Copy of Lab 11 Physics.docx
pdf
keyboard_arrow_up
School
Laney College *
*We aren’t endorsed by this school
Course
4A
Subject
Mechanical Engineering
Date
Jan 9, 2024
Type
Pages
5
Uploaded by BaronZebra1585
Lab 11 - Physical Pendulum
Procedure
In this experiment, we assembled the necessary equipment, including a Vernier Rotary
Motion Sensor, a right-angle clamp, a vertical support rod, the LabQuest App, and other
related materials. After weighing the aluminum rod and cylindrical weights and
measuring the rotation radius (r), we connected the sensor to the interface and adjusted
the resolution to X4 mode.
In the initial phase, we initiated data collection and used a protractor to displace the rod
through 5, 10, 15, and 20 degree angles, subsequently releasing it. We repeated this
process for various amplitudes, recording data for each run to determine the oscillation
period (T) based on 4 cycles for each graph. Utilizing these values of T, we computed
the angular frequency for each oscillation and documented all collected data in a
dedicated table for Part 1.
Moving to Part 2, we adjusted the weight's position along the rod and measured the
length between the pivot point and the weight's center. Employing a 15-degree
amplitude, we conducted 8 runs, progressively shifting the weight up the rod by 2cm for
each run. All the data from these runs was meticulously recorded in the corresponding
data table for Part 2.
In Part 3, we introduced an additional cylindrical weight to the rod, determining the
distance between the pivot point and this weight's center of mass. Employing the same
15-degree amplitude, we carried out 3 runs, altering the positions of the two weights
along the rod. The resulting data was recorded in the designated data table for Part 3.
Data
Part 1:
Mass of rod: 41.6g
Mass of weight (with screw): 80.5g
Radius: 34cm
L = 38cm
X = 3.3cm
Run #
Amplitude (degrees)
Period of oscillation
(T)
Angular frequency
(w)
1
5 degrees
0.866
7.255
2
10 degrees
0.862
7.289
3
15 degrees
0.862
7.289
4
20 degrees
0.864
7.273
1. The number of angular frequency (w) doesn't seem to change with the range of oscillations.
The rotational frequency pretty much stayed the same as we raised the amplitude. Over all 4
runs, the average rotational frequency was found to be 7.277.
2. Write the formula for the force that pulls the weight back to where it was before it was
released.
Torque = Force * Distance from pivot * sin(theta), where theta is the angle between
the force and the position vector.
3.Write the Newton's second law equation that shows how the weight will move around the pivot
point after it is let go. As a function of time, write the angular acceleration as the second
derivative of the angle theta.
Sum of torques = moment of inertia (I) * angular acceleration (a)
a = d^2(theta)/(dt^2)
4.After dividing your second equation by I, adjust the parts so that the equation equals 0.
Congratulations, you have now made a second order differential equation that describes how
the pendulum bob moves.
(Sum of torques / I) - (d^2 theta / (dt^2 I) = 0
Part 2:
Amplitude: 15 degrees
Mass of rod: 41.6g
Mass of weight (with screw): 80.5g
L = 38cm
X = 3.3cm
Radius
(cm)
h (cm)
I total
(kg*m^3)
w
theoretical
(rad/s)
w
measured
(rad/s)
% diff
w force
(rad/s)
% diff 2
34 cm
27.77
cm
1551.74
kg m^3
4.63 rad/s
7.27 rad/s
57.02%
5.08
rad/s
43.11%
32 cm
26.45
cm
1415.71
kg m^3
4.73 rad/s
5.57 rad/s
17.75%
5.08
rad/s
9.65%
30 cm
25.13
cm
1287.56
kg m^3
4.83 rad/s
5.82 rad/s
20.49%
5.08
rad/s
14.57%
28 cm
23.81
cm
1167.31
kg m^3
4.94 rad/s
5.98 rad/s
21.05%
5.08
rad/s
17.72%
26 cm
22.49
cm
1054.94
kg m^3
5.05 rad/s
6.07 rad/s
20.19%
5.08
rad/s
19.49%
24 cm
21.17
cm
950.47
kg m^3
5.16 rad/s
6.42 rad/s
24.42%
5.08
rad/s
26.38%
22 cm
19.85
cm
853.89
kg m^3
5.27 rad/s
6.61 rad/s
25.43%
5.08
rad/s
30.12%
20 cm
18.53
cm
765.19
kg m^3
5.38 rad/s
6.68 rad/s
24.16%
5.08
rad/s
31.50%
Part 3:
Mass of rod: 41.6g
Your preview ends here
Eager to read complete document? Join bartleby learn and gain access to the full version
- Access to all documents
- Unlimited textbook solutions
- 24/7 expert homework help
Mass of weight (with screw): 80.5g
radius (2) = 33cm
Amplitude = 15 degrees
L = 38cm
X = 3.3cm
Run #
T (period)
Positions of 2 weights
(cm)
w (rad/s)
1
1.14
33 cm
5.51 rad/s
2
0.88
18 cm
7.14 rad/s
3
0.765
8 cm
8.21 rad/s
Calculations
Angular Frequency:
w theoretical = sqrt(Mgh/I)
w measured = 2pi/T
w force = sqrt(g/L) → w force = sqrt(9.8/0.38) =
5.08 rad/s
Moment of Inertia:
I = I(point) + I(rod)
I = mr^2 + 1/12m(rod)
I = mr^2 + 1/2m(rod)L^2 + m(rod)h^2
Mass:
M = m + m(rod)
M = 122.1g
Location of Center of Mass from Pivot:
h = (m(rod) * (L/2 - x) + mr) / (m(rod) + m)
h (part 2 run 1) = [41.6g (38cm/2 - 3.3cm) + 80.5g (34cm)] / (41.6g + 80.5g) =
27.77 cm
Percent Differences:
%diff = (absolute value (w theoretical - w measured)) / w theoretical * 100%
%diff 2 = (absolute value (w measured - w force)) / w force * 100%
Sources of Error
During the whole experiment, there were many things that could go wrong. It's possible
that mistakes were made because of problems with the initial setting, such as small
changes or misaligned weight places. If the gadget used to collect the data wasn't set
up correctly, it could have changed the variation time data that was gathered. It was
important that the results from the motion detectors were correct, so any changes in the
angle vs. time data could have caused uncertainty. A lot of measurements, like the size
of the equipment, were taken by hand, so even small mistakes in these measurements
could have changed the results. Also, the large number of formulas needed for data
analysis meant that mistakes could happen at different times, which could lead to
mistakes in the end results.
Conclusion
In summary, our experiment taught us a lot about how a real pendulum moves and what
changes its behavior when the mass of the system isn't seen as a point mass at the end
of a massless string. We used the data we gathered from various runs that looked at
changes in amplitude, radius, and mass to find the actual angular frequency (w)
numbers for each run. In Part 2, we compared our actual angular frequency to
theoretical values and found that they were pretty close, with a difference of only about
21% on average. As we already said, this difference could be due to mistake sources
and the settings of the experiment. We also noticed that the first run in Part 2 (radius =
34 cm) didn't match up with the other results. Overall, our experiment went well, and the
results were very close to what we thought they would be based on theory. This
research helped us learn more about real pendulums that aren't perfect and showed
how small mistakes in experiments can change the results.
Related Documents
Related Questions
Subject: Mechanical Measurements
Do not copy other online answers
arrow_forward
Produce a 3D solid model of the Guard casing and test boss in solidworks and send a file of it that can be downloaded.
Email: lukecass3456@gmail.com
arrow_forward
Please show step by step work
arrow_forward
A chamber of unknown volume is filled with an unknown amount of ideal gas. A cylinder with an open bottom and calibrated volume is connected to the chamber and is closed with a movable piston. A gas pressure sensor is also mounted on the chamber as shown in the figure. The whole experimental setup is kept at a constant temperature of 300 K. Doris moves the piston from mark 0 to mark 200 mL in steps of 50 mL and records the corresponding pressure in the chamber (see the table below). She moves the piston very slowly and waits several minutes before recording the pressure values.
VCyl(mL)
P(105N/m2))
0
4.35
50
3.85
100
3.50
150
3.15
200
2.90
Determine the volume of the chamber using Doris's data in the table. (Note: This is a problem that requires linearization of data.)
Determine the number of moles of gas. (Note: This is a problem that requires linearization of data.)
arrow_forward
You are watching a live concert. You can also find the concert streaming live on Spotify. About how far must you stand from the stage in order for
the live concert and the live stream to be perfectly in sync?
HINT: Assume the radio signal (Spotify) has to travel all the way around the Earth.
circumference of the Earth (average): 40,041,000 m
Speed of sound: 345 m/s
Speed of light: 300,000,000 m/s
arrow_forward
Sensor systems for obstacle detection and avoidance in mobile robots.
• Design and develop a suitable processor-based Data Acquisition (DAQ) system and external hardware to interface, measure, display and store the responses from the selected sensors.
arrow_forward
System Specification
The aim of task 2 is to design a simulated obstacle detection sensor system for a mobile robot platform. You
should assume your chosen sensors will be placed on a small mobile robot platform as designed in task 1.
The sensor system must be able to detect objects within the range of 0mm to 1000mm and have a field of
vision of 90 degrees (see diagram below). You may need to use multiple sensors to achieve the desired
specification.
Robot
platform
H
0-1000mm
range
90° sensor
view
Example
object
arrow_forward
Steps-Part aStep 1) In order to calculate the spring constant, the spring is positioned vertically, and a small mass is attached to its lower hook.Step 2) Visit the site:https://phet.colorado.edu/sims/html/masses-and-springs/latest/masses-and-springs_en.htmlStep 3) Select the Lab icon.Step 4) Make sure the damping is set to none. Using the ruler, measure the displacement of the spring and calculate the spring constant.Step 5) The mass is removed and securely attached to an inelastic cord. On other end of the cord is attached to the spring. Another segment of cord is attached to the other side of the spring. The opposite end of this cord is left free. This is the end in which the system will be rotated. The setup is shown in Fig. 1. The ball is rotated in a horizontal circle.Step 6) The radius of the system is measured before the spring is displaced.Step 7) The system is now spun around until uniform circular motion is achieved and the spring displacement is measured.
Steps-Part bStep…
arrow_forward
The single degree of freedom (SDOF) system that you studied under free vibration in Assignment #3 - Laboratory Component has been subjected to a strong ground motion. The acceleration at the base (excitation) and the acceleration at the roof (response) of the SDOF system was recorded with sampling rate 50 Hz (50 samples per second, or dt= 0.02 seconds). The file ElCentro.txt includes the two columns of acceleration data. The first column lists the acceleration at the base of the SDOF system. The second column lists the acceleration at the roof of the SDOF system. (a) Plot the time histories of the recorded accelerations at the base and at the roof of the SDOF system. (b) Compute the acceleration, velocity and displacement time histories of the roof of the SDOF system subjected to the recorded base acceleration using the Central Difference method. Plot the accel- eration, velocity and displacement time histories. Plot the restoring force, the damping force, and the inertia force time…
arrow_forward
The single degree of freedom (SDOF) system that you studied under free vibration in Assignment #3 - Laboratory Component has been subjected to a strong ground motion. The acceleration at the base (excitation) and the acceleration at the roof (response) of the SDOF system was recorded with sampling rate 50 Hz (50 samples per second, or dt= 0.02 seconds). The file ElCentro.txt includes the two columns of acceleration data. The first column lists the acceleration at the base of the SDOF system. The second column lists the acceleration at the roof of the SDOF system. (a) Plot the time histories of the recorded accelerations at the base and at the roof of the SDOF system. (b) Compute the acceleration, velocity and displacement time histories of the roof of the SDOF system subjected to the recorded base acceleration using the Central Difference method. Plot the accel- eration, velocity and displacement time histories. Plot the restoring force, the damping force, and the inertia force time…
arrow_forward
I’m having trouble in my statics course. We are covering moments and I am confused about (1) what to use for the distance (2) when to use rFsin(theta), r(cross)F, or M=Fd. I keep using the wrong method and I really just need to know the way I approach the problem. For instance, on the problem below, I used rxF and the solutions said instead to simply use rFsin(theta)
arrow_forward
Draw the mechanism when the driver link 2 is at 90 degrees with respect to the mechanism ground
(aligned with the lower case y axis). Note, the mechanism ground is not the same thing as the Earth
ground in this mechanism. Draw the mechanism at a useful scale and determine the angles of link 3 and
link 4 with respect to the mechanism ground.
Repeat this analysis by using the computational approach to determine the angle for link 3 and 4.
Compare your results.
51.26
В
4
3
80
Y
47.5
76
14
12
02
arrow_forward
Figure 3 shows the numerical solution of the advection equation for a scalar u along x at three
consecutive timesteps.
1.0
0.8-
0.6
0.4-
0.2
0.0
00
-0.2
-0.4
-0.6-
3.0
3.5
4.0
4.5
5.0
5.5
6.0
6.5
Figure 3: Advection equation, solution for three different timesteps.
arrow_forward
Assume the Fourier number, Fo, is greater than or equal to 0.2 (note that you still need to calculate the Biot number, and possibly a second Biot number).
arrow_forward
I need help coding in MATLAB. Can you code an example of calibration problem of magnetometers? Assume the uncalibrated values.
arrow_forward
3. Microfluidic channels will need to be fabricated on a key micro-scale sensor used by aerospace
industries. Before running machining tests and analyzing machined quality, preliminary efforts are needed
to evaluate selected materials and factors affecting machining process¹. Three material candidates have
been selected, including 422SS (stainless steel), IN718 (nickel alloy), and Ti64 (titanium alloy) with their
measured tensile properties and equation of true stress-true strain relationship used listed below. Tref25°C.
Specifically, three factors will need to be evaluated, including different materials, temperature, and size
effect. Please calculate true stress values for true strain ranging between 0-3 for each case listed below.
Material
A (MPa)
& (S-¹)
Tm (°C)
870
0.01
1520
422SS (Peyre et al., 2007)
IN718 (Kobayashi et al., 2008)
Ti64 (Umbrello, 2008)
980
1
1300
782.7
1E-5
1660
Material
422SS (CINDAS, 2011)
IN718 (Davis, 1997)
Ti64 (Fukuhara and Sanpei, 1993)
0 =
X
G (GPa)
1+
B…
arrow_forward
SEE MORE QUESTIONS
Recommended textbooks for you
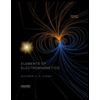
Elements Of Electromagnetics
Mechanical Engineering
ISBN:9780190698614
Author:Sadiku, Matthew N. O.
Publisher:Oxford University Press
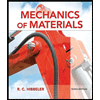
Mechanics of Materials (10th Edition)
Mechanical Engineering
ISBN:9780134319650
Author:Russell C. Hibbeler
Publisher:PEARSON
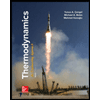
Thermodynamics: An Engineering Approach
Mechanical Engineering
ISBN:9781259822674
Author:Yunus A. Cengel Dr., Michael A. Boles
Publisher:McGraw-Hill Education
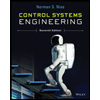
Control Systems Engineering
Mechanical Engineering
ISBN:9781118170519
Author:Norman S. Nise
Publisher:WILEY
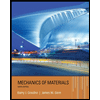
Mechanics of Materials (MindTap Course List)
Mechanical Engineering
ISBN:9781337093347
Author:Barry J. Goodno, James M. Gere
Publisher:Cengage Learning
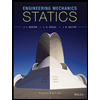
Engineering Mechanics: Statics
Mechanical Engineering
ISBN:9781118807330
Author:James L. Meriam, L. G. Kraige, J. N. Bolton
Publisher:WILEY
Related Questions
- A chamber of unknown volume is filled with an unknown amount of ideal gas. A cylinder with an open bottom and calibrated volume is connected to the chamber and is closed with a movable piston. A gas pressure sensor is also mounted on the chamber as shown in the figure. The whole experimental setup is kept at a constant temperature of 300 K. Doris moves the piston from mark 0 to mark 200 mL in steps of 50 mL and records the corresponding pressure in the chamber (see the table below). She moves the piston very slowly and waits several minutes before recording the pressure values. VCyl(mL) P(105N/m2)) 0 4.35 50 3.85 100 3.50 150 3.15 200 2.90 Determine the volume of the chamber using Doris's data in the table. (Note: This is a problem that requires linearization of data.) Determine the number of moles of gas. (Note: This is a problem that requires linearization of data.)arrow_forwardYou are watching a live concert. You can also find the concert streaming live on Spotify. About how far must you stand from the stage in order for the live concert and the live stream to be perfectly in sync? HINT: Assume the radio signal (Spotify) has to travel all the way around the Earth. circumference of the Earth (average): 40,041,000 m Speed of sound: 345 m/s Speed of light: 300,000,000 m/sarrow_forwardSensor systems for obstacle detection and avoidance in mobile robots. • Design and develop a suitable processor-based Data Acquisition (DAQ) system and external hardware to interface, measure, display and store the responses from the selected sensors.arrow_forward
- System Specification The aim of task 2 is to design a simulated obstacle detection sensor system for a mobile robot platform. You should assume your chosen sensors will be placed on a small mobile robot platform as designed in task 1. The sensor system must be able to detect objects within the range of 0mm to 1000mm and have a field of vision of 90 degrees (see diagram below). You may need to use multiple sensors to achieve the desired specification. Robot platform H 0-1000mm range 90° sensor view Example objectarrow_forwardSteps-Part aStep 1) In order to calculate the spring constant, the spring is positioned vertically, and a small mass is attached to its lower hook.Step 2) Visit the site:https://phet.colorado.edu/sims/html/masses-and-springs/latest/masses-and-springs_en.htmlStep 3) Select the Lab icon.Step 4) Make sure the damping is set to none. Using the ruler, measure the displacement of the spring and calculate the spring constant.Step 5) The mass is removed and securely attached to an inelastic cord. On other end of the cord is attached to the spring. Another segment of cord is attached to the other side of the spring. The opposite end of this cord is left free. This is the end in which the system will be rotated. The setup is shown in Fig. 1. The ball is rotated in a horizontal circle.Step 6) The radius of the system is measured before the spring is displaced.Step 7) The system is now spun around until uniform circular motion is achieved and the spring displacement is measured. Steps-Part bStep…arrow_forwardThe single degree of freedom (SDOF) system that you studied under free vibration in Assignment #3 - Laboratory Component has been subjected to a strong ground motion. The acceleration at the base (excitation) and the acceleration at the roof (response) of the SDOF system was recorded with sampling rate 50 Hz (50 samples per second, or dt= 0.02 seconds). The file ElCentro.txt includes the two columns of acceleration data. The first column lists the acceleration at the base of the SDOF system. The second column lists the acceleration at the roof of the SDOF system. (a) Plot the time histories of the recorded accelerations at the base and at the roof of the SDOF system. (b) Compute the acceleration, velocity and displacement time histories of the roof of the SDOF system subjected to the recorded base acceleration using the Central Difference method. Plot the accel- eration, velocity and displacement time histories. Plot the restoring force, the damping force, and the inertia force time…arrow_forward
- The single degree of freedom (SDOF) system that you studied under free vibration in Assignment #3 - Laboratory Component has been subjected to a strong ground motion. The acceleration at the base (excitation) and the acceleration at the roof (response) of the SDOF system was recorded with sampling rate 50 Hz (50 samples per second, or dt= 0.02 seconds). The file ElCentro.txt includes the two columns of acceleration data. The first column lists the acceleration at the base of the SDOF system. The second column lists the acceleration at the roof of the SDOF system. (a) Plot the time histories of the recorded accelerations at the base and at the roof of the SDOF system. (b) Compute the acceleration, velocity and displacement time histories of the roof of the SDOF system subjected to the recorded base acceleration using the Central Difference method. Plot the accel- eration, velocity and displacement time histories. Plot the restoring force, the damping force, and the inertia force time…arrow_forwardI’m having trouble in my statics course. We are covering moments and I am confused about (1) what to use for the distance (2) when to use rFsin(theta), r(cross)F, or M=Fd. I keep using the wrong method and I really just need to know the way I approach the problem. For instance, on the problem below, I used rxF and the solutions said instead to simply use rFsin(theta)arrow_forwardDraw the mechanism when the driver link 2 is at 90 degrees with respect to the mechanism ground (aligned with the lower case y axis). Note, the mechanism ground is not the same thing as the Earth ground in this mechanism. Draw the mechanism at a useful scale and determine the angles of link 3 and link 4 with respect to the mechanism ground. Repeat this analysis by using the computational approach to determine the angle for link 3 and 4. Compare your results. 51.26 В 4 3 80 Y 47.5 76 14 12 02arrow_forward
arrow_back_ios
SEE MORE QUESTIONS
arrow_forward_ios
Recommended textbooks for you
- Elements Of ElectromagneticsMechanical EngineeringISBN:9780190698614Author:Sadiku, Matthew N. O.Publisher:Oxford University PressMechanics of Materials (10th Edition)Mechanical EngineeringISBN:9780134319650Author:Russell C. HibbelerPublisher:PEARSONThermodynamics: An Engineering ApproachMechanical EngineeringISBN:9781259822674Author:Yunus A. Cengel Dr., Michael A. BolesPublisher:McGraw-Hill Education
- Control Systems EngineeringMechanical EngineeringISBN:9781118170519Author:Norman S. NisePublisher:WILEYMechanics of Materials (MindTap Course List)Mechanical EngineeringISBN:9781337093347Author:Barry J. Goodno, James M. GerePublisher:Cengage LearningEngineering Mechanics: StaticsMechanical EngineeringISBN:9781118807330Author:James L. Meriam, L. G. Kraige, J. N. BoltonPublisher:WILEY
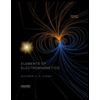
Elements Of Electromagnetics
Mechanical Engineering
ISBN:9780190698614
Author:Sadiku, Matthew N. O.
Publisher:Oxford University Press
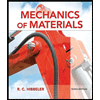
Mechanics of Materials (10th Edition)
Mechanical Engineering
ISBN:9780134319650
Author:Russell C. Hibbeler
Publisher:PEARSON
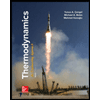
Thermodynamics: An Engineering Approach
Mechanical Engineering
ISBN:9781259822674
Author:Yunus A. Cengel Dr., Michael A. Boles
Publisher:McGraw-Hill Education
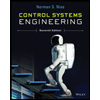
Control Systems Engineering
Mechanical Engineering
ISBN:9781118170519
Author:Norman S. Nise
Publisher:WILEY
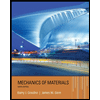
Mechanics of Materials (MindTap Course List)
Mechanical Engineering
ISBN:9781337093347
Author:Barry J. Goodno, James M. Gere
Publisher:Cengage Learning
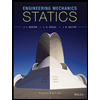
Engineering Mechanics: Statics
Mechanical Engineering
ISBN:9781118807330
Author:James L. Meriam, L. G. Kraige, J. N. Bolton
Publisher:WILEY