MEE 324 Lab 1
docx
keyboard_arrow_up
School
Arizona State University, Tempe *
*We aren’t endorsed by this school
Course
324
Subject
Mechanical Engineering
Date
Apr 3, 2024
Type
docx
Pages
7
Uploaded by ColonelMusic7302
Lab 1: Material Characterization
Fabian Ameen
Lab Number: Thursday 10:30 - 11:35 AM
Date of Experiment: 1/25/2024
Due Date: 2/9/2024
Abstract:
This lab experiment aimed to characterize the mechanical properties of plain carbon steel and aluminum 2024 specimens through tensile testing. A loading machine applied axial tensile load on bone-shaped specimens, with load and displacement data collected using a load cell and strain gauge. Displacement was maintained at a constant rate of 1 mm/min until complete fracture. Through the experimental data the Young’s Modulus (E), yield strength (S
Y
), ultimate tensile strength (S
UTS
), % elongation, percentage of reduction of area, fracture strength (S
F
), and power-law plasticity coefficients can be obtained. Stress-strain curves were plotted, utilizing linear regression and zero shift to eliminate non-meaningful data. Data Analysis:
The first step of the lab was to take measurements of both dog-bone samples to determine the initial length and diameter. The samples had fixed attachment points on both ends which were measured (L
1 and L
2
) and then subtracted from the total length of the sample (L
3
) to determine the true initial length of the sample. The measurements were all taken three times and then averaged to compensate for measurement errors. The gathered data is shown in
Figure 1.
Aluminum 2024 (mm)
Measurement
L
1
L
2
L
3,o
L
3,i
d
o
d
i
1
9.26
7.57
47.98
50.37
2.51
2.05
2
9.44
7.51
48.04
50.41
2.52
2.39
3
9.16
7.72
48.14
50.15
2.53
2.26
AVG
9.29
7.6
48.05
50.31
2.52
2.23
Carbon Steel (mm)
Measurement
L
1
L
2
L
3,o
L
3,i
d
o
d
i
1
8.65
9.12
50.14
52.75
2.49
1.81
2
8.73
9.2
49.21
52.81
2.51
1.52
3
8.59
9.15
49.15
52.79
2.54
1.66
AVG
8.66
9.16
49.5
52.78
2.51
1.66
Figure 1 Lengths and diameter of samples to be tested.
After measuring the initial length, the samples were put under load in the extensometer and the load applied (in kN) and the elongation (in mm) were recorded as the load was increased until failure was reached. From this data the stress and strain of both samples can be calculated and plotted as shown in Figure 2 & 3
0
0.02
0.04
0.06
0.08
0.1
0.12
0
0.05
0.1
0.15
0.2
0.25
0.3
0.35
0.4
Engineering Stress-Strain Aluminum 2024
Engineering Strain
Engineering Stress
Figure 2: Engineering Stress-Strain curve of Aluminum 2024 sample
0
0.05
0.1
0.15
0.2
0.25
0
0.1
0.2
0.3
0.4
0.5
0.6
0.7
Engineering Stress-Strain Carbon Steel
Engineering Strain
Engineering Stress
Figure 3: Engineering Stress-Strain curve of Carbon Steel sample
Performing a linear regression on the linear portion of both curves (before the yield point) gives an estimate for the Young’s Modulus of both samples. Using excel, a value of 85.13 GPa was obtained for aluminum and 217.74 GPa for carbon steel.
By examining the Stress-Strain curves of both the aluminum and carbon steel the yield strength, ultimate tensile strength, and fracture strength of both samples can be determined.
Your preview ends here
Eager to read complete document? Join bartleby learn and gain access to the full version
- Access to all documents
- Unlimited textbook solutions
- 24/7 expert homework help
Yield strength can be found by looking at the max load within the elastic range for steel and by using young’s modulus with an offset of 0.002 for aluminum, the maximum total load for ultimate tensile strength, and the load at failure for fracture strength.
Aluminum
Carbon Steel
Yield Strength (MPa)
220
466
Ultimate Tensile Strength (MPa)
337
582
Fracture Strength (MPa)
270
402
Figure 4: Strength of both samples at different points.
The percentage of elongation can be determined by converting the engineering strain at the fracture point into a percentage. This gives a value of 11% for aluminum and 21.2% for carbon steel.
Using equation 6 from the lab handout, the percentage area reduction can be calculated as shown in figure 5.
%R.A
Aluminum
=
100
∗
A
o
−
A
f
A
o
=
100
∗
4.98759
−
3.9057
4.98759
=
21.1%
%R.A
CarbonSteel
=
100
∗
A
o
−
A
f
A
o
=
100
∗
4.94808
−
2.16424
4.94808
=
56.26%
Figure 5: Calculations for percentage area reduction of the two samples.
The true stress and strain are calculated using the actual dimensions of the sample accounting for deformation.
0
0.02
0.04
0.06
0.08
0.1
0.12
0
0.05
0.1
0.15
0.2
0.25
0.3
0.35
0.4
0.45
0.5
True Stress-Strain Aluminum 2024
True Strain
True Stress
Figure 6: True Stress-Strain curve of Aluminum 2024
0
0.05
0.1
0.15
0.2
0.25
0
0.2
0.4
0.6
0.8
1
1.2
1.4
True Stress-Strain Carbon Steel
True Strain
True Stress
Figure 7: True Stress-Strain curve of Carbon Steel
By selecting the data of the true stress and strain within the plastic range (between the yield strength and ultimate tensile strength) and plotting it on a log-log graph the resulting graph should be linear. Taking a linear regression of this line should provide the stress and hardening coefficients.
0
0.01
0.1
0.1
1
10
f(x) = 0.07 ln(x) + 0.65
Log-Log of True Stress-Strain Aluminum 2024
True Strain
True Stress
Figure 8: Log-Log plot of True Stress-Strain curve of Aluminum 2024
0.02
0.2
1
10
f(x) = 0.16 ln(x) + 1.7
Log-Log of True Stress-Strain Carbon Steel
True Strain
True Stress
Figure 9: Log-Log plot of True Stress-Strain curve of Carbon Steel
Literature Values
For Aluminum the modulus of elasticity was similar to the expected value however, both the yield and ultimate tensile strength were much higher than expected. This could be due to improper measurement of the diameter of the sample causing an error in calculating the strain placed upon the sample. If the diameter measured was smaller than the true diameter it would cause all of the calculations of the stress to be increased potentially causing the error in the data. In the case of the carbon steel sample the modulus of elasticity was closer to the expected
value than the aluminum. However, like the aluminum the yield and ultimate tensile strength were off by a larger margin. In the case of both samples the modulus of elasticity was much closer to the expected value than the yield and ultimate tensile strength were.
Aluminum 2024
Calculated
Literature
Carbon Steel
calculated
Literature
E
85.13
73.1
E
217.74
203
Yield
220
75.8
Yield
466
684
UTS
337
186
UTS
582
986
Figure 10: Comparison of calculated values from experimental data and researched literature
values from MatWeb.
Conclusion
In conclusion, the experiment provided insights into the mechanical properties of aluminum and carbon steel. By analyzing the stress-strain diagrams, material properties such as Young's Modulus, yield strength, and ultimate tensile strength can be characterized. The experiment highlighted differences in material behavior between the aluminum and carbon steel and offered the opportunity to compare the results with literature values. Overall, this experiment deepened my understanding of material mechanics and provided a foundation for further study in structural mechanics.
Your preview ends here
Eager to read complete document? Join bartleby learn and gain access to the full version
- Access to all documents
- Unlimited textbook solutions
- 24/7 expert homework help
References
“Aluminum 2024.” Overview of Materials for Aluminum 2024
, www.matweb.com/search/DataSheet.aspx?
MatGUID=642e240585794f0ab91428aa78c27b4e. Accessed 9 Feb. 2024. “Medium Carbon Steel.” Overview of Materials for Medium Carbon Steel
, www.matweb.com/search/DataSheet.aspx?
MatGUID=098700ed63b24b14bd3bfdbec937489f. Accessed 9 Feb. 2024.
Related Documents
Related Questions
Figure 1 shows the tensile testing results for different materials. All specimens have an initial
diameter of 12 mm and an initial gauge length of 50 mm.
300
250
Low carbon steel
Network polymer
200
Crystalline polymer
150
Amorphous polymer
100
50
5
10
15
20
25
30
Strain (%)
Figure 1: Stress-strain curve
b. Determine the following parameters for each material:
• the tensile strength
the 0.2% offset yield strength
the modulus of elasticity
• the ductility
Stress (MPa)
LO
arrow_forward
6. State your answers to the following questions.Strain Gauge represents the deformation of a material through a change in resistance. If so, explain how temperature will affect the strain gauge in the experimental environment.①:In this experiment, the Strain Gauge measures the strain in micro units. Explain one possible error factor when applying a load by hanging a weight on the material with the strain gauge attached. (Hint: It is easy to shake by hanging the weight using a thread)①:
arrow_forward
A tensile test was performed on a metal specimen with a diameter of
1/2 inch and a gage length (the length over which the elongation is meas-
ured) of 4 inches. The data were plotted on a load-displacement graph,
P vs. AL. A best-fit line was drawn through the points, and the slope of
the straight-line portion was calculated to be P/AL = 1392 kips/in. What
is the modulus of elasticity?
BI
arrow_forward
1. A tensile test was conducted on a metal "505" specimen and the following stress-strain curves
were generated, both curves generated from the same set of data. Use the graphs to fill in the
mechanical properties of the material tested in the box below. Don't forget units!
Stress vs Strain
Stress, psi
Stress, psi
80000
70000
60000
50000
40000
30000
20000
10000
0
0.00
80000
70000
60000
50000
40000
30000
20000
10000
0.02
0
0.000 0.002
0.04
0.004
0.06
0.006
0.08
0.10
Strain
Stress vs Strain
0.008
0.12
Elastic Modulus, E:
0.2% Offset Yield Strength, oo:
Tensile Strength, ou:
Breaking Strength, of:
% Elongation:
0.14
0.010 0.012 0.014
Strain
0.16
0.18
0.016 0.018
0.20
0.020
arrow_forward
The following data were obtained from the tensile test of Aluminum alloy. The initial diameter of testspecimen was 0.505 inch and gauge length was 2.0 inch. Plot the stress strain diagram and determine(a) Proportional Limit (b) Modulus of Elasticity (c) Yield Stress at 0.2% offset (d) Ultimate Stress and(e) Nominal Rupture Stress.
arrow_forward
Can anyone explain why there are two strains calculated here (Engineering and true)
arrow_forward
Engineering and true strain
arrow_forward
Consider the graph below for 3 test samples A, B and C of the same metal
composition which have been cold-worked, but to different extents. If you had to
sort the samples by the degree of cold-working they have undergone, how would
you rank them?
Stress (MPa)
600
500
4006
300
200
100
0
A
B
0.05
1
0.1
0.15
Strain
Select the correct answer:
a. A
arrow_forward
Stress Strain Diagram
The Data shown in the table have been obtained from a tensile test conducted on
a high-strength steel. The test specimen had a diameter of 0.505 inch and a gage
length of 2.00 inch. Using software. plot the Stress-Strain Diagram for this steel
and determine its:
A= TTdT(050s
A
%3D
1. Proportional Limit,
2. Modulus of Elasticity,
3. Yield Strength (SY) at 0.2% Offset,
4. Ultimate Strength (Su),
5. Percent Elongation in 2.00 inch,
6. Percent Reduction in Area,
7. Present the results (for Steps 1-6) in a highly organized table.
e Altac ie sheet (as problelle
4
A = 0.2.002
BEOINNING of the effort
Elongation
(in)
Elongation
(In)
Load
Load
#:
#3
(Ib)
(Ib)
1
0.0170
15
12,300
0.0004
1,500
16
12,200
0.0200
0.0010
3.
3,100
17
12,000
0.0275
0.0016
4,700
18
13,000
0.0335
5.
6,300
0.0022
19
15,000
0.0400
0.0026
6.
8,000
20
16,200
0.055
0.0032
9,500
21
17,500
0.0680
0.0035
8.
11,000
22
18,800
0.1080
0.0041
11,800
23
19,600
0.1515
0.0051
24
20,100
0.2010
10
12,300
0.0071
25…
arrow_forward
(d) Following experimental data (TableQ1b) has obtained from the
torsion test for the specimen dimension given in Table Q1a.
Determine the material of a circular bar. (Take the material
Poisson's Ratio as 0.32)
Table Q1a Specimen Dimensions
Dimensions
Material
Diameter (mm)
6
Length (mm)
77.15
TableQ1b Experimental Results from Torsion test
Angular Deflection
Degree
Radian
Torque/Nm
0.5
0.008727
0.06
1
0.017453
0.47
1.5
0.02618
0.76
2
0.034907
1.01
2.5
0.043633
1.32
3
0.05236
1.65
3.5
0.061087
1.99
4
0.069813
2.32
4.5
0.07854
2.66
5
0.087267
3.00
5.5
0.095993
3.33
6
0.10472
3.64
10
0.174533
5.92
20
0.349066
7.74
30
0.523599
8.07
40
0.698132
8.17
50
0.872665
7.93
60
1.047198
8.10
70
1.221731
8.2
80
1.396264
8.4
90
1.570797
8.24
100
1.74533
8.7
110
1.919863
8.7
120
2.094396
8.7
180
3.141594
9.02
240
4.188792
9.11
300
5.23599
9.48
360
6.283188
9.51
420
7.330386
9.71
arrow_forward
The results of a tensile test are:
Diameter of the specimen
Gauge length
Load at limit of Proportionality
Extension at the limit of Proportionality
Maximum Load
: 10mm
:40 mm
: 70kN
:0.08mm.
:100 kN
Calculate stress at limit of proportionality and young's modulus.
arrow_forward
5. The following data were collected from a standard 0.505-in.-diameter test
specimen of a copper alloy (initial length lo= 2.0 in.). After fracture, the total
length was 3.014 in. and the diameter was 0.374 in.
Load
(Ib)
Al
(in.)
00000
3,000
6,000
0.00167
0.00333
7,500
0.00417
9,000
10,500
0.0090
0.040
12,000
0.26
12,400
11,400
0.50 (maximum load)
1.02 (fracture)
a)
Plot the data as engineering stress versus engineering strain.
b)
Compute the modulus of elasticity.
c)
Determine the yield strength at a strain offset of 0.002.
d)
Determine the tensile strength of this alloy.
e)
What is the approximate ductility, in percent elongation?
f)
Compute the modulus of resilience.
g)
Compute from the data and plot true stress versus true strain diagram.
arrow_forward
Calculate the young’s modulus from one of these two graphs?
arrow_forward
A sample of crosslinked polvisoprene rubber undergoes a constant strain rate axial tension experiment
The initial sample measurements are 3.60 cm gauge length (axial direction); 0.b2 cm wide; 0.1/ cm thick:
arrow_forward
You have been given the following test sample data following mechanical testing of 15
test pieces of a modified Alumina.
What is the Weibull modulus of this material?
Would you advise the use of this material over one with a Weibull Modulus of 19.6 and a
mean failure stress of 270 MPa, if you anticipate that the peak stress on the material
could be 255 MPa?
Sample
1
2
3
4
5
6
7
8
9
10
11
12
13
14
15
Select one or more:
a. 185
b. No
Yes
□d. 49
□e. 28.6
3.7
Failure Stress (MPa)
297
293
270
300
g. 22.8
260
296
265
295
280
288
263
290
298
275
arrow_forward
Question
A cylindrical specimen of metal having a diameter of 12.88 mm and a gauge length
of 63.50 mm is tested using a tensile testing machine. The elongation measurement
are recorded in Table 3.
nPlot the stress-strain curve on the graph paper provided based on data in
Table 3
Based on the stress-strain curved plotted in (i):
Compute the modulus of elasticity
Determine the yield strength at a strain offset of 0.002.
Determine the tensile strength
Determine the ductility in percent elongation and percent area reduction
Table 3: Load-elongation readings for a metal specimen
Jadual 3: Bacaan beban pemanjangan untuk statu spesimen logam)
Load (N)
Elongation (mm)
1380
0.03
2780
0.06
5630
0.12
7430
0.2
8140
0.25
9870
0.64
12850
1.91
14100
3.18
14340
4.45
13830
5.72
12500
6.99
Fracture
arrow_forward
3. Two specimens with the same dimensions and made from two different materials, A and B, were subjected to tensile testing. The percentage
reduction in the area of the specimen made of material 'A' was calculated 3 times that of the specimen made of material B. In this case,
O A lthe ductility of material A and B is equal
O Bthe material A is brittle and material B is ductile
O Cthe material B is more ductile than material A
O D nhe material A is more ductile than material B
1.
20
O Aramak için buraya yazıin
arrow_forward
I just can't find The percent elongation at fracture.
arrow_forward
SEE MORE QUESTIONS
Recommended textbooks for you
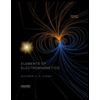
Elements Of Electromagnetics
Mechanical Engineering
ISBN:9780190698614
Author:Sadiku, Matthew N. O.
Publisher:Oxford University Press
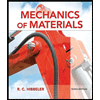
Mechanics of Materials (10th Edition)
Mechanical Engineering
ISBN:9780134319650
Author:Russell C. Hibbeler
Publisher:PEARSON
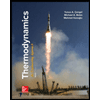
Thermodynamics: An Engineering Approach
Mechanical Engineering
ISBN:9781259822674
Author:Yunus A. Cengel Dr., Michael A. Boles
Publisher:McGraw-Hill Education
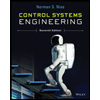
Control Systems Engineering
Mechanical Engineering
ISBN:9781118170519
Author:Norman S. Nise
Publisher:WILEY
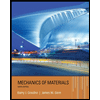
Mechanics of Materials (MindTap Course List)
Mechanical Engineering
ISBN:9781337093347
Author:Barry J. Goodno, James M. Gere
Publisher:Cengage Learning
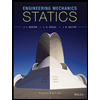
Engineering Mechanics: Statics
Mechanical Engineering
ISBN:9781118807330
Author:James L. Meriam, L. G. Kraige, J. N. Bolton
Publisher:WILEY
Related Questions
- Figure 1 shows the tensile testing results for different materials. All specimens have an initial diameter of 12 mm and an initial gauge length of 50 mm. 300 250 Low carbon steel Network polymer 200 Crystalline polymer 150 Amorphous polymer 100 50 5 10 15 20 25 30 Strain (%) Figure 1: Stress-strain curve b. Determine the following parameters for each material: • the tensile strength the 0.2% offset yield strength the modulus of elasticity • the ductility Stress (MPa) LOarrow_forward6. State your answers to the following questions.Strain Gauge represents the deformation of a material through a change in resistance. If so, explain how temperature will affect the strain gauge in the experimental environment.①:In this experiment, the Strain Gauge measures the strain in micro units. Explain one possible error factor when applying a load by hanging a weight on the material with the strain gauge attached. (Hint: It is easy to shake by hanging the weight using a thread)①:arrow_forwardA tensile test was performed on a metal specimen with a diameter of 1/2 inch and a gage length (the length over which the elongation is meas- ured) of 4 inches. The data were plotted on a load-displacement graph, P vs. AL. A best-fit line was drawn through the points, and the slope of the straight-line portion was calculated to be P/AL = 1392 kips/in. What is the modulus of elasticity? BIarrow_forward
- 1. A tensile test was conducted on a metal "505" specimen and the following stress-strain curves were generated, both curves generated from the same set of data. Use the graphs to fill in the mechanical properties of the material tested in the box below. Don't forget units! Stress vs Strain Stress, psi Stress, psi 80000 70000 60000 50000 40000 30000 20000 10000 0 0.00 80000 70000 60000 50000 40000 30000 20000 10000 0.02 0 0.000 0.002 0.04 0.004 0.06 0.006 0.08 0.10 Strain Stress vs Strain 0.008 0.12 Elastic Modulus, E: 0.2% Offset Yield Strength, oo: Tensile Strength, ou: Breaking Strength, of: % Elongation: 0.14 0.010 0.012 0.014 Strain 0.16 0.18 0.016 0.018 0.20 0.020arrow_forwardThe following data were obtained from the tensile test of Aluminum alloy. The initial diameter of testspecimen was 0.505 inch and gauge length was 2.0 inch. Plot the stress strain diagram and determine(a) Proportional Limit (b) Modulus of Elasticity (c) Yield Stress at 0.2% offset (d) Ultimate Stress and(e) Nominal Rupture Stress.arrow_forwardCan anyone explain why there are two strains calculated here (Engineering and true)arrow_forward
- Engineering and true strainarrow_forwardConsider the graph below for 3 test samples A, B and C of the same metal composition which have been cold-worked, but to different extents. If you had to sort the samples by the degree of cold-working they have undergone, how would you rank them? Stress (MPa) 600 500 4006 300 200 100 0 A B 0.05 1 0.1 0.15 Strain Select the correct answer: a. Aarrow_forwardStress Strain Diagram The Data shown in the table have been obtained from a tensile test conducted on a high-strength steel. The test specimen had a diameter of 0.505 inch and a gage length of 2.00 inch. Using software. plot the Stress-Strain Diagram for this steel and determine its: A= TTdT(050s A %3D 1. Proportional Limit, 2. Modulus of Elasticity, 3. Yield Strength (SY) at 0.2% Offset, 4. Ultimate Strength (Su), 5. Percent Elongation in 2.00 inch, 6. Percent Reduction in Area, 7. Present the results (for Steps 1-6) in a highly organized table. e Altac ie sheet (as problelle 4 A = 0.2.002 BEOINNING of the effort Elongation (in) Elongation (In) Load Load #: #3 (Ib) (Ib) 1 0.0170 15 12,300 0.0004 1,500 16 12,200 0.0200 0.0010 3. 3,100 17 12,000 0.0275 0.0016 4,700 18 13,000 0.0335 5. 6,300 0.0022 19 15,000 0.0400 0.0026 6. 8,000 20 16,200 0.055 0.0032 9,500 21 17,500 0.0680 0.0035 8. 11,000 22 18,800 0.1080 0.0041 11,800 23 19,600 0.1515 0.0051 24 20,100 0.2010 10 12,300 0.0071 25…arrow_forward(d) Following experimental data (TableQ1b) has obtained from the torsion test for the specimen dimension given in Table Q1a. Determine the material of a circular bar. (Take the material Poisson's Ratio as 0.32) Table Q1a Specimen Dimensions Dimensions Material Diameter (mm) 6 Length (mm) 77.15 TableQ1b Experimental Results from Torsion test Angular Deflection Degree Radian Torque/Nm 0.5 0.008727 0.06 1 0.017453 0.47 1.5 0.02618 0.76 2 0.034907 1.01 2.5 0.043633 1.32 3 0.05236 1.65 3.5 0.061087 1.99 4 0.069813 2.32 4.5 0.07854 2.66 5 0.087267 3.00 5.5 0.095993 3.33 6 0.10472 3.64 10 0.174533 5.92 20 0.349066 7.74 30 0.523599 8.07 40 0.698132 8.17 50 0.872665 7.93 60 1.047198 8.10 70 1.221731 8.2 80 1.396264 8.4 90 1.570797 8.24 100 1.74533 8.7 110 1.919863 8.7 120 2.094396 8.7 180 3.141594 9.02 240 4.188792 9.11 300 5.23599 9.48 360 6.283188 9.51 420 7.330386 9.71arrow_forwardThe results of a tensile test are: Diameter of the specimen Gauge length Load at limit of Proportionality Extension at the limit of Proportionality Maximum Load : 10mm :40 mm : 70kN :0.08mm. :100 kN Calculate stress at limit of proportionality and young's modulus.arrow_forward5. The following data were collected from a standard 0.505-in.-diameter test specimen of a copper alloy (initial length lo= 2.0 in.). After fracture, the total length was 3.014 in. and the diameter was 0.374 in. Load (Ib) Al (in.) 00000 3,000 6,000 0.00167 0.00333 7,500 0.00417 9,000 10,500 0.0090 0.040 12,000 0.26 12,400 11,400 0.50 (maximum load) 1.02 (fracture) a) Plot the data as engineering stress versus engineering strain. b) Compute the modulus of elasticity. c) Determine the yield strength at a strain offset of 0.002. d) Determine the tensile strength of this alloy. e) What is the approximate ductility, in percent elongation? f) Compute the modulus of resilience. g) Compute from the data and plot true stress versus true strain diagram.arrow_forwardarrow_back_iosSEE MORE QUESTIONSarrow_forward_ios
Recommended textbooks for you
- Elements Of ElectromagneticsMechanical EngineeringISBN:9780190698614Author:Sadiku, Matthew N. O.Publisher:Oxford University PressMechanics of Materials (10th Edition)Mechanical EngineeringISBN:9780134319650Author:Russell C. HibbelerPublisher:PEARSONThermodynamics: An Engineering ApproachMechanical EngineeringISBN:9781259822674Author:Yunus A. Cengel Dr., Michael A. BolesPublisher:McGraw-Hill Education
- Control Systems EngineeringMechanical EngineeringISBN:9781118170519Author:Norman S. NisePublisher:WILEYMechanics of Materials (MindTap Course List)Mechanical EngineeringISBN:9781337093347Author:Barry J. Goodno, James M. GerePublisher:Cengage LearningEngineering Mechanics: StaticsMechanical EngineeringISBN:9781118807330Author:James L. Meriam, L. G. Kraige, J. N. BoltonPublisher:WILEY
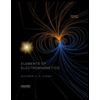
Elements Of Electromagnetics
Mechanical Engineering
ISBN:9780190698614
Author:Sadiku, Matthew N. O.
Publisher:Oxford University Press
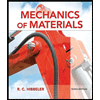
Mechanics of Materials (10th Edition)
Mechanical Engineering
ISBN:9780134319650
Author:Russell C. Hibbeler
Publisher:PEARSON
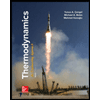
Thermodynamics: An Engineering Approach
Mechanical Engineering
ISBN:9781259822674
Author:Yunus A. Cengel Dr., Michael A. Boles
Publisher:McGraw-Hill Education
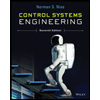
Control Systems Engineering
Mechanical Engineering
ISBN:9781118170519
Author:Norman S. Nise
Publisher:WILEY
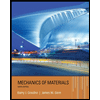
Mechanics of Materials (MindTap Course List)
Mechanical Engineering
ISBN:9781337093347
Author:Barry J. Goodno, James M. Gere
Publisher:Cengage Learning
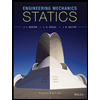
Engineering Mechanics: Statics
Mechanical Engineering
ISBN:9781118807330
Author:James L. Meriam, L. G. Kraige, J. N. Bolton
Publisher:WILEY