Lean production Revision
docx
keyboard_arrow_up
School
Maseno University *
*We aren’t endorsed by this school
Course
413
Subject
Management
Date
Nov 24, 2024
Type
docx
Pages
69
Uploaded by SargentGuineaPigMaster1200
Quality Management 1
A STUDY ON QUALITY MANAGEMENT, LEAN PRODUCTION SYSTEM, AND
CONTINUOUS IMPROVEMENT: THESE KEY FACTORS THAT HAVE ENABLED
TOYOTA MOTORS TO REMAIN AS THE LEADING CAR PRODUCER
Logistics & Supply Chain Management United Kingdom
2021
Quality Management 2
Abstract
With the current stiff competition in the global market in almost all industry sectors, corporations
have been forced to ensure sustained effort in order to remain afloat in the market by improving their production process and products. The automobile industry is one of the many sectors that have always given relevant scenarios of organisations that have managed to attain exemplary business excellence by putting their customers’ interests and product quality aspects at the centre of their production system. Toyota Motor Corporation is one of such companies which has hit a significant breakthrough in large-scale automotive manufacturing. The corporation has consistently deployed the concept of total quality management, lean production, and continuous improvement to perpetually design, implement, and develop the known Toyota Production System that has not only impacted the upcoming of various business excellence models but has also enable the company to remain as the leading global car producer for over the last one decade. This study explores how Toyota Corporation has implemented quality management, lean production system, and continuous improvement concepts to sustain itself as the leading car producer in the world despite tough competition in the global market. The researcher opted for a quality secondary study to explore the impact of the identified three production factors on Toyota's operational performance and productivity in terms of waste reduction, minimisation of defects and product recalls, and customer satisfaction. The study has used the existing literature, books, websites, government reports, magazines, research reports, etc. to retrieved relevant information to achieve the research objectives. The study found that Toyota has fully relied on the full implementation of quality control, lean production, and continuous improvement related concepts such as employee involvement and customer focus among other factors to attain its success as the leading car producer.
Quality Management 3
Table of Contents
Abstract
............................................................................................................................................
2
Chapter 1: Introduction
....................................................................................................................
5
1.1 History of Toyota Motors
..........................................................................................................
5
1.2 Total Quality management
.........................................................................................................
6
1.3 Lean production system
.............................................................................................................
7
1.4. Continuous improvement
..........................................................................................................
9
1.5. Problem statement
..................................................................................................................
10
1.6. Research questions
..................................................................................................................
11
1.7. Aim and objective
...................................................................................................................
11
1.8. Limitation of the study
............................................................................................................
12
Chapter 2: Background Research
..................................................................................................
13
2.1. Toyota’s growth path
..............................................................................................................
15
2.2. Quality management and culture
............................................................................................
17
2.3. Lean production system and competitive skills
......................................................................
20
2.4. Continuous improvement and product recall crisis phenomenon
...........................................
22
Chapter 3: Method Justification and Explanation
.........................................................................
25
3.1. Research design
......................................................................................................................
25
3.2. Study population and sample design
......................................................................................
26
3.3. Data collection
........................................................................................................................
27
3.3.1. Inclusion/exclusion criteria
.................................................................................................
28
3.3.2. Secondary data
....................................................................................................................
28
3.4. Data analysis
...........................................................................................................................
29
Your preview ends here
Eager to read complete document? Join bartleby learn and gain access to the full version
- Access to all documents
- Unlimited textbook solutions
- 24/7 expert homework help
Quality Management 4
3.5. Limitation of the study
............................................................................................................
29
3.6. Ethical consideration
..............................................................................................................
30
Chapter 4: Results and Analysis
....................................................................................................
31
4.1. Results
.....................................................................................................................................
31
4.1.1 Quality management
.............................................................................................................
31
4.1.1.1 Customer focus
..................................................................................................................
35
4.1.1.2. Empowerment of employees
.............................................................................................
36
4.1.2. Lean production system
.......................................................................................................
37
4.1.2.1. Kanban
..............................................................................................................................
38
4.1.2.2. Perceived benefits of the lean production system
.............................................................
39
4.1.3. Continuous improvement (Kaizen)
......................................................................................
40
4.2. Analysis
...................................................................................................................................
41
4.2.1. Quality management systems (QMS) for minimized costs and improved productivity
.....
41
4.2.2. Quality control, lean production, and continuous improvement and market branding
.......
42
4.2.3. Modern production system and product quality
..................................................................
43
4.2.4. Quality control, lean production, and continuous improvement and supply chain
.............
44
Chapter 5: Recommendations and Implementation
.......................................................................
46
Bibliography
..................................................................................................................................
52
Appendices …………………………………………………………………………………….. 62
a.
CPR Proposal
b.
Ethical Approval
Quality Management 5
Chapter 1: Introduction With the current competitive global markets, producers are compelled to look for possibilities or ways of enhancing their production efficiency for effective competitiveness. As such, Yang and Yang (2013) asserted that such improvements in production efficiency could be achieved through several approaches, including the acquisition of most current and modern technologies, services improvement, waste reduction, and quality enhancement. Similarly, the principles of quality management, lean production system, and continuous improvement are well
known and applied in several auto manufacturing companies. Most companies that use these principles have generally focused and emphasized developing higher quality products ensuring less waste to enhance their level of customer satisfaction and increase competitiveness in the ever-downsizing global market (
Hallam, Muesel, and Flannery, 2010). Toyota Motor on the other
side has continuously deployed all the principles as a set, a strategy which seems to have enabled
it to remain outstanding as the leading car producer.
1.1 History of Toyota Motors
Toyota is a renowned Japanese corporation founded in 1937 to design, produce/manufacture, assemble, and sell commercial vehicles, passenger cars, minivans, and related accessories and parts in Japan, Europe, etc. (
Kehr and Proctor, 2017). The corporation is globally known as the eleventh largest world company by revenue and was listed the largest worldwide automobile manufacturing corporation in the year 2010 by the quantity of production (
Kariuki and Mburu, 2013). Toyota has been recognized and declared as a leader in the manufacturing and production of cars through their development and execution of the Toyota Production System (TPS), a strategy deemed to be a clear precursor to the concept of lean manufacturing, continuous improvement, and quality control philosophies. Barney and Kirby
Quality Management 6
(2014) argued that having been invented by Taiichi Ohno and Eiji Toyoda at the Toyota Motor Corporation in Japan following the Second World War, the TPS approach is today regarded as the most unique manufacturing system. Even though the strategy was innovated specifically for the automotive system of production, it is currently more recognized particularly for its revolutionary approach toward the operation of businesses, which is characterized by the involvement of workers in decision-making, more efficient productivity, and more choices for customers. The company consequently came up with new kinds of concepts in management, including lean thinking and quality management, that their application in manufacturing contributed largely to shortened cycle time for production and development, reduced cost of manufacturing, and enhanced competitiveness of the corporation as an enterprise.
1.2 Total Quality Management
According to Anvari, Ismail, and Hojjati (2011), various scholars have over the year postulated different theories of management some of which have been regarded as merely management fashions and, they have been equally criticized for presenting serious shortcomings or defects. Total quality management is one of the theories focusing on optimisation; however, various views and ideas have been presented about it. Total quality management is reported to involved monitoring or controlling of quality at every single stage of operation, all the way from the planning and design phases to overall production improvement opportunities (
Schonberger, 2014). For Schonberger (2014), total quality management would be seen as a corporate culture usually characterized by an enhanced customer satisfaction by ensuring continuous improvement
whereby all the employees of the organisation are involved in active participation in various critical decision-making processes. Alternatively, total quality management has been claimed as both a set of guiding principles and philosophy applied for effective management of business
Your preview ends here
Eager to read complete document? Join bartleby learn and gain access to the full version
- Access to all documents
- Unlimited textbook solutions
- 24/7 expert homework help
Quality Management 7
organisations with a specific focus on customer satisfaction through control of relevant business processes. Specifically, Mácsay and Bányai (2017) specified that for Toyota Motor, activities such as quality engineering, supply control, statistical control, and overall improvement are key components making up total quality control. Hallam, Muesel, and Flannery (2010) argued that total quality management as applied in many organisations, in many cases, has focused largely on improving the organisations’ efficiency, effectiveness, as well as responsiveness to the needs of customers alongside stakeholders by constantly tapping employees’ competencies and skills; thus, leading to the attainment of the projected organisational performance. In other words, total quality management is a philosophy that is aiming to realise success in ensuring stable organisational growth and development through an active engagement of every
member of staff in the economical production of quality that the customer wants (
Pech and Vaněček, 2018). Therefore, the approach implies the utilisation of quality principles in management in every aspect of the organisation such as suppliers, customers, services, products, and smooth integration in various business processes involved (
Keitany and Riwo-Abudho, 2014). By that, it would be noted that the attainment of excellent in a business organisation is based on the performance of total quality management which tends to represent a robust and multidimensional concept involving several elements, including external and internal customer satisfaction, focus on quality, shared responsibility, robust design, systemic vision, quality control, training and education, strategic process, cultural change, supplier integration, statistical thinking, teamwork, and quality control. 1.3 Lean Production System
As it has been mentioned previously, a lean production system implies the business model emphasising meeting the expectation of customers by simply ensuring the delivery of top-
Quality Management 8
quality products and services at the least cost and at the right time when needed (
Loyd et al., 2020). In quoting the Lean Aerospace Initiative, lean thinking has been defined as the dynamic, customer-focused, knowledge-driven process through which every individual within a defined enterprise continuously participates towards waste elimination to create value as the main goal (
Mady et al., 2020). Lean thinking philosophy is regarded as a concept that could be seen, as well as implemented at various levels and as a process of commitment to continuous improvement that would greatly affect the competitiveness, of the organisation. According to Wee and Wu (2009), effective use of the lean concept has contributed to the resolution of serious organisational challenges as well as a powerful and reliable approach to collected and coordinate multiple transformation initiatives. Chiarini, Baccarani, and Mascherpa (2018) claimed that in mass or batch production scenarios, approximately ninety-eight per cent of time activities are not value-adding. In that light, many scholars have emphasized total commitment by the senior management, if organisations have to achieve success in the implementation of lean management (
Stamm, Neitzert, and Singh, 2009; Keitany and Riwo-Abudho, 2014). Notably, Toyota Motor is reported to pursue lean production specifically in response to their needs and challenges such as product recalls to fundamentally enhance their business competitiveness by reducing overall costs of production and improving customer satisfaction by increasing quality and responsiveness to customer needs. Moreover, the company managers in all the branches across the globe have been
reported to constantly work together in creating interest and passion in implementing a lean production system (
Schonberger, 2014). Such efforts could be attributable to the enhanced business competitiveness of the organisation which has increased direct global competition, constantly evolving customer, and rapidly spiralling expectations in the supply chain.
Quality Management 9
Additionally, Toyota Motor as a lean practitioner is claimed to have acknowledged the fact that successful implementation of a lean production system requires either perceived or real business crisis such as product recalls, high volumes of waste, and stiff market competition in order to foster receptiveness to the most important transformation that lean thinking requires of organisations’ processes and culture to be like (
Mácsay and Bányai, 2017). Several pieces of research have been conducted to explore the importance of lean production system that has, indeed, established that the lean approach has not only enhanced ergonomics, reduced inventory, and improved procedures in business operations, but it also enables the corporation to align its processes and remain up-to-date with most important changes in the customer demand (
Keitany and Riwo-Abudho, 2014). 1.4. Continuous Improvement
Continuous improvement is one philosophy that Deming perceived to be comprising of improvement measures that increase chances of success while reducing possibilities of failure (Bhuiyan and Baghel, 2015). Similarly, whereas Yella and Atem (2007) viewed continuous improvement as a corporation-wide process involving focused as well as incremental innovation,
Oliveira, Sá, and Fernandes (2017) on the other hand regarded continuous improvement as either
a side shoot of currently available initiatives such as quality management or as a new technique of increasing creativity as well as attaining competitive excellence in the current global market. Pinto et al. (2019) argued that the aspect of quality management could be attained by consistently
pursuing continuous improvement through active engagement of employees from across all organisational levels. For Toyota Motor, continuous improvement is indicated to have been adopted as a culture
or a way of sustained improvement that targets the elimination of all waste in the entire systems
Your preview ends here
Eager to read complete document? Join bartleby learn and gain access to the full version
- Access to all documents
- Unlimited textbook solutions
- 24/7 expert homework help
Quality Management 10
as well as processes of the organisation (
Womack, Jones, and Roos, 2007). The implementation of the concept requires the involvement of every individual working together to actualise true improvements without necessarily undertaking big capital investments. Moreover, it is widely established that an integrated approach towards quality management and continuous improvement that focuses on lean thinking is more important than different techniques and methods applied in traditional mass production (
Yella and Atem, 2007). Perhaps, such principles remain to be the main foundation and basis for total quality management, which for Toyota Motor, have continuously engaged all their junior and senior employees to actively take part in the continuous improvement of processes, services, and products (
Yang and Yang, 2013). Eventually, the concepts of total quality management, lean production, and continuous improvement have emerged as the dominating key factors that have enabled the organisation to achieve significant success through market competitiveness and customer satisfaction. Therefore, with reference to Toyota Motor, the study will deploy a qualitative approach to explore how lean manufacturing, continuous improvement, and quality control factors have contributed to sustaining the company to remain on the lead in car production despite the stiff competition in the global automobile industry. 1.5. Problem Statement
With current global markets increasingly becoming quite competitive and customers’ needs tending to be more dynamic and unpredictable (
Hansen, 2001
; Hallam, Muesel, and Flannery, 2010), large-scale producers such as Toyota Motor are challenged to source alternative approaches to improve on their production efficiencies and competitiveness while ensuring zero waste and customer satisfaction through quality products and timely delivery. Toyota Motor is one of the large-scale producers specialized in automobile manufacturing and has adopted and
Quality Management 11
implemented total quality management, lean production system, and continuous improvement amid myriads of challenges, including recall of products. Therefore, the current study has sought to examine how effective Toyota Motor has utilized the concepts of total quality management, lean production system, and continuous improvement to emerge outstanding as the leading car producer globally. The study will establish the role that the three factors have played towards the success of Toyota Motors in the automobile industry.
1.6. Research Questions
The qualitative study will be directed by the following research questions; i.
How does Toyota leverage on quality system to minimise its production cost
while improving productivity?
ii.
What compels to Toyota to rely more on continuous improvement, lean
production, and quality control in marketing its brand?
iii.
Are modern production and quality management systems helpful in minimising
production defect products and recall of the same from the market?
iv.
How does the concepts of continuous improvement, lean manufacturing, and
quality control relate with the aspect of organisational productivity as applied in the supply
chain?
1.7. Aim and Objectives The aim of the study is to explore the impact of quality management, lean management system, and continuous improvement on Toyota Motor over the previous years despite the many challenges. The following are the objectives that guide the current research. i.
To evaluate in detail the quality management system, lean manufacturing, and continuous improvement as applied in the Toyota manufacturing business context.
Quality Management 12
ii.
To establish the impact of total quality management, continuous improvement, and lean manufacturing on the productivity of Toyota Motor in the past decade.
iii.
To analysis how Toyota uses continuous improvement, quality management, and lean production concepts to address the issue of product recalls and stiff market competition.
1.8. Limitations of the Study Despite the focus of the study to achieve its highlighted objectives, it is anticipated to present certain shortcomings that would comprise its success, including the validity of the outcome. The results, as well as recommendations of the research, will be fully based on the findings of the theoretical literature and, will not be a guarantee of fact-finding about Toyota Motors. In addition, accessing the organisation’s data bank would extremely challenging if not impossible as the management might be worried of being exposed in any case, they had not been applying the recommended management tools in the most appropriate way.
Your preview ends here
Eager to read complete document? Join bartleby learn and gain access to the full version
- Access to all documents
- Unlimited textbook solutions
- 24/7 expert homework help
Quality Management 13
Chapter 2: Background Research Economic globalisation has generally made organisational performance an essential aspect of existence as well as the prosperity of businesses in the increasingly hostile and turbulent environment. In fact, Kehr and Proctor (2017) argued that it is this hostility of the market environment that has made the quality of products remain a necessary factor for many business organisations to achieve their successes. In that regard, many scholars have described the approaches of improving quality in production as well as the application in business organisations. Chiarini, Baccarani, and Mascherpa (2018) intuited that there is no definite definition of quality management, lean production, and continuous improvement, a phenomenon which has perhaps contributed to some communication difficulties and complications in researching the field of study. Several authors have described the combination of quality management, lean production, and continuous improvements concepts as an integrated system of
several different principles and methods of management operations (
Hallam, Muesel, and Flannery, 2010; Oliveira, Sá, and Fernandes, 2017; Pinto et al., 2019). Nonetheless, Loyd et al. (2020) accentuated it is explicit that achievement of better efficiency, quality, and performance of
production processes is not only dependent on the methods themselves but also on their continued interaction and application. In this way, it is unquestionable that such methods should be complimentary in how they operate.
Specifically, an integrated system comprising of quality control, lean thinking, and continuous improvement is perceived as a modern philosophy of management in which a clear focus on the minimisation of different categories of waste to enhance the overall customer value (
Wickramasinghe and Wickramasinghe, 2016). By reducing the aggregate quantity of waste, the quality of products and services is greatly enhanced whereas both the production costs and time
Quality Management 14
are substantially reduced. In a bid to address the problem of waste, stiff market competition, and poor customer satisfaction, Toyota Motor has embraced the use of several techniques with lean manufacturing at the core. Other tools that the organisation considered using as complimentary include, total quality management, regular process analysis, and total productive maintenance. Hansen (2001) indicate that today’s worldwide competition dictates all kind of business corporations to constantly work on the improvement of their processes, services, and products. As result, Kakuro (2014) stated it has become widely believed and proven that organisations have great potential to achieve customer satisfaction and competitive market advantage from total quality management, lean production, and continuous improvement practices. Keitany and Riwo-Abudho (2014) asserted that these practices have enabled business organisations to achieve
outstanding performances through massive reduction of production waste and costs. Rajasekera (2013) concurred with this argument and iterated that most industries or individual organisations are today experiencing challenges associated with broad production which has contributed to serious wastages. Similarly, Lakhe and Mohanty (1993) alluded that such problems have seen many corporations encounter equivalent wastage problems along their supply chains as well as the liability on them to ensure quality products or services for customer satisfaction. Therefore, Keitany and Riwo-Abudho (2014) observed that it is upon the procurement managers of organisations to adopt new management production techniques such as total quality improvement, lean production systems, and continuous improvements as business initiatives necessary to achieve the reduction of waste, increased market competitiveness, and enhanced customer satisfaction, especially in manufacturing production. To such extents, it would be noticed that such initiatives leverage large business organisations to attain long-term competitive advantages by ensuring proper technologies and appropriate production systems are put in place,
Quality Management 15
with regard to shortening design time of products, enhancing end-customer satisfaction through waste reduction, product quality, and inventory management. 2.1. Toyota’s Growth Path
Toyota Motor company has largely relied on technologies and innovations to make its success story specifically in the approaches or processes it uses to produce its automobile products and to which it achieves customer satisfaction. Initially, Liker (2004) recounted that Sakichi Toyoda came up with the very first design/prototype car in the year 1936, a project which was accomplished after a capital investment of approximately $395,000. However, Magee
(2010) and Loureiro (2013) noted that Toyota had a very rough time in establishing its brand in the Japanese market since Henry Ford and General Motors had not only dominated the market but had also taken over the entire global market. Despite such market-related challenges, Toyota Motor still managed to produce 100,000 cars by 1947 (
Minto, 2010). Additionally, NYSE (2010)
indicated that the corporation was also experiencing financial turmoil shortly after the end of the Second World War citing large mounting debts, which compelled it to come up with a new strategy, including restructuring its operations and management. Subsequently in the mid-20
th
century, Toyota Motor invented a new system strategy referred to as Toyota Production System (TPS) that regulated the process of production of all their vehicles (
Benders and Morita, 2007).
Being regarded as an exceptional efficiency production system, Kehr and Proctor (2017) pointed that the set of principle therein the strategy, has since then set a clear trend and guidelines that have been adopted and used as the point of reference in the same motor industry and in other industrial sectors. Furthermore, the TPS would then propel the corporation to greater
levels of profitability, especially amidst the oil crisis witnessed in 1943. Reports by Organisation Internationale des Constructeurs d’Automobiles (OICIA) presented during the 2008-2014 period,
Your preview ends here
Eager to read complete document? Join bartleby learn and gain access to the full version
- Access to all documents
- Unlimited textbook solutions
- 24/7 expert homework help
Quality Management 16
ranked the Toyota Motor Company on top within the highly competitive motor or automotive industry. In fact, the profit of the corporation for the 2014 fiscal year was more than that of Chrysler, General Motors, and Henry Ford’s combined. In that regard, this impressive performance was linked to the TPS strategy which was largely lean production in kind. Within half a decade, Toyota Motor estimated its net revenue as $213 billion. Moving forwards, Toyota Motor Corporation is one of the organisations that have long been acknowledged as leaders in enhanced product quality and lean manufacturing through dedicated practices of waste reduction/elimination techniques and continuous improvement of production processes as hallmarked in the context of their Toyota Way Principles and TPS (
Alsughayir, 2013). In agreement with this finding, Morgan and Liker (2006) added that Toyota’s
quality achievements and elaborate success history have inspired several business organisations not only in the automobile field but within a variety of industry’s who have sought the adoption and implementation of TPS in their models of production processes. The company continuously works towards organic and profitable growth by identifying, transferring, and implementing best practices to achieve its globally recognized superior performances (
Toma and Naruo, 2017). Moreover, with the availability of systems for sharing and implementing best practices in the public domain, it has become easier for business organisations such as Toyota Motor to spread out the most relevant improvement techniques from one area to the other. Therefore, Oliveira, Sá, and Fernandes (2017) reserved that the exponential increase in research related to quality management, lean production, and continuous improvement as best practices in large-scale manufacturing has demonstrated an increased concern in benchmarking and business excellence. Morgan and Liker (2006) indicated that attaining business excellence comes with significant endeavours not only for Toyota Motors but also for all business corporations globally.
Quality Management 17
Specifically, it is the main reason why, for Toyota, striving for excellence and distinction has turned out to be of high priority. Truly, as an excellent company, Minto (2010) concurred and observed that Toyota has remained clear on the key management basics while working hard to maintain simple business operations, insisting on high quality, and treating with regard both its employees and customers. Similarly, Womack, Jones, and Roos (2007) agreed with the assertion and claimed that apart from Toyota Motor, other major companies such as General Motors have done exceptionally well in ensuring optimized engagements of all their available resources. Therefore, Mácsay and Bányai (2017) noted that most of these companies’ approaches have traced their roots or origin to total quality management, lean production system, and continuous improvement which Toyota Motor has proven to bear positive impacts on its performance as a large-scale automobile manufacturing corporation. 2.2. Quality Management and Culture Within the most recent centuries, automobiles have solely been manufactured by simple craftsmen who could not give any consideration to the important quality aspects such as the generation of product prototypes even where such products bear the same blueprint (
Brah, Wong,
and Rao, 2000).
Foster and Ogden (2008) supported this argument by iterating that the then manufacturers of automobiles were largely concentrating on the culture of customized products instead of focusing on identical motors. Kaynak (2003) informed in addition that different contractors would produce various parts of automobiles using somewhat varied gauges, a cultural business practice which caused slight variations in the sizes of vehicle components/parts leading to dimensional creep; thus, resulting in relatively large differences by the time the final vehicle is produced. Later, Wee and Wu (2009) observed that following Henry Ford’s invention of mass or large-scale production, the need for mass production at much lower costs had risen
Quality Management 18
sharply. Therefore, a vast body of literature in the field/area of manufacturing, business, and management has stressed the relevance of best practices comprising of total quality management in every production activity (
Oakland, 1989; Hansen, 2001; Toma and Naruo, 2017).
Stimec and Grima (2019) intuited that the philosophy of total quality management, maps
the highest excellent standards for processes, services, and products. In parallel to this finding, Holweg (2007) stated that the practice of total quality management could be directly associated with excellence in the large-scale automobile manufacturing industry, and the analysis of its connection with other relevant philosophies such as lean production, and continuous improvement has become quite relevant to the need to improve overall performance in individual
business corporations. Like Ford, Hallam, Muesel, and Flannery (2010) noted that Toyota Motor has equally insisted on establishing a standard gauge for all its contractors responsible to produce
similar auto-parts to achieve performance excellence, eliminating the issue of dimensional creep.
In this way, Toyota Motor has ensured high total quality management of all products which allows it to minimise greatly the rate of producing defects as well as recalls of such from the global market. Moreover, Brah, Wong, and Rao (2000) added that such aspects of quality management have enabled Toyota to reduce the cost associated with waste by having parts collected from different contractors to easily fit on each other. According to Keitany and Riwo-
Abudho (2014), the interchangeability of various parts of automobiles should be highly flexible to enable the assembler to randomly pick components from a group and easily assemble/fix it with other randomly picked component. To achieve such a system of production, the machine used should be in a position of producing such automobile parts with the least minimum variations within the required specification. Therefore, it is quite apparent that for Toyota
Your preview ends here
Eager to read complete document? Join bartleby learn and gain access to the full version
- Access to all documents
- Unlimited textbook solutions
- 24/7 expert homework help
Quality Management 19
Motors, the urge to control or regulate strict compliance to the required design specifications is accorded much credit for deliberately fuelling the evolutionary change of quality principles. Yella and Atem (2007) recounted that quality emphasis within the Office of Physical Plants (OPP) could trace their origin from the year 1981 with the renowned Quality Cycle Program, and in 1989 it progressed with Action Group whereby in 1990 and 1993, continuous quality improvement (CQI) teams were subsequently formed. By 1992, the Joint Commission on Accreditation of Health Care Organisation (JCAHCO) which is based in the United States introduced CQI as their standard recognized to achieve the goal of attaining optimal possible quality level instead of least essential quality level (
American Society for Quality, 2018). The CQI achieves this difference by utilising small steps of quality improvements instead of executing one big step of improvement. Toyota Motor on its own has adopted a comprehensive Japanese term known as ‘kaizen’ which brings together every individual in the organisation. Vost et al. are recognized to be among the very first scholars to have statistically tested the validity of connection/correlation between total quality management as one of the best practices in large-scale manufacturing and the resulting organisational business performance (
Yella and Atem, 2007). These scholars first classified the concept of total quality management as technical or hard and social or soft quality management. The latter social dimension is primarily revolving around effective management of human resources and emphasizes the need for employee involvement, training, teamwork, and productive leadership (
Lai, Weerakoon, and Cheng, 2002; Claver-Cortés et al., 2008; Stamm, Neitzert, and Singh, 2009). Technical dimension, on the other hand, Kakuro (2014) pointed out that it focuses on the fundamental orientation towards the improvement of the methods of production and operations while seeking to identify a viable working approach through the reinforcement of well-defined procedures and
Quality Management 20
processes to ensure continuous improvement of quality of services and products delivered to the customers through the supply chain. In agreement with the findings, Liker (2004) confirmed that the organisational business performance comprises a reduced cost of production and waste, an improved financial outcome in terms of profit, product market, and the return of shareholders which reflected why both the management of both technical and social dimensions comes in handy. Specifically, Toma and Naruo (2017) added that Toyota Motor’s philosophy of quality management has overtime focused mostly on improving its organisational efficiency and effectiveness; however, such cannot be achieved in isolation of either pertinent technical or social issues. Similarly, Yella and Atem (2007) illustrated the productive engagement between the implementation of quality control practice and the organisational performances by showing that both technical and social dimensions should be closely interrelated while mutually supporting one another; thus, portraying the holistic aspect of total quality management initiatives. Therefore, quality management could be declared as a form of best business practices that are adopted by top-performing corporations to achieve some significant impacts on their performances, and Toyota Motor is not an exception. 2.3. Lean Production System and Competitive Skills Essentially, the essence of establishing and sustaining substantial business performance is
the true driving force behind the adoption of the lean production system. Milovanovic (2014) argued that Toyota Motors integrated lean production into its operation with the main objective to create substantial value with the focus of making use of the available resources to their best advantage. Nonetheless, Deflorin and Scherrer-Rathje (2012) considered it imperative to appreciate the fact that lean production could only be actualized in a setting where the topmost levels of management consistently encourage the implementation. This has been the case with
Quality Management 21
Toyota Motor, an organisation that has constantly kept looking for all the possibilities of increasing both their production efficiencies and competitiveness (
Magee, 2010; Yang andYang, 2013). As such, Foster (2008) noted that keeping up to date with the most current and effective lean production management strategies has emerged as one of the key strategies that Toyota Motor has adopted to remain relevant as well as competitive in the global market (
Loyd, 2016) while minimising their costs of production and maintaining continuous improvement in sales and
revenues. Imperatively, it remains the sole responsibility of every staff member to contribute to striking a balance between the management system and quality control to positively influence the
supply chain of the organisation for enhanced customer satisfaction. Moreover, Wickramasinghe and Wickramasinghe (2016) indicated that besides the need to engage every member of the staff in the lean production system, its successful implementation
also depends on the availability of well-trained and high skilled employees. Loyd et al. (2020) complement this finding by declaring that effective training and acquisition of skills is very important in a lean production environment if the organisation is to create a workforce with the capability to take care of increased responsibilities, nurture multi-skilled staff, and develop an environment whereby employees have both the ability and skills to champion for continuous improvement in terms of product quality and customer satisfaction. Similarly, Yang and Yang (2013) suggested that organisation’s give priority to their employees, including allocation of a greater amount of resources for capacity building of their human resources through training have been indicated to have improved productivity and minimized cost of production for over the last 10 years. Toyota Motor has always implemented lean production with a total shift towards exposure as well as problem-solving through group problem solving and teamwork. Therefore, it
would be testified that group problem solving, and teamwork are critical aspects of lean
Your preview ends here
Eager to read complete document? Join bartleby learn and gain access to the full version
- Access to all documents
- Unlimited textbook solutions
- 24/7 expert homework help
Quality Management 22
production systems responsible for removing barriers and improvement of information flow within an organisation (
Loyd, 2016); thus, leading to greatly enhanced productivity. Toyota Motor is reported to be on record for encouraging and supporting group working /systems and utilising the most effective problem-solving approaches/strategies, which has contributed to its highly increased efficiency as well as pride. However, Anvari, Ismail, and Hojjati (2011) insisted that the design of appropriate lean production systems largely depends on the key attributes that could influence the behaviour of the customers since their satisfaction mostly depends on various attributes or aspects such as quality, price, and delivery time of the products and services they are supplied. One scenario is when a group of customers appears to be
more concerned about the price of the services or products and, therefore, the organisation needs to necessarily focus on cost reduction while improving productivity (
Kariuki and Mburu, 2013). Therefore, Toyota Motor has endeavoured to apply competitive business strategies related skills to several dimensions such as based resources, dynamic capabilities, business relationship, essential characteristics, and competitive priorities. 2.4. Continuous Improvement and Product Recall Crisis Phenomenon
With continued production over a period, Lakhe and Mohanty (1993) noted that large-
scale manufacturing organisations are required to increase/adjust the level of predictability, institutionalise key best practices, focus on execution, and process control to enhance their performances. Barney and Kirby (2014) added to this establishment that increased product recall crisis has necessitated most of the companies, especially those in the automobile industry, Toyota
included, to ensure continuous improvement by keeping and adjusting to newly developing technologies in production. Similarly, Bhuiyan and Baghel (2015) concluded that continuous improvement through keeping up to date with the new production technologies is an initiative in
Your preview ends here
Eager to read complete document? Join bartleby learn and gain access to the full version
- Access to all documents
- Unlimited textbook solutions
- 24/7 expert homework help
Quality Management 23
tandem with evolution in product quality which has completely changed from the norm of ‘just sell what you are capable of producing’ to ‘produce what will precisely meet the needs of customers.’ Therefore, Bhuiyan and Baghel (2015) found that the philosophy or concept of continuous improvement has remained to be one of the most critical tools in the controlling of quality within many organisations, both in service and manufacturing sectors. In fact, the popularity of continuous improvement as a concept has become deeply rooted in the business strategy of various large-scale manufacturing organisations, especially with the constantly increasing demand for quality among a diverse range of customers. In drawing to the case of Toyota Motor, the company has in the previous years, encountered several serious operation problems including high operational costs and poor-quality
production. Deflorin and Scherrer-Rathje (2012) noted that minimising waste products was initially a priority idea of Toyota Motor shortly after the Second World War, and its first method was lean production. Arguably, the main aim of implementing such lean production approaches was primarily to produce more with relatively fewer resources (
Pech and Vaněček, 2018). As time goes by, the company considered adopting relevant and effective improvement steps to ensure the elimination of all wastes and subsequent development as well as the execution of just-
in-time system automation. Nkomo (2019) observed that one of the key pillars Toyota Motors have adopted in ensuring effective lean production systems, and continued improvement is a renewed approach or strategy toward quality management which involves the replacement of all the traditional and outdated mass production systems with the most current production technologies.
According to Minto (2010), one of the possible root causes for the product recall in Toyota Motor was its inability to keep pace with the recent changes in technology and rapidly
Your preview ends here
Eager to read complete document? Join bartleby learn and gain access to the full version
- Access to all documents
- Unlimited textbook solutions
- 24/7 expert homework help
Quality Management 24
growing diversity in the demand of customers. Moving forward, Kehr and Proctor (2017) reported on President Hiroshi Okuda’s 1995 initiative to launch an aggressive continuous improvement among other growth plans to reconstitute or remake Toyota Motor, a move which was engraved in the 2005 vision. This continuous improvement strategy focused on increasing Toyota market share across the globe from 7.3 per cent in 1995 up to 10 per cent in 2005 and, eventually, the corporation attained a 9.7 per cent market share which motivated the management
to update their goal to 15 per cent by the end of 2010 (
Kehr and Proctor, 2017). On that note, Toyota was in 2008 on its path to hitting the agreed market share target, unfortunately, an unpredicted product recall crisis pushed the strategy into oblivion, a situation which proved the organisation was not keen to implement the philosophy of continuous improvement to the required standards (
Magee, 2010). Otherwise, if only Toyota would have given continuous improvement the much attention it deserves, it could have operated with new production facilities and kept up with the rapidly increasing motor complexities as well as trends in business
globalisation.
Your preview ends here
Eager to read complete document? Join bartleby learn and gain access to the full version
- Access to all documents
- Unlimited textbook solutions
- 24/7 expert homework help
Quality Management 25
Chapter 3: Method Justification and Explanation This chapter describes the primary research methods used and justifies the methods chosen to conduct the study by highlighting their advantages, specifically in the context of the current study. Where the identified methods are found to have potential disadvantages, the reasons as to why such disadvantages are not that important, or perhaps how the study minimized
such shortcomings through effective design of the research. Moreover, the chapter has discussed the techniques used in the collection as well as analysis of primary data to justify the validity of the results. Therefore, the section discusses research design, sample design, study population, data collection and analysis, and ethical consideration. 3.1. Research Design The design of the current research has focused on the structural framework applied to perform the study as Maxwell’s (2012) recommends, which has specifically, focused on exploring how effective Toyota Motor implements total quality management, lean manufacturing, and continuous improvement tools to remain as the leading care producer. The study adopted the exploratory research design since it is not yet clear if Toyota Motor had been implementing the three main tools identified and whether they are the main factors behind the organisation's success in the global motor industry. According to Ponelis (2015), exploratory design often involves casual research which generally offers in-depth and more detailed phenomena that had been studied previously using a descriptive form of research design. The research design was, therefore, deemed appropriate and suitable for the current study which could not get access and collect primary data and so, had to rely on gathering secondary data presented in journal articles, peer-review journals, books, as well as other academic sources extracted from various databases such as Emerald and Google
Your preview ends here
Eager to read complete document? Join bartleby learn and gain access to the full version
- Access to all documents
- Unlimited textbook solutions
- 24/7 expert homework help
Quality Management 26
Scholar. Moreover, the explorative research design is recognized to bear two-fold objectives, including identifying both cause and effect variables and explaining the correlation or relationship nature shared by the variable (
Reiter, 2013). Similarly, exploratory research has been
applied to identify the three factors and their effects on Toyota Motor's success and establish the connection of these factors to the company being the leading car producer globally. The fact that the study has used exploratory design by adopting a secondary qualitative approach where earlier
literature available in the public domain and relating to total quality management, lean production system, and continuous improvement as implemented at Toyota Motor, according to Lewis (2015) and Malterud, Siersma, and Guassora (2016), offer the basis for the generation of the key study variables of the research’s preliminary conceptual framework. The use of the exploratory design in the current study is justified since the problem was not clear at the onset of the research which conforms to Ponelis’ (2015) recommendation. For instance, I am not certain whether Toyota Motor has been using total quality management, lean manufacturing, and continuous improvement or if so, then the extent or degree to which such techniques and tools have been used. On that note, an informal exploration became essential to enable me to investigate the research topic from several sources by reviewing existing literature while focusing on the specific underpinning concepts and theories, reports, research papers, and case studies existing around quality management, lean manufacturing, and continuous improvement implementation in the automobile industry. 3.2. Study Population and Sample Design
Toyota Motor was the unit of study whereby all the available secondary materials relevant to the operations and management of Toyota Motor were considered. The study prioritized records and literature that targeted various Toyota Motor plants across the globe with
Your preview ends here
Eager to read complete document? Join bartleby learn and gain access to the full version
- Access to all documents
- Unlimited textbook solutions
- 24/7 expert homework help
Quality Management 27
an emphasis on management, operation, and human resource management. The main criteria for which Toyota Motor was selected for study was its outstanding track records of implementing total quality management, lean production, and continuous improvement principles (
Yang and Yang, 2013), which is suspected to have contributed significantly to its overall success in the global motor industry.
3.3. Data Collection and Search Strategy
Onwuegbuzie, Leech, and Collins (2010) asserted that data collection in secondary qualitative research involves gathering of data and may vary from simple review to detailed scrutiny of literature, case studies, and reports among other secondary sources that may be available at the disposal of the researcher. Currently, large volumes of data are gathered and archived by scholars from across the globe for various research that are increasingly becoming widespread. This study considered such data as of important use since it did not only help to save
time, but it was also the only alternative to accomplish the study objective following the move by
Toyota Motor to decline my request to authorise the collection of first-hand data. The data for the study was gathered through the literature review and scrutinising existing
previous journal articles and case studies available externally in the public domain. Terms such as quality management, lean production system, and continuous improvement, Toyota Motor was
used as keywords. Search was conducted to on ProQuest Central, ScienceDirect, and EBSCO databases. These data included both unpublished and published categories. Published data included a range of publications such as statistical statements, financial statements, annual reports, research reports, books, newspapers, magazines, trade and technical journals, websites, public statistics and records, and historical documents relevant to Toyota Motor. On the other hand, unpublished data were acquired from sources such as labour bureaus, trade associations,
Your preview ends here
Eager to read complete document? Join bartleby learn and gain access to the full version
- Access to all documents
- Unlimited textbook solutions
- 24/7 expert homework help
Quality Management 28
and unpublished biographies of the target organisation. Therefore, the study only involved secondary data for the analysis. 3.3.1. Inclusion/exclusion criteria
Studies that focused on quality management, lean production, and continuous improvement aspects were included. All relevant secondary sources including, articles, were include provided they were up to date and not older than 15 years. For articles, only those that used primary qualitative approach were considered for inclusion. Sources that only focused on manufacturing and production without quality, employee involvement, and improvement were excluded as were studies that lacked market performance information about Toyota Motor. 3.3.2. Secondary data
Secondary data consist of second-hand information already gathered and collated by other researchers, usually for different purposes other than that of the current research (
Ellram and Tate, 2016). In that perspective, secondary data has been used to acquire new perspectives pertaining to the implementation of quality management, lean production, and continuous improvement at Toyota Motor. This was considered since the effort to access primary data through semi-structured interviews had proved futile.. Secondary data were, therefore, extracted from other sources external to Toyota Motor. Some of this data had to be drawn from control sheets to establish deviations in the product quality and help in studying the maintenance practices from a range of shift records. The company’s website and the online resources relating to the company’s adoption of the lean production management were useful during the study. In this case, both qualitative and quantitative data were used. For instance, the Toyota company trends in production prior and after the acquisition of the Lean production was much helping. The information, obtained from the secondary sources, facilitated the analysis to provide
Your preview ends here
Eager to read complete document? Join bartleby learn and gain access to the full version
- Access to all documents
- Unlimited textbook solutions
- 24/7 expert homework help
Quality Management 29
meaningful conclusion of the production technique. Published commercial papers including Wall
Steet and New York Times played a crucial role in methodology used. The secondary information they on Toyota commercial progress over years could not be ignored. Journals, Magazines, and combination of other online sources on the prior information on Lean production
and its effect in the entire production process was used in the research. Otherwise, gathering secondary data was justified as less costly and timesaving while providing a larger database than what would be offered when collecting data such data on a face-to-face basis. 3.4. Data Analysis The collected data were first edited to achieve accuracy, consistency, completeness, uniformity, and well-organized for tabulation and coding prior to the final analysis. Since the research collected only secondary data, it necessitated the use of content analysis. The results were presented clearly with the aid of tables, proportions, percentages, pie charts, and frequency distribution. Percentages and frequency distribution were used to establish enablers in the execution of lean production, continuous improvement, and quality control for the success of Toyota Motor. 3.5. Limitations of the Study
Since the study has entirely relied on secondary data sources, including literature review, newspapers, books, magazines, websites, etc., the authenticity, validity, and reliability of the presented information would not be verified and justified. Moreover, the research involved a secondary qualitative approach which according to Long-Sutehall, Sque, and Addington-Hall (2011), the stakes of error in such analysis are high since it depends on how the researcher perceives the subject matter as well as their ability to effectively interpret the information acquired. Moreover, secondary data may be too general as well as vague and in the view of
Your preview ends here
Eager to read complete document? Join bartleby learn and gain access to the full version
- Access to all documents
- Unlimited textbook solutions
- 24/7 expert homework help
Quality Management 30
Ellram and Tate (2016), might not provide meaningful information that would help the researcher to draw insightful conclusions and recommendations. Other limitations such as the possibility of the sample size utilized to produce the presented secondary information being very same, data being outdated, and possible inaccuracy of the secondary could interfere with the quality of the data collected (
Long-Sutehall, Sque, and Addington-Hall, 2011). However, the current study has overcome such limitations through a thorough literature review to equip the me
with the necessary knowledge to establish the underpinning facts, concepts, and theories. The data source had to be checked repeatedly and confirmed. 3.6. Ethical Consideration According to Aluwihare-Samaranayake (2012), ethical issues are especially crucial when the research concerns a qualitative study. Usually, informed consent and confidentiality are treated as the most essential aspects for ethical consideration in any piece of research (
Hesse et al., 2019). Therefore, in the context of the current study, moral principles have been applied in all
stages of research. To begin with, the I looked to seek the consent of data owners as well as bloggers and adhere to copyright guidelines as set by various databases such as websites before extracting any secondary data. Moreover, for reasons of ensuring confidentiality, I remained determined not to expose delicate and sensitive information about the case study company and for that reason, this research will only be submitted to the University. Furthermore, my main objective when conducting the research was focused on using impartially the survey tools and methodological so as to avoid any misleading finding as well as insufficient justification. Additionally, I considered within the study the protection against any inappropriate or misleading
utilisation or misinterpretation of the data collected as a prerequisite.
Your preview ends here
Eager to read complete document? Join bartleby learn and gain access to the full version
- Access to all documents
- Unlimited textbook solutions
- 24/7 expert homework help
Quality Management 31
Chapter 4: Results and Analysis
This chapter presents the results and data analysis with a detailed discussion about total quality management, lean production system, and continuous improvement with specific reference to Toyota Motor, particularly how it has achieved to implement three concepts to emerge and remain as the leading global car producer. While a variety of research methods are available, they are commonly classified as either qualitative and quantitative (
Queirós, Faria, and
Almeida, 2017). Ultimately, the current research has considered qualitative research methodology to achieve the best outcome considering the ethical related constraints. 4.1. Results In the findings, Toyota Motor is found to have embraced and focused on constant improvement through varied operation strategies, including quality management, lean production
system, and continuous improvement. Toyota Motor has utilized these strategies with a clear focus on its performance objectives, which include expansion, waste elimination, improving customer satisfaction, minimising production cost while enhancing profit, and maximise shareholders' value. 4.1.1 Quality management With constantly increasing competition in businesses, the aspect of quality management has become an important consideration factor for business organisations and their customers. Based on the findings in this study, Toyota Motor is found to have perceived and implemented
Your preview ends here
Eager to read complete document? Join bartleby learn and gain access to the full version
- Access to all documents
- Unlimited textbook solutions
- 24/7 expert homework help
Quality Management 32
total quality management as a strategy centered around improving their efficiency, effectiveness, and overall responsiveness to the needs of customers and stakeholders by actively tapping competencies and skills of human resource in strict pursuit of attaining sustainable improvements
to performance (
Vanichchinchai and Igel, 2011.). Similarly, Salleh, Kasolang, and Jaffar insisted,
“
Toyota Motor simply adopted the philosophy of quality management as a form of management approach aiming to foster stable growth as a committed business organization through active engagement of every member (employees and shareholders) in an economical production of quality automobile products that customer would want
’’ (2012, p.1705). In this way, it is explicit Toyota Motor has regarded the concept of total quality management and utilise it as cardinal quality control principles applicable to all its aspects and integration of the entire business processes (
Khalili et al., 2018). Therefore, Toyota Motor has eminently recognized the fact that the achievement of its business excellence remains to be at the centre of total quality management which seems to represent a multidimensional concept that includes several aspects such as the satisfaction of both external and internal customers, emphasis on quality, robust design, systemic vision, quality control, teamwork, training and education, integration of suppliers, strategic process, and cultural change. Going by the Japanese corporation performance report, it is clearly recorded that Toyota Motor Corporation’s performance in the automobile industry has fully attained business excellence. Gao and Low further established, “
The main source of business excellence for Toyota
Motor is purely attributable to its TPS and the genesis of such system would be directly traced from the five main precepts of Toyoda encapsulating thinking and general life of Sakichi
” (
2014, p.672). According to Bani Ismail (2012), the first precept emphasizes Toyota Motor’s mission to contribute to the holistic development of society and improvement of its welfare based on the
Your preview ends here
Eager to read complete document? Join bartleby learn and gain access to the full version
- Access to all documents
- Unlimited textbook solutions
- 24/7 expert homework help
Quality Management 33
common idea of benefiting the nation at large. The second precept encourages constant action towards improved production through invention and effective application of new technology. The
third precept primarily prioritized features (simplicity, integrity, and loyalty) of the Mikawa community which is known as the home of Toyota Motor’s headquarters. The fourth precept provisioned that employee’s must be held with the highest regards and treated as an important part of the Toyota fraternity; thus, the internal setting of the organisation should be made very appropriate, pleasant, and beneficial for them. The final precept called and advocated for meaningful reconciliation between morality and the business. Thun et al. (2010) discovered that the need for absolute waste elimination was the main foundation that drove the concept of TPS (Toyota Production System) as it perceived waste as any form of human activity that consumes resources but eventually creates no value. “
Toyota Motor has aimed to offer the highest quality at the lowest possible costs and within shortest achievable lead time with automation and just-in-time being the two fundamental pillars of its TPS strategy
” (
Htun, AMaw, and Khaing, 2019, p.41). In a busy flow process, Toma, and Naruo (2017) described just-in-time as an operational phenomenon where the right component reaches the assembly line at the appropriate time and in the recommended quantity and quality. Although as a concept it appeared quite simple, Toyota Motor at first found the implementation of just-in-
time proving challenging since it necessitated the elimination of essential inventories. On the other side, automation itself signified that the machine had the capability of detecting and avoiding errors such as defective products and services autonomously (
Bani Ismail, 2012). The two key pillars have been perceived to work in coordination to sustain the effectiveness of the concept of the Toyota Production System as illustrated in a simple flow chart in Figure 1.
Your preview ends here
Eager to read complete document? Join bartleby learn and gain access to the full version
- Access to all documents
- Unlimited textbook solutions
- 24/7 expert homework help
Quality Management 34
Figure 1
. Presentation of just-in-time and automation as two key pillars supporting TPS (Andrew
Male, 2021)
Khalili et al. (2018) found that the production system implemented in Toyota Motor has encompassed the aspect of technology application in terms of machinery and equipment as well as meta-technology both in form of methods, techniques, and know-how. Salleh, Kasolang, and Jaffar are quoted stating, “
The corporation’s production system structured in such a way that it entirely based on the consistency of the underpinning business philosophy emphasizing the distinctive relevance accorded to system’s notal point and quality aspect that compels the need for effective implementation of total quality management at Toyota Motor
” (2012, p.1703). In that regard, it is depictable that the element of quality management manifests in the invisible and visible parts of Toyota Motor’s production system. Marksberry et al. (2010) further supported the
finding by clarifying that while the invisible part implies routine (kata) and management thinking, the visible part consists of applicable principles such as zero-defect principle and instruments such as statistical quality control and practices, including quality circle. The invisible
and visible work by interlocking and complementing each other into a complex production system incorporating multiple interconnected elements such as continuous improvement and lifelong learning. In return, the aspect of integrating quality management in the production Toyota Production System (TPS)
Automation
Just-in-Time
Your preview ends here
Eager to read complete document? Join bartleby learn and gain access to the full version
- Access to all documents
- Unlimited textbook solutions
- 24/7 expert homework help
Quality Management 35
system has contributed significantly to the attainment of business excellence (
Phan and Matsui, 2010). In that light, Toyota Motor has adopted certain best practices such as customer focus and employees’ empowerment among others as core strategies to pursue total quality management. 4.1.1.1 Customer focus The most important best practice in total quality management is the attention that the organisation accords to their customers. In their study, Isac stated, “
the aspect of customer focus emerges within an automotive corporation such as Toyota Motor in that, the product quality must fully satisfy as well as overcome the expectation of the customers
” (2010, p.188). The best practice now begins with the identification and subsequent satisfaction of the needs of the customer. Thun, Drüke, and Grübner (2010) stated by maintaining that, a good system of total quality management must admit, even perfectly processed and assembled products have significantly reduced values provided it does not merit what the customer expected. In that regard, Toyota Motor has always maintained that the required quality level of their
automotive products has always been determined by their potential customers from across the globe. However, Shammot reported, “
Toyota Motor has always admitted it as a challenge to establish a permanent solution as to what the customer would want or desire since their preferences and tastes do vary widely from time to time as well as from one population to the other
” (2011, p.27). Specifically, the customer preferences in the automotive industry quickly change as from four-wheeled vehicles to small cars and then back to four-wheeled cars. Toyota Motor, however, has overcome this challenge by constantly gathering relevant information through meeting with customers, market studies, and research groups so as to keep updated with preferences of their customers leading to their success in the competitive global automotive
Your preview ends here
Eager to read complete document? Join bartleby learn and gain access to the full version
- Access to all documents
- Unlimited textbook solutions
- 24/7 expert homework help
Quality Management 36
industry (
Phan and Matsui, 2010). Toyota has, been compelled to establish a mechanism for perfect balance between specification quality and product quality as shown in Figure 1 below. Figure 2. Interconnection between specifications quality and product quality (Andrew Male, 2021)
4.1.1.2. Empowerment of employees Amasaka (2013) found the involvement of employees is a critical part of business requirements to achieve significant performance improvement. “
The impacts of human resources
in an organization largely depend on the type of empowerment accorded to them
” (
Isac, 2010, p.191). Toyota Motor has elevated the employees’ role to an extent that is completely different from what it used to be like in the traditional manufacturing system as part of total quality management (
Jones, Latham, and Betta, 2013). Employees are fully empowered and given equal platforms to participate in making decisions that pertain to quality management along the chain of production. On that note, Toyota Motor has repeatedly been on the record for considering their employees as vital elements of commitment and effort towards the attainment of high-quality products (
Sullivan, 2011). In fact, their suggestions are executed instantly, and technical Process result quality Quality of specification
Expectations
Needs
Desires
Specifications
Requirements Products
Products
Your preview ends here
Eager to read complete document? Join bartleby learn and gain access to the full version
- Access to all documents
- Unlimited textbook solutions
- 24/7 expert homework help
Quality Management 37
contributions towards quality performance are highly valued. In order for employees to take part in production line quality management, Toyota Motor has accorded employees extensive and continual training in total quality management equipment and tools (
Isac, 2010). Participation in decision-making with the corporation involves logical activity processes where employees opt for action variants applicable for multiple possibilities. Based on this principle, the most effective
and appropriate quality control decisions are underpinned by safe and complete information, which are deemed to be analytically intuitive and logical in terms of applicability. Therefore, effective empowerment of employees involves an effective perception of the needs of the customer and their full reflection in the quality (Q5) of the finished products and must be composed based on decision-making as well as measures in other quality development stages (Q1-Q4) within the system. Refer to Figure 3. Decisions Measures
Figure 3.
Major checkpoints for quality (Andrew Male, 2021)
Quality Management
Inputs
Tenderer Systems Transformation
performances
Outputs
Beneficiary
system Q1
Q2
Q3
Q4
Q5
Your preview ends here
Eager to read complete document? Join bartleby learn and gain access to the full version
- Access to all documents
- Unlimited textbook solutions
- 24/7 expert homework help
Quality Management 38
4.1.2. Lean production system
At Toyota Motor, the production system is exactly synonymous with lean manufacturing or lean production terms which researchers have mainly coined in the International Motor Vehicle Program. Haleem (2015) asserts that Toyota Motor’s lean production system has positively impacted the wider manufacturing industry. By using various lean tools, Toyota Motor
has achieved valuable and continuous propositions for its main stakeholders. “
Toyota’s lean production system initiative is largely focused on increasing turnovers and cost reduction by continuously and systematically zero involvement in non-value-added activities
” (
Powell and Reke, 2019, p.65). Owing to the competitive automotive market, Toyota Motor has remained keen to use lean production strategy as the ultimate solution to success and survival challenges in
the manufacturing industry; therefore, helping it to remain the best performer while minimising product recall rates, volume of wastage, and overcoming market competition (
Forrester et al., 2010). The organisation has used lean manufacturing with the aim of achieving its target productivity by introducing maintainable and easy-to-apply tools and techniques. The fundamental principle of the lean production system is in tandem with Toyota Motor’s focus to ensure total waste reduction or elimination which necessitates the corporation to
engrain the concept into its culture and convert every process of production into significant profits (
Khalili et al., 2018). However, effective implementation of a lean production system requires several tools including the Five S, Six Sigma, Kaizen, and value stream mapping, as well as Kanban. Despite partially making use of all these tools for the implementation of the lean
production system, Toyota Motor is widely known to have specialized in using Kanban.
Your preview ends here
Eager to read complete document? Join bartleby learn and gain access to the full version
- Access to all documents
- Unlimited textbook solutions
- 24/7 expert homework help
Quality Management 39
4.1.2.1. Kanban
Kanban was initially developed by Ohno on the production lines of Toyota and it eventually emerged as the perfect solution to the problem of frequent overproduction. “
The tool was used to establish the most effective way of minimising the wastes and ensuring quality production by establishing appropriate means of delivering the necessary quantity and quality of
items when required
” (
Adnan et al., 2013, p.6). Mohamed (2016) argued that the Kanban tool could be interpreted from Japanese as a signal or card and applies a visual input deployable in a pull system. Being a lean tool.
Thun, Drüke, and Grübner (2010) have similarly recommended Kanban for use in the development of effective automotive production by pulling materials out of the production line within the mindset of ‘just-in-time’ concept. The application principles of the Kanban tool constitute the promotion of material restocking only whenever it is needed or necessary by receipting and issuing prompt signals normally in form of cards. Toyota Motor engages this process both externally and internally to ensure it effectively address the needs of their customers in a more efficient manner by supplying only the specific automotive products that the customers need with zero recalls (
Mohamed, 2016). The product delivery chain is monitored, and prompt improvements are executed if needed. 4.1.2.2. Perceived benefits of the lean production system
The introduction and implementation of the lean production system is one of the strategies that has not only contributed to the success of Toyota Motor but has specifically enabled them to attain several benefits including waste reduction. “
Specifically, through the use of lean production, Toyota Motor has achieved eighty per cent reduction of wastes, fifty per cent reduction of cost of production, fifty per cent decrease in time of the manufacturing cycle, fifty per cent reduction in labour cost while increasing or maintaining output, and eighty per cent
Your preview ends here
Eager to read complete document? Join bartleby learn and gain access to the full version
- Access to all documents
- Unlimited textbook solutions
- 24/7 expert homework help
Quality Management 40
reduction in inventory
” (
Holweg, 2007, p.431). Moreover, Powell and Reke (2019) added higher flexibility in the production system, higher profits, higher quality, enhanced cash flow through advancing buying and shipping frequencies, and improved strategic focus as some of the benefits
associated with lean implementation. Nonetheless, it is imperative to note that continued emphasis on waste reduction guarantees endless benefits or profits to the organisation. 4.1.3. Continuous improvement (Kaizen)
Often, the aspect of total quality entails “soft” management elements such as organisational and leadership culture and “hard” management elements such as statistical techniques and organisational systems (
Marksberry et al., 2010). As a philosophy, continuous improvement is entirely attributed to Kaizen who acknowledged it as an important component of the Toyota Production System which assumes that everyone, including workers and managers, must be engaged in making small but continuous efforts for improvement at the workplace. There are several Kaizen strategies such as standardized-do-check-act cycle, cost, quality, delivery cycle, and plan-do-check-act cycle among others that are target towards achieving a common objective of total waste (muda) elimination.
By considering the working mechanisms of the concept of continuous improvement, many researchers have liked it with normal maintenance. As such, Prošić (2011) insisted that continuous improvement alongside an emphasis on the development of staff are the most critical aspects of any identifiable maintenance strategy. Similarly, Toyota Motor is indicated to have implemented the concept of continuous improvement as a special form of maintenance strategy. Iwao stated, “
Toyota has effectively utilized total productive maintenance concept as the key approach to aligning its essential maintenance organizational structure as to encourage the philosophy of continuous improvement in its daily maintenance practices
” (2017, p.31). In
Your preview ends here
Eager to read complete document? Join bartleby learn and gain access to the full version
- Access to all documents
- Unlimited textbook solutions
- 24/7 expert homework help
Quality Management 41
today’s globally competitive automotive market, Toyota Motors has deliberately adopted continuous improvement practices as a strategy to keep it afloat amidst the increasing industry changes marked by continued streaming of new innovative information. 4.2. Analysis
From the results, it is clear the concept of total quality management, lean production system, and continuous improvement bear the same origin which is the evolution of manufacturing quality in Japan, though developed varyingly. Essentially, the concept of total quality management, lean production system, as well as continuous improvement became popular philosophies in the early 1990s to which Toyota Motor has capitalised to minimise cost and improve productivity (
American Society for Quality, 2018; Thun, Drüke, and Grübner, 2010). In fact, many researchers, practitioners, as well as scholars in automotive manufacturing have subsequently pointed to Toyota Motors for many businesses and organisations in the global automotive manufacturing industry to emulate. 4.2.1. Quality management systems (QMS) for minimised costs and improved productivity
According to Gao and Low (2014), Toyota corporation identified clear quality criteria and parameters that an effective quality management system advocated and recognized the need to tap opportunities to achieve minimized costs of production and improved productivity. Similarly, Barney and Kirby (2014) and Iwao (2017) reported that the main objective of the Toyota Corporation undertaking the initiative to implement in totality the concept of total quality
management, has been to improve its overall operational performance. The implementation process has, therefore, involved the corporation in an active application of standards for quality management to all its key business elements as procurement, manufacturing, packaging and product delivery for the satisfaction of customers (
Marksberry et al., 2010). Furthermore,
Your preview ends here
Eager to read complete document? Join bartleby learn and gain access to the full version
- Access to all documents
- Unlimited textbook solutions
- 24/7 expert homework help
Quality Management 42
Hallam, Muesel, and Flannery (2010) remarked that the implementation of total quality management demanded Toyota Corporation to apply quality management standards in totality adopting a total quality process that is simply describable, clear and unambiguous throughout
Htun, Maw, and Khaing (2019) established that Toyota treated total quality processes as an integrated philosophy in management and set of organisational practices that focus on satisfying customer needs, continuous improvement, and increased teamwork through inclusive employment involvement. Additionally, the organisation applied the concept to attain competitive benchmarking, effective process design, frequent measurement of results, team-
centered problem solving, and a close relationship with the suppliers (
Chiarini, Baccarani, and Mascherpa, 2018). In return, Toyota is seen to have consistently capitalized on all the provisions associated with quality management systems which have enabled it to significantly minimise its cost production which improve productivity. Nevertheless, Bani Ismail (2012) presented a contrary finding that the execution of total quality management did not only come with benefits to the corporation but has also presented myriads of challenges which squarely lies on how operations and management should work in coordination to attain the utmost potential for successful delivery of automotive products to customers. 4.2.2. Quality control, lean production, and continuous improvement and market branding
Based on the results of the study, it is explicit that establishing an integrated system constituting all three factors; quality management system, lean production, and continuous improvement directly leads to the development of a hybrid and efficient operation system (
Loyd, 2016). Continuous learning from operational experiences is indicated to be one of the benefits accruing from the use of such a hybrid system, especially for mass manufacturing settings. Powell and Reke (2019) stressed that such learning from experiences serves as a key factor
Your preview ends here
Eager to read complete document? Join bartleby learn and gain access to the full version
- Access to all documents
- Unlimited textbook solutions
- 24/7 expert homework help
Quality Management 43
responsible for the unlocking of organisations’ market potentials and advocates for its development as a global firm by repositioning and adjusting the product brand. Apparently, it is without doubt through the effective integration of quality management system, lean production, and continuous improvement aspects that Toyota is today globally recognized as one best automotive manufacture producing what is deemed to be the most efficient and top selling brand worldwide. Thun, Drüke, and Grübner (2010) stated that Toyota Corporation has significantly learned
from global best practices ranging from quality management, lean manufacturing, to continuous improvement which has not only improved its productivity but also contributed to a better position of its brand in the global market. Similarly, Kehr and Proctor (2017) observed that, in 1955, Toyota is indicated to have estimated its brand as the third after Ford and General Motors and later as the best in 2005. The company had to learn from the then giant car makers and eventually came up with its own production system, also currently known as the TPS, which it relied on to design and develop its own outstanding brand (
Foster, 2008; Sullivan, 2011). Eventually, this system positioned Toyota to specialise on improving its brand by mixing quality control, lean production, and continuous improvement precepts as ingredients to market its brand, specifically by manufacturing only automotive products that customers order both in the most efficient way and delivered quickly. Therefore, the need to satisfy customers’ needs, compete effectively in the global market, and improve profit. It is undoubtedly the key informants of the corporation to put more emphasis on the three production factors for effective brand marketing.
Your preview ends here
Eager to read complete document? Join bartleby learn and gain access to the full version
- Access to all documents
- Unlimited textbook solutions
- 24/7 expert homework help
Quality Management 44
4.2.3. Modern production system and product quality
Salleh, Kasolang, and Jaffar (2012) reported that through effective implementation of modern quality management and lean production system, Toyota Motor has been able to achieve a significant strategic advantage in the automotive industry. Further, Benders and Morita (2007) supported the finding stating that such advantages are associated with advancement in operational performance resulting from better positioning for market competitiveness. In this way, the organisation has achieved a massive increase their global market share by enhancing the
product quality. Shammot (2011) observed that lean production has set Toyota Motor a favourable ground
for mass production which has enabled it to attain 90% reduction in lead-time, 90% reduction in inventory, 90% reduction in quality cost, and 50% increase in productivity of labour. Subsequently, the quality of products delivered to customers alongside the supply chain is greatly
enhanced with a significant decline in the cases of defective products or zero recalls of the products on the market. Drawing from these benefits, Nkomo (2019) noted that implementing lean equally implies that the organisation has completely examined all areas of operation, including how orders are processed, the way manufacturing is carried out, and how the raw materials are procured. Conclusively, it is undeniable that the adoption of modern quality management and production system simply buys the idea of total approach which necessitate the need for manufacturing organisations to bring together all socio-technical systems which involves combining socio-systems and technology to test and approve products’ quality. With all these in place, Toyota has always achieved one-time delivery of products with zero or minimal defects or recall of products already delivered in the market.
Your preview ends here
Eager to read complete document? Join bartleby learn and gain access to the full version
- Access to all documents
- Unlimited textbook solutions
- 24/7 expert homework help
Quality Management 45
4.2.4. Quality control, lean production, and continuous improvement and supply chain
From the presented results, it is evidenced that both quality control, lean production, and continuous improvement bear close association and work to complement one another to ensure a smooth flow in the supply chain. Yang and Yang (2013) found that the concept of total quality is a philosophy of management that, for Toyota Motor, has progressed incrementally with time and still maintains doing so with the concept of continuous improvement as the key driver toward sustainable organisational productivity. Since both maintenance and quality aspects are inevitable
complimentary within a manufacturing environment, total quality control and lean production do
share several regulatory and management philosophies in common and continuous improvement (
Iwao, 2017; Wee and Wu, 2009). Other philosophies shared include a cross-functional approach and employee involvement. In that regard, Toyota Motor is reported to have brought together and
executed quality control, lean production, and continuous improvement as a set in several ways such by establishing customers’ requirements (both external and internal), complying with the dynamics in manufacturing quality, measuring the level of success, and continued check on the customers’ expectations or needs to identify parameters that require improvement (
Kakuro, 2014). In other words, Toyota Motor has implemented continuous improvement as in specific set
routines to help improve their overall performances. According to Khalili et al. (2018), Toyota Motors successful implementation of continuous improvement is largely since its management has embraced the philosophy involving a dynamic process that focuses on programs for improvement as well as their relationships to other related organisational aspects within the corporation. As part of the implementation strategies, Toyota Motor considered several routines to develop a mutual association or relationship between quality control, lean production, and continuous improvement for
Your preview ends here
Eager to read complete document? Join bartleby learn and gain access to the full version
- Access to all documents
- Unlimited textbook solutions
- 24/7 expert homework help
Quality Management 46
maximum potential in the organisation using routines as capturing and deploying individual learning and learning from daily experiences among others (
Vanichchinchai and Igel, 2011). This
approach supports Rajasekera’s (2013) findings which alluded that a learning-centered work environment has motivated employees to offer feedback for the assessment of performance; thus,
enabling active interaction between quality control, lean production, and continuous improvement activities outcomes, to be integrated into the organisation’s knowledge base. This would ensure a strong performance support base for enhanced organisational productivity necessary for the effective operation of the supply chain.
The application of lean production in running the company has seen to have worked in the company. For Instance, the quality control and continuous improvement, quality management
systems portraited consistent improvement in the consistency, efficiency, and effectiveness of the
company’s production. Besides, the increase in efficiency and production of automobiles over years since the incorporation of Lean production in the manufacturing process is witnessed. This proved the reliability and validity of the test.
Chapter 5: Recommendations and Implementation 5.1. Conclusion and Implementation
In conclusion, today’s business organisations especially those in the mass production industry are competing in an increasingly adverse and volatile market environment. This study has mainly contributed to the enhancement of existing literature from the perspective of mass production quality. Based on a theoretical standpoint, it is to note that this has achieved some extent of clarification concerning the concept of quality management, lean manufacturing, and continuous improvement as far as performance is concerned. The corporations are, therefore,
Your preview ends here
Eager to read complete document? Join bartleby learn and gain access to the full version
- Access to all documents
- Unlimited textbook solutions
- 24/7 expert homework help
Quality Management 47
compelled to seek and obtain exemplary performance if they wish to develop and survive in the highly globalized business world. In that regard, effective execution of quality control, lean production system, and continuous improvement of product quality and delivery through the supply chain has turned out to be key priorities for many automotive manufactures of which Toyota Corporation is no exception. Specifically, Toyota Motor is currently on record for effectively applying quality and lean
controls as well as continuous improvement practices with an explicit focus on improving its operational performance specifically for the satisfaction of potential customers. Through the implementation of these three factors, Toyota Motor has managed to address and resolve nearly all its organisational problems such as minimal defects and recalls of products, improved product
branding, and overcoming market competition. Through ensuring continuous improvement and lean manufacturing, Toyota has found a powerful and reliable approach to collect and synchronise multiple change initiatives that are constantly progressing through, which has kept it
a leading car producer for over the past ten years. As a business corporation, Toyota Motor has objectively pursued lean manufacturing of automobile products, specifically in response to its need and desire to fundamentally improve its market brand for business competitiveness by minimising the cost of production while enhancing
quality as well as customer responsiveness such as fulfilling delivery time. Moreover, the corporation has adopted lean production and quality control practices as strategies to not only remain competitive in the global automotive market but also to ensure profitability. However, sustaining such practices it is imperative for several sufficient strategies and approaches to help solve possible associated adverse impacts; thus, improving the overall organisational performance. Undoubtedly, Toyota Motor has appropriately implemented these practices, and
Your preview ends here
Eager to read complete document? Join bartleby learn and gain access to the full version
- Access to all documents
- Unlimited textbook solutions
- 24/7 expert homework help
Quality Management 48
based on the results of the literature and the qualitative secondary study, the corporation has subsequently attained significant savings which have resulted in decreased defect recalls of products, reduced cost of production, and lower cost of supervision. The corporation has achieved top market branding, low cycle time, increased investment and profit margin, increased sales, and customer responsiveness through ensuring prompt satisfaction. Furthermore, several significant strategies and approaches are influencing the implementation of the identified factors and based on the outcomes of this study, it has been established that staff involvement, customer focus, inventory management system, effective integration of technology, and just-in-time substantially improves the performance of lean, quality control, and continuous improvement practices. Nevertheless, the research discovered several challenges which seem to impede Toyota in implementing lean production, quality control, and continuous improvement system. These include the dire need for skilled personnel, accurate forecasting of production, lack of close relationship with suppliers, inadequate ICT infrastructure, value chain integration complexities, insufficient implementation time, high staff training cost, and staff resistance. The activities involved in continuous improvement are found to be associated with the change of material aspects of the organisational routine, usually executed because of performing related improvement activities, which mostly faces the risk of staff resistance. This finding is consistent with the theoretical model of routine dynamics which admit that the uptake of new technologies and operation technique in an organisational setting are often faced with the challenge of resistance among the staff which lowers the rate of absorption. However, Toyota has
constantly relied on the synchronisation of the three main aspects of routine such as performative, ostensive, and material: attaining better management of its continuous
Your preview ends here
Eager to read complete document? Join bartleby learn and gain access to the full version
- Access to all documents
- Unlimited textbook solutions
- 24/7 expert homework help
Quality Management 49
improvement activities. Additionally, the corporation has ensured only a small and manageable range of possible responsibilities or actions for its employees, which enable it to increase their probabilities of achieving the intended effects of continuous improvement. Moreover, Toyota has
deliberately embraced the fact that making artifacts (production material aspects), and not employees, accounts for organisational performance as one of the essential strategies to narrow or minimise the action range for employees. In this way, the organisation has not only achieved effective employee’ involvement but has also ensured their specialisation, which in turn contributes to improved product quality and subsequent customer satisfaction. Coherently, firms, especially in the mass production arena, where artifacts are held accountable for performance whereas employees for strict adherence to procedures and rules have successfully changed for better their production operations and significantly improved their overall performance in the long run. Effective synchronisation of quality control, lean production, and continuous improvement are proven means for supplementing the concerted market branding efforts by resolving human resources, equipment, and technologies among other related challenges that adversely influence the performance of a mass automotive manufacturing system. From the study of Toyota Motors, it is demonstrated clearly that the implementation of quality control, continuous improvement, and lean production practices in large-scale manufacturing corporations is responsible for effective optimized employee involvement and equipment effectiveness, elimination of minor stoppage of processes, waste reduction, and promotion of autonomous operation maintenance necessary for minimised production cost and overall improved productivity. The use of lean manufacturing and quality control practices has significantly helped Toyota Corporation to improve the synergy amongst its various departments
Your preview ends here
Eager to read complete document? Join bartleby learn and gain access to the full version
- Access to all documents
- Unlimited textbook solutions
- 24/7 expert homework help
Quality Management 50
of production, quality control, and other improvement functions. Such strategies have resulted in the minimisation of defects, improved reliability of manufacturing processes, and affecting operation cost reduction; hence, strengthening all the sustainability efforts of Toyota Corporation
to win the cut-throat global market competition and achieve business excellence. These production factors have, therefore, provided excellent means to enhance the overall efficiency, especially of the mass production or manufacturing system such as for Toyota Motor which has for over remained the leading car producer globally. The results obtained from the research is a clear indication that Lean production effectively and affordably works in the manufacturing sector. With the concept of Lean production, it is evident that consistent production, high quality,
build of brand, expansion, competitiveness among other factors are achieved by the company at little costs of production and easy management. 5.2. Recommendations
The study conducted has so for generated great ideas and knowledge leading to the birth of several recommendations for either implementation or for consideration in future studies. All the lean production, quality control, and continuous improvement practices at Toyota Motor are part of their business excellence attributes and are recommended for prompt dissemination and implementation in other corporations, especially those dealing in mass production. Furthermore, research should be conducted as to help widen the spectrum of successful practices of these manufacturing philosophies and expand the analysis in relation to the concept of the TPS. To improve on productivity and waste reduction, it is recommended for the management of organisations to try to match resource availability and ability with the task for execution to improve effectiveness and efficiency in product delivery along the supply chain.
Your preview ends here
Eager to read complete document? Join bartleby learn and gain access to the full version
- Access to all documents
- Unlimited textbook solutions
- 24/7 expert homework help
Quality Management 51
Despite the need for the organisation to increase the level of specialisation in various production departments by narrowing the range of actions for employees, but this study recommends merging and combing some of the roles. Such strategies will help large-scale manufacturing corporations to minimise their wage bills while maximising the available scarce resources and at the same time sharpen their competitive edges in the global market. Similarly, management of various production operations is recommended as essential to ensure consistency
between ostensive, production material aspects, and performative aspects of the organisational daily work routine. Moreover, the production material aspects are recommended for the promotion of creativity in manufacturing organisations even if the artifact element could prove to
constrain employees’ action within the organisation. The findings of the current study have disclosed the fact that productivity improvement and customer satisfaction do not simply occur; therefore, the study recommends the need for standard operation procedures (SOP’s) as well as incentives necessary for strict adherence to such protocols. Since the current study has only involved qualitative exploration, future studies requires quantitative research with statistical support to substantiate the essence of implementing quality control, lean production, and continuous improvement in manufacturing operation and supply chain management. Additionally, further study is needed to establish how automotive manufacturing operations at Toyota Corporation would change if employee involvement and their range of action, as well as customer focus, are sufficiently managed. Furthermore, future studies should also investigate critical aspects, including organisational corporate culture and institutional elements, and establish how they impact the overall performance and productivity of
large-production plants. Lastly, this study has investigated only one corporation (Toyota Motors) without control case studies for comparisons, therefore, it is recommended further studies to
Your preview ends here
Eager to read complete document? Join bartleby learn and gain access to the full version
- Access to all documents
- Unlimited textbook solutions
- 24/7 expert homework help
Quality Management 52
involve multiple organisations for comparative analysis to establish the effectiveness of implementing quality control, lean production, and continuous improvement concepts and their impacts on productivity, operation performance, employee involvement, market branding, waste reduction, defects, and product recalls, and the level of customer satisfaction.
Your preview ends here
Eager to read complete document? Join bartleby learn and gain access to the full version
- Access to all documents
- Unlimited textbook solutions
- 24/7 expert homework help
Quality Management 53
References
Adnan, A.N.B., Jaffar, A.B., Yusoff, N.B. and Halim, N.H.B.A., 2013. Implementation of just in time production through Kanban system.
System
,
3
(6).
Alsughayir, A., 2013. ’The Impact of Quality Practices on Productivity and Profitability in the Saudi Arabian Dried Date Industry. World Scholars
.
Aluwihare-Samaranayake, D., 2012. Ethics in qualitative research: a view of the participants' and
researchers' world from a critical standpoint.
International Journal of Qualitative Methods
,
11
(2), pp.64-81.
Amasaka, K., 2013. The development of a total quality management system for transforming technology into effective management strategy.
International Journal of Management
,
30
(2), p.610.
American Society for Quality, 2018. What Is quality management (TQM)?
[Online] Available at: http://asq.org/learn-about-quality/total-quality-management/overview/overview.html
. [Accessed 10 March 2021].
Anvari, A., Ismail, Y. and Hojjati, S.M.H., 2011. A study on total quality management and lean manufacturing: through lean thinking approach.
World Applied Sciences Journal
,
12
(9), pp.1585-1596.
Bani Ismail, L., 2012.
An evaluation of the implementation of Total Quality Management (TQM) within the construction sector in the United Kingdom and Jordan
. Doctoral dissertation, University of Huddersfield.
Barney, H. and Kirby, S.N., 2014. Toyota production system/lean manufacturing.
Organizational
improvement and accountability: Lessons for Education from Other Sectors
, pp.35-50.
Your preview ends here
Eager to read complete document? Join bartleby learn and gain access to the full version
- Access to all documents
- Unlimited textbook solutions
- 24/7 expert homework help
Quality Management 54
Benders, J., and Morita, M., February 21, 2007. Changes in Toyota Motors’ operations management.
Bhuiyan, N. and Baghel, A., 2015. An overview of continuous improvement: from the past to the
present. Management Decision
.
Brah, S., Wong, J. and Rao, B., 2000. ‘TQM and business performance in the service sector: a Singapore study’ Chiarini, A., Baccarani, C. and Mascherpa, V., 2018. Lean production, Toyota production system and kaizen philosophy.
The TQM Journal
.
Claver-Cortés, E., Pereira-Moliner, J., Tari, J.J., and Molina-Azorin, J.F., 2008. ‘TQM, managerial factors and performance in the Spanish hotel industry.
Deflorin, P. and Scherrer-Rathje, M., 2012. Challenges in the transformation to lean production from different manufacturing-process choices: a path-dependent perspective.
International Journal of Production Research
,
50
(14), pp.3956-3973.
Ellram, L.M. and Tate, W.L., 2016. The use of secondary data in purchasing and supply management (P/SM) research.
Journal of Purchasing and Supply Management
,
22
(4), pp.250-254.
Forrester, P.L., Shimizu, U.K., Soriano
‐
Meier, H., Garza
‐
Reyes, J.A. and Basso, L.F.C., 2010. Lean production, market share and value creation in the agricultural machinery sector in Brazil.
Journal of Manufacturing Technology Management
.
Foster, S. T. Jr. and Ogden, J., 2008. On differences in how operations and supply chain managers approach quality management.
Foster, S.T. Jr., 2008. Towards an understanding of supply chain quality management.
Your preview ends here
Eager to read complete document? Join bartleby learn and gain access to the full version
- Access to all documents
- Unlimited textbook solutions
- 24/7 expert homework help
Quality Management 55
Gao, S. and Low, S.P., 2014. The Toyota Way model: an alternative framework for lean construction.
Total Quality Management & Business Excellence
,
25
(5-6), pp.664-682.
Haleem, R.M., Salem, M.Y., Fatahallah, F.A. and Abdelfattah, L.E., 2015. Quality in the pharmaceutical industry–A literature review.
Saudi Pharmaceutical Journal
,
23
(5), pp.463-469.
Hallam, C.R., Muesel, J. and Flannery, W., 2010, July. Analysis of the Toyota Production System
and the genesis of Six Sigma programs: An imperative for understanding failures in technology management culture transformation in traditional manufacturing companies. In
Picmet 2010 Technology Management for Global Economic Growth
(pp. 1-11). IEEE.
Hansen, T., 2001. ‘Quality in the marketplace: a theoretical and empirical investigation’ Hesse, A., Glenna, L., Hinrichs, C., Chiles, R. and Sachs, C., 2019. Qualitative research ethics in the big data era.
American Behavioral Scientist
,
63
(5), pp.560-583.
Holweg, M., 2007. The genealogy of lean production.
Journal of Operations Management
,
25
(2), pp.420-437.
Htun, A.R.K.A.R., Maw, T.T. and Khaing, C., 2019. Lean Manufacturing, Just in Time and Kanban of Toyota Production System (TPS).
Isac, N., 2010. Principles of TQM in automotive industry.
Romanian Economic and Business Review
,
5
(4), p.187.
Iwao, S., 2017. Revisiting the existing notion of continuous improvement (Kaizen): literature review and field research of Toyota from a perspective of innovation.
Evolutionary and Institutional Economics Review
,
14
(1), pp.29-59.
Your preview ends here
Eager to read complete document? Join bartleby learn and gain access to the full version
- Access to all documents
- Unlimited textbook solutions
- 24/7 expert homework help
Quality Management 56
Jones, R., Latham, J. and Betta, M., 2013. Creating the illusion of employee empowerment: lean production in the international automobile industry.
The International Journal of Human Resource Management
,
24
(8), pp.1629-1645.
Kakuro, A., 2014. Development of ‘Science TQM’, a new principle of quality management: effectiveness of strategic stratified task team at Toyota.
International Journal of Production Research
,
42
(17), pp.3691-3706.
Kariuki, B.M. and Mburu, D.K., 2013. Role of lean manufacturing on organization competitiveness.
Industrial Engineering Letters
,
3
(10), pp.81-82.
Kaynak, H., 2003. The relationship between total quality management practices and their effects on firm performance.
Kehr, T.W. and Proctor, M.D., 2017. People Pillars: Re
‐
structuring the Toyota Production System
(TPS) House Based on Inadequacies Revealed During the Automotive Recall Crisis.
Quality and Reliability Engineering International
,
33
(4), pp.921-930.
Keitany, P. and Riwo-Abudho, M., 2014. Effects of lean production on organizational performance: a case study of flour producing company in Kenya.
Eur J Logistics Purchasing Supply Chain Mgmt
,
2
(2), pp.1-14.
Khalili, A., Ismail, M.Y., Karim, A.N.M. and Daud, M.R.C., 2018. Soft total quality management
and lean manufacturing initiatives: model development through structural equation modelling.
International Journal of Productivity and Quality Management
,
23
(1), pp.1-
30.
Lai, H. K., Weerakoon, S.T. and Cheng, E.C.T., 2002. The state of quality management implementation: a cross-sectional study of quality-oriented companies in Hong Kong.
Your preview ends here
Eager to read complete document? Join bartleby learn and gain access to the full version
- Access to all documents
- Unlimited textbook solutions
- 24/7 expert homework help
Quality Management 57
Lakhe, R. R. and Mohanty, R. P., 1993. Total quality management: Concepts, evolution and acceptability in developing economies. Lewis, S., 2015. Qualitative inquiry and research design: Choosing among five approaches.
Health Promotion Practice
,
16
(4), pp.473-475.
Liker, J. K., 2004. The Toyota way: 14 management principles from the world’s greatest manufacturer. New York: McGraw-Hill.
Long-Sutehall, T., Sque, M. and Addington-Hall, J., 2011. Secondary analysis of qualitative data:
a valuable method for exploring sensitive issues with an elusive population? Journal of Research in Nursing
,
16
(4), pp.335-344.
Loureiro, S. M. C., December 01, 2013. The effect of perceived benefits, trust, quality, brand awareness/associations and brand loyalty on internet banking brand equity.
Loyd, N., 2016. Empirical study of Toyota Motor Corporation relative to the good to great framework.
Loyd, N., Harris, G., Gholston, S. and Berkowitz, D., 2020. Development of a lean assessment tool and measuring the effect of culture from employee perception.
Journal of Manufacturing Technology Management
.
Maarof, M.G. and Mahmud, F., 2016. A review of contributing factors and challenges in implementing kaizen in small and medium enterprises.
Procedia Economics and Finance
,
35
, pp.522-531.
Mácsay, V. and Bányai, T., 2017. Toyota production system in milkrun based in-plant supply.
J. Prod. Eng
,
20
(1), pp.141-146.
Your preview ends here
Eager to read complete document? Join bartleby learn and gain access to the full version
- Access to all documents
- Unlimited textbook solutions
- 24/7 expert homework help
Quality Management 58
Mady, S.A., Arqawi, S.M., Al Shobaki, M.J. and Abu-Naser, S.S., 2020. Lean Manufacturing Dimensions and Its Relationship in Promoting the Improvement of Production Processes in Industrial Companies.
Magee, D., 2010. ‘How Toyota became #1, CBS News
. New York: Penguin Group
, <
http://www.cbsnews.com/stories/2010/03/02/business/main6258603.shtml> [Accessed 10 March 2021]. Malterud, K., Siersma, V.D. and Guassora, A.D., 2016. Sample size in qualitative interview studies: guided by information power.
Qualitative Health Research
,
26
(13), pp.1753-
1760.
Marksberry, P., Badurdeen, F., Gregory, B. and Kreafle, K., 2010. Management directed kaizen: Toyota's Jishuken process for management development.
Journal of Manufacturing Technology Management
.
Maxwell, J.A., 2012.
Qualitative research design: An interactive approach
(Vol. 41). Sage Publications.
Milovanovic, V., 2014. Total Quality Management as Profitability Factor in the Hotel Industry. Minto, R., 2010. Toyota's recall – the details’ Financial Times
. Mohamed, A., 2016.
Employee perspective on lean implementation-a qualitative study in a Finnish pension insurance company
. Master's thesis.
Morgan, J. M., & Liker, J. K., 2006. The Toyota product development system: Integrating people, process and technology
. New York: Productivity Press
Nkomo, T., 2019. Analysis of Toyota Motor Corporation.
NYSE, 2010. The New York Stock Exchange. [Online] Available at: <
http://www.nyse.com/> [Accessed 10 March 2021].
Your preview ends here
Eager to read complete document? Join bartleby learn and gain access to the full version
- Access to all documents
- Unlimited textbook solutions
- 24/7 expert homework help
Quality Management 59
Oakland, J.S., 1989. Total Quality Management. Heinemann Professional, London
Oliveira, J., Sá, J.C. and Fernandes, A., 2017. Continuous improvement through" Lean Tools": An application in a mechanical company.
Procedia Manufacturing
,
13
, pp.1082-1089.
Onwuegbuzie, A.J., Leech, N.L. and Collins, K.M., 2010. Innovative data collection strategies in
qualitative research.
Qualitative Report
,
15
(3), pp.696-726.
Pech, M. and Vaněček, D., 2018. Methods of Lean production to improve quality in manufacturing.
Quality Innovation Prosperity
,
22
(2), pp.01-15.
Pepper, M.P. and Spedding, T.A., 2010. The evolution of lean Six Sigma.
The International Journal of Quality & Reliability Management
,
27
(2), p.138.
Phan, C.A. and Matsui, Y., 2010. Contribution of quality management and just-in-time production practices to manufacturing performance.
International Journal of Productivity
and Quality Management
,
6
(1), pp.23-47.
Pinto, G.F.L., Silva, F.J.G., Campilho, R.D.S.G., Casais, R.B., Fernandes, A.J. and Baptista, A., 2019. Continuous improvement in maintenance: a case study in the automotive industry involving Lean tools.
Procedia Manufacturing
,
38
, pp.1582-1591.
Ponelis, S.R., 2015. Using interpretive qualitative case studies for exploratory research in doctoral studies: A case of Information Systems research in small and medium enterprises.
International Journal of Doctoral Studies
,
10
(1), pp.535-550.
Powell, D. and Reke, E., 2019, September. No lean without learning: rethinking lean production as a learning system. In
IFIP International Conference on Advances in Production Management Systems
(pp. 62-68). Springer, Cham.
Prošić, S., 2011. Kaizen management philosophy. In
I International Symposium Engineering Management and Competitiveness, June
(pp. 24-25).
Your preview ends here
Eager to read complete document? Join bartleby learn and gain access to the full version
- Access to all documents
- Unlimited textbook solutions
- 24/7 expert homework help
Quality Management 60
Queirós, A., Faria, D. and Almeida, F., 2017. Strengths and limitations of qualitative and quantitative research methods.
European Journal of Education Studies
.
Rajasekera, J., 2013. Challenges to Toyota caused by recall problems, social networks and digitisation.
Reiter, B., 2013. The epistemology and methodology of exploratory social science research: Crossing Popper with Marcuse.
Robinson, O.C., 2014. Sampling in interview-based qualitative research: A theoretical and practical guide.
Qualitative Research in Psychology
,
11
(1), pp.25-41.
Salleh, N.A.M., Kasolang, S. and Jaffar, A., 2012. Simulation of integrated total quality management (TQM) with lean manufacturing (LM) practices in forming process using Delmia Quest.
Procedia Engineering
,
41
, pp.1702-1707.
Schonberger, R., 2014. Quality management and lean: a symbiotic relationship.
Quality Management Journal
,
21
(3), pp.6-10.
Shammot, M.M., 2011. Quality management practices and their impact on organizational performance, and customer behavior.
European Journal of Economics, Finance and Administrative Sciences
,
34
(2), pp.21-33.
Stamm, M.L., Neitzert, T. and Singh, D.P.K., 2009. TQM, TPM, TOC, Lean and Six Sigma-
Evolution of manufacturing methodologies under the paradigm shift from Taylorism/Fordism to Toyotism.
Stimec, A. and Grima, F., 2019. The impact of implementing continuous improvement upon stress within a Lean production framework.
International Journal of Production Research
,
57
(5), pp.1590-1605.
Your preview ends here
Eager to read complete document? Join bartleby learn and gain access to the full version
- Access to all documents
- Unlimited textbook solutions
- 24/7 expert homework help
Quality Management 61
Sullivan, K.T., 2011. Quality management programs in the construction industry: best value compared with other methodologies.
Journal of Management in Engineering
,
27
(4), pp.210-219.
Thun, J.H., Drüke, M. and Grübner, A., 2010. Empowering Kanban through TPS-principles–an empirical analysis of the Toyota Production System.
International Journal of Production Research
,
48
(23), pp.7089-7106.
Toma, S.G. and Naruo, S., 2017. Total quality management and business excellence: the best practices at Toyota Motor Corporation.
Amfiteatru Economic Journal
,
19
(45), pp.566-
580.
Vanichchinchai, A. and Igel, B., 2011. The impact of total quality management on supply chain management and firm's supply performance.
International Journal of Production Research
,
49
(11), pp.3405-3424.
Wee, H.M. and Wu, S., 2009. Lean supply chain and its effect on product cost and quality: a case
study on Ford Motor Company.
Supply Chain Management: An International Journal
.
Wickramasinghe, G.L.D. and Wickramasinghe, V., 2016. Effects of continuous improvement on shop-floor employees’ job performance in Lean production.
Research Journal of Textile and Apparel
.
Womack, J.P., Jones, D.T. and Roos, D., 2007.
The machine that changed the world: The story of
lean production--Toyota's secret weapon in the global car wars that is now revolutionizing world industry
. Simon and Schuster.
Yang, C.C. and Yang, K.J., 2013. An integrated model of the Toyota production system with total
quality management and people factors.
Human Factors and Ergonomics in Manufacturing & Service Industries
,
23
(5), pp.450-461.
Your preview ends here
Eager to read complete document? Join bartleby learn and gain access to the full version
- Access to all documents
- Unlimited textbook solutions
- 24/7 expert homework help
Quality Management 62
Yella, G.N. and Atem, T.I., 2007. Continuous quality improvement: implementation and sustainability.
Your preview ends here
Eager to read complete document? Join bartleby learn and gain access to the full version
- Access to all documents
- Unlimited textbook solutions
- 24/7 expert homework help
Quality Management 63
Appendix a
Your preview ends here
Eager to read complete document? Join bartleby learn and gain access to the full version
- Access to all documents
- Unlimited textbook solutions
- 24/7 expert homework help
Quality Management 64
Consultancy Project Proposal template
Approx. 500 words
Consultancy Project Topic/ Title Provisional topic and title for the report.
RESEARCH PROPOSAL ON QUALITY MANAGEMENT, LEAN PRODUCTION SYSTEM, AND CONTINUOUS IMPROVEMENT: THESE KEY FACTORS THAT HAVE ENABLED TOYOTA MOTORS’ TO REMAIN AS THE LEADING CAR PRODUCER
Project Description
Please explain the problem, issue or opportunity that the research will try to address. You need to give evidence to support your explanation – for example, if the research is going to be about staff absenteeism, provide evidence of the current rate of absenteeism, how this compares with relevant sector rates, whether the problem is getting worse, what consequences there are for the business (direct costs and wider impacts on staff and customers) etc.
Currently, many organizations in the manufacturing and supply chain industries are encountering stiff global competition that has compelled them to adopt and implement suitable manufacturing and supply chain management strategies for better efficiency and keener competition. Moreover, large-scale manufacturers are today faced with the problem or challenge of a wide range of production which results in volumes of wastage. This problem of wastage is encountered by many companies in their supply chain in order to make quality products. Consequently, the philosophies of quality management, lean production system, and continuous improvement are some of the strategies that have been adopted by these large-scale manufacturing organizations such as Toyota Motors Inc. Therefore, with reference to Toyota Motor, the proposed project will focus on exploring
how these three factors have contributed to sustaining the company to remain on the lead in car production. Background Please include a summary of relevant factual background necessary for the reader to understand the proposed topic, such as what the organisation does, location, size, profitability, etc.
Toyota Motor Corporation is a renowned Japanese company founded in 1937 to design, produce/manufacture, assemble, and sell commercial vehicles, passenger cars, minivans, and related
accessories and parts in basically in Japan, Europe, North America, and Asia. Toyota Motor has continued to be the leading auto manufacturers as well as the eighth largest corporation globally. This success is attributed to the fact that Toyota Motors has recognized the concept of quality management, lean production system, and continuous improvement as key to better organizational performance. More crucial is Toyota’s integrated approach to quality management emphasizing lean
thinking which involves all staff of the organization to take part in the continuous improvement system maintaining Toyota as a leading car producer.
Core Literature
Please list the sources you have already found which will be key for your research. Anvari, A., Ismail, Y. and Hojjati, S.M.H., 2011. A study on total quality management and lean manufacturing: through lean thinking approach.
World applied sciences journal
,
12
(9), pp.1585-
1596.
Barney, H. and Kirby, S.N., 2014. Toyota production system/lean manufacturing.
Organizational improvement and accountability: Lessons for education from other sectors
, pp.35-50.
Chiarini, A., Baccarani, C. and Mascherpa, V., 2018. Lean production, Toyota production system and kaizen philosophy.
The TQM Journal
.
Your preview ends here
Eager to read complete document? Join bartleby learn and gain access to the full version
- Access to all documents
- Unlimited textbook solutions
- 24/7 expert homework help
Quality Management 65
Kehr, T.W. and Proctor, M.D., 2017. People Pillars: Re‐structuring the Toyota Production System (TPS) House Based on Inadequacies Revealed During the Automotive Recall Crisis.
Quality and Reliability Engineering International
,
33
(4), pp.921-930.
Loyd, N., Harris, G., Gholston, S. and Berkowitz, D., 2020. Development of a lean assessment tool and measuring the effect of culture from employee perception.
Journal of Manufacturing Technology Management
.
Mady, S.A., Arqawi, S.M., Al Shobaki, M.J. and Abu-Naser, S.S., 2020. Lean Manufacturing Dimensions and Its Relationship in Promoting the Improvement of Production Processes in Industrial Companies.
Mácsay, V. and Bányai, T., 2017. Toyota production system in milkrun based in-plant supply.
J. Prod. Eng
,
20
(1), pp.141-146.
Maarof, M.G. and Mahmud, F., 2016. A review of contributing factors and challenges in implementing kaizen in small and medium enterprises.
Procedia economics and Finance
,
35
, pp.522-531.
Nkomo, T., 2019. Analysis of Toyota Motor Corporation.
Oliveira, J., Sá, J.C. and Fernandes, A., 2017. Continuous improvement through" Lean Tools": An application in a mechanical company.
Procedia Manufacturing
,
13
, pp.1082-1089.
Aim and objectives
Please set out the overall aim of the research in one sentence, with supporting objectives for the
background research/literature review, primary research and recommendations.
The aim of the proposed study will be to explore the impact of quality management, lean management system, and continuous improvement on Toyota Motor over the previous years. The focus will be on how the three factors have helped the organization to enhance its operations despite the challenges of product recalls as well as heightened competition in the global motor industry
. Methodology and Data Resources
Please indicate the proposed method, including the planned sample size and whether you have
confirmed access to the chosen organisation(s).
The proposed study will adopt a blend of qualitative and quantitive research methodologies
whereby the employees and financial records will be relied upon as the primary and
secondary data sources. The study has planned to random sample approximately 15
employees of Toyota Motor Corporation to obtain the needed primary data. The company is
yet to be served with the consent seeking form and the research will commence
immediately upon the approval.
Data Collection Approach Please summarise the data collection methods to be applied
The proposed study plans to use semi-structured interviews with employees and prospecting of secondary data stored from of annual financial/accounting records. Data Analysis Approach / Method
Please summarise the data analysis methods to be applied
Since the proposed study will rely on both primary and secondary data collected from Toyota Motor’s employees and documented financial reports, respectively; narrative and content analyses
will be used as the data analysis approach to interpreting the data acquired from the interviewees. Moreover, tables and charts will also be used to analyse secondary data retrieved from the organization’s database.
Your preview ends here
Eager to read complete document? Join bartleby learn and gain access to the full version
- Access to all documents
- Unlimited textbook solutions
- 24/7 expert homework help
Quality Management 66
Ethical Considerations
Please highlight any specific ethical issues that may be of concern, such as the research involves
people aged under 18, or deception of research participants. Otherwise, explain how you will
address ethical matters
The proposed research will only begin upon the approval of the consent form by Toyota Motor as the target corporation. Secondly, the researcher will ensure the anonymity of the respondents by protecting their identity. Lastly, all the information given by the employees will be kept confidential
for strict use in the study and discarded immediately upon the completion of the study. Referencing system to be used
Confirm use of recognised Referencing Systems e.g. Harvard including expectation for appropriate
in- text citations
The proposed study will adopt the Harvard reference system Confirmation of Originality
Please confirm that this project and the final report will be your own work and will not be copied,
written by another or plagiarised. Should this be suspected, the work will be referred to the
University of Chichester in line with item 8E of the Academic Regulations. I hereby confirm to the university that the final report as proposed will be my own work and will neither be plagiarized nor written by any other scholar. I will, therefore, be liable for any violation of originality requirements. Student name
Andrew Male
Signed
Date
16
Feb
2021
Signed
Approval date
Appendix b
Your preview ends here
Eager to read complete document? Join bartleby learn and gain access to the full version
- Access to all documents
- Unlimited textbook solutions
- 24/7 expert homework help
Quality Management 67
APPLICATION FORM FOR ETHICAL APPROVAL
MBA/MSc/MA TOP-UP PROGRAMME
Project details
Project title
RESEARCH PROPOSAL ON QUALITY MANAGEMENT, LEAN PRODUCTION SYSTEM, AND CONTINUOUS IMPROVEMENT: THESE KEY FACTORS THAT HAVE ENABLED TOYOTA MOTORS TO REMAIN AS THE LEADING CAR PRODUCER
Student name
Andrew Male
Project Description
Currently, many organizations in the manufacturing and supply chain industries are encountering stiff global competition that has compelled them to adopt and implement suitable manufacturing and supply chain management strategies for better efficiency and keener competition. Moreover, large-
scale manufacturers are today faced with the problem or challenge of a wide range of production which results in volumes of wastage. This problem of wastage is encountered by many companies in their supply chain in order to make quality products. Consequently, the philosophies of quality management, lean production system, and continuous improvement are some of the strategies that have been adopted by these large-scale manufacturing organizations such as Toyota Motors Inc. Therefore, with reference to Toyota Motor, the proposed project will focus on exploring how these three factors have contributed to sustaining the company to remain on the lead in car production. Methodology and Data Resources
The proposed study will adopt a qualitative research methodology whereby reports, technical documents, blogs and financial records will be relied upon as secondary data sources. The study had planned to random sample employees of Toyota Motor Corporation to obtain the needed primary data. Data Collection Approach Please summarise the data collection methods to be applied
The proposed study plans the prospecting and collection of secondary data stored from annual financial/accounting records, technical papers, websites, and blogs. Informed Consent Please detail how you are managing informed consent. N.B. You must submit your consent form and associated participant information with this completed consent form.
The Toyota company was contacted regarding seeking consent to carry out primary research. I have since received an email reply informing me that they will not be able to support my request. Note: The sections above should be copied from the approved version of your consultancy project report proposal form.
Your preview ends here
Eager to read complete document? Join bartleby learn and gain access to the full version
- Access to all documents
- Unlimited textbook solutions
- 24/7 expert homework help
Quality Management 68
Ethical approach
Please indicate how you will be addressing relevant ethical issues concerning your research. If you tick No for any of the questions, please provide an explanation of how you intend to address this issue as an annex to the form.
Yes
No
N/A
The research will not involve children under 18 or adults with known health, mental or social problems
X
The research will not cause physical or psychological harm to any participant or other person
X
The research will not involve any payment, gift or inducement being given to anyone
X
The research will not involve any actual or potential conflict of interest
X
The research will not involve withholding relevant information or misleading participants as part of its methodology
X
The research will not give rise to any potential risk of harm or distress to myself
X
I will seek and obtain written informed consent from all participants before conducting interviews or focus groups
X
I will provide adequate information for participants in
a questionnaire survey so that they can make an informed decision whether or not to participate
X
I have already obtained permission from a responsible individual in the chosen organisation in order to carry out my primary research there and/or to use other data and facilities in connection with my
research
X
I will ensure participant data, including recordings, is
treated confidentially and stored securely during the
research project and is destroyed once I have completed the programme
X
I will ensure that the anonymity of participants is maintained and/or that an individual’s responses are
not linked with their identity
X
I will respect the principle of voluntary participation in research
X
I will not publish my final research or use data collected during the research project without first gaining the written consent of London Graduate School and the organisation where the primary research was conducted
X
I will carry out my research in a way that does not X
Your preview ends here
Eager to read complete document? Join bartleby learn and gain access to the full version
- Access to all documents
- Unlimited textbook solutions
- 24/7 expert homework help
Quality Management 69
damage the reputation of the University of Chichester or London Graduate School
Confirmation by the applicant
In signing this research ethics application form, I am also confirming that:
•
The research study must not begin until ethical approval has been granted.
•
The form is accurate to the best of my knowledge and belief.
•
There is no potential material interest that may, or may appear to, impair my independence and objectivity in conducting this project.
•
Subject to the research being approved, I undertake to adhere to the commitments made in this approval form without deviation (unless with the specific and prior agreement of my supervisor).
•
I understand that the project, including research records and data, may be subject to inspection for audit purposes, if required in future, in keeping with the University’s Privacy Standard.
•
I understand that personal data about me as a researcher in this form will be held by those involved in the ethics review procedure for five years after approval and that this will be managed according to Data Protection Act principles.
•
I understand my responsibilities to work within a set of safety, ethical and other guidelines as agreed in advance with my supervisor and understand that I must always comply with the University’s regulations and any other applicable code of ethics.
Full Name of Applicant: Signature of Applicant:
Andrew Male
authorised, for retention.
Your preview ends here
Eager to read complete document? Join bartleby learn and gain access to the full version
- Access to all documents
- Unlimited textbook solutions
- 24/7 expert homework help
Related Documents
Recommended textbooks for you
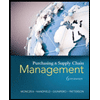
Purchasing and Supply Chain Management
Operations Management
ISBN:9781285869681
Author:Robert M. Monczka, Robert B. Handfield, Larry C. Giunipero, James L. Patterson
Publisher:Cengage Learning
Marketing
Marketing
ISBN:9780357033791
Author:Pride, William M
Publisher:South Western Educational Publishing
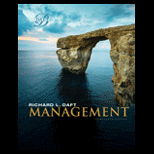
Management, Loose-Leaf Version
Management
ISBN:9781305969308
Author:Richard L. Daft
Publisher:South-Western College Pub
Recommended textbooks for you
- Purchasing and Supply Chain ManagementOperations ManagementISBN:9781285869681Author:Robert M. Monczka, Robert B. Handfield, Larry C. Giunipero, James L. PattersonPublisher:Cengage LearningMarketingMarketingISBN:9780357033791Author:Pride, William MPublisher:South Western Educational Publishing
- Management, Loose-Leaf VersionManagementISBN:9781305969308Author:Richard L. DaftPublisher:South-Western College Pub
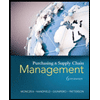
Purchasing and Supply Chain Management
Operations Management
ISBN:9781285869681
Author:Robert M. Monczka, Robert B. Handfield, Larry C. Giunipero, James L. Patterson
Publisher:Cengage Learning
Marketing
Marketing
ISBN:9780357033791
Author:Pride, William M
Publisher:South Western Educational Publishing
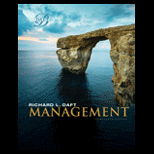
Management, Loose-Leaf Version
Management
ISBN:9781305969308
Author:Richard L. Daft
Publisher:South-Western College Pub