EBK MANUFACTURING ENGINEERING & TECHNOL
7th Edition
ISBN: 9780100793439
Author: KALPAKJIAN
Publisher: YUZU
expand_more
expand_more
format_list_bulleted
Concept explainers
Question
Chapter 32, Problem 45SDP
To determine
Obtain a soldering iron and attempt to solder two wires together. First, try to apply the solder at the same time as you first put the soldering iron tip to the wires. Second, preheat the wires before applying the solder. Repeat the same procedure for a cool surface and a heated surface. Record your results and explain your findings.
Expert Solution & Answer

Want to see the full answer?
Check out a sample textbook solution
Students have asked these similar questions
1. A 40 lb. force is applied at point E. There are pins at
A, B, C, D, and F and a roller at A.
a. Draw a FBD of member EFC showing all the known and
unknown forces acting on it.
b. Draw a FBD of member ABF showing all the known and
unknown forces acting on it.
c. Draw a FBD of member BCD showing all the known and
unknown forces acting on it.
d. Draw a FBD of the entire assembly ADE showing all the
known and unknown forces acting on it.
e. Determine the reactions at A and D.
f. Determine the magnitude of the pin reaction at C.
40 lbs.
B
A
6 in.
4 in.
D
F
-5 in.4 in 4.
A crude oil of specific gravity0.85 flows upward at a volumetric rate of flow of 70litres per
second through
a vertical
venturimeter,with an inlet diameter of 250 mm and a throat
diameter of 150mm. The coefficient
of discharge of venturimeter is 0.96. The vertical
differences betwecen the pressure toppings is
350mm.
i)
Draw a well labeled diagram to represent the above in formation
i)
If the two pressure gauges are connected at the tapings such that they are
positioned at the levels of their corresponding tapping points,
determine the
difference of readings in N/CM² of the two pressure gauges
ii)
If a mercury differential
manometer
is connected in place of pressure gauges,
to the tappings such that the connecting tube up to mercury are filled with oil
determine the difference in the level of mercury column.
Can you solve it analytically using laplace transforms and with Matlab code as well please. Thank You
Chapter 32 Solutions
EBK MANUFACTURING ENGINEERING & TECHNOL
Ch. 32 - What is the difference between brazing and...Ch. 32 - Are fluxes necessary in brazing? If so, why?Ch. 32 - Why is surface preparation important in...Ch. 32 - What materials are typically used in solder?Ch. 32 - Soldering is generally applied to thinner...Ch. 32 - Explain the reasons why a variety of mechanical...Ch. 32 - List three brazing and three soldering techniques.Ch. 32 - Describe the similarities and differences between...Ch. 32 - What precautions should be taken in the...Ch. 32 - What difficulties are involved in joining...
Ch. 32 - Prob. 11RQCh. 32 - What are the principles of (a) wave soldering...Ch. 32 - What is a peel test? Why is it useful?Ch. 32 - What is a combination joint?Ch. 32 - Prob. 15RQCh. 32 - Prob. 16QLPCh. 32 - Prob. 17QLPCh. 32 - Comment on your observations concerning the...Ch. 32 - Give examples of combination joints other than...Ch. 32 - Discuss the need for fixtures for holding...Ch. 32 - Explain why adhesively bonded joints tend to be...Ch. 32 - It is common practice to tin-plate electrical...Ch. 32 - Give three applications where adhesive-bonding is...Ch. 32 - Prob. 24QLPCh. 32 - If you are designing a joint that must be strong...Ch. 32 - Prob. 26QLPCh. 32 - Rate lap, butt, and scarf joints in terms of...Ch. 32 - Prob. 28QLPCh. 32 - Prob. 29QTPCh. 32 - Prob. 30QTPCh. 32 - Prob. 31QTPCh. 32 - Figure 32.4 shows qualitatively the tensile and...Ch. 32 - When manufacturing the fuselage of a commuter...Ch. 32 - Prob. 34SDPCh. 32 - Name several products that have been assembled...Ch. 32 - Suggest methods of attaching a round bar (made of...Ch. 32 - Prob. 38SDPCh. 32 - Prob. 39SDPCh. 32 - Prob. 40SDPCh. 32 - Prob. 41SDPCh. 32 - Describe part shapes that cannot be joined by...Ch. 32 - Prob. 43SDPCh. 32 - Prob. 44SDPCh. 32 - Prob. 45SDPCh. 32 - Prob. 46SDPCh. 32 - Review Fig. 32.9a and explain the shortcoming...
Knowledge Booster
Learn more about
Need a deep-dive on the concept behind this application? Look no further. Learn more about this topic, mechanical-engineering and related others by exploring similar questions and additional content below.Similar questions
- Can you solve it analytically using laplace transforms and with Matlab code as well please. Thank You.arrow_forwardQ11. Determine the magnitude of the reaction force at C. 1.5 m a) 4 KN D b) 6.5 kN c) 8 kN d) e) 11.3 KN 20 kN -1.5 m- C 4 kN -1.5 m B Mechanical engineering, No Chatgpt.arrow_forwardplease help with this practice problem(not a graded assignment, this is a practice exam), and please explain how to use sohcahtoaarrow_forward
- Solve this problem and show all of the workarrow_forwardSolve this problem and show all of the workarrow_forwardaversity of Baoyion aculty of Engineering-AIMusyab Automobile Eng. Dep. Year: 2022-2023, st Course, 1st Attempt Stage: 3rd Subject: Heat Transfer I Date: 2023\01\23- Monday Time: 3 Hours Q4: A thick slab of copper initially at a uniform temperature of 20°C is suddenly exposed to radiation at one surface such that the net heat flux is maintained at a constant value of 3×105 W/m². Using the explicit finite-difference techniques with a space increment of Ax = = 75 mm, determine the temperature at the irradiated surface and at an interior point that is 150 mm from the surface after 2 min have elapsed. Q5: (12.5 M) A) A steel bar 2.5 cm square and 7.5 cm long is initially at a temperature of 250°C. It is immersed in a tank of oil maintained at 30°C. The heat-transfer coefficient is 570 W/m². C. Calculate the temperature in the center of the bar after 3 min. B) Air at 90°C and atmospheric pressure flows over a horizontal flat plate at 60 m/s. The plate is 60 cm square and is maintained at a…arrow_forward
- University of Baby on Faculty of Engineering-AIMusyab Automobile Eng. Dep. Year: 2022-2023. 1 Course, 1" Attempt Stage 3 Subject Heat Transfer I Date: 2023 01 23- Monday Time: 3 Hours Notes: Q1: • • Answer four questions only Use Troles and Appendices A) A flat wall is exposed to an environmental temperature of 38°C. The wall is covered with a layer of insulation 2.5 cm thick whose thermal conductivity is 1.4 W/m. C, and the temperature of the wall on the inside of the insulation is 315°C. The wall loses heat to the environment by convection. Compute the value of the convection heat-transfer coefficient that must be maintained on the outer surface of the insulation to ensure that the outer-surface temperature does not exceed 41°C. B) A vertical square plate, 30 cm on a side, is maintained at 50°C and exposed to room air at 20°C. The surface emissivity is 0.8. Calculate the total heat lost by both sides of the plate. (12.5 M) Q2: An aluminum fin 1.5 mm thick is placed on a circular tube…arrow_forwardSolve using graphical method and analytical method, only expert should solvearrow_forwardSolve this and show all of the workarrow_forward
arrow_back_ios
SEE MORE QUESTIONS
arrow_forward_ios
Recommended textbooks for you
- Welding: Principles and Applications (MindTap Cou...Mechanical EngineeringISBN:9781305494695Author:Larry JeffusPublisher:Cengage Learning
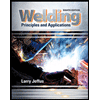
Welding: Principles and Applications (MindTap Cou...
Mechanical Engineering
ISBN:9781305494695
Author:Larry Jeffus
Publisher:Cengage Learning
Metal Joining Process-Welding, Brazing and Soldering; Author: Toc H Kochi;https://www.youtube.com/watch?v=PPT5_fDSzGY;License: Standard YouTube License, CC-BY