Chapter 6 hw edit
pdf
keyboard_arrow_up
School
Mt San Antonio College *
*We aren’t endorsed by this school
Course
8
Subject
Mechanical Engineering
Date
Apr 3, 2024
Type
Pages
5
Uploaded by SuperCheetahMaster783
Madelaine Tew
4/3/2023
HW 5
6.3 A specimen of aluminum having a rectangular cross section 10 mm * 12.7 mm (0.4
in.0.5 in.) is pulled in tension with 35,500 N (8000 lbf) force, producing only elastic
deformation. Calculate the resulting strain
Stress = 35500 / (10*12.7) = 279.53
Strain = 279.53 / 70E3 = 3.99 * 10^-3
6.7 For a bronze alloy, the stress at which plastic deformation begins is 275 MPa (40,000
psi), and the modulus of elasticity is 115 GPa (16.7 106 psi).
(a) What is the maximum load that may be applied to a specimen with a cross-sectional
area of 325 mm2 (0.5 in.2) without plastic deformation?
-
275 * 325 = 89,375
(b) If the original specimen length is 115 mm (4.5 in.), what is the maximum length to
which it may be stretched without causing plastic deformation?
-
115 * (1 + 275/115E3) = 115.28
6.15 A cylindrical specimen of aluminum having a diameter of 19 mm (0.75 in.) and length
of 200 mm (8.0 in.) is deformed elastically in tension with a force of 48,800 N (11,000 lbf).
Using the data contained in Table 6.1, determine the following:
(a) The amount by which this specimen will elongate in the direction of the applied
stress.
-
Area = pi r^2 = Pi (9.5)^2 = 283.53
-
E = youngs = 69E3
-
(48,800 * 200) / (285.53 * 69E3) = 0.50
(b) The change in diameter of the specimen. Will the diameter increase or decrease?
-
-(0.33 * 19 * 0.498) / 200 = -0.0156 which means it will be decreasing
6.18 A cylindrical specimen of a hypothetical metal alloy is stressed in compression. If its
original and final diameters are 20.000 and 20.025 mm, respectively, and its final length is
74.96 mm,
compute its original length if the deformation is totally elastic
. The elastic and
shear moduli for this alloy are 105 GPa and 39.7 GPa, respectively
-
6.21 A cylindrical metal specimen 12.7 mm (0.5 in.) in diameter and 250 mm (10 in.) long
is to be subjected to a tensile stress of 28 MPa (4000 psi); at this stress level, the
resulting deformation will be totally elastic.
(a) If the elongation must be less than 0.080 mm (3.2 10-3 in.), which of the metals in
Table 6.1 are suitable candidates? Why?
-
0.080 / 250 = 3.2E-4
-
28 / 3.2E-4 = 87.5 meaning anything except for aluminum or magnesium. This is
determined when we look at table 6.1
(b) If, in addition, the maximum permissible diameter decrease is 1.2 10-3 mm (4.7 10-5
in.) when the tensile stress of 28 MPa is applied, which of the metals that satisfy the
criterion in part (a) are suitable candidates? Why?
-
Because we are given the max permissible diameter we have to use it to find poisson's
ratio.
-
-1.2E-3 / 12.7 = -9.45E-5
-
Aluminum = (0.33 * 28E6) / (69 * 10E9) = 1.34E-4
-
Magnesium = (0.29 * 28E6) / (45 * 10E9) = 1.80E-4
-
Brass = (0.34 * 28E6) / (97 * 10E9) = 9.81E-5
Copper = (0.34 * 28E6) / (110 * 10E9) = 8.65E-5
Nickel = (0.31 * 28E6) / (207 * 10E9) = 4.19E-5
Steel = (0.30 * 28E6) / (207 * 10E9) = 4.06E-5
Titanium = (0.34 * 28E6) / (107 * 10E9) = 8.90E-5
Tungsten = (0.28 * 28E6) / (407 * 10E9) = 1.93E-5
6.27 A load of 85,000 N (19,100 lbf) is applied to a cylindrical specimen of a steel alloy
(displaying the stress–strain behavior shown in Figure 6.22) that has a cross-sectional
diameter of 15 mm (0.59 in.).
(a) Will the specimen experience elastic and/or plastic deformation? Why?
-
Area = pi (7.5)^2 = 176.71
-
85,000 / 176.71 = 481 When looking at the graph we know that elastic deformation is
before the curve begins while elastic + plastic is during the curve. In this case it would be
both elastic and plastic.
(b) If the original specimen length is 250 mm (10 in.), how much will it increase in length
when this load is applied?
-
250 * 0.0140 = 3.5mm
6.30 A specimen of ductile cast iron having a rectangular cross section of dimensions 4.8
mm 15.9 mm (3/16 in. 5/8 in.) is deformed in tension. Using the load-elongation data
shown in the following table, complete problems (a) through (f)
Area: 0.0048 * 0.0159 = 7.63E-5 m
(a) Plot the data as engineering stress versus engineering strain.
-
Engineering stress = load / area
-
Engineering strain = (Deformed - original length) / original length
Load
Length
Length change
Area
Stress
Strain
0
7.50E-02
0.00E+00
7.63E+05
0
0.00E+00
4740
7.50E-02
2.50E-05
7.63E+05
6.21E-03 3.33E-04
9140
7.51E-02
5.00E-05
7.63E+05
1.20E-02 6.66E-04
12,920
7.51E-02
7.50E-05
7.63E+05
1.69E-02 9.99E-04
16,540
7.51E-02
1.13E-04
7.63E+05
2.17E-02 1.50E-03
18,300
7.52E-02
1.50E-04
7.63E+05
2.40E-02 2.00E-03
20,170
7.52E-02
2.25E-04
7.63E+05
2.64E-02 2.99E-03
22,900
7.54E-02
3.75E-04
7.63E+05
3.00E-02 4.98E-03
25,070
7.55E-02
5.25E-04
7.63E+05
3.29E-02 6.95E-03
26,800
7.58E-02
7.50E-04
7.63E+05
3.51E-02 9.90E-03
28,640
7.65E-02
1.50E-03
7.63E+05
3.75E-02 1.96E-02
30,240
7.80E-02
3.00E-03
7.63E+05
3.96E-02 3.85E-02
31,100
7.95E-02
4.50E-03
7.63E+05
4.08E-02 5.66E-02
31,280
8.10E-02
6.00E-03
7.63E+05
4.10E-02 7.41E-02
30,820
8.25E-02
7.50E-03
7.63E+05
4.04E-02 9.09E-02
29,180
8.40E-02
9.00E-03
7.63E+05
3.82E-02 1.07E-01
27,190
8.55E-02
1.05E-02
7.63E+05
3.56E-02 1.23E-01
24,140
8.70E-02
1.20E-02
7.63E+05
3.16E-02 1.38E-01
18,970
8.87E-02
1.37E-02
7.63E+05
2.49E-02 1.55E-01
Your preview ends here
Eager to read complete document? Join bartleby learn and gain access to the full version
- Access to all documents
- Unlimited textbook solutions
- 24/7 expert homework help
(b) Compute the modulus of elasticity.
-
169.29 - 119.76 / 0.001 - 0.0005 = 99060
(c) Determine the yield strength at a strain offset of 0.002.
-
264.28
(d) Determine the tensile strength of this alloy.
-
409.85
(e) Compute the modulus of resilience.
-
264.28 * 0.003 / 2 = 0.396
(f) What is the ductility, in percent elongation?
-
88.725 - 75 / 75 * 100 = 18.30%
6.37 Determine the modulus of resilience for each of the following alloys:
-
Steel alloy: 550^2 / 400E3 = 0.76
-
Brass alloy: 350^2 / 200E3 = 0.61
-
Aluminum alloy: 250^2 / 140E3 = 0.45
-
Titanium alloy: 800^2 / 220E3 = 2.91
6.42 A tensile test is performed on a metal specimen, and it is found that a true plastic
strain of 0.20 is produced when a true stress of 575 MPa (83,500 psi) is applied; for the
same metal, the value of K in Equation 6.19 is 860 MPa (125,000 psi). Calculate the true
strain that results from the application of a true stress of 600 MPa (87,000 psi).
-
True strain = ln (1 + Engineering strain)
-
True stress = engineering stress ( 1 + engineering strain)
-
575 = 860 *0.20^n -> 0.668 = 0.20^n -> ln0.668 = n ln0.20 n = 0.25
-
600 = 860 * x^0.25 -> 0.698 = x^0.25 x = 0.24
6.50 A steel alloy specimen having a rectangular cross section of dimensions 12.7 mm ×
6.4 mm (0.5 in. × 0.25 in.) has the stress–strain behavior shown in Figure 6.22. If this
specimen is subjected to a tensile force of 38,000 N (8540 lbf) then
(a) Determine the elastic and plastic strain values.
-
Elastic: 38000 / (12.7 * 6.4) = 467.52 ->
467.52 / 207E3 = 0.0023
-
Plastic: 0.010 - 0.0023 = 0.0077
(b) If its original length is 460 mm (18.0 in.), what will be its final length after the load in
part (a) is applied and then released?
-
Final length: (460)(1 + 0.0077) = 463.54
6.51 (a) A 10-mm-diameter Brinell hardness indenter produced an indentation 1.62 mm in
diameter in a steel alloy when a load of 500 kg was used. Compute the HB of this
material.
-
HB = (2 * 500) / (pi * 10 (10 - (10^2 - 1.62^2)^(½)) ) = 241
(b) What will be the diameter of an indentation to yield a hardness of 450 HB when a 500
kg load is used?
-
450 = 500 / diameter of an indentation
-
(100 - (10 - (2*500 / 450*pi*10))^2)^½ = 1.20
6.54 Estimate the Brinell and Rockwell hardnesses for the following:
(a) The naval brass for which the stress–strain behavior is shown in Figure 6.12.
-
450mpa / 3.45 = 130.43
(b) The steel alloy for which the stress–strain behavior is shown in Figure 6.22.
-
500mpa / 3.45 = 144.93
Related Documents
Related Questions
Compound axial member ABC has a uniform diameter of d = 1.45 in. Segment (1) is an aluminum [E₁ = 10,000 ksi] alloy rod with a
length of L₁ = 85 in. Segment (2) is a copper [E₂ = 17,000 ksi] alloy rod with a length of L₂ = 121 in. When axial force P is
applied, a strain gage attached to copper segment (2) measures a normal strain of 2 = 1800 μin./in. in the longitudinal direction.
What is the total elongation of member ABC?
SABC =
i
eTextbook and Media
GO Tutorial
Save for Later
L
Aluminum
in.
B
L₂2
Copper
CP
Attempts: 0 of 5 used Submit Answer
arrow_forward
Part 1
A thin square plate PQRS is symmetrically deformed into the shape shown by the dashed lines in the figure. Assume d = 255 mm,
d₁ = 256.1 mm, and d₂ = 253.6 mm. For the deformed plate, determine
(a) the normal strain of diagonal QS.
(b) the shear strain Yxy at corner P.
d₂
Answer: dos
d
= i
d₁
Undeformed
Calculate the deformation of diagonal QS.
R
Deformed
X
mm
arrow_forward
A rectangular steel block is 300mm in the x direction, 200mm in the y direction and 150mm in the z direction. The block is subjected to a triaxial loading consisting of three uniformly distributed forces as follows: 250kN tension in the x direction, 320kN compression in the y direction and 180kN tension in the z direction. For steel, v=0.30 and E=200,000MPa. Determine the total strain in the x direction due to the forces applied in the three directions.
arrow_forward
Problem F2
stress (ksi)
130
120
110
100
90
80
70
60
50
40
30
20
10
0
0.000 0.025 0.050
0.075 0.100 0.125 0.150 0.175
strain (in/in)
Above you will find the experimental
stress-strain diagram of 1045 steel.
Calculate the permanent set if a
cylindrical specimen with a diameter of
2 in is loaded to the ultimate stress and
then unloaded. Provide your answer in
units of in/in with 3 significant figures
after the decimal. The elastic modulus
of 1045 steel is 29,000 ksi.
arrow_forward
●
Example 3.2
A 60mm diameter solid shaft has a strain gauge mounted at
65° to the axis of the shaft. In service a torque is applied to
the shaft and the strain gauge reads 200 x 10-6. Calculate
the value of the torque if the shaft is made from steel with E
= 207 GPa and v = 0.3.
(BC&A question 11.18)
Strain Transformations
Mechanical Engineering
Mechanics of Materials 2
Solution 3.2
Applied torque alone will produce only shear stress/strain
in the directions parallel and perpendicular to the torque.
The strain gauge is mounted at 65° to the axis of the shaft.
Strain Transformations
Mechanical Engineering
Mechanics of Materials 2
Now
Strain
gauge
From the strain circle
65⁰
Strain Transformations
Note that for circular shaft
4
D
J = ² (2) ²*
33
Dr PJ Martin
Lecture Notes
34
Dr PJ Martin
Lecture Notes
35
arrow_forward
On the free surface of a component, a
strain rosette was used to obtain the following normal strain
data: €a = 300µɛ, ɛp = 400µs, and Ec = 200µe. Calculate
the normal and shear strains in the x-y plane.
arrow_forward
Please show each and every step in detail. Dont miss any steps and highlight the final answer. Thanks!
arrow_forward
Problem 8. Re-write the strain compatibility condition
€22,33 + €33,22
in the engineering notation.
= 2 e23,23
arrow_forward
Q3
arrow_forward
Compound axial member ABC has a uniform diameter of d=1.45 in. Segment (1) is an aluminum [E1=10,000 ksi] alloy rod with a length of L1=88 in. Segment (2) is a copper [E2=17,000 ksi] alloy rod with a length of L2=128 in. When axial force P is applied, a strain gage attached to copper segment (2) measures a normal strain of ε2=2200 μin./in. in the longitudinal direction. What is the total elongation of member ABC?
answer is in inches
arrow_forward
My answer is displayed and incorrect. Please give answer in ksi.
arrow_forward
400
350
300
250
200
150
100
50
0.002
0.004
0.006
0.008
0.01
Strain
Stress (MPa)
arrow_forward
124,000s
o(2)
0 s85 0.03 (o in MPa)
1+ 300ɛ
(a) Find the axial normal strain in the cable and its
elongation due to the load W = 6.8 kN.
(b) If the forces are removed, what is the permanent
set of the cable?
Hint: Start with constructing the stress-strain dia-
gram and determine the modulus of elasticity, E, and
the 0.2% offset yield stress.
D
2 m
A 1.5 m
B
1.5 m
E
m--1 m-
0.75 m
0.25 m
W = 6.8 kN
arrow_forward
Analyse the differences between the 2 attached stress-strain curves for 0.9% carbon steel and 0.15% carbon steel.
arrow_forward
SEE MORE QUESTIONS
Recommended textbooks for you
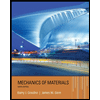
Mechanics of Materials (MindTap Course List)
Mechanical Engineering
ISBN:9781337093347
Author:Barry J. Goodno, James M. Gere
Publisher:Cengage Learning
Related Questions
- Compound axial member ABC has a uniform diameter of d = 1.45 in. Segment (1) is an aluminum [E₁ = 10,000 ksi] alloy rod with a length of L₁ = 85 in. Segment (2) is a copper [E₂ = 17,000 ksi] alloy rod with a length of L₂ = 121 in. When axial force P is applied, a strain gage attached to copper segment (2) measures a normal strain of 2 = 1800 μin./in. in the longitudinal direction. What is the total elongation of member ABC? SABC = i eTextbook and Media GO Tutorial Save for Later L Aluminum in. B L₂2 Copper CP Attempts: 0 of 5 used Submit Answerarrow_forwardPart 1 A thin square plate PQRS is symmetrically deformed into the shape shown by the dashed lines in the figure. Assume d = 255 mm, d₁ = 256.1 mm, and d₂ = 253.6 mm. For the deformed plate, determine (a) the normal strain of diagonal QS. (b) the shear strain Yxy at corner P. d₂ Answer: dos d = i d₁ Undeformed Calculate the deformation of diagonal QS. R Deformed X mmarrow_forwardA rectangular steel block is 300mm in the x direction, 200mm in the y direction and 150mm in the z direction. The block is subjected to a triaxial loading consisting of three uniformly distributed forces as follows: 250kN tension in the x direction, 320kN compression in the y direction and 180kN tension in the z direction. For steel, v=0.30 and E=200,000MPa. Determine the total strain in the x direction due to the forces applied in the three directions.arrow_forward
- Problem F2 stress (ksi) 130 120 110 100 90 80 70 60 50 40 30 20 10 0 0.000 0.025 0.050 0.075 0.100 0.125 0.150 0.175 strain (in/in) Above you will find the experimental stress-strain diagram of 1045 steel. Calculate the permanent set if a cylindrical specimen with a diameter of 2 in is loaded to the ultimate stress and then unloaded. Provide your answer in units of in/in with 3 significant figures after the decimal. The elastic modulus of 1045 steel is 29,000 ksi.arrow_forward● Example 3.2 A 60mm diameter solid shaft has a strain gauge mounted at 65° to the axis of the shaft. In service a torque is applied to the shaft and the strain gauge reads 200 x 10-6. Calculate the value of the torque if the shaft is made from steel with E = 207 GPa and v = 0.3. (BC&A question 11.18) Strain Transformations Mechanical Engineering Mechanics of Materials 2 Solution 3.2 Applied torque alone will produce only shear stress/strain in the directions parallel and perpendicular to the torque. The strain gauge is mounted at 65° to the axis of the shaft. Strain Transformations Mechanical Engineering Mechanics of Materials 2 Now Strain gauge From the strain circle 65⁰ Strain Transformations Note that for circular shaft 4 D J = ² (2) ²* 33 Dr PJ Martin Lecture Notes 34 Dr PJ Martin Lecture Notes 35arrow_forwardOn the free surface of a component, a strain rosette was used to obtain the following normal strain data: €a = 300µɛ, ɛp = 400µs, and Ec = 200µe. Calculate the normal and shear strains in the x-y plane.arrow_forward
- Compound axial member ABC has a uniform diameter of d=1.45 in. Segment (1) is an aluminum [E1=10,000 ksi] alloy rod with a length of L1=88 in. Segment (2) is a copper [E2=17,000 ksi] alloy rod with a length of L2=128 in. When axial force P is applied, a strain gage attached to copper segment (2) measures a normal strain of ε2=2200 μin./in. in the longitudinal direction. What is the total elongation of member ABC? answer is in inchesarrow_forwardMy answer is displayed and incorrect. Please give answer in ksi.arrow_forward400 350 300 250 200 150 100 50 0.002 0.004 0.006 0.008 0.01 Strain Stress (MPa)arrow_forward
arrow_back_ios
SEE MORE QUESTIONS
arrow_forward_ios
Recommended textbooks for you
- Mechanics of Materials (MindTap Course List)Mechanical EngineeringISBN:9781337093347Author:Barry J. Goodno, James M. GerePublisher:Cengage Learning
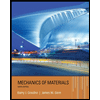
Mechanics of Materials (MindTap Course List)
Mechanical Engineering
ISBN:9781337093347
Author:Barry J. Goodno, James M. Gere
Publisher:Cengage Learning