 291-302
Theron, C., Lander, R., Purdie, H. and Roth, P. (2020), ‘The value of supplier codes of conduct: supporting transparency and improving performance’, Ardea International, Available at: https://www.ardeainternational.com/resources/publications/the-value-of-supplier-codes-of-
conduct/
(Accessed 3 Oct 2022). 4
Related Documents
Recommended textbooks for you
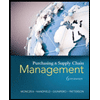
Purchasing and Supply Chain Management
Operations Management
ISBN:9781285869681
Author:Robert M. Monczka, Robert B. Handfield, Larry C. Giunipero, James L. Patterson
Publisher:Cengage Learning
Recommended textbooks for you
- Purchasing and Supply Chain ManagementOperations ManagementISBN:9781285869681Author:Robert M. Monczka, Robert B. Handfield, Larry C. Giunipero, James L. PattersonPublisher:Cengage Learning
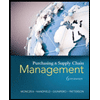
Purchasing and Supply Chain Management
Operations Management
ISBN:9781285869681
Author:Robert M. Monczka, Robert B. Handfield, Larry C. Giunipero, James L. Patterson
Publisher:Cengage Learning