IE 312 Joining Module Lab Recitation FA22
docx
keyboard_arrow_up
School
Pennsylvania State University *
*We aren’t endorsed by this school
Course
312
Subject
Mechanical Engineering
Date
Dec 6, 2023
Type
docx
Pages
7
Uploaded by BarristerSandpiperPerson121
Joining Module – 2 hr Recitation With Data for Lab Reports
In Recitation:
-quiz on Machining Module 2/2
-welding and joining fundamentals
-discussion of welding data and lab reports (Week 1/2 and Week 2/2)
Welding Lab Data and Report (Week 1/2):
Weld Property Analysis
Investigate the effect of heat from a welding arc on the hardness (strength) in the fusion zone (FZ or
weld metal) and the heat-affected zone (HAZ) of steel and aluminum welds. The resultant hardness
and strength across the weld depend on the chemistry and microstructure of the material being
welded.
When selecting materials for welded construction,
it is the welded properties in fusion zone
and the HAZ rather than the properties of the base metal that typically limit performance.
Cross Section Through a Steel Weld (polished and etched) to reveal the BM, HAZ and FZ
1
Full penetration butt welds in various materials have been performed, similar to the weld shown.
The load to
failure of the base material before welding and the tensile strength of the final welded joint has been
measured.
In addition, hardness measurements have been made across the weld region from the fusion zone
(FZ), through the heat-affected zone (HAZ), and into the base metal (BM).
Base Metals
AISI 1018 steel – HR condition
AISI 4340 steel – Q&T condition
1100-H14 aluminum
6061-T6 aluminum
Welds Performed
Base Metal
Filler Metal
Welding Process Used
1018 steel
E6013
SMAW
4340 steel
E7018
SMAW
1100-H14 aluminum
1100 and 4043 aluminum
GTAW
6061-T6 aluminum
1100 and 4043 aluminum
GTAW
Data
Steel Welds
sample thickness = 0.125 in.
sample width = 1.0 in.
SMAW conditions:
180 amps, AC, electrode dia. =
0.125 in., no weld pre-heat
Base metal
1018 steel
4330 steel
Electrode type
E6013
E10018
Initial base metal hardness
(HV)
160
423
Base material TS before welding
60,000 psi
180,000 psi
Hardness after welding
(HV)
fusion zone
2 mm from the weld
4 mm in from the weld
6 mm from the weld
10 mm from the weld
20 mm from the weld
170 HV
157 HV
158 HV
159 HV
160 HV
160 HV
380 HV
560 HV
530 HV
520 HV
415 HV
423 HV
Location of fracture
HAZ
HAZ
Welded fracture load
7,500 lbs
15,000 lbs
Fracture type
ductile failure
brittle cracking
2
Aluminum Welds
sample thickness = 0.125 in.
sample width = 1.0 in.
GTAW conditions:
110amps, AC,
argon flow rate = 25 ft
3
/hr
Base metal (BM)
1100-H14
6061-T6
Filler wire type
1100
4043
1100
4043
Initial BM hardness
(HRF)
92
98
Base material TS before welding
15,020 psi
24,050 psi
Hardness after welding
(HRF)
Hardness after welding (HRF)
fusion zone
2mm from the weld
4 mm in from the weld
6 mm from the weld
10 mm from the weld
20 mm from the weld
84
82
84
86
91
92
99
82
84
86
91
92
84
88
90
92
96
98
99
88
90
92
96
98
Location of final fracture
HAZ
HAZ
FZ
HAZ
Welded fracture load (lbs)
1,200 lbs
1,200 lbs
1,775 lbs
2,270 lbs
Fundamental concepts that you need to understand to correctly analyze the Part A data
-What happens to the microstructure and properties of a cold worked material (Ex: 1100-H14) when it
is heated above its recrystallization temperature?
-What happens to the microstructure and properties of a precipitation hardened material (Ex: 6061-T6
aluminum) when it is heated above its solution temperature or above its peak aging temperature?
-What happens to the microstructure and properties in the HAZ of a steel in with good weldability (Ex:
1018 HR steel) when it is cooled rapidly during a typical weld cooling cycle?
-What happens to the microstructure and properties of a steel in the HAZ with poor weldability (Ex:
4330 Q&T steel) when it is cooled rapidly during a typical weld cooling cycle?
Report
(2 pages text, single-spaced + figures and tables)
Comment on the relative strength (hardness) observed in the fusion zone (FZ) and the heat-affected
zone (HAZ) for all of the weld data shown.
For each material describe the specific microstructure
change that happens in the HAZ that is at the root cause of the HAZ hardness changes observed.
Describe welding technique changes that could be used to improve the overall strength (if possible)
for each base metal/filler metal combination.
3
Your preview ends here
Eager to read complete document? Join bartleby learn and gain access to the full version
- Access to all documents
- Unlimited textbook solutions
- 24/7 expert homework help
Welding Lab Data and Report (Week 2/2):
Weld Process Control
Control of arc welding variables is key to producing high quality welds of proper size and shape.
In this task,
we will investigate the effects of flux-cored arc welding (FCAW) variable for making ‘bead-on-plate
”
welds on
AISI 1020 steel.
An automatic torch travel welding device to allow us to control the variables that we want to analyze
by removing human variability from manual FCAW. The device is set up with Flux-Core wire that is also
aided by inert gas (75% Argon and 25% Carbon Dioxide).
A total of 16 weld were made using the
following welding conditions:
4
For each welding condition the welding heat input (kJ/in) can be calculated
Each weld was cross sectioned, ground, polished and etched to reveal the cross-sectional geometry of
the weld beads.
This includes the overall height and width of the weld bead as well as the depth of
penetration into the metal and the amount of reinforcement above the surface of the welded plate.
5
Data
The resultant weld geometry data for each weld is indicated here.
Units are in inches.
Weld Images
6
Your preview ends here
Eager to read complete document? Join bartleby learn and gain access to the full version
- Access to all documents
- Unlimited textbook solutions
- 24/7 expert homework help
Report
(2 pages text, single-spaced + figures and tables)
The FCAW welding guide posted on CANVAS is a useful guide for understanding the influence of
welding conditions on weld bead geometry.
Refer to it for assistance in completing your report.
What is the influence of individual welding variables
and heat input (a combined variable) on the
various aspects of weld bead geometry.
(Data plots and statistical analysis are needed.)
Which
variables have the most dominant effects on the various aspects of weld bead geometry?
Do the results of your experiment agree with the literature?
Discuss.
Problem solving:
Write a 2-paragraph description that would be part of a training guide for new
welders that describes what FCAW welders should do to maintain adequate weld penetration during
manual welding.
Make sure that you include discussion of other significant welding variables that may
have been held constant in the lab data that you analyzed.
7
Related Documents
Related Questions
Note: If you have already answered the problems in this post, kindly ignore it. If not, then answer it. Thank you, Tutor! S.2
Statics of Rigid Bodies
Content Covered:
- Method of Joints
Direction: Create 1 problem based on the topic "Method of Joints" and then solve them with a complete solution. In return, I will give you a good rating. Thank you so much!
Note: Please bear in mind to create 1 problem based on the topic "Method of Joints." Be careful with the calculations in the problem. Kindly double check the solution and answer if there is a deficiency. And also, box the final answer. Thank you so much!
arrow_forward
Assignment activity and guidance
Steel Framework Beam Analysis report
You are presented with the following technical information concerning an I section beam
and a rectangular box section forming part of the steam plant's supporting steel framework
and are asked to produce a report that illustrates the shear force and bending moment
diagrams for the I section beam, and the bending stress distribution diagram for the
rectangular steel box section.
The report will include several calculations of interest to the team:
.
The I section beam's maximum bending moment and its position, and the maximum
stress in the I section beam.
The maximum bending stress in the walls of the rectangular box section.
The I section beam is shown in the diagram below and has a section modulus of 308 cm³
and a depth of 260 mm. It is simply supported at each end over a span AB of X1 metres;
and carries a uniformly distributed load of W1 kN/m over its entire length and a
concentrated load of Y1 kN acting…
arrow_forward
Question 3
You are working on a design team at a small orthopaedic firm. Your team is starting to work on a lower limb
(foot-ankle) prosthesis for individuals who have undergone foot amputation (bone resection at the distal tibia). You remember hearing
about "osseointegration" in an exciting orthopaedic engineering class you attended at Clemson, so you plan to attach the foot
prosthesis using a solid metal rod inserted into the distal tibia. You think stainless steel or titanium alloy might be a useful rod material.
You decide to begin this problem by identifying typical tibial bone anatomy and mechanical behavior (as provided in the tables and
image below). You assume the tibial bone can be modeled as a hollow cylinder of cortical bone, as represented in the image. You
anticipate the length of the rod will be 1/2 the length of the tibia.
Q3G: Critical Thinking: What would you propose to your team as the next step in this analysis? Is it reasonable to assume the rod
will experience the…
arrow_forward
Need help with this
arrow_forward
Help!!! Please answer all Correctly!!! Please
arrow_forward
Help!!! Please answer part B correctly!!! Please
arrow_forward
Help!!! Please answer all Correctly!!! Please
arrow_forward
Assignment Booklet 4B
ce 24: Module 4
6 Identify the safety features shown in this automobile from the following list. Place
your answers in the blank spaces given.
• bumper
• hood
• crumple zones
• roll cage
• side-impact beams
Return to page 75 of the Student Module Booklet and begin Lesson 2.
For questions 7 to 10, read each question carefully. Decide which of the choices BEST
completes the statement or answers the question. Place your answer in the blank
space given.
7. According to Transport Canada, how many Canadians owe their lives to
seat belts between 1990 and 2000?
A. 690
В. 1690
С. 1960
D. 11 690
8. By what percent is the webbing of a seat belt designed to stretch to help
absorb energy in a collision?
A. 0%
B. 5-10%
C. 10-15%
D. 15-20%
9. What is the level of seat belt use in Alberta?
A. 90%
В. 70%
С. 50%
D. 30%
Teacher
arrow_forward
I need parts 8, 9, and 10 answered. Number 1 is an example of how it should be answered.
NOTE: Read the instructions, no where does it say any drawing is required. It is really frustrating when I wait all this time for an answer to a question and some tutor does even read the instructions and just declines it...its ridicilous.
arrow_forward
answer a & b. Please show all your work!!
arrow_forward
LESSON: AUTODESK AUTOCAD
Choose from the choices:
arrow_forward
Create a reading outline for the given text "STRESS and STRAIN".
arrow_forward
This is a practice hw question not graded!!
arrow_forward
Develop a format for technical/lab report writing?
arrow_forward
Can someone please help me to solve ALL of the following questions correctly PLEASE and THANK YOU!!!!!
arrow_forward
ADVANCED CHEMISTRY! RATE WILL BE GIVEN! PLEASE WRITE THE COMPLETE SOLUTIONS
A Steam at 400 deg C an 8,200 kilo Pascals enters a turbine and leaves at 10 kPa. What is the entropy of the leaving steam if the efficiency of the turbine is 0.76. Round the answers in to 2 decimal places.
Hint: Turbine's efficiency is the ratio of work delivered by the actual turbine to the work delivered by an isentropic turbine (no entropy change)
H (kJ/kg)
S (kj/kg-K)
8200 kPa, 400 degrees
3137.6
6.3534
10 kPa, sat. liquid
191.832
0.6493
10 kPa, sat. vapor
2584.8
8.1511
arrow_forward
SEE MORE QUESTIONS
Recommended textbooks for you
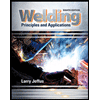
Welding: Principles and Applications (MindTap Cou...
Mechanical Engineering
ISBN:9781305494695
Author:Larry Jeffus
Publisher:Cengage Learning
Related Questions
- Note: If you have already answered the problems in this post, kindly ignore it. If not, then answer it. Thank you, Tutor! S.2 Statics of Rigid Bodies Content Covered: - Method of Joints Direction: Create 1 problem based on the topic "Method of Joints" and then solve them with a complete solution. In return, I will give you a good rating. Thank you so much! Note: Please bear in mind to create 1 problem based on the topic "Method of Joints." Be careful with the calculations in the problem. Kindly double check the solution and answer if there is a deficiency. And also, box the final answer. Thank you so much!arrow_forwardAssignment activity and guidance Steel Framework Beam Analysis report You are presented with the following technical information concerning an I section beam and a rectangular box section forming part of the steam plant's supporting steel framework and are asked to produce a report that illustrates the shear force and bending moment diagrams for the I section beam, and the bending stress distribution diagram for the rectangular steel box section. The report will include several calculations of interest to the team: . The I section beam's maximum bending moment and its position, and the maximum stress in the I section beam. The maximum bending stress in the walls of the rectangular box section. The I section beam is shown in the diagram below and has a section modulus of 308 cm³ and a depth of 260 mm. It is simply supported at each end over a span AB of X1 metres; and carries a uniformly distributed load of W1 kN/m over its entire length and a concentrated load of Y1 kN acting…arrow_forwardQuestion 3 You are working on a design team at a small orthopaedic firm. Your team is starting to work on a lower limb (foot-ankle) prosthesis for individuals who have undergone foot amputation (bone resection at the distal tibia). You remember hearing about "osseointegration" in an exciting orthopaedic engineering class you attended at Clemson, so you plan to attach the foot prosthesis using a solid metal rod inserted into the distal tibia. You think stainless steel or titanium alloy might be a useful rod material. You decide to begin this problem by identifying typical tibial bone anatomy and mechanical behavior (as provided in the tables and image below). You assume the tibial bone can be modeled as a hollow cylinder of cortical bone, as represented in the image. You anticipate the length of the rod will be 1/2 the length of the tibia. Q3G: Critical Thinking: What would you propose to your team as the next step in this analysis? Is it reasonable to assume the rod will experience the…arrow_forward
- Help!!! Please answer all Correctly!!! Pleasearrow_forwardAssignment Booklet 4B ce 24: Module 4 6 Identify the safety features shown in this automobile from the following list. Place your answers in the blank spaces given. • bumper • hood • crumple zones • roll cage • side-impact beams Return to page 75 of the Student Module Booklet and begin Lesson 2. For questions 7 to 10, read each question carefully. Decide which of the choices BEST completes the statement or answers the question. Place your answer in the blank space given. 7. According to Transport Canada, how many Canadians owe their lives to seat belts between 1990 and 2000? A. 690 В. 1690 С. 1960 D. 11 690 8. By what percent is the webbing of a seat belt designed to stretch to help absorb energy in a collision? A. 0% B. 5-10% C. 10-15% D. 15-20% 9. What is the level of seat belt use in Alberta? A. 90% В. 70% С. 50% D. 30% Teacherarrow_forwardI need parts 8, 9, and 10 answered. Number 1 is an example of how it should be answered. NOTE: Read the instructions, no where does it say any drawing is required. It is really frustrating when I wait all this time for an answer to a question and some tutor does even read the instructions and just declines it...its ridicilous.arrow_forward
arrow_back_ios
SEE MORE QUESTIONS
arrow_forward_ios
Recommended textbooks for you
- Welding: Principles and Applications (MindTap Cou...Mechanical EngineeringISBN:9781305494695Author:Larry JeffusPublisher:Cengage Learning
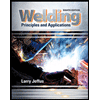
Welding: Principles and Applications (MindTap Cou...
Mechanical Engineering
ISBN:9781305494695
Author:Larry Jeffus
Publisher:Cengage Learning