Assignment #4 - Fernie Memorial Arena Incident
pdf
keyboard_arrow_up
School
Fleming College *
*We aren’t endorsed by this school
Course
MISC
Subject
Mechanical Engineering
Date
Dec 6, 2023
Type
Pages
4
Uploaded by AmbassadorTankVulture29
Assignment #4 - Fernie Memorial Arena Incident Course
Name: Occupational Healthy and Safety
Management
Name: Merlin Shajumon
Student ID: 219905181
Instructor Name: Sarah Gayer
Q1. Could a similar incident have occurred in your workplace (Why or why not?)
I work in a restaurant, and compared to the Fernie Memorial arena, our system is different, less intricate,
and less advanced, thus the likelihood of an incident like the one there happening here is remote.
However, it's critical to be knowledgeable about any potential risks that can exist in a restaurant setting.
Here are a few instances:
•
Dough Mixers: When using dough mixers, contact with the spinning blades might result in hand
injuries.
•
Walk-in Freezer/Refrigerator: Getting trapped inside a walk-in freezer or refrigerator is a possible
risk. Condensation may also make the floors slick in some regions, raising the danger of accidents.
•
Burner or stoves: Getting in touch with hot ranges or stove surfaces poses a burn danger, and there
is also a chance of electric shocks, spills of flame or hot liquid and trips and falls due to open burner
or stove doors.
•
High Shelves: Extending too far to reach objects on high shelves might cause muscle strain.
Additionally, when items are taken off these shelves, there is a chance that they will fall.
•
Lifting: Moving bulky, heavy items around the restaurant might cause muscular strain.
•
Liquids or spills
on the Surface: Any liquids that spill or substances on the floor could pose a trip
and fall risk, leading to possible injury.
To protect the safety and wellbeing of individuals working in the restaurant, it is imperative to address
these possible hazards and adopt the proper preventive measures.
Q2. What hazards were they aware of? Which ones did they miss?
Corrosion brought on by ageing resulted in the development of a small hole in the chiller at the Fernie
Memorial arena. Unfortunately, the required repairs were not made during the 2017 summer seasonal
outage. As a result, the chiller was restarted on October 16 without attending to the pinhole problem. The
operators were also not aware that brine had gotten into the compressor oil. Therefore, only a small
number of the previously shut valves were examined. The following day, there was a major ammonia leak.
The event was cited as the result of a failing refrigeration system and several years of ignored warnings by
WorkSafeBC, a workplace safety organisation.
According to a news source, WorkSafeBC has issued eight citations to the City of Fernie for breaches of the
Workers Compensation Act and Occupational Health and Safety Regulations. A workplace ammonia
exposure management strategy is also missing, as well as frequent workplace inspections that should have
been done to avoid hazardous working conditions.
The refrigeration company in question, Toromont Industries Ltd. (CIMCO Refrigeration), was also found
guilty of two infractions by WorkSafeBC. These infractions involve failing to protect the safety and health
of CIMCO employees, which includes starting maintenance work without properly removing and
controlling any workplace dangers.
Q3. What specific control strategies (e.g. engineering, administrative or personal protective equipment)
did the employer have in place to reduce risk? What control strategies should they have had in place?
The company lacks thorough control methods to lessen the risks associated with ammonia exposure.
Personal protective equipment (PPE), personal ammonia exposure monitors, a backup team, or dedicated
emergency responders weren't in place. Additionally, the employees lacked access to full facepiece
respirators that were effective. The only mechanism they had was an automatic alarm from an ammonia
gas detector that would alert the security firm and fire department in the event of an emergency.
The following control strategies ought to have been used by the organisation, as per
to the Technical Safety
BC report:
•
recognising the threat that ammonia leakage poses and making sure that such hazards are
professionally disclosed.
•
creating policies for owner upkeep and organisational planning to manage and prevent dangers.
•
ensuring that operators, mechanics, and owners' representatives are informed regarding
ammonia-related safety procedures.
•
preparing and building a backup coolant system in case of refrigerant leaks.
•
By developing an open culture around technical systems and keeping communication with the
public transparent, it is possible to guarantee that knowledge about potential risks is freely shared.
Adopting these control measures would have improved everyone's working conditions and helped
reduce the hazards related to ammonia exposure.
Q4.
What was the arena management’s main concern? Could this have led to the death of the
workers?
The video unequivocally demonstrates that repairing and restoring the compressor was the arena
management's top priority to save the curling rink. However, due to the uncertainty surrounding the
ammonia presence at the time, this choice tragically resulted in the death of a worker. The municipal
officials had originally intended to substitute the air compressor in 2013 at a cost of $70,000, according to
the Technical Safety BC (TSBC) study. But because of money issues, they put off replacement till 2014 and
subsequently dropped it entirely from their budgeting.
The investigation claims that "the choice of how to handle the leaking chiller had an important part in the
development of the incident." It goes on to describe that once the leaky chiller was restarted, actions and
choices were made in reaction to a succession of malfunctions that cascaded, exceeding the knowledge
and contextual awareness of individuals involved in those activities.
A chiller typically lasts around 20 and twenty-five years on average. The Fernie chiller had been in
operation for 31 years when it failed. Clearly, the awful fatalities may have been prevented if the
administration had given this issue sufficient thought.
Your preview ends here
Eager to read complete document? Join bartleby learn and gain access to the full version
- Access to all documents
- Unlimited textbook solutions
- 24/7 expert homework help
Q5.
Where the workers following proper protection when going into the arena to fix the problem?
Would the outcome have been different if they had followed proper protection protocol?
The employees that arrived to address the issue lacked the necessary safety measures. The video shows
that they were not using personal ammonia exposure monitors, protective clothing, and gear (PPE),
backup teams, or emergency personnel. Ammonia is a very unpleasant gas that can irritate the skin, eyes,
digestive system, respiratory system, and eyes. It creates an alkaline solution called ammonium hydroxide
when it combines with moisture found in the human body's mucous membranes. The length of time and
the ammonia's concentration all affect how much harm an individual will experience. At 300 parts per
million (ppm) in the air, there is an imminent threat to life and health.
First responders should wear a Level A protective suit and a Chemical, Biological, Radiological, and Nuclear
(CBRN) Self Contained Breathing Apparatus (SCBA) that has been certified by NIOSH for use in hazardous
environments. Up until monitoring establishes the presence and amounts of the pollutant, level A
protection should be kept in place. To lessen contact with the eyes and respiratory system when ammonia
concentrations are below the IDLH limit (300 ppm), full-face respirators with ammonia cartridges can be
utilised. P100 filters should be added to the cartridges in high-humidity conditions to remove mist. Multi-
functional atmosphere-supplying respirators can be utilised when working on refrigeration systems that
could potentially leak ammonia or have unknown exposure levels. Self-contained breathing apparatus
(SCBA) is frequently used in situations involving an ammonia leak and unknown airborne contaminants.
In all Canadian locations, SCBA breathing protection is allowed while accessing potentially dangerous
environments.
The safe work procedure for compressor room maintenance, as detailed in the incident report by
WorkSafeBC, calls for the use of PPE, including a full-facepiece respirator with air-purifying cartridges.
However, none of the personnel involved in the deadly incident were wearing or having any respirators,
and none were discovered at the scene of the occurrence. They were found to be using half-facepiece
respirators, which are not compliant with the requirements for personal protective equipment because
they do not offer eye protection, have a lower protection factor, or satisfy the standards for personal
protective equipment. The workers in Fernie were never given full-facepiece respirators, according to
WorkSafeBC's findings, making it difficult for them to adhere to all safety regulations. Therefore, this
tragedy may have been prevented if the personnel had adhered to the recommended protection protocol.
Related Documents
Related Questions
As an engineer responsible for monitoring works in the area of mechanical systems, you must evaluate the following situation: a large client in the retail area has a refrigeration system where it stores some chilled or frozen products to be sold on the sales floor.Recently, the customer's maintenance department has been questioning the system's performance and requested an evaluation of the system's behavior. You went to the location and requested some information from the maintenance manager about the system, who provided the following data: - The system operates with R-134a refrigerant;- The refrigerated environment is maintained at 0°C and the external environment at 26°C;- The refrigerant flow rate in the system is 0.08 kg/s; In addition to the data provided, you carried out some tests and measured the temperature of the refrigerant fluid at some specific points in the system, such as the compressor inlet and condenser outlet, finding values of 0°C and 26°C respectively.…
arrow_forward
As an engineer responsible for monitoring works in the area of mechanical systems, you must evaluate the following situation: a large client in the retail area has a refrigeration system where it stores some chilled or frozen products to be sold on the sales floor.Recently, the customer's maintenance department has been questioning the system's performance and requested an evaluation of the system's behavior. You went to the location and requested some information from the maintenance manager about the system, who provided the following data: - The system operates with R-134a refrigerant;- The refrigerated environment is maintained at 0°C and the external environment at 26°C;- The refrigerant flow rate in the system is 0.08 kg/s; In addition to the data provided, you carried out some tests and measured the temperature of the refrigerant fluid at some specific points in the system, such as the compressor inlet and condenser outlet, finding values of 0°C and 26°C respectively.…
arrow_forward
Case Study – The New Engineer
Jeff was just hired by GSI, Inc. to be their Environmental and Safety Coordinator. This is Jeff's first position after completing his engineering degree. He had taken a course in safety engineering as part of his studies and felt confident that he could handle the job.
Management at GSI, Inc. has assured him that they are committed to maintaining a safe workplace. They have never had an individual dedicated to this task full-time. They will implement his recommendations if he can justify them.
As Jeff begins to get familiar with the operations, he spends considerable time on the production floor. He notices workers clean their tools before break with a liquid from an unmarked 55-gallon drum. They also use this liquid to clean residue from their skin. They use paper towels to dry their tools and hands, throw these towels in the trash, and head to the break room for a snack and/or smoke.
In talking with the workers, Jeff learns of some of…
arrow_forward
Case Study – The New Engineer
Jeff was just hired by GSI, Inc. to be their Environmental and Safety Coordinator. This is Jeff's first position after completing his engineering degree. He had taken a course in safety engineering as part of his studies and felt confident that he could handle the job.
Management at GSI, Inc. has assured him that they are committed to maintaining a safe workplace. They have never had an individual dedicated to this task full-time. They will implement his recommendations if he can justify them.
As Jeff begins to get familiar with the operations, he spends considerable time on the production floor. He notices workers clean their tools before break with a liquid from an unmarked 55-gallon drum. They also use this liquid to clean residue from their skin. They use paper towels to dry their tools and hands, throw these towels in the trash, and head to the break room for a snack and/or smoke.
In talking with the workers, Jeff learns of some of…
arrow_forward
Help.
arrow_forward
Please answer the 4th question
arrow_forward
Question 2
You are a biomedical engineer working for a small orthopaedic firm that fabricates rectangular shaped fracture
fixation plates from titanium alloy (model = "Ti Fix-It") materials. A recent clinical report documents some problems with the plates
implanted into fractured limbs. Specifically, some plates have become permanently bent while patients are in rehab and doing partial
weight bearing activities.
Your boss asks you to review the technical report that was generated by the previous test engineer (whose job you now have!) and used to
verify the design. The brief report states the following... "Ti Fix-It plates were manufactured from Ti-6Al-4V (grade 5) and machined into
solid 150 mm long beams with a 4 mm thick and 15 mm wide cross section. Each Ti Fix-It plate was loaded in equilibrium in a 4-point bending
test (set-up configuration is provided in drawing below), with an applied load of 1000N. The maximum stress in this set-up was less than the
yield stress for the…
arrow_forward
Topics:
Statics of Rigid Bodies, Equilibrium of Rigid Bodies, Equilibrium in Two Dimensions, etc.
I will rate you with “LIKE/UPVOTE," if it is COMPLETE STEP-BY-STEP SOLUTION.
If it is INCOMPLETE SOLUTION and there are SHORTCUTS OF SOLUTION, I will rate you with “DISLIKE/DOWNVOTE.”
THANK YOU FOR YOUR HELP.
PS: If you have answered this already, don’t answer it again; give chance to other experts to answer it. I want to verify if all of you will arrive in the same final answer; thats why I ask it multiple times. If you answer it again, i'll dislike all your entries/answers.
arrow_forward
Topics:
Statics of Rigid Bodies, Equilibrium of Rigid Bodies, Equilibrium in Two Dimensions, etc.
I will rate you with “LIKE/UPVOTE," if it is COMPLETE STEP-BY-STEP SOLUTION.
If it is INCOMPLETE SOLUTION and there are SHORTCUTS OF SOLUTION, I will rate you with “DISLIKE/DOWNVOTE.”
THANK YOU FOR YOUR HELP.
PS: If you have answered this already, don’t answer it again; give chance to other experts to answer it. I want to verify if all of you will arrive in the same final answer; thats why I ask it multiple times. If you answer it again, i'll dislike all your entries/answers.
arrow_forward
SUBJECT: Industrial Safety Engineering
Do not use chatgpt and draw in handwritten note
Draw decision tree for following machines I. Any one machine tool Pump II. Air compressor III. Internal combustion engine IV. Boiler V. Electrical motors.
arrow_forward
Direction: Graph the heating curve of ethanol using the information given. Check off each item as you add additional information to your graph so that none is missed.
Background information of Ethanol:
Boiling Point = 78 0C
Melting Point = -114 0C
Starting Temperature = -120 0C
After two minutes, frozen cold ethanol starts to melt. It takes two minutes to melt completely.
After eight more minutes, it begins to boil. It boils for six minutes.
Heat is added for two more minutes until ethanol reaches 80 0C.
Label “melting” where this takes place.
Label “vaporization” where this takes place.
Label “phase change” where a phase change occurs.
Indicate where ethanol is only a SOLID, only a LIQUID, and only a GAS.
Of the three phases, label which phase has: weakest IMF, strongest IMF, and medium IMF.
arrow_forward
SEE MORE QUESTIONS
Recommended textbooks for you
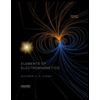
Elements Of Electromagnetics
Mechanical Engineering
ISBN:9780190698614
Author:Sadiku, Matthew N. O.
Publisher:Oxford University Press
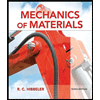
Mechanics of Materials (10th Edition)
Mechanical Engineering
ISBN:9780134319650
Author:Russell C. Hibbeler
Publisher:PEARSON
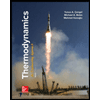
Thermodynamics: An Engineering Approach
Mechanical Engineering
ISBN:9781259822674
Author:Yunus A. Cengel Dr., Michael A. Boles
Publisher:McGraw-Hill Education
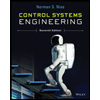
Control Systems Engineering
Mechanical Engineering
ISBN:9781118170519
Author:Norman S. Nise
Publisher:WILEY
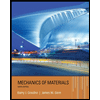
Mechanics of Materials (MindTap Course List)
Mechanical Engineering
ISBN:9781337093347
Author:Barry J. Goodno, James M. Gere
Publisher:Cengage Learning
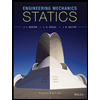
Engineering Mechanics: Statics
Mechanical Engineering
ISBN:9781118807330
Author:James L. Meriam, L. G. Kraige, J. N. Bolton
Publisher:WILEY
Related Questions
- As an engineer responsible for monitoring works in the area of mechanical systems, you must evaluate the following situation: a large client in the retail area has a refrigeration system where it stores some chilled or frozen products to be sold on the sales floor.Recently, the customer's maintenance department has been questioning the system's performance and requested an evaluation of the system's behavior. You went to the location and requested some information from the maintenance manager about the system, who provided the following data: - The system operates with R-134a refrigerant;- The refrigerated environment is maintained at 0°C and the external environment at 26°C;- The refrigerant flow rate in the system is 0.08 kg/s; In addition to the data provided, you carried out some tests and measured the temperature of the refrigerant fluid at some specific points in the system, such as the compressor inlet and condenser outlet, finding values of 0°C and 26°C respectively.…arrow_forwardAs an engineer responsible for monitoring works in the area of mechanical systems, you must evaluate the following situation: a large client in the retail area has a refrigeration system where it stores some chilled or frozen products to be sold on the sales floor.Recently, the customer's maintenance department has been questioning the system's performance and requested an evaluation of the system's behavior. You went to the location and requested some information from the maintenance manager about the system, who provided the following data: - The system operates with R-134a refrigerant;- The refrigerated environment is maintained at 0°C and the external environment at 26°C;- The refrigerant flow rate in the system is 0.08 kg/s; In addition to the data provided, you carried out some tests and measured the temperature of the refrigerant fluid at some specific points in the system, such as the compressor inlet and condenser outlet, finding values of 0°C and 26°C respectively.…arrow_forwardCase Study – The New Engineer Jeff was just hired by GSI, Inc. to be their Environmental and Safety Coordinator. This is Jeff's first position after completing his engineering degree. He had taken a course in safety engineering as part of his studies and felt confident that he could handle the job. Management at GSI, Inc. has assured him that they are committed to maintaining a safe workplace. They have never had an individual dedicated to this task full-time. They will implement his recommendations if he can justify them. As Jeff begins to get familiar with the operations, he spends considerable time on the production floor. He notices workers clean their tools before break with a liquid from an unmarked 55-gallon drum. They also use this liquid to clean residue from their skin. They use paper towels to dry their tools and hands, throw these towels in the trash, and head to the break room for a snack and/or smoke. In talking with the workers, Jeff learns of some of…arrow_forward
- Case Study – The New Engineer Jeff was just hired by GSI, Inc. to be their Environmental and Safety Coordinator. This is Jeff's first position after completing his engineering degree. He had taken a course in safety engineering as part of his studies and felt confident that he could handle the job. Management at GSI, Inc. has assured him that they are committed to maintaining a safe workplace. They have never had an individual dedicated to this task full-time. They will implement his recommendations if he can justify them. As Jeff begins to get familiar with the operations, he spends considerable time on the production floor. He notices workers clean their tools before break with a liquid from an unmarked 55-gallon drum. They also use this liquid to clean residue from their skin. They use paper towels to dry their tools and hands, throw these towels in the trash, and head to the break room for a snack and/or smoke. In talking with the workers, Jeff learns of some of…arrow_forwardHelp.arrow_forwardPlease answer the 4th questionarrow_forward
- Question 2 You are a biomedical engineer working for a small orthopaedic firm that fabricates rectangular shaped fracture fixation plates from titanium alloy (model = "Ti Fix-It") materials. A recent clinical report documents some problems with the plates implanted into fractured limbs. Specifically, some plates have become permanently bent while patients are in rehab and doing partial weight bearing activities. Your boss asks you to review the technical report that was generated by the previous test engineer (whose job you now have!) and used to verify the design. The brief report states the following... "Ti Fix-It plates were manufactured from Ti-6Al-4V (grade 5) and machined into solid 150 mm long beams with a 4 mm thick and 15 mm wide cross section. Each Ti Fix-It plate was loaded in equilibrium in a 4-point bending test (set-up configuration is provided in drawing below), with an applied load of 1000N. The maximum stress in this set-up was less than the yield stress for the…arrow_forwardTopics: Statics of Rigid Bodies, Equilibrium of Rigid Bodies, Equilibrium in Two Dimensions, etc. I will rate you with “LIKE/UPVOTE," if it is COMPLETE STEP-BY-STEP SOLUTION. If it is INCOMPLETE SOLUTION and there are SHORTCUTS OF SOLUTION, I will rate you with “DISLIKE/DOWNVOTE.” THANK YOU FOR YOUR HELP. PS: If you have answered this already, don’t answer it again; give chance to other experts to answer it. I want to verify if all of you will arrive in the same final answer; thats why I ask it multiple times. If you answer it again, i'll dislike all your entries/answers.arrow_forwardTopics: Statics of Rigid Bodies, Equilibrium of Rigid Bodies, Equilibrium in Two Dimensions, etc. I will rate you with “LIKE/UPVOTE," if it is COMPLETE STEP-BY-STEP SOLUTION. If it is INCOMPLETE SOLUTION and there are SHORTCUTS OF SOLUTION, I will rate you with “DISLIKE/DOWNVOTE.” THANK YOU FOR YOUR HELP. PS: If you have answered this already, don’t answer it again; give chance to other experts to answer it. I want to verify if all of you will arrive in the same final answer; thats why I ask it multiple times. If you answer it again, i'll dislike all your entries/answers.arrow_forward
- SUBJECT: Industrial Safety Engineering Do not use chatgpt and draw in handwritten note Draw decision tree for following machines I. Any one machine tool Pump II. Air compressor III. Internal combustion engine IV. Boiler V. Electrical motors.arrow_forwardDirection: Graph the heating curve of ethanol using the information given. Check off each item as you add additional information to your graph so that none is missed. Background information of Ethanol: Boiling Point = 78 0C Melting Point = -114 0C Starting Temperature = -120 0C After two minutes, frozen cold ethanol starts to melt. It takes two minutes to melt completely. After eight more minutes, it begins to boil. It boils for six minutes. Heat is added for two more minutes until ethanol reaches 80 0C. Label “melting” where this takes place. Label “vaporization” where this takes place. Label “phase change” where a phase change occurs. Indicate where ethanol is only a SOLID, only a LIQUID, and only a GAS. Of the three phases, label which phase has: weakest IMF, strongest IMF, and medium IMF.arrow_forward
arrow_back_ios
arrow_forward_ios
Recommended textbooks for you
- Elements Of ElectromagneticsMechanical EngineeringISBN:9780190698614Author:Sadiku, Matthew N. O.Publisher:Oxford University PressMechanics of Materials (10th Edition)Mechanical EngineeringISBN:9780134319650Author:Russell C. HibbelerPublisher:PEARSONThermodynamics: An Engineering ApproachMechanical EngineeringISBN:9781259822674Author:Yunus A. Cengel Dr., Michael A. BolesPublisher:McGraw-Hill Education
- Control Systems EngineeringMechanical EngineeringISBN:9781118170519Author:Norman S. NisePublisher:WILEYMechanics of Materials (MindTap Course List)Mechanical EngineeringISBN:9781337093347Author:Barry J. Goodno, James M. GerePublisher:Cengage LearningEngineering Mechanics: StaticsMechanical EngineeringISBN:9781118807330Author:James L. Meriam, L. G. Kraige, J. N. BoltonPublisher:WILEY
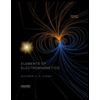
Elements Of Electromagnetics
Mechanical Engineering
ISBN:9780190698614
Author:Sadiku, Matthew N. O.
Publisher:Oxford University Press
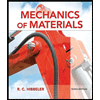
Mechanics of Materials (10th Edition)
Mechanical Engineering
ISBN:9780134319650
Author:Russell C. Hibbeler
Publisher:PEARSON
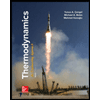
Thermodynamics: An Engineering Approach
Mechanical Engineering
ISBN:9781259822674
Author:Yunus A. Cengel Dr., Michael A. Boles
Publisher:McGraw-Hill Education
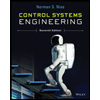
Control Systems Engineering
Mechanical Engineering
ISBN:9781118170519
Author:Norman S. Nise
Publisher:WILEY
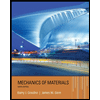
Mechanics of Materials (MindTap Course List)
Mechanical Engineering
ISBN:9781337093347
Author:Barry J. Goodno, James M. Gere
Publisher:Cengage Learning
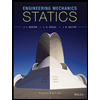
Engineering Mechanics: Statics
Mechanical Engineering
ISBN:9781118807330
Author:James L. Meriam, L. G. Kraige, J. N. Bolton
Publisher:WILEY