EP PRIN.OF OPERATIONS MGMT.-MYOMLAB
10th Edition
ISBN: 9780134183848
Author: HEIZER
Publisher: PEARSON CO
expand_more
expand_more
format_list_bulleted
Concept explainers
Question
Chapter 13, Problem 15P
Summary Introduction
To determine: The minimum cost using transportation method.
Introduction: Aggregate planning using transportation method helps to attain the minimum cost with the optimal plan. The major advantage of transportation method is to achieve the optimal solution using optimal plans.
Expert Solution & Answer

Want to see the full answer?
Check out a sample textbook solution
Students have asked these similar questions
Identify specific performance management processes covered in this course and how each aligns with an elements of LaFevor’s HCMS Model.
Identify specific performance management processes covered in this course and how each aligns with LaFevor’s HCMS Model.
LaFevor, K. (2017). What’s in Your Human Capital Management Strategy? The Game Plan, the Path, and Achieving
assess how Human Capital Management Strategy is aimed at building an effective integrated performance management system:
Discuss how human capital management strategy relates to performance management.
Chapter 13 Solutions
EP PRIN.OF OPERATIONS MGMT.-MYOMLAB
Ch. 13 - Make the case for, and then against, this pricing...Ch. 13 - Prob. 1DQCh. 13 - Why are SOP teams typically cross-functional?Ch. 13 - Prob. 3DQCh. 13 - Prob. 4DQCh. 13 - Prob. 5DQCh. 13 - Prob. 6DQCh. 13 - Prob. 7DQCh. 13 - Prob. 8DQCh. 13 - Prob. 9DQ
Ch. 13 - Prob. 10DQCh. 13 - Prob. 11DQCh. 13 - Prob. 12DQCh. 13 - Prob. 13DQCh. 13 - Prob. 14DQCh. 13 - Prob. 1PCh. 13 - Prob. 2PCh. 13 - The president of Hill Enterprises, Terri Hill,...Ch. 13 - Prob. 4PCh. 13 - Prob. 5PCh. 13 - Prob. 6PCh. 13 - Consuelo Chua, Inc., is a disk drive manufacturer...Ch. 13 - Prob. 8PCh. 13 - Prob. 9PCh. 13 - Prob. 10PCh. 13 - Prob. 11PCh. 13 - Southeast Soda Pop, Inc., has a new fruit drink...Ch. 13 - Ram Roys firm has developed the following supply,...Ch. 13 - Jerusalem Medical Ltd., an Israeli producer of...Ch. 13 - Prob. 15PCh. 13 - Prob. 16PCh. 13 - Prob. 17PCh. 13 - Prob. 18PCh. 13 - Dwayne Cole, owner of a Florida firm that...Ch. 13 - Prob. 24PCh. 13 - Prob. 25PCh. 13 - Prob. 26PCh. 13 - Evaluate the various configurations of operating...Ch. 13 - Prob. 2CSCh. 13 - After researching revenue (yield) management in...Ch. 13 - The Magic used its original pricing systems of...Ch. 13 - Prob. 3VC
Knowledge Booster
Learn more about
Need a deep-dive on the concept behind this application? Look no further. Learn more about this topic, operations-management and related others by exploring similar questions and additional content below.Similar questions
- CASE STUDY 9-1 Was Robert Eaton a Good Performance Management Leader? R obert Eaton was CEO and chairman of Chrys- ler from 1993 to 1998, replacing Lee Iacocca, who retired after serving in this capacity since 1978. Eaton then served as cochairman of the newly merged DaimlerChrysler organization from 1998 to 2000. In fact, Eaton was responsible for the sale of Chrysler Corporation to Daimler-Benz, thereby creating DaimlerChrysler. With 362,100 employees, DaimlerChrysler had achieved revenues of €136.4 billion in 2003. DaimlerChrysler's passenger car brands included Maybach, Mercedes-Benz, Chrysler, Jeep, Dodge, and Smart. Commercial vehicle brands included Mercedes-Benz, Freightliner, Sterling, Western Star, and Setra. From the beginning of his tenure as CEO, Eaton communicated with the people under him. He immediately shared his plans for the future with his top four executives, and upon the advice of his colleague, Bob Lutz, decided to look around the company before making any hasty…arrow_forwardCritically assess Martin’s coaching style.arrow_forwardCompare Robert Eaton’s performance management leadership presented in the case against the performance management leadership principles, functions, and behaviors. What recommendations can be made about what he might do more effectively? Explain and defend your answer.arrow_forward
- In the context of the material in Chapter 9, provide a critical analysis of the decisions that Henry has made in assigning Martin to this role.arrow_forwardpanies (pp. 80-118). New York, NY: Times Books, specifically Chap. 4, "Robert Eaton and Robert Lutz; The Copilots." CASE STUDY 9-2 Performance Management Leadership at Henry's Commercial Sales and Leasing H enry is the owner of a small real estate agency that handles the sale and leasing of commercial property. He has two real estate agents working in the office, along with himself. He also has two customer service representatives (CSRs), each of whom has a real estate license, and one receptionist who has worked for the company for about three months. Henry has recently decided that he needs another customer service representative. He hasarrow_forwardDiscuss possible solutions to help Tara become an effective CSR. What should martin be doing to help her?arrow_forward
- What are the ethical challenges regarding employees (i.e., diversity, discrimination, sexual harassment, privacy, employee theft, bad leadership, etc.) that Apple Inc. has faced over the past five to ten years and that they should prepare to face in the next five to ten years. Once a developed list of challenges is created, consider how having faced those challenges will impact and be impacted by the social cause you've selected. Propose the findings on the ethical challenges faced by Apple Inc. in recent history and the near future. Analyze ways in which each challenge was (and/or could be) appropriately handled and areas for improvement. Evaluate the ethical/moral aspects of Apple Inc. that protected it from ethical challenges in the past and could protect it in the future. Assess how ethical challenges and handling of ethical challenges could positively or negatively impact the charitable cause are selected and how the selection of your social cause could positively or negatively…arrow_forwardBy selecting Cigna Accredo pharmacy that i identify in my resand compare the current feedback system against the “Characteristics of a Good Multiple Source Feedback Systems” described in section 8-3-3. What can be improved? As a consultant, what recommendations would you make?arrow_forwardScenario You have been given a task to create a demand forecast for the second year of sales of a premium outdoor grill. Accurate forecasts are important for many reasons, including for the company to ensure they have the materials they need to create the products required in a certain period of time. Your objective is to minimize the forecast error, which will be measured using the Mean Absolute Percentage Error (MAPE) with a goal of being below 25%. You have historical monthly sales data for the past year and access to software that provides forecasts based on five different forecasting techniques (Naïve, 3-Month Moving Average, Exponential Smoothing for .2, Exponential Smooth for .5, and Seasonal) to help determine the best forecast for that particular month. Based on the given data, you will identify trends and patterns to create a more accurate forecast. Approach Consider the previous month's forecast to identify which technique is most effective. Use that to forecast the next…arrow_forward
- Approach Consider the previous month's forecast to identify which technique is most effective. Use that to forecast the next month. Remember to select the forecasting technique that produces the forecast error nearest to zero. For example: a. Naïve Forecast is 230 and the Forecast Error is -15. b. 3-Month Moving Forecast is 290 and the Forecast Error is -75. c. Exponential Smoothing Forecast for .2 is 308 and the Forecast Error is -93. d. Exponential Smoothing Forecast for .5 is 279 and the Forecast Error is -64. e. Seasonal Forecast is 297 and the Forecast Error is -82. The forecast for the next month would be 230 as the Naïve Forecast had the Forecast Error closest to zero with a -15. This forecasting technique was the best performing technique for that month. You do not need to do any external analysis-the forecast error for each strategy is already calculated for you in the tables below. Naïve Month Period Actual Demand Naïve Forecast Error 3- Month Moving Forecast 3- Month Moving…arrow_forwardScenario You have been given a task to create a demand forecast for the second year of sales of a premium outdoor grill. Accurate forecasts are important for many reasons, including for the company to ensure they have the materials they need to create the products required in a certain period of time. Your objective is to minimize the forecast error, which will be measured using the Mean Absolute Percentage Error (MAPE) with a goal of being below 25%. You have historical monthly sales data for the past year and access to software that provides forecasts based on five different forecasting techniques (Naïve, 3-Month Moving Average, Exponential Smoothing for .2, Exponential Smooth for .5, and Seasonal) to help determine the best forecast for that particular month. Based on the given data, you will identify trends and patterns to create a more accurate forecast. Approach Consider the previous month's forecast to identify which technique is most effective. Use that to forecast the next…arrow_forwardUse the internet to obtain crash safety ratings for passenger vehicles. Then, answer thesequestions:a. Which vehicles received the highest ratings? The lowest ratings?b. How important are crash-safety ratings to new car buyers? Does the degree of importancedepend on the circumstances of the buyer?c. Which types of buyers would you expect to be the most concerned with crash-safety ratings?d. Are there other features of a new car that might sway a buyer from focusing solely on crashsafety? If so, what might they be?arrow_forward
arrow_back_ios
SEE MORE QUESTIONS
arrow_forward_ios
Recommended textbooks for you
- Practical Management ScienceOperations ManagementISBN:9781337406659Author:WINSTON, Wayne L.Publisher:Cengage,Purchasing and Supply Chain ManagementOperations ManagementISBN:9781285869681Author:Robert M. Monczka, Robert B. Handfield, Larry C. Giunipero, James L. PattersonPublisher:Cengage Learning
- MarketingMarketingISBN:9780357033791Author:Pride, William MPublisher:South Western Educational Publishing
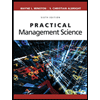
Practical Management Science
Operations Management
ISBN:9781337406659
Author:WINSTON, Wayne L.
Publisher:Cengage,
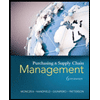
Purchasing and Supply Chain Management
Operations Management
ISBN:9781285869681
Author:Robert M. Monczka, Robert B. Handfield, Larry C. Giunipero, James L. Patterson
Publisher:Cengage Learning
Marketing
Marketing
ISBN:9780357033791
Author:Pride, William M
Publisher:South Western Educational Publishing
Inventory Management | Concepts, Examples and Solved Problems; Author: Dr. Bharatendra Rai;https://www.youtube.com/watch?v=2n9NLZTIlz8;License: Standard YouTube License, CC-BY