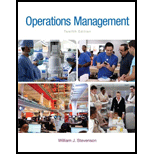
Concept explainers
a)
To compute: The labor productivity under each system.
Introduction: Labor productivity is the measure of productivity of a worker during a period of time. It the ratio of total output to the total productivity hours.
a)

Answer to Problem 4P
Explanation of Solution
Given information:
Prior to buying new equipment:
After buying new equipment:
After buying new equipment, one worker is transferred to another department, equipment cost is increased by $10/hour and output increased by four carts/hour.
Formula:
Calculation of Labor productivity:
Prior to buying new equipment:
Labor productivity prior to buying new equipment is calculated by dividing number of carts of 80 with the number of workers 5 which yields 16 carts/worker/hour
After buying new equipment:
Labor productivity after buying new equipment is calculated by dividing number of carts of 84 with the number of workers 4which yields 21 carts/worker/hour.
Hence, labor productivity before buying new equipment is 16 carts/worker/hour and after buying new equipment is 21 carts/worker/hour.
b)
To compute: The multifactor productivity.
Introduction: Multifactor productivity is also referred as total factor productivity. It is the measure of economic performance by comparing the amount of goods and services produced to the total input used to produce the output.
b)

Answer to Problem 4P
Explanation of Solution
Given information:
Prior to buying new equipment:
After buying new equipment:
After buying new equipment, one worker is transferred to another department, equipment cost is increased by $10/hour and output increased by four carts/hour.
Formula:
Calculation of Multifactor productivity:
Prior to buying new equipment:
Labor cost is calculated by multiplying number of workers (5) with 10/ hours which gives 50/hour.
Multifactor productivity is calculated by dividing output of 80 carts with the total cost of $90 ($50+$40) which yields 0.89 carts/dollar.
After buying new equipment:
Labor cost is calculated by multiplying number of workers (4) with 10/ hours which gives 40/hour.
Multifactor productivity is calculated by dividing output of 84 carts with the total cost of $90 ($40+$50) which yields 0.93 carts/dollar.
Hence, multifactor productivity prior to buying new equipment is 0.89 carts/dollar and after buying new equipment is 0.93 carts/dollar.
c)
To determine: The changes in productivity and comment the best one.
Introduction: Productivity is the measure of performance of a person, machine or an organization. It is computed by dividing the average output per period by the total cost incurred or resources used in the process.
c)

Answer to Problem 4P
Explanation of Solution
Given information:
Prior to buying new equipment:
After buying new equipment:
After buying new equipment, one worker is transferred to another department, equipment cost is increased by $10/hour and output increased by four carts/hour.
Formula:
Labor productivity growth:
The labor productivity growth is calculated by dividing the difference of 21 and 16 with 16 which gives 31.25%
Multifactor productivity growth:
Multifactor productivity growth is calculated by dividing the difference of 0.93 and 0.89 with 0.89 which gives 4.49%.
Hence, labor productivity growth is 31.25% and multifactor productivity growth is 4.49%.
Want to see more full solutions like this?
Chapter 2 Solutions
Loose-leaf for Operations Management (The Mcgraw-hill Series in Operations and Decision Sciences)
- Yellow Press, Inc., buys paper in 1,500-pound rolls for printing. Annual demand is 2,250 rolls. The cost per roll is $625, and the annual holding cost is 20 percent of the cost. Each order costs $75. a. How many rolls should Yellow Press order at a time? Yellow Press should order rolls at a time. (Enter your response rounded to the nearest whole number.)arrow_forwardPlease help with only the one I circled! I solved the others :)arrow_forwardOsprey Sports stocks everything that a musky fisherman could want in the Great North Woods. A particular musky lure has been very popular with local fishermen as well as those who buy lures on the Internet from Osprey Sports. The cost to place orders with the supplier is $40/order; the demand averages 3 lures per day, with a standard deviation of 1 lure; and the inventory holding cost is $1.00/lure/year. The lead time form the supplier is 10 days, with a standard deviation of 2 days. It is important to maintain a 97 percent cycle-service level to properly balance service with inventory holding costs. Osprey Sports is open 350 days a year to allow the owners the opportunity to fish for muskies during the prime season. The owners want to use a continuous review inventory system for this item. Refer to the standard normal table for z-values. a. What order quantity should be used? lures. (Enter your response rounded to the nearest whole number.)arrow_forward
- In a P system, the lead time for a box of weed-killer is two weeks and the review period is one week. Demand during the protection interval averages 262 boxes, with a standard deviation of demand during the protection interval of 40 boxes. a. What is the cycle-service level when the target inventory is set at 350 boxes? Refer to the standard normal table as needed. The cycle-service level is ☐ %. (Enter your response rounded to two decimal places.)arrow_forwardOakwood Hospital is considering using ABC analysis to classify laboratory SKUs into three categories: those that will be delivered daily from their supplier (Class A items), those that will be controlled using a continuous review system (B items), and those that will be held in a two bin system (C items). The following table shows the annual dollar usage for a sample of eight SKUs. Fill in the blanks for annual dollar usage below. (Enter your responses rounded to the mearest whole number.) Annual SKU Unit Value Demand (units) Dollar Usage 1 $1.50 200 2 $0.02 120,000 $ 3 $1.00 40,000 $ 4 $0.02 1,200 5 $4.50 700 6 $0.20 60,000 7 $0.90 350 8 $0.45 80arrow_forwardA part is produced in lots of 1,000 units. It is assembled from 2 components worth $30 total. The value added in production (for labor and variable overhead) is $30 per unit, bringing total costs per completed unit to $60 The average lead time for the part is 7 weeks and annual demand is 3800 units, based on 50 business weeks per year. Part 2 a. How many units of the part are held, on average, in cycle inventory? enter your response here unitsarrow_forward
- assume the initial inventory has no holding cost in the first period and back orders are not permitted. Allocating production capacity to meet demand at a minimum cost using the transportation method. What is the total cost? ENTER your response is a whole number (answer is not $17,000. That was INCORRECT)arrow_forwardRegular Period Time Overtime Supply Available puewag Subcontract Forecast 40 15 15 40 2 35 40 28 15 15 20 15 22 65 60 Initial inventory Regular-time cost per unit Overtime cost per unit Subcontract cost per unit 20 units $100 $150 $200 Carrying cost per unit per month 84arrow_forwardassume that the initial inventory has no holding cost in the first period, and back orders are not permitted. Allocating production capacity to meet demand at a minimum cost using the transportation method. The total cost is? (enter as whole number)arrow_forward
- The S&OP team at Kansas Furniture, led by David Angelow, has received estimates of demand requirements as shown in the table. Assuming one-time stockout costs for lost sales of $125 per unit, inventory carrying costs of $30 per unit per month, and zero beginning and ending inventory, evaluate the following plan on an incremental cost basis: Plan B: Vary the workforce to produce the prior month's demand. Demand was 1,300 units in June. The cost of hiring additional workers is $35 per unit produced. The cost of layoffs is $60 per unit cut back. (Enter all responses as whole numbers.) Note: Both hiring and layoff costs are incurred in the month of the change (i.e., going from production of 1,300 in July to 1300 in August requires a layoff (and related costs) of 0 units in August). Hire Month 1 July Demand 1300 Production (Units) Layoff (Units) Ending Inventory Stockouts (Units) 2 August 1150 3 September 1100 4 October 1600 5 November 1900 6 December 1900arrow_forwardThe S&OP team at Kansas Furniture, led by David Angelow, has received estimates of demand requirements as shown in the table. Assuming one-time stockout costs for lost sales of $100 per unit, inventory carrying costs of $20 per unit per month, and zero beginning and ending inventory, evaluate the following plan on an incremental cost basis: Plan A: Produce at a steady rate (equal to minimum requirements) of 1,100 units per month and subcontract additional units at a $65 per unit premium cost. Subcontracting capacity is limited to 800 units per month. (Enter all responses as whole numbers). Ending Month Demand Production Inventory Subcontract (Units) 1 July 1300 1,100 0 2 August 1150 1,100 0 3 September 1100 1,100 0 4 October 1600 1,100 0 5 November 1900 1,100 0 6 December 1200 1,100 0arrow_forwardPlease help me expand upon my research even more in detail please. Need help added more to mine from the photos please. Not sure what more I can add.arrow_forward
- Practical Management ScienceOperations ManagementISBN:9781337406659Author:WINSTON, Wayne L.Publisher:Cengage,Understanding Management (MindTap Course List)ManagementISBN:9781305502215Author:Richard L. Daft, Dorothy MarcicPublisher:Cengage Learning
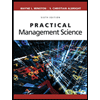
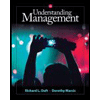