Tensile[89]
pdf
keyboard_arrow_up
School
Florida State University *
*We aren’t endorsed by this school
Course
3003
Subject
Mechanical Engineering
Date
Dec 6, 2023
Type
Pages
14
Uploaded by Slick97
1
LAB REPORT 2
Gabriel Parsonis
Oct/10/2022
Objective
The objective of this lab is to better understand how a tensile-tension test works and how
it applies to engineering stress/ strain and true stress/strain. This lab provided the first
opportunity for students (this semester) to have hands on experience working real
engineering testing technology in a laboratory setting. Students after the lab should be
able to visualize the differences of ductility and strength between two materials and how
they can be measured or visually observed before and after testing.
Experimental:
Figure 1: Polycarbonate specimen before and after tensile testing
2
Figure 2: Aluminum specimen before and after tensile testing
Figure 3: Data collected representing plastic and metal pre and post testing measurements
3
Figure 4: Aluminum specimen Excel Sheet1
Figure 5: Aluminum specimen Excel Sheet2
Your preview ends here
Eager to read complete document? Join bartleby learn and gain access to the full version
- Access to all documents
- Unlimited textbook solutions
- 24/7 expert homework help
4
Figure 6: Aluminum specimen Excel Sheet3
5
Figure 7: Plastic specimen Excel Sheet1
Figure 8: Plastic specimen Excel Sheet2
6
Results and Discussion:
Part I. Experimental Results and Data Analysis of Al alloy Samples
1.
With the raw data obtained from the tension test, compute and plot engineering stress
s vs.
engineering strain e.
The plot should be generated with a computer (e.g.,
Microsoft Excel). No credit will be given to a hand-generated plot.
To find the engineering stress vs strain graph, one must individually calculate the
Engineering Strain (stroke/original length) and Engineering Stress (force/original
area) for each of the three specimens (Figure 9). Following this an average of each
point must be taken in order of there to be a singular line in a singular graph (Figure
10). Engineering Strain on the X axis and Engineering Stress on the Y axis.
Figure 9:
-50
0
50
100
150
200
250
300
350
-0.05
0
0.05
0.1
0.15
0.2
0.25
0.3
Engineering Stress
Engineering Strain
Similarity of Stress/Strain Curves for three
Aluminum tests
Your preview ends here
Eager to read complete document? Join bartleby learn and gain access to the full version
- Access to all documents
- Unlimited textbook solutions
- 24/7 expert homework help
7
Figure 10:
2.
Compute and plot true stress s vs. true strain e. Plot on the same graph as
engineering stress vs. engineering strain so that you can clearly see the differences
between the curves.
Figure 11:
The true stress/strain curve (yellow line) was derived from the average engineering
stress/strain numbers. True stress was found by multiplying engineering stress with
(1+engineering strain) and true strain was found by taking ln (1 + engineering strain).
y = 22,904,741.73x
6
- 22,382,902.23x
5
+ 6,991,959.97x
4
-
775,408.52x
3
- 7,029.65x
2
+ 6,602.01x
R² = 0.99
y = 5770x
0
50
100
150
200
250
300
350
0
0.05
0.1
0.15
0.2
0.25
Engineering Stress
Engineering Strain
Averages for stress vs strain for the three
Aluminum Tests
y = 22,904,741.73x
6
- 22,382,902.23x
5
+ 6,991,959.97x
4
-
775,408.52x
3
- 7,029.65x
2
+ 6,602.01x
R² = 0.99
y = 5770x
0
50
100
150
200
250
300
350
400
450
0
0.05
0.1
0.15
0.2
0.25
Stress
Strain
Averages for stress vs strain for the three
Aluminum Tests with true stress and
strain curve
8
a)
Elastic property and strength measures
1.
Determine the elastic modulus E.
To determine the Modulus, one first must find the average of the 3 graphs as one
graph. Following this they then find the trendline of the “straight portion” of this
graph leading to the yield point. Then the slope of this line is the Elastic modulus
which is y=5770x.
2.
Determine the 0.2% offset yield strength (sY) .
In order to obtain the 0.2% offset. One must first calculate the 0.2% offset yield point.
To determine this one must obtain the 0.2 percent offset stress and strain. The 0.2
strain is found by adding 0.2% in excel to the average of the three strains and the
stress is found through multiplying the modulus and the avg strain. The plot for this
on the graph demonstrates where the yield point is (grey line and blue line). Through
finding the yield point if one locates its coordinates on the graph the which is 241 on
the y axis.
b)
Ductility measures
1.
Determine the true fracture strain.
In order for one to find the true fracture strain they must divide the largest average
strain by the original length.
0.23568 / 25 = 0.0094272
9
2.
Determine the percent reduction in area.
Before test:
5.76 mm (width)
1.59 mm (thickness)
9.1584 mm^2 (area)
After test:
5.53 mm (width 1)
1.53 mm (thickness 1)
5.49 mm (width 2)
1.50 mm (thickness 2)
5.51 (avg width)
1.515 (avg thickness)
8.34765 (avg area)
Calculations:
= [(Old-new)/old] *100
= [(9.1584-8.34765)/ 9.1584] *100
= 8.85 percent
3.
Determine the toughness of the material.
In order to find the toughness of a curve one must find the area under the curve
through integration. Here the best formula one could derive is
( 22,904,741.73x6 - 22,382,902.23x5 + 6,991,959.97x4 - 775,408.52x3 - 7,029.65x2
+ 6,602.01x ). Once deriving this equation, one must then integrate from 0 to
0.229337773 (largest strain number) so the integral takes the entire curves length into
account entire curve length. However, I was unable to find a website that worked into
deriving a proper number.
4.
Does this material exhibit necking?
Yes, this material exhibits necking. One could tell visually from the in-elastic, shape
deformation the material goes through. In addition to this the material necks after the
UTS is hit as the slope of the graphs becomes negative.
Your preview ends here
Eager to read complete document? Join bartleby learn and gain access to the full version
- Access to all documents
- Unlimited textbook solutions
- 24/7 expert homework help
10
c)
Determine the power-hardening constants (K, n) in the equation s = K(e^n). Use only the
data before the onset of necking. (Note that the power-hardening relationship is an
approximation of a true stress vs. true strain curve.) Hint: Use the “Add Trendline”
function in Excel to fit a power function, i.e. y = A(x^b) , to the true stress-strain curve.
Figure 12:
K= 414.29
N= 0.1323
d)
Compare the modulus, strength, and ductility measures with published data and
comment.
Provide plausible explanations (or sources of error) if there are significant differences.
The measurements which were gathered from the experiment and correspondingly
calculated in excel were majority the same yet had slight differences. This can be due to
the tightness of the clamps on the tensile test, which held the material in place. Another
possible differences in measurements could be due to the placement of the material and
its distance from the base of the clamp. This could cause uneven breakages or a bias
towards an early or late fracture.
y = 414.29x
0.1323
0
50
100
150
200
250
300
350
0
0.02
0.04
0.06
0.08
0.1
0.12
0.14
0.16
0.18
Stress
Strain
Power Hardening graph
11
Part II. Experimental Results and Data Analysis of Polycarbonate Samples
a)
Stress-strain curves
1.
With the raw data obtained from the tension test, compute and plot engineering stress
s vs. engineering strain e. The plot should be generated with a computer
(e.g.Microsoft Excel). No credit will be given to a hand-generated plot.
Figure 13:
To find the engineering stress vs strain graph, one must individually calculate the
Engineering Strain (stroke/original length) and Engineering Stress (force/original
area) for each of the three specimens (Figure 9). Following this an average of each
point must be taken in order of there to be a singular line in a singular graph (Figure
10). Engineering Strain on the X axis and Engineering Stress on the Y axis.
-10
0
10
20
30
40
50
60
70
0
0.05
0.1
0.15
0.2
0.25
Eng Stress
Eng Strain
Similarity of Stress/Strain Curves for
three Plastic tests
12
2.
Compute and plot true stress s vs. true strain e. Plot on the same graph as engineering
stress vs. engineering strain so that you can clearly see the differences between the
curves.
Figure 14:
The true stress/strain curve (yellow line) was derived from the average engineering
stress/strain numbers. True stress was found by multiplying engineering stress with
(1+engineering strain) and true strain was found by taking ln (1 + engineering strain).
b)
Elastic property and strength measures
1.
Determine the elastic modulus E.
To determine the Modulus, we first must find the average of the 3 graphs as one
graph then finding the trendline of the “straight portion” of the graph leading to the
yield point. Then the slope of this line is the Elastic modulus which is y = 670.72x.
2.
Determine the 0.2% offset yield strength (sY) .
In order to obtain the 0.2% offset. One must first calculate the 0.2% offset yield point.
To determine this one must obtain the 0.2 percent offset stress and strain. The 0.2
strain is found by adding 0.2% in excel to the average of the three strains and the
stress is found through multiplying the modulus and the avg strain. The plot for this
on the graph demonstrates where the yield point is (grey line and blue line). Through
finding the yield point if one locates its coordinates on the graph the which is 39.45
on the y axis.
y = 670.72x
0
20
40
60
80
0
0.05
0.1
0.15
0.2
Stress
Strain
Averages for stress vs strain for
the three Plastic Tests
Your preview ends here
Eager to read complete document? Join bartleby learn and gain access to the full version
- Access to all documents
- Unlimited textbook solutions
- 24/7 expert homework help
13
3.
Determine the ultimate tensile strength.
In order to find the UTS one must locate the highest stress. This can most efficiently
be completed by typing =MAX (avg stress column) into a cell. In this case the UTS is
59.54
c)
Determine the failure strain of the material.
In order to determine the failure strain, one must locate where the strain on the graph dips
right before fracture (almost perpendicular to the x axis) after the UTS. In this case it was
0.229337773.
Conclusion
In conclusion the tensile testing lab brought engineering stress/strain and true stress and
strain into real life and visual representation. Students were able to gain hands on
experience in learning how to handle real life engineering machinery along with how the
machinery interacts with our study’s. There’s an important connection when an
individual is able to bridge a gap from the classroom to live experiences. This can help
students not only visualize topics to a higher degree but also spark interest in leaning. The
lab continued its teachings that not all materials have the same ductility or strength.
Students were able to measure and observe these differences, which paved a key
foundation into understanding the subject matter.
14
References
1)
https://famu-fsueng.instructure.com/courses/9259/files/
456939?module_item_id=115132 (online zoom lesson)
Related Documents
Related Questions
Academic)
The following tensile data were collected from a standard 12.827 mm diameter test specimen of
copper alloy. The specimen was tested under tensile load until rupture.
After fracture, the sample length is 76.708 mm and the diameter is 9.5 mm.
Load (kN) Sample Length (mm)
50.8
13.4
50.842
26.7
50.897
33.4
50.957
40.0
51.0286
46.7
51.816
53.4
57.404
55.2
63.5
50.7
76.708
Calculate:
1. Ultimate Engineering Tensile strength:
2. Engineering stress at fracture:
3. True stress at fracture:
4. Percent elongation of the tested copper alloy specimen:
5. Percent reduction of area of the tested copper alloy specimen:
arrow_forward
Pls don’t use ai and fast :)
arrow_forward
Don’t use ai pls
arrow_forward
Question 3
You are working on a design team at a small orthopaedic firm. Your team is starting to work on a lower limb
(foot-ankle) prosthesis for individuals who have undergone foot amputation (bone resection at the distal tibia). You remember hearing
about "osseointegration" in an exciting orthopaedic engineering class you attended at Clemson, so you plan to attach the foot
prosthesis using a solid metal rod inserted into the distal tibia. You think stainless steel or titanium alloy might be a useful rod material.
You decide to begin this problem by identifying typical tibial bone anatomy and mechanical behavior (as provided in the tables and
image below). You assume the tibial bone can be modeled as a hollow cylinder of cortical bone, as represented in the image. You
anticipate the length of the rod will be 1/2 the length of the tibia.
Q3G: Critical Thinking: What would you propose to your team as the next step in this analysis? Is it reasonable to assume the rod
will experience the…
arrow_forward
HOMEWORK
Engineering Materials
1. Consider a cylindrical specimen of some hypothetical metal alloy that has a diameter of 10.0 mm.
A tensile force of 1500 N produces an elastic reduction in diameter of 6.7 x 10 mm. Compute the
elastic modulus of this alloy, given that Poisson's ratio is 0.35.
arrow_forward
Help!!! Please answer part B correctly!!! Please
arrow_forward
I want help with these questions
arrow_forward
2- A piece of muscle specimen has the initial length of 30mm and square cross section with original
side of 12 mm was tested using a tensile test. The applied tensile force of 20 N resulted in
deformation (AL) of 10mm.The muscle remained in the elastic deformation region during the test.
a) Determine the modulus of elasticity of the muscle specimen (make sure to include stress (ơ)
and strain (ɛ1ong)in your answers)
b) If the side of square cross section measured at the maximum longitudinal stretch was 10.5
mm, determine the Poisson ratio of the muscle specimen
c) Determine modulus of rigidity (G)
(Ans: E=0.4167 MPa, v=0.375, G=0.1515 MPa)
arrow_forward
Select three:
Three commonly used tests to measure the hardness related properties of materials are:
Rebound
Fracture
Indentation
Scratch
Charpy
Yield
arrow_forward
question C please
arrow_forward
In your summer internship, you are tasked with measuring the ultimate tensile strength of a material to determine if it meets your company’s (Superior Super Ships Inc) specification. Your boss is worried that the new low-cost supplier, Shoddy Alloys Inc, may not be reliable but it is the only way to source on-time the SS304 needed to make finishings for Jeff Bezos’ new yacht, the Black Pearl. You collect several load versus displacement curves, as illustrated below. The initial diameter of the round gauge section is 0.25 in.
You also collect the instantaneous diameter of the specimen during the test using a laser.
Using the provided data, calculate what is the ultimate tensile strength measured in this test?
arrow_forward
Task 1
You have been moved into the laboratory for the fluid testing for hydraulic devices and a considerable amount of research has been
carried out in an attempt to understand the exact nature of the temperature variation of viscosity. Inspect the table given below and
note the relative values of viscosity for each Newtonian fluid at a given temperature. Compare the results of a viscosity test and
comment on why the viscosity of ethanol and water is considerably lower than motor oil and explain any discrepancies.
Temperature
[°C]
Water (μ)
Ethanol (μ)
Motor oil (SAE 15W-40) (μ)
[mPa s]/ cP
[mPa s]/ cP
[mPa s]/ cP
10
1.30600
1.4475
582.95
20
1.00160
1.1841
287.23
30
0.79722
0.9764
155.31
40
0.65272
0.8151
91.057
50
0.54650
0.694
57.172
60
0.46602
0.6034
38.071
70
0.40353
0.5231
26.576
80
0.35404
0.01043
19.358
90
0.31417
0.01074
14.588
100
0.28158
0.1104
11.316
To complete this task, it is required to evaluate the effects of shear force on three Newtonian and three non-Newtonian…
arrow_forward
SEE MORE QUESTIONS
Recommended textbooks for you
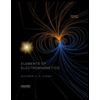
Elements Of Electromagnetics
Mechanical Engineering
ISBN:9780190698614
Author:Sadiku, Matthew N. O.
Publisher:Oxford University Press
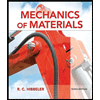
Mechanics of Materials (10th Edition)
Mechanical Engineering
ISBN:9780134319650
Author:Russell C. Hibbeler
Publisher:PEARSON
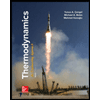
Thermodynamics: An Engineering Approach
Mechanical Engineering
ISBN:9781259822674
Author:Yunus A. Cengel Dr., Michael A. Boles
Publisher:McGraw-Hill Education
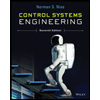
Control Systems Engineering
Mechanical Engineering
ISBN:9781118170519
Author:Norman S. Nise
Publisher:WILEY
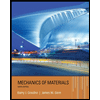
Mechanics of Materials (MindTap Course List)
Mechanical Engineering
ISBN:9781337093347
Author:Barry J. Goodno, James M. Gere
Publisher:Cengage Learning
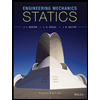
Engineering Mechanics: Statics
Mechanical Engineering
ISBN:9781118807330
Author:James L. Meriam, L. G. Kraige, J. N. Bolton
Publisher:WILEY
Related Questions
- Academic) The following tensile data were collected from a standard 12.827 mm diameter test specimen of copper alloy. The specimen was tested under tensile load until rupture. After fracture, the sample length is 76.708 mm and the diameter is 9.5 mm. Load (kN) Sample Length (mm) 50.8 13.4 50.842 26.7 50.897 33.4 50.957 40.0 51.0286 46.7 51.816 53.4 57.404 55.2 63.5 50.7 76.708 Calculate: 1. Ultimate Engineering Tensile strength: 2. Engineering stress at fracture: 3. True stress at fracture: 4. Percent elongation of the tested copper alloy specimen: 5. Percent reduction of area of the tested copper alloy specimen:arrow_forwardPls don’t use ai and fast :)arrow_forwardDon’t use ai plsarrow_forward
- Question 3 You are working on a design team at a small orthopaedic firm. Your team is starting to work on a lower limb (foot-ankle) prosthesis for individuals who have undergone foot amputation (bone resection at the distal tibia). You remember hearing about "osseointegration" in an exciting orthopaedic engineering class you attended at Clemson, so you plan to attach the foot prosthesis using a solid metal rod inserted into the distal tibia. You think stainless steel or titanium alloy might be a useful rod material. You decide to begin this problem by identifying typical tibial bone anatomy and mechanical behavior (as provided in the tables and image below). You assume the tibial bone can be modeled as a hollow cylinder of cortical bone, as represented in the image. You anticipate the length of the rod will be 1/2 the length of the tibia. Q3G: Critical Thinking: What would you propose to your team as the next step in this analysis? Is it reasonable to assume the rod will experience the…arrow_forwardHOMEWORK Engineering Materials 1. Consider a cylindrical specimen of some hypothetical metal alloy that has a diameter of 10.0 mm. A tensile force of 1500 N produces an elastic reduction in diameter of 6.7 x 10 mm. Compute the elastic modulus of this alloy, given that Poisson's ratio is 0.35.arrow_forwardHelp!!! Please answer part B correctly!!! Pleasearrow_forward
- I want help with these questionsarrow_forward2- A piece of muscle specimen has the initial length of 30mm and square cross section with original side of 12 mm was tested using a tensile test. The applied tensile force of 20 N resulted in deformation (AL) of 10mm.The muscle remained in the elastic deformation region during the test. a) Determine the modulus of elasticity of the muscle specimen (make sure to include stress (ơ) and strain (ɛ1ong)in your answers) b) If the side of square cross section measured at the maximum longitudinal stretch was 10.5 mm, determine the Poisson ratio of the muscle specimen c) Determine modulus of rigidity (G) (Ans: E=0.4167 MPa, v=0.375, G=0.1515 MPa)arrow_forwardSelect three: Three commonly used tests to measure the hardness related properties of materials are: Rebound Fracture Indentation Scratch Charpy Yieldarrow_forward
- question C pleasearrow_forwardIn your summer internship, you are tasked with measuring the ultimate tensile strength of a material to determine if it meets your company’s (Superior Super Ships Inc) specification. Your boss is worried that the new low-cost supplier, Shoddy Alloys Inc, may not be reliable but it is the only way to source on-time the SS304 needed to make finishings for Jeff Bezos’ new yacht, the Black Pearl. You collect several load versus displacement curves, as illustrated below. The initial diameter of the round gauge section is 0.25 in. You also collect the instantaneous diameter of the specimen during the test using a laser. Using the provided data, calculate what is the ultimate tensile strength measured in this test?arrow_forwardTask 1 You have been moved into the laboratory for the fluid testing for hydraulic devices and a considerable amount of research has been carried out in an attempt to understand the exact nature of the temperature variation of viscosity. Inspect the table given below and note the relative values of viscosity for each Newtonian fluid at a given temperature. Compare the results of a viscosity test and comment on why the viscosity of ethanol and water is considerably lower than motor oil and explain any discrepancies. Temperature [°C] Water (μ) Ethanol (μ) Motor oil (SAE 15W-40) (μ) [mPa s]/ cP [mPa s]/ cP [mPa s]/ cP 10 1.30600 1.4475 582.95 20 1.00160 1.1841 287.23 30 0.79722 0.9764 155.31 40 0.65272 0.8151 91.057 50 0.54650 0.694 57.172 60 0.46602 0.6034 38.071 70 0.40353 0.5231 26.576 80 0.35404 0.01043 19.358 90 0.31417 0.01074 14.588 100 0.28158 0.1104 11.316 To complete this task, it is required to evaluate the effects of shear force on three Newtonian and three non-Newtonian…arrow_forward
arrow_back_ios
arrow_forward_ios
Recommended textbooks for you
- Elements Of ElectromagneticsMechanical EngineeringISBN:9780190698614Author:Sadiku, Matthew N. O.Publisher:Oxford University PressMechanics of Materials (10th Edition)Mechanical EngineeringISBN:9780134319650Author:Russell C. HibbelerPublisher:PEARSONThermodynamics: An Engineering ApproachMechanical EngineeringISBN:9781259822674Author:Yunus A. Cengel Dr., Michael A. BolesPublisher:McGraw-Hill Education
- Control Systems EngineeringMechanical EngineeringISBN:9781118170519Author:Norman S. NisePublisher:WILEYMechanics of Materials (MindTap Course List)Mechanical EngineeringISBN:9781337093347Author:Barry J. Goodno, James M. GerePublisher:Cengage LearningEngineering Mechanics: StaticsMechanical EngineeringISBN:9781118807330Author:James L. Meriam, L. G. Kraige, J. N. BoltonPublisher:WILEY
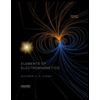
Elements Of Electromagnetics
Mechanical Engineering
ISBN:9780190698614
Author:Sadiku, Matthew N. O.
Publisher:Oxford University Press
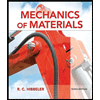
Mechanics of Materials (10th Edition)
Mechanical Engineering
ISBN:9780134319650
Author:Russell C. Hibbeler
Publisher:PEARSON
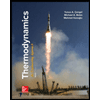
Thermodynamics: An Engineering Approach
Mechanical Engineering
ISBN:9781259822674
Author:Yunus A. Cengel Dr., Michael A. Boles
Publisher:McGraw-Hill Education
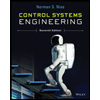
Control Systems Engineering
Mechanical Engineering
ISBN:9781118170519
Author:Norman S. Nise
Publisher:WILEY
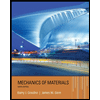
Mechanics of Materials (MindTap Course List)
Mechanical Engineering
ISBN:9781337093347
Author:Barry J. Goodno, James M. Gere
Publisher:Cengage Learning
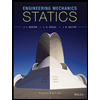
Engineering Mechanics: Statics
Mechanical Engineering
ISBN:9781118807330
Author:James L. Meriam, L. G. Kraige, J. N. Bolton
Publisher:WILEY