Lab_Report_Sample (1)
docx
keyboard_arrow_up
School
McGill University *
*We aren’t endorsed by this school
Course
261
Subject
Mechanical Engineering
Date
Feb 20, 2024
Type
docx
Pages
5
Uploaded by KidLeopard3246
MECH 261/262
Measurement Lab
Lab 0: Aircraft Wind-Tunnel Testing
GROUP 1
Dimitri CALOMIRIS 123456788
Raphael LIMBOURG 123456789
January 25
th
, 2021
Abstract
The main purpose of this lab was to determine the aerodynamic forces acting on an aircraft, and
experimentally confirm that the lift and drag forces were within reasonable theoretical expectations. The model
aircraft in question was conceptually designed as a capstone project, scaled down in size and 3D printed. After
conducting several tests, the experiment concluded that the aircraft would indeed have sufficient lift for takeoff
and landing, however did not closely match the predicted efficiency for cruising flight – with an error of about
36%.
Introduction
The main objective of the lab experiment is to verify that the actual forces acting on a scaled-down aircraft
match those predicted by the theoretical equations. This will be accomplished by testing the model in a wind-
tunnel, for three configurations: takeoff, cruise and landing. The wind-tunnel uses an analog force-balance to
measure the aerodynamic forces, lift and drag. These values will then be used to determine the aerodynamic
efficiency and compared with the theory. The following will introduce the reader to some basic aerodynamics for
the purposes of this report.
The driving force behind aircraft flight is the lift force, and is often calculated using equation (1). One simple
way of describing lift force is by pressure. Underneath the wings, typically exists a high pressure region, whereas
above is usually low pressure. This difference is often created by rotating the fluid around a particular geometry,
such as an airfoil.
L
=
1
2
ρU
2
SC
L
(1)
A frictional force that opposes the flow motion is referred to the drag force. In aeronautics, the usual goal is to
minimize the drag such that the vehicle can perform more efficiently. Having less drag results in longer flight and
can save up to millions of dollars of fuel over an entire fleet [1]. Similarly to lift, the drag can be calculated using
equation (2).
D
=
1
2
ρU
2
SC
D
(2)
Another important concept in aerodynamics is how efficient the vehicle can be. Often this value is used to
calculate the extended range, and optimal performance of an aircraft. The aerodynamic efficiency, also labeled the
lift-to-drag ratio, is described in equation (3). Aerospace engineers often use the maximum lift-to-drag ratio to
select their airfoils based on the flight regime and Reynolds number; see MECH 331,533, and other aerodynamic
courses to learn more.
η
=
L
D
(3)
The following section will detail the experimental procedure and apparatus used to acquire the data necessary
to complete the lab objectives. The data will then be post-processed, analyzed and discussed.
NOTE: Any additional background information relevant to the lab, experiment or analysis that is not common
knowledge should be described in this section. Treat a lab report audience as someone who is familiar in your
field, however is not directly in your class and may require a reminder on how an apparatus functions or how an
important parameter is calculated. If you take any information from the Lab Manual, make sure to properly cite it. Experimental Apparatus and Methodology
In order to properly conduct the experiment, the equipment listed below was required
. After ensuring all the
equipment was functioning properly, the 3D printed aircraft was mounted in the wind-tunnel using a support rod
apparatus. Several measurements were taken, at velocity increments of 1 m/s, starting at 10 m/s until 22 m/s was
reached. It was recommended not to exceed 22 m/s because of equipment limitations. Due to the configuration of
the wind tunnel scales for lift and drag forces, the jet had to be mounted on its side. At each step, the force and
drag forces were recorded. Once the experiment was conducted, it was also important to measure the effects of the
mounting rod, to properly estimate the aerodynamics of the aircraft alone. To do this, force and drag
measurements were taken for this external piece, and then respectively subtracted from the initial ones. One
Lab 0
Group 1
Page 1
additional requirement that was not listed in the lab handout [2]
, necessary to successfully complete the lab, was
to zero the force balance before taking any measurements because of a vibrational issue with the apparatus. The experimental methodology used to accomplish the objectives of this lab takes the actual force
measurements, and with proper scaling techniques, estimates the full-scale aircraft aerodynamics. These final
results will then be analyzed, and compared to the theoretical predictions – highlighting the major advantages of
scale down modelling techniques, or perhaps the limitations of the equipment. NOTES: Please, DO NOT write one line stating: “A full experimental procedure and equipment list can be found
in the handout [1]”. Briefly explain the main methodology of the experiment required to accomplish the lab
objectives, list the important equipment and provide any additional details necessary for the reader to comprehend.
Results and Discussion
The final results
of the experiment have been summarized in Table 1
. By observation, it is clear that there are
several differences between the measured and theoretical values
for lift, drag and aerodynamic efficiency. These
values have also been plotted to better witness the effects of velocity on the aerodynamic forces; which can be
found in Figure 1. The trend from this chart depicts increasing lift and drag force with increasing velocity
. At a
quick glance, this trend demonstrates the proportionality between the forces and velocity given by the theoretical
equations, (1) and (2). However, the percent difference between the measurements and mathematical solutions are
as high as 150%. Several reasons could explain these discrepancies, and will be discussed thoroughly shortly. Table 1: Summary Table of Final Results at 22 m/s
Type
Lift [N]
Drag [N]
Aerodynamic Efficiency [ ]
Takeoff Configuration
Actual Experiment
1.40
0.50
3.0
Theoretical Prediction
1.50
0.20
7.5
% Difference
6.67 %
150.0 %
60.00 %
Cruise Configuration
Actual Experiment
0.38
0.10
7.6
Theoretical Prediction
0.60
0.05
12.0
% Difference
36.67 %
100.0 %
36.67 %
Lab 0
Group 1
Page 2
Your preview ends here
Eager to read complete document? Join bartleby learn and gain access to the full version
- Access to all documents
- Unlimited textbook solutions
- 24/7 expert homework help
Figure 1: Chart depicting the effects of velocity on lift and drag force
Answer Discussion Questions Here.
Each lab report will have unique questions, and are considered to be the most
important part of the lab. Try to separate each question in a paragraph but make sure they are incorporated into
your text. Point form is not acceptable.
Conclusion
In this lab, we measured the aerodynamic forces exerted on a scaled down aircraft; accomplished by mounting
the model in a wind tunnel and using an analog force balance to measure lift and drag. The actual measurements
and the theoretical calculations were then compared, as per the main goal of the experiment.
In conclusion, the objectives of the lab were mostly successful. The final results demonstrated the aircraft was
capable of producing sufficient lift force for takeoff and cruise. The final values during takeoff, for a velocity of 22
m/s, were found to be 1.4 [N] of lift, 0.5 [N] of drag and an aerodynamic efficiency of 3, which is actually quite
lower than expected. In fact, there were several discrepancies between the actual values, and the predicted ones;
some of which were as high as 150%. Although several sources of error were listed, the main concern was the
intense vibrations coming from the wind tunnel and thus inconsistency of the analog force measurements.
Nevertheless, the overall trends predicted the theory presented in the introduction, and the team is satisfied with
the results.
If another iteration were to be conducted, the experiment should attempt to minimize the vibrations of the
wind-tunnel and take the measurements once again. Furthermore, a smoother model would be used than the one in
the experiment, which had many chips and ridges along the wings; can be seen in the appendix figures. References
[1] Wheeler, A. J., & Ganji, A. R. (1996). Introduction to engineering experimentation
. Pearson Education.
Lab 0
Group 1
Page 3
Appendix
Raw Data Tables Here.
Figure 2: Wings (with flaps) of the 3D-printed Aircraft
Lab 0
Group 1
Page 4
Related Questions
2. A student team is to design a human-powered submarine for a design competition. The overall
length of the prototype submarine is 4.85 m, and its student designers hope that it can travel fully
submerged through water at 0.440 m/s. The water is freshwater (a lake) at T = 15 °C. The design
team builds a one-fifth scale model to test in their university's wind tunnel, as shown in the Fig. A
shield surrounds the drag balance strut so that the aerodynamic drag of the strut itself does not
influence the measured drag. The air in the wind tunnel is at 25 °C and at one standard atmosphere
pressure. At what air speed do they need to run the wind tunnel in order to achieve similarity?
Take for water at T = 15 °C and atmospheric pressure, p = 999.1 kg/m³ and µ = 1.138 × 10-³ Pa.s.
Take for air at T = 25 °C and atmospheric pressure, p = 1.184 kg/m³ and µ = 1.849 × 105 Pa.s.
Wind tunnel test section
V
Poo, P
Model
Shield
FD
Drag balance
Strut
arrow_forward
2. A student team is to design a human-powered submarine for a design competition. The overall
length of the prototype submarine is 4.85 m, and its student designers hope that it can travel fully
submerged through water at 0.440 m/s. The water is freshwater (a lake) at T = 15 °C. The design
team builds a one-fifth scale model to test in their university's wind tunnel, as shown in the Fig. A
shield surrounds the drag balance strut so that the aerodynamic drag of the strut itself does not
influence the measured drag. The air in the wind tunnel is at 25 °C and at one standard atmosphere
pressure. At what air speed do they need to run the wind tunnel in order to achieve similarity?
Take for water at T = 15 °C and atmospheric pressure, p = 999.1 kg/m³ and µ = 1.138 × 10-³ Pa.s.
Take for air at T = 25 °C and atmospheric pressure, p = 1.184 kg/m³ and µ = 1.849 × 10-³ Pa.s.
V
Por P
Wind tunnel test section
Model
Shield
FD
Drag balance
Strut
arrow_forward
A one-fourth scale model of a car is to be tested in a wind tunnel. The conditions of the actual car are V = 45 km/h and T = 0°C and the air temperature in the wind tunnel is 20°C. In order to achieve similarity between the model and the prototype, the wind tunnel is run at 180 km/h. The properties of air at 1 atm and 0°C: ? = 1.292 kg/m3, ? = 1.338 × 10−5 m2/s. The properties of air at 1 atm and 20°C: ? = 1.204 kg/m3, ? = 1.516 × 10−5 m2/s. If the average drag force on the model is measured to be 70 N, the drag force on the prototype is (a) 66.5 N (b) 70 N (c) 75.1 N (d ) 80.6 N (e) 90 N
arrow_forward
Fluid Mechanics Problem
Note: Fluids are assumed to be at 20oC.
arrow_forward
part a) An air ship is to operate at 20 m/s in air at standard conditions. A model is constructed to 1/20 scale and tested in a wind tunnel at the same air temperature to determine drag. What criterion should be considered to obtain dynamic similarity?
part b) If the model is tested at 75 m/s. what pressure should be used in the wind tunnel? If the model drag force is 250 N, what will be the drag of the prototype?
arrow_forward
Fluid Mechanics Problem
Note: Fluids are assumed to be at 20oC.
arrow_forward
(b) A wind-tunnel experiment is performed on a small 1:5 linear-scale model of a car, in order
to assess the drag force F on a new full-size car design. A dimensionless "drag coefficient"
Ca is defined by
C, =-
pu'A
where A is the maximum cross-sectional area of the car in the flow. With the model car, a
force of 3 N was recorded at a flow velocity u of 6 m s. Assuming that flow conditions
are comparable (i.e., at the same Reynolds number), calculate the expected drag force for
the full-sized car when the flow velocity past it is 31 m s (equivalent to 70 miles per
hour). [The density of air p= 1.2 kg m.]
arrow_forward
2. Outcomes 1 and 4.Show and explain all work. You must show and explain all work. The drag
on the hull of a sailboat can be shown to depend on the boat velocity V, the water density p and viscosity
μ, the length of the hull f, and the acceleration due to gravity g.
JIH
Class 40 Racing Yacht.
30
arrow_forward
Given:
The plane accelerates in its current trajectory with a= 100 m/s^2
Farag
Angle theta= 5°
W=105 kips
F_drag= 80 kips
m= 1000 lbs
Find: F_thrust, F_lift
Please include the KD.
Fthrust
Futel t Fueight
000
BY NC SA
2013 Michael Swanbom
arrow_forward
22°F
Clear
DDÈ DDE MMMBU BU ► ► ► 2GQ==§¤¤✰=aaa=Û¤ı1 × PDF PDF PDF PDF PDE
File | C:/Users/ignor/Downloads/Assignment%203%20(2).pdf
T❘ Read aloud
Draw
Ask Copilot
a) Use Newton's second law
b) Use the Torque equation
a
Search
TWO
Particle P is sliding along a circular path of radius r . The circular path is placed on top of a
truck that is moving to the left with a velocity of v and an acceleration of a. The friction is
negligible. Find the EOM of particle P.
O
0
2
r
of 6
| CD
P
eac
СО da | +
o
ENG
60
T
6L
N
{0}
7:39 PM
1/17/2024
x
arrow_forward
I need help with my MATLAB code. There is an error in the following code. The error says my orbitaldynamics function must return a column vector. Can you help me fix it?
mu_earth = 398600.4418; % Earth's gravitational parameter (km^3/s^2)
R_earth = 6378.137; % Earth's radius (km)
C_d = 0.3; % Drag coefficient (assumed)
A = 0.023; % Cross-sectional area of ISS (km^2)
m = 420000; % Mass of ISS (kg)
% Initial conditions: position and velocity (ISS state vector)
% ISS initial state vector (km and km/s) - sample data
state_ISS =[-2.1195e+03, 3.9866e+03, 5.0692e+03, -5.3489, -5.1772, 1.8324];
% Time span for 10 revolutions
T_orbit = 2 * pi * sqrt((norm(state_ISS(1:3))^3) / mu_earth);
time_span = [0, 10 * T_orbit];
% Step 3: Numerical integration using ODE solver
options = odeset('RelTol', 1e-12, 'AbsTol', 1e-12);
[t, state] = ode45(@orbitalDynamics, time_span, state_ISS, options);
% Step 4: Plot the results
figure;
plot3(state(:, 1), state(:, 2), state(:, 3));
xlabel('X…
arrow_forward
(Review experimental scaling) A lightweight parachute is being designed for
military use. Its diameter D is 20 ft and the total weight W of the falling payload,
parachute, and equipment is 190 lb. The design terminal settling speed V. (or
terminal velocity) of the parachute at this weight is 16 ft/s. A one-twelfth scale
model of the parachute is tested in a wind tunnel. The wind tunnel temperature and
pressure are the same as those of the prototype, which is 70 °F and standard
atmospheric pressure.
a) Calculate the drag coefficient of the prototype. (Hint: At terminal velocity,
speed is constant so weight is in equilibrium with aerodynamic drag.)
b) At what speed should the wind tunnel be run in order to achieve dynamic
similarity?
c) Find the aerodynamic drag force of the model parachute in the wind tunnel
in pounds.
Payload
arrow_forward
The drag force of a new sports car is to be predicted at a speed of 65 mi/h at an air temperature of 25 C. Automotive engineers build a 0.333333333333333 scale model of the car to test in a wind tunnel. The temperature of the wind tunnel air is also 25 C. Determine how fast (in mi/h) the engineers should run the wind tunnel to achieve similarity between the model and the prototype.
arrow_forward
A model pump has an impeller diameter of 30 cm. During a manufacturer's test, this model achieved an efficiency of 80%. A prototype in the same family (geometrically similar) is 10 times larger
than this tested model. Under the same operating conditions dynamically similar to those in the model test, what most approximately will be the efficiency of the prototype pump?
O 74%
OOOO
O 64%
O 84%
O 94%
arrow_forward
3. In the study of aerodynamic drag on a stationary body, an appropriate non-dimensional grouping has been
found to be:
QAU3
where, P is the power lost, p is the density of the fluid, A is a typical area, and U is the velocity of the fluid. In
laboratory tests with a 1:10 scale model (ratio of the length) at 25°C, the power lost was measured as 5 w
when the air velocity was 0.5 m/s. Calculate the power lost in the prototype (kW) at 25°C when the air velocity
is 1 m/s.
arrow_forward
M Inbox - wep10@zips.uakron.edu
O My Akron Experience - The Univ
B Homepage - Statics 801
O Pearson MyLab and Mastering
b The equivalent resultant force, di x
Course Home
A https://openvellum.ecollege.com/course.html?courseld=16245503&OpenVellumHMAC=67fab398401alafde96db3b49e605db9#10001
O My Courses
KAssignment 10o
Course Home
Problem 4.137
3 of 4
Syllabus
I Review
Scores
Replace the three forces acting on the plate by a wrench. Suppose
that FA = {450i}N, FB = {-350k} N, and Fc = {300j} N.
(Figure 1)
Part B
eТext
Determine the couple moment of the wrench.
Express your answer to three significant figures and include the appropriate units. Enter positive value if the sense of direction of the couple moment is the
same as that of the resultant force and negative value if the sense of direction of the couple moment is opposite to that of the resultant force.
Study Area
Document Sharing
TH HẢ
?
User Settings
Value
Units
Course Tools
>
Submit
Previous Answers Request Answer
X Incorrect; Try…
arrow_forward
=
MMB 241 Tutorial 2.pdf
1 / 3
75%
+ +
Tutorial z
Topic: Kinematics of Particles:-.
QUESTIONS
1. Use the chain-rule and find y and ŷ in terms of x, x and x if
a) y=4x²
b) y=3e
c) y = 6 sin x
2. The particle travels from A to B. Identify the three unknowns, and write the three
equations needed to solve for them.
8 m
10 m/s
30°
B
x
3. The particle travels from A to B. Identify the three unknowns, and write the three
equations needed to solve for them.
A
40 m/s
20 m
B
1
arrow_forward
A fighter aircraft is to operate at 200 m/s in air at standard conditions (p= 1.2 kg/m³). A
model is constructed to 1/20 scale (length ratio) and tested in a wind tunnel at the same
air temperature (same air viscosity) to determine the drag force. The drag force Fp is a
function of the air density p and viscosity µ, the velocity V and the cross section length of
the airplane D.
a) Use dimensional analysis to prove that:
F,
and
PV²D²
pVD
What are these two dimensionless numbers?
b) If the model is tested at 50 m/s, what air density should be used in the wind
tunnel? Comment the result and give a recommendation.
c) If the model drag force is 250 N at 50 m/s, what will be the drag force of the
prototype?
Lift force
200 m/s
Drag force
arrow_forward
2. Casson model was discussed in class in the context of blood rheology. This
phenomenological model is often used to describe the shear stress vs. shear rate relationship
in colloidal suspensions where particle aggregation might cause the measured viscosity to
increase at low shear rates. In an experiment, data for the shear stress and the applied
shear rate S were fitted to the Casson model written below (in a slightly different form
compared to that given in the lecture notes):
√t = √²₁+√as.
(1)
The best least square fit parameters to the experimental data were found to be 40 mPa for the yield
stress to and 2.5 mPa s for the parameter a, which is referred to as the plastic viscosity.
a. Using Eq. (1), derive an expression for the fluid viscosity u as a function of S.
b. Plot the viscosity of the fluid as a function of S for 0.1s¹ ≤S≤ 10 s¹.
c. Based on class discussion on fluid classification, how would you characterize this fluid?
arrow_forward
SEE MORE QUESTIONS
Recommended textbooks for you
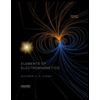
Elements Of Electromagnetics
Mechanical Engineering
ISBN:9780190698614
Author:Sadiku, Matthew N. O.
Publisher:Oxford University Press
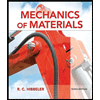
Mechanics of Materials (10th Edition)
Mechanical Engineering
ISBN:9780134319650
Author:Russell C. Hibbeler
Publisher:PEARSON
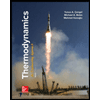
Thermodynamics: An Engineering Approach
Mechanical Engineering
ISBN:9781259822674
Author:Yunus A. Cengel Dr., Michael A. Boles
Publisher:McGraw-Hill Education
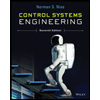
Control Systems Engineering
Mechanical Engineering
ISBN:9781118170519
Author:Norman S. Nise
Publisher:WILEY
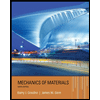
Mechanics of Materials (MindTap Course List)
Mechanical Engineering
ISBN:9781337093347
Author:Barry J. Goodno, James M. Gere
Publisher:Cengage Learning
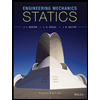
Engineering Mechanics: Statics
Mechanical Engineering
ISBN:9781118807330
Author:James L. Meriam, L. G. Kraige, J. N. Bolton
Publisher:WILEY
Related Questions
- 2. A student team is to design a human-powered submarine for a design competition. The overall length of the prototype submarine is 4.85 m, and its student designers hope that it can travel fully submerged through water at 0.440 m/s. The water is freshwater (a lake) at T = 15 °C. The design team builds a one-fifth scale model to test in their university's wind tunnel, as shown in the Fig. A shield surrounds the drag balance strut so that the aerodynamic drag of the strut itself does not influence the measured drag. The air in the wind tunnel is at 25 °C and at one standard atmosphere pressure. At what air speed do they need to run the wind tunnel in order to achieve similarity? Take for water at T = 15 °C and atmospheric pressure, p = 999.1 kg/m³ and µ = 1.138 × 10-³ Pa.s. Take for air at T = 25 °C and atmospheric pressure, p = 1.184 kg/m³ and µ = 1.849 × 105 Pa.s. Wind tunnel test section V Poo, P Model Shield FD Drag balance Strutarrow_forward2. A student team is to design a human-powered submarine for a design competition. The overall length of the prototype submarine is 4.85 m, and its student designers hope that it can travel fully submerged through water at 0.440 m/s. The water is freshwater (a lake) at T = 15 °C. The design team builds a one-fifth scale model to test in their university's wind tunnel, as shown in the Fig. A shield surrounds the drag balance strut so that the aerodynamic drag of the strut itself does not influence the measured drag. The air in the wind tunnel is at 25 °C and at one standard atmosphere pressure. At what air speed do they need to run the wind tunnel in order to achieve similarity? Take for water at T = 15 °C and atmospheric pressure, p = 999.1 kg/m³ and µ = 1.138 × 10-³ Pa.s. Take for air at T = 25 °C and atmospheric pressure, p = 1.184 kg/m³ and µ = 1.849 × 10-³ Pa.s. V Por P Wind tunnel test section Model Shield FD Drag balance Strutarrow_forwardA one-fourth scale model of a car is to be tested in a wind tunnel. The conditions of the actual car are V = 45 km/h and T = 0°C and the air temperature in the wind tunnel is 20°C. In order to achieve similarity between the model and the prototype, the wind tunnel is run at 180 km/h. The properties of air at 1 atm and 0°C: ? = 1.292 kg/m3, ? = 1.338 × 10−5 m2/s. The properties of air at 1 atm and 20°C: ? = 1.204 kg/m3, ? = 1.516 × 10−5 m2/s. If the average drag force on the model is measured to be 70 N, the drag force on the prototype is (a) 66.5 N (b) 70 N (c) 75.1 N (d ) 80.6 N (e) 90 Narrow_forward
- Fluid Mechanics Problem Note: Fluids are assumed to be at 20oC.arrow_forwardpart a) An air ship is to operate at 20 m/s in air at standard conditions. A model is constructed to 1/20 scale and tested in a wind tunnel at the same air temperature to determine drag. What criterion should be considered to obtain dynamic similarity? part b) If the model is tested at 75 m/s. what pressure should be used in the wind tunnel? If the model drag force is 250 N, what will be the drag of the prototype?arrow_forwardFluid Mechanics Problem Note: Fluids are assumed to be at 20oC.arrow_forward
- (b) A wind-tunnel experiment is performed on a small 1:5 linear-scale model of a car, in order to assess the drag force F on a new full-size car design. A dimensionless "drag coefficient" Ca is defined by C, =- pu'A where A is the maximum cross-sectional area of the car in the flow. With the model car, a force of 3 N was recorded at a flow velocity u of 6 m s. Assuming that flow conditions are comparable (i.e., at the same Reynolds number), calculate the expected drag force for the full-sized car when the flow velocity past it is 31 m s (equivalent to 70 miles per hour). [The density of air p= 1.2 kg m.]arrow_forward2. Outcomes 1 and 4.Show and explain all work. You must show and explain all work. The drag on the hull of a sailboat can be shown to depend on the boat velocity V, the water density p and viscosity μ, the length of the hull f, and the acceleration due to gravity g. JIH Class 40 Racing Yacht. 30arrow_forwardGiven: The plane accelerates in its current trajectory with a= 100 m/s^2 Farag Angle theta= 5° W=105 kips F_drag= 80 kips m= 1000 lbs Find: F_thrust, F_lift Please include the KD. Fthrust Futel t Fueight 000 BY NC SA 2013 Michael Swanbomarrow_forward
- 22°F Clear DDÈ DDE MMMBU BU ► ► ► 2GQ==§¤¤✰=aaa=Û¤ı1 × PDF PDF PDF PDF PDE File | C:/Users/ignor/Downloads/Assignment%203%20(2).pdf T❘ Read aloud Draw Ask Copilot a) Use Newton's second law b) Use the Torque equation a Search TWO Particle P is sliding along a circular path of radius r . The circular path is placed on top of a truck that is moving to the left with a velocity of v and an acceleration of a. The friction is negligible. Find the EOM of particle P. O 0 2 r of 6 | CD P eac СО da | + o ENG 60 T 6L N {0} 7:39 PM 1/17/2024 xarrow_forwardI need help with my MATLAB code. There is an error in the following code. The error says my orbitaldynamics function must return a column vector. Can you help me fix it? mu_earth = 398600.4418; % Earth's gravitational parameter (km^3/s^2) R_earth = 6378.137; % Earth's radius (km) C_d = 0.3; % Drag coefficient (assumed) A = 0.023; % Cross-sectional area of ISS (km^2) m = 420000; % Mass of ISS (kg) % Initial conditions: position and velocity (ISS state vector) % ISS initial state vector (km and km/s) - sample data state_ISS =[-2.1195e+03, 3.9866e+03, 5.0692e+03, -5.3489, -5.1772, 1.8324]; % Time span for 10 revolutions T_orbit = 2 * pi * sqrt((norm(state_ISS(1:3))^3) / mu_earth); time_span = [0, 10 * T_orbit]; % Step 3: Numerical integration using ODE solver options = odeset('RelTol', 1e-12, 'AbsTol', 1e-12); [t, state] = ode45(@orbitalDynamics, time_span, state_ISS, options); % Step 4: Plot the results figure; plot3(state(:, 1), state(:, 2), state(:, 3)); xlabel('X…arrow_forward(Review experimental scaling) A lightweight parachute is being designed for military use. Its diameter D is 20 ft and the total weight W of the falling payload, parachute, and equipment is 190 lb. The design terminal settling speed V. (or terminal velocity) of the parachute at this weight is 16 ft/s. A one-twelfth scale model of the parachute is tested in a wind tunnel. The wind tunnel temperature and pressure are the same as those of the prototype, which is 70 °F and standard atmospheric pressure. a) Calculate the drag coefficient of the prototype. (Hint: At terminal velocity, speed is constant so weight is in equilibrium with aerodynamic drag.) b) At what speed should the wind tunnel be run in order to achieve dynamic similarity? c) Find the aerodynamic drag force of the model parachute in the wind tunnel in pounds. Payloadarrow_forward
arrow_back_ios
SEE MORE QUESTIONS
arrow_forward_ios
Recommended textbooks for you
- Elements Of ElectromagneticsMechanical EngineeringISBN:9780190698614Author:Sadiku, Matthew N. O.Publisher:Oxford University PressMechanics of Materials (10th Edition)Mechanical EngineeringISBN:9780134319650Author:Russell C. HibbelerPublisher:PEARSONThermodynamics: An Engineering ApproachMechanical EngineeringISBN:9781259822674Author:Yunus A. Cengel Dr., Michael A. BolesPublisher:McGraw-Hill Education
- Control Systems EngineeringMechanical EngineeringISBN:9781118170519Author:Norman S. NisePublisher:WILEYMechanics of Materials (MindTap Course List)Mechanical EngineeringISBN:9781337093347Author:Barry J. Goodno, James M. GerePublisher:Cengage LearningEngineering Mechanics: StaticsMechanical EngineeringISBN:9781118807330Author:James L. Meriam, L. G. Kraige, J. N. BoltonPublisher:WILEY
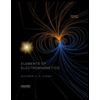
Elements Of Electromagnetics
Mechanical Engineering
ISBN:9780190698614
Author:Sadiku, Matthew N. O.
Publisher:Oxford University Press
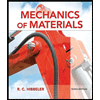
Mechanics of Materials (10th Edition)
Mechanical Engineering
ISBN:9780134319650
Author:Russell C. Hibbeler
Publisher:PEARSON
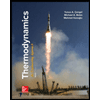
Thermodynamics: An Engineering Approach
Mechanical Engineering
ISBN:9781259822674
Author:Yunus A. Cengel Dr., Michael A. Boles
Publisher:McGraw-Hill Education
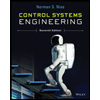
Control Systems Engineering
Mechanical Engineering
ISBN:9781118170519
Author:Norman S. Nise
Publisher:WILEY
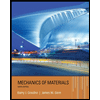
Mechanics of Materials (MindTap Course List)
Mechanical Engineering
ISBN:9781337093347
Author:Barry J. Goodno, James M. Gere
Publisher:Cengage Learning
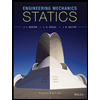
Engineering Mechanics: Statics
Mechanical Engineering
ISBN:9781118807330
Author:James L. Meriam, L. G. Kraige, J. N. Bolton
Publisher:WILEY