A shaft is loaded in bending and torsion such that Ma = 62 N · m, Ta = 48 N · m, Mm = 54 N · m, and Tm = 25 N · m. For the shaft, Su = 700 MPa and Sy = 560 MPa, and a fully corrected endurance limit of Se = 210 MPa is assumed. Let Kf = 2.2 and Kfs = 1.8. With a design factor of 2.0 determine the minimum acceptable diameter of the shaft in mm using the DE-Goodman criterion.
Design Against Fluctuating Loads
Machine elements are subjected to varieties of loads, some components are subjected to static loads, while some machine components are subjected to fluctuating loads, whose load magnitude tends to fluctuate. The components of a machine, when rotating at a high speed, are subjected to a high degree of load, which fluctuates from a high value to a low value. For the machine elements under the action of static loads, static failure theories are applied to know the safe and hazardous working conditions and regions. However, most of the machine elements are subjected to variable or fluctuating stresses, due to the nature of load that fluctuates from high magnitude to low magnitude. Also, the nature of the loads is repetitive. For instance, shafts, bearings, cams and followers, and so on.
Design Against Fluctuating Load
Stress is defined as force per unit area. When there is localization of huge stresses in mechanical components, due to irregularities present in components and sudden changes in cross-section is known as stress concentration. For example, groves, keyways, screw threads, oil holes, splines etc. are irregularities.
A shaft is loaded in bending and torsion such that Ma = 62 N · m, Ta = 48 N · m, Mm = 54 N · m, and Tm = 25 N · m. For the shaft, Su = 700 MPa and Sy = 560 MPa, and a fully corrected endurance limit of Se = 210 MPa is assumed. Let Kf = 2.2 and Kfs = 1.8. With a design factor of 2.0 determine the minimum acceptable diameter of the shaft in mm using the DE-Goodman criterion.

Step by step
Solved in 2 steps with 1 images

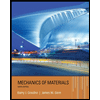
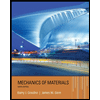