Lab4_Strain_Gauge_100322
pdf
keyboard_arrow_up
School
University of Massachusetts, Lowell *
*We aren’t endorsed by this school
Course
3020
Subject
Mechanical Engineering
Date
Dec 6, 2023
Type
Pages
6
Uploaded by PrivateWater4873
MECH.3020 - Strain Gage Measurement Lab
1
Rev 100322
MECH3020 - Experiment 3
Strain Gauge Measurements
Introduction
The design of components for many engineering systems is based on the application of
theoretical models.
The accuracy of these models can be verified through testing.
One way of
validating a math model is to use a strain gage measurement system to measure the strain at the
surface of a structure.
The sensor used to transfer a mechanical strain to a quantifiable output is
the strain gage.
The strain gage has a resistance which changes as a function of mechanical
strain.
Although the change in resistance can be quantified using an ohm meter, signal
conditioning is used to convert the change in resistance to a voltage.
The voltage may then be
amplified, thus reducing quantization errors.
The relationship between the input strain and the
output voltage may be determined using the system sensitivity.
The objective of this assignment is to experimentally determine the system sensitivity and
compare it to the ideal sensitivity of a strain gage measurement system.
The actual system
sensitivity will then be used to determine the modulus of elasticity of a cantilever beam.
Pre-Lab Assignment
Pre-Lab assignments are to be done in your lab notebook following normal lab notebook
documentation procedures.
The Pre-Labs are not to be handed in but will be checked in the lab
to assure that they have been completed.
1.
Determine the ideal system sensitivity of a strain gage system expressed in
millivolts per microstrain, given the following: Sg = 2.130, Ei = 1.5 Vdc, G = 500.
Also, determine the ideal slope of the calibration equation in microstrain per millivolt.
2.
Using a Excel spreadsheet, calculate the deflection required to produce 100, 200, 300, 400,
500, 600, 700, 800, and 900 microstrain at a strain gage mounted to a cantilever beam.
The
geometry of the beam and location of the gage is as follows:
b =
1.0"
(beam width)
t
=
0.125"
(beam thickness)
L =
11.5"
(length of cantilever beam)
x =
10.0"
(distance from the strain gage to the micrometer)
Copy your results to your logbook.
Save your spreadsheet in your USB drive and bring it
to the lab
.
MECH.3020 - Strain Gage Measurement Lab
2
Rev 100322
3.
Determine ten different beam loading values that will be used in lab to end load a cantilever
beam using weights.
Load values should increase by 100 gram intervals with an initial load
of approximately 200 grams. Calculate the stress levels generated at the strain gage location
for each load. Copy your results to your logbook.
Save your spreadsheet in your USB
drive and bring it to the lab
.
4.
Read Section 8.1 and 8.6 in Wheeler & Gangi text 2
nd
edition.
5.
Review the additional notes appended at the end of this document or on the webpage (Old
Writeup), (These are critically important to understand every part of this lab assignment).
Assignment 1: Equipment Configuration & Initialization
Procedure
1.
Install the cantilever beam into the Flexor if not already assembled.
The beam should be
placed with the strain gage on the upper surface closest to the clamp.
Adjust the free end of
the beam so that motion is not impeded by the sides of the Flexor.
2.
Measure and record the following cantilever beam dimensions:
x
- distance from the center of the strain gage to the micrometer load point.
L - distance from the clamped end of the beam to the micrometer load point.
b -
beam width
t
- beam thickness
3.
Compare the measured values with dimensions used in the pre-lab assignment. If the values
of x, b, and t differ, pre-lab calculations must be recalculated using your excel spreadsheet.
4.
Connect the lead wires of the strain gage to
P3 Strain Indicator’s Channel 1
as shown in
Figure 1.
MECH.3020 - Strain Gage Measurement Lab
3
Rev 100322
Figure 1
–
Quarter Bridge Connections
–
P+ (Red), S- (White) and D
350
(Black)
5.
Turn on the P3 Strain Indicator.
6.
Press the
BAL
button to bring the Balance menu up. Press
BAL
again to initialize the
Balancing algorithm. Finally, press the
RECORD
button to save the balance parameters.
7.
The Gage factor has to be updated to
2.130
. In order to do so, press the
GF/SCALING
button, then select
Gage Factor
using the arrows located around the
MENU
button. Once
the change is made, press
MENU
to go back to the main screen.
8.
Using a BNC cable, connect the Strain Indicator output to the multimeter. Remember, the
signal generated by the P3 is a DC signal.
9.
Press the MENU button, select “Options” and press MENU. Then, select “Outputs”. Here
turn the “Analog Out” to “Chan 1”. Then, set the “Out Range” to “Normal”. Finally, press
MENU.
The P3 will display the level of strain while the multimeter a constant voltage. This will be
the initial voltage. Record both values.
10.
Press down on the beam.
Note the change in output voltage on the multimeter as well as
strain on the Strain Indicator display.
As the strain gage is mechanically strained, the change
in resistance is sensed by the wheatstone bridge and a resultant output voltage is generated
which is automatically converted to strain by the Strain Indicator
Your preview ends here
Eager to read complete document? Join bartleby learn and gain access to the full version
- Access to all documents
- Unlimited textbook solutions
- 24/7 expert homework help
MECH.3020 - Strain Gage Measurement Lab
4
Rev 100322
Assignment 2:
Determine the System Sensitivity
The system sensitivity of the strain gage measurement system can be determined by displacing
the free end of the cantilever beam a known distance and recording the output voltage generated
by the signal conditioning module.
The strain induced in the beam at the strain gage location is
determined using the following equation:
where
is the strain at the surface of the beam at the gage location,
is the deflection at the
free end of the beam,
is the beam's thickness,
is the distance from the strain gage to the
point where the load is applied, and
is the cantilever beam length (
Note: this L is different
from the one of Assignment 1
).
Procedure
1.
Adjust the micrometer on the Flexor so that the tip is just touching the cantilever beam.
Record the reading on the micrometer, Strain Indicator and the multimeter as the initial
displacement and corresponding output voltage for the undeflected beam.
2.
Using the micrometer, deflect the beam an amount that will produce a strain of 100
microstrain at the strain gage.
Record the strain level, the micrometer setting, and the output
voltage indicated by the multimeter.
3.
Deflect the beam an amount that will produce strain levels of 200, 300, 400, 500, 600, 700,
800, and 900 microstrain at the strain gage.
Record the strain level, beam deflection, and
output voltage from the system.
4.
Unload the beam and record the final output voltage.
The output should return to the initial
value with no load on the beam.
If the two values do not coincide, record the final value.
Why do you think this may have occurred?
MECH.3020 - Strain Gage Measurement Lab
5
Rev 100322
Assignment 3:
Young's Modulus Determination
The Modulus of Elasticity of the cantilever beam can be determined by hanging known weights
from the free end of the beam and recording the corresponding output voltage from the signal
conditioning amplifier.
The flexure formula
can be used to calculate the stress
level at the gage, while the strain gage system sensitivity is used to quantify the strain.
Plotting
stress and strain data and performing a regression analysis on the linear elastic range will result
in the determination of the Modulus of Elasticity of the beam.
NOTE: Make sure you check your units!
Procedure
1.
Add the weight necessary to produce the first stress level calculated in the pre-lab assignment
question #3. Now, the weight will be placed at the tip of the beam. Update your Excel
spreadsheet with the new values of x and L.
2.
Note that the weights can be "piggy-backed" to achieve the desired weight, as shown in
Figure 2.
Record the weight and the corresponding output voltage and corresponding strain.
Repeat this process for a total of ten loading values calculated in the pre-lab.
3.
Unload the beam and record the final output voltage.
The output should return to the initial
value with no load on the beam.
If the two values do not coincide, record the final value.
Why do you think this may have occurred? Document your observations on your logbook.
Weights
Figure 2 - Young's Modulus Determination
MECH.3020 - Strain Gage Measurement Lab
6
Rev 100322
Post-lab Analysis
NOTE:
Be brief, concise and to the point in all responses.
Provide clear, concise answers to
questions.
Lengthy responses that ramble will not be graded and may lose additional points.
1.
Determine the strain gage system sensitivity.
Compare the actual system sensitivity to the
ideal value determined from the pre-lab assignment.
Discuss possible sources of error.
2.
Make a proper engineering plot of the strain produced at the strain gage and the
corresponding output voltage from the signal conditioning amplifier.
Properly distinguish
experimental data from curve fit data.
3.
Using the calibrated system sensitivity, determine the strain produced at the strain gage in
Assignment #3.
4.
Compare the ten values of strain obtained while loading the beam to those obtained during
unloading. Discuss why differences may have occurred. Are these differences acceptable?
5.
Calculate the stress levels generated from end loading the cantilever beam in Assignment #3.
6.
Make a proper engineering plot of the stress vs. strain from Assignment #3.
Perform a
regression analysis on the data to determine Young's Modulus.
7.
What type of material is the beam made of?
Support conclusions with theoretical and
experimental proof as well as listing any publications referenced.
8.
Explain two methods of increasing the strain gage system sensitivity.
Why would the strain
gage measurement system sensitivity need to be increased?
Your preview ends here
Eager to read complete document? Join bartleby learn and gain access to the full version
- Access to all documents
- Unlimited textbook solutions
- 24/7 expert homework help
Related Documents
Related Questions
Lab 2-Measurement Asynch - Tagged.pdf
Page 4 of 7
?
Part I: Taking Measurements & Estimating Uncertainties for a single measurement
www.stefanelli.eng.br
The mass of the object is_
0
i
Parts on a tripie peam palance
0
0
10 20 30
1
100
2 3
40
200
4
+/-
50 60 70
5
300
7
400
80
Qv Search
8
90
9
500
100
9
10 g
www.stefanelli.eng.br
arrow_forward
E and 5 v X
O file:///C:/Users/Hp/Desktop/mm/OUTCOME%20NO.2%20and%205%20with%20Problems.pdf
+
O Fit to page
D Page view
A Read aloud
1 Add notes
Problems
1. A brass rod of diameter 25 mm and length 250 mm is
subjected to a tensile load of 50 kN and the extension of
the rod is equal to 0.3 mm. Find the Young's Modulus or
Modulus of Elasticity.
99+
to search
hp
delete
prt sc
14 DI
backs
&
7
8
24
4
P
EJR
-0
J
K
H
D.
F
arrow_forward
A mechanical system is presented as
below. There are four simulation
graphs for different values for m, b
and c tested for a step response.
Identify the graph for m=4 kg, b=0.3
N.s/m and k=1 N/m (Hint: you may
need to use matlab simulation to find
it).
m
1.8
1.6
1.4
b
·f(t)
Step Response
arrow_forward
The stress profile shown below is applied to six different biological materials:
Log Time (s]
The mechanical behavior of each of the materials can be modeled as a Voigt body. In response to o,= 20 Pa
applied to each of the six materials, the following responses are obtained:
2 of
Maferial 6
Material 5
0.12
0.10
Material 4
0.08
Material 3
0.06
0.04
Material 2
0.02
Material 1
(a) Which of the materials has the highest Young's Modulus (E)? Why?
Log Time (s)
(b) Using strain value of 0.06, estimate the coefficient of viscosity (n) for Material 6.
Stress (kPa)
Strain
arrow_forward
Vibrations
arrow_forward
. 2) A following figure and table display creep test data obtained from a uniaxial specimen
having an initial gauge length of 2 cm. Calculate the steady-state creep rate.
Length
|(cm)
2.3
Time
| (h)
2.25
2.004
2.2
100
2.010
200
2.020
400
2.030
1000
2000
2.045
2.075
2.1
2.05
4000
2.135
6000
2.193
7000
2.230
1.95
8000
2.300
1000
2000
3000
4000
5000
6000
7000
8000
Time (h)
(rupture) |
Length between the gauge marks (cm)
2.
arrow_forward
explains how the two methods of parameter estimation, namely the method of parameter estimation and the method of moments and percentile matching, are used to fit distributions to data for actuarial calculations.
arrow_forward
Can someone please help me to solve all of the following problem ON PAPER showing all work. Thank you!
arrow_forward
Is answer 0.1111?
I am just asking ,Not sure.
Looking for someone who is 100% sure.
arrow_forward
A thermocouple is used to
measure the temperature T1. The
thermocouple reference junction
labeled 2 is at a temperature of
20°C. The voltage output is
measured using a potentiometer
and found to be 4.686 mV. What
is T1 in degrees
RK: if the temperature values are
not in the table, you have to use
interpolation.
Select one:
O a. 98
O b. 118
O c. 105
O d. 108
Previous page
Next page
arrow_forward
Which of these statements are correct?
arrow_forward
2) A device used in a ground radar system has age to failure that is described approximately by a
Weibull distribution with mean life 83 h, shape parameter 1.5, and location parameter zero.
When it fails it takes on average 3.5 h to repair:
a) Calculate the reliability over a 25 h period, and the 'steady state' availability of the device.
b) Calculate the reliability over 25 h, and the ‘steady state' availability of a subsystem that
consists of two of these devices in active parallel redundancy.
arrow_forward
phpO9puZM.png
arrow_forward
Need help, round answers to 3 sig figs please
arrow_forward
62. •A 5-kg object is constrained to move along a straight
line. Its initial speed is 12 m/s in one direction, and its final
speed is 8 m/s in the
opposite
Complete the graph of
force versus time with
direction.
F (N)
(s)
appropriate values for
both variables (Figure
7-26). Several answers
are correct, just be sure
that your answer is
internally consistent.
Figure 7-26 Problem 62
arrow_forward
100
80
60
40
20
0.002
0.004
0.006
0.008
0.01
0.012
Strain, in/in.
FIGURE P1.17
1.18 Use Problem 1.17 to graphically determine the following:
a. Modulus of resilience
b. Toughness
Hint: The toughness (u) can be determined by calculating the area under
the stress-strain curve
u =
de
where & is the strain at fracture. The preceding integral can be approxi-
mated numerically by using a trapezoidal integration technique:
u, = Eu, = o, + o e, - 6)
%3D
c. If the specimen is loaded to 40 ksi only and the lateral strain was found to
be -0.00057 in./in., what is Poisson's ratio of this metal?
d. If the specimen is loaded to 70 ksi only and then unloaded, what is the
permanent strain?
Stress, ksi
arrow_forward
4:07
3G l.
Moodle
A bbb2.du.edu.om
EE
...Session (15-3-
Said Grami O
College of Engineering
Vision for the Future
Question 3
During a step function calibration, a first-order instrument
is exposed to a step change of 200 units.
1- If after 1.5 s the instrument indicates 140 units, find the
instrument time constant.
2- find the error in the indicated value after 2 s
S.
3- Find the raise time at 90 % of the system.
y(0)=0 units; K=1 unit/unit.
Question 4
A first order instrument with a time constant of 2 seconds is to
be used to measure a periodic input. If a dynamic error of
±2% can be tolerated,
1- determine the maximum frequency of periodic input that
can be measured.
2- What is the associated time lag (in seconds) at that
frequency?
MECH374: Instrumentation and Measurement
Said Grami
Practice
arrow_forward
HEAT TRANSFER
CASE: I want to know what temperature in (°F) the cylinder will have inside. It's a heat transfer problem.
what is T2 ?
HEAT TRANSFER
They gave me an answer all squashed together that i can't make sense of it. If you could help me makes sense of it thank you!
arrow_forward
K
mylabmastering.pearson.com
Chapter 12 - Lecture Notes.pptx: (MAE 272-01) (SP25) DY...
P Pearson MyLab and Mastering
Mastering Engineering
Back to my courses
Course Home
Scores
Course Home
arrow_forward
A thermocouple was used to measure the temperature. Over the range of temperatures expected in the experiment, a linear regression
analysis was performed for the temperature as a function of voltage. The best-fit equation was T = (-0.008563 + 220*V), where V is
the thermocouple voltage. The voltage was fed into a 11-bit A/D converter with a voltage range of -8 V to 8 V.
Determine the measurement resolution (in °C) due to the ADC?
O 0.851
None
O 3.113
1.710
0.393
4.960
1.144
O 3.797
arrow_forward
In matlab code
arrow_forward
SEE MORE QUESTIONS
Recommended textbooks for you
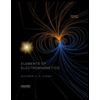
Elements Of Electromagnetics
Mechanical Engineering
ISBN:9780190698614
Author:Sadiku, Matthew N. O.
Publisher:Oxford University Press
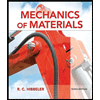
Mechanics of Materials (10th Edition)
Mechanical Engineering
ISBN:9780134319650
Author:Russell C. Hibbeler
Publisher:PEARSON
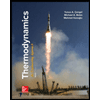
Thermodynamics: An Engineering Approach
Mechanical Engineering
ISBN:9781259822674
Author:Yunus A. Cengel Dr., Michael A. Boles
Publisher:McGraw-Hill Education
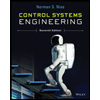
Control Systems Engineering
Mechanical Engineering
ISBN:9781118170519
Author:Norman S. Nise
Publisher:WILEY
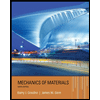
Mechanics of Materials (MindTap Course List)
Mechanical Engineering
ISBN:9781337093347
Author:Barry J. Goodno, James M. Gere
Publisher:Cengage Learning
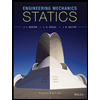
Engineering Mechanics: Statics
Mechanical Engineering
ISBN:9781118807330
Author:James L. Meriam, L. G. Kraige, J. N. Bolton
Publisher:WILEY
Related Questions
- Lab 2-Measurement Asynch - Tagged.pdf Page 4 of 7 ? Part I: Taking Measurements & Estimating Uncertainties for a single measurement www.stefanelli.eng.br The mass of the object is_ 0 i Parts on a tripie peam palance 0 0 10 20 30 1 100 2 3 40 200 4 +/- 50 60 70 5 300 7 400 80 Qv Search 8 90 9 500 100 9 10 g www.stefanelli.eng.brarrow_forwardE and 5 v X O file:///C:/Users/Hp/Desktop/mm/OUTCOME%20NO.2%20and%205%20with%20Problems.pdf + O Fit to page D Page view A Read aloud 1 Add notes Problems 1. A brass rod of diameter 25 mm and length 250 mm is subjected to a tensile load of 50 kN and the extension of the rod is equal to 0.3 mm. Find the Young's Modulus or Modulus of Elasticity. 99+ to search hp delete prt sc 14 DI backs & 7 8 24 4 P EJR -0 J K H D. Farrow_forwardA mechanical system is presented as below. There are four simulation graphs for different values for m, b and c tested for a step response. Identify the graph for m=4 kg, b=0.3 N.s/m and k=1 N/m (Hint: you may need to use matlab simulation to find it). m 1.8 1.6 1.4 b ·f(t) Step Responsearrow_forward
- The stress profile shown below is applied to six different biological materials: Log Time (s] The mechanical behavior of each of the materials can be modeled as a Voigt body. In response to o,= 20 Pa applied to each of the six materials, the following responses are obtained: 2 of Maferial 6 Material 5 0.12 0.10 Material 4 0.08 Material 3 0.06 0.04 Material 2 0.02 Material 1 (a) Which of the materials has the highest Young's Modulus (E)? Why? Log Time (s) (b) Using strain value of 0.06, estimate the coefficient of viscosity (n) for Material 6. Stress (kPa) Strainarrow_forwardVibrationsarrow_forward. 2) A following figure and table display creep test data obtained from a uniaxial specimen having an initial gauge length of 2 cm. Calculate the steady-state creep rate. Length |(cm) 2.3 Time | (h) 2.25 2.004 2.2 100 2.010 200 2.020 400 2.030 1000 2000 2.045 2.075 2.1 2.05 4000 2.135 6000 2.193 7000 2.230 1.95 8000 2.300 1000 2000 3000 4000 5000 6000 7000 8000 Time (h) (rupture) | Length between the gauge marks (cm) 2.arrow_forward
- explains how the two methods of parameter estimation, namely the method of parameter estimation and the method of moments and percentile matching, are used to fit distributions to data for actuarial calculations.arrow_forwardCan someone please help me to solve all of the following problem ON PAPER showing all work. Thank you!arrow_forwardIs answer 0.1111? I am just asking ,Not sure. Looking for someone who is 100% sure.arrow_forward
- A thermocouple is used to measure the temperature T1. The thermocouple reference junction labeled 2 is at a temperature of 20°C. The voltage output is measured using a potentiometer and found to be 4.686 mV. What is T1 in degrees RK: if the temperature values are not in the table, you have to use interpolation. Select one: O a. 98 O b. 118 O c. 105 O d. 108 Previous page Next pagearrow_forwardWhich of these statements are correct?arrow_forward2) A device used in a ground radar system has age to failure that is described approximately by a Weibull distribution with mean life 83 h, shape parameter 1.5, and location parameter zero. When it fails it takes on average 3.5 h to repair: a) Calculate the reliability over a 25 h period, and the 'steady state' availability of the device. b) Calculate the reliability over 25 h, and the ‘steady state' availability of a subsystem that consists of two of these devices in active parallel redundancy.arrow_forward
arrow_back_ios
SEE MORE QUESTIONS
arrow_forward_ios
Recommended textbooks for you
- Elements Of ElectromagneticsMechanical EngineeringISBN:9780190698614Author:Sadiku, Matthew N. O.Publisher:Oxford University PressMechanics of Materials (10th Edition)Mechanical EngineeringISBN:9780134319650Author:Russell C. HibbelerPublisher:PEARSONThermodynamics: An Engineering ApproachMechanical EngineeringISBN:9781259822674Author:Yunus A. Cengel Dr., Michael A. BolesPublisher:McGraw-Hill Education
- Control Systems EngineeringMechanical EngineeringISBN:9781118170519Author:Norman S. NisePublisher:WILEYMechanics of Materials (MindTap Course List)Mechanical EngineeringISBN:9781337093347Author:Barry J. Goodno, James M. GerePublisher:Cengage LearningEngineering Mechanics: StaticsMechanical EngineeringISBN:9781118807330Author:James L. Meriam, L. G. Kraige, J. N. BoltonPublisher:WILEY
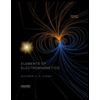
Elements Of Electromagnetics
Mechanical Engineering
ISBN:9780190698614
Author:Sadiku, Matthew N. O.
Publisher:Oxford University Press
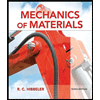
Mechanics of Materials (10th Edition)
Mechanical Engineering
ISBN:9780134319650
Author:Russell C. Hibbeler
Publisher:PEARSON
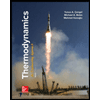
Thermodynamics: An Engineering Approach
Mechanical Engineering
ISBN:9781259822674
Author:Yunus A. Cengel Dr., Michael A. Boles
Publisher:McGraw-Hill Education
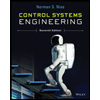
Control Systems Engineering
Mechanical Engineering
ISBN:9781118170519
Author:Norman S. Nise
Publisher:WILEY
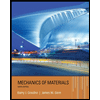
Mechanics of Materials (MindTap Course List)
Mechanical Engineering
ISBN:9781337093347
Author:Barry J. Goodno, James M. Gere
Publisher:Cengage Learning
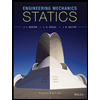
Engineering Mechanics: Statics
Mechanical Engineering
ISBN:9781118807330
Author:James L. Meriam, L. G. Kraige, J. N. Bolton
Publisher:WILEY