AURLTQ012 WRITTERN ASSESSMENT ANAS IJAZ 20220490
docx
keyboard_arrow_up
School
Cambridge International College, Australia *
*We aren’t endorsed by this school
Course
MISC
Subject
Mechanical Engineering
Date
Feb 20, 2024
Type
docx
Pages
24
Uploaded by anas4343
AURLTQ012 Diagnose and repair light vehicle drive shafts
Assessment 1 – Questioning – Written Assessment
Student Name
Anas ijaz
Student ID Number
20220490
Unit Start Date
02/04/2023
Unit End Date
31/04/2023
Assessment Due Date
27/04/2023
Date Submitted
26/04/2023
This cover sheet is to be completed by the student and assessor and used as a record to determine student competency in this assessment task
The assessment process and tasks were fully explained.
Yes / No
I am aware of which evidence will be collected and how.
Yes / No
I am aware of my right to appeal an assessment decision.
Yes / No
I am aware that I can locate The RTO Complaints and Appeals Policy and Procedure on their website at (Insert Website Link)
Yes / No
I have discussed any additional educational support or reasonable adjustments I require in order to undertake this assessment with the Student Support Services Officer and Trainer / Assessor, (if applicable). e.g. Student Handbook and Access and Equity Policy (Insert Website Link)
Yes / No
I have access to all required resources?
Yes / No
Cheating & Plagiarism Declaration
Student Declaration: In accordance with The RTO Plagiarism Policy, I hereby acknowledge by signing this declaration that I have not cheated or plagiarised any work regarding the assessment tasks undertaken in this unit of competency except where the work has been correctly acknowledged.
NOTE: Student must sign this prior to submitting their assessments to the assessor
Signature
ANAS Ijaz
Date
:
26
/ 04
/ 2023
Assessment Results
Satisfactory
or
Not Yet Satisfactory
(Please circle the assessment result for this task)
Feedback to Student - Please provide general feedback on the Student’s performance
Document Name:
Student Written Knowledge Assessment – AURLTQ012
Created Date:
12
th
Aug 2020
Document No:
Trinity Institute (Australia) – AURLTQ012
Version No:
1.0
Last Modified
Date:
©Trinity Institute (Australia) | RTO Code: 41310 | CRICOS Code: 03556F
Page Sequence:
Page 1 of 24
AURLTQ012 Diagnose and repair light vehicle drive
shafts
Student Declaration: - I verify that the work completed is my own and that I was adequately informed of the assessment process prior to commencing this assessment task.
Assessor Declaration: - I verify that I have adequately
explained and negotiated the assessment tasks with
the student prior to commencing assessment.
Student Name: anas ijaz
Assessor’s Name:
Student Signature anas ijaz
Date 26/04/2023
Assessor Signature
Date
Student Guide for Written Knowledge Assessment
Overview of Assessment
This is a written assessment task you will be assess on your knowledge of diagnosing
and repairing light vehicle drive shafts.
The topics that will be covered in the assessment are:
1
Diagnose light vehicle drive shafts
2
Repair and test light vehicle drive shafts
3
Complete work processes
This assessment will ensure that the elements, performance criteria, performance
evidence and knowledge evidence required, and conditions are adhered to demonstrate
competency in this unit assessment task.
•
Read the assessment carefully before commencing.
•
Your Assessor will use the assessment criteria in this document and will provide feedback / comment.
•
You MUST
answer all the questions in the assessment tasks in your own words and own handwriting.
•
This is an “Open Book” assessment, and students can use the resources listed in the “Resources Required” section below.
Task/s to be assessed
To complete this written assessment, you will need to answer the 52
questions comprising of Multiple Choice, True and False, Fill-in the Gap and Short Answer questions.
Time allowed
On average, the Assessment should take 4 – 6 hours to complete.
Location
This theory assessment will be completed in a classroom under the supervision of a trainer/assessor.
Decision making
rules
To receive a ‘satisfactory’ outcome for this assessment students MUST
successfully answer all questions. If a student achieves less than 100%, they can reattempt the assessment after further study has taken place. Students who cannot achieve a minimum of 100% you will not have satisfactorily completed this assessment
Document Name:
Student Written Knowledge Assessment – AURLTQ012
Created Date:
12
th
Aug 2020
Document No:
Trinity Institute (Australia) – AURLTQ012
Version No:
1.0
Last Modified
Date:
©Trinity Institute (Australia) | RTO Code: 41310 | CRICOS Code: 03556F
Page Sequence:
Page 2 of 24
AURLTQ012 Diagnose and repair light vehicle drive
shafts
Your assessor will be looking for the following in this assessment task: -
•
Key policies and procedures relating to the diagnosis, testing and repair of light vehicle drive shafts, including:
o
How to locate and identify manufacturers specifications or equivalent documentation and workplace procedures for the diagnosis and repair of light vehicle drive shafts
o
The following workplace health and safety requirements for diagnosis and repair of light vehicle drive shafts:
–
Safety procedures for working with hazardous oils
•
The following environmental requirements for diagnosis and repair of light vehicle drive shafts:
o
Procedures for trapping, storing and disposing of oils released from drive shafts
•
The following diagnostic testing procedures for light vehicle drive shafts:
o
Road testing that include drive shaft noise and vibration
•
The following repair procedures for light vehicle drive shafts:
o
Dismantling drive shafts
o
Inspecting drive shafts
o
Reassembling and aligning components
•
Post-repair testing procedures for light vehicle drive shafts
•
Workplace housekeeping procedures
•
Light vehicle drive shafts and associated components information, including:
o
The operating principles of:
–
Torque reaction of rear axle housings
–
Torque steer
o
The purpose and operation of the following propeller shafts:
–
Single and multi-piece shafts
–
Universal joints
–
Cross and yoke joints
–
Double cardan joints
–
Lobro joints
–
Velocity fluctuation of universal joints
–
Shaft alignment
o
The purpose and operation of the following constant velocity joints:
-
Tripod joints.
Assessment conditions
The assessment MUST
:
•
Include access to:
o
An automotive repair workplace or simulated workplace that reflects workplace conditions - where simulation is used, it MUST
reflect real working conditions by modelling industry operating conditions and contingencies, as well as, using suitable facilities, equipment and resources
o
Repair orders and workplace instructions relating to diagnose and repair activity
o
Workplace procedures relating to diagnose and repair activity
o
Manufacturer light vehicle drive shaft specifications and procedures or
Document Name:
Student Written Knowledge Assessment – AURLTQ012
Created Date:
12
th
Aug 2020
Document No:
Trinity Institute (Australia) – AURLTQ012
Version No:
1.0
Last Modified
Date:
©Trinity Institute (Australia) | RTO Code: 41310 | CRICOS Code: 03556F
Page Sequence:
Page 3 of 24
Your preview ends here
Eager to read complete document? Join bartleby learn and gain access to the full version
- Access to all documents
- Unlimited textbook solutions
- 24/7 expert homework help
Document Name:
Student Written Knowledge Assessment – AURLTQ012
Created Date:
12
th
Aug 2020
Document No:
Trinity Institute (Australia) – AURLTQ012
Version No:
1.0
Last Modified
Date:
©Trinity Institute (Australia) | RTO Code: 41310 | CRICOS Code: 03556F
Page Sequence:
Page 4 of 24
AURLTQ012 Diagnose and repair light vehicle drive
shafts
equivalent documentation to complete diagnose and repair activity
o
Light vehicle with front engine and rear wheel drive
o
Light vehicle with front wheel drive constant velocity joint drive shaft
o
Diagnostic equipment for light vehicle drive shafts
o
Tools, equipment and materials required for repair of light vehicle drive shafts
•
Be demonstrated in the workplace or in a simulated environment that reflects workplace conditions
•
Be conducted in a safe environment
•
Automotive repair workplace or simulated workplace
•
Be assessed in compliance with relevant policies, procedures, processes
and operational manuals directly related to the industry sector for which it is
being assessed
•
Confirm consistent performance can be applied in a range of relevant
workplace circumstances.
Assessor Requirements
Assessors of this unit MUST
:
•
Satisfy the assessor requirements in applicable vocational education and training legislation, frameworks and/or standards.
Resources required
Learning Resources available to students include:
•
Automotive Technology (A System Approach) 6
th
Edition – Chapters 5, 6, 7, & 40
•
Websites
•
Trainer Handouts
Results/Re- assessment
•
The Assessor will grade the assessment and record the result on the front page of this document (S) – Satisfactory if all observable behaviours are correct and (NS) not satisfactory if any areas are left incorrect
•
Feedback will be provided on either result
•
Where a student receives a ‘NS – Not Satisfactory’ result, the assessor will discuss the area of the non-compliant observable behaviour and an opportunity given for re- assessment. This may be through direct observation or a different method of assessment e.g. verbal/oral questioning, problem solving exercise.
•
If the outcome is again not satisfactory the student result will be deemed (NYC) not
yet competent. Additional feedback will be given, and a time agreed upon for further assessment after additional training and skills practice has taken place, this information will be recorded, dated and signed in the re-assessment area on the last page of this document
•
Where all the assessment tasks have been graded (S) Satisfactory, the student will
be deemed C – Competent for the practical component and the result recorded
and signed in the area indicated on the last page of this document
Reasonable Adjustment
If the participant is unable to undertake the written assessment as designed, an interview (verbal questioning) may be used as an alternate approach.
Document Name:
Student Written Knowledge Assessment – AURLTQ012
Created Date:
12
th
Aug 2020
Document No:
Trinity Institute (Australia) – AURLTQ012
Version No:
1.0
Last Modified
Date:
©Trinity Institute (Australia) | RTO Code: 41310 | CRICOS Code: 03556F
Page Sequence:
Page 5 of 24
AURLTQ012 Diagnose and repair light vehicle drive shafts
Assessment 1 – Questioning
Written Assessment
1.
Identify five (5) important items of personal safety when working on drive shafts in an automotive workplace?
1
Wearing helmet important to protect oneself from head injuries
2
Wearing safety eyewear is needed to protect from eye injuries
3
Correct clothing must be worn
4
Gloves should be worn
5
Hearing should be protect with ear equipment
2.
What are the precautions that you should be aware of when handling final drive oil?
It is important to wear gloves and safety shoes to ensure safety.
It is significant not to strike or drop the Linear Bushing as it can result in damage or injury.
3.
How should waste final drive oils be stored and disposed?
The waste oil should be collected in a secure drum with clear labelled. If the oil is stored in a double-skinned tank then bunding is not needed. If disposing the product should be properly disposed as industrial waste such as dumping in landfills, incineration or dust suppression (Sikdar, Siddaiah and Menezes, 2020).
Multiple choice. Circle the correct answer
4.
When removing the drive shafts, what should you use to catch the waste final drive oil?
A.
Drain
pan. B.
Mop bucket.
C.
Storm water drain.
D.
Funnel.
AURLTQ012 Diagnose and repair light vehicle drive shafts
Document Name:
Student Written Knowledge Assessment – AURLTQ012
Created Date:
12
th
Aug 2020
Document No:
Trinity Institute (Australia) – AURLTQ012
Version No:
1.0
Last Modified
Date:
©Trinity Institute (Australia) | RTO Code: 41310 | CRICOS Code: 03556F
Page Sequence:
Page 6 of 24
5.
When handling, trapping, storing and disposing of new or waste final drive oils, which document should you use to find this information?
It is essential to use the workshop manual
True or False question
6.
Torque reaction is when the axle housing tries to rotate in a direction opposite to wheel rotation
☒ True
or
☐ False
7.
What is torque steer?
Torque steer is when the power is applied in an uneven manner to the drive wheel (Dornhege, Nolden and Mayer, 2017).
8.
Name the eight [8] components of a drive shaft below.
Your preview ends here
Eager to read complete document? Join bartleby learn and gain access to the full version
- Access to all documents
- Unlimited textbook solutions
- 24/7 expert homework help
AURLTQ012 Diagnose and repair light vehicle drive shafts
Document Name:
Student Written Knowledge Assessment – AURLTQ012
Created Date:
12
th
Aug 2020
Document No:
Trinity Institute (Australia) – AURLTQ012
Version No:
1.0
Last Modified
Date:
©Trinity Institute (Australia) | RTO Code: 41310 | CRICOS Code: 03556F
Page Sequence:
Page 7 of 24
1
Slip Yoke
2
External
3
Spider
4
Bearing
5
Internal
6
Drive shaft
7
Flange
8
Universal Joint
Multiple choice. Circle the correct answer
9.
Drive shafts are made of .
A.
Seamless
steel
tubing.
B.
Reinforced fiberglass.
C.
Aluminium.
D.
All answers are correct.
10.
What is a slip yoke?
A slip yoke is a crucial component of a drive shaft assembly as it helps the PTOs and drive shafts to slip or flex with their given application. It assists in the rotation of U-joints (Sakai, Yoshidaand Tajima, 2018).
Fill in the Gaps
11.
Complete the following statement about propeller shafts using the following words.
Words: Compress, Differential, Drive, Engine, Length, Power, Transmission, Torque, U-joints
1
Bearing cups
2
Seal
3
Bearing
4
Trunnion
5
Grease Fitting
AURLTQ012 Diagnose and repair light vehicle drive shafts
Document Name:
Student Written Knowledge Assessment – AURLTQ012
Created Date:
12
th
Aug 2020
Document No:
Trinity Institute (Australia) – AURLTQ012
Version No:
1.0
Last Modified
Date:
©Trinity Institute (Australia) | RTO Code: 41310 | CRICOS Code: 03556F
Page Sequence:
Page 8 of 24
A drive shaft must smoothly transfer torque
while rotating, changing length, and moving up and
down. The different designs of drive
shafts all attempt to ensure a vibration-free transfer of the engine’s power
from the transmission to the differential. This goal is complicated by the fact that the differential
and transmission are bolted solidly to the frame of the car, whereas the
engine
is mounted on springs. As the rear wheels go over bumps in the road or changes in the
road’s surface, the springs compress
or expand, changing the angle of the drive shaft between
the transmission
and the differential, as well as the distance between the two. To allow for these changes, the Hotchkiss-type drive shaft is fitted with one or more U-joint
to permit variations in the angle of the drive, and a slip joint that permits the effective length
of the drive shaft to change.
True or False question
12.
Two-piece drive shafts have a drive shaft support bearing called a centre bearing.
☒ True
or
☐ False
13.
Name the five [5] components of a universal joint below.
True or False question
14.
U-joints rotate at a constant velocity and are vibration free.
☐
True
or
☒ False
AURLTQ012 Diagnose and repair light vehicle drive shafts
Document Name:
Student Written Knowledge Assessment – AURLTQ012
Created Date:
12
th
Aug 2020
Document No:
Trinity Institute (Australia) – AURLTQ012
Version No:
1.0
Last Modified
Date:
©Trinity Institute (Australia) | RTO Code: 41310 | CRICOS Code: 03556F
Page Sequence:
Page 9 of 24
Multiple choice. Circle the correct answer
15.
The bearing cups of a conventional U-joint are retained by .
A.
A snap ring that fits into a groove machined in the outer end of the yoke.
B.
An external snap ring that fits into a groove machined in the bearing cup on the end closest to the grease seal.
C.
Nylon injected into machined grooves in the yoke and cup. D.
All answers are correct.
True or False question
16.
A universal joint is a flexible coupling located at each end of the drive shaft between the slip yoke and the pinion flange on the drive axle assembly.
☐
True
or
☒ False
True or False question
17.
The U-joint is basically a double-hinged joint consisting of two Y-shaped yokes, one on the driving or input shaft and the other on the driven or output shaft, plus a cross-shaped unit called the cross.
☒ True
or
☐ False
18.
Name the three (3) common designs of U-joints:
1
Cardan Joint
2
Spicer Joint
3
Bendix-Weiss
Fill in the Gaps
19.
Complete the following statement about Löbro constant-velocity joint using the following words.
Your preview ends here
Eager to read complete document? Join bartleby learn and gain access to the full version
- Access to all documents
- Unlimited textbook solutions
- 24/7 expert homework help
2
Boot Band
3
Rubber packaging
4
Boot
5
Washer
6
Balls
8
Companion flange
9
Outer race
10
Inclined ball
11
Inner Race
12
Cage
AURLTQ012 Diagnose and repair light vehicle drive shafts
Words: Cage, Centre, Changes, Drive, Flange, Inner, Joint, Race, Propeller
A Löbro constant velocity joint
, has an outer race, an inner race and a cage
with
steel balls. The outer race is bolted to the flange
of the front propeller shaft, and the inner race is splined to the front end of the rear drive
shaft. The joint is enclosed by a dust shield and boot. The front shaft is supported by a _
centre
bearing.
This type of joint is designed to allow changes
in propeller shaft angle and also changes in propeller shaft length. Both the inner
race and the outer race have angular grooves for the balls. The balls transfer propeller
from one race to the other but, at the same time, the inner
race
is able to move in or out in the grooves or change its angle.
20.
Name the twelve [12] components of a Löbro constant-velocity joint below.
1
Tulip
7
Snap ring
Document Name:
Student Written Knowledge Assessment – AURLTQ012
Created Date:
12
th
Aug 2020
Document No:
Trinity Institute (Australia) – AURLTQ012
Version No:
1.0
Last Modified
Date:
©Trinity Institute (Australia) | RTO Code: 41310 | CRICOS Code: 03556F
Page Sequence:
Page 10 of 24
AURLTQ012 Diagnose and repair light vehicle drive shafts
Document Name:
Student Written Knowledge Assessment – AURLTQ012
Created Date:
12
th
Aug 2020
Document No:
Trinity Institute (Australia) – AURLTQ012
Version No:
1.0
Last Modified
Date:
©Trinity Institute (Australia) | RTO Code: 41310 | CRICOS Code: 03556F
Page Sequence:
Page 11 of 24
AURLTQ012 Diagnose and repair light vehicle drive shafts
Document Name:
Student Written Knowledge Assessment – AURLTQ012
Created Date:
12
th
Aug 2020
Document No:
Trinity Institute (Australia) – AURLTQ012
Version No:
1.0
Last Modified
Date:
©Trinity Institute (Australia) | RTO Code: 41310 | CRICOS Code: 03556F
Page Sequence:
Page 12 of 24
True or False question
21.
U-joint operating angle is determined by taking the difference between the transmission installation angle and the drive shaft installation angle.
☐
True
or
☒ False
22.
What does the term “constant velocity” mean?
Constant velocity is the term used when an object in motion is moving in a straight line at a constant speed. This velocity can be either positive or negative and is usually indicated by the sign of the slope (Schöller et al
., 2020). This helps in analysing the direction in which the object is moving. For example, a bus traveling at a constant speed without changing its direction.
True or False question
23.
In a two-piece driveshaft, when the yokes are in the same plane, the joints are said to be in phase.
☐
True
or
☒ False
24.
What is meant by U-joint phasing?
Phasing is the process that helps in aligning the universal joint yokes on both ends of a drive shaft in a parallel manner (Liu et al
., 2020). If these joints are note phased in a proper manner then they will start operating at different speed throughout each revolution which might result in second order vibration.
Your preview ends here
Eager to read complete document? Join bartleby learn and gain access to the full version
- Access to all documents
- Unlimited textbook solutions
- 24/7 expert homework help
AURLTQ012 Diagnose and repair light vehicle drive shafts
Document Name:
Student Written Knowledge Assessment – AURLTQ012
Created Date:
12
th
Aug 2020
Document No:
Trinity Institute (Australia) – AURLTQ012
Version No:
1.0
Last Modified
Date:
©Trinity Institute (Australia) | RTO Code: 41310 | CRICOS Code: 03556F
Page Sequence:
Page 13 of 24
1
Boots
2
CV joint
3
Stub Axle
4
Drive Axle
5
Inboard CV joint
AURLTQ012 Diagnose and repair light vehicle drive shafts
Document Name:
Student Written Knowledge Assessment – AURLTQ012
Created Date:
12
th
Aug 2020
Document No:
Trinity Institute (Australia) – AURLTQ012
Version No:
1.0
Last Modified
Date:
©Trinity Institute (Australia) | RTO Code: 41310 | CRICOS Code: 03556F
Page Sequence:
Page 14 of 24
25.
Examine the illustration below and note that the operating angle at the front of the drive shaft is offset by the one at the rear of the drive shaft. Why?
The angle of the front drive shaft is offsetting the angle of the rear drive shaft because if the u-joint accelerates making a vibration the rear universal joint is decelerates which results in vibration
26.
Name the five [5] external components of the drive axle below.
True or False question
AURLTQ012 Diagnose and repair light vehicle drive shafts
Document Name:
Student Written Knowledge Assessment – AURLTQ012
Created Date:
12
th
Aug 2020
Document No:
Trinity Institute (Australia) – AURLTQ012
Version No:
1.0
Last Modified
Date:
©Trinity Institute (Australia) | RTO Code: 41310 | CRICOS Code: 03556F
Page Sequence:
Page 15 of 24
27.
Both CV joints on a half shaft used in an RWD vehicle with independent rear suspension may be of the plunging style.
☐
True
or
☒ False
True or False question
28.
Constant velocity joints are used to transfer uniform torque at a constant speed, while operating through a wide range of angles.
☒ True
or
☐ False
True or False question
29.
Plunge-type CV joints allow the length of the axle assembly to change as the wheel travels up and down.
☒ True
or
☐ False
Multiple choice. Circle the correct answer
30.
The CV joints nearest the transaxle are called the inner
joints.
A.
Inner.
B.
Inboard.
C.
Outboard.
D.
Both “inner” and “inboard”.
Multiple choice. Circle the correct answer
31.
CV joints provide .
A.
Uniform torque transfer.
B.
Constant speed.
C.
Operation through a wide range of angles.
D.
All answers are correct.
Your preview ends here
Eager to read complete document? Join bartleby learn and gain access to the full version
- Access to all documents
- Unlimited textbook solutions
- 24/7 expert homework help
1
Boot retaining clamp
2
Boot
3
Outer bearing race
4
Housing
5
Outboard CV joint
6
Spacer Ring
7
Driver shaft
8
Lock Ring
9
Bushing
10 Spider
11 Retaining ring
AURLTQ012 Diagnose and repair light vehicle drive shafts
Document Name:
Student Written Knowledge Assessment – AURLTQ012
Created Date:
12
th
Aug 2020
Document No:
Trinity Institute (Australia) – AURLTQ012
Version No:
1.0
Last Modified
Date:
©Trinity Institute (Australia) | RTO Code: 41310 | CRICOS Code: 03556F
Page Sequence:
Page 16 of 24
32.
Name the eleven [11] components of the tripod plunge-type joint below.
33.
Identify three (3) symptoms of a failed U-joint.
1. squeaking or weird noise when starting to move in a forward direction
2. vibration felt in the entire vehicle when moving forward in speed
3. leakage of transmission fluid from the rear of transmission
True or False question
34.
An inclinometer is used to check the operating angle of the drive shaft.
☐
True
or
☒ False Multiple choice. Circle the correct answer
AURLTQ012 Diagnose and repair light vehicle drive shafts
Document Name:
Student Written Knowledge Assessment – AURLTQ012
Created Date:
12
th
Aug 2020
Document No:
Trinity Institute (Australia) – AURLTQ012
Version No:
1.0
Last Modified
Date:
©Trinity Institute (Australia) | RTO Code: 41310 | CRICOS Code: 03556F
Page Sequence:
Page 17 of 24
35.
If a noise is heard while driving straight ahead but it ceases on turns in the same direction, what is the most likely cause?
A.
A
bad
wheel
bearing.
B.
A worn inner cv joint.
C.
A worn outer cv joint.
D.
A bad intermediate shaft bearing.
Multiple choice. Circle the correct answer
36.
A shudder or vibration only when accelerating is most likely caused by .
A.
Out-of-balance axle shaft.
B.
Excessive play in the inboard plunge joint.
C.
Both
“out-of-balance
axle
shaft”
and
“excessive
play
in
the
inboard
plunge
joint”.
D.
Neither “out-of-balance axle shaft” nor “excessive play in the inboard plunge joint”.
Multiple choice. Circle the correct answer
37.
A humming or growling noise in the front of the vehicle that changes with road speed could be caused by
.
A.
Inadequate lubrication of the inner CV joint.
B.
Worn or damaged wheel bearings.
C.
A bad intermediate shaft bearing [equal length axle shaft system].
D.
All
answers
are
correct.
True or False question
38.
An FWD vehicle that makes a clunking noise when the automatic transmission is shifted into gear is being diagnosed. The problem could be excessive play in an inner or outer CV joint.
☒ True
or
☐ False
Multiple choice. Circle the correct answer
39.
A popping or clicking noise when turning indicates a possible worn outer_ CV joint.
A.
Outer.
B.
Inner.
AURLTQ012 Diagnose and repair light vehicle drive shafts
Document Name:
Student Written Knowledge Assessment – AURLTQ012
Created Date:
12
th
Aug 2020
Document No:
Trinity Institute (Australia) – AURLTQ012
Version No:
1.0
Last Modified
Date:
©Trinity Institute (Australia) | RTO Code: 41310 | CRICOS Code: 03556F
Page Sequence:
Page 18 of 24
C.
Both “inner” and “outer”.
D.
Neither “inner” nor “outer”.
Fill in the Gaps
40.
Complete the following statement about CV joint inspection using the following words. Words: Boot, Condition, Deformed, Escapes, Heat, Normal, Rubbing
Begin CV joint inspection by checking the condition
of the boots. Splits, cracks, tears, punctures, or thin spots caused by rubbing
call for immediate boot replacement. If the boot appears rotted, this indicates improper greasing or excessive heat
, and it should be replaced. Squeeze all boots. If any air _
escapes
, replace the boot. If the inner boot appears to be collapsed or deformed
, venting it (allowing air to enter) might solve the problem. Place a round- tipped rod between the boot
and drive shaft. This equalizes the outside and inside air and allows the boot to return to its normal
shape.
41.
From the list below of FWD drive shaft customer concerns, list the possible causes and corrective remedy.
Customer Concern
Possible Cause
Corrective Remedy
Vibration throughout vehicle
Defective tire, a worn driveline U- joint,
Changing tires, replacing the U-joint
Vibration throughout vehicle at low speed
Misshapen tyre
Separation of Internal belts and tread from the body of the tyre
Changing the overall body of the tyre is needed.
Vibrations during acceleration
Due to play in the outboard or inboard joints. It can also be due to a worn in the inboard plunge joint. It
can also be caused due to a bad intermediate shaft bearing on the transaxles. It can be caused by a broken engine mounts.
Replacing broken motor mount Ensuing that all the equipment’s are
well maintained. Changing the inboard plunge joint.
Grease dipping on the ground or spraying on chassis parts
Gravity is analysed to work on a stationary grease in order to draw oil
to a low point. It is noted that if the low point is not sealed properly oil can leak away from the grease tube
It is essential that the new grease tubes or cartridges should be stored in an upright position with a plastic cap at all times. If the cartridge is left
within a grease gun it is vital to depressurize the gun and stored in a
horizontal position
Your preview ends here
Eager to read complete document? Join bartleby learn and gain access to the full version
- Access to all documents
- Unlimited textbook solutions
- 24/7 expert homework help
Document Name:
Student Written Knowledge Assessment – AURLTQ012
Created Date:
12
th
Aug 2020
Document No:
Trinity Institute (Australia) – AURLTQ012
Version No:
1.0
Last Modified
Date:
©Trinity Institute (Australia) | RTO Code: 41310 | CRICOS Code: 03556F
Page Sequence:
Page 19 of 24
AURLTQ012 Diagnose and repair light vehicle drive shafts
Clicking or popping noise heard when turning curves and corners
This can be caused due to a damaged or worn outer cv joint
The CV shaft assembly needs to be replaced
A clunk during accelerating, decelerating, or putting an automatic transaxle into drive
This noise occurs because of excessive play of the inner joint in the FWD application, either outer or an inner joint in a RWD independent
suspension. It can also happen due to excessive play of the driveshaft CV joint.
After diagnosing the exact issue, the joint causing the problem will have to be replaced.
A clunk noise when putting an automatic transmission into gear or when starting out from a stop
Transmission and motor mounts provide a cushioned point of contact
between the vehicles frame (Galvagno et al., 2019). As the age of the vehicle increases, the cushions often shrink becoming brittle, falling out of place and may even split. All the mentioned
conditions can cause clunking noise
It is vital that the motor mounts should be repaired and maintained in order to enhance their performance.
A shudder or vibration when accelerating
This can happen by excessive play in the outboard or inboard joints, but
the most prominent cause is a worn out inboard plunge joint.
The inboard and outboard joints should be replaced.
A cyclic vibration that comes and goes between 45 and 60mph (72
and 100 km/h)
The most common cause of this type of vibration is due to worn out tyres. If the tyres of the car is out of
balance then the steering wheels might shake.
The tyres of the car should be replaced
True or False question
42.
A vibration that occurs during all modes of driving, especially at 56 – 72 kph (35 – 45 mph), is most often caused by a faulty universal joint, a bent drive pinion shaft, or a damaged pinion flange. All of these will cause the drive shaft to have excessive runout.
☐
True
or
☒ False
Fill in the Gaps
43.
Complete the following statement about removing and replacing a CV joint using the following words.
Words: Axle, Brake, Circlip, Control, Damaging, Discarding, Grease, Ground, Hammer, Inboard, Inspect, Joint, Location, Needs, Pressure, Position, Raising, Reinstall, Removal, Separate, Slide, Steering, Wheel
AURLTQ012 Diagnose and repair light vehicle drive shafts
Document Name:
Student Written Knowledge Assessment – AURLTQ012
Created Date:
12
th
Aug 2020
Document No:
Trinity Institute (Australia) – AURLTQ012
Version No:
1.0
Last Modified
Date:
©Trinity Institute (Australia) | RTO Code: 41310 | CRICOS Code: 03556F
Page Sequence:
Page 20 of 24
1
Removing the axle from the car begins with the removal of the wheel cover and wheel hub
cover. The hub nut should be loosened before raising
the car and removing the wheel.
2
After the car is raised and the wheel
is removed, the hub nut can be unscrewed from the axle shaft.
3
The brake
line holding clamp must be loosened from the suspension.
4
The ball joint must be separated from the steering
knuckle assembly. To do this, first remove the ball joint retaining bolt. Then pry down on the control
arm until the ball joint is free.
5
The inboard
joint can be pulled free from the transaxle.
6
A special tool is normally needed to separate
the axle shaft from the hub allowing the axle to be removed from the car. Never hit the end of the axle with a hammer
.
7
The axle shaft should be mounted in a soft-jawed vise for work on the joint
. Pieces of wood
on either side of the axle work well to secure the axle without damaging
it.
8
Begin boot removal by cutting and discarding
the boot clamps
9
Scribe a mark around the axle
to indicate the boots position on the shaft. Then move the boot off the joint
10
Remove the circlip
and separate the joint from the shaft.
11
side
the old boot off the shaft
12
Clean and inspect
the joint, then wipe the axle shaft clean and install the new boot onto the shaft.
13
Place the boot into its proper location
on the shaft and install a new clamp.
14
Using a new circlip, reinstall the joint on the shaft. Pack joint grease
into the joint and boot. The entire packet of grease that comes with a new boot needs
to be forced into the boot and
joint.
15
Pull the boot over the joint and into its proper position
. Use a dull screwdriver to lift an edge
of the boot up to equalize the pressure
inside the boot with the outside air.
16
Install the new large boot clamp and reinstall
the axle into the car. Torque the hub nut after the wheels have been reinstalled and the car is sitting on the ground
. Always follow the correct procedure for the clamp being installed.
AURLTQ012 Diagnose and repair light vehicle drive shafts
Document Name:
Student Written Knowledge Assessment – AURLTQ012
Created Date:
12
th
Aug 2020
Document No:
Trinity Institute (Australia) – AURLTQ012
Version No:
1.0
Last Modified
Date:
©Trinity Institute (Australia) | RTO Code: 41310 | CRICOS Code: 03556F
Page Sequence:
Page 21 of 24
Fill in the Gaps
44.
Complete the following statement about removing and replacing a U- joint using the following words.
Words: Assembly, Bearing, Brass, Carefully, Correct, Drive, Ear, Index, Joint, Large, Position, Press, Push, Retaining, Rings, Shaft, Socket, Spider, Start, Trunnion, Yoke,
1
Clamp the slip yoke
in a vise and support the outer end of the drive shaft.
2
Remove the lock rings on the tops of the bearing cups. Make joint
marks in the yoke so that
the joint can be assembled with the correct
phasing.
3
Select a socket that has an inside diameter large
enough for the bearing cup to fit into;
usually a 1¼-inch socket works.
4
Select a second socket
that can slide into the shaft’s bearing cup bore – usually a 9/16-
inch socket.
5
Place the large socket against one vise jaw. Position the bearing
shaft yoke so that the
socket is around a bearing cup.
6
Position the other socket to the center of the brass
cup opposite to the one in line with the
large socket.
7
Carefully tighten the vise to push
the bearing cup out of the yoke and into the large socket.
8
Separate the joint by turning the trunnion
over in the vise and driving the cross and
remaining bearing cup down through the yoke with a assembly
drift and hammer.
9
Use a drift and hammer to drive the shaft
out of the other yokes.
10
Clean any dirt from the yoke and the index
ring grooves.
11
carefully
remove the bearing cups from the new U-joint.
12
Place the new _
ear
inside the yoke and push it to one side.
13
Start one cup into the yoke’s ear and over the cross’s drive
.
14
Carefully place the spider
in a vise or U-joint bearing press and press the cup partially through the ear.
15
Remove the shaft from the vise and press
the cross toward the other side of the yoke.
16
push
a cup into the yoke’s ear and over the trunnion.
17
Place the shaft in the vise and tighten the jaws to press the bearing cup into the retaining
and over the trunnion. Then install the snap ring
. Make sure they are seated in their grooves.
Your preview ends here
Eager to read complete document? Join bartleby learn and gain access to the full version
- Access to all documents
- Unlimited textbook solutions
- 24/7 expert homework help
AURLTQ012 Diagnose and repair light vehicle drive shafts
Document Name:
Student Written Knowledge Assessment – AURLTQ012
Created Date:
12
th
Aug 2020
Document No:
Trinity Institute (Australia) – AURLTQ012
Version No:
1.0
Last Modified
Date:
©Trinity Institute (Australia) | RTO Code: 41310 | CRICOS Code: 03556F
Page Sequence:
Page 22 of 24
18
position
the joint’s cross in the drive shaft yoke and install the two remaining bearing cups.
Multiple choice. Circle the correct answer
45.
Before servicing the rear U-joint, slip joint, or centre bearing on a two-piece drive shaft, .
A.
Make index marks on both ends of the driveshaft.
B.
Measure the pinion shaft angle.
C.
Measure the distance between the centre bearing and slip joint. D.
All answers are correct.
46.
What parts are included in a typical CV joint service kit?
Axle shaft, inner boot, outer boot, clamp, cv joint
True or False question
47.
You should use an impact wrench to tighten axle hub nuts.
☒ True
or
☐ False
True or False question
48.
Stake the axle hub nuts after they are tightened to lock them in place.
☐
True
or
☒ False
Multiple choice. Circle the correct answer
49.
CV joints are lubricated with .
A.
GL1 chassis grease.
B.
iSilicone polymer-based grease.
C.
White lithium grease.
D.
Special
high-temperature,
high-pressure
grease
made
specifically
for
CV
joints.
Your preview ends here
Eager to read complete document? Join bartleby learn and gain access to the full version
- Access to all documents
- Unlimited textbook solutions
- 24/7 expert homework help
AURLTQ012 Diagnose and repair light vehicle drive shafts
Document Name:
Student Written Knowledge Assessment – AURLTQ012
Created Date:
12
th
Aug 2020
Document No:
Trinity Institute (Australia) – AURLTQ012
Version No:
1.0
Last Modified
Date:
©Trinity Institute (Australia) | RTO Code: 41310 | CRICOS Code: 03556F
Page Sequence:
Page 23 of 24
50.
Consider the various post repair checks that you would make during a road test on the vehicle drive shafts?
It is important to identify the sounds that it is making during the right as well as left turning
Multiple choice. Circle the correct answer
51.
Which source of information will give you the most detail about diagnosing and repairing light vehicle drive shafts on the vehicle you are working on?
A.
Workshop
manual.
B.
Owner’s manual.
C.
Google.
D.
Textbooks.
52.
Why is it very important that the Job Card is completed correctly?
A job card helps in encompassing the details of a work that is required to be performed. Jo cards are used to understand the task therefore; job card application is used for creating and managing job cards (Lichter and Schiprowski, 2021). The planning and scheduling information are required while creating the job card which are later used by the work order and task cards tracking applications.
Your preview ends here
Eager to read complete document? Join bartleby learn and gain access to the full version
- Access to all documents
- Unlimited textbook solutions
- 24/7 expert homework help
AURLTQ012 Diagnose and repair light vehicle drive shafts
Document Name:
Student Written Knowledge Assessment – AURLTQ012
Created Date:
12
th
Aug 2020
Document No:
Trinity Institute (Australia) – AURLTQ012
Version No:
1.0
Last Modified
Date:
©Trinity Institute (Australia) | RTO Code: 41310 | CRICOS Code: 03556F
Page Sequence:
Page 24 of 24
Liu, Y., Li, M., Haupt, R.L. and Guo, Y.J., 2020. Synthesizing shaped power patterns for linear and planar
antenna arrays including mutual coupling by refined joint rotation/phase optimization. IEEE Transactions on
Antennas and Propagation, 68(6), pp.4648-4657.
Sakai, R., Yoshida, Y. and Tajima, K., 2018. Study on Analysis of Torque-Slip Characteristics of Axial Gap Induction Motor. Transaction of the Magnetics Society of Japan Special Issues, 2(1), pp.43-47.
Schöller, C., Aravantinos, V., Lay, F. and Knoll, A., 2020. What the constant velocity model can teach us about pedestrian motion prediction. IEEE Robotics and Automation Letters, 5(2), pp.1696-1703.
Sikdar, S., Siddaiah, A. and Menezes, P.L., 2020. Conversion of waste plastic to oils for tribological applications. Lubricants, 8(8), p.78.
Your preview ends here
Eager to read complete document? Join bartleby learn and gain access to the full version
- Access to all documents
- Unlimited textbook solutions
- 24/7 expert homework help
Related Documents
Related Questions
Please assist with answering the following question?
arrow_forward
Select atleast two testing devices from among the categories (you may go beyond two). Discuss its application and methods of use. a. testing for speed (Tachometer), b. Testing of Air Consumption (Air-box method/viscous-flow meter), c. testing of exhaust smoke (Bosch/Hartridge/PHS), d. testing of exhaust emission (flame ionization detector/spectroscopic analyzers/gas chromatography) e. testing of torque (absorption dynamometer/transmission dynamometer).
arrow_forward
replace the mechanical and electrical components of motor vehicles, such as gaskets, belts,
hoses, timing belts, water pumps, radiators, alternators, and starters. They may not replace major
Question 3
Not yet
answered
components such as engines and transmissions.
Marked out of
1.00
Select one:
P Flag
question
O a. Light line technicians
O b. Heavy line technicians
O c. Lube technicians
O d. Chassis and brake technicians
Next pa
Previous page
arrow_forward
4
arrow_forward
The design process
Identify the problem
Do research
Develop possible solutions
Choose one solution
Design and construct a prototype.
Test the prototype
Communicate results
Evaluate and redesign.
8. How would an engineer use the design process to build a car that uses less gas?
arrow_forward
please read everything properly... Take 3 4 5 hrs but solve full accurate drawing on bond paper don't use chat gpt etc okk
arrow_forward
to see what will happen to
3. Safety engineers use
people in a collision.
4. Decide whether each of the following statements is true (T) or false (F). Place your
answer in the blank space provided.
a. Restraining features operate continuously while you are driving.
b. Operational features hold vehicle occupants in place.
C. Brakes are an example of a structural feature.
d. Crumple zones are examples of operational features.
e. An air bag is an example of a restraining feature.
of the collision between the
5. Crumple zones increase the
occupants and the interior of the vehicle.
arrow_forward
00
T
R
%24
Bb R
V qa
du/webapps/assessment/take/launch.jsp?course_assessment_id%=_254968_1&course_id%3D 3565256_1&content id= 52826
* Question Completion Status:
Attach File
Browse Local Files
Browse Content Collection
QUESTION 2
A company needs to choose one supplier for a particular type of silicon wafer used'in the production of
semiconductors. The company has three options. Supplier A sells the silicon wafers for $2.50 per wafer,
independently of the number of wafers ordered. Supplier B sells the wafers for $2.40 each but does not
consider an order for less than 2,000 wafers. Supplier C sells the wafers for $2.30 each but does not accept
an order for less than 3,000 wafers. Assume an order setup cost of $100 and an annual requirement of 20,000
wafers. Assume a 20% annual interest rate for holding cost calculations.
a. Which supplier should be chosen to minimize the total annual cost for the wafers, and what is the
optimal order quantity?
b. If the replenishment lead time for wafers…
arrow_forward
The answer from Bartleby is missing/blank. Can someone help answer it please and credit this question if possible since it would have been included/explained?
Thank you
Chapter 50 multiple Choice #5 what is the cause of an extremely hard brake pedal
arrow_forward
I need answers for problems 4, 5, and 6 pertaining to the print provided.
arrow_forward
Given the removal and replacement time data in the table, calculate IMART (mean time to repair)
Part identity
Bolts
Earth strap
Power lead
Signal lead
Cover plate
Brushes
Lesson 1.2 HW#1
Quantity Failure rate x 10-4 (h) Total M task time (h)
3
0.20
1
0.10
0.36
0.10
0.26
0.35
2
0.46
0.12
0.36
1.16
1.05
23.6
arrow_forward
An accident investigation report must include all of the following except:
The date of the accident
Names of those witnessing the accident
A description of the incident
Factors that contributed to the incident
arrow_forward
Hi please assist with the 3 questions attached
arrow_forward
I need parts 4, 5, and 6 answered pertaining to the print provided.
arrow_forward
Which of the following are not used for creativity enhancement?
TRIZ
Questioning assumptions
The Kung-Lo method
Six Thinking Hats
Please correctly answer within 5 minutes
arrow_forward
SEE MORE QUESTIONS
Recommended textbooks for you
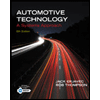
Automotive Technology: A Systems Approach (MindTa...
Mechanical Engineering
ISBN:9781133612315
Author:Jack Erjavec, Rob Thompson
Publisher:Cengage Learning
Related Questions
- Please assist with answering the following question?arrow_forwardSelect atleast two testing devices from among the categories (you may go beyond two). Discuss its application and methods of use. a. testing for speed (Tachometer), b. Testing of Air Consumption (Air-box method/viscous-flow meter), c. testing of exhaust smoke (Bosch/Hartridge/PHS), d. testing of exhaust emission (flame ionization detector/spectroscopic analyzers/gas chromatography) e. testing of torque (absorption dynamometer/transmission dynamometer).arrow_forwardreplace the mechanical and electrical components of motor vehicles, such as gaskets, belts, hoses, timing belts, water pumps, radiators, alternators, and starters. They may not replace major Question 3 Not yet answered components such as engines and transmissions. Marked out of 1.00 Select one: P Flag question O a. Light line technicians O b. Heavy line technicians O c. Lube technicians O d. Chassis and brake technicians Next pa Previous pagearrow_forward
- 4arrow_forwardThe design process Identify the problem Do research Develop possible solutions Choose one solution Design and construct a prototype. Test the prototype Communicate results Evaluate and redesign. 8. How would an engineer use the design process to build a car that uses less gas?arrow_forwardplease read everything properly... Take 3 4 5 hrs but solve full accurate drawing on bond paper don't use chat gpt etc okkarrow_forward
- to see what will happen to 3. Safety engineers use people in a collision. 4. Decide whether each of the following statements is true (T) or false (F). Place your answer in the blank space provided. a. Restraining features operate continuously while you are driving. b. Operational features hold vehicle occupants in place. C. Brakes are an example of a structural feature. d. Crumple zones are examples of operational features. e. An air bag is an example of a restraining feature. of the collision between the 5. Crumple zones increase the occupants and the interior of the vehicle.arrow_forward00 T R %24 Bb R V qa du/webapps/assessment/take/launch.jsp?course_assessment_id%=_254968_1&course_id%3D 3565256_1&content id= 52826 * Question Completion Status: Attach File Browse Local Files Browse Content Collection QUESTION 2 A company needs to choose one supplier for a particular type of silicon wafer used'in the production of semiconductors. The company has three options. Supplier A sells the silicon wafers for $2.50 per wafer, independently of the number of wafers ordered. Supplier B sells the wafers for $2.40 each but does not consider an order for less than 2,000 wafers. Supplier C sells the wafers for $2.30 each but does not accept an order for less than 3,000 wafers. Assume an order setup cost of $100 and an annual requirement of 20,000 wafers. Assume a 20% annual interest rate for holding cost calculations. a. Which supplier should be chosen to minimize the total annual cost for the wafers, and what is the optimal order quantity? b. If the replenishment lead time for wafers…arrow_forwardThe answer from Bartleby is missing/blank. Can someone help answer it please and credit this question if possible since it would have been included/explained? Thank you Chapter 50 multiple Choice #5 what is the cause of an extremely hard brake pedalarrow_forward
- I need answers for problems 4, 5, and 6 pertaining to the print provided.arrow_forwardGiven the removal and replacement time data in the table, calculate IMART (mean time to repair) Part identity Bolts Earth strap Power lead Signal lead Cover plate Brushes Lesson 1.2 HW#1 Quantity Failure rate x 10-4 (h) Total M task time (h) 3 0.20 1 0.10 0.36 0.10 0.26 0.35 2 0.46 0.12 0.36 1.16 1.05 23.6arrow_forwardAn accident investigation report must include all of the following except: The date of the accident Names of those witnessing the accident A description of the incident Factors that contributed to the incidentarrow_forward
arrow_back_ios
SEE MORE QUESTIONS
arrow_forward_ios
Recommended textbooks for you
- Automotive Technology: A Systems Approach (MindTa...Mechanical EngineeringISBN:9781133612315Author:Jack Erjavec, Rob ThompsonPublisher:Cengage Learning
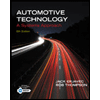
Automotive Technology: A Systems Approach (MindTa...
Mechanical Engineering
ISBN:9781133612315
Author:Jack Erjavec, Rob Thompson
Publisher:Cengage Learning