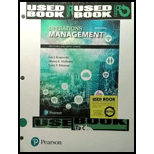
Operations Management: Processes And Supply Chains (12th Edition) (what's New In Operations Management)
12th Edition
ISBN: 9780134742205
Author: Lee J. Krajewski, Manoj K. Malhotra, Larry P. Ritzman
Publisher: PEARSON
expand_more
expand_more
format_list_bulleted
Concept explainers
Textbook Question
Chapter 9, Problem 9P
Yellow Press, Inc. buys paper in 1,500-pound rolls for printing. Annual demand is 2,500 rolls. The cost per roll is $800, and the annual holding cost is 15 percent of the cost. Each order costs $50 to process.
- How many rolls should Yellow Press, Inc. order at a time?
- What is the time between orders?
Expert Solution & Answer

Want to see the full answer?
Check out a sample textbook solution
Students have asked these similar questions
Yellow Press, Inc., buys paper in 1,500-pound rolls for print-ing. Annual demand is 2,500 rolls. The cost per roll is $800,and the annual holding cost is 15 percent of the cost. Eachorder costs $50 to process.a. How many rolls should Yellow Press, Inc., order at a time?b. What is the time between orders?
Yellow Press, Inc., buys paper in 1,500-pound rolls for printing. Annual demand is 2,500 rolls. The cost per roll is $800, and the annual holding cost is 15 percent of the cost. Each order costs $50 to process.a. How many rolls should Yellow Press, Inc., order at a time?b. What is the time between orders?
Yellow Press, Inc., buys paper in 1,500-pound rolls for printing. Annual demand is
3,000
rolls. The cost per roll is
$1,000,
and the annual holding cost is
28
percent of the cost. Each order costs
$75.
Part 2
a. How many rolls should Yellow Press order at a time?
Yellow Press should order
enter your response here
rolls at a time. (Enter your response rounded to the nearest whole number.)
Part 3
b. What is the time between orders? (Assume
200
workdays per year.)
The time between orders is
enter your response here
days. (Enter your response rounded to one decimal place.)
Chapter 9 Solutions
Operations Management: Processes And Supply Chains (12th Edition) (what's New In Operations Management)
Ch. 9 - What is the relationship between inventory and the...Ch. 9 - Suppose that a large discount retailer with a lot...Ch. 9 - Will organizations ever get to the point where...Ch. 9 - A part is produced in lots of 1,000 units. It is...Ch. 9 - Prince Electronics, a manufacturer of consumer...Ch. 9 - Terminator, Inc. manufactures a motorcycle part in...Ch. 9 - Ruby-Star Incorporated is considering two...Ch. 9 - Haley Photocopying purchases paper from an...Ch. 9 - Prob. 6PCh. 9 - Southern Markets, Inc. is considering the use of...
Ch. 9 - New Wave Shelving’s inventory manager would like...Ch. 9 - Yellow Press, Inc. buys paper in 1,500-pound rolls...Ch. 9 - Babble, Inc. buys 400 blank cassette tapes per...Ch. 9 - At Dot Com, a large retailer of popular books,...Ch. 9 - Leaky Pipe, a local retailer of plumbing supplies,...Ch. 9 - Sam’s Cat Hotel operates 52 weeks per year, 6...Ch. 9 - Consider again the kitty litter ordering policy...Ch. 9 - In a Q system, the demand rate for strawberry ice...Ch. 9 - Petromax Enterprises uses a continuous review...Ch. 9 - In a continuous review inventory system, the lead...Ch. 9 - In a two-bin inventory system, the demand for...Ch. 9 - You are in charge of inventory control of a highly...Ch. 9 - Your firm uses a continuous review system and...Ch. 9 - A company begins a review of ordering policies for...Ch. 9 - Prob. 22PCh. 9 - The Farmer’s Wife is a country store...Ch. 9 - Prob. 24PCh. 9 - Prob. 25PCh. 9 - Prob. 26PCh. 9 - In a P system, the lead time for a box of...Ch. 9 - Suppose that Sam’s Cat Hotel in Problem 13 uses...Ch. 9 - Your firm uses a periodic review system for all...Ch. 9 - Using the same information as in Problem 21,...Ch. 9 - Wood County Hospital consumes 1,000 boxes of...Ch. 9 - A golf specialty wholesaler operates 50 weeks per...Ch. 9 - What is the EOQ and what is the lowest total cost?Ch. 9 - What is the annual cost of holding inventory at...Ch. 9 - Prob. 3AMECh. 9 - Prob. 4AMECh. 9 - Prob. 5AMECh. 9 - Prob. 6AMECh. 9 - Comment on the sensitivity of the EOQ model to...Ch. 9 - Consider the pressures for small versus large...Ch. 9 - Prob. 2VCCh. 9 - The Marker Maker© product recently experienced an...Ch. 9 - Put yourself in Sue McCaskey’s position and...Ch. 9 - By how much do your recommendations for these two...
Additional Business Textbook Solutions
Find more solutions based on key concepts
What is precedent, and how does it affect common law?
Business in Action (8th Edition)
2. In what circumstances might a market-pull approach or a technology-push approach to new-product design be th...
OPERATIONS MANAGEMENT IN THE SUPPLY CHAIN: DECISIONS & CASES (Mcgraw-hill Series Operations and Decision Sciences)
The flowchart for the process at the local car wash. Introduction: Flowchart: A flowchart is a visualrepresenta...
Principles Of Operations Management
Many companies including Company OM tried to implement dynamic pricing in their ticketing system. The dynamic p...
Principles of Operations Management: Sustainability and Supply Chain Management (10th Edition)
Knowledge Booster
Learn more about
Need a deep-dive on the concept behind this application? Look no further. Learn more about this topic, operations-management and related others by exploring similar questions and additional content below.Similar questions
- The chapter presented various approaches for the control of inventory investment. Discuss three additional approaches not included that might involve supply chain managers.arrow_forward#14 Can you show me how to do this?arrow_forwardYellow Press, Inc., buys paper in 1,500-pound rolls for printing. Annual demand is 2,250 rolls. The cost per roll is $625, and the annual holding cost is 20 percent of the cost. Each order costs $35. a. How many rolls should Yellow Press order at a time? Yellow Press should order _____rolls at a time. (Enter your response rounded to the nearest whole number.)arrow_forward
- Energyzer , a regional electronics retailer , estimates that sells 13 , 000 4-packs of batteries per year (or 250 per week). Each 4-pack of batteries costs the retailer $2.00; with a carrying cost rate of 32%; and ordering costs of $40.00 per order. a. Calculate the optimum order period—in terms of weeks , b. Calculate the economic order quantity PLEASE SHOW WORKarrow_forwardYellow Press, Inc., buys paper in 1,500-pound rolls for printing. Annual demand is 3 comma 0003,000 rolls. The cost per roll is $1 comma 0001,000, and the annual holding cost is 2828 percent of the cost. Each order costs $4545. Part 2 a. How many rolls should Yellow Press order at a time?arrow_forwardRocket Racer builds 200,000 go-carts a year and purchases the motors for these carts for $850 each. Ordering costs are $1,040, and Rocket Racer's inventory carrying costs average 15% of the inventory value. What is the total inventory costs for an inventory order size of 4000?arrow_forward
- An architect firm uses an average of 60 boxes of copier paper a day. The firm operates 280 days a year. Storage and handling costs for the paper are $30 a year per box, and its costs approximately $60 to order and receive a shipment of paper.(a) What quantity order size would minimize the total annual inventory cost?arrow_forwardThe company uses 150,000 gallons of alcohol per month. The cost of carrying the alcohol in inventory is P0.50 per gallon per year, and the cost of ordering is P150 per order. The firm uses the alcohol at a constant rate throughout the year. It takes 18 days to receive an order once it is placed. The reorder point is?arrow_forwardCosts for storing = 8 % on inventory. Raw material per unit = $ 2 Ordering cost per order is $ 50 Materials = 10000 units. Find the quantity to be ordered with works.arrow_forward
- Please do not give solution in image format thankuarrow_forwardGiven the following information, compute the economic order quantity, annual holding cost, annual order cost, and annual total inventory cost. Annual requirements (R) = 50,000 units Order cost (S) = $150 per order Holding rate (k) = 15% Unit cost (C) = $100 per unitarrow_forwardSoutheastern Bell stocks a certain switch connector at its central warehouse for supplying field service offices. The yearly demand for these connectors is 15,000 units. Southeastern estimates its annual holding cost for this item to be $24 per unit. The cost to place and process an order from the supplier is $73. The company operates 300 days per year, and the lead time to receive an order from the supplier is 3 working days.arrow_forward
arrow_back_ios
SEE MORE QUESTIONS
arrow_forward_ios
Recommended textbooks for you
- Purchasing and Supply Chain ManagementOperations ManagementISBN:9781285869681Author:Robert M. Monczka, Robert B. Handfield, Larry C. Giunipero, James L. PattersonPublisher:Cengage Learning
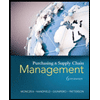
Purchasing and Supply Chain Management
Operations Management
ISBN:9781285869681
Author:Robert M. Monczka, Robert B. Handfield, Larry C. Giunipero, James L. Patterson
Publisher:Cengage Learning
Inventory Management | Concepts, Examples and Solved Problems; Author: Dr. Bharatendra Rai;https://www.youtube.com/watch?v=2n9NLZTIlz8;License: Standard YouTube License, CC-BY