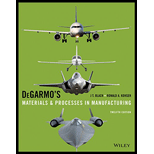
DeGarmo's Materials and Processes in Manufacturing
12th Edition
ISBN: 9781118987674
Author: J. T. Black, Ronald A. Kohser
Publisher: WILEY
expand_more
expand_more
format_list_bulleted
Concept explainers
Question
Chapter 24, Problem 18RQ
To determine
The basic principle of a universal dividing head.
Expert Solution & Answer

Want to see the full answer?
Check out a sample textbook solution
Students have asked these similar questions
for this 4 figuredarw the Kinematic Diagram:DoF:F=Type/Name ofmechanismEvolution:
Two channels and two plates are used to formthe column section shown. For b = 200 mm,determine the moments of inertia and theradii of gyration of the combined section withrespect to the centroidal x and y axes.For the section of problem, determine thefirst moment of the upper plate about thecentroidal x-axis
Determine by direct integration the moment of inertia of theshaded area at right with respect to the x axis shown.
Determine by direct integration the moment of inertia of theshaded area of the figure with respect to the y axis shown.
Chapter 24 Solutions
DeGarmo's Materials and Processes in Manufacturing
Ch. 24 - Suppose that you wanted to machine cast iron with...Ch. 24 - How is the feed per tooth related to the feed rate...Ch. 24 - Why must the number of teeth on the cutter be...Ch. 24 - Why is the question of up or down milling more...Ch. 24 - For producing flat surfaces in mass-production...Ch. 24 - Milling has a higher metal removal rate than...Ch. 24 - Which type of milling (up or down) is being done...Ch. 24 - Why does down milling dull the cutter more rapidly...Ch. 24 - What parameters do you need to specify in order to...Ch. 24 - In Figure 24.2b, the tool material is carbide....
Ch. 24 - What is the advantage of a helical-tooth cutter...Ch. 24 - What would the cutting force diagram for Fc look...Ch. 24 - Could the stub arbor-mounted face mill shown in...Ch. 24 - In a typical solid arbor milling cutter shown in...Ch. 24 - Make some sketches to show how you would you set...Ch. 24 - Make some sketches to show how you would set up a...Ch. 24 - Explain how controlled movements of the work m...Ch. 24 - Prob. 18RQCh. 24 - What is the purpose of the hole-circle plate on a...Ch. 24 - You have selected a feed per tooth and a cutting...Ch. 24 - How much time will be required for a milling...Ch. 24 - If the depth of cut is 0.35 in., what is the metal...Ch. 24 - Prob. 4PCh. 24 - Calculate the spindle rpm and table feed (ipm) for...Ch. 24 - A gray cast iron surface 6 in. wide and 18 in....Ch. 24 - Prob. 7PCh. 24 - In Figure 24.12, the feed is 0.006 in. per tooth....Ch. 24 - Suppose you want to do the job described in...Ch. 24 - The Bridgeport vertical-spindle milling machine is...Ch. 24 - The KC Machine Works, which does job shop...
Knowledge Booster
Learn more about
Need a deep-dive on the concept behind this application? Look no further. Learn more about this topic, mechanical-engineering and related others by exploring similar questions and additional content below.Similar questions
- For the following MATLAB code, I need to answer a few questions. Can you identify the curves as elliptic functions? Which curves reflect the sn, cn, and dn functions?From the curves, determine the maximum amplitudes and the period corresponding toeach angular velocity component. clc; clear all; I = [500; 125; 425]; w = [0.2; 0.1; 0.2]; rev = 0:0.01:10; C = eye(3); % Using ode45 to integrate the KDE and DDE options = odeset('RelTol',1e-9,'AbsTol',1e-9); result = ode45(@K_DDE, rev, [w; I; C(:)], options); v = result.x; % Extracting information from the ode45 solver w = result.y(1:3, :); C_ode = reshape(result.y(7:end, :), [3,3,length(v)]); plot(v, w) xlabel('rev') ylabel('w (rad/s)') legend('w1', 'w2', 'w3') % Functions function dwCdt = K_DDE(~, w_IC) % Extracting the initial condtions to a variable w = w_IC(1:3); I = w_IC(4:6); C = reshape(w_IC(7:end), [3, 3]); I1 = I(1); I2 = I(2); I3 = I(3); K1 = -(I3-I2)/I1; K2 = -(I1-I3)/I2; K3 = -(I2-I1)/I3; %…arrow_forwardplease show a drawing/image and explain how to properly do the question. thanksarrow_forwardFor the four-bar- linkage shown in the following figure. BC=68mm, CD=100mm, AD=120mm. Determine the range of AB to make it a crank-rocker mechanism. B Darrow_forward
- all of those 4 fi 1)Draw kinematic diagram: 2)DOF: 3)type/name of mechanism 4)evolution:arrow_forward7.4 Impeller viscometer The rheology of a Penicillium chrysogenum broth is examined using an impeller viscometer. The density of the cell suspension is approximately 1000 kg m³. Samples of broth are stirred under laminar conditions using a Rushton turbine of diameter 4 cm in a glass beaker of diameter 15 cm. The average shear rate generated by the impeller is greater than the stirrer speed by a factor of about 10.2. When the stirrer shaft is attached to a device for measuring torque and rotational speed, the following results are recorded. Stirrer speed (s¹) Torque (Nm) 0.185 3.57 × 10-6 0.163 3.45 × 10-6 0.126 3.31 x 10-6 0.111 3.20×10-6 Can the rheology be described using a power-law model? If so, evaluate K and n.arrow_forward(read image)arrow_forward
- (read image) Answer Providedarrow_forwardThis is part B Part A's question and answer was find moment of inertia (Ix = 3.90×10^5) and radius of gyration (kx = 21.861) Determine the centroid ( x & y ) of the I-section, Calculate the moment of inertia of the section about itscentroidal x & y axes. How or why is this result different fromthe result of a previous problem?arrow_forwardDetermine by direct integration the moment of inertia of theshaded area of figure with respect to the y axis shownarrow_forward
- Consider the feedback controlled blending system shown below, which is designed to keep theoutlet concentration constant despite potential variations in the stream 1 composition. The density of all streamsis 920 kg/m3. At the nominal steady state, the flow rates of streams 1 and 2 are 950 and 425 kg/min,respectively, the liquid level in the tank is 1.3 m, the incoming mass fractions are x1 = 0.27, x2 = 0.54. Noticethe overflow line, indicating that the liquid level remains constant (i.e. any change in total inlet flow ratetranslates immediately to the same change in the outlet flow rate). You may assume the stream 1 flowrate andthe stream 2 composition are both constant. Use minutes as the time unit throughout this problem. Identify any controlled variable(s) (CVs), manipulated variable(s) (MVs),and disturbance variable(s) (DVs) in this problem. For each, explain how you know that’show it is classified.CVs: ___________, MVs: _____________, DVs: ______________ b) Draw a block diagram…arrow_forwardA heat transfer experiment is conducted on two identical spheres which are initially at the same temperature. The spheres are cooled by placing them in a channel. The fluid velocity in the channel is non-uniform, having a profile as shown. Which sphere cools off more rapidly? Explain. V 1arrow_forwardMy ID# 016948724 last 2 ID# 24 Last 3 ID# 724 Please help to find the correct answer for this problem using my ID# first write le line of action and then help me to find the forces {fx= , fy= mz= and for the last find the moment of inertial about the show x and y axes please show how to solve step by steparrow_forward
arrow_back_ios
SEE MORE QUESTIONS
arrow_forward_ios
Recommended textbooks for you
- Precision Machining Technology (MindTap Course Li...Mechanical EngineeringISBN:9781285444543Author:Peter J. Hoffman, Eric S. Hopewell, Brian JanesPublisher:Cengage Learning
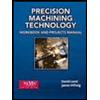
Precision Machining Technology (MindTap Course Li...
Mechanical Engineering
ISBN:9781285444543
Author:Peter J. Hoffman, Eric S. Hopewell, Brian Janes
Publisher:Cengage Learning