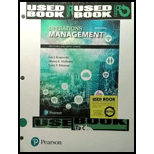
Concept explainers
A golf specialty wholesaler operates 50 weeks per year. Management is trying to determine an inventory policy for its 1-irons, which have the following characteristics:
- If the company uses a periodic review system, what should P and T be? Round P to the nearest week.
- If the company uses a continuous review system, what should R be?

Want to see the full answer?
Check out a sample textbook solution
Chapter 9 Solutions
Operations Management: Processes And Supply Chains (12th Edition) (what's New In Operations Management)
Additional Business Textbook Solutions
Accounting Information Systems (14th Edition)
Essentials of MIS (13th Edition)
Gitman: Principl Manageri Finance_15 (15th Edition) (What's New in Finance)
Principles of Operations Management: Sustainability and Supply Chain Management (10th Edition)
Financial Accounting, Student Value Edition (5th Edition)
Horngren's Cost Accounting: A Managerial Emphasis (16th Edition)
- oimmnjjjharrow_forwardSummarize the ethical dilemma encountered in Walmart Inc. Which of Kohlberg's stages of moral development is represented? Is there other theories of moral development that better describes the example? Postulate the (hypothetical or real) best- and worst-case outcomes of this dilemma. Is it agreeable with the selection of Kohlberg's stages of moral development for their examples? Is there another theory of moral development that would better describe their examples?arrow_forwardFour-drive theory recommends that companies must keep fulfillment of the four drives in balance. What is this “balance” and why is it important? Can you Give an example (real or hypothetical) of how a company maintains balanced drive fulfillment. Also describe a company that does not provide this balance, including the consequences of this imbalance on employees’ attitudes and behavior. Thank youarrow_forward
- what criteria would you utilize to determine if someone's pay is “fair” or “egregious?” Additionally, what should be the mechanism or process to determine how much greater an organizational executive should be paid versus line-level employees?arrow_forwardDefine the concept of a compensation philosophy, including the components that should be addressed in a compensation philosophy. Assess why a compensation philosophy is so foreign to most organizations and how you can best encourage an organization to create its own compensation philosophy that is beneficial to attracting the best talent.arrow_forward1) View the videos Taco Bell test-drives Live Mas restaurant concept in South Bay (0.32 mins, Ctrl+Click on the link) https://www.youtube.com/watch?v=04wRc5Wg8GU , and First-ever Taco Bell Live Mas Café serving exclusive drinks in Chula Vista (1.56 mins, Ctrl+Click on the link) https://www.youtube.com/watch?v=fq6jDxJk1LM , and answer the following questions: a) What is driving Taco Bell to try a beverage-focused format? b) What type of a process strategy does their beverage-focused format represent? c) What operational issues do you think Taco Bell would face from their beverage-focused format? d) What do you think are the main advantages and disadvantages of kiosk ordering? Note: As a rough guideline, please try to keep the written submission to one or two paragraphs for each of the questions. 2) Taipei Pharmaceuticals is planning to open a new manufacturing facility as part of its expansion plans. The firm has narrowed down the search to locate its new manufacturing facility…arrow_forward
- 1) View the videos Taco Bell test-drives Live Mas restaurant concept in South Bay (0.32 mins, Ctrl+Click on the link) https://www.youtube.com/watch?v=04wRc5Wg8GU , and First-ever Taco Bell Live Mas Café serving exclusive drinks in Chula Vista (1.56 mins, Ctrl+Click on the link) https://www.youtube.com/watch?v=fq6jDxJk1LM , and answer the following questions: a) What is driving Taco Bell to try a beverage-focused format? b) What type of a process strategy does their beverage-focused format represent? c) What operational issues do you think Taco Bell would face from their beverage-focused format? d) What do you think are the main advantages and disadvantages of kiosk ordering? Note: As a rough guideline, please try to keep the written submission to one or two paragraphs for each of the questions. 2) Taipei Pharmaceuticals is planning to open a new manufacturing facility as part of its expansion plans. The firm has narrowed down the search to locate its new manufacturing facility…arrow_forwardThe Clothing Shack is an online retailer of men's, women's, and children's clothing. The company has been in business for four years and makes a modest profit from its online sales. However, in an effort to compete successfully against online retailing heavyweights, the Clothing Shack's marketing director, Makaya O'Neil, has determined that the Clothing Shack's marketing information systems need improvement. Ms. O'Neil feels that the Clothing Shack should begin sending out catalogs to its customers, keep better track of its customer's buying habits, perform target marketing, and provide a more personalized shopping experience for its customers. Several months ago, Ms. O'Neil submitted a systems service request (SSR) to the Clothing Shack's steering committee. The committee unanimously approved this project. You were assigned to the project at that time and have since helped your project team successfully complete the project initiation and planning phase. Your team is now ready to move…arrow_forwardb-1. Activity ES EF LS LF Slack 1 2 3 4 5 6 7 8 9 b-2. Identify the critical activities, and determine the duration of the project. The critical activities are .arrow_forward
- The forecast for each week of a four-week schedule is 50 units. The MPS rule is to schedule production if the projected on-hand Inventory would be negative without it. Customer orders (committed) are follows: Week Customer Order 1 52 35 20 12 Use a production lot size of 75 units and no beginning Inventory. Determine the available-to-promise (ATP) quantities for each period. Note: Leave no cells blank - be certain to enter "0" wherever required. Period ATP 1 2 3arrow_forwardPrepare a master schedule given this information: The forecast for each week of an eight-week schedule is 60 units. The MPS rule is to schedule production if the projected on-hand Inventory would be negative without it. Customer orders (committed) are as follows: Week Customer Orders 1 2 36 28 4 1 Use a production lot size of 85 units and no beginning inventory. Note: In the ATP row, enter a value of 0 (zero) in any periods where ATP should not be calculated. Leave no cells blank - be certain to enter "0" wherever required. June July 1 2 3 4 5 8 7 8 Forecast 60 60 60 60 60 60 60 60 Customer Orders 38 28 4 1 0 0 0 0 Projected On-Hand Inventory MPS ATParrow_forwardSales of tablet computers at Marika Gonzalez's electronics store in Washington, D.C., over the past 10 weeks are shown in the table below: Week 1 2 3 4 5 6 7 8 9 10 Demand 21 21 27 38 25 30 35 24 25 30 a) The forecast for weeks 2 through 10 using exponential smoothing with a = 0.50 and a week 1 initial forecast of 21.0 are (round your responses to two decimal places): Week 1 2 3 4 5 6 7 8 9 10 Demand 21 21 27 38 25 30 35 24 25 30 Forecast 21.0 21 21 24 31 28 29 32 28 26.50 b) For the forecast developed using exponential smoothing (a = 0.50 and initial forecast 21.0), the MAD = |||||sales (round your response to two decimal places).arrow_forward
- Purchasing and Supply Chain ManagementOperations ManagementISBN:9781285869681Author:Robert M. Monczka, Robert B. Handfield, Larry C. Giunipero, James L. PattersonPublisher:Cengage LearningMarketingMarketingISBN:9780357033791Author:Pride, William MPublisher:South Western Educational PublishingPractical Management ScienceOperations ManagementISBN:9781337406659Author:WINSTON, Wayne L.Publisher:Cengage,
- Foundations of Business (MindTap Course List)MarketingISBN:9781337386920Author:William M. Pride, Robert J. Hughes, Jack R. KapoorPublisher:Cengage LearningFoundations of Business - Standalone book (MindTa...MarketingISBN:9781285193946Author:William M. Pride, Robert J. Hughes, Jack R. KapoorPublisher:Cengage Learning
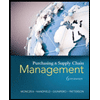
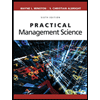
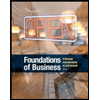
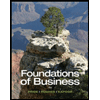