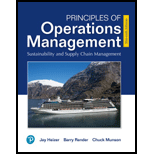
Concept explainers
a)
To determine: The optimal order quantity with the minimum annual cost for purchasing the integrated chips.
Introduction:
Quantity discount model:
Quantity discount model is a scenario where manufacturing companies receive price discount for ordering large quantities. The firm will estimate if the discount quantity is profitable for the firm and make the decision.
Economic order quantity (EOQ):
EOQ is the quantity of units a company must add to its inventory so as to minimize the total inventory costs. It will determine the ideal order quantity which will decrease the inventory management costs.
Annual holding cost:
Annual holding cost is the cost involved in holding the excess inventory present within a firm. The excess inventory will be carried on for the next year and used for production.
Annual ordering cost:
Annual ordering cost is the cost involved in making a purchase order and the following up of that order. It will account for the labor involved and other associated costs.
Purchase cost:
Purchase cost is the cost incurred to purchase the require components to satisfy the demand of the firm. The cost will vary according to the demand.
Total cost:
Total cost is the overall cost taking into estimation of the holding, ordering and the purchase cost of the materials.
a)

Answer to Problem 22P
The optimal order quantity is 200 units with the minimum annual cost of $1,446,380
Explanation of Solution
Given information:
Monthly demand (d)= 400 / month
Holding cost (H) = $35 / unit / year
Ordering cost (S) = $120 / order
Purchase price (P) = $350 / chip
Price structure:
Quantity purchased | Price / unit |
1 – 99 units | $350 |
100 – 199 units | $325 |
200 or more units | $300 |
Formula to calculate EOQ:
Formula to calculate annual holding cost:
Formula to calculate annual ordering cost:
Formula to calculate purchase cost:
Formula to calculate total cost:
Calculation of EOQ:
The obtained EOQ value is in the range of (100 – 199 units). Hence, the price of that range will be used for calculation.
Calculation of values at (EOQ = 181):
Calculation of annual holding cost at (EOQ = 181):
Calculation of annual ordering cost at (EOQ = 181):
Calculation of purchase cost:
Calculation of total cost at (EOQ = 181):
The total cost at the (EOQ = 181) is $1,566,350.
Calculation of values at discount quantity (200):
The next price break after the EOQ at 181 units is (200 or more units). The price of that range will be used in the following calculation.
Calculation of annual holding cost at (EOQ = 200):
Calculation of annual ordering cost at (EOQ = 200):
Calculation of purchase cost:
Calculation of total cost at (EOQ = 200):
The total cost at the (EOQ = 200) is $1,446,380
Calculation of difference in cost:
The total cost at (EOQ = 181) is $1,566,350. The total cost at (EOQ = 200) is $1,446,380. Therefore (EOQ = 200) has lesser cost ($1,446,380 < 1,566,350).
Hence, the optimal order quantity is 200 units with the minimum annual cost of $1,446,380
b)
To determine: The optimal order quantity with the minimum annual cost for purchasing the integrated chips.
b)

Answer to Problem 22P
The optimal order quantity is 200 units with the minimum annual cost of $1,445,880
Explanation of Solution
Given information:
Monthly demand (d)= 400 / month
Holding cost (H) = 10 % of purchase price of the price structure
Ordering cost (S) = $120 / order
Purchase price (P) = $350 / chip
Price structure:
Quantity purchased | Price / unit |
1 – 99 units | $350 |
100 – 199 units | $325 |
200 or more units | $300 |
Formula to calculate EOQ:
Formula to calculate annual holding cost:
Formula to calculate annual ordering cost:
Formula to calculate purchase cost:
Formula to calculate total cost:
Calculation of EOQ at each price structure:
EOQ at price = $350
EOQ at price = $325
EOQ at price = $300
EOQ = 181, cannot be bought at the price of $350. EOQ = 196 cannot be bought at the price of $300.
Hence, the EOQ is 188 units.
The obtained EOQ value is in the range of (100 – 199 units). Hence, the price of that range will be used for calculation.
Calculation of values at (EOQ = 188):
Calculation of annual holding cost at (EOQ = 188):
Calculation of annual ordering cost at (EOQ = 188):
Calculation of purchase cost:
Calculation of total cost at (EOQ = 188):
The total cost at the (EOQ = 188) is $1,566,319.
Calculation of values at discount quantity (200):
The next price break after the EOQ at 188 units is (200 or more units). The price of that range will be used in the following calculation.
Calculation of annual holding cost at (EOQ = 200):
Calculation of annual ordering cost at (EOQ = 200):
Calculation of purchase cost:
Calculation of total cost at (EOQ = 200):
The total cost at the (EOQ = 200) is $1,445,880
Calculation of difference in cost:
The total cost at (EOQ = 188) is $1,566,319. The total cost at (EOQ = 200) is $1,445,880. Therefore (EOQ = 200) has lesser cost ($1,445,880 < 1,566,319).
Hence, the optimal order quantity is 200 units with the minimum annual cost of $1,445,880.
Want to see more full solutions like this?
Chapter 12 Solutions
EBK PRINCIPLES OF OPERATIONS MANAGEMENT
- Currently a company that designs Web sites has five customers in its backlog. The time since the order arrived, processing time, and promised due dates are given in the following table. The customers are ready to be scheduled today, which is the start of day 190. Time Since Order Arrived Customer (days ago) Processing Time (days) Due Date (days from now) A 3 24 58 B 2 32 100 с 10 20 26 D E 8 6 12 28 50 66 a. Develop separate schedules by using the FCFS and EDD rules. Compare the schedules on the basis of average flow time and average days past due. Using the FCFS (first come, first served) decision rule for sequencing the customers, the order is: Sequence Customer 1 2 3 4 5arrow_forwardThe Donald Fertilizer Company produces industrial chemical fertilizers. The projected manufacturing requirements (in gallons) for the next four quarters are 60,000, 90,000, 90,000, and 140,000 respectively. A level workforce is desired, relying only on anticipation inventory as a supply option. Stockouts and backorders are to be avoided, as are overtime and undertime. a. Determine the quarterly production rate required to meet total demand for the year, and minimize the anticipation inventory that would be left over at the end of the year. Beginning inventory is 0. The quarterly production rate is ☐ gallons. (Enter your response as an integer.)arrow_forwardHow would you design an operations plan and schedule for a new product/service? What factors would you consider and what challenges would you anticipate? Why are these factors and challenges relevant and how would you address them?arrow_forward
- You are the newly appointed CEO of TechSouth, a South African multinational technology company based in Cape Town. TechSouth specialises in manufacturing smartphones, laptops, and smart home devices. The company has a significant presence in the African market and has recently expanded into Europe and Asia. However, TechSouth is facing several critical challenges:· Declining Market Share - Over the past three years, TechSouth has lost considerable market share to both localcompetitors and international giants like Samsung and Apple. The company's products are perceived as outdated and lacking innovation.· Employee Engagement Issues - Recent employee surveys indicate low morale and engagement levels, particularly among the younger workforce, leading to high turnover rates. Many employees feel disconnected from the company's vision and mission.· Siloed Departments - The organizational structure at TechSouth is highly siloed, with departments operatingindependently rather than…arrow_forwardWhat is the best way to manage emotions and thoughts? How to work through Emotions and thoughts?arrow_forwardWhat are the emotions or stressful thoughts? What are the differences between them? How can we work through the emotions or stressful thoughts? How can we avoid or prevent emotions or stressful thoughts from happening or occurring? What are the obstacles?arrow_forward
- Main Challenges at TechInnovateStrategic DirectionTechInnovate's board of directors is pushing for a more aggressive expansion into emerging markets, particularly in Africaand Southeast Asia. However, there's internal disagreement about whether to focus on these new markets or consolidatetheir position in existing ones. Sarah Chen favors rapid expansion, while some senior executives advocate for a morecautious approach.Ethical ConcernsThe company's AI algorithms have come under scrutiny for potential biases, particularly in facial recognition technology.There are concerns that these biases disproportionately affect minority groups. Some employees have voiced ethicalconcerns about selling this technology to law enforcement agencies without addressing these issues.Team Leadership and DiversityTechInnovate's leadership team is predominantly male and Western, despite its global presence. There's growing pressurefrom employees and some board members to diversify the leadership team to…arrow_forwardSarah Anderson, the Marketing Manager at Exeter Township's Cultural Center, is conducting research on the attendance history for cultural events in the area over the past ten years. The following data has been collected on the number of attendees who registered for events at the cultural center. Year Number of Attendees 1 700 2 248 3 633 4 458 5 1410 6 1588 7 1629 8 1301 9 1455 10 1989 You have been hired as a consultant to assist in implementing a forecasting system that utilizes various forecasting techniques to predict attendance for Year 11. a) Calculate the Three-Period Simple Moving Average b) Calculate the Three-Period Weighted Moving Average (weights: 50%, 30%, and 20%; use 50% for the most recent period, 30% for the next most recent, and 20% for the oldest) c) Apply Exponential Smoothing with the smoothing constant alpha = 0.2. d) Perform a Simple Linear Regression analysis and provide the adjusted…arrow_forwardRuby-Star Incorporated is considering two different vendors for one of its top-selling products which has an average weekly demand of 70 units and is valued at $90 per unit. Inbound shipments from vendor 1 will average 390 units with an average lead time (including ordering delays and transit time) of 4 weeks. Inbound shipments from vendor 2 will average 490 units with an average lead time of 2 weeksweeks. Ruby-Star operates 52 weeks per year; it carries a 4-week supply of inventory as safety stock and no anticipation inventory. Part 2 a. The average aggregate inventory value of the product if Ruby-Star used vendor 1 exclusively is $enter your response here.arrow_forward
- Sam's Pet Hotel operates 50 weeks per year, 6 days per week, and uses a continuous review inventory system. It purchases kitty litter for $13.00 per bag. The following information is available about these bags: > Demand 75 bags/week > Order cost = $52.00/order > Annual holding cost = 20 percent of cost > Desired cycle-service level = 80 percent >Lead time = 5 weeks (30 working days) > Standard deviation of weekly demand = 15 bags > Current on-hand inventory is 320 bags, with no open orders or backorders. a. Suppose that the weekly demand forecast of 75 bags is incorrect and actual demand averages only 50 bags per week. How much higher will total costs be, owing to the distorted EOQ caused by this forecast error? The costs will be $higher owing to the error in EOQ. (Enter your response rounded to two decimal places.)arrow_forwardYellow Press, Inc., buys paper in 1,500-pound rolls for printing. Annual demand is 2,250 rolls. The cost per roll is $625, and the annual holding cost is 20 percent of the cost. Each order costs $75. a. How many rolls should Yellow Press order at a time? Yellow Press should order rolls at a time. (Enter your response rounded to the nearest whole number.)arrow_forwardPlease help with only the one I circled! I solved the others :)arrow_forward
- Purchasing and Supply Chain ManagementOperations ManagementISBN:9781285869681Author:Robert M. Monczka, Robert B. Handfield, Larry C. Giunipero, James L. PattersonPublisher:Cengage LearningPractical Management ScienceOperations ManagementISBN:9781337406659Author:WINSTON, Wayne L.Publisher:Cengage,
- Contemporary MarketingMarketingISBN:9780357033777Author:Louis E. Boone, David L. KurtzPublisher:Cengage LearningMarketingMarketingISBN:9780357033791Author:Pride, William MPublisher:South Western Educational Publishing
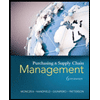
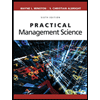
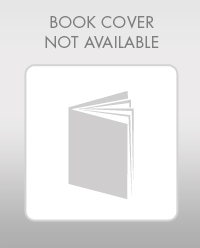