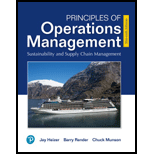
Concept explainers
a)
To calculate: The economic production quantity (EPQ).
Introduction:
Economic production quantity (EPQ):
The economic production quantity is used to determine the amount a company or a retail outlet should purchase at every order so as to minimize the associated total inventory costs. It is done by balancing the holding cost and the ordering cost.
a)

Answer to Problem 18P
The economic production quantity (EPQ) is 671 units.
Explanation of Solution
Given information:
Annual Demand (D) = 12,500 units
Number of working days (N) = 250 / year
Holding cost (H) = $2 / unit / year
Ordering cost (S) = 30 / order
Daily production (p) = 300 / day
Formula to calculate EPQ:
Calculation of EPQ:
Hence, the economic production quantity (EPQ) is 671 units.
b)
To calculate: The number of production runs per year.
Introduction:
Production runs:
The production run is the development of similar or associated goods by utilizing a particular approach or processes.
b)

Answer to Problem 18P
The number of production runs per yearis 18.63.
Explanation of Solution
Given information:
Annual Demand (D) = 12,500 units
Number of working days (N) = 250 / year
Holding cost (H) = $2 / unit / year
Ordering cost (S) = 30 / order
Daily production (p) = 300 / day
Formula to calculate number of production runs:
Calculation of number of production runs:
Hence, the number of production runs per year is 18.63.
c)
To calculate: The maximum inventory level.
Introduction:
Maximum inventory level:
The maximum inventory level is the level of inventory in a firm which should not be exceeded at any circumstances. It is to ensure that the cost of capital is not increased.
c)

Answer to Problem 18P
The maximum inventory level is 559 units.
Explanation of Solution
Given information:
Annual Demand (D) = 12,500 units
Number of working days (N) = 250 / year
Holding cost (H) = $2 / unit / year
Ordering cost (S) = 30 / order
Daily production (p) = 300 / day
Formula to calculate maximum inventory level:
Calculation of maximum inventory level:
Hence, the maximum inventory level is 559 units.
d)
To determine: The percentage of time the facility will be producing components.
d)

Answer to Problem 18P
The percentage of time the facility will be producing componentsis 16.7%.
Explanation of Solution
Given information:
Annual Demand (D) = 12,500 units
Number of working days (N) = 250 / year
Holding cost (H) = $2 / unit / year
Ordering cost (S) = 30 / order
Daily production (p) = 300 / day
Formula to calculate days of demand:
Formula to calculate days of production:
Calculation of days of demand satisfied by each production run:
Calculation of days in production for each order:
Calculation of percent time of production:
The percentage of the time the facility is producing components is calculated by dividing the days in production by the days of demand.
Hence, the percentage of time the facility will be producing components is 16.7%.
e)
To determine: The annual cost of ordering and holding inventory.
e)

Answer to Problem 18P
The annual cost of ordering and holding inventory is $1,117.90
Explanation of Solution
Given information:
Annual Demand (D) = 12,500 units
Number of working days (N) = 250 / year
Holding cost (H) = $2 / unit / year
Ordering cost (S) = 30 / order
Daily production (p) = 300 / day
Formula to calculate the annual cost of ordering and holding inventory:
Calculation of annual cost of ordering and holding inventory:
Hence, the annual cost of ordering and holding inventory is $1,117.90.
Want to see more full solutions like this?
Chapter 12 Solutions
EBK PRINCIPLES OF OPERATIONS MANAGEMENT
- Prepare a graph of the monthly forecasts and average forecast demand for Chicago Paint Corp., a manufacturer of specialized paint for artists. Compute the demand per day for each month (round your responses to one decimal place). Month B Production Days Demand Forecast Demand per Day January 21 950 February 19 1,150 March 21 1,150 April 20 1,250 May 23 1,200 June 22 1,000' July 20 1,350 August 21 1,250 September 21 1,050 October 21 1,050 November 21 December 225 950 19 850arrow_forwardThe president of Hill Enterprises, Terri Hill, projects the firm's aggregate demand requirements over the next 8 months as follows: 2,300 January 1,500 May February 1,700 June 2,100 March April 1,700 1,700 July August 1,900 1,500 Her operations manager is considering a new plan, which begins in January with 200 units of inventory on hand. Stockout cost of lost sales is $125 per unit. Inventory holding cost is $25 per unit per month. Ignore any idle-time costs. The plan is called plan C. Plan C: Keep a stable workforce by maintaining a constant production rate equal to the average gross requirements excluding initial inventory and allow varying inventory levels. Conduct your analysis for January through August. The average monthly demand requirement = units. (Enter your response as a whole number.) In order to arrive at the costs, first compute the ending inventory and stockout units for each month by filling in the table below (enter your responses as whole numbers). Ending E Period…arrow_forwardMention four early warning indicators that a business may be at risk.arrow_forward
- 1. Define risk management and explain its importance in a small business. 2. Describe three types of risks commonly faced by entrepreneurs. 3. Explain the purpose of a risk register. 4. List and briefly describe four risk response strategies. (5 marks) (6 marks) (4 marks) (8 marks) 5. Explain how social media can pose a risk to small businesses. (5 marks) 6. Identify and describe any four hazard-based risks. (8 marks) 7. Mention four early warning indicators that a business may be at risk. (4 marks)arrow_forwardState whether each of the following statements is TRUE or FALSE. 1. Risk management involves identifying, analysing, and mitigating risks. 2. Hazard risks include interest rate fluctuations. 3. Entrepreneurs should avoid all forms of risks. 4. SWOT analysis is a tool for risk identification. 5. Scenario building helps visualise risk responses. 6. Risk appetite defines how much risk an organisation is willing to accept. 7. Diversification is a risk reduction strategy. 8. A risk management framework must align with business goals. 9. Political risk is only relevant in unstable countries. 10. All risks can be eliminated through insurance.arrow_forward9. A hazard-based risk includes A. Political instability B. Ergonomic issues C. Market demand D. Taxation changesarrow_forward
- Purchasing and Supply Chain ManagementOperations ManagementISBN:9781285869681Author:Robert M. Monczka, Robert B. Handfield, Larry C. Giunipero, James L. PattersonPublisher:Cengage LearningPractical Management ScienceOperations ManagementISBN:9781337406659Author:WINSTON, Wayne L.Publisher:Cengage,
- MarketingMarketingISBN:9780357033791Author:Pride, William MPublisher:South Western Educational PublishingContemporary MarketingMarketingISBN:9780357033777Author:Louis E. Boone, David L. KurtzPublisher:Cengage Learning
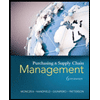
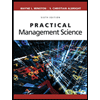
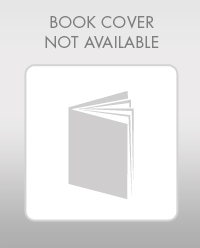