CEE 320L Lab_03_Group 9
docx
keyboard_arrow_up
School
University of Hawaii *
*We aren’t endorsed by this school
Course
320
Subject
Mechanical Engineering
Date
Dec 6, 2023
Type
docx
Pages
21
Uploaded by MinisterTank8797
CEE 320 Fluid Mechanics Fundamentals Lab
Calibration of a Venturi Flow Meter
Almard Pasion
Jason Nguyen
Eulamai Tingco
Kailah Vergara
University of Hawaii at Manoa
CEE 320L Fluid Mechanics
November 03, 2023
CEE 320L Fluid Mechanics
Fall 2023
Laboratory (No.3)
EXECUTIVE SUMMARY
The aim of this project was to evaluate the Venturi flow meter, which enabled an accuracy
assessment and the effectiveness of the Venturi apparatus. Through the utilization of
mathematical equations, the team validated whether the anticipated calculated values for the flow
rate closely corresponded to the readings obtained from the instrumentation with roughly an 8%
difference between values. These findings contributed to a deeper comprehension of the
connection between pressure differentials and flow discharges.
By processing the raw data obtained from the Venturi flow meter and associated equipment,
the team conducted several calculations to determine the flow discharge, pressure differential,
Reynolds number, and calibration constant. The group concluded elevations in pressure resulted
in heightened flow discharge. Additionally, the Reynolds number had a negligible impact on the
calibration constant.
Page
i
CEE 320L Fluid Mechanics
Fall 2023
Laboratory (No.3)
TABLE OF CONTENTS
EXECUTIVE SUMMARY………………...
……………………………………………………………...i
1
INTRODUCTION
..................................................................................................................
1
1.1
B
ACKGROUND
....................................................................................................................
1
1.2
R
EASON
FOR
E
XPERIMENT
................................................................................................
1
1.3
T
HEORY
.............................................................................................................................
2
1.4
O
BJECTIVE
.........................................................................................................................
2
2
APPROACH
...........................................................................................................................
2
2.1
T
EST
S
ETUP
AND
I
NSTRUMENTATION
................................................................................
2
2.2
T
EST
S
PECIMENS
...............................................................................................................
6
2.3
T
EST
P
ROCEDURE
..............................................................................................................
6
3
RESULTS
................................................................................................................................
7
3.1
T
ABLES
..............................................................................................................................
7
4
ANALYSIS/ERROR
.............................................................................................................
11
4.1
T
ABLES
............................................................................................................................
11
4.2
T
HE
VERIFICATION
OF
Q
AND
∆ P
THROUGH
COMPUTATION
.....................................
11
4.3
T
HE
ADVANTAGES
OF
L
OG
-
LOG
PLOTTING
......................................................................
11
4.4
P
ROPAGATED
E
RROR
........................................................................................................
12
4.5
E
RRORS
(
RANDOM
,
SYSTEMATIC
,
ETC
.)
...........................................................................
12
5
CONCLUSIONS/RECOMMENDATIONS
.......................................................................
12
6
REFERENCES
.....................................................................................................................
13
7
APPENDIX
...........................................................................................................................
14
TABLE OF FIGURES
Figure 2-1: Venturi Pump
................................................................................................................
3
Figure 2-2: Adjust flow valves
........................................................................................................
4
Figure 2-3:
Pressure gauge
.............................................................................................................
4
Figure 2-4: Weighing tank with flowing water
................................................................................
5
Figure 2-5: Water pipe system
.........................................................................................................
5
Figure 2-6: Pressure gauge in operation during the tests
.................................................................
6
Figure 3-1: Linear relationship between the Reynold’s number and the calibration constant
........
9
Figure 3-2: Log-log graph – the relationship between pressure difference and the volumetric flow
rate
.................................................................................................................................................
10
TABLE OF TABLES
Table 2-1: Material list
.....................................................................................................................
6
Page
ii
Your preview ends here
Eager to read complete document? Join bartleby learn and gain access to the full version
- Access to all documents
- Unlimited textbook solutions
- 24/7 expert homework help
CEE 320L Fluid Mechanics
Fall 2023
Laboratory (No.3)
Table 3-1 - Experimental Values for the water drainage time over 50 lb weight intervals and the
corresponding change in pressure for 7 trials
..................................................................................
7
Table 3-2 - Calculated flow rate, calibration factor, initial velocity, and Reynolds number form
experiment values (data passed on Table 4.1)
.................................................................................
8
Table 3-3 - Comparison of calculated flow rate values
...................................................................
9
Table 3-4 - Propagated error for each measurement
......................................................................
10
Table 7-1 – Raw experimental data
...............................................................................................
17
Page
iii
CEE 320L Fluid Mechanics
Fall 2023
Laboratory (No.3)
1
Introduction
1.1
Background
In the realm of engineering, you'll be introduced to a variety of flow meter instruments, and
one of these instruments utilized in our experiment was the Venturi flow meter. The Venturi flow
meter gauges the flow rate of a fluid by narrowing the cross-sectional area in the flow path,
thereby generating a pressure differential. At this point of pressure variance, the fluid is directed
through a pressure recovery exit section, where it can recover as much as 80% of the pressure
differential created at the narrowest point. This phenomenon adheres to the Bernoulli Equation.
To assess and validate the performance of this specific flow meter, a standard procedure known
as calibration is employed. Calibration is the method of configuring an instrument to provide
results for samples within an acceptable range. The Venturi effect refers to the phenomenon of
fluid pressure drop that occurs when a fluid passes through a narrow segment of a pipe. As the
velocity of the fluid increases within the constriction, there is a corresponding decrease in
pressure. The underlying concept corresponds to the continuity equation in the field of fluid
mechanics. In the case of an incompressible fluid, it is important that the mass flow rate remains
constant at all locations within a pipe, even when alterations in cross-sectional area occur.
1.2
Reason for Experiment
Accuracy is of utmost importance in all flow measurement applications. Flow rate
measurements are significant in critical applications such as municipal water delivery and
chemical processing, as any inaccuracies might have severe consequences. The utilization of a
well calibrated venturi tube effectively reduces measurement errors and uncertainty. Technicians
Page
1
CEE 320L Fluid Mechanics
Fall 2023
Laboratory (No.3)
conduct calibration testing on the venturi meter at different flow rates to determine the
calibration constant C prior to its installation.
1.3
Theory
In this laboratory experiment, we investigated the Venturi Flow Meter's capability to
measure flow while minimizing pressure loss. The unique design and structure of the Venturi
facilitated the precise measurement of a small pressure differential, which was then compared to
the flow discharge. To determine the pressure differential, we measured pressure both upstream
and at the throat of the Venturi flow meter.
1.4
Objective
The primary goals of this laboratory experiment encompassed enhancing the precision in the
measurement of flow values obtained from the Venturi flow meter. Furthermore, the experiment
sought to reaffirm the fundamental connection between flow rates and pressure differentials,
thereby contributing to a more comprehensive understanding of the Venturi flow meter's
performance characteristics.
2
Approach
2.1
Test Setup and Instrumentation
To begin with, the experiment necessitated the use of a Venturi pump to induce a pressure
differential within the water flow. Figure 2-1 provides an illustration of the actual Venturi pump
employed during the experiment. In addition, valves were affixed to the pipeline to regulate the
water flow and maintain a consistent flow rate, with Figure 2-2 depicting the specific valve
responsible for adjusting the water flow rate. This valve was positioned downstream of the
Venturi pump. To monitor the pressure differential, a pressure gauge was affixed to the Venturi
Page
2
Your preview ends here
Eager to read complete document? Join bartleby learn and gain access to the full version
- Access to all documents
- Unlimited textbook solutions
- 24/7 expert homework help
CEE 320L Fluid Mechanics
Fall 2023
Laboratory (No.3)
pump, enabling the measurement of the pressure disparity between the pipe and the Venturi
throat. Figure 2-3 presents a visual depiction of the pressure gauge utilized in the experiment,
complete with multiple tubes for calculating an average pressure difference. The quantification
of water flow involved the use of a weight scale, which measured the quantity of water passing
through the pipe. Figure 2-4 showcases the weight scale employed in this capacity. Lastly, a
network of water pipes interconnected all the instruments, facilitating the seamless flow of water
through the entire experimental setup. Figure 2-5 illustrates the tubing that served as the conduit
for the experiment, ensuring the transportation of water to and from the respective instruments.
Figure 2.6 shows the pressure gage in operation during the testing phase of the experiment. For
an overview of the experimental setup and the instruments used, please refer to Figures 2-1, 2-2,
2-3, 2-4, 2-5, and 2-6.
Figure 2-1: Venturi Pump
Page
3
CEE 320L Fluid Mechanics
Fall 2023
Laboratory (No.3)
Figure 2-2: Adjust flow valves.
Figure 2-3:
Pressure gauge
Page
4
CEE 320L Fluid Mechanics
Fall 2023
Laboratory (No.3)
Figure 2-4: Weighing tank with flowing water.
Figure 2-5: Water pipe system
Page
5
Your preview ends here
Eager to read complete document? Join bartleby learn and gain access to the full version
- Access to all documents
- Unlimited textbook solutions
- 24/7 expert homework help
CEE 320L Fluid Mechanics
Fall 2023
Laboratory (No.3)
Figure 2-6: Pressure gauge in operation during the tests.
2.2
Test Specimens
Table 2-1: Material list
Material List
Venturi meter pump
Flow valve
Pressure gage
Weight scale/Weighing tank
Stopwatch
2.3
Test Procedure
The procedure commenced by activating both the pump and the downstream valve. During
this phase, water circulated from the sump through the piping system, traversing the Venturi, and
then returning to the sump by way of the open valve leading to the weighing tank. The valve near
the pump was fine-tuned to establish the initial ten discrete flow cycles through the system.
Students were divided into two groups, with one stationed near the weighing tank and the other
positioned near the pressure gauge. The dump valve for the weighing tank was sealed to collect
Page
6
CEE 320L Fluid Mechanics
Fall 2023
Laboratory (No.3)
water, and at this juncture, the first group documented the initial and final weights, noting the
time interval using a stopwatch. Simultaneously, the second group recorded the pressure
differential readings, which served as the basis for the gauge reading.
3
Results
3.1
Tables
Table 3-2 - Experimental Values for the water drainage time over 50 lb weight intervals and
the corresponding change in pressure for 7 trials.
Trials
ΔW
(
lb
)
ΔP
(
psi
)
ΔP
(
psf
)
Δt ,
(
s
)
1
50
4.3
619.2
6.24
2
50
3.8
574.2
7.8
3
50
3.4
489.6
8.01
4
50
3
432
7.42
5
50
2.5
360
7.67
6
50
1.9
273.6
8.81
7
50
0.6
86.4
15.64
Table 3-3 - Calculated flow rate, calibration factor, initial velocity, and Reynolds number
form experiment values (data passed on Table 4.1)
Trials
Q (
ft
3
/
s
¿
C
V
1
(
ft
s
)
Re
1
0.13
0.9
18.5
1988.3
2
0.103
0.78
14.8
1590.6
Page
7
CEE 320L Fluid Mechanics
Fall 2023
Laboratory (No.3)
3
0.1
0.79
14.4
1548.9
4
0.109
0.91
15.6
1672.1
5
0.104
0.962
15.04
1617.6
6
0.09
0.961
13.1
1408.3
7
0.05
0.963
7.3
793.3
Figure 3-7: Linear relationship between the Reynolds’ number and the calibration
constant.
Table 3-4 - Comparison of calculated flow rate values.
Trials
Q
2
=CK(
∆ P
1
/
2
¿
(
ft
3
/
s
¿
Q
1
=
∆ P
¿
α
β
¿
Percent
Difference
(%)
1
0.13
0.12
8.0
2
0.103
0.114
10.1
3
0.1
0.11
9.5
4
0.107
0.103
9.79
Page
8
Your preview ends here
Eager to read complete document? Join bartleby learn and gain access to the full version
- Access to all documents
- Unlimited textbook solutions
- 24/7 expert homework help
CEE 320L Fluid Mechanics
Fall 2023
Laboratory (No.3)
5
0.104
0.096
8.0
6
0.09
0.086
4.54
7
0.05
0.053
5.83
% Difference Mean
7.97
Figure 3-8: Log-log graph – the relationship between pressure difference and the
volumetric flow rate.
Table 3-5 - Propagated error for each measurement
(
∆t
)/
t
(s)
(
∆W
)/
W
(lb)
∆
(
∆ P
)/
∆ P
(psi)
∆C
/
C
C
∆C
0.00160256
0.01
0.01162791
0.01741652
0.9
0.015675
0.00128205
0.01
0.01315789
0.017861
0.78
0.013932
0.00124844
0.01
0.01470588
0.01860138
0.79
0.014695
0.00134771
0.01
0.01666667
0.01968105
0.91
0.01791
0.00130378
0.01
0.02
0.02130378
0.962
0.020494
0.00113507
0.01
0.02631579
0.02429297
0.961
0.023346
0.00063939
0.01
0.08333333
0.05230606
0.963
0.050371
Page
9
CEE 320L Fluid Mechanics
Fall 2023
Laboratory (No.3)
∆
(
∆W
)
=
0.5
lb
,
∆
(
∆t
)
=
0.01
s
,
∆
(
∆P
)
=
0.05
psi
4
Analysis/Error
4.1
Tables 3.1 – 3.4
The raw experimental data gathered throughout the seven trials is displayed in Table 3.1: The
constant weight of water in the weighing tank, denoted as ΔW, is 50 pounds. The measured
pressure difference, expressed in psi, between the venturi input and throat is called ΔP. As the
flow rate is lowered, these falls. Table 3.2 consists of the volumetric flow rate, or Q, is
determined using ΔW and Δt. The calibration constant C is determined by utilizing the values of
Q and ΔP. Based on Q, V1 is the starting velocity in the input pipe. The Reynolds’ number, or
Re, indicates whether a flow is turbulent or laminar. The measured Q values and those derived
from the ΔP vs. Q relationship are contrasted in Table 3.3. The calibration is confirmed by the
near match. The propagating measurement uncertainty based on errors in ΔW, Δt, and ΔP is
displayed in Table 3.4. Reasonably minor mistakes are shown by ΔC/C values.
4.2
The verification of Q and
∆ P
through computation.
Within an 8% discrepancy, the flow rates Q2 computed using the calibration constant
equation nearly correspond to the flow rates Q1 found using the ΔP vs. Q connection. This
confirms the basic idea between pressure drop and flow rate by showing that the measured ΔP
values agree well with the measured flow rates Q. Calculation approximations or tiny
measurement errors may be the cause of slight discrepancies. The calibration of the venturi meter
is validated overall by the agreement.
4.3
The advantages of Log-log plotting.
Over a broad range of values, the power law relationship between ΔP and Q is linearized
by log-log scaling. This facilitates the generation of the formula linking the variables by making
Page
10
CEE 320L Fluid Mechanics
Fall 2023
Laboratory (No.3)
it simple to identify the exponents α and β. Higher flow rates would result in the values being
squeezed on a normal scale. For improved viewing, log-log spreads them out. Log - log scale
also provides information about possible measurement mistakes or departures from the best
possible theoretical behavior.
4.4
Propagated Error
Based on errors in W, t, and ΔP, the partial derivates were deduced to estimate the relative
error ΔC/C. The partial derivatives can be found in the appendix of this lab report.
4.5
Errors (random, systematic, etc.)
Random errors expected from uncertainty in reading analog scales and stopwatches.
Approximations in calculations and curve fitting could also contribute to errors. Systematic
errors could occur in pressure or flow measurements if instruments are mis-calibrated.
5
Conclusions/Recommendations
Through the “Calibration of a Venturi Flow Meter” experiment, we explored the Venturi
flow meter’s performance by the recorded pressure, time, weight, calibration factor, initial
velocity, and Reynolds number. The experiment reaffirmed the essential connection between the
flow rates and pressure differentials, to understand the Venturi flow meter’s capabilities and
significance in various applications. Examining the calculated results, the following can be
concluded:
Based on table 3-3, the mean percentage difference is around 8%.
Based on table 3-4, the average calibration factor is 0.90.
Page
11
Your preview ends here
Eager to read complete document? Join bartleby learn and gain access to the full version
- Access to all documents
- Unlimited textbook solutions
- 24/7 expert homework help
CEE 320L Fluid Mechanics
Fall 2023
Laboratory (No.3)
The relationship between the volumetric flow rate (Q) and Pressure differential (ΔP) was
determined by the exponential function derived. The relationship was shown in Figure 4-2.
The calculated flow rates Q2 closely align with the measured flow rates Q1 with an 8%
discrepancy, which confirmed the relationship between pressure drop and flow rate.
The advantage of using a log-log scale when overseeing the range of the values collected is
that it compressed it into a more manageable linear range. Compared to utilizing a power
function, it allowed for the development of a formula which would accurately calculate the
flow rates based on the data collected such as pressure.
Recommendations that can be used to improve the experiment if done again:
More than one person is to record the time the trails. With the average of the recorded time
for each trial, the time data would be more accurate.
To ensure an accurate time measure when the tank is filled to a particular weight, the water in
the tank should be removed for each trial for little errors to occur.
6
References
Gerhart. (n.d.).
Video library
. Gerhart, Hochstein: Munson, Young and Okiishi’s Fundamentals
of Fluid Mechanics, 8th Edition - Instructor Companion Site.
https://bcs.wiley.com/hebcs/Books?
action=resource&bcsId=9930&itemId=1119080703&resourceId=39618
Hyoungsu, Park (2023).
Lab3_F23.
Retrieved from
Page
12
CEE 320L Fluid Mechanics
Fall 2023
Laboratory (No.3)
https://laulima.hawaii.edu/access/content/group/MAN.XLSCEE320hp.202410/Lab/Lab3/la
b3_F23.pdf
7
Appendix
A-1 Equations:
Bernoulli Equation:
P
1
+
1
2
ρv
1
2
+
z
1
=
P
2
+
1
2
ρv
2
2
+
z
2
Alternative version:
P
1
+
1
2
ρv
1
2
+
ρgh
1
=
P
+
1
2
ρv
2
2
+
ρg h
2
P: pressure
ρ
:
density
v
:
Fluid Velocity
g
:
Force of gravity
h
:
height
Volumetric Discharge:
Q
=
∆W
γ ∆t
Q: Volumetric Discharge
γ
: Specific weight of water (9.807
kN
/
m
3
)
∆W
: Weight flow rate
∆t
: Avg measured time.
Pertinent Overall Equation:
Q
=
CK
√
∆P
, where K and C can be found using:
K
=
A
2
√
2
g
γ
[
1
−
(
D
1
D
2
)
]
C
=
Q
K
√
∆ P
Page
13
CEE 320L Fluid Mechanics
Fall 2023
Laboratory (No.3)
Q: Volumetric Discharge
C: Calibration constant
K: Constant for a given venturi installation
∆ P
: Pressure difference
*
Q
=
β
(
Δ p
)
α
ß Relationship between Q and
Δ p
.
Initial Velocity:
D
1
¿
2
π
4
¿
V
1
=
Q
A
1
=
Q
¿
V
1
: Initial Velocity
Q: Volumetric Discharge
A
1
: Area of section 1
Flow Discharge Difference:
∆Q
=
|
Q
2
−
Q
1
|
Q
2
+
Q
1
2
×
100%
∆Q
: Flow discharge difference
Q
2
: Experimental values of flow rate or volumetric discharge
Q
1
: Graphed values of flow rate or volumetric discharge
Reynolds Number
:
R
e
=
VD
ν
R
e
:
Reynolds number
V
:
Fluid Velocity
Page
14
Your preview ends here
Eager to read complete document? Join bartleby learn and gain access to the full version
- Access to all documents
- Unlimited textbook solutions
- 24/7 expert homework help
CEE 320L Fluid Mechanics
Fall 2023
Laboratory (No.3)
D
:
Diameter
ν
:
Fluid Kinematic Viscosity
Error
Propagation
–
from
W,
t,
and
∆ P
to
C:
∆C
=
∂f
∂W
∆W
+
∂ f
∂t
∆t
+
∂f
∂
(
∆ P
)
∆
(
∆ P
)
W: measured weight
t: measured time
∆ P
: measured pressure differential
Partial Derivatives for Error Propagation:
Given:
C
=
f
(
W ,t ,∆ P
)
=
W
Kγt √∆ P
,
∆C
=
∂f
∂W
∆W
+
∂ f
∂t
∆t
+
∂f
∂
(
∆ P
)
∆
(
∆ P
)
∂ f
∂W
∆W
=
(
W
Kγt
√
∆ P
)
d
dW
=
W
(
1
Kγt
√
∆ P
)
d
dW
=
(
1
Kγt
√
∆ P
)
(
∂ f
∂t
∆W
C
)
=
(
1
Kγt
√
∆ P
)
W
Kγt
√
∆ P
=
∆W
W
∂f
∂t
∆ t
=
(
W
Kγt
√
∆ P
)
d
dt
=
(
W
Kγ
√
∆ P
)
t
−
1
d
dt
=
−
W
Kγ
√
∆ P
(
t
−
2
)
(
∂ f
∂t
∆t
C
)
=
−
W
Kγ
√
∆P
(
t
−
2
)
W
Kγt
√
∆ P
=
−
−
W
Kγt
2
√
∆P
W
Kγt
√
∆ P
=
−
∆t
t
=
|
−
∆t
t
|
=
∆t
t
Page
15
CEE 320L Fluid Mechanics
Fall 2023
Laboratory (No.3)
∂ f
∂
(
∆P
)
∆
(
∆ P
)=
(
W
Kγt
√
∆ P
)
d
d ∆P
=
−
W
2
Kγt
√
∆ P
3
(
∂ f
∂t
∆
(
∆ P
)
C
)
=
−
W
2
Kγt
√
∆ P
3
W
Kγt
√
∆ P
=
−
1
∆ P
(
∆ P
)
2
∆ P
=
|
−
1
∆ P
(
∆ P
)
2
∆P
|
=
1
∆
(
∆ P
)
2
∆ P
∨
1
2
∆
(
∆ P
)
∆P
Therefore, with the partial derivatives and the calibration constant, the relative error formula is:
∆C
C
=
¿
∆W
W
+
∆t
t
+
1
∆
(
∆ P
)
2
∆ P
.
A-2 Sample Calculations:
Table 3.1
*Using sample 1.
psi to psf:
0.6
psi
(
144
¿
2
ft
2
)=
86.4
psf
Table 3.2
*Using sample 1.
Q
=
∆W
γ ∆t
=
50
lb
62.41
lb
ft
3
(
6.24
s
)
=
0.128389
C =
0.13
f t
3
/
s
0.006
√
86.4
psf
=
0.96
3
V
1
=
0.13
f t
3
/
s
π
4
(
2
12
ft
)
2
=
7.3
ft
/
s
Re =
18.5
ft
/
s
(
2
12
ft
)
0.00155
=
793.3
Table 3.3
Q
2
=
0.963
⋅
0.0057
√
86.4
=
0.05
f t
3
/
s
*Using sample 7.
Q
1
=
0.0082
⋅
86.4
0.4179
=
0.053
f t
3
/
s
*Using sample 7.
Page
16
CEE 320L Fluid Mechanics
Fall 2023
Laboratory (No.3)
% difference:
|
Q
2
−
Q
1
|
Q
2
+
Q
1
2
×
100%
=
|
0.05
−
0.053
|
0.05
+
0.053
2
×
100%
=
5.8252%
*Using sample 7.
x
=
∑
x
n
=
8
+
10.1
+
9.5
+
9.79
+
8
+
4.54
+
5.83
7
=
7.96642
Table 3.4
*Using sample 1.
(
∆t
)
t
(
s
)
=
0.01
6.24
=
0.00160256
(
∆W
)
W
(
lb
)
=
0.5
50
=
0.01
∆
(
∆ P
)
∆ P
(
psi
)
=
0.05
4.3
=
0.01162791
∆C
C
=
(
∆W
)
W
+
(
∆t
)
t
+
1
2
∆
(
∆ P
)
∆ P
=
0.01
+
0.00160256
+
1
2
(
0.01162791
)
=
¿
0.01741652
∆C
=
∆C
C
(
C
)
=
0.01741652
(
0.9
)
=
0.015675
A-2
Raw Data:
Table 7-6 – Raw experimental data
Trials
Weight (lb)
Time (s)
Gage Pressure (psi)
1
50
6.24
4.3
2
50
7.8
3.8
3
50
8.01
3.4
4
50
7.42
3
5
50
7.67
2.5
6
50
8.81
1.9
7
50
15.64
0.6
Page
17
Your preview ends here
Eager to read complete document? Join bartleby learn and gain access to the full version
- Access to all documents
- Unlimited textbook solutions
- 24/7 expert homework help
Related Documents
Related Questions
QUESTION 7
A model tow-tank test is conducted on a bare hull model at the model design
speed in calm water. Determine the effective horsepower (hp) for the ship,
including appendage and air resistances. The following parameters apply to the
ship and model:
Ship
1,100
Model
Length (ft)
Hull Wetted Surface Area (ft2)
Speed (knots)
30
250,000
15
Freshwater
Water
Seawater 50°F
70°F
Projected Transverse Area (ft²)
Cair
7,500
0.875
Appendage Resistance (% of bare hull)
10%
Hull Resistance (Ibf)
20
arrow_forward
Question 7
The following formulas are commonly used by engineers to predict the lift and drag of an airfoil:
where L and Dare the lift and drag forces, V is the airspeed, S is the wing span, is the air density, and CL and CD are the lift and drag coefficients. Both CL and CD depend on α , the angle of attack, the angle between the relative air velocity and the airfoil’s chord line.
Wind tunnel experiments for a particular airfoil have resulted in the following formulas.
where α is in degrees.
arrow_forward
Question 4
Viscosity. From studies of the flow of neutrophils in micropipets, it is possible to
measure the apparent viscosity of the cytoplasm. From the data below, do you
think the cytoplasm is Newtonian? If not, determine the rheological relationship
that best describes the behavior of the cytoplasmic viscosity
Shear rate (s1) Apparent Viscosity
(Pa s)
450
0.111
1
137
2.70
97
5.75
58
7
58
arrow_forward
C
Dynamic Analysis and Aeroelasticity
SECTION B
Answer TWO questions from this section
ENG2012-N
The moment of inertia of a helicopter's rotor is 320kg. m². The rotor starts from rest
and at t = 0, the pilot begins by advancing the throttle so that the torque exerted on
the rotor by the engine (in N.m) is modelled by as a function of time (in seconds) by
T = 250t.
a) How long does it take the rotor to turn ten revolutions?
b) What is the rotor's angular velocity (in RPM) when it has turned ten
revolutions?
arrow_forward
Chapter 12 - Lecture Notes.pptx: (MAE 272-01) (SP25) DY...
Scores
arrow_forward
Subject: Air Pollution Formation and Control
Do not just copy and paster other online answers
arrow_forward
Question 7
arrow_forward
Record the dimensions of the known (calibration) block using the caliper and dial gauge on the table below. Indicate the
units of each measurement. Calculate the average length of each side of the block.
Dimension
Caliper (Units)
0.995
1.455
0.985
Ruler(in) A: 0.9
B: 1.5
C: 0.9
A
B
C
Dimension
A
B
Instrument
Use the average dimensions (see Problem 2a) of the known block to calibrate the LVDT at your workstation. Record the
voltage on the table below:
LVDT Offset: 0.556 (Do not include the offset value in your average dimensions)
C
Ave Dimension (Units)
(Dial Gauge)
0.997
1.659
0.949
0.964 in
1.538 in
0.945 in
oltage
Average Dimension
1.244 volt
1.994
1.28
0.964 in
1.538 in
0.945 in
arrow_forward
this is a practice problem, not a graded assignment
arrow_forward
University of Babylon
Collage of Engineering\Al-Musayab
Department of Automobile
Engineering
Under Grad/Third stage
Notes:
1-Attempt Four Questions.
2- Q4 Must be Answered
3-Assume any missing data.
4 تسلم الأسئلة بعد الامتحان مع الدفتر
Subject: Mechanical
Element Design I
Date: 2022\01\25
2022-2023
Time: Three Hours
Course 1
Attempt 1
Q1/ Design a thin cylindrical pressure tank (pressure vessel) with hemispherical ends to the
automotive industry, shown in figure I below. Design for an infinite life by finding the
appropriate thickness of the vessel to carry a sinusoidal pressure varied from {(-0.1) to (6) Mpa}.
The vessel is made from Stainless Steel Alloy-Type 316 sheet annealed. The operating
temperature is 80 C° and the dimeter of the cylinder is 36 cm. use a safety factor of 1.8.
Fig. 1
(15 Marks)
Q2/ Answer the following:
1- Derive the design equation for the direct evaluation of the diameter of a shaft to a desired
fatigue safety factor, if the shaft subjected to both fluctuated…
arrow_forward
Access Pearson
Mastering Engineering
Back to my courses
Course Home
Course Home
Scores
Review
Next >
arrow_forward
Don't Use Chat GPT Will Upvote
arrow_forward
https://eagleonline.hccs.edu/courses/156500/quizzes/969413/take
Question 40
5 pts
A pressure gauge on a tank reads 25 psi. What is the absolute pressure in atmospheres and psia?
Formular:
1 atm = 760 mmHg = 76 cm Hg = 14.7 psia =29.92 in Hg = 33.91 feet H2O
%3D
%3D
%3D
Pabs
Pgauge + Patm
where
Pabs is absolute pressure
Pgauge is gauge pressure
Patm is atmospheric pressure
Upload
Choosc a File
Subimit Quiz
arrow_forward
CHAPTER 5 : DIESEL ENGINE POWER PLANT
A six cylinder, four-stroke CI engine is tested against a water brake dynamometer for which
B.P = WN/17x10' in kW, where W is the brake load in newton and N is the speed of the
engine in the r.p.m. The air consumption was measured by means of a sharp edged orifice.
During the test following observersations were taken :
• Bore
• Stroke
• Speed
• Brake load
Barometer reading
= 10 cm
= 14 cm
= 2500 rpm
= 480 N
= 76 cm Hg
• Orifice diameter
• Co-efficient of discharge of orifice
• Pressure drop across orifice
• Room temperature
Fuel Consumption
= 3.3 cm
= 0.62
= 14 cm of Hg
= 25°C
= 0.32 kg/min
Calculate following :
i.
The volumetric efficiency
The brake mean effective pressure ( b.m.e.p)
The engine torque
The brake specific fuel consumption ( b.s.f.c )
ii.
iv.
arrow_forward
Access Pearson
Mastering Engineering
Back to my courses
Course Home
Course Home
Scores
arrow_forward
I want to briefly summarize what he is talking about and what you conclude.
pls very urgent
arrow_forward
00
T
R
%24
Bb R
V qa
du/webapps/assessment/take/launch.jsp?course_assessment_id%=_254968_1&course_id%3D 3565256_1&content id= 52826
* Question Completion Status:
Attach File
Browse Local Files
Browse Content Collection
QUESTION 2
A company needs to choose one supplier for a particular type of silicon wafer used'in the production of
semiconductors. The company has three options. Supplier A sells the silicon wafers for $2.50 per wafer,
independently of the number of wafers ordered. Supplier B sells the wafers for $2.40 each but does not
consider an order for less than 2,000 wafers. Supplier C sells the wafers for $2.30 each but does not accept
an order for less than 3,000 wafers. Assume an order setup cost of $100 and an annual requirement of 20,000
wafers. Assume a 20% annual interest rate for holding cost calculations.
a. Which supplier should be chosen to minimize the total annual cost for the wafers, and what is the
optimal order quantity?
b. If the replenishment lead time for wafers…
arrow_forward
Thermodynamics question. please help
(2nd Attachment is the table question B is referring to)
arrow_forward
Please correctly answer all parts of the question. Thank you will upvote if correct!
arrow_forward
Chrome
File
Edit
View
History
Bookmarks
People
Tab
Window
Help
McGraw-Hill Campus - ALEKS Science - CHM1045 GEN CHEM 1 BLENDED 669113
A bconline.broward.edu/d21/le/content/466883/fullscreen/12868783/View
McGraw-Hill Campus - ALEKS Science
O GASES
Interconverting pressure and force
A chemistry graduate student is designing a pressure vessel for an experiment. The vessel will contain gases at pressures up to 470.0 MPa. The student's
design calls for an observation port on the side of the vessel (see diagram below). The bolts that hold the cover of this port onto the vessel can safely withstand
a force of 2.80 MN.
pressure vessel
bolts
side
View
port
Calculate the maximum safe diameter w of the port. Round your answer to the nearest 0.1 cm.
O cm
Explanation
Check
O2021 McGraw-Hill Education. All Rights Reserved. Terms of Use
FEB
arrow_forward
1. To determine the dynamic viscosity of a liquid you take repeated measurements of the liquid density and kinematic
viscosity. These data are summarized in the following table:
Avg. measurement
Total Uncertainty
P
999 kg/m³
±0.5%
V
1.23 mm²/s
±0.01 mm²/s
kg
Ns
What is the dynamic viscosity? Give dynamic viscosity in units of; which is the same as
ms
2. Determine the absolute and relative uncertainties in the dynamic viscosity.
arrow_forward
SEE MORE QUESTIONS
Recommended textbooks for you
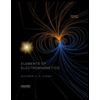
Elements Of Electromagnetics
Mechanical Engineering
ISBN:9780190698614
Author:Sadiku, Matthew N. O.
Publisher:Oxford University Press
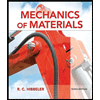
Mechanics of Materials (10th Edition)
Mechanical Engineering
ISBN:9780134319650
Author:Russell C. Hibbeler
Publisher:PEARSON
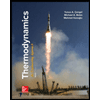
Thermodynamics: An Engineering Approach
Mechanical Engineering
ISBN:9781259822674
Author:Yunus A. Cengel Dr., Michael A. Boles
Publisher:McGraw-Hill Education
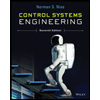
Control Systems Engineering
Mechanical Engineering
ISBN:9781118170519
Author:Norman S. Nise
Publisher:WILEY
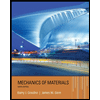
Mechanics of Materials (MindTap Course List)
Mechanical Engineering
ISBN:9781337093347
Author:Barry J. Goodno, James M. Gere
Publisher:Cengage Learning
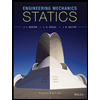
Engineering Mechanics: Statics
Mechanical Engineering
ISBN:9781118807330
Author:James L. Meriam, L. G. Kraige, J. N. Bolton
Publisher:WILEY
Related Questions
- QUESTION 7 A model tow-tank test is conducted on a bare hull model at the model design speed in calm water. Determine the effective horsepower (hp) for the ship, including appendage and air resistances. The following parameters apply to the ship and model: Ship 1,100 Model Length (ft) Hull Wetted Surface Area (ft2) Speed (knots) 30 250,000 15 Freshwater Water Seawater 50°F 70°F Projected Transverse Area (ft²) Cair 7,500 0.875 Appendage Resistance (% of bare hull) 10% Hull Resistance (Ibf) 20arrow_forwardQuestion 7 The following formulas are commonly used by engineers to predict the lift and drag of an airfoil: where L and Dare the lift and drag forces, V is the airspeed, S is the wing span, is the air density, and CL and CD are the lift and drag coefficients. Both CL and CD depend on α , the angle of attack, the angle between the relative air velocity and the airfoil’s chord line. Wind tunnel experiments for a particular airfoil have resulted in the following formulas. where α is in degrees.arrow_forwardQuestion 4 Viscosity. From studies of the flow of neutrophils in micropipets, it is possible to measure the apparent viscosity of the cytoplasm. From the data below, do you think the cytoplasm is Newtonian? If not, determine the rheological relationship that best describes the behavior of the cytoplasmic viscosity Shear rate (s1) Apparent Viscosity (Pa s) 450 0.111 1 137 2.70 97 5.75 58 7 58arrow_forward
- C Dynamic Analysis and Aeroelasticity SECTION B Answer TWO questions from this section ENG2012-N The moment of inertia of a helicopter's rotor is 320kg. m². The rotor starts from rest and at t = 0, the pilot begins by advancing the throttle so that the torque exerted on the rotor by the engine (in N.m) is modelled by as a function of time (in seconds) by T = 250t. a) How long does it take the rotor to turn ten revolutions? b) What is the rotor's angular velocity (in RPM) when it has turned ten revolutions?arrow_forwardChapter 12 - Lecture Notes.pptx: (MAE 272-01) (SP25) DY... Scoresarrow_forwardSubject: Air Pollution Formation and Control Do not just copy and paster other online answersarrow_forward
- Question 7arrow_forwardRecord the dimensions of the known (calibration) block using the caliper and dial gauge on the table below. Indicate the units of each measurement. Calculate the average length of each side of the block. Dimension Caliper (Units) 0.995 1.455 0.985 Ruler(in) A: 0.9 B: 1.5 C: 0.9 A B C Dimension A B Instrument Use the average dimensions (see Problem 2a) of the known block to calibrate the LVDT at your workstation. Record the voltage on the table below: LVDT Offset: 0.556 (Do not include the offset value in your average dimensions) C Ave Dimension (Units) (Dial Gauge) 0.997 1.659 0.949 0.964 in 1.538 in 0.945 in oltage Average Dimension 1.244 volt 1.994 1.28 0.964 in 1.538 in 0.945 inarrow_forwardthis is a practice problem, not a graded assignmentarrow_forward
- University of Babylon Collage of Engineering\Al-Musayab Department of Automobile Engineering Under Grad/Third stage Notes: 1-Attempt Four Questions. 2- Q4 Must be Answered 3-Assume any missing data. 4 تسلم الأسئلة بعد الامتحان مع الدفتر Subject: Mechanical Element Design I Date: 2022\01\25 2022-2023 Time: Three Hours Course 1 Attempt 1 Q1/ Design a thin cylindrical pressure tank (pressure vessel) with hemispherical ends to the automotive industry, shown in figure I below. Design for an infinite life by finding the appropriate thickness of the vessel to carry a sinusoidal pressure varied from {(-0.1) to (6) Mpa}. The vessel is made from Stainless Steel Alloy-Type 316 sheet annealed. The operating temperature is 80 C° and the dimeter of the cylinder is 36 cm. use a safety factor of 1.8. Fig. 1 (15 Marks) Q2/ Answer the following: 1- Derive the design equation for the direct evaluation of the diameter of a shaft to a desired fatigue safety factor, if the shaft subjected to both fluctuated…arrow_forwardAccess Pearson Mastering Engineering Back to my courses Course Home Course Home Scores Review Next >arrow_forwardDon't Use Chat GPT Will Upvotearrow_forward
arrow_back_ios
SEE MORE QUESTIONS
arrow_forward_ios
Recommended textbooks for you
- Elements Of ElectromagneticsMechanical EngineeringISBN:9780190698614Author:Sadiku, Matthew N. O.Publisher:Oxford University PressMechanics of Materials (10th Edition)Mechanical EngineeringISBN:9780134319650Author:Russell C. HibbelerPublisher:PEARSONThermodynamics: An Engineering ApproachMechanical EngineeringISBN:9781259822674Author:Yunus A. Cengel Dr., Michael A. BolesPublisher:McGraw-Hill Education
- Control Systems EngineeringMechanical EngineeringISBN:9781118170519Author:Norman S. NisePublisher:WILEYMechanics of Materials (MindTap Course List)Mechanical EngineeringISBN:9781337093347Author:Barry J. Goodno, James M. GerePublisher:Cengage LearningEngineering Mechanics: StaticsMechanical EngineeringISBN:9781118807330Author:James L. Meriam, L. G. Kraige, J. N. BoltonPublisher:WILEY
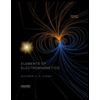
Elements Of Electromagnetics
Mechanical Engineering
ISBN:9780190698614
Author:Sadiku, Matthew N. O.
Publisher:Oxford University Press
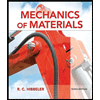
Mechanics of Materials (10th Edition)
Mechanical Engineering
ISBN:9780134319650
Author:Russell C. Hibbeler
Publisher:PEARSON
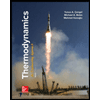
Thermodynamics: An Engineering Approach
Mechanical Engineering
ISBN:9781259822674
Author:Yunus A. Cengel Dr., Michael A. Boles
Publisher:McGraw-Hill Education
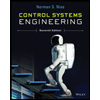
Control Systems Engineering
Mechanical Engineering
ISBN:9781118170519
Author:Norman S. Nise
Publisher:WILEY
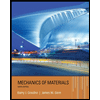
Mechanics of Materials (MindTap Course List)
Mechanical Engineering
ISBN:9781337093347
Author:Barry J. Goodno, James M. Gere
Publisher:Cengage Learning
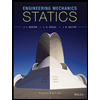
Engineering Mechanics: Statics
Mechanical Engineering
ISBN:9781118807330
Author:James L. Meriam, L. G. Kraige, J. N. Bolton
Publisher:WILEY