CPCCCM2012 Class activity book - Student (1)
docx
keyboard_arrow_up
School
Canberra Institute of Technology *
*We aren’t endorsed by this school
Course
MISC
Subject
Mechanical Engineering
Date
Apr 3, 2024
Type
docx
Pages
20
Uploaded by LieutenantThunder13361
Class Activities: Version 3.0
Effective Date: 01/07/2021
Review Date: 01/11/2023
All printed copies of this Document are considered 'Uncontrolled Copies'. Printed copies are only valid for the day printed
. Page 3
of 20
CPCCCM2012
Work safely at heights
CLASS ACTIVITIES - Student
CPCCCM2012 - Work safely at heights
Question 1: According to Safe Work Australia’s 2018, what are the areas that need special attention
while working at heights?
The areas that need special attention are:
close to an exposed edge that isn't covered, like the edges of leading formwork or unfinished
stairwells.
utilizing tools to perform tasks at an elevated height, such as portable ladders or elevating
work platforms (EWPs)
on any building or equipment that is being built, installed, dismantled, inspected, tested,
cleaned, or repaired.
on or near a delicate surface, such as skylights, rusted metal roofs, cement sheeting roofs, or
fiberglass sheeting roofs.
close to a hole, shaft, or pit that a worker could fall into, such as trenches;
on a sloping or slippery surface where it is difficult for people to maintain their balance; and
on an unstable surface, such as one where there is a chance of the ground collapsing.
Question 2: Explain the steps to determine job priorities and sequence job tasks in consultation with
a relevant person on site.
Compile job instructions:
The qualities required to finish a specific job or task are known as work specifications and
strategies. A guidebook that contains designs, specifications, standards for quality, operational information,
and accuracy checks on the work might be necessary. Prioritize tasks and arrange them in order of completion:
Worksite, environmental, and organizational safety strategies must be followed at all times.
Procedures ensure that the work is done safely, preventing damage to tools and placing people in
risky situations. They also aid in making sure that the tasks are finished in the proper sequence
and don't interfere with or obstruct other tasks being done on the site.
Class Activities: Version 3.0
Effective Date: 01/07/2021
Review Date: 01/11/2023
All printed copies of this Document are considered 'Uncontrolled Copies'. Printed copies are only valid for the day printed
. Page 3
of 20
Question 3: Write down the various factors to consider while preparing SWMS for a specific task.
The various factors to consider while preparing SWMS for a specific task are:
Address about high-risk construction activity like risks, hazards and control methods and
communicate with appropriate construction workers.
A column labelled "High-Risk Construction Work" should exist, providing an overview of
the high-risk construction projects that need to be performed.
A column of hazards and risks.
Conditions like work environment that influence how the construction work with high-risk
will be done, for example: construction plan, working environment, safe work methods
and pant to be used
A column of “control measures” with hierarchy of controls.
Question 4: Explain various control measures to avoid any risk at workplace.
The control measures to avoid any risk at workplace are:
Use PPE kits – this preventive measure is of the bottom order and applied when other
measures are not effective. It does not lower the hazard.
Use signs – there are different signs available according to need. These are prohibition signs,
mandatory, restriction, hazard, emergency, fire signs
Use fall restraint device - it protects the person from fall. Guard rail and barriers are installed
for more protection.
Use a fall arrest system – it protects the worker by avoiding the fall before striking the ground
after he fell.
Use administrative controls – this is effective when other measures are unsuccessful. It
comprises numerous design methods and actions to minimise hazards.
Class Activities: Version 3.0
Effective Date: 01/07/2021
Review Date: 01/11/2023
All printed copies of this Document are considered 'Uncontrolled Copies'. Printed copies are only valid for the day printed
. Page 3
of 20
Your preview ends here
Eager to read complete document? Join bartleby learn and gain access to the full version
- Access to all documents
- Unlimited textbook solutions
- 24/7 expert homework help
Question 5: Mention below the various locations of anchor points for safe access to the work area. The various locations of anchor points for safe access to the work area are:
1.
Roof – they are mostly permanent type and pinned into the roof surface. A simple anchor
connection contains a D-ring connection whereas complex system comprises a complete
lifeline system.
2.
Door and windows - To install anchor points, a jamb anchor is used to secure the window and
door frames. It is always wider than door or window frame
3.
Walls – permanent anchor points can be nailed into the walls. After drilling a hole in the wall
and then anchor points is fixed
4.
Crane or vehicle – anchor points can be connected on a crane or vehicle which can bear high
load and stable Question 6: What are various types of protection required and their descriptions
Protection location
Description
Hand Gloves Respiratory Filtering respirators and masks
Skin Sunscreen cream
Foot Steel toe boots
Class Activities: Version 3.0
Effective Date: 01/07/2021
Review Date: 01/11/2023
All printed copies of this Document are considered 'Uncontrolled Copies'. Printed copies are only valid for the day printed
. Page 3
of 20
Eyes
Safety glasses
Noise Ear muffs
Head Hard hats
Question 7: How can you prevent the risk of fall from height?
The risk of fall from height can be prevented by using following measures:
Using fall prevention devices – the fall prevention devices such as guard rails and scaffolding
can be used to reduce the risk of fall due to unbalanced and fragile surfaces.
Using different types of work positioning systems – work positioning system such as a rope
access system can also be used. Question 8: What is meant by Elevated work platforms (EWPs)? List its types, characteristics, uses
and limitations.
Elevated work platform is a mobile machine (device) featuring at least a work platform with
controls, an extending frame, and a chassis is meant to transfer people, tools, and materials to
working locations.
Types- Self-propelled elevating work platforms, Boom-type elevating work platform and elevating
Rolling work platforms
Characteristics – packed position, monitor from the work platform Uses – during working at height used for lifting or lowering weights.
Limitations – chances of toppling
Class Activities: Version 3.0
Effective Date: 01/07/2021
Review Date: 01/11/2023
All printed copies of this Document are considered 'Uncontrolled Copies'. Printed copies are only valid for the day printed
. Page 3
of 20
Question 9: What are the safety manuals and instructions for checking plant, tools and equipment?
The safety manuals and instructions for checking plant, tools and equipment are:
Operation manuals – the detailed document that helps workers operating well by providing
information of equipment and its parts. Each tool or equipment has a ‘Operation manual’
which explains their working. These are essential guidelines which guarantees the safe usage
of the tools or equipment.
Manufacturer specifications - this provides technical data of tools and equipment which guard
the workers form the hazards related to a tool or equipment.
Safety signs and load charts for plants: these are available in several layouts in order to
protect workers from possible hazard resulting from defective tools, equipment and plants.
Load chart is an illustration and diagram that shows how much authorised work a tool, plant,
or equipment would be able to carry out.
Question 10: What is meant by signs? List the correct titles for these signs.
Signs are essential components of any construction site since they are vital instruments for
guaranteeing security and safety. These are extremely important for directing workers,
communicating important information, and warning guests of potential dangers. They can be in
pictures, written or both. The various forms of signs are:
Prohibition signs (don’t do)
Restriction signs (limiting)
Hazard signs (warning signs)
Mandatory signs (must do)
Fire signs
Emergency signs (medical, exit etc.)
Class Activities: Version 3.0
Effective Date: 01/07/2021
Review Date: 01/11/2023
All printed copies of this Document are considered 'Uncontrolled Copies'. Printed copies are only valid for the day printed
. Page 3
of 20
Your preview ends here
Eager to read complete document? Join bartleby learn and gain access to the full version
- Access to all documents
- Unlimited textbook solutions
- 24/7 expert homework help
Question 11: How you can install fall protection equipment such as scaffolding and guard rails?
Scaffold need to be installed on secured foundation
Measure the space between the screw jacks and begin positioning the scaffold frame above
the screw jack. Use pins to secure the bracing to the frame's two ends. Additionally, use a
spirit level to ensure the frame's level.
Lay planks across the scaffold's whole width. As it helps to provide guidance for subsequent
planks, set the first board on the frame first, levelling and square it. There should be no more
than a 10mm space between boards.
At the working platform, guard rails are installed to keep workers and machinery from falling
out. Furthermore, ladders are the scaffold-like structure that serves as a stairway to access
the working platform. A gate panel must be installed along the ladder, and the ladder's
maximum slope should be 1:6.
After carefully inspecting the scaffold, the final bay should be assembled and the building
process is then completed.
Question 12: Explain some issues or events that can influence the uprightness and safety of
scaffolding.
The issues and events that can influence the uprightness and safety of scaffolding are:
Knocked – this happens when scaffold is erected near vehicle passages or shipment docks
where it gets consistently knock and thumped.
Class Activities: Version 3.0
Effective Date: 01/07/2021
Review Date: 01/11/2023
All printed copies of this Document are considered 'Uncontrolled Copies'. Printed copies are only valid for the day printed
. Page 3
of 20
Tough components – with heavy equipment, materials and vehicles scaffold is damaged.
Wear – scaffold corrode and wear away over time. There should be regular inspection for
corrosion and wear.
Worked loose – scaffold may lose its stability over time, so regular inspection of connections.
Out of level – regular checking of ground conditions and footing. Heavy rainfall may lead the
scaffolding out of level.
Removed/changed by users – when some trade persons removed some components to make
their job easy. Question 13: What are the points that you should implement while installation of fall protection
equipment is carried out?
The points that should be implemented while fall protection system is installed are:
Different types of harnesses have advantages and disadvantages. The material of the harness
should be selected according to the different climatic conditions.
Every worker should be given proper training for safe installation and inspection of fall
restraint equipment.
Harness and lanyard should be inspected for wear and tear before use
All the buckles and straps should be straight and present in the right place. Make sure legs
and arms are lined up correctly. Slip the straps over shoulders to centre the connecting D ring
between the shoulder blades. Furthermore, Buckle the leg straps and chest straps; after that,
pull them to tighten. All straps should be tight as if these straps are too loose, then the
harness will slide up one’s body while working at height.
Harness should be snug fit; straps should not be too loose pr tight as it can become
uncomfortable and deter movement.
Consider the worker's height and the distance between anchor points when choosing the
lanyard in the first place. Next, fasten the lanyard carabiner to the harness using the D ring;
the connector needs to be locked and tightened. Additionally, make sure the hook is locked
and securely fastened before attaching the lanyard to the anchorage point.
Question 14: List the points to be considered by a relevant person while checking adjustments,
fittings and installation of fall protection equipment.
The points to be considered while checking adjustments, fittings and installation of fall protection
Class Activities: Version 3.0
Effective Date: 01/07/2021
Review Date: 01/11/2023
All printed copies of this Document are considered 'Uncontrolled Copies'. Printed copies are only valid for the day printed
. Page 3
of 20
equipment are:
All hooks, D-rings and metal parts should be well fitted.
Every part of fall protection equipment needs to be stable and fault free.
Examine the lanyard as a whole to make sure it didn't break while twisting.
Verify that there are no tears, broken stitches, cuts, or other signs of impact load on the
breakaway jacket.
Check that any modifications do not reduce the equipment's efficiency.
Look for broken hooks and ensure that tongues are securely fastened to shoulder buckles.
Before performing the inspection, read the manufacturer's instructions.
To reduce the chance of falling, check the free fall distance.
Verify the anchor point locations; the worker cannot be permitted to work above the anchor
points, which would increase the overall fall distance.
Question 15: What are various equipment that are generally used to access work area safely?
Ladder – it is used in work site for getting to raised work areas.
Scaffold stairs – it is used to move tools, equipment and material and guard rails are attached
to the side of the scaffold to provide safe access.
Hoist – they are used with scaffolding in construction of high-rise building for safe access and
also used in an emergency. The loading capacity should be checked and licensed person
should install it.
Crawl board - These are the kinds of boards that are temporarily lowered to a higher work
area in order to catch employees, supplies, and equipment in the event that they fall.
Ramp – made either of wood or metal and provides access to workers to elevated work areas.
Question 16: What do you understand by safety data sheet?
Safety Data Sheets (SDSs) are concise manuals that list a product's hazards and offer guidance on
Class Activities: Version 3.0
Effective Date: 01/07/2021
Review Date: 01/11/2023
All printed copies of this Document are considered 'Uncontrolled Copies'. Printed copies are only valid for the day printed
. Page 3
of 20
Your preview ends here
Eager to read complete document? Join bartleby learn and gain access to the full version
- Access to all documents
- Unlimited textbook solutions
- 24/7 expert homework help
safety measures. SDSs are typically created by the product's manufacturer or supplier, and they
have to be given by those who supply hazardous goods at the point of sale. Compared to the
label, SDSs offer more thorough information about the product's hazards. They are a valuable
source of information about the product(s) used that workplaces and employees can use.
Question 17: List the PPE’s is required to work safely at heights.
The PPE required to work safely at heights are:
Hard hat
Safety glasses
Steel toe shoes
Gloves
Harness or lanyards
Class Activities: Version 3.0
Effective Date: 01/07/2021
Review Date: 01/11/2023
All printed copies of this Document are considered 'Uncontrolled Copies'. Printed copies are only valid for the day printed
. Page 3
of 20
Question 18: Explain the points you must considered to maintain communication with the relevant
person.
The points to considered to maintain communication with the relevant person are:
Create an official communication channel to ensure that information reaches the proper time
to the appropriate person.
Make sure all messages are simple and clear, and choose the appropriate platform for the
message.
To ensure that everyone is reachable, use communication channels that are optimized for
mobile devices.
Make sure there is two-way communication to ensure that all information reaches the
appropriate person at the location immediately and that the connection is maintained.
Make use of communication channels to keep lines of communication open and
uninterrupted.
Question 19: Mention below the points that you should considered during placement of scaffold and
barriers.
A permanent scaffold should be erected at the site to perform any work that requires access
to areas higher than 10 meters.
Ascertain that every part of the scaffolds is firmly attached and secured.
To prevent falling out, use a ladder with a scaffold attached to it.
Guard rails and other barriers should be erected around the scaffolding to shield the workers
from the edges.
Check that the guard rail and toe board are installed at each elevated, open side platform.
Every floor hole that a worker might unintentionally walk into needs to have a barrier
installed.
To eliminate the possibility of a fall while working at a height, every component needs to stay
stable.
Class Activities: Version 3.0
Effective Date: 01/07/2021
Review Date: 01/11/2023
All printed copies of this Document are considered 'Uncontrolled Copies'. Printed copies are only valid for the day printed
. Page 3
of 20
Question 20: What are various consultation methods for changing site conditions?
The consultation methods for changing site conditions are:
Meetings
Public forums
Community house meetings
Workshops
Exchange of letters and informative material
Question 21: Explain the guidelines that should be followed during removal of tools and equipment.
The guidelines that should be followed during removal of tools and equipment are:
Collect all the tools in a bucket or a bag while carrying up and down a ladder.
When handing tools from one worker to other care should be taken.
Stack all the tools in a manner and do not mix.
Storage room should be water-resistant because some tools absorb moisture from the surface
and stop working.
Tools should be placed on a proper platform and in sequence.
Make a list of tools and inspect them properly and regularly to detect any faults.
Storekeeper should maintain a proper report of tools an submit to the supervisor.
Class Activities: Version 3.0
Effective Date: 01/07/2021
Review Date: 01/11/2023
All printed copies of this Document are considered 'Uncontrolled Copies'. Printed copies are only valid for the day printed
. Page 3
of 20
Your preview ends here
Eager to read complete document? Join bartleby learn and gain access to the full version
- Access to all documents
- Unlimited textbook solutions
- 24/7 expert homework help
Question 22: What is meant by Good housekeeping?
The goal of good housekeeping in the workplace is to establish a tidy, safe, and orderly
workspace. It includes everything from making sure hazardous chemicals are properly labeled and
stored to keeping floors clear of debris. It also entails keeping your workspace neat, practicing
good ergonomics, and keeping yourself clean.
Question 23: Write a short note on Environmental management plan.
Environmental management plans primarily outline actions that have an impact on the
surrounding natural environment and clearly outline an individual's commitment to researching
ways to minimize, reduce, and manage environmental impact. The actions to dispose of recycled
material at the construction site will be guided by the environmental management plan (EMP).
Everyone who works on the site has an obligation to enhance workplace environmental practices
and policies.
Class Activities: Version 3.0
Effective Date: 01/07/2021
Review Date: 01/11/2023
All printed copies of this Document are considered 'Uncontrolled Copies'. Printed copies are only valid for the day printed
. Page 3
of 20
Class Activities: Version 3.0
Effective Date: 01/07/2021
Review Date: 01/11/2023
All printed copies of this Document are considered 'Uncontrolled Copies'. Printed copies are only valid for the day printed
. Page 3
of 20
Class Activities: Activity 1: In this activity, you are required to discuss the process to work safely at heights with your classmates
and you can take help of your teacher or any support person.
Firstly, you are supposed to identify the task requirements, consider the following points:
Steps to determine job priorities and sequence job tasks in consultation with a relevant
person on site.
Points to considered while preparing SWMS for a specific task.
Things to follow at the civil construction worksite according to WHS laws.
Ways to review completed SWMS and clarify issues with relevant persons.
It's crucial to adhere to a systematical procedure that involves multiple crucial steps if you want to
work at heights safely. These actions include determining the needs for the task, creating a Safe
Work Method Statement (SWMS), adhering to WHS regulations on the job site, and discussing and
elaborating on matters with pertinent parties.
Identifying task requirements: It's important to have a clear understanding of the requirements
before beginning any work at heights. This entails figuring out the extent of the task, recognizing
the risks and dangers connected to working at heights, and making sure the required tools and
resources are on hand. The order of tasks and job priorities can be decided upon in consultation
with an appropriate person on site. Creating a Statement of Safe Work Practices (SWMS) A SWMS is a document that provides a step-
by-step guide on how to carry out a particular task safely. There are various things to take into
account when creating a SWMS for working at heights. Among them are:
defining the risks and hazards related to working at heights and providing control measures to
lessen those risks. This could entail employing fall protection gear, making sure that work
platforms are stable, and giving employees training.
establishing the job's task sequence and making sure each task is carried out safely and logically.
Describing the tools and materials needed to complete the task.
Laws and regulations relating to Work Health and Safety (WHS) set forth requirements and
guidelines for working at heights. To maintain a safe workplace, adherence to these laws is crucial.
Under WHS regulations, the following are important guidelines to adhere to at a civil construction
worksite:
Identifying risks and putting control measures in place by doing a risk assessment.
Ensuring that employees receive the proper instruction and oversight to guarantee they possess
the abilities needed to work safely at heights.
Utilizing and keeping up with the required safety gear, such as guardrails, anchor points, and
harnesses.
Equipment should be routinely inspected and maintained to make sure it is in good operating
order.
putting in place processes for reporting dangers, incidents, and near misses.
After the SWMS is finished, it's critical to review it and discuss any questions with the appropriate
parties. This could entail going over the document with the employees who will be performing the
task, getting their input, and modifying or adding to the SWMS as needed.
Class Activities: Version 3.0
Effective Date: 01/07/2021
Review Date: 01/11/2023
All printed copies of this Document are considered 'Uncontrolled Copies'. Printed copies are only valid for the day printed
. Page 3
of 20
Your preview ends here
Eager to read complete document? Join bartleby learn and gain access to the full version
- Access to all documents
- Unlimited textbook solutions
- 24/7 expert homework help
Activity 2: This activity is in continuation with the previous activity.
Secondly, you are required to discuss the process to access and assess the work area, considering
the following points:
Steps to install fall protection equipment such as scaffolding and guard rails.
Some issues or events can influence the uprightness and safety of scaffolding.
Points to implement while installation of fall protection equipment is carried out.
Points to consider by a relevant person while checking adjustments, fittings and installation
of fall protection equipment.
Equipment’s that are generally used to access work area safely.
Installing guard rails and scaffolding, among other fall protection equipment:
First, determine the best places to erect guard rails and scaffolding by inspecting them. Make sure
the equipment's weight can be supported by the stable ground. To ensure proper equipment
assembly and installation, adhere to the manufacturer's instructions. Look out for potential
dangers surrounding the work area, such as hanging power lines or unstable buildings, and take
the necessary safety measures.
Problems or occurrences that may affect the scaffolding's safety and uprightness:
Unfavorable weather conditions, such as intense rain or strong winds, can compromise the
stability of scaffolding. In order to reduce these risks, it's critical to routinely inspect and secure the
equipment.
To identify any problems, the work area must be regularly monitored.
The following guidelines should be followed when installing fall protection equipment:
Make certain that every employee participating in the installation has received the necessary
instruction and is conversant with the assembly guidelines.
Make use of the appropriate PPE, such as safety shoes, harnesses, and helmets.
To ensure that the equipment is in good operating order, perform routine maintenance and
inspections.
Utilize only gear that has been approved, certified, and complies with safety regulations.
A responsible party should take the following into account when inspecting the installation,
fittings, and adjustments of fall protection equipment:
Verify that every piece of equipment is securely fastened and connected.
Make sure there is no excessive movement or wobbling of the scaffolding and that it is level and
stable.
Verify that the mid-rails, guardrails, and toe boards are properly installed and at the appropriate
height.
Usually, operated tools for securely entering the work area:
Stepladders: Make sure the ladder is in good condition and choose the right one for the task.
When using it, make sure the surface is level and stable, and when climbing, always have three
points of contact.
Mobile elevated work platforms, or MEWPs, are devices that allow people to safely access heights.
To operate MEWPs, operators need to be qualified and skilled.
Cherry pickers, also known as scaffold towers, offer secure working platforms at different heights.
As recommended by the manufacturer and by industry best practices, they should be set up and
used appropriately.
Fall arrest systems: These work in tandem with anchor points to prevent falls. They comprise
Class Activities: Version 3.0
Effective Date: 01/07/2021
Review Date: 01/11/2023
All printed copies of this Document are considered 'Uncontrolled Copies'. Printed copies are only valid for the day printed
. Page 3
of 20
persol fall arrest systems, safety harnesses, and lifelines.
Class Activities: Version 3.0
Effective Date: 01/07/2021
Review Date: 01/11/2023
All printed copies of this Document are considered 'Uncontrolled Copies'. Printed copies are only valid for the day printed
. Page 3
of 20
Class Activities: Version 3.0
Effective Date: 01/07/2021
Review Date: 01/11/2023
All printed copies of this Document are considered 'Uncontrolled Copies'. Printed copies are only valid for the day printed
. Page 3
of 20
Your preview ends here
Eager to read complete document? Join bartleby learn and gain access to the full version
- Access to all documents
- Unlimited textbook solutions
- 24/7 expert homework help
Activity 3: In this activity, discuss the steps to conduct work tasks, consider the points given below:
Obligations under the compliance documents.
Ways to traverse between anchor points while remaining connected to the fall prevention
system and protected from a risk of a fall from height.
Ways to keep fall prevention equipment adjusted to prevent falling off or through a
structure using the restraint technique.
Steps to considered during placement of scaffold and barriers.
Requirements under compliance documents: Read through any relevant compliance documents,
including policies, procedures, and safety manuals.
Recognize and fulfill the responsibilities delineated in these documents, making sure adhering to
the necessary safety protocols and laws.
Moving back and forth between anchor points while staying connected:
Determine and set up anchor points, such as lanyards and harnesses, where you can safely attach
fall prevention equipment.
To move between these anchor points while maintaining connection to the fall prevention
system, use the designated walkways, platforms, or access points.
Steer clear of any dangerous paths or shortcuts that could endanger safety.
Readjusting fall protection devices by applying the restraint method:
Make sure lifelines, lanyards, and harnesses are in good working order by giving them a regular
inspection.
Make sure the equipment fits snugly but comfortably by correctly adjusting it to body type and
size.
Employ the restraint technique, which is fastening yourself securely to avoid any future falls or
slips and maintaining the tightness of the fall prevention gear.
Actions to think about when erecting barriers and a scaffold:
As directed by employer or the relevant regulatory bodies, abide by the scaffold and barrier
policies.
Give careful thought to where to place the scaffolding in order to create a safe working area.
Make sure that all scaffold parts are assembled according to the correct procedures and are
securely fastened.
Class Activities: Version 3.0
Effective Date: 01/07/2021
Review Date: 01/11/2023
All printed copies of this Document are considered 'Uncontrolled Copies'. Printed copies are only valid for the day printed
. Page 3
of 20
Activities 1-3
Answer may vary but student must address the questions according to the following resources:
Learner Guide
PowerPoint presentation
Self-study Guide
Live Training sessions and discussions with trainers/assessors Class Activities: Version 3.0
Effective Date: 01/07/2021
Review Date: 01/11/2023
All printed copies of this Document are considered 'Uncontrolled Copies'. Printed copies are only valid for the day printed
. Page 3
of 20
Related Documents
Related Questions
Case Study – The New Engineer
Jeff was just hired by GSI, Inc. to be their Environmental and Safety Coordinator. This is Jeff's first position after completing his engineering degree. He had taken a course in safety engineering as part of his studies and felt confident that he could handle the job.
Management at GSI, Inc. has assured him that they are committed to maintaining a safe workplace. They have never had an individual dedicated to this task full-time. They will implement his recommendations if he can justify them.
As Jeff begins to get familiar with the operations, he spends considerable time on the production floor. He notices workers clean their tools before break with a liquid from an unmarked 55-gallon drum. They also use this liquid to clean residue from their skin. They use paper towels to dry their tools and hands, throw these towels in the trash, and head to the break room for a snack and/or smoke.
In talking with the workers, Jeff learns of some of…
arrow_forward
Case Study – The New Engineer
Jeff was just hired by GSI, Inc. to be their Environmental and Safety Coordinator. This is Jeff's first position after completing his engineering degree. He had taken a course in safety engineering as part of his studies and felt confident that he could handle the job.
Management at GSI, Inc. has assured him that they are committed to maintaining a safe workplace. They have never had an individual dedicated to this task full-time. They will implement his recommendations if he can justify them.
As Jeff begins to get familiar with the operations, he spends considerable time on the production floor. He notices workers clean their tools before break with a liquid from an unmarked 55-gallon drum. They also use this liquid to clean residue from their skin. They use paper towels to dry their tools and hands, throw these towels in the trash, and head to the break room for a snack and/or smoke.
In talking with the workers, Jeff learns of some of…
arrow_forward
I need parts 1, 2, and 3 answered pertaining to the print provided.
NOTE: If you refuse to answers all 3 parts and insist on wasting my question, then just leave it for someone else to answer. I've never had an issue until recently one single tutor just refuses to even read the instructions of the question and just denies it for a false reasons or drags on 1 part into multiple parts for no reason.
arrow_forward
Help!!! Please answer part b correctly like part A. Please!!!!
arrow_forward
Help!!! Please answer all Correctly!!! Please
arrow_forward
please read everything properly... Take 3 4 5 hrs but solve full accurate drawing on bond paper don't use chat gpt etc okk
arrow_forward
LESSON: AUTODESK AUTOCAD
Choose from the choices:
arrow_forward
Please Use excel Shee t
Note:-
• Do not provide handwritten solution. Maintain accuracy and quality in your answer. Take care of plagiarism.
• Answer completely.
• You will get up vote for sure.
arrow_forward
University of Babylon
Collage of Engineering\Al-Musayab
Department of Automobile
Engineering
Under Grad/Third stage
Notes:
1-Attempt Four Questions.
2- Q4 Must be Answered
3-Assume any missing data.
4 تسلم الأسئلة بعد الامتحان مع الدفتر
Subject: Mechanical
Element Design I
Date: 2022\01\25
2022-2023
Time: Three Hours
Course 1
Attempt 1
Q1/ Design a thin cylindrical pressure tank (pressure vessel) with hemispherical ends to the
automotive industry, shown in figure I below. Design for an infinite life by finding the
appropriate thickness of the vessel to carry a sinusoidal pressure varied from {(-0.1) to (6) Mpa}.
The vessel is made from Stainless Steel Alloy-Type 316 sheet annealed. The operating
temperature is 80 C° and the dimeter of the cylinder is 36 cm. use a safety factor of 1.8.
Fig. 1
(15 Marks)
Q2/ Answer the following:
1- Derive the design equation for the direct evaluation of the diameter of a shaft to a desired
fatigue safety factor, if the shaft subjected to both fluctuated…
arrow_forward
Please give me the answers for this i been looking at this for a hour and my head hurts
arrow_forward
Please do not copy other's work and do not use ChatGPT or Gpt4,i will be very very very appreciate!!!
Thanks a lot!!!!!
arrow_forward
Access Pearson
Mastering Engineering
Back to my courses
Course Home
Course Home
Scores
■Review
Next >
arrow_forward
I need answers for problems 13, 14, and 15 pertaining to the print provided.
NOTE: If you refuse to answers all 3 parts and insist on wasting my question by breaking down 1 simple question into 3 parts, then just leave it for someone else to answer. Thank you.
arrow_forward
I need parts 8, 9, and 10 answered. Number 1 is an example of how it should be answered.
NOTE: Read the instructions, no where does it say any drawing is required. It is really frustrating when I wait all this time for an answer to a question and some tutor does even read the instructions and just declines it...its ridicilous.
arrow_forward
Please give a complete solution in Handwritten format.
Strictly don't use chatgpt,I need correct answer.
Engineering dynamics
arrow_forward
Case Study: Paula’s Pain
Paula has worked for Brindle Corporation for 3 years. During this time, she has worked as a machine operator/cell leader in various work cells. Recently, the plant went to mandatory 12-hour shifts and plans to remain on this schedule for several months.
Paula’s present work cell is manufacturing 3-inch diameter exhaust tubes that are made from stainless steel. These tubes get a hole punched in them, a flange welded on, and burrs ground off. The pipe then gets placed into a gage to check that it was made correctly. (The tubes weigh about six pounds.)
Paula has been performing the welding operation. She leans into the machine and loads the part into a fixture then positions the flange. Both pieces are clamped (using hand clamps) into position and the machine is cycled by depressing two palm buttons.
The gaging operation requires placing the finished part into the gage and clamping it (using hand clamps) into place. A pin is depressed to verify the position…
arrow_forward
Please answer LETTER C
arrow_forward
Please assist with answering the following question?
arrow_forward
Mech. Engg. Dept.
4th year 2022-2023
Solar Energy
Spring course MEC364
Dr. Mahmoud U. Jasim
Review/Recap Sheet
Q1- Answer with true or false and rewrite the false statements completely in
correct form, otherwise no mark will be put on the false statements.
1
2
To represent a location on earth surface you need to define its altitude and longitude
angles.
3
Solar zenith and solar incidence angles have the same value for horizontal surface.
At sunset time the value of solar altitude angle is maximum.
4
The angle which represents the inclination of a given surface is the zenith angle
5
6
7
8
When the absolute value of sun-wall azimuth angle exceeds 90' this means that the sun
rays are reaching the receiving plane.
The solar irradiance and the solar irradiation have the same physical meaning.
In the case of clear sky weather, the beam solar irradiation on a horizontal surface is less
than the diffused irradiation.
The total solar radiation received by a tilted surface is the same as that…
arrow_forward
SEE MORE QUESTIONS
Recommended textbooks for you
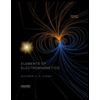
Elements Of Electromagnetics
Mechanical Engineering
ISBN:9780190698614
Author:Sadiku, Matthew N. O.
Publisher:Oxford University Press
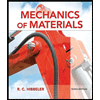
Mechanics of Materials (10th Edition)
Mechanical Engineering
ISBN:9780134319650
Author:Russell C. Hibbeler
Publisher:PEARSON
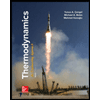
Thermodynamics: An Engineering Approach
Mechanical Engineering
ISBN:9781259822674
Author:Yunus A. Cengel Dr., Michael A. Boles
Publisher:McGraw-Hill Education
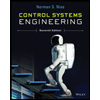
Control Systems Engineering
Mechanical Engineering
ISBN:9781118170519
Author:Norman S. Nise
Publisher:WILEY
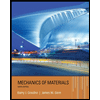
Mechanics of Materials (MindTap Course List)
Mechanical Engineering
ISBN:9781337093347
Author:Barry J. Goodno, James M. Gere
Publisher:Cengage Learning
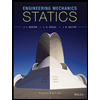
Engineering Mechanics: Statics
Mechanical Engineering
ISBN:9781118807330
Author:James L. Meriam, L. G. Kraige, J. N. Bolton
Publisher:WILEY
Related Questions
- Case Study – The New Engineer Jeff was just hired by GSI, Inc. to be their Environmental and Safety Coordinator. This is Jeff's first position after completing his engineering degree. He had taken a course in safety engineering as part of his studies and felt confident that he could handle the job. Management at GSI, Inc. has assured him that they are committed to maintaining a safe workplace. They have never had an individual dedicated to this task full-time. They will implement his recommendations if he can justify them. As Jeff begins to get familiar with the operations, he spends considerable time on the production floor. He notices workers clean their tools before break with a liquid from an unmarked 55-gallon drum. They also use this liquid to clean residue from their skin. They use paper towels to dry their tools and hands, throw these towels in the trash, and head to the break room for a snack and/or smoke. In talking with the workers, Jeff learns of some of…arrow_forwardCase Study – The New Engineer Jeff was just hired by GSI, Inc. to be their Environmental and Safety Coordinator. This is Jeff's first position after completing his engineering degree. He had taken a course in safety engineering as part of his studies and felt confident that he could handle the job. Management at GSI, Inc. has assured him that they are committed to maintaining a safe workplace. They have never had an individual dedicated to this task full-time. They will implement his recommendations if he can justify them. As Jeff begins to get familiar with the operations, he spends considerable time on the production floor. He notices workers clean their tools before break with a liquid from an unmarked 55-gallon drum. They also use this liquid to clean residue from their skin. They use paper towels to dry their tools and hands, throw these towels in the trash, and head to the break room for a snack and/or smoke. In talking with the workers, Jeff learns of some of…arrow_forwardI need parts 1, 2, and 3 answered pertaining to the print provided. NOTE: If you refuse to answers all 3 parts and insist on wasting my question, then just leave it for someone else to answer. I've never had an issue until recently one single tutor just refuses to even read the instructions of the question and just denies it for a false reasons or drags on 1 part into multiple parts for no reason.arrow_forward
- LESSON: AUTODESK AUTOCAD Choose from the choices:arrow_forwardPlease Use excel Shee t Note:- • Do not provide handwritten solution. Maintain accuracy and quality in your answer. Take care of plagiarism. • Answer completely. • You will get up vote for sure.arrow_forwardUniversity of Babylon Collage of Engineering\Al-Musayab Department of Automobile Engineering Under Grad/Third stage Notes: 1-Attempt Four Questions. 2- Q4 Must be Answered 3-Assume any missing data. 4 تسلم الأسئلة بعد الامتحان مع الدفتر Subject: Mechanical Element Design I Date: 2022\01\25 2022-2023 Time: Three Hours Course 1 Attempt 1 Q1/ Design a thin cylindrical pressure tank (pressure vessel) with hemispherical ends to the automotive industry, shown in figure I below. Design for an infinite life by finding the appropriate thickness of the vessel to carry a sinusoidal pressure varied from {(-0.1) to (6) Mpa}. The vessel is made from Stainless Steel Alloy-Type 316 sheet annealed. The operating temperature is 80 C° and the dimeter of the cylinder is 36 cm. use a safety factor of 1.8. Fig. 1 (15 Marks) Q2/ Answer the following: 1- Derive the design equation for the direct evaluation of the diameter of a shaft to a desired fatigue safety factor, if the shaft subjected to both fluctuated…arrow_forward
- Please give me the answers for this i been looking at this for a hour and my head hurtsarrow_forwardPlease do not copy other's work and do not use ChatGPT or Gpt4,i will be very very very appreciate!!! Thanks a lot!!!!!arrow_forwardAccess Pearson Mastering Engineering Back to my courses Course Home Course Home Scores ■Review Next >arrow_forward
arrow_back_ios
SEE MORE QUESTIONS
arrow_forward_ios
Recommended textbooks for you
- Elements Of ElectromagneticsMechanical EngineeringISBN:9780190698614Author:Sadiku, Matthew N. O.Publisher:Oxford University PressMechanics of Materials (10th Edition)Mechanical EngineeringISBN:9780134319650Author:Russell C. HibbelerPublisher:PEARSONThermodynamics: An Engineering ApproachMechanical EngineeringISBN:9781259822674Author:Yunus A. Cengel Dr., Michael A. BolesPublisher:McGraw-Hill Education
- Control Systems EngineeringMechanical EngineeringISBN:9781118170519Author:Norman S. NisePublisher:WILEYMechanics of Materials (MindTap Course List)Mechanical EngineeringISBN:9781337093347Author:Barry J. Goodno, James M. GerePublisher:Cengage LearningEngineering Mechanics: StaticsMechanical EngineeringISBN:9781118807330Author:James L. Meriam, L. G. Kraige, J. N. BoltonPublisher:WILEY
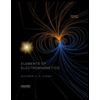
Elements Of Electromagnetics
Mechanical Engineering
ISBN:9780190698614
Author:Sadiku, Matthew N. O.
Publisher:Oxford University Press
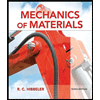
Mechanics of Materials (10th Edition)
Mechanical Engineering
ISBN:9780134319650
Author:Russell C. Hibbeler
Publisher:PEARSON
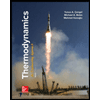
Thermodynamics: An Engineering Approach
Mechanical Engineering
ISBN:9781259822674
Author:Yunus A. Cengel Dr., Michael A. Boles
Publisher:McGraw-Hill Education
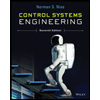
Control Systems Engineering
Mechanical Engineering
ISBN:9781118170519
Author:Norman S. Nise
Publisher:WILEY
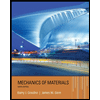
Mechanics of Materials (MindTap Course List)
Mechanical Engineering
ISBN:9781337093347
Author:Barry J. Goodno, James M. Gere
Publisher:Cengage Learning
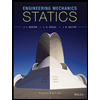
Engineering Mechanics: Statics
Mechanical Engineering
ISBN:9781118807330
Author:James L. Meriam, L. G. Kraige, J. N. Bolton
Publisher:WILEY