EBK MANUFACTURING ENGINEERING & TECHNOL
7th Edition
ISBN: 9780100793439
Author: KALPAKJIAN
Publisher: YUZU
expand_more
expand_more
format_list_bulleted
Concept explainers
Textbook Question
Chapter 23, Problem 21QLP
Explain why the sequence of drilling, boring, and reaming produces a hole that is more accurate than drilling and reaming it only.
Expert Solution & Answer

Want to see the full answer?
Check out a sample textbook solution
Students have asked these similar questions
Solve this problem and show all of the work
Given that an L-shaped member (OAB) can rotate about OA, determine the moment vector created by the force about the line OA at the instant shown in the figure below. OA lies in the xy-plane, and the AB part is vertical. Express your answer as a Cartesian vector.
Determine the magnitude of the moment created by the force about the point A.
Chapter 23 Solutions
EBK MANUFACTURING ENGINEERING & TECHNOL
Ch. 23 - Describe the types of machining operations that...Ch. 23 - What is turning? What kind of chips are produced...Ch. 23 - What is the thrust force in turning? What is the...Ch. 23 - What are the components of a lathe?Ch. 23 - (a) What is a tracer lathe? (b) What is an...Ch. 23 - Describe the operations that can be performed on a...Ch. 23 - Why were power chucks developed?Ch. 23 - Explain why operations such as boring on a lathe...Ch. 23 - Why are turret lathes typically equipped with more...Ch. 23 - Describe the differences between boring a...
Ch. 23 - How is drill life determined?Ch. 23 - What is the difference between a conventional...Ch. 23 - Why are reaming operations performed?Ch. 23 - Explain the functions of the saddle on a lathe.Ch. 23 - Describe the relative advantages of (a)...Ch. 23 - Explain how external threads are cut on a lathe.Ch. 23 - Prob. 17RQCh. 23 - Explain the reasoning behind the various design...Ch. 23 - Note that both the terms tool strength and...Ch. 23 - (a) List and explain the factors that contribute...Ch. 23 - Explain why the sequence of drilling, boring, and...Ch. 23 - Why would machining operations be necessary even...Ch. 23 - A highly oxidized and uneven round bar is being...Ch. 23 - Describe the difficulties that may be encountered...Ch. 23 - (a) Does the force or torque in drilling change as...Ch. 23 - Explain the similarities and differences in the...Ch. 23 - Describe the advantages and applications of having...Ch. 23 - Assume that you are asked to perform a boring...Ch. 23 - Explain the reasons for the major trend that has...Ch. 23 - Describe your observations concerning the contents...Ch. 23 - The footnote to Table 23.12 states that as the...Ch. 23 - In modern manufacturing, which types of metal...Ch. 23 - Sketch the tooling marks you would expect if a...Ch. 23 - What concerns would you have in turning a powder...Ch. 23 - The operational severity for reaming is much lower...Ch. 23 - Review Fig. 23.6, and comment on the factors...Ch. 23 - Explain how gun drills remain centered during...Ch. 23 - Comment on the magnitude of the wedge angle on the...Ch. 23 - If inserts are used in a drill bit (see Fig....Ch. 23 - Refer to Fig. 23.11b, and in addition to the tools...Ch. 23 - Calculate the same quantities as in Example 23.1...Ch. 23 - Estimate the machining time required to rough turn...Ch. 23 - A high-strength cast-iron bar 8 in. in diameter is...Ch. 23 - A 0.30-in.-diameter drill is used on a drill press...Ch. 23 - In Example 23.4, assume that the workpiece...Ch. 23 - For the data in Problem 23.45, calculate the power...Ch. 23 - A 6-in.-diameter aluminum cylinder 10 in. in...Ch. 23 - A lathe is set up to machine a taper on a bar...Ch. 23 - Assuming that the coefficient of friction is 0.25,...Ch. 23 - A 3-in.-diameter, gray cast iron cylindrical part...Ch. 23 - Would you consider the machining processes...Ch. 23 - Would it be difficult to use the machining...Ch. 23 - If a bolt breaks in a hole, it typically is...Ch. 23 - An important trend in machining operations is the...Ch. 23 - Review Fig. 23.8d, and explain if it would be...Ch. 23 - Boring bars can be designed with internal damping...Ch. 23 - A large bolt is to be produced from extruded...Ch. 23 - Make a comprehensive table of the process...
Knowledge Booster
Learn more about
Need a deep-dive on the concept behind this application? Look no further. Learn more about this topic, mechanical-engineering and related others by exploring similar questions and additional content below.Similar questions
- = MMB 241- Tutorial 1.pdf 2/3 80% + + 10. Determine a ats = 1 m v (m/s) 4 s (m) 2 11. Draw the v-t and s-t graphs if v = 0, s=0 when t=0. a (m/s²) 2 t(s) 12. Draw the v-t graph if v = 0 when t=0. Find the equation v = f(t) for each a (m/s²) 2 segment. 2 -2 13. Determine s and a when t = 3 s if s=0 when t = 0. v (m/s) 2 t(s) t(s) 2arrow_forwardQ.5) A cylinder is supported by spring AD and cables AB and AC as shown. The spring has an at rest length (unstretched length) of 4 meters. If the maximum allowable tension in cables AB and AC is 200 N, determine (a) the largest mass (kg) of cylinder E the system can support, (b) the necessary spring constant (stiffness) to maintain equilibrium, and (b) the tension (magnitude) in each cable when supporting the maximum load found in part (a). B 4 m 3 m A E 1 m 3 m D 5 marrow_forwardDetermine the moment created by the force about the point O. Express your answer as a Cartesian vector.arrow_forward
- 4. An impeller rotating at 1150 rpm has the following data: b, = 1 ¼ in., b2 = ¾ in., d, = 7 in., d2 = 15 in., B1 = 18", B2 = 20°, cross-sectional area A = Db if vane thickness is neglected. Assuming radial inlet flow, determine the theoretical capacity in gpm head in ft horsepower 5. If the impeller in Problem (4) develops an actual head of 82 ft and delivers 850 gpm at the point of maximum efficiency and requires 22 BHP. Determine overall pump efficiency virtual velocities V2 and W2arrow_forward(30 pts) Problem 1 A thin uniform rod of mass m and length 2r rests in a smooth hemispherical bowl of radius r. A moment M mgr 4 is applied to the rod. Assume that the bowl is fixed and its rim is in the horizontal plane. HINT: It will help you to find the length l of that portion of the rod that remains outside the bowl. M 2r a) How many degrees of freedom does this system have? b) Write an equation for the virtual work in terms of the angle 0 and the motion of the center of mass (TF) c) Derive an equation for the variation in the position of the center of mass (i.e., Sŕƒ) a. HINT: Use the center of the bowl as the coordinate system origin for the problem. d) In the case of no applied moment (i.e., M 0), derive an equation that can be used to solve for the equilibrium angle of the rod. DO NOT solve the equation e) In the case of an applied moment (i.e., M = mgr = -) derive an equation that can be used to 4 solve for the equilibrium angle of the rod. DO NOT solve the equation. f) Can…arrow_forwardPlease show all work step by steparrow_forward
- Copyright 2013 Pearson Education, publishing as Prentice Hall 2. Determine the force that the jaws J of the metal cutters exert on the smooth cable C if 100-N forces are applied to the handles. The jaws are pinned at E and A, and D and B. There is also a pin at F. E 400 mm 15° D B 30 mm² 80 mm/ 20 mm 15° $15° 20 mm 400 mm 15° 100 N 100 N 15°arrow_forwardDraw for it make a match which directionarrow_forwardQ.1) Block A is connected to block B by a pulley system as shown. The weights of blocks A and B are 100 lbs and 70 lbs, respectively. Assume negligible friction between the rope and all pulleys as well as between block B and the incline and neglect the mass of all pulleys and cables. Determine the angle 0 required to keep the system in equilibrium. (At least two FBDs must be drawn for full credit) B Ꮎ 000arrow_forward
- pls solvearrow_forward+1. 0,63 fin r= 0.051 P The stepped rod in sketch is subjected to a tensile force that varies between 4000 and 7000 lb. The rod has a machined surface finish everywhere except the shoulder area, where a grinding operation has been performed to improve the fatigue resistance of the rod. Using a 99% probability of survival, determine the safety factor for infinite life if the rod is made of AISI 1080 steel, quenched and tempered at 800°c Use the Goodman line. Does the part fail at the fillet? Explainarrow_forwardSolve this problem and show all of the workarrow_forward
arrow_back_ios
SEE MORE QUESTIONS
arrow_forward_ios
Recommended textbooks for you
- Precision Machining Technology (MindTap Course Li...Mechanical EngineeringISBN:9781285444543Author:Peter J. Hoffman, Eric S. Hopewell, Brian JanesPublisher:Cengage Learning
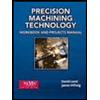
Precision Machining Technology (MindTap Course Li...
Mechanical Engineering
ISBN:9781285444543
Author:Peter J. Hoffman, Eric S. Hopewell, Brian Janes
Publisher:Cengage Learning
The Most Common Metal Machining Processes (Metal Machining Video 1); Author: Sofeast Ltd;https://www.youtube.com/watch?v=uxVJ3qtezGw;License: Standard YouTube License, CC-BY
Machining process and Machine Tools; Author: Amar Gandhi;https://www.youtube.com/watch?v=X2mUJ8baaE0;License: Standard Youtube License