Reference Procedure - MEMS Mask 2 (Lab 9)
pdf
keyboard_arrow_up
School
University of Florida *
*We aren’t endorsed by this school
Course
5354L
Subject
Mechanical Engineering
Date
Apr 3, 2024
Type
Pages
5
Uploaded by pepsicoke28
EEE5354L: Semiconductor Device Fabrication Laboratory (Fall 2023) Reference Procedure: Photolithography #2 and BOE 1.
Pre-Lab Questions 1.1.
What is the purpose of Mask #2? 1.2.
Your TA deposited Cr followed by Ni on the wafer and performed lift-off. What is the purpose of these metals? 1.1.
What are the rules for using BOE? 2.
Laboratory Procedure 2.1.
TA: Make sure there is enough AZ1512 and BOE for the lab. 2.2.
TA: Set up the spin coater as was done in previous labs 2.3.
TA: Set the hotplate to 112ºC for the pre-bake. 2.4.
Remember to take pictures of your wafers throughout the lab! 2.5.
Using the Filmetrics, measure the thickness of the oxide in two places. One should be an area that has just SOG, such as the center, and the other should be an area with SOG and thermal oxide. 2.6.
Bake the wafers on the hotplate for 5-10 minutes at 112°C. This drives out water from the wafers, creating a hydrophobic surface that is needed for good photoresist adhesion. In very precise processes (critical lengths under 20μm), an additional process called HMDS [1] is used to create a very hydrophobic surface. 2.7.
Use aluminum foil to cover the inside of the spinner for easy cleanup 2.8.
Insert the vacuum chuck into the spinner port 2.9.
Turn on the vacuum pump to the spinner 2.10.
Turn on the spinner controller 2.11.
Using a dummy wafer, set the spin speed for the spinner to 1800 RPM a.
Place dummy wafer on the vacuum chuck b.
Hit foot pedal (this pulls vacuum and starts spinning) c.
Adjust the control knob to set the spin speed d.
Either click the foot pedal to stop or wait for wafer to stop spinning e.
Set the spin time knob to 30 seconds f.
Remove dummy wafer from vacuum chuck g.
If the wafer does not spin, have the TA remove the chuck and check for a black, rubber ring inside of it. If the ring is not there, there may be some near the spin-
coater. If help is needed, contact one of the NRF staff. 2.12.
Remove one wafer from the hotplate and place on the metal on the side of the spinner. This allows the wafer to cool quickly in about 10 seconds.
EEE5354L Reference Procedure Photopatterning and BOE 2 2.13.
Spin AZ1512 photoresist on the wafer a.
Place wafer on vacuum chuck as close to centered as possible b.
Click foot pedal to start spinning c.
Check if the wafer is centered well enough. If not, stop the spinning, adjust the wafer, and try again d.
Once wafer is centered, stop the spinning e.
Use a pipette to suck up a small amount of photoresist (consult your TA for how much is sufficient). Squeeze the pipette bulb before inserting into the photoresist to prevent bubbles f.
Start spinning the wafer g.
While the wafer is spinning dispense the photoresist in a steady stream with the pipette vertical over the center of the wafer. Do not try and get all the photoresist out by squeezing the pipette bulb multiple times. If the resist drips onto your water, it will dry unevenly creating a bullseye pattern. This pattern will limit the resolution you can achieve when exposing the photoresist. However, in our process, there is no need for particularly high resolution, so bullseye patterns are ok and do not need to be redone. h.
Monitor the spinning process to completion. You will see the color of the resist rapidly change from red to green and back again many times. This indicates that the resist is thinning (different wavelengths of light are resonating in the resist). At some point, the color will remain constant. After several seconds of constant color, it is usually ok to stop the spinning process. However, the extra few seconds to create a repeatable process are more important so allow the spinner to spin the whole time. 2.14.
Softbake/prebake the wafer for 120 seconds at 112°C on the hotplate 2.15.
Repeat steps 2.11-2.13 for all the wafers 2.16.
Turn off the vacuum pump for the spinner 2.17.
Turn on the vacuum pump for the mask aligner 2.18.
Unscrew and remove the mask holder 2.19.
Align the mask (mask 2 provided by your TA) to the guides on the mask holder with the non-
shiny side facing up (this will be the side in contact with your wafers) 2.20.
Flip the vacuum switch to pull vacuum on the mask 2.21.
Using your hand as a catch in case the vacuum is not good enough, flip the mask holder and load it back in the aligner, then screw it back in place. The mask holder may be difficult to lift as the opening on the back of the mask may also be under vacuum. If this is the case, carefully slide the holder to the edge of the table to release the vacuum behind the mask. 2.22.
Set the lamp power supply to output the lamp power 2.23.
Without a wafer loaded, press the green button to begin an exposure and check the lamp’s power (units are mW
/cm
2
)
EEE5354L Reference Procedure Photopatterning and BOE 3 2.24.
Calculate the time needed for a complete exposure based on the exposure dose of 110 mJ/cm
3
per micron thickness
. This will depend on the lamp’s power. A few seconds are added to overexpose the photoresist. 2.25.
Set the exposure time on the front of the aligner, adding a few seconds from the calculated time to ensure the photoresist is fully exposed in places where it may be a little thicker. 2.26.
Ensure that all three micrometers (x, y, and θ) are all approxim
ately in their middle position. 2.27.
Load a wafer onto the sliding wafer holder and align it to the reference mark 2.28.
Slide the wafer holder slowly into the aligner being sure not to bump it at the end (this could shift your wafer) 2.29.
Attach the phone holder to one of the mask aligner’s eyepieces
, and put your phone in so that you can see through the camera on your phone. 2.30.
Use the microscope to inspect the mask and wafer. The microscope has pneumatic brakes in the x and y directions, which are released with their corresponding buttons on the microscope, control lever. Do not try to move the microscope in either direction without pressing the button to release the brakes as this may damage the system. 2.31.
Align your wafer using the alignment marks on the left and right of the center box. You may need to bring the wafer close to being in contact with the mask. Do not move the wafer if the contact light is lit, or you will smear photoresist on the mask. 2.32.
Once you think your wafer is aligned, bring the wafer into contact with the mask. Is it still aligned? 2.33.
Have the TA check the alignment before you expose the wafer. 2.34.
Press the green button to expose the sample. Do not look at the sample while it is being exposed (UV is harmful to your eyes)
. Does the power of the lamp as reported by the lamp power supply register the same as before? Why or why not? 2.35.
Once the exposure is completed, rotate the second lever on the left side of the aligner back to its original position 2.36.
Slide the first lever towards you to its original position 2.37.
Slowly slide the sample holder out of the aligner and remove the wafer 2.38.
Repeat steps 2.25-2.36 for all the wafers 2.39.
Unload the mask in the same manner as it was loaded 2.40.
Turn off the vacuum to the mask aligner 2.41.
In the fume hood, pour the resist developer into one of the shallow glass beakers 2.42.
Fill the other with DI water 2.43.
Develop each of the wafers for 75 seconds a.
Submerge the wafer in the developer and start the timer b.
Very gently swish the developer. You are not trying to add energy to the development process (as in an ultrasonic bath), just refreshing the developer at the surface of the photoresist
Your preview ends here
Eager to read complete document? Join bartleby learn and gain access to the full version
- Access to all documents
- Unlimited textbook solutions
- 24/7 expert homework help
EEE5354L Reference Procedure Photopatterning and BOE 4 c.
When the timer goes off, remove the wafer and immediately submerge in the DI water. 2.44.
Clean the wafers using DI water. First immerse the wafers in a large beaker and then place the beaker under a running DI water faucet. Make sure the water is running at a steady pace, but not too fast! This process washes out developer from tiny pockets without damaging patterns, and works well for water-soluble developers. 2.45.
Dry the wafers using the nitrogen gun. Since there is now a pattern, do not have the nitrogen blowing too hard! 2.46.
Once everyone’s wafers are developed, run the wafers through the plasma O
2
asher for 15-
30 seconds to clean them. This is commonly known as a “descum” process, and is performed to clear the oxide surface of residue that might interfere with later processes. 2.47.
Post-bake the wafers for 5 minutes on the hot plate at 112 °C. This hardens the photoresist to make it more resistant to peeling and other effects that might occur during etching. 2.48.
Fill one of the plastic tubs 2/3 full with DI water and place it in the etch tray inside the fume hood. This is the rinse tub 2.49.
Place the second plastic tub in the etch tray directly next to the rinse tub. This is the etch tub. A small, Teflon beaker that can fit two wafers is also acceptable, and may work better. The beaker would need less BOE. 2.50.
Wearing just the nitrile gloves get the BOE bottle out of chemical storage by grasping the handle on the bottle jacket 2.51.
Lock a wafer in each of the plastic single-wafer holders. These holders are not damaged by BOE, and allow us to move the wafers around without breaking them. 2.52.
Put on the neoprene suit, neoprene gloves and face mask over your lab coat and nitrile gloves 2.53.
Carefully pour the BOE into the etch tub to a depth of about 1cm (or if using a beaker, a little more than 5 cm or 2 inches) using only the actual bottle handle. Leave the BOE bottle in the bottle jacket in the fume hood 2.54.
Slowly submerge the wafer into the BOE for 2 minutes to remove the oxide that is exposed by the pattern. There will be some undercut in areas with thinner oxide. 2.55.
Repeat etching as needed, using the filmetrics to measure the oxide. 2.56.
After the etch is completed, carefully remove the wafer and holder, allowing as much BOE to drip off WITHOUT trying to shake it off, and submerge the wafer and holder completely in the rinse tub 2.57.
Allow the wafer and holder 5 minutes to dilute the BOE. 2.58.
While still wearing the neoprene suit, remove the wafer and holder allowing the rinse to drip off the wafer. 2.59.
Place the wafer and holder into a rinse beaker. 2.60.
Take the wafer and holder to the DI water faucet and thoroughly rinse including the hands of the neoprene gloves. This will dilute remaining BOE in small valleys while also not being too harsh on the pattern.
EEE5354L Reference Procedure Photopatterning and BOE 5 2.61.
Place the wafer aside. 2.62.
Inspect the neoprene suit for any wetness that could be splashed BOE etchant. 2.63.
While wearing the neoprene gloves, again wash the gloves thoroughly 2.64.
Dry with paper towels, which can be disposed in the regular trash (the HF has been sufficiently diluted to be safe) 2.65.
Remove the neoprene gloves, neoprene suit, and face mask 2.66.
Inspect the wafer under the microscope. Try to estimate how much undercut there is (it is ok to have a little undercut, as long as the PR isn’t peeling)
2.67.
Use the Filmetrics to measure the oxide thickness. There may be some error due to the photoresist. 2.68.
Repeat etching as needed. 2.69.
While wearing the HF PPE, carefully pour the contents of the etch tub into the HF waste bottle 2.70.
Wash the etch tub and the rinse tub with water, allowing the tubs to completely fill at least three times to sufficiently dilute and remaining HF. Then place them on the drying rack 2.71.
Clean up the lab! 2.72.
Make sure the probe station, microscope lights, hotplate, and Filmetrics light are turned off! 3.
Post-Lab Questions These are suggested questions to help guide you when writing your lab report. Do not simply answer these questions as your report. Use the posted sample lab report as a guide and incorporate your data as well as your in-lab discussions with your TA to write your report. Remember, every lab member must contribute to every lab report. 3.1.
How can we improve the alignment accuracy? 3.2.
Are the alignment marks easy to use? 3.3.
How might misalignment affect the MEMS devices (hint: think about why the PR needs to be wider than the metal)? 3.4.
(Answer only if etching was done in your lab) Were there any accidents with BOE? 4.
Recommended References and Websites None this week
Related Documents
Related Questions
What type of CAD software could be used to test the medical scaffold made out of TPU that will be printed using stereolithography (SLA). The medical scaffold will be surgically implanted around the pancreas to enable the infusion of Islet beta cells which are encapsulated within the scaffold to provide diabetic patients with a functional pancreas.
E.g. hydrostatic pressure testing/torsion tests
What other type of physical testings should be taken? E.g. Brunauer–Emmett–Teller (BET) test to check the porosity of the material
arrow_forward
26)
arrow_forward
Question 4
The following diagram shows the basic structure of the gamma camera used for medical imaging
to data-logger
and computer
Photomultiplier
tube
Sodium iodide
crystal
Lead grating
Describe how the gamma camera detects gamma rays allowing the production of images.
[Suggested word count 130] [2.1]
arrow_forward
The title of our study is "Design and Fabrication of an Agricultural Spraying Attachment for
an Autonomous Rover"
we need help in the machine design part of our study, specifically Pump selection, battery
selection, and center of gravity computation
Rover weight capacity 35 kilo grams (payload)
Rover measurements:
Wheel distance - 14.5 inches and 8.5 inches
Rover platform size (width & length) 14.4 inches x 10.4 inches
Height- 15.8 inches
arrow_forward
CNC vs additive Manufactoring
arrow_forward
"Design and Fabrication of an Agricultural Spraying Attachment foran Autonomous Rover"we need help in the machine design part of our study, specifically Pump selection, batteryselection, and center of gravity computation.
Rover weight capacity 35 kilo grams (payload)Rover measurements:Wheel distance - 14.5 inches and 8.5 inchesRover platform size (width & length) 14.4 inches x 10.4 inchesHeight- 15.8 inches.
....help it
arrow_forward
Number 3
arrow_forward
The title of our study is "Design and Fabrication of an Agricultural Spraying Attachment for an Autonomous Rover" we need help in the machine design part of our study, specifically Pump selection, battery selection, and center of gravity computation I already sent you the image of the rover Rover weight capacity 35 kilo grams (payload) Rover measurements: Wheel distance - 14.5 inches and 8.5 inches Rover platform size (width & length) 14.4 inches x 10.4 inches Height- 15.8 inches. Water tank selection More or less 25 liters *For tank selection we need to justify the size with the center of gravity, proving that is the maximum dimension or liters of the tank because the center of gravity will be higher making the rover prone to toppling Pump selection *Our sprayer design has two nozzles which splits using a tee splitter, we need to find the size of the pump to obtain the same discharge rate of a normal sprayer. A normal sprayer has a 12V pump and a pressure from 0.2 to 0.45 mpa…
arrow_forward
MECT361
Mechatronics Components and Instrumentation
8.1. Why is it not possible to connect sensors such as thermocouples, strain gages, and
accelerometers directly to a digital computer or microprocessor?
PLEASE GIVE ME THE REFRENCE
I Will get zero if you didn't put the refrence
arrow_forward
MECT361
Mechatronics Components and Instrumentation
PLEASE GIVE ME THE short answer and wite it by keyword
thanks
arrow_forward
Problem 2:
Review the below link, and choose 3 practical examples to solve structural/performance-based issues using
finite element product. Discuss what you understand from these examples. Use your own words.
https://www.hitechfea.com/fea-projects.html
hitech
Since
Your Partner in Digital Excellence 1992
SERVICES ✓ PROJECTS ✓
» FEA Projects
CLIENTS
FEA shortens the Design
Cycle for Thermal Radiation
Detector System for Power
Plant
BLOG
ABOUT US CONTACT US
Finite Element Analysis - FEA Projects / Case Studies
Please review few of the FEA projects, FEA case studies and FEA work samples that represent the FEA
solutions HiTech FEA engineers have provided to our global clientele from different industries.
Simulation using ANSYS
Professional NLS helps to
reduce Product Development
Cycle
Effective Static Structural
Services conducting
Structural Seismic Analysis of
RTO System Base
arrow_forward
Please write me a detailed answer in the following question. It is URGENT.
Thank you in advance.
arrow_forward
Multiple choice questions, please help thank you!!
1. The chemical potential (μ) of smaller size clusters is bigger than that of bigger size clusters because of
(a) their small size
(b) the fewer number of atoms in them
(c) surface area is smaller
(d) their surface is more curved
2. Which of these characteristics would you associate with SEM:
A surface imaging tool
Maintained under vacuum
Provides imaging and compositional data
Uses a scanned electron beam
All of the above
3. Secondary electrons (SE) are best described as
Low energy electrons from the sample surface
High energy electrons from the sample surface
Low energy primary beam electrons
High energy primary beam electrons
4. Atomic force microscopy (AFM) is the most widely used form of scanning probe microscopes for the characterization of nanomaterials since it require:
(a) electrically conductive and optically transparent samples
(b) neither electrically conductive nor optically transparent samples
(c) electrically…
arrow_forward
Multiple-Choice Questions
In 4D printing, what is the fourth dimension?
A. Space
B. Movement
C. Time
D. Material
What inspired the team at the MIT self-assembly lab to conceive the Autonomous
Mass Assembly concept?
A. The natural growth of viruses
B. Japanese architecture
C.
Islamic patterns in traditional ornaments
D. The movie "Avatar"
Which of the following are possible applications of 4D printing? Select all correct
answers.
A. Smart water pipes
B. Self-assembled structures
C. Ready-made electronic devices
D. Superior sound systems
What activating energies are used in the 4D products presented in the lesson?
A. Heat
B. Water
C. Microwave
D. Sound-waves
arrow_forward
Digital linage Processin
arrow_forward
Plz don't use chatgpt
arrow_forward
3. Design a Voltaic cell in which the addition of solid NaCl to the cathode cell will cause the voltage to
decrease. Label the diagram below and explain why the addition of NaCl(s) reduces the voltage.
KNO
anode metal
_cathode metal
anode solution
cathode solution
overall balanced equation:
4. Write the balanced overall equation for a combination of metals and standard solutions whose anode
[ion] increases at half the rate that the cathode [ion] decreases as the cell runs. Use the circles below to
draw a particulate view of what is occurring at the surface of each electrode.
Overall equation:
cathode
anode
solution
solution
cathode
anode
metal
metal
Page
arrow_forward
SEE MORE QUESTIONS
Recommended textbooks for you
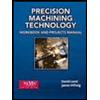
Precision Machining Technology (MindTap Course Li...
Mechanical Engineering
ISBN:9781285444543
Author:Peter J. Hoffman, Eric S. Hopewell, Brian Janes
Publisher:Cengage Learning
Related Questions
- What type of CAD software could be used to test the medical scaffold made out of TPU that will be printed using stereolithography (SLA). The medical scaffold will be surgically implanted around the pancreas to enable the infusion of Islet beta cells which are encapsulated within the scaffold to provide diabetic patients with a functional pancreas. E.g. hydrostatic pressure testing/torsion tests What other type of physical testings should be taken? E.g. Brunauer–Emmett–Teller (BET) test to check the porosity of the materialarrow_forward26)arrow_forwardQuestion 4 The following diagram shows the basic structure of the gamma camera used for medical imaging to data-logger and computer Photomultiplier tube Sodium iodide crystal Lead grating Describe how the gamma camera detects gamma rays allowing the production of images. [Suggested word count 130] [2.1]arrow_forward
- The title of our study is "Design and Fabrication of an Agricultural Spraying Attachment for an Autonomous Rover" we need help in the machine design part of our study, specifically Pump selection, battery selection, and center of gravity computation Rover weight capacity 35 kilo grams (payload) Rover measurements: Wheel distance - 14.5 inches and 8.5 inches Rover platform size (width & length) 14.4 inches x 10.4 inches Height- 15.8 inchesarrow_forwardCNC vs additive Manufactoringarrow_forward"Design and Fabrication of an Agricultural Spraying Attachment foran Autonomous Rover"we need help in the machine design part of our study, specifically Pump selection, batteryselection, and center of gravity computation. Rover weight capacity 35 kilo grams (payload)Rover measurements:Wheel distance - 14.5 inches and 8.5 inchesRover platform size (width & length) 14.4 inches x 10.4 inchesHeight- 15.8 inches. ....help itarrow_forward
- Number 3arrow_forwardThe title of our study is "Design and Fabrication of an Agricultural Spraying Attachment for an Autonomous Rover" we need help in the machine design part of our study, specifically Pump selection, battery selection, and center of gravity computation I already sent you the image of the rover Rover weight capacity 35 kilo grams (payload) Rover measurements: Wheel distance - 14.5 inches and 8.5 inches Rover platform size (width & length) 14.4 inches x 10.4 inches Height- 15.8 inches. Water tank selection More or less 25 liters *For tank selection we need to justify the size with the center of gravity, proving that is the maximum dimension or liters of the tank because the center of gravity will be higher making the rover prone to toppling Pump selection *Our sprayer design has two nozzles which splits using a tee splitter, we need to find the size of the pump to obtain the same discharge rate of a normal sprayer. A normal sprayer has a 12V pump and a pressure from 0.2 to 0.45 mpa…arrow_forwardMECT361 Mechatronics Components and Instrumentation 8.1. Why is it not possible to connect sensors such as thermocouples, strain gages, and accelerometers directly to a digital computer or microprocessor? PLEASE GIVE ME THE REFRENCE I Will get zero if you didn't put the refrencearrow_forward
- MECT361 Mechatronics Components and Instrumentation PLEASE GIVE ME THE short answer and wite it by keyword thanksarrow_forwardProblem 2: Review the below link, and choose 3 practical examples to solve structural/performance-based issues using finite element product. Discuss what you understand from these examples. Use your own words. https://www.hitechfea.com/fea-projects.html hitech Since Your Partner in Digital Excellence 1992 SERVICES ✓ PROJECTS ✓ » FEA Projects CLIENTS FEA shortens the Design Cycle for Thermal Radiation Detector System for Power Plant BLOG ABOUT US CONTACT US Finite Element Analysis - FEA Projects / Case Studies Please review few of the FEA projects, FEA case studies and FEA work samples that represent the FEA solutions HiTech FEA engineers have provided to our global clientele from different industries. Simulation using ANSYS Professional NLS helps to reduce Product Development Cycle Effective Static Structural Services conducting Structural Seismic Analysis of RTO System Basearrow_forwardPlease write me a detailed answer in the following question. It is URGENT. Thank you in advance.arrow_forward
arrow_back_ios
SEE MORE QUESTIONS
arrow_forward_ios
Recommended textbooks for you
- Precision Machining Technology (MindTap Course Li...Mechanical EngineeringISBN:9781285444543Author:Peter J. Hoffman, Eric S. Hopewell, Brian JanesPublisher:Cengage Learning
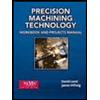
Precision Machining Technology (MindTap Course Li...
Mechanical Engineering
ISBN:9781285444543
Author:Peter J. Hoffman, Eric S. Hopewell, Brian Janes
Publisher:Cengage Learning