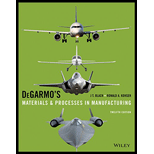
DeGarmo's Materials and Processes in Manufacturing
12th Edition
ISBN: 9781118987674
Author: J. T. Black, Ronald A. Kohser
Publisher: WILEY
expand_more
expand_more
format_list_bulleted
Concept explainers
Question
Chapter 40, Problem 6P
To determine
To determine the lot size to justify the use of jig.
Expert Solution & Answer

Want to see the full answer?
Check out a sample textbook solution
Students have asked these similar questions
The pickup truck weighs 3220 Ib and reaches a speed of 30 mi/hr from rest in a distance of 200 ft up the 10-percent incline with constant acceleration. Calculate the normal force under each pair of wheels and the friction force under the rear driving wheels. The effective coefficient of friction between the tires and the road is known to be at least 0.8.
1.
The figure shows a car jack to support 400kg (W=400kg). In the drawing, the angle (0) varies
between 15 and 70 °. The links are machined from AISI 1020 hot-rolled steel bars with a
minimum yield strength of 380MPa. Each link consists of two bars, one on each side of the
central bearings. The bars are 300mm in length (/) and 25 mm in width (w). The pinned ends
have the buckling constant (C) of 1.4 for out of plane buckling. The design factor (nd) is 2.5.
(1) Find the thickness (t) of the bars and the factor of safety (n).
(2) Check if the bar is an Euler beam.
D
(Read image)
Chapter 40 Solutions
DeGarmo's Materials and Processes in Manufacturing
Ch. 40 - What are the two primary functions of a...Ch. 40 - Prob. 2RQCh. 40 - An early treatise defined a jig as a device that...Ch. 40 - Does an ordinary vise qualify as a fixture? Why or...Ch. 40 - What basic criteria should be considered in...Ch. 40 - In any part drawing, what are the critical...Ch. 40 - What difficulties can result from not keeping...Ch. 40 - Prob. 8RQCh. 40 - Which of the basic design principles relating to...Ch. 40 - What are the two reasons for not having drill...
Ch. 40 - Why does the use of down milling often make it...Ch. 40 - Prob. 12RQCh. 40 - A large assembly jig for an airplane-wing...Ch. 40 - Explain why the use of a given fixture may not be...Ch. 40 - Prob. 15RQCh. 40 - In the clamps shown in Figure 40.20, what is the...Ch. 40 - What are other common types of clamp?Ch. 40 - What is the purpose of dimensioning the...Ch. 40 - Prob. 19RQCh. 40 - In Figure 49.9. why arent there three points put...Ch. 40 - Which set of locators in Figure 49.9 establishes...Ch. 40 - What are the four stages of the SMED methodology...Ch. 40 - Prob. 23RQCh. 40 - How could the intermediate jig concept be used in...Ch. 40 - Develop a sequence of operations to produce the...Ch. 40 - Suppose in the sample problem at the end of this...Ch. 40 - Notice that the holes in the part in Figure 49.9...Ch. 40 - Prob. 6PCh. 40 - A part has two holes located for drilling by...
Knowledge Booster
Learn more about
Need a deep-dive on the concept behind this application? Look no further. Learn more about this topic, mechanical-engineering and related others by exploring similar questions and additional content below.Similar questions
- UNIVERSIDAD NACIONAL DE SAN ANTONIO ABAD DEL CUSCO PRIMER EXAMEN PARCIAL DE MECÁNICA DE FLUIDOS I ............ Cusco, 23 de setiembre de 2024 AP. Y NOMBRES: ........ 1.- Para el tanque de la figura: a) Calcule la profundidad de la hidrolina si la profundidad del agua es de 2.8 m y el medidor del fondo del tanque da una lectura de 52.3kPa. b) Calcule la profundidad del agua si la profundidad de la hidrolina es 6.90 m y el medidor de la parte inferior del tanque registra una lectura de 125.3 kPa. Hidrolina Sp=0.90 Abertura Agua sup suge to but amulor quit y 2.- Calcule la magnitud de la fuerza resultante sobre el área A-B y la ubicación del centro de presión. Señale la fuerza resultante sobre el área y dimensione su ubicación con claridad. 3.5 ft 12 in: Oil (38-0.93) 14 in 8 inarrow_forwardplease solve this problem and give me the correct answer step by steparrow_forwardplease solve this problem step by step and show the best way that can be explainedarrow_forward
- 1 8 4 Add numbers so that the sum of any row or column equals .30 Use only these numbers: .1.2.3.4.5.6.10.11.12.12.13.14.14arrow_forwardUppgift 2 (9p) I77777 20 kN 10 kN/m 4 [m] 2 2 Bestäm tvärkrafts- och momentdiagram för balken i figuren ovan. Extrempunkter ska anges med både läge och värde i diagrammen.arrow_forward**Problem 8-45.** The man has a mass of 60 kg and the crate has a mass of 100 kg. If the coefficient of static friction between his shoes and the ground is \( \mu_s = 0.4 \) and between the crate and the ground is \( \mu_c = 0.3 \), determine if the man is able to move the crate using the rope-and-pulley system shown. **Diagram Explanation:** The diagram illustrates a scenario where a man is attempting to pull a crate using a rope-and-pulley system. The setup is as follows: - **Crate (C):** Positioned on the ground with a rope attached. - **Rope:** Connects the crate to a pulley system and extends to the man. - **Pulley on Tree:** The rope runs over a pulley mounted on a tree which redirects the rope. - **Angles:** - The rope between the crate and tree forms a \(30^\circ\) angle with the horizontal. - The rope between the tree and the man makes a \(45^\circ\) angle with the horizontal. - **Man (A):** Pulling on the rope with the intention of moving the crate. This arrangement tests the…arrow_forward
- please solve this problems follow what the question are asking to do please show me step by steparrow_forwardplease first write the line action find the forces and them solve the problem step by steparrow_forwardplease solve this problem what the problem are asking to solve please explain step by step and give me the correct answerarrow_forward
arrow_back_ios
SEE MORE QUESTIONS
arrow_forward_ios
Recommended textbooks for you
- Elements Of ElectromagneticsMechanical EngineeringISBN:9780190698614Author:Sadiku, Matthew N. O.Publisher:Oxford University PressMechanics of Materials (10th Edition)Mechanical EngineeringISBN:9780134319650Author:Russell C. HibbelerPublisher:PEARSONThermodynamics: An Engineering ApproachMechanical EngineeringISBN:9781259822674Author:Yunus A. Cengel Dr., Michael A. BolesPublisher:McGraw-Hill Education
- Control Systems EngineeringMechanical EngineeringISBN:9781118170519Author:Norman S. NisePublisher:WILEYMechanics of Materials (MindTap Course List)Mechanical EngineeringISBN:9781337093347Author:Barry J. Goodno, James M. GerePublisher:Cengage LearningEngineering Mechanics: StaticsMechanical EngineeringISBN:9781118807330Author:James L. Meriam, L. G. Kraige, J. N. BoltonPublisher:WILEY
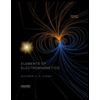
Elements Of Electromagnetics
Mechanical Engineering
ISBN:9780190698614
Author:Sadiku, Matthew N. O.
Publisher:Oxford University Press
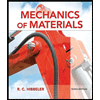
Mechanics of Materials (10th Edition)
Mechanical Engineering
ISBN:9780134319650
Author:Russell C. Hibbeler
Publisher:PEARSON
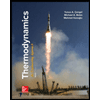
Thermodynamics: An Engineering Approach
Mechanical Engineering
ISBN:9781259822674
Author:Yunus A. Cengel Dr., Michael A. Boles
Publisher:McGraw-Hill Education
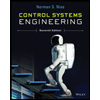
Control Systems Engineering
Mechanical Engineering
ISBN:9781118170519
Author:Norman S. Nise
Publisher:WILEY
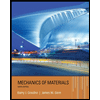
Mechanics of Materials (MindTap Course List)
Mechanical Engineering
ISBN:9781337093347
Author:Barry J. Goodno, James M. Gere
Publisher:Cengage Learning
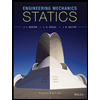
Engineering Mechanics: Statics
Mechanical Engineering
ISBN:9781118807330
Author:James L. Meriam, L. G. Kraige, J. N. Bolton
Publisher:WILEY
Types of Manufacturing Process | Manufacturing Processes; Author: Magic Marks;https://www.youtube.com/watch?v=koULXptaBTs;License: Standard Youtube License