Experiment D - Fluid Dynamics Write-up 2022
pdf
keyboard_arrow_up
School
University of British Columbia *
*We aren’t endorsed by this school
Course
264
Subject
Mechanical Engineering
Date
Apr 3, 2024
Type
Pages
46
Uploaded by CorporalQuetzalPerson999
CHBE 264 Manual Experiment D: Fluids Revised on 11 February 2022 Back to Table of Contents -1-
Table of Contents Table of Contents ..........................................................................................................
1
Scenario
.........................................................................................................................
2
Relevant Course Content in the 2
nd
Year CHBE Curriculum .......................................
2
General Instructions ......................................................................................................
3
Part 1: Flow through Pipes
........................................................................................
4
1.1 Learning Objectives ....................................................................................
4
1.2 Background .................................................................................................
4
1.3 Apparatus ....................................................................................................
8
1.4 Procedure ..................................................................................................
11
1.5 Data Analysis ............................................................................................
16
Part 2: Draining Tank
..............................................................................................
16
2.1 Learning Objectives ..................................................................................
16
2.2 Background ...............................................................................................
16
2.3 Apparatus ..................................................................................................
19
2.4 Procedure ..................................................................................................
21
2.5 Data Analysis ............................................................................................
22
References ...................................................................................................................
23
Nomenclature ..............................................................................................................
24
Appendix A: Raw and Calculated Data Tables .........................................................
A1
Part 1: Flow through Pipe ..............................................................................
A1
Part 2: Draining Tank
.....................................................................................
A5
Appendix B: Sample Calculations .............................................................................
B1
Part 1: Flow through Pipe ..............................................................................
B1
Part 2: Draining Tank
.....................................................................................
B4
Appendix C: Error Analysis
.......................................................................................
C1
Appendix D: Supplementary Information .................................................................
D1
CHBE 264 Manual Experiment D: Fluids Revised on 11 February 2022 Back to Table of Contents -2-
Scenario Imagine... Your company requires you to replace a section of a process line requiring the equipment sizing for new pumps and other fluid handling devices. Chemical engineers need to know how to calculate the pressure drop through a piping system using friction factors and minor loss coefficients in order to fully design a chemical plant. Whether the plant is processing liquids, gases, or even solids, there will be piping, valves, pumps, compressors, and fittings, all of which will produce frictional energy losses that build up the amount of electrical power needed to drive the various downstream process units. Figure 1: Piping network [18]
Relevant Course Content in the 2
nd
Year CHBE Curriculum •
Transport Phenomenon (CHBE 251) ----- Friction factor, Moody diagram, Reynolds number, Navier-Stokes, Bernoulli Associated Keywords/Phrases: Bulk velocity, empirical, flow rates, friction factor, laminar, Moody diagram, pressure drop, relative roughness, Reynolds number, turbulent, viscosity, minor losses
CHBE 264 Manual Experiment D: Fluids Revised on 11 February 2022 Back to Table of Contents -3-
General Instructions In this experiment, students will learn concepts associated with fluid flow through piping network with various pipe fittings, mechanical pumps and valves. There are 2 parts to this experiment; 1) flow through pipes and 2) draining tank. Students must read the entire lab manual, including the figures and appendices before coming to the lab. This ensures that students will have a clear understanding of the theories behind the calculations and procedures that need to be carried out in the lab. 1.
Learning Objectives Students must clearly understand the goals of the experiment, principles that will be demonstrated, instruments to be used and data that needed to be collected and calculated before coming into the lab. 2.
Background This section presents background information required to achieve the objectives of the experiment. Students must be capable of using the information provided in this manual to justify whether the experiment is running as expected. Furthermore, the calculations required, as well as the nature of the data needed for those calculations, should be clearly understood. 3.
Apparatus Flow diagram, apparatus and equipment specification are provided in this section. Students must study the experimental setup prior to coming to the lab. Before starting the experiment, students should trace through the apparatus to better understand the system and the operation of the instrument. Appendix D provides useful instructions on how to use a dial caliper. Students are expected to know which direction is for closing and opening valves. In addition, students should be aware that a gear pump can never run dry eg. no fluid flow. It is recommended that students bring their own copy of the flow diagram for referencing when following the procedure. 4.
Procedure The step-by-step procedure for each experiment is given in this section. Students are expected to understand the reason behind each action. For safety reason, the “wet floor” sign must be placed on the ground to inform others. Each group should bring two laptops to the lab. This will allow the raw data to be entered into the Excel spreadsheet and most of the calculations to be completed before leaving the lab. Two TAs are available from 3-6 pm in Rm.4.06 to assist students with the calculations. 5.
Data Analysis The required calculations, graphs and thought questions are listed and must be presented and discussed in the lab report.
Your preview ends here
Eager to read complete document? Join bartleby learn and gain access to the full version
- Access to all documents
- Unlimited textbook solutions
- 24/7 expert homework help
CHBE 264 Manual Experiment D: Fluids Revised on 11 February 2022 Back to Table of Contents -4-
Part 1: Flow through Pipes
1.1 Learning Objectives Watch Video Clip Fluids Introduction (0 –
2.34 min) •
Investigate the effect of different pipe diameters, materials and elbows on major and minor head losses •
Apply Darcy-Weisbach equation to calculate friction factor •
Compare experimental graph of friction factor against Reynolds number with Moody diagram obtained from literature •
Compare pipe roughness calculated from Colebrook equation and theoretical pipe roughness obtained from Moody diagram •
Apply Bernoulli principle to determine K-loss coefficient and compare experimental K-loss coefficient to the theoretical one •
Observe laminar and turbulent flow using dye injection 1.2 Background Watch Video Clip Fluids Introduction (2.34 –
8.44 min) 1.
Bernoulli Equation The Navier-Stokes equations are a set of equations that describ the motion of a fluid derived from the basic principles of conservation of mass, momentum, and energy. The equations are based on the assumption that the fluid flow has properties of being continuous, incompressible, and with a constant viscosity. Another assumption is that gravity is the only substantial body force. Equation 1 shows the Navier-Stokes equations in the vector form [17]
.
? (
𝜕𝑣
⃑ 𝜕𝑡
+ 𝑣
∙ ∇𝑣
) = −∇? + 𝜇∇
2
v
⃑ + ρg
⃑ (1) where ρ = fluid density [kg/m
3
] 𝑣
= flow velocity vector [m/s] t = time [s] p = static pressure [Pa] μ = fluid viscosity [Pa s]
g = gravitational acceleration [m/s
2
] ∇ = gradient operator
CHBE 264 Manual Experiment D: Fluids Revised on 11 February 2022 Back to Table of Contents -5-
By neglecting frictional losses and thermal changes, the Navier-Stokes equations can be used to derive Bernoulli
’s
equation. This equation is a mathematical expression of the principle of conservation of energy for steady, frictionless, incompressible, and inviscid fluid flow, as shown in Equation 2. ?
?
+
𝑣
2
2
+ 𝑧? = 𝐻 = 𝐶????𝑎??
(2) where H = amount of pressure a fluid exerts on its containment [m
2
/s
2
] z = elevation [m] Bernouilli’s equation can be expressed in terms of energy per unit mass as above, but is most often computed in units of length by dividing Equation 2 by gravity (
g
), as shown in Equation 3. The pressure or head of a fluid is modified by its static pressure, elevation, and dynamic pressure or velocity. While fluids moving at different velocities can have the same head, the faster fluid will have either smaller static pressure or be at a higher elevation. The equation states that the sum of the pressure head, velocity head (kinetic energy per unit weight of flowing fluid), and elevation head is constant. ?
??
+
𝑣
2
2?
+ 𝑧 = 𝐻′ = 𝐶????𝑎??
(3) where ?
??
= Head due to local static pressure 𝑣
2
2?
= Head due to local dynamic pressure 𝑧
= Head due to elevation 2.
Major and Minor Head Losses Although Bernoulli’s equation works well
for computing the pressure head of a system, it is an idealized model that does not consider irreversible energy losses that occur during any real process. The irreversible loss of energy due to friction, heat transfer, shaft, or viscous work is called head loss for fluid systems. The Bernoulli equation can be adjusted to account for frictional losses. Equation 4 expresses the relationship for conservation of energy of a fluid flowing between points 1 and 2 with losses. ?
1
−?
2
??
+
𝑣
1
2
−𝑣
1
2
2?
+ 𝑧
1
− 𝑧
2
= ℎ
?
+ ℎ
?
(4)
CHBE 264 Manual Experiment D: Fluids Revised on 11 February 2022 Back to Table of Contents -6-
Head losses are classified as either major losses (h
f
) or minor loses (h
m
). Major losses are due to wall shear stress. They can be calculated by applying Bernouilli’s equation a
cross a straight section of pipe, taken in the form of the Darcy-Weisback formula, as shown in Equation 5. ℎ
?
= ? (
𝐿
?
)
𝑣
2
2?
(5) where h
f = major loss [m] f = friction factor d = diameter of pipe [m] L = length of pipe [m] The minor losses (h
m
) are due to local geometry changes in a pipe network, and are calculated from Equation 6. As fluids turn corners, vortices may result, reducing the amount of energy in the stream. Values of the minor loss coefficient, K, are dimensionless and depend on the size and shape of the pipe, and can be found in CHBE 251 course notes. Select minor loss factors are presented in Table 1. ℎ
?
= ?
𝑣
2
2?
(6) Table 1: K factors for Different Pipe Elements Pipe Head Loss Source K Loss Coefficient 90
o elbow 2 45
o elbow 0.39 Sharp entrance 0.5 Sharp exit 1 Couplings 0.1 100% open ball valve 1.3 100% open gate valve 0.1 75% open gate valve 1 50% open gate valve 4 25% open gate valve 11 The terms major and minor describe the type of head loss rather than the quantity. In some cases, major head losses can be ignored while minor head losses contribute greatly to the amount of energy loss in the system. Combining Equations 4, 5, and 6 yields Equation 7.
Your preview ends here
Eager to read complete document? Join bartleby learn and gain access to the full version
- Access to all documents
- Unlimited textbook solutions
- 24/7 expert homework help
CHBE 264 Manual Experiment D: Fluids Revised on 11 February 2022 Back to Table of Contents -7-
?
1
−?
2
??
+
𝑣
1
2
−𝑣
2
2
2?
+ 𝑧
1
− 𝑧
2
= ℎ
?
+ ℎ
?
=
𝑣
2
2?
(∑
?
?
𝐿
𝑖
?
𝑖
?
?=1
+ ∑
?
?
?
?=1
)
(7) where K
j = minor loss coefficient for pipe feature j Figure 2: Flow through pipe model with gate valve For flow through pipe experiment, the pipe is parallel to the floor as shown in Figure 2 so z
1
and z
2
are equivalent. In addition, the pipes are constant in diameter so v
1
and v
2
are identical. Thus Equation 7 can be further simplified to Equation 8. ?
1
−?
2
??
= ℎ
?
+ ℎ
?
=
𝑣
2
2?
(∑
?
?
𝐿
𝑖
?
𝑖
?
?=1
+ ∑
?
?
?
?=1
)
(8) If there are no elbows, pipe fittings or valves, the minor loss or h
m
term can be eliminated from Equation 8 to obtain Equation 9. ?
1
−?
2
??
= ℎ
?
=
𝑣
2
2?
(∑
?
?
𝐿
𝑖
?
𝑖
?
?=1
)
(9) 3.
Friction Factor The friction factor used to calculate the major losses is dependent upon the Reynolds number, defined by Equation 10, which indicates either laminar or turbulent flow by expressing the inertial to viscous force ratio [17]
. The friction factor is defined by Equation 11 for laminar flow and Equation 12 (Colebrook Equation) for turbulent flow. ?? =
?𝑣?
?𝑖??
𝜇
(10) ? =
64
??
??? ?? < 2100
(11) ? =
1
√?
= −2???
10
(
𝜀
3.7?
?𝑖??
+
2.51
??√?
) ??? ?? ≥ 2100
(12) 1 2 z
CHBE 264 Manual Experiment D: Fluids Revised on 11 February 2022 Back to Table of Contents -8-
where Re = Reynolds number ε = roughness (m) 4.
Moody Diagram The theoretical friction factor for a pipe of known diameter can alternatively be read off the Moody diagram using the calculated Reynolds number and the roughness,
, from the pipe manufacturer’s specifications. The Moody Diagram is shown in Figure 3, below and a larger version of it is provided in Appendix B for calculations. Figure 3: Friction factors for fluid flow in pipes The mean velocity of a fluid can be found from the volumetric flow rate and cross sectional area of the pipe. This is given by Equation 13. ? = 𝑣𝐴
𝑝?𝑝?
(13) where Q = volumetric flow rate [m
3
/s] v = mean velocity [m/s] A
pipe
= cross sectional area of the pipe [m
2
] 1.3 Apparatus
CHBE 264 Manual Experiment D: Fluids Revised on 11 February 2022 Back to Table of Contents -9-
Watch Video Clip Part 1: Flow through Pipes (0 –
2.30 min) Figure 4: Flow through pipes experiment We have two Flow through Tube stations. There are minor differences between two units and they are: Station A: This station has two water tanks. In Station A, water flowing through pipes L-1 and L-2 are set to the drain to avoid contaminating the water inside the tanks and fouling of the pipes. Station B: This station has only one water tank. In Station B, water flowing through pipe L-1 is set to the drain to avoid contaminating the water inside the tanks.
Your preview ends here
Eager to read complete document? Join bartleby learn and gain access to the full version
- Access to all documents
- Unlimited textbook solutions
- 24/7 expert homework help
CHBE 264 Manual Experiment D: Fluids Revised on 11 February 2022 Back to Table of Contents -10-
Figure 5:
Flow through pipes experiment schematics The main feature of this experimental apparatus shown in Figure 5 is the seven pipes that are positioned in parallel. Five of these pipes (L-2 to L-6) are used to measure the head loss across 1 meter of piping that vary in diameter and material of construction. Venturi meter is located in L-1. Pipeline L-1 is made of clear acrylic and accepts the injection of a dye to facilitate the observation of flow through the pipe; manometer tubes (M-1 and M-2) allows for the visualization of the pressure difference across a flow element. Inner diameter of acrylic pipe is 0.750” and diameter of throat section is 0.375”.
Ball valves are incorporated throughout the apparatus to guide the flow. After flowing through one or more of the seven main paths, the flow can be returned to the water reservoir to form a closed system. This apparatus is equipped with a pump, two rotameters of different scales (R-
1 and R-2) and eighteen quick connect ports (P-xx). Pressure is mainly measured by connecting a DP cell to any two of the quick connect ports.
CHBE 264 Manual Experiment D: Fluids Revised on 11 February 2022 Back to Table of Contents -11-
1.4 Procedure Watch Video Clip Part 1: Flow through Pipes (2.30 –
7.21 min) Trace through the pipe arrangement before conducting the experiment. Study each valve and rotameter, and ensure you understand which direction is open and which direction is close. In this experiment, water flowing through pipes L-1 and L-2 cannot be recycled back to the tanks since acrylic pipe L-1 is used for dye injection and steel pipe L-2 contains rust. As a result, pipes L-1 and L-2 are set to the drain to avoid contaminating the water inside the tanks and fouling of the pipes. 1.4.1 Removal of Rusty Water and Pipe Inspection for Leaks Station A: 1.
Open tank lids and check the water quality. Ensure that the water in both tanks is clear. If the water is unclear, follow steps below. If the water is clear, go to step 2. •
Open V-13 to drain water. •
Close V-13 and fill the tank with water by opening V-4. Consult the TA, if necessary. •
Open V-4 to fill the tanks to overflow marks. •
U
se brushes to stir rusty water and clean the wall of both tanks to drain out the rust. •
Open V-13 to drain water.
•
Repeat above steps many times until the water is clear. Buckets can be used to quickly remove rusty water from the tanks. •
Close V-13 and fill up the tanks with water to the overflow marks. Station B: Check the water quality. Ensure that the water in the tank is clear. If the water is unclear, follow steps below. If the water is clear, go to step 2. •
Open V-13 to drain water.
•
Close V-13 and fill the tank with water using the hose connected to the tap (V-4) near the sink. Consult the TA, if necessary. •
Repeat above steps many times until the water is clear. •
Close V-13 and fill up the tank with water to the overflow mark. 2.
Open V-7 and close V-3, V-5,V-6, and V-8 to V-12 such that water flows only through 3/4” steel tube. 3.
Ensure that the water outlet is directed to the drain. Set V-2 to drain to prevent rust from the steel line entering the water tanks.
4.
Set V-1 to R-1 to direct water flow towards rotameter 1. 5.
Open R-1 and close R-2.
CHBE 264 Manual Experiment D: Fluids Revised on 11 February 2022 Back to Table of Contents -12-
6.
Check the water level in the tank(s). If necessary, add water by opening V- 4. Once the water level in the tank(s) are close V-4. Switch on the power bar to start the pump. When necessary, open V- 4 2) to maintain water levels in the tanks.
7.
Turn the pump off to collect water in the tanks and set the rotameter to a reading of 0. Open valves V-5 to V-
12, 1/2” ball valve and 1/2” gate valve so that water flows through all pipes. Make sure V-2 is set to drain. Switch on the power bar to start the pump. 8.
Allow the system to run for 3 minutes.
9.
Check for any leaks in the piping network and set V-2 to recycle. Ensure that V-4 is closed when the water level in the tank reaches the overflow point. 1.4.2 Pipe Diameter and Length Measurements 10.
Prepare a table similar to Table A1 to enter your measurements into UBC lab data book. 11.
Measure pipe inner diameters and record them in Table A1. Refer to Appendix D for instructions on how to use dial calipers. 12.
Measure pipe lengths and record them in Table A1. Measure from the center of one DP cell port to the center of the other port using measuring tape. Refer to Table A1 for DP cell ports involved in every pipe segment. 1.4.3 Flow through Pipes of Different Materials and Diameters IMPORTANT! Always have one line open to avoid pressure build up in the system. Before closing a valve, open another valve. Your objective is to determine the pressure drop across pipes of different material and different diameters. To do this you will use the DP Cell as specified in the instructions below. Note, the ports P-xx will vary based on which pipe you
’
re testing. •
Connect the DP cell to ports P-xx and P-xx. Zero the DP cell by pressing the MIN/MAX
and HOLD
buttons at the same time. The display should read “ZERO IN PROGRESS” while the bottom line counts down from 9. Make sure the DP cell is at the same level as the ports. •
If the DP Cell displays a reading which is negative or very large, repeat above step to zero the DP Cell again. Note: If the DP Cell displays “ZERO RANGE ERROR”, it means that the new zero value generated is outside ±5% of the original factory calibrated zero. Make sure there are no air bubbles in the lines and the DP cell is at the same level as the ports to avoid this error. For each pipe indicated below, write procedural steps which specify the following: •
Which valves will be open or closed before you begin (think about where water will flow) •
Where the DP cell will be connected
Your preview ends here
Eager to read complete document? Join bartleby learn and gain access to the full version
- Access to all documents
- Unlimited textbook solutions
- 24/7 expert homework help
CHBE 264 Manual Experiment D: Fluids Revised on 11 February 2022 Back to Table of Contents -13-
•
Which valves will be open or closed to begin flowing water through the pipe you are testing •
Which flow rate you will test initially and what you will adjust to target that flow rate •
Note which data you will collect and record in Table A2 •
Specify which 3 additional flow rates you will test Note: Blank steps are provided below (e.g., 14-18) –
add or remove blank steps as needed based on the procedure you develop. Adjust the step numbers accordingly. 13.
Prepare a table similar to Table A2 to enter your measurements into UBC lab data book. Run for 3/4" Steel Tube
14.
15.
16.
17.
18.
19.
Press the MIN/MAX
button on DP cell and wait for 30 sec. Record the minimum and maximum pressure differences on Table A2. 20.
Repeat for three additional flow rates confirmed with the TA. Record the flow rate and pressure readings on Table A2. Run for 3/4" Copper Tube [Fill in procedural steps] Press the MIN/MAX
button on DP cell and wait for 30 sec. Record the minimum and maximum pressure differences on Table A2. Repeat for three additional flow rates confirmed with the TA. Record the flow rate and pressure readings on Table A2. Run for the 3/4" SS Tube
[Fill in procedural steps]
CHBE 264 Manual Experiment D: Fluids Revised on 11 February 2022 Back to Table of Contents -14-
Run for 1/4" SS Tube [Fill in procedural steps] Run for the 1/2" SS Tube [Fill in procedural steps] 1.4.4 Flow through Elbows [Fill in procedural steps] For the sections below, follow the procedure as written. 1.4.5 Observation of the behaviour across the expansion section 21.
Open V-7 and ensure that valves V-3, V-5 to V-6 and V-8 to V-12 are closed, V-1 is set to R-2 and V-2 is set to recycle. 22.
Prepare a table similar to Table A3 to enter your measurements into UBC lab data book. 23.
Zero DP cell. Collect data using the respective quick connect ports for the pipe segments as indicated in Table A2. 24.
For 3/4” acrylic tube, open V
-5 to V-6 and close V-7. Set R-2 to 3 USGPM and record the minimum and maximum pressure differences for the required segments using the DP cell. Then disconnect the DP Cell from the quick connect ports. 25.
Now reduce the flow through R-2 to 1 USGPM and open the ports for the three manometers. Slowly close V-6 until the water level in the manometers starts to rise and air bubbles are not present. Once the water levels in all three are steady, close all the manometer ports simultaneously and record their respective heights in Table A3. 26.
For each pipe segment in this section, use a ruler to measure the height of water in the manometers. Record them in Table A3.
CHBE 264 Manual Experiment D: Fluids Revised on 11 February 2022 Back to Table of Contents -15-
1.4.6 Dye Injection: Observation of flow behaviour 27.
Set V-2 to drain. 28.
Set and record flow rate of rotameter 2 (R-2) to 0.5 GPM. 29.
Open V-5 and V-
6 fully while also opening the three manometers on the ¾” acrylic line.
30.
Close V-7. 31.
Slowly close V-6 until the water level in the manometers starts to rise and air bubbles are not present. Then close the ports for the manometers. 32.
Inject 0.5 mL of dye through the injection port and observe the flow regimes. The dye might take a few minutes to fully enter the water stream from the injection port. Allow the system to flush out the dye for 3 minutes. 33.
Once you have observed the flow regimes with the dye, fully open V-6 and increase the flow rate on R-2 to flush out the line further. Open and adjust V-4 to maintain a water level below the over flow line. 1.4.6 Dye Injection: Observation of flow behaviour 34.
Set V-2 to drain. 35.
Set and record flow rate of rotameter 2 (R-2) to 0.5 GPM. 36.
Open V-5 and V-
6 fully while also opening the three manometers on the ¾” acrylic line.
37.
Close V-7. 38.
Slowly close V-6 until the water level in the manometers starts to rise and air bubbles are not present. Then close the ports for the manometers. 39.
Inject 0.5 mL of dye through the injection port and observe the flow regimes. The dye might take a few minutes to fully enter the water stream from the injection port. Allow the system to flush out the dye for 3 minutes. 40.
Once you have observed the flow regimes with the dye, fully open V-6 and increase the flow rate on R-2 to flush out the line further. Open and adjust V-4 to maintain a water level below the over flow line. Shut Down 41.
Open V-5 to V-12 to allow flow through all pipes. 42.
Set V-1 to R-1 and V-2 to drain. 43.
Close V-4 to stop water supply and turn off the pump. 44.
Open V-3 to purge the system with compressed air for 2 minutes. Then close V-3, set V-
2 drain and switch on the power bar for the pump. Let the system flush with water once again for 2 minutes. 45.
Turn off the pump and open V-3 again to purge the system with compressed air for 2 minutes. 46.
Close V-3, R-1 and R-2. 47.
Open V-13 to drain the water from the two tanks.
Your preview ends here
Eager to read complete document? Join bartleby learn and gain access to the full version
- Access to all documents
- Unlimited textbook solutions
- 24/7 expert homework help
CHBE 264 Manual Experiment D: Fluids Revised on 11 February 2022 Back to Table of Contents -16-
1 1.5 Data Analysis Part 1: Flow through Pipes 1.
Determine the average pressure drops between each pair of DP cell ports 2.
Calculate major head loss then determine friction factor for pipes L-2 to L-6 3.
Calculate major head loss then determine minor head loss for pipe L-7 4.
Determine experimental K-loss coefficient for pipe L-7 and compare the experimental results to the theoretical total K-loss coefficients. Explain any deviances and sources of error. 5.
Calculate Reynolds Number and determine pipe roughness for pipes L-2 to L-7 6.
Plot friction factor against Reynolds Number on Moody Diagram provided in Appendix B (print out and plot the data points by hand). Insert your experimental relative pipe roughness in the provided box on the right-hand side of the diagram. Compare the experimental plot and literature Moody diagram. 7.
Obtain corresponding pipe roughness from literature Moody Diagram shown in Figure 3. Discuss how the pipe roughness from Moody Diagram compares to the experimental value. 8.
Calculate the percentage difference between pressure drops measured using manometer and DP cell for pipe L-1 (as a percentage of the DP cell value). Part 2: Draining Tank 2.1 Learning Objectives Watch Video Clip Fluids Introduction (0 –
2.34 min) •
Study the effect of different piping configurations and gate valve percent opening on draining time
•
Determine aggregate and velocity correction factors to predict draining time and compare the predicted time to the actual draining time
2.2 Background 1.
Pressure Drop z
CHBE 264 Manual Experiment D: Fluids Revised on 11 February 2022 Back to Table of Contents -17-
Figure 6: Draining tank model Figure 6 shows a reservoir tank filled with a constant level of water such that flow out through an exit pipe is at steady state and can be modeled using the engineering Bernoulli equation. The velocity in the tank (v
1
) can be set to zero due to the large cross-sectional area of the tank. By choosing the height of the exit pipe (z
2
) to be zero, Equation 13 and Equation 8 can be combined to yield Equation 14. From Equation 14, the pressure drop (P
1
-P
2
) of the draining system from the liquid surface in the tank to the point where the water leaves the sharp exit (K = 1) at the end of the pipe can be computed. In order to solve for P
2
, P
1
is set to atmospheric pressure as this is the pressure at the interface with the atmosphere. ?
1
−?
2
??
+ 𝑧
1
=
8?
2
??
2
?
?𝑖??
4
(1 + ∑
?
?
𝐿
𝑖
?
𝑖
?
?=1
+ ∑
?
?
?
?=1
)
(14) Like steady-state flow models, which are important to understand for continuous processes, unsteady state draining models are essential for chemical engineers to design large-
scale batch draining processes. 2.
Volumetric Flow Rate In order to calculate the time required to drain the tank, one must find the relationship between the outflow rate and tank height. The formula for the outflow rate is shown in Equation 15, below. V
represents the volume of water remaining in the tank. Because the volume of water is decreasing during the draining, a negative sign is placed at the front of the equation to produce a positive flow rate, Q
. Q=-
∂V
∂t
(15) Since the cross sectional area of the reservoir tank and the area of the exit pipe are both constant, the volumetric outflow rate can be alternatively expressed by Equation 16, by factoring out the constant areas. Note the signs in this equation. This equation can be perceived as a mass balance of the overall system, with the middle term being the accumulation and the last term being the outflow. Q=-A
tank
∂z
∂t
= 𝐴
𝑝?𝑝?
𝑣
(16) where A
tank
= cross sectional area of the tank, [m
2
] z = height of water in the tank, [m] 2
CHBE 264 Manual Experiment D: Fluids Revised on 11 February 2022 Back to Table of Contents -18-
3.
Velocity Correction Factor It can be determined from the energy balance that the potential energy in the tank is equal to the kinetic energy of the stream flowing out through the pipe. Equation 17 expresses this theory, providing an expression for v
, which is combined with Equation 16 to produce Equation 18. 1
2
𝑣
2
= ?𝑧
(17) −𝐴
𝑡𝑎??
𝜕𝑧
𝜕𝑡
= 𝐴
𝑝?𝑝?
𝑣 = 𝐴
𝑝?𝑝?
(?√2?𝑧
)
(18) where c
is the velocity correction factor, which can be solved under a variety of height conditions. Under ideal assumption, fluid flows with constant velocity over the entire cross-
section of the pipe. However, the real flow has non-uniform velocity distribution due to the friction along the sidewall of the pipe. Thus the velocity correction factor is introduced to account for the non-ideality in viscid flows. 4.
Predicted Draining Time The mass balance can be rearranged into Equation 19, − ∫
?𝑧
√𝑧
𝑧
𝑧
?
=
𝐴
?𝑖??
𝐴
𝑡𝑎?𝑘
?√2?
∫ ??
𝑡
0
(19) and can be integrated to give Equation 20, which is the model for the height of the water in the tank with respect to time. 𝑧 = (√𝑧
0
−
?𝑡
2
)
2
(20) k
in this case is the dimensionless aggregate correction factor. The aggregate correction factor is used to relate volumetric flow rate and tank height to determine predicted drain time while accounting for losses in the system. 5.
Aggregate Correction Factor Equation 21 shows the relationship between the velocity correction factor, c
and the aggregate correction factor, k
. ? =
𝐴
?𝑖??
𝐴
𝑡𝑎?𝑘
?√2?
=
?
𝐴
𝑡𝑎?𝑘
√𝑧
(21) Equation 21 also shows how k
is computed using the tank water level and volumetric flow rate. Another method of calculating k
begins by rearranging the equation such that Q
is
Your preview ends here
Eager to read complete document? Join bartleby learn and gain access to the full version
- Access to all documents
- Unlimited textbook solutions
- 24/7 expert homework help
CHBE 264 Manual Experiment D: Fluids Revised on 11 February 2022 Back to Table of Contents -19-
proportional to the square root of z
by the constant kA
tank
. By performing a linear regression with different heights and flow rates, the slope is determined and can be manipulated to determine k
. 2.3 Apparatus Part 2: Draining Tank Watch Video Clip Part 2: Draining Tank (0 –
2.10 min) Figure 7: Drainage experiment
CHBE 264 Manual Experiment D: Fluids Revised on 11 February 2022 Back to Table of Contents -20-
Figure 8: Drainage experiment piping configurations Figure 9: Drainage experiment schematic The experimental apparatus shown in Figure 7 consists of a piping setup that leads to a catch basin and is fed by a level controlled holding tank. There are two different piping configurations used in the experiment. The first configuration consists of several different pieces of piping with the same inner diameter (ID), a variety of 90° bends and 45° bends, and a gate valve (V2) as depicted by Figure 8. The second configuration is a simple straight pipe with a gate valve attached. The piping systems attach to the base of the feed tanks by screwing into a union that follows the stainless steel ball valve (V1). The tanks also have four portholes on their sides that allow for water level control. There are four possible steady state levels, controlled by valves V3 to V6 (Figure 9). The flow rate into the feed tank is controlled by a ball valve, V7 on a pump hose. During operation the piping system and level control overflow ports drain into a water reservoir on the floor. Inside the water reservoir is a RIDGID
1/6 HP Submersible Utility Pump with a flow rate of 3000 GPH that discharges through a ¾” garden hose. The garden hose is routed back up to the feed tank to complete the water cycle. The water in the system is simple tap water.
CHBE 264 Manual Experiment D: Fluids Revised on 11 February 2022 Back to Table of Contents -21-
2.4 Procedure Watch Video Clip Part 2: Draining Tank (2.10 –
5.41 min) Ensure you have placed the “wet floor” sign on the ground to let others know to be careful. There are two stations for draining tank experiment with different piping configurations. The piping arrangement of drainage station 1 is shown in Figure 8 on the left and drainage station 2 is on the right. The following procedure will be performed at the same time in both stations; two students in each station. Ensure that all the valves V1 to V7 are closed. Prepare tables similar to tables A9 - A12 and A15-A18 to enter your measurements into UBC lab data book. 2.4.1 Piping Arrangement and Start-up 1.
Take an inventory of the piping (measuring the length) and the pipe fittings. Measure the inner diameters of the tank and the outflow pipe and record them.
2.
Turn the gate valve (V2) clockwise until it is fully closed. 1.
Turn the gate valve counterclockwise until it is fully open, counting the number of complete rotations. 2.
Using the total number of rotations, calculate how many turns are needed for the valve to be 25% open (i.e. if fully open is 4 turns, then 75% open will be 3 turns). 3.
Check to ensure that the water level in the catch basin (the basin on the floor) is higher than half the height of the pump. If the water level is too low, add water to the catch basin. 4.
Close the ball valve V1 at the base of the tank. The ball valves for this apparatus turn 90 degrees from open to close. Ensure you understand which direction is open and which direction is closed. 5.
Open the first side port using valve V at 25% of the tank height. 6.
Ensure the pump hose to the feed tank is securely connected at both ends. 7.
Plug the pump into an electrical outlet to turn the pump on. 2.4.2 Pressure Drop Model 1.
With valves V3 and V7 fully open and valves V1-V2 and V4-V6 closed, allow the feed tank to fill until water flows through the first overflow port (V3). 2.
Close V7 and V3. 3.
Record the tank water level and open V7, V1 and V2 (100% open) so that flow in is equal to flow out and the system is at steady state by maintaining the tank water level at the same height.
Your preview ends here
Eager to read complete document? Join bartleby learn and gain access to the full version
- Access to all documents
- Unlimited textbook solutions
- 24/7 expert homework help
CHBE 264 Manual Experiment D: Fluids Revised on 11 February 2022 Back to Table of Contents -22-
4.
Using the 1 L graduated cylinder and a stop watch, fill the cylinder with the outflow from the piping system. Record the volume and duration time in order to calculate the volumetric outflow rate. Repeat this measurement 2 more times. 5.
Close valves V1 and V7 and open valve V4 to allow the water level in the tank to reach the second overflow level. 6.
Close V4. 7.
Repeat steps 3 and 4. 8.
Close valves V1 and V7 and open valve V5 to allow the water level in the tank to reach the third overflow level. 9.
Close V5. 10.
Repeat steps 3 and 4. 11.
Close valves V1 and V7 and open valve V6 to allow the water level in the tank to reach the fourth overflow level. 12.
Close V6. 13.
Repeat steps 3 and 4. 14.
Repeat steps 1-13with V2 at 25% open. 15.
Close valve V1 and V7 and unplug the pump. 2.4.3 Draining Tank Model 1.
The TA will specify a desired volume to be drained from the tank with it initially filled. Calculate the resulting height after the specified volume is drained. 2.
With a stopwatch, open valve V1 and V2 (100% open) and record the time it takes for the calculated height to be reached. 3.
Repeat the measurement with V2 at 25% open. Shut Down 1.
Unplug pump. 2.
Open valves V1 and V2 fully and allow the tank to drain into the catch basin. 3.
Close all valves (V1-V7). 4.
Mop/wipe up any water spills. 2.5 Data Analysis Experiment 2: Draining Tank 1.
Calculate exit flow rates under different gate valve openings, and then determine the average exit flow rates for both configurations. 2.
Calculate velocity correction factors using both numerical and graphical methods. Compare and discuss values obtained by the different methods. Comment on the effect of piping configuration on correction factors. 3.
Calculate average aggregate correction factors and predicted tank draining times
Your preview ends here
Eager to read complete document? Join bartleby learn and gain access to the full version
- Access to all documents
- Unlimited textbook solutions
- 24/7 expert homework help
CHBE 264 Manual Experiment D: Fluids Revised on 11 February 2022 Back to Table of Contents -23-
4.
Determine percent difference between predicted and actual tank draining times (as a percentage of the predicted tank draining time). Discuss reasons for deviations between predicted and actual values. References
1.
Boulder, M. (2011). Bernoulli Equation & Manometers: Youtube Bernoulli Equation & Manometers: Fluids. University of Colorado, 45
(2), 114. 2.
Chapra, S. C. (2006). Applied Numerical Methods with MATLAB for Engineers and Scientists
(Vol. 2 edition). McGraw-Hill Science/Engineering/Math. 3.
Chapra, S. C. (2008). Applied numerical methods with MATLAB for engineers and scientists.
Boston: McGraw-Hill Higher Education. 4.
CHBE 262 (2005). Expt. K: Flow Through Tubes. CHBE 262 Lab Manual, 2005. 5.
Cheremisinoff, N.P., Cheremisinoff, P.N., “Pumps and Pumping Operations”, Prentice
-
Hall, Inc. New Jersey (1992). 6.
Co., C. (1983). Flow of fluids through valves, fittings and pipe.
London: Crane. 7.
Crane Co., “Flow of Fluids Through Valves, Fittings and Pipe”, Crane Canada Ltd., Technical Paper No. 410-C (1957). 8.
Fox, R.W. and A.T. McDonald, "Introduction to Fluid Mechanics", 7
th
ed., J. Wiley and Sons, Inc., New York (2008). 9.
Hrenya, C. (2011). Active Learning in Fluid Mechanics: Youtube Tube Flow and Puzzling Fluids Questions. Chemical engineering education, 45
(2), 114. 10.
Karassik, I.J. et al., “Pump Handbook", 3
rd
ed., McGraw-Hill, New York (2001), chapters 2 and 3. 11.
Kirk, R., Othmer, D., “Kirk
-
Othmer Encyclopedia of Chemical Technology”, John Wiley & Sons, Inc., New Jersey (2001). 12.
Koretsky, M. (2008). Enhancement of Student Learning in Experimental Design Using a Virtual Laboratory. IEEE transactions on education, 51
(1), 76. 13.
Mandal, M. (2009). Experimental Study on Pressure Drop and Heat Transfer of Turbulent Flow in Tube in Tube Helical Heat Exchanger. Industrial & engineering chemistry research, 48
(20), 9318. 14.
Marlin, T. (2010). Teaching “operability” in undergraduate chemical engineering design education. Computers & Chemical Engineering, 34
(9), 1421-1431. 15.
Nayyar, Mohinder L., “Piping Handbook”, 7
th
ed., McGraw-Hill, New York (2000), chapter A10 16.
Perry, R.H., Green, D.W, “Perry's Chemical Engineers' Handbook", 8
th
ed., McGraw- Hill, New York (1997), sections 6 and 10. 17.
White, F. M., & Kliens, S. (2011). Fluid Mechanics.
New York: McGraw-Hill. 18.
"Freedom Process Piping, Inc." Freedom Process Piping, Inc. Web.
Your preview ends here
Eager to read complete document? Join bartleby learn and gain access to the full version
- Access to all documents
- Unlimited textbook solutions
- 24/7 expert homework help
CHBE 264 Manual Experiment D: Fluids Revised on 11 February 2022 Back to Table of Contents -24-
Nomenclature Symbol Units ρ fluid density kg/m
3
𝑣
flow velocity vector m/s t Time s p static pressure Pa μ
fluid viscosity Pa s g gravitational acceleration m/s
2
∇
gradient operator H amount of pressure a fluid exerts on its containment m
2
/s
2
z elevation m h
f Major loss m f Friction factor d Diameter of pipe m L Length of pipe m Re Reynolds Number ε
Roughness m h
m Minor loss m Q
volumetric flow rate m
3
/s v mean velocity m/s A
pipe
cross sectional area of the pipe m
2
k Aggregate correction factor m
0.5
/s c Velocity correction factor
Your preview ends here
Eager to read complete document? Join bartleby learn and gain access to the full version
- Access to all documents
- Unlimited textbook solutions
- 24/7 expert homework help
CHBE 264 Manual –
Appendix A Experiment D: Fluids Revised on 11 February 2022 Back to Table of Contents A-1 Appendix A: Raw and Calculated Data Tables Pressure Drop Through Piping Part 1: Flow through Pipe
Table A1
: Pipe Diameter and Length Pipe/Elbow Port 1 Port 2 Pipe Inner Diameter Pipe Length Units ± Uncertainty 3/4’’ Steel Tube
P-21 P-22 3/4’’ Copper Tube P-31 P-32 3/4’’ SS Tube
P-41 P-42 1/4’’ SS Tube
P-51 P-52 1/2’’ SS Tube
P-61 P-62 Elbow 1 P-71 P-72 Elbow 2 P-72 P-73 Elbow 3 P-73 P-74 Two Elbows P-71 P-73 Three Elbows P-71 P-74 Expansion P-11 P-13 Pre-Expansion P-11 P-12 Post-Expansion P-12 P-13 IMPORTANT •
Use these tables to enter your data •
Units must be included in each table •
Include all errors as a ±factor in the tables
Your preview ends here
Eager to read complete document? Join bartleby learn and gain access to the full version
- Access to all documents
- Unlimited textbook solutions
- 24/7 expert homework help
CHBE 264 Manual –
Appendix A Experiment D: Fluids Revised on 11 February 2022 Back to Table of Contents A-2 Table A2
: Flow Rate, Maximum and Minimum Pressure Differences Pipe/Elbow Port 1 Port 2 Flow Rate Max Pressure Drop Min Pressure Drop Units ± Uncertainty 3/4’’ Steel Tube
P-21 P-22 3/4’’ Copper Tube P-31 P-32 3/4’’ SS Tube
P-41 P-42 1/4’’ SS Tube P-51 P-52 1/2’’ SS Tube
P-61 P-62 Elbow 1 P-71 P-72 Elbow 2 P-72 P-73 Elbow 3 P-73 P-74 Two Elbows P-71 P-73 Three Elbows P-71 P-74 Expansion P-11 P-13 Pre-Expansion P-11 P-12 Post-Expansion P-12 P-13 Table A3
: Flow Rates and Manometer Heights Pipe L-1 Manometer 1 Manometer 2 Manometer 3 Units ± Uncertainty Flow Height
Your preview ends here
Eager to read complete document? Join bartleby learn and gain access to the full version
- Access to all documents
- Unlimited textbook solutions
- 24/7 expert homework help
CHBE 264 Manual –
Appendix A Experiment D: Fluids Revised on 11 February 2022 Back to Table of Contents A-3 Table A4
: Major Head Loss and Friction Factor for Pipes L-2 to L-6 Pipe L-2 to L-6 Flow Rate Average Pressure Drop Major Head Loss Friction Factor Units ± Uncertainty N/A 3/4’’ Steel Tube
± ±
±
±
3/4’’ Copper Tube ±
±
±
±
3/4’’ SS Tube
±
±
±
±
1/4’’ SS Tube
±
1/2’’ SS Tube
±
±
± ± Table A5
: Major and Minor Head Losses for Pipe L-7 Pipe L-7 Elbow Flow Rate Average Pressure Drop Friction Factor Major Head Loss Minor Head Loss Units ± Uncertainty N/A N/A Elbow 1 ± ± Elbow 2 ± ± Elbow 3 ± ± Two Elbows ± ± Three Elbows ± ± Table A6
: Theoretical and Experimental K-loss Coefficients for Pipe L-7 Pipe L-7 Elbow Theoretical Total K-Loss Coefficient Experimental K-Loss Coefficient Units ± Uncertainty N/A N/A Elbow 1 ± Elbow 2 ± Elbow 3 ±
Your preview ends here
Eager to read complete document? Join bartleby learn and gain access to the full version
- Access to all documents
- Unlimited textbook solutions
- 24/7 expert homework help
CHBE 264 Manual –
Appendix A Experiment D: Fluids Revised on 11 February 2022 Back to Table of Contents A-4 Two Elbows ± Three Elbows ±
Your preview ends here
Eager to read complete document? Join bartleby learn and gain access to the full version
- Access to all documents
- Unlimited textbook solutions
- 24/7 expert homework help
CHBE 264 Manual –
Appendix A Experiment D: Fluids Revised on 11 February 2022 Back to Table of Contents A-5 Table A7
: Theoretical and Experimental Pipe Roughness for Pipes L-2 to L-6 Pipe/Elbow Reynolds Number Pipe Roughness from Moody Diagram Experimental Pipe Roughness Units ± Uncertainty N/A N/A 3/4’’ Steel Tube
±
±
± ± ± ± ± ± 3/4’’ Copper Tube ± ± ± ± ± ± ± ± 3/4’’ SS Tube
± ± ± ± ± ± ± ± 1/4’’ SS Tube
± ± 1/2’’ SS Tube
± ± ± ± ±
±
±
±
Elbow 1 ±
±
Elbow 2 ±
±
Elbow 3 ±
±
Two Elbows ±
±
Three Elbows ±
±
Table A8
: Percent Difference in Pressure Measurements with Manometer and DP Cell Pipe L-1 DP Cell Pressure Drop Manometer Pressure Drop Percent Difference Units ± Uncertainty N/A Expansion ± Pre-Expansion ± Post-Expansion ± Part 2: Draining Tank
Table A9
: System Dimensions for Station 1 Value ± Uncertainty
Tank Inner Diameter (m) Pipe Inner Diameter (m) Pipe Length (m)
Your preview ends here
Eager to read complete document? Join bartleby learn and gain access to the full version
- Access to all documents
- Unlimited textbook solutions
- 24/7 expert homework help
CHBE 264 Manual –
Appendix A Experiment D: Fluids Revised on 11 February 2022 Back to Table of Contents A-6 Table A10
: Head Loss in Piping Station 1 Pipe Head Loss Source Frequency in Line Table A11
: Water Level, Volume and Time for Station 1 Gate Valve Opening Water Level Collected Volume Collection Time Units ± Uncertainty 100% 25% Table A12
: Initial and Final Water Level, and Time for Station 1 Gate Valve Opening Initial Tank Height Final Tank Height Actual Draining Time Units ± Uncertainty 100% 25% Table A13
: Aggregate and Velocity Factors for Station 1 Parameter Gate Valve Opening Numerical Method Graphical Method Aggregate Correction Factor 100% ±
±
25% ±
±
Velocity Correction Factor 100% ±
±
25% ±
±
Your preview ends here
Eager to read complete document? Join bartleby learn and gain access to the full version
- Access to all documents
- Unlimited textbook solutions
- 24/7 expert homework help
CHBE 264 Manual –
Appendix A Experiment D: Fluids Revised on 11 February 2022 Back to Table of Contents A-7 Table A14
: Actual and Predicted Tank Drain Times for Station 1 Trial Actual Draining Time Predicted Draining Time Percent Difference Units ± Uncertainty N/A N/A 1 ±
±
2 ±
±
3 ±
±
Table A15
: System Dimensions for Station 2 Value ± Uncertainty
Tank Inner Diameter (m) Pipe Inner Diameter (m) Pipe Length (m) Table A16
: Head Loss in Piping Station 2 Pipe Head Loss Source Frequency in Line Table A17
: Water Level, Volume and Time for Station 2 Gate Valve Opening Water Level Collected Volume Collection Time Units ± Uncertainty 100% 25%
Your preview ends here
Eager to read complete document? Join bartleby learn and gain access to the full version
- Access to all documents
- Unlimited textbook solutions
- 24/7 expert homework help
CHBE 264 Manual –
Appendix A Experiment D: Fluids Revised on 11 February 2022 Back to Table of Contents A-8 Table A18
: Initial and Final Water Level, and Time for Station 2 Gate Valve Opening Initial Tank Height Final Tank Height Actual Draining Time Units ± Uncertainty 100% 25% Table A19
: Aggregate and Velocity Factors for Station 2 Parameter Gate Valve Opening Numerical Method Graphical Method Aggregate Correction Factor 100% ±
±
25% ±
±
Velocity Correction Factor 100% ±
±
25% ±
±
Table A20
: Actual and Predicted Tank Drain Times for Station 2 Trial Actual Draining Time Predicted Draining Time Percent Difference Units ± Uncertainty N/A N/A 1 ±
±
2 ±
±
3 ±
±
Your preview ends here
Eager to read complete document? Join bartleby learn and gain access to the full version
- Access to all documents
- Unlimited textbook solutions
- 24/7 expert homework help
CHBE 264 Manual –
Appendix B Experiment D: Fluids Revised on 11 February 2022 Back to Table of Contents B-1 Appendix B: Sample Calculations Pressure Drop Through Piping Refer to the experiment procedure and background for necessary equations NOTE
: Pay attention to units and apply necessary conversions. Part 1: Flow through Pipe
a)
Determine the average pressure difference based on recorded maximum and minimum pressure b)
Calculate major head loss using equation (9) then determine friction factor using Darcy-Weisback equation (5) for pipes L-2 to L-6 c)
Calculate major head loss for pipe L-7 using Darcy-Weisback equation (5). Note that the friction factor for L-7 is the same as friction factor for L-6 at the same flow rate since L-7 has the same diameter and material as L-6. d)
Calculate minor head loss for pipe L-7 using Bernoulli equation (8). e)
Using equation (6), determine experimental K-loss coefficient for pipe L-7. Compare the experimental results to the theoretical total K-loss coefficients obtained from Table 1. Explain any deviances and sources of error f)
Calculate Reynolds Number using equation (10) and determine pipe roughness for pipes L-2 to L-7 using Colebrook equation (12). IMPORTANT •
The sample calculations must be handwritten •
Equations used should be mentioned clearly and the symbols should also be explained •
Each equation should be followed by one example •
Complete the tables given in Appendix A using the following instructions •
All the measurements and values must be written along with their units •
Report only the significant digits of each value •
Hand in the original data sheets
Your preview ends here
Eager to read complete document? Join bartleby learn and gain access to the full version
- Access to all documents
- Unlimited textbook solutions
- 24/7 expert homework help
CHBE 264 Manual –
Appendix B Experiment D: Fluids Revised on 11 February 2022 Back to Table of Contents B-2 g)
Plot friction factor against Reynolds Number on Moody Diagram provided (print out and plot the data points by hand). Insert your experimental relative pipe roughness in the provided box on the right-hand side of the diagram. Compare the experimental plot and literature Moody diagram. h)
Read off relative pipe roughness from literature Moody Diagram in Figure 3 for each data point and multiply by diameter to achieve pipe roughness. Discuss how the pipe roughness from Moody Diagram compares to the experimental value.
Your preview ends here
Eager to read complete document? Join bartleby learn and gain access to the full version
- Access to all documents
- Unlimited textbook solutions
- 24/7 expert homework help
CHBE 264 Manual –
Appendix B Experiment D: Fluids Revised on 11 February 2022 Back to Table of Contents B-3
Your preview ends here
Eager to read complete document? Join bartleby learn and gain access to the full version
- Access to all documents
- Unlimited textbook solutions
- 24/7 expert homework help
CHBE 264 Manual –
Appendix B Experiment D: Fluids Revised on 11 February 2022 Back to Table of Contents B-4 Part 2: Draining Tank
a)
Calculate the correction factor, c, analytically •
Determine the dimensionless aggregate correction factor, k, at each water level tested using equation (21). •
Determine the correction factor, c, for each gate valve position using an averaged value of k across all water levels tested using equation (21). b)
Determine the correction factor, c, graphically •
Plot appropriate functional forms, according to equation (21), of the water level and flow rate and determine the regression slope using LINEST. •
Calculate the dimensionless aggregate correction factor, k, for each gate valve position based on the slope. •
Determine the correction factor, c, for each gate valve position using the dimensionless aggregate correction factor, k, using equation (21). c)
Compare and discuss values obtained by the different methods. Comment on the effect of piping configuration on correction factors d)
Compare the measured drainage time with the calculated drainage time •
Calculate the predicted drainage time using equation (20) with the aggregate correction factor that you derived numerically. •
Compare the predicted time with the actual time you measured.
Your preview ends here
Eager to read complete document? Join bartleby learn and gain access to the full version
- Access to all documents
- Unlimited textbook solutions
- 24/7 expert homework help
CHBE 264 Manual –
Appendix C Experiment D: Fluids Revised on 11 February 2022
Back to Table of Contents C-1 Appendix C: Error Analysis Pressure Drop through Piping IMPORTANT •
The error analysis must be handwritten •
Equations used should be mentioned clearly and the symbols should also be explained •
Provide one example for all the errors calculated •
Errors must be written along with their units •
Include all errors as a ±factor in the tables in Appendix A
•
Hand in the original sheets Note: •
Use the following values to determine the error: o
Volume ± 5mL o
Time ± 0.5s o
Length ± 0.005m •
You do not need to calculate the error associated with the friction factor. In calculations involving the friction factor, you may assume that there is no error associated with it. •
You may assume that there are no errors associated with parameters describing the characteristics of the fluid or the pipe (except physical dimensions).
Your preview ends here
Eager to read complete document? Join bartleby learn and gain access to the full version
- Access to all documents
- Unlimited textbook solutions
- 24/7 expert homework help
CHBE 264 Manual –
Appendix C Experiment D: Fluids Revised on 11 February 2022
Back to Table of Contents C-2 a)
Error Associated with Major Head Loss for Pipes L-2 to L-6 h
?
=
?
2
− ?
1
??
∆h
?
= |
𝜕h
?
𝜕?
2
∆?
2
| + |
𝜕h
?
𝜕?
1
∆?
1
|
∆h
?
=
(|∆?
2
| + |−∆?
1
|)
??
Yo
u may assume that there is no error associated with ρ and g.
b)
Error Associated with Friction Factor from Major Loss ? = (
?
?
)
2?
𝑣
2
h
?
=
?
2
??
5
h
?
8??
2
∆? = |
𝜕?
𝜕h
?
∆h
?
| + |
𝜕?
𝜕?
∆?| + |
𝜕?
𝜕?
∆?| + |
𝜕?
𝜕?
∆?|
∆? =
?
2
?
8
(|
?
5
??
2
∆h
?
| + |
5?
4
h
?
??
2
∆?| + |−
?
5
h
?
?
2
?
2
∆?| + |−
2?
5
h
?
??
3
∆?|)
Calculate errors associated with the following parameters: a)
Major head loss for pipes L-2 to L-6 b)
Friction factor from major head loss c)
Major head loss for pipe L-7 d)
Minor head loss e)
K-loss coefficient f)
Reynolds number g)
Pipe roughness h)
Flow rate i)
Aggregate correction factor (analytical) j)
Aggregate correction factor (graphical at 95% confidence) k)
Correction factor l)
Predicted time for tank draining The experimental error in this lab is to be computed using partial differentiation
Your preview ends here
Eager to read complete document? Join bartleby learn and gain access to the full version
- Access to all documents
- Unlimited textbook solutions
- 24/7 expert homework help
CHBE 264 Manual –
Appendix C Experiment D: Fluids Revised on 11 February 2022
Back to Table of Contents C-3 c)
Error Associated with Major Head Loss for Pipe L-7 h
?
= ? (
?
?
)
𝑣
2
2?
=
8???
2
?
2
?
5
?
∆h
?
= |
𝜕h
?
𝜕?
∆?| + |
𝜕h
?
𝜕?
∆?| + |
𝜕h
?
𝜕d
∆d| + |
𝜕h
?
𝜕Q
∆Q|
∆h
?
=
8
?
2
?
(|
??
2
?
5
∆?| + |
??
2
?
5
∆?| + |
2???
?
5
∆?| + |−
5???
2
?
6
∆?|)
d)
Error Associated with Minor Head Loss h
?
=
?
2
− ?
1
??
− h
?
∆h
?
= |
𝜕h
?
𝜕?
2
∆?
2
| + |
𝜕h
?
𝜕?
1
∆?
1
| + |
𝜕h
?
𝜕h
?
∆h
?
|
∆h
?
=
(|∆?
2
| + |−∆?
1
|)
??
+ |−∆h
?
|
e)
Error Associated with K-loss Factor K =
?
2
??
4
ℎ
?
8?
2
∆K = |
𝜕K
𝜕?
∆?| + |
𝜕K
𝜕ℎ
?
∆ℎ
?
| + |
𝜕K
𝜕Q
∆Q|
∆K =
?
2
?
8
(|
4?
3
ℎ
?
?
2
∆?| + |
?
4
?
2
∆ℎ
?
| + |−
2?
4
ℎ
?
?
3
∆?|)
f)
Error Associated with Reynolds Number Re =
?𝑣?
𝑝?𝑝?
𝜇
=
4??
??
𝑝?𝑝?
𝜇
∆Re = |
𝜕Re
𝜕?
𝑝?𝑝?
∆?
𝑝?𝑝?
| + |
𝜕Re
𝜕?
∆?|
∆Re = |
−4??
??
𝑝?𝑝?
2
𝜇
∆?
𝑝?𝑝?
| + |
4?
??
𝑝?𝑝?
𝜇
∆?|
You may assume that there is no error associated with μ.
Your preview ends here
Eager to read complete document? Join bartleby learn and gain access to the full version
- Access to all documents
- Unlimited textbook solutions
- 24/7 expert homework help
CHBE 264 Manual –
Appendix C Experiment D: Fluids Revised on 11 February 2022
Back to Table of Contents C-4 g)
Error Associated with Pipe Roughness 𝜀 = 3.7?
𝑝?𝑝?
(10
(
1
−2√?
)
−
2.51
Re√?
)
∆𝜀 = |
𝜕𝜀
𝜕?
𝑝?𝑝?
∆?
𝑝?𝑝?
| + |
𝜕𝜀
𝜕?
∆?| + |
𝜕𝜀
𝜕Re
∆Re|
∆𝜀 = |3.7 (0.1
(
1
2√?
)
−
2.51
Re√?
) ∆?
𝑝?𝑝?
| + |
−
(
3.7 ln(10) ?
𝑝?𝑝?
(0.1)
(
1
2√?
)
4?
1.5
+
4.6435?
𝑝?𝑝?
Re?
1.5
)
∆?|
+ |
9.287?
𝑝?𝑝?
Re
2
√?
∆Re|
h)
Error Associated with Flow Rate ? =
𝑉
?
∆? = |
𝜕?
𝜕𝑉
∆𝑉| + |
𝜕?
𝜕?
∆?|
∆? = |
1
?
∆𝑉| + |
−𝑉
?
2
∆?|
i)
Error Associated with Aggregate Correction Factor (Analytical) ? =
4?
??
𝑡𝑎??
2
√𝑧
∆? = |
𝜕?
𝜕?
∆?| + |
𝜕?
𝜕?
𝑡𝑎??
∆?
𝑡𝑎??
| + |
𝜕?
𝜕𝑧
∆𝑧|
∆? = |
4
??
𝑡𝑎??
2
√𝑧
∆?| + |
−8?
??
𝑡𝑎??
3
√𝑧
∆?
𝑡𝑎??
| + |
−2?
??
𝑡𝑎??
2
𝑧√𝑧
∆𝑧|
j)
Error Associated with Aggregate Correction Factor (Graphical) Please see the excel tutorial on the use of the LINEST function. This tutorial will teach you about how to use the function and find its error. ? =
4?
??
𝑡𝑎??
2
Your preview ends here
Eager to read complete document? Join bartleby learn and gain access to the full version
- Access to all documents
- Unlimited textbook solutions
- 24/7 expert homework help
CHBE 264 Manual –
Appendix C Experiment D: Fluids Revised on 11 February 2022
Back to Table of Contents C-5 ∆? = |
𝜕?
𝜕?
∆?| + |
𝜕?
𝜕?
𝑡𝑎??
∆?
𝑡𝑎??
|
∆? = |
4
??
𝑡𝑎??
2
∆?| + |
−8?
??
𝑡𝑎??
3
∆?
𝑡𝑎??
|
k)
Error Associated with Correction Factor ? =
0.25??
𝑡𝑎??
2
?
0.25??
𝑝?𝑝?
2
√2?
=
?
𝑡𝑎??
2
?
?
𝑝?𝑝?
2
√2?
∆? = |
𝜕?
𝜕?
𝑡𝑎??
∆?
𝑡𝑎??
| + |
𝜕?
𝜕?
𝑝?𝑝?
∆?
𝑝?𝑝?
| + |
𝜕?
𝜕?
∆?|
∆? = |
2?
𝑡𝑎??
?
?
𝑝?𝑝?
2
√2?
∆?
𝑡𝑎??
| + |
−2?
𝑡𝑎??
2
?
?
𝑝?𝑝?
3
√2?
∆?
𝑝?𝑝?
| + |
?
𝑡𝑎??
2
?
𝑝?𝑝?
2
√2?
∆?|
Note that the uncertainty of an average value is the standard deviation of the entire set, which can be obtained using the standard deviation function in Microsoft Excel. l)
Error Associated with Predicted Time for Tank Draining ? =
2(√𝑧
???𝑡?𝑎?
−
√
𝑧
???𝑎?
)
?
∆? = |
𝜕?
𝜕𝑧
???𝑡?𝑎?
∆𝑧
???𝑡?𝑎?
| + |
𝜕?
𝜕𝑧
???𝑎?
∆𝑧
???𝑎?
| + |
𝜕?
𝜕?
∆?|
∆? = |
1
?√𝑧
???𝑡?𝑎?
∆𝑧
???𝑡?𝑎?
| + |
−1
?
√
𝑧
???𝑎?
∆𝑧
???𝑎?
| + |
−2(√𝑧
???𝑡?𝑎?
−
√
𝑧
???𝑎?
)
?
2
∆?|
Your preview ends here
Eager to read complete document? Join bartleby learn and gain access to the full version
- Access to all documents
- Unlimited textbook solutions
- 24/7 expert homework help
CHBE 264 Manual –
Appendix D Experiment D: Fluids Revised on 11 February 2022 Back to Table of Contents D-1 Appendix D: Supplementary Information 1.
Fowler Dial Calipers Calipers are precision measuring tools commonly used for outside, inside, step, and depth measurements. Dial calipers consist of 15 parts: inside and outside measuring jaws, reference edge, dial, lock screw, slider, main scales in centimetres and inches, beam, fixed and sliding jaws, bezel clamp, dial indicators, thumb screw, and depth probe as depicted in Figure D1. The inside jaws are used for inside measurements such as inner diameter while the outside jaws can be used to measure outer diameter, space width, length and object thickness. The outside jaw located at the end of the calipers is fixed to the beam and known as fixed jaw. However, the sliding jaw attached to the slider is mobile. The thumb screw is used to adjust the opening of the measuring jaws and the position of the slider. The lock screw allows the measuring jaws to be secured in place for reading. The depth probe is stored inside the beam and is used to determine hole depth. The two main scales are located on the beam for coarse reading which can be obtained from the reference edge. Conversely, the dial indicators display fine reading; red indicator shows reading in millimetres while black indicator shows reading in inches. The dial indicators rotate inside the dial when the slider is moved along the beam. The bezel clamp locks the calibration setting to ensure precise reading. Figure D1: Fowler Dial Calipers
D1
In this experiment, Fowler 6”/150 mm inch/metric reading dial caliper 52-030-006 is used to measure the inner diameter of the outflow pipe for the draining tank experiment. Reference Edge Outside Jaws Inside Jaws Depth Probe Main Scale in Centimetres Main Scale in Inches Dial Thumb Screw Lock Screw Bezel Clamp Beam Dial Indicator Slider Fixed Jaw Sliding Jaw
Your preview ends here
Eager to read complete document? Join bartleby learn and gain access to the full version
- Access to all documents
- Unlimited textbook solutions
- 24/7 expert homework help
CHBE 264 Manual –
Appendix D Experiment D: Fluids Revised on 11 February 2022 Back to Table of Contents D-2 D1
http://www.fowlerprecision.com/Products/Dial-Calipers/6-150mm-Inch-Metric- Reading-Dial-Caliper-52-030-006.html Taking Measurements Using Dial Calipers Figure D2: Calipers Measurements a) Space Width
D2
b) Inner Diameter
D2
c) Step Distance
D2
d) Hole Depth
D2
D2
http://www3.nd.edu/~jott/Solids/Solids_lab/Lab1/how_to_read_a_dial_caliper.pdf a)
Outside Measurement 1.
Hold the calipers by the beam and use your thumb to turn the thumb screw in the counter-
clockwise direction to widen the measuring jaws a) b) c) d)
Your preview ends here
Eager to read complete document? Join bartleby learn and gain access to the full version
- Access to all documents
- Unlimited textbook solutions
- 24/7 expert homework help
CHBE 264 Manual –
Appendix D Experiment D: Fluids Revised on 11 February 2022 Back to Table of Contents D-3 2.
Ensure that the outside measuring jaws are wider than the object 3.
Place the object in between the outside measuring jaws and turn the thumb screw in the clockwise direction until the jaws touch the edges of the object 4.
Turn the lock screw to lock the measuring jaws in place 5.
Remove the object and read the value b)
Inside Measurement 1.
Hold the calipers by the beam and use your thumb to turn the thumb screw in the clockwise direction to zero the reading 2.
Ensure that the dial indicators are stopped at the 0 mark when the measuring jaws are fully closed 3.
Place the inside measuring jaws into the object and turn the thumb screw in the counter-
clockwise direction until the jaws touch the edges of the hole 4.
Turn the lock screw to lock the measuring jaws in place 5.
Remove the object and read the value c)
Step Measurement 1.
Place the sliding jaws on the upper step of the object and turn the thumb screw until the fixed jaws reach the bottom step (refer to Figure D2) 2.
Ensure that the head of the calipers is perpendicular to the top step 3.
Turn the lock screw to lock the measuring jaws in place 4.
Remove the object and read the value d)
Depth Measurement 1.
Position the depth probe such that the probe is perpendicular to the bottom of the hole and flat against the internal wall of the hole (refer to Figure D2) 2.
Gradually turn the thumb screw until the end of the beam reaches the top of the hole 3.
Turn the lock screw to lock the measuring jaws in place 4.
Remove the object and read the value Reading the Dial Calipers The main scales are divided into 10 subscales as illustrated in Figure D3. Each increment represents 0.100 cm and 0.100 inch for centimeter and inch scales, respectively. However, an increment in dial scales is equivalent to 0.02 mm and 0.001 inch for red and black indicators,
Your preview ends here
Eager to read complete document? Join bartleby learn and gain access to the full version
- Access to all documents
- Unlimited textbook solutions
- 24/7 expert homework help
CHBE 264 Manual –
Appendix D Experiment D: Fluids Revised on 11 February 2022 Back to Table of Contents D-4 respectively. After one complete rotation of the black dial indicator, the reference edge will move by 1 increment or 0.100 inch. In contrary, one complete rotation of the red dial indicator will move the reference edge by 2 increments or 0.200 cm. The combination of the main and dial scales provides a precise reading with 3 decimal places. Figure D3: Main and Dial Scales in Centimeters and Inches Example Reading from Figure D3: a)
Reading in Inches 1.
Read the main scale. The reference edge is in between 1 and 2 inches, so the first digit is 1 or 1.000 inch. 0.100 inch 0.100 cm 0.02 mm 0.001 inch
Your preview ends here
Eager to read complete document? Join bartleby learn and gain access to the full version
- Access to all documents
- Unlimited textbook solutions
- 24/7 expert homework help
CHBE 264 Manual –
Appendix D Experiment D: Fluids Revised on 11 February 2022 Back to Table of Contents D-5 The reference edge passes the second subscale, so the second digit is 2 or 0.200 inch. 2.
Read the dial. The black dial is in between 10 and 20, so the third digit is 1 or 0.010 inch. The black dial is at the eighth subscale, so the fourth digit is 8 or 0.008 inch. Therefore, the inch reading is 1.218 inch. b)
Reading in Centimeters 1.
Read the main scale. The reference edge is in between 3 and 4 cm, so the first digit is 3 or 3.000 cm. The reference edge is on the first subscale, so the second digit is 0 or 0.000 cm.* 2.
Read the dial. The red dial is in between 0.9 and 0, so the third digit is 9 or 0.090 cm. The red dial is at the second subscale, so the fourth digit is 4 or 0.004 cm. Therefore, the centimetre reading is 3.094 cm. *For the main scale only: If the reference edge is on the scale mark (eg. 1.000 cm) and has not completely passed that mark, you must read the number from the scale mark prior to the scale mark that the reference edge is currently on (eg. 0.900 cm).
Your preview ends here
Eager to read complete document? Join bartleby learn and gain access to the full version
- Access to all documents
- Unlimited textbook solutions
- 24/7 expert homework help
Related Documents
Related Questions
bliuzodt to mopolb
9. If machine parts are degreased by means of kerosene as shown in the diagram,
how much kerosene make-up is needed per day? How much kerosene has to enter
the degreasing vat per day? There are about 3 lb of grease per 100 lb of machine
parts, and 60 tons of machine parts are processed each day. Five thousand pounds
of kerosene (the 10% solution) are carried away by the machine parts each day
but drip off and are caught and put back in the degreasing vat. Two hundred
pounds of the 10% solution are lost each day from the vat by evaporation, spillage,
or by being carried away.
arrow_forward
Define the following terms and provide an example in each case
d. Reynolds experience and Reynolds number.
e. Steady and unsteady flow processes.
f. Closed system and control volume.
g. The difference between extensive and intensive properties.
h. Cavitation mechanism and water hammer.
i. Mach number and its dependence on temperature.
j. Fluid viscosity and its dependence on temperature for both liquids and gases.
k. Surface tension and capillary effect.
arrow_forward
1. If 1 gallon of oil = 1.4 therm, how many gallons have been wasted by heat loss in Feb? (1 therm = 100,000 BTU)_____________________________________________________________________________________2. If $1.30 per therm, how much did you waste from house heat loss in Feb?
arrow_forward
Newton's Law of cooling states that the rate at which heat is lost by a heated body is
proportional to the difference in temperature between the body and the surrounding
medium. Match the following statements/phrases with the corresponding item in the
drop down box. Choices in the box
1. In accordance with the stated law obove, we have the equation?
2. If a thermometer is taken outdoors where the temperoture is 5 deg C, from a
room in which the temperature is 20 deg C and the reading drops 10 deg C in one
minute, the working equation is?
3. In the obove problem, separoting the variables and integrating will result to?
4. In the obove problem, how long, in minutes, after its removal from the room will
the reading be 6 deg C?
5. In the obove problem, ofter 30 seconds, whot will be the thermometer reading?
5.2
dT(body temp)/dt = k(Temp of medium - 5)
dr(body temp)/dt = k(Temp of body - Temp of medium)
Temp of body = Cenkt +5
2.5
13.7
dr(body temp)/dt = k(Temp of medium - Temp of body)…
arrow_forward
Three types of fluids stack in an open tank as shown in the plot.
Select the expression of the gage pressure at location 2, P2(gage)=______
A.
B.
C.
D.
patm
arrow_forward
please help me with this
arrow_forward
Three types of fluids stack in an open tank as shown in the plot.
Select the expression of the gage pressure at location 1, P1(gage)=______
A.
Patm
B.
0
C.
101.325 kPa
D.
It can not be determined.
arrow_forward
Which of the following formulas describe the thermal efficiency of a cycle?
Select all that applies.
1 - qin/qout
worknet/qout
worknet/qin
1 - qout/qin
arrow_forward
Not Ai generated please show all steps
arrow_forward
Hello I have two pictures with some questions Id like to get answers to! Short and great explanations please thank you !
arrow_forward
Engineering Thermofluids (GENG-1200-1)
6. A boundary layer is:
a) A thin layer of fluid
(b) A thin layer of fluid in contact with a solid surface that does not move due to fluid
viscosity.
c)
A thin layer of fluid near the solid surface formed by relative motion between the fluid
and surface.
d) None of the above
7. Cavitation can be avoided by:
a) Maintaining the local fluid pressure above the vapor pressure
b) Maintaining the local fluid pressure below the vapor pressure
(c)) Ensuring that the flow is turbulent.
d) Maximizing the temperature of the fluid
8.
An oil droplet with a diameter of 250 µm (Micrometer) and surface tension of 0.030 N/m
experiences a AP of:
a) 240 Pa
b) 480 Pa
c) 1.2 MPa
d) 24 kPa
9. The Bernoulli equation is valid for:
a) Steady, inviscid, and incompressible flow
b) Compressible and incompressible flow
c) Steady, viscous, and incompressible flow
d) Steady, inviscid, and compressible flow
10. The fundamental difference between liquids and gases is:
a) Liquids…
arrow_forward
= 14
15
16
17
18
19
20
21
22
23
24
25
26
A gas storage cylinder in an ordinary chemical laboratory measures 3.9 cm wide and 16. cm high.
This is the label on it.
olo
Contents: N, gas
Pressure: 7.93 atm
If the cylinder is opened and the gas allowed to escape into a large empty plastic bag, what will be the final volume of nitrogen gas, including what's collected in
the plastic bag and what's left over in the cylinder? Write your answer in liters. Round your answer to 2 significant digits.
?
arrow_forward
ased on the corresponding mass flow rates (and NOT the original volumetric flow rates) determine:
a) The mass flow rate of the mixed air (i.e., the combination of the two flows) leaving the chamber in kg/s.
b) The temperature of the mixed air leaving the chamber.
Please use PyscPro software for solving this question.
Notes:
For part (a), you will first need to find the density or specific volume for each state (density = 1/specific volume).
The units the 'v' and 'a' are intended as subscripts:
· kgv = kg_v = kgv = kilogram(s) [vapour]
kga = kg_a =kga = kilogram(s) [air]
arrow_forward
SEE MORE QUESTIONS
Recommended textbooks for you
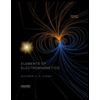
Elements Of Electromagnetics
Mechanical Engineering
ISBN:9780190698614
Author:Sadiku, Matthew N. O.
Publisher:Oxford University Press
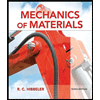
Mechanics of Materials (10th Edition)
Mechanical Engineering
ISBN:9780134319650
Author:Russell C. Hibbeler
Publisher:PEARSON
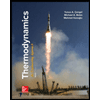
Thermodynamics: An Engineering Approach
Mechanical Engineering
ISBN:9781259822674
Author:Yunus A. Cengel Dr., Michael A. Boles
Publisher:McGraw-Hill Education
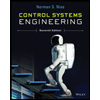
Control Systems Engineering
Mechanical Engineering
ISBN:9781118170519
Author:Norman S. Nise
Publisher:WILEY
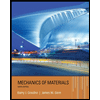
Mechanics of Materials (MindTap Course List)
Mechanical Engineering
ISBN:9781337093347
Author:Barry J. Goodno, James M. Gere
Publisher:Cengage Learning
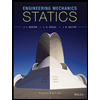
Engineering Mechanics: Statics
Mechanical Engineering
ISBN:9781118807330
Author:James L. Meriam, L. G. Kraige, J. N. Bolton
Publisher:WILEY
Related Questions
- bliuzodt to mopolb 9. If machine parts are degreased by means of kerosene as shown in the diagram, how much kerosene make-up is needed per day? How much kerosene has to enter the degreasing vat per day? There are about 3 lb of grease per 100 lb of machine parts, and 60 tons of machine parts are processed each day. Five thousand pounds of kerosene (the 10% solution) are carried away by the machine parts each day but drip off and are caught and put back in the degreasing vat. Two hundred pounds of the 10% solution are lost each day from the vat by evaporation, spillage, or by being carried away.arrow_forwardDefine the following terms and provide an example in each case d. Reynolds experience and Reynolds number. e. Steady and unsteady flow processes. f. Closed system and control volume. g. The difference between extensive and intensive properties. h. Cavitation mechanism and water hammer. i. Mach number and its dependence on temperature. j. Fluid viscosity and its dependence on temperature for both liquids and gases. k. Surface tension and capillary effect.arrow_forward1. If 1 gallon of oil = 1.4 therm, how many gallons have been wasted by heat loss in Feb? (1 therm = 100,000 BTU)_____________________________________________________________________________________2. If $1.30 per therm, how much did you waste from house heat loss in Feb?arrow_forward
- Newton's Law of cooling states that the rate at which heat is lost by a heated body is proportional to the difference in temperature between the body and the surrounding medium. Match the following statements/phrases with the corresponding item in the drop down box. Choices in the box 1. In accordance with the stated law obove, we have the equation? 2. If a thermometer is taken outdoors where the temperoture is 5 deg C, from a room in which the temperature is 20 deg C and the reading drops 10 deg C in one minute, the working equation is? 3. In the obove problem, separoting the variables and integrating will result to? 4. In the obove problem, how long, in minutes, after its removal from the room will the reading be 6 deg C? 5. In the obove problem, ofter 30 seconds, whot will be the thermometer reading? 5.2 dT(body temp)/dt = k(Temp of medium - 5) dr(body temp)/dt = k(Temp of body - Temp of medium) Temp of body = Cenkt +5 2.5 13.7 dr(body temp)/dt = k(Temp of medium - Temp of body)…arrow_forwardThree types of fluids stack in an open tank as shown in the plot. Select the expression of the gage pressure at location 2, P2(gage)=______ A. B. C. D. patmarrow_forwardplease help me with thisarrow_forward
- Three types of fluids stack in an open tank as shown in the plot. Select the expression of the gage pressure at location 1, P1(gage)=______ A. Patm B. 0 C. 101.325 kPa D. It can not be determined.arrow_forwardWhich of the following formulas describe the thermal efficiency of a cycle? Select all that applies. 1 - qin/qout worknet/qout worknet/qin 1 - qout/qinarrow_forwardNot Ai generated please show all stepsarrow_forward
- Hello I have two pictures with some questions Id like to get answers to! Short and great explanations please thank you !arrow_forwardEngineering Thermofluids (GENG-1200-1) 6. A boundary layer is: a) A thin layer of fluid (b) A thin layer of fluid in contact with a solid surface that does not move due to fluid viscosity. c) A thin layer of fluid near the solid surface formed by relative motion between the fluid and surface. d) None of the above 7. Cavitation can be avoided by: a) Maintaining the local fluid pressure above the vapor pressure b) Maintaining the local fluid pressure below the vapor pressure (c)) Ensuring that the flow is turbulent. d) Maximizing the temperature of the fluid 8. An oil droplet with a diameter of 250 µm (Micrometer) and surface tension of 0.030 N/m experiences a AP of: a) 240 Pa b) 480 Pa c) 1.2 MPa d) 24 kPa 9. The Bernoulli equation is valid for: a) Steady, inviscid, and incompressible flow b) Compressible and incompressible flow c) Steady, viscous, and incompressible flow d) Steady, inviscid, and compressible flow 10. The fundamental difference between liquids and gases is: a) Liquids…arrow_forward= 14 15 16 17 18 19 20 21 22 23 24 25 26 A gas storage cylinder in an ordinary chemical laboratory measures 3.9 cm wide and 16. cm high. This is the label on it. olo Contents: N, gas Pressure: 7.93 atm If the cylinder is opened and the gas allowed to escape into a large empty plastic bag, what will be the final volume of nitrogen gas, including what's collected in the plastic bag and what's left over in the cylinder? Write your answer in liters. Round your answer to 2 significant digits. ?arrow_forward
arrow_back_ios
SEE MORE QUESTIONS
arrow_forward_ios
Recommended textbooks for you
- Elements Of ElectromagneticsMechanical EngineeringISBN:9780190698614Author:Sadiku, Matthew N. O.Publisher:Oxford University PressMechanics of Materials (10th Edition)Mechanical EngineeringISBN:9780134319650Author:Russell C. HibbelerPublisher:PEARSONThermodynamics: An Engineering ApproachMechanical EngineeringISBN:9781259822674Author:Yunus A. Cengel Dr., Michael A. BolesPublisher:McGraw-Hill Education
- Control Systems EngineeringMechanical EngineeringISBN:9781118170519Author:Norman S. NisePublisher:WILEYMechanics of Materials (MindTap Course List)Mechanical EngineeringISBN:9781337093347Author:Barry J. Goodno, James M. GerePublisher:Cengage LearningEngineering Mechanics: StaticsMechanical EngineeringISBN:9781118807330Author:James L. Meriam, L. G. Kraige, J. N. BoltonPublisher:WILEY
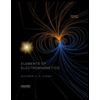
Elements Of Electromagnetics
Mechanical Engineering
ISBN:9780190698614
Author:Sadiku, Matthew N. O.
Publisher:Oxford University Press
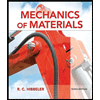
Mechanics of Materials (10th Edition)
Mechanical Engineering
ISBN:9780134319650
Author:Russell C. Hibbeler
Publisher:PEARSON
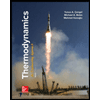
Thermodynamics: An Engineering Approach
Mechanical Engineering
ISBN:9781259822674
Author:Yunus A. Cengel Dr., Michael A. Boles
Publisher:McGraw-Hill Education
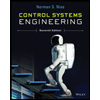
Control Systems Engineering
Mechanical Engineering
ISBN:9781118170519
Author:Norman S. Nise
Publisher:WILEY
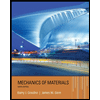
Mechanics of Materials (MindTap Course List)
Mechanical Engineering
ISBN:9781337093347
Author:Barry J. Goodno, James M. Gere
Publisher:Cengage Learning
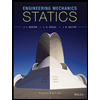
Engineering Mechanics: Statics
Mechanical Engineering
ISBN:9781118807330
Author:James L. Meriam, L. G. Kraige, J. N. Bolton
Publisher:WILEY